
8 minute read
Managing the Mass-Production of Tablets with Efficient
from IPI Winter 2020
by Senglobal
Managing the Mass-production of Tablets with Efficient Processes
The growing demand for increased tablet quantities and the goal of reducing time to market is putting pressure on tablet manufacturers. In order to keep up with this requirement, innovative processes and systems need to be adopted to improve production efficiency. Here we look at the importance of tool management systems and online training in the quest to produce high quantities of quality tablets.
Tablet Tool Management The availability and condition of tools is of primary importance for uninterrupted production. This is especially important in the pharmaceutical solid dose manufacturing environment where productivity is key. Shorter lead times and cost implications are putting pressure on manufacturers to invest in new technologies and processes. One area where investment is being made to meet demand is through new software solutions. The implementation of a comprehensive tool management system (TMS) is critical for a successful operation which improves the efficiency of manufacturing quality tablets. A primary objective of a TMS is to ensure that tooling is never a cause for delay in the production schedule.
Ask yourself these questions: Do you know where your tools are? Do you know what condition they are in? Is all the tooling available when required to ensure production runs smoothly? If the answer to any of these is ‘no’, it is time to invest in a proficient TMS. Operating a manufacturing process without the appropriate management in place will affect productivity and profitability. Effective tooling management will not only increase efficiency, but also keep up with growing industry demands.
The growing requirement for quality mass-produced tablets has highlighted clear trends within modern tablet production. They include the increase of capacity, flexibility, the speed of response and robust traceability with the core objective of maximised press uptime. Gone is the time when tool monitoring was achieved through modest manual methods. Recording data on paper is not sufficient or productive for today’s demanding high-volume manufacturing processes, which must be tightly controlled. Any problems within tool inventory management can have serious implications on the bottom line. In addition, manufacturers should have a complete audit trail covering tooling usage and maintenance. This is not only good practice but an important regulatory requirement in many tablet manufacturing environments. Without a robust management system that controls and documents the procedure efficiently, the consequences will be costly. Tablet tooling was once considered an expendable part of the manufacturing process and deemed part and parcel of production. But there are less obvious costs to consider, for example, those generated by the unavailability of tools due to avoidable damage or unexpected replacement – both leading to tablet press downtime. Through the development of computerbased monitoring systems, viewing tablet compression tooling as consumable items is changing and manufacturers are now maximising productivity per punch.
A core feature of a TMS is its capacity to keep track of the tooling maintenance. This is critical in obtaining the maximum life from punches and dies. It is important to maintain a logical, planned and professional approach to tooling maintenance to ensure tablet tooling failures are avoided; a TMS helps to achieve this. By implementing an advanced management system, problems like wear to punch heads and tips can be detected before they impact on production. It can also highlight when specific punch and die cleaning actions are required. These can be essential to avoid issues such as sticking and picking, cross contamination and corrosion.
Implementation of a tooling management system can also drastically improve tooling inventory availability. Without this information, either unnecessary tooling replacements are made, reducing productivity, or punches are deployed when they should be in maintenance or replaced. The latter circumstance produces problems with the end tablet when it is found that the tooling being used does not meet the highly demanding process of tablet manufacture. Rejected tablets, wasted formulation, very expensive press damage and press downtime is a common result. In addition to this, not having a clear picture of tooling availability may lead to the loss of opportunities in a fast-moving and competitive environment. Key Points to Finding the Right System With a number of different tool management systems on the market, it is important to choose one which can effectively record everything required for greater productivity. Make sure the TMS covers the following essential features:
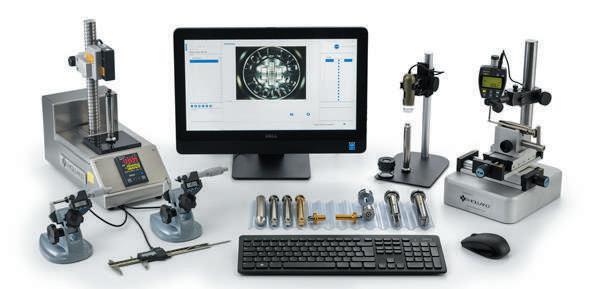
• Check it can proactively monitor tooling rotations, inventory which covers the tooling life-cycle and maintenance. • It should be compliant with protocols like the FDA’s Code of Federal Regulations – 21-CFR part 11, so important electronic records can be traced. • User-definable reporting will help to keep track of key performance indicators such as tablet quantities produced, per batch or yield. • Tool measurement capability which is compatible with industry standard measuring equipment. • It can access standard format documents so all previous drawings and images can be included. • It incorporates an in-depth guide to tooling specification and troubleshooting so any problems flagged up can be traced and rectified. • It features a warning to alert users of any problems including over-compression, when maintenance is required and even
when tooling replacements should be planned. • It includes an industry guide to compression tooling; for example, the
Eurostandard educational suite. This advises tablet manufacturers on tablet tooling terminology, configuration and procurement and includes the latest technical specification compatible with
ISO 18084:2005(E) – ‘Press Tools for
Tablets’. • It is a multilingual and adaptable system which is available in different configurations to work flexibly and seamlessly within an established manufacturing facility in any country.
This ensures all sites in a global company can work from the same system.
Through the use of a tool management system, tablet manufacturers can fulfil a core requirement of managing tooling in an ordered and traceable way. It knows where every tool is, what condition it is in and how long it has been in service, and can identify maintenance issues or poor handling problems by auditing all tooling and its respective processes. Educate to Accumulate To optimise tablet production, you must combine many factors, all of which will lead to better processes and a quality end product. Although the use of a tool management system will have a significantly positive effect on production, another method helping to improve production efficiency is education. Ensuring staff are skilled and knowledgeable in their roles is essential. In terms of tablet manufacture, knowledgeable staff can detect problems before they occur and identify solutions to overcome any issues that arise. Both lead to minimised tablet press downtime and will ultimately increase efficiency.
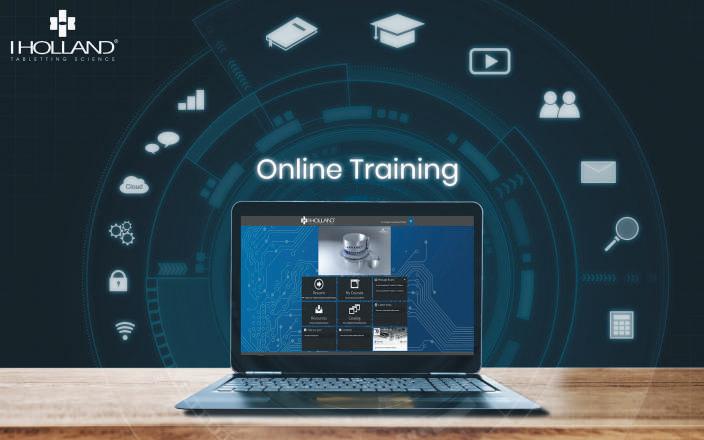
Although training may take place ‘on the job’, finding the time and correct information is not always easy. The introduction of electronic enabled learning is helping companies improve the skills of their staff and is seeing huge growth in recent years. This increase is being seen through all industries including those in tablet manufacturing. E-learning programmes can combine comprehensive and flexible courses in a wide variety of disciplines with the convenience of learning taking place in the workplace or off-site. The material should be delivered in a multimedia format incorporating engaging animations, webinars and interactive content. Furthermore, the information can be validated by interactive quizzes to ensure key points are understood. This is accessed via desktop computers or mobile devices making it easily available, permitting
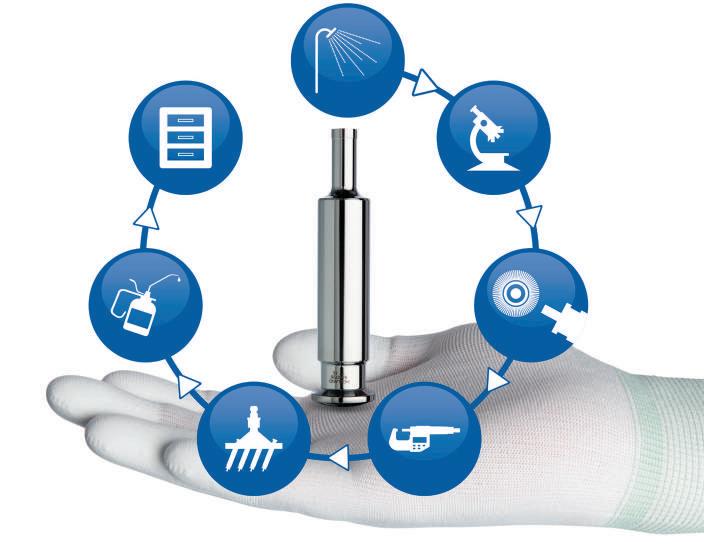
employees to be educated and updated on the best industry practices and tablet tooling developments whenever is best convenient.
‘E-Learning is a way to provide quick delivery of lessons. As compared to traditional teaching methods, this mode has relatively quick delivery cycles. This indicates that the time required to learn is reduced to 25%–60% of what is required in traditional learning.’1
Importantly e-learning can accommodate everyone from director level to engineers and operators looking to improve their knowledge in areas of tablet compression tooling. Newly developed courses are also designed with a hierarchical system giving training managers and supervisors a full audit, tracking and reporting of employee development and certification. Following the completion of each course, certification can be issued in line with a company’s operating procedures and guidelines including scheduling re-qualification after a period of elapsed time. With a compartmentalised structure, courses can be used across different departments, job roles, sites and even countries for comparison purposes. By ensuring key training is achieved and being used, manufacturers are helping to make processes more effective and efficient, therefore helping to increase the output and quality of the tablet. Take Control It is important to take control of tooling and production processes in order to achieve maximum productivity. Production management solutions have never been more important when it comes to the manufacture of tablets. The global growth of high-quality solid dose medication to be produced quickly and cost-effectively is putting an extra strain on manufacturers. To lessen the burden, new procedures need to be used, including incorporating advanced tooling management systems and investing in staff. Online training should be recognised as an important tool with which to share knowledge and improve technical skills and understanding.
They say ‘knowledge is power’, and this is true when it comes to optimising tablet manufacture. By ensuring the correct skills, procedures and tooling are in place, manufacturing processes can only advance. REFERENCES
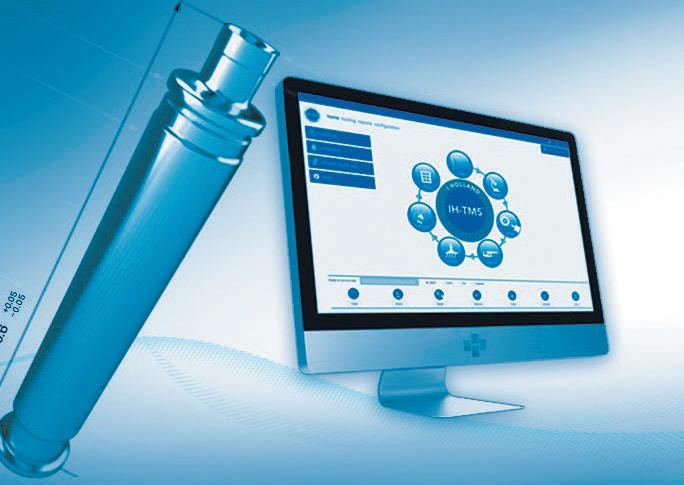

1. https://elearningindustry.com/9-benefits-ofelearning-for-students
Marianna D’Onghia
Marianna joined I Holland in 2016 after completing her master’s degree in marketing management. She recently hosted I Holland’s latest webinar and is heavily involved in the creation of the online training system platform. Marianna also hosts I Holland’s biannual Ultimate Guide Seminar.