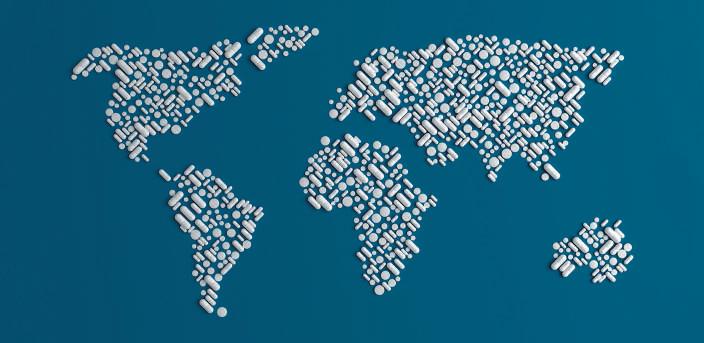
11 minute read
Automated Quality Systems in Supply Chains
from IPI Spring 2020
by Senglobal
Automated Quality Systems in Supply Chains Save Lives
Logistics for Pharmaceutical Organisations Require Lean Processes
Ensuring high product quality while simultaneously increasing efficiency along the supply chain is only possible if suppliers and logistics service providers consistently supply customers with high-quality materials. Precise control of the material is indispensable. This is particularly true when it comes to handling pharmaceuticals and biotechnological goods that are intended to save lives.
To ensure quality, many companies rely on a detailed internal quality management system based on Lean and total quality management (TQM) processes. The challenge is these companies often overlook quality related to manufacturing and material handling as part of the delivery process of warehousing, port transfers, and inter-modal transportation and the advantages from which they could benefit: By providing automated quality proofs during the production and delivery cycle, companies can ensure compliance, minimise material waste, and effectively save time and money on internal quality measures.
Challenging Industry Demands Innovative Solutions The pharmaceutical industry is the most challenging and specific industry in the world. Logistical processes, temperature- and time-related issues, and compliance, in particular, are more complex than those of conventional goods. A large number of raw materials for pharmaceuticals and goods used in biotechnology require transport under special conditions. The real-time control of materials along the entire production and transport chain is an important factor in quality assurance for both suppliers and customers. This approach enables companies to move from purely reactive management to proactive problem prevention throughout the global supply chain.
Now imagine the following situation: a single drug, utilised in thousands of hospitals, doctors' surgeries and pharmacies across Europe, is distributed
The pharmaceutical industry is the most challenging and specific industry in the world. © iStock.com/_Svetlana Mokrova worldwide – or the individual raw materials for this drug are produced in different companies all over the world. A widespread circulation of drugs like this complicates the tracking and the managing of quality, orders, inventory, and shipments.
As more and more of the supply chain today falls outside of the direct administration of the pharmaceutical manufacturer, digitisation of supply chain processes is key to maintaining control and visibility. More importantly, digitisation is required to help meet government regulations of track and trace of materials, from raw material suppliers to patients.
A digital supply network that extends control and visibility beyond the four walls of the manufacturer to all partners, including material suppliers, distributors, hospitals, pharmacies, packagers, and transporters will allow everyone on the network to see relevant information so they can better manage their component of the supply chain and guarantee high quality.
Capturing Quality Information of Raw Materials Track and trace from raw material suppliers through to the end patient requires data structures that support batch numbers, lot numbers, serial numbers, packaging levels, quality information, etc. and are able to link across raw materials and finished goods. In fact, a finished good certificate of analysis (COA) ideally will reflect the quality characteristics of the finished goods and each of its components. The certificate should include all details (manufacturing, movements, operations, quality, etc.) of raw materials and finished goods as they move through the supply chain and ultimately to the patient.
Today’s pharmaceutical companies often rely upon contract manufacturers to maximise flexible, high-quality production at minimum cost. Possibilities to check the quality results of the contractual partner should be as relevant as the costs. Using digitised internal and external quality controls of the pharmaceutical manufacturer through the logistics processes eliminates the possibility of tampering with specifications that drive counterfeiting in the supply chain. With continuous controls of the entire supply chain, inferior materials and mishandling during transport would be prevented. In the long term, waste can be reduced, spoilage is minimised and the patient receives a high-quality medication that helps to improve his or her health.
In order to improve process quality, it is necessary to integrate all quality-relevant functions and processes throughout the entire company and within the global supply chain. If the processes
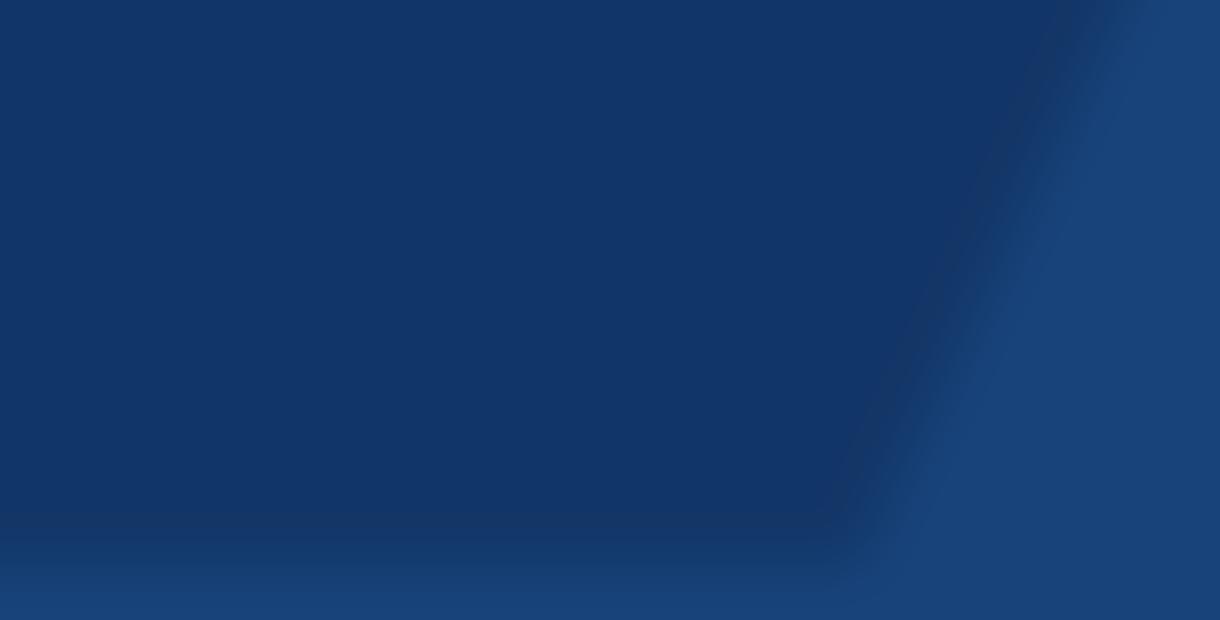
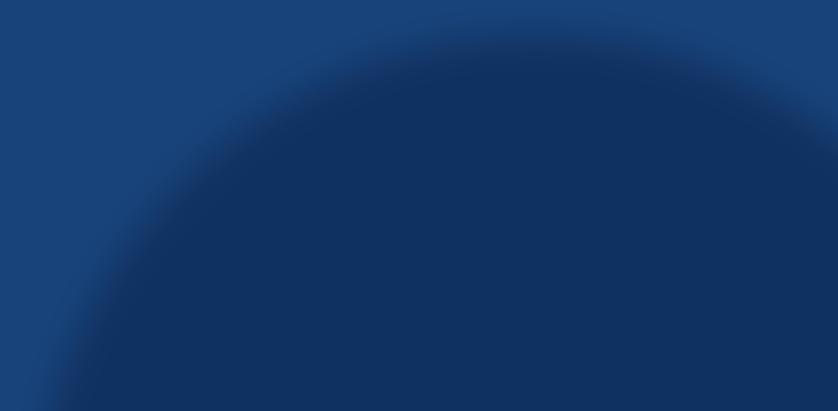
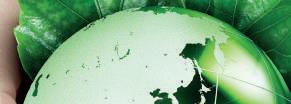
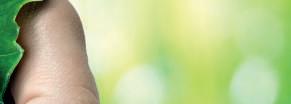
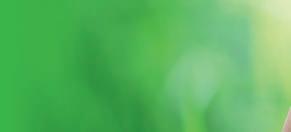

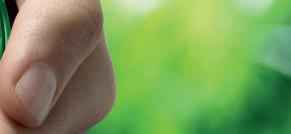

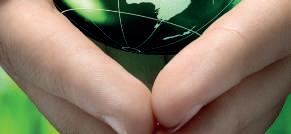

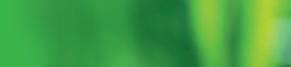
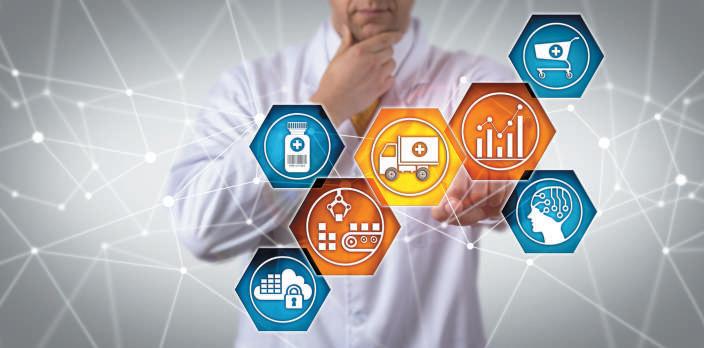
Logistical processes, temperature- and time-related issues, and compliance for pharmaceuticals are more complex than those of conventional goods. © iStock.com/LeoWolfert along the supply chain are precisely coordinated, the medical provider or patient will always feel confident in the quality of the medication. Thanks to optimised incoming goods processes, pharmaceutical manufacturers benefit from reduced inventory levels. With a trend toward more specialised, smaller batches of medicines produced, the systems of the extended supply chain need to be integrated to provide “pull” synchronisation of demand signals and process visibility. Data flows from these systems need to be orchestrated, including raw material and packaging orders; contract manufacturing orders; raw and intermediate materials and finished goods movements; transportation orders and status; shipment status; receipt of goods status; etc.
In addition, a global supply chain is extremely error-prone due to poor internet connections in specific geographies or data capture methods. Imagine a scenario in which dispersion of medications in specific regions are in the wrong packaging quanties based on cold chain stocking levels. Or inventory updates for re-ordering cannot be updated quickly based on poor internet connection of actual consumption rates. The entire supply chain is exposed in the blink of an eye relative to stocking levels, wastes, and shortages. Such risks can only be minimised if downstream partners operate in a secure environment with upstream fulfilment needs being communicated effectively. Some pharmaceutical companies are currently gaining initial experience in this field with the channels of distribution using blockchain technologies. Though in pilot type projects today, these innovative approaches will also considerably relieve quality management concerns in the future.
Data Analysis Enables Consistent Quality Another important point is the quality of exchanged data. The quality-relevant data for automated testing processes are already available: The internet of things, social media, structured customer feedback, and human perception generate a wealth of information that is of central importance for analysis. This data could identify early indicators of performance problems, prevent a recurrence of CAPA (corrective and preventive action), and help diagnose customer complaints faster. Many companies are already using the existing data to analyse risks and opportunities arising from the entire product development cycle and the customer journey.
In the case of temperature-dependent goods within the pharmaceutical industry, monitoring of temperature fluctuations and handling is necessary and has significant impacts. Transporting biologics is neither an easy task nor inexpensive. Each shipment of these specialised medications, which are
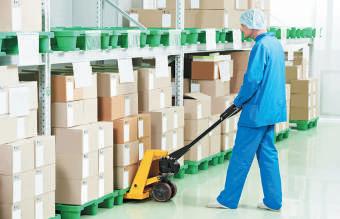
A large number of raw materials for pharmaceuticals and goods used in biotechnology require transport under special conditions. © iStock.com/kadmy produced using living organisms, requires a strict temperature range of two to eight degrees Celsius and can be worth up to 45 million Euros. The necessary temperature-controlled containers and storage facilities is a capacity issue in certain global regions. According to the current state of the art, this data can be collected, for example, by sensors or smart pallets where applicable.
In order to meet high-quality requirements, the regulation of temperature fluctuations is not the only decisive factor. Improper container movements and time-sensitive formulations such as vaccines at the port or in the warehouse can also be the cause of quality losses. The aim is, therefore, to use the analysis to identify trouble areas and support logistics providers and suppliers in optimising their processes.
Other aspects that should be taken into account are fluctuations in the actual formulation of the medication. Statistical process control and Pareto analysis based on global regulated guidelines for production are good methods for the tracking of material fluctuations. Typically, this is a cumbersome and labour-intensive activity. Non-conformance and corrective actions can be implemented for the logistics process. The ideal solution for suppliers and logistics service partners is to provide all material properties and formulations digitally, so that drug variations can be found immediately and shared between suppliers, producers, and the channels of distribution.
Track and Trace for Product Recalls The complexity of today’s global supply chains leaves companies increasingly vulnerable to unexpected supply disruptions, forcing many companies to view returns and recalls (due to cross-contamination with another drug or impurity substance) as a cost of doing business.
A drug recall is the most effective way to protect the public from a defective or potentially harmful product. According to governmental regulations, a recall needs to be communicated to the public to remove a defective drug product from the market. This communication is supported through supply chain processes related to serialised track
and trace, both forward and backward from consumers to the pharmaceutical manufacturer. Future recalls can be reduced as a part of extending the quality management solution into the logistics process for greater results.
Traceability of raw materials is possible in two directions: The first direction leads to product tracking. Using product tracking, the available data from the network provides information about where the raw material or medication is currently located – within the entire supply chain. This allows companies to find and remove necessary medications at the stocking level and goods in transit. Product tracing, on the other hand, identifies the origin of the drug or a group of raw materials. This allows companies to trace the product origin down to the smallest detail. Product recalls, quality defects and customer complaints can thus be traced down to the last detail and health concerns remedied.
Individual Treatments Need Supply Chain Transparency In addition, the paradigm shift in the biopharmaceutical manufacturing away from general treatments to personalised therapies for smaller patient groups creates new challenges for the area of quality management and the supply chain. These include a proliferation of stock keeping units (SKUs) to manage, production issues around producing very small batches of time-sensitive medications, and the logistical issues of delivery. These cell and gene therapies have to be tailored to the individual patient and bred individually.
These complex and highly targeted treatments can be lucrative but present a number of challenges in the era of personalised medicine supply chains. Precise, real-time control is crucial to avoiding quality issues, so the usage of regional manufacturing hubs will be necessary for these small batch items. To meet changing market demands, manufacturers are realising that technology, digitisation and especially connection along worldwide supply chains will be decisive components of the process.
These new personalised therapies are much more complex to produce, manage, and distribute than traditional medicines and cannot be made on the scale, the speed, reliability, and traceability required. The impact on the quality assurance functions in the organisation and across the supply chain are of paramount difference. The necessary error rates of nearly 0% will pose the biggest challenge as unique medications and treatments are added to the process. With 25% of pharmaceutical costs and 40% of medical device costs tied to the supply chain, there are opportunities for significant cost savings.
Improving the cold chain capabilities throughout the supply chain for transportation and storage requires a digital supply network integrating with time and temperature sensors from factories, warehouses, trucks, labs, and pharmacies that can monitor and send this information for both clinical trial supplies and approved products. These IoT tracking sensors tied to a digital supply network help pharmaceutical organisations to ensure the safety of their products in transit and in storage. The need for complete visibility and ability to respond quickly when needed will have an enormous impact on the current pharmaceutical supply chain model.
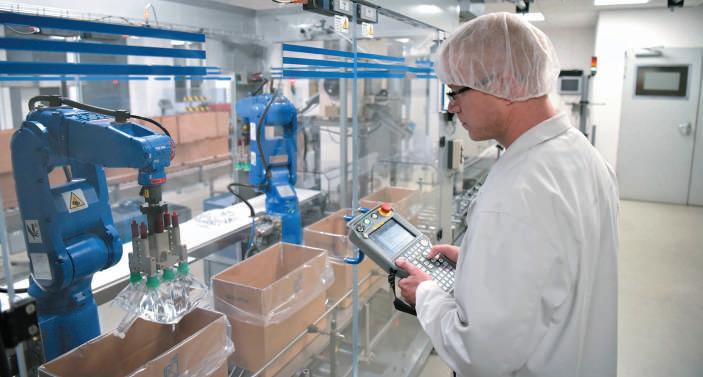
Conclusion In today’s global marketplace, quality management needs to be extended across the supply chain from manufacturer to logistics service providers, hospitals, pharmacies, and patients. Operational silos can be eliminated by having all participants connect to a digital supply network, fostering improved communications and collaboration to all. With a supply chain quality management solution built within a digital supply network, all participants on the network are privy to data, analysis, and information on what is happening across the supply chain. The data collected across the network gives deeper insights into quality information.
This is necessary since in the future the manufacturing of pharmaceuticals will become more automated and personalised. Track and trace and quality management solutions will be embedded in the everyday workings of pharmaceutical manufacturers, making it easier to solve the counterfeit drug challenges and to save lives.
David Cahn
David heads up Global Marketing at Elemica, the digital supply network provider for manufacturing industries. He has been implementing, marketing, and product managing leading enterprise applications for over 30 years, including ERP, SCM, TMS, and WMS solutions, and lived the world of customer-facing solutions and customer experience for the past few years. David has held leadership positions at Phillips, KPMG, CA, AMR Research, Aptean, and Infor. Additionally, he has started, built, and sold his own e-commerce and supply chain software company during the dot-com days, and had his own corporate development consulting company to the software industry for over ten years.