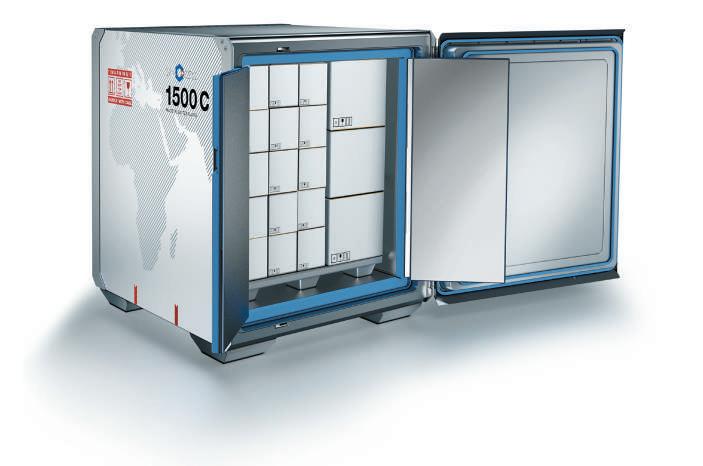
19 minute read
How Technology can Help Build a Fairer, Healthier World
from IPI Summer 2021
by Senglobal
Everyone can agree that the world has changed irreversibly – so much so that the term ‘new normal’ has been dropped, as it has become the normal that we now live by. Over the past couple of years, how we live our lives and do business has both fundamentally and irrevocably shifted. With a ‘glass half full’ mindset, I believe that despite the hurdles we’ve had to jump this year, technology has continued to meet and answer these challenges and will set us up for a fairer, and healthier future – if used correctly.
The pandemic has meant that technology has become deeply ingrained throughout society and has put the limitations of equal access into stark perspective. In order to create a fairer, and healthier, world, we need to ensure that access to life-saving medicines and the technologies that deliver them are felt in every corner of the world – not just the countries who can afford them.
Though not a new issue, with sensitive medicines such as the current batch of COVID-19 vaccines – from Pfizer to AstraZeneca – temperature control and safe transport are more crucial than ever. With limited ability to manufacture vaccines at the scale the world needs, making every drop count is of the utmost importance. With accidental temperature excursions, lack of storage facilities and potentially long waiting times in-transit, it is imperative that technology answers this problem to help ensure that within the supply chain, margin for error is removed and where possible, vaccines are not spoiled and will indeed reach their end destination – saving millions of lives.
Luckily, innovations driving new technology meeting these challenges have emerged to meet this increased demand – necessity is the mother of invention, after all. As such, technology can be an equaliser in this space, with new innovations that look to ensure lack of access to basic technology does not stop anyone, anywhere, from receiving the medications they need.
A truly global problem, with every country in the world affected, the COVID-19 pandemic has shown us that we need to make access to life-saving pharmaceuticals ubiquitous across the globe. Shining a light on resources available to first world vs third world countries, with rich nations vaccinating one person every second vs poorer nations who are yet to give a single dose, there is a clear divide between the two and their respective access to these medicines. This is a present and growing threat, as for these countries without access to vaccines, the risk of outbreak and further spreading of the virus is rising. It must be a massive global effort, by rich and poor countries alike, to work together to stop the spread and eliminate COVID-19 altogether. In fact, People’s Alliance, which includes Oxfam and Amnesty International, have stated that at least 90 per cent of people in 67 low income countries stand almost no chance of getting vaccinated this year because wealthier nations have reserved more than they need. In the UK, 400 experts have called on the Prime Minister to waive vaccine patents. However, if we suspend patents entirely, it will kill off innovation if the vaccine needs to be updated, or in the next pandemic. We should instead ensure that countries can obtain a licence and be able to manufacture the vaccine properly. This divide, with wealthy countries vaccinating their populations and poorer nations unable to get enough doses, has essentially created a ‘vaccine apartheid’.
With changes to the aforementioned intellectual property laws, efforts of the global vaccine project will be increased tenfold, and would address the disparity between wealthy and poor, ensuring equal access to vaccines. This would also reduce the politicisation of vaccines and transform vaccines from a benefit afforded to some to a guaranteed right. Funding is also an issue, with poorer nations having difficulty affording doses. Though the hope is that the expected 90 million Covax doses will help even out distribution, with rising cases in both India and Europe that is looking ever more unlikely, as countries continue to prioritise their immediate needs and not long-term global requirements.
COVID-19 is extremely infectious – it may seem logical to prioritise vaccinating a single national population, but in a globalised world, this health crisis only truly ends with a concerted international effort. A harrowing parallel to draw is the patent laws and distribution of HIV/AIDS drugs, also resulting in deaths – still to this day, there are countries where this is seen as merely a chronic condition, but there are others
where an HIV/AIDS diagnosis is in effect a death sentence. In this current crisis, we must learn from the mistakes of our past.
For most countries, vaccine rollout will continue to gain momentum over the coming months, and the pharmaceutical supply chain will need to continue to both adapt and be flexible in this unprecedented environment for the foreseeable future, and possibly forever. This pressure applies to all vendors within the supply chain, from manufacturers producing the vaccines, to the distributors managing logistics, to the carriers transporting these vaccines to their end destination.
Prior to COVID-19, the supply chain within the pharmaceutical industry was not a point of discussion. Before the pandemic, vaccines made up just 1.5% of global pharmaceutical sales and so their distribution has always been a niche aspect of the supply chain. Now, with the healthcare industry across the globe aiming to vaccinate around seven billion people, most requiring a double-dose, 14 billion doses will need to be manufactured and distributed with minimal spoilage, which would counteract these efforts. Strain is to be expected, and distribution will take time, but it can be said that the ‘teething stage’ within the entire supply chain might just be behind us, or might nearly be behind us if the right moves are made and laws are revised appropriately.
There are many challenges facing the safe delivery of vaccines to poorer nations, due to remote locations and lack of infrastructure, as well as the political roadblocks that inevitably exacerbate these issues. Often, climate is a factor, leading to even more problems when timing is everything and infrastructure is lacking. This presents a considerable challenge, with every solution unique to each country by necessity.
At the beginning of the pandemic, UNICEF pre-emptively reserved a stockpile of a half a billion syringes outside the countries producing them. However, countries put export controls on both vaccines and syringes and as prices rose, supplies were of course limited. Other countries followed suit, leading to a sort of ‘vaccine nationalism’, effectively putting a massive chink in the global vaccine supply chain and disrupting fair and consistent rollout.
Though the rollout of Covax vaccine is looking promising in achieving more widespread distribution, only the countries that are part of Covax have the infrastructure needed to get the vaccine pallets off planes and into refrigerated storage warehouses. Ghana is one of these lucky countries to successfully distribute Covax doses, though countries in West Africa, for example, do not have that luxury. It is critical that the means of distribution are adaptable to different environments. This can be on a large scale, such as adapting to temperature fluctuations within a given country, with things as simple as making sure vaccine containers can withstand both metaphorical and literal bumps in the road.
As I mentioned above, funding remains one of the quintessential roadblocks to fair distribution. With remote areas lacking infrastructure to house vaccine shipments, funding is needed to support the construction of warehouses. Though there have been many contributions from countries, from the EU to the UK and the US,
TOPRA Symposium now online!
22–24 September 2021 | Online event
Revolution in Regulatory Affairs: How the pandemic is shaping regulatory science
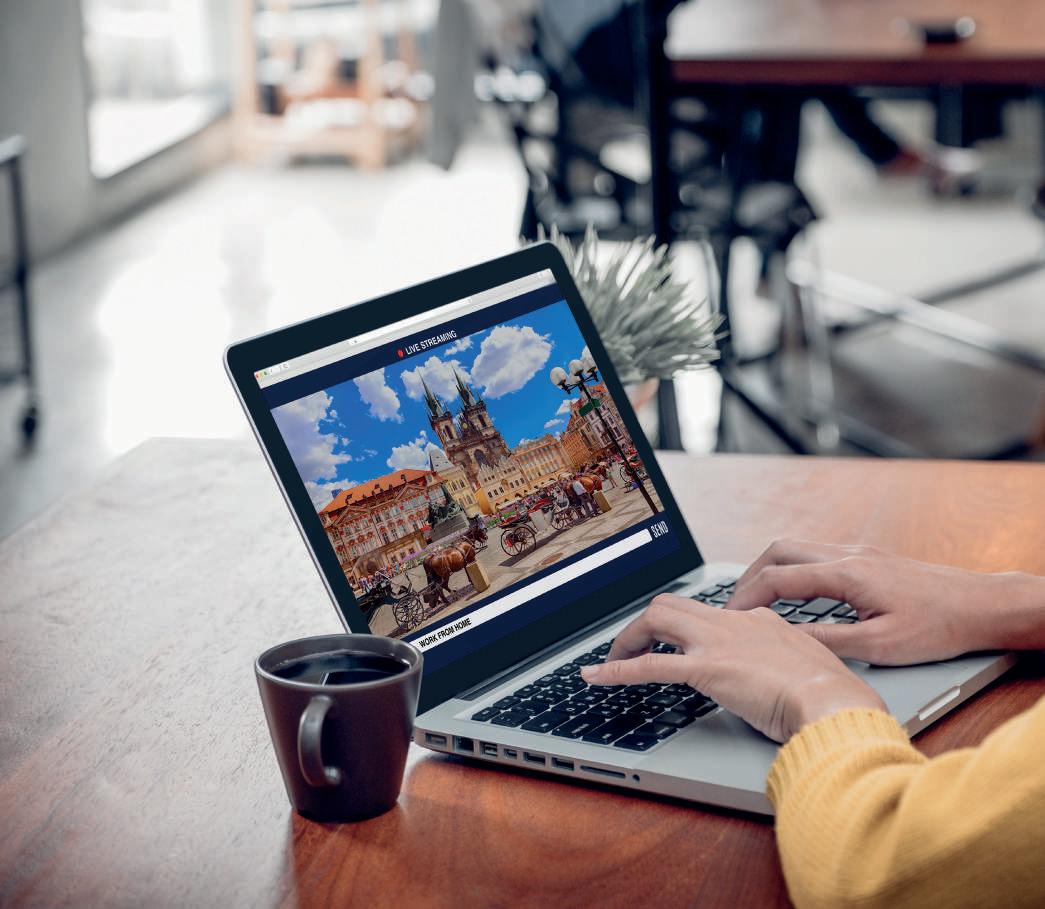
Register now www.topra.org/ipi-sym21
What is TOPRA?
TOPRA is the professional membership organisation for individuals working in healthcare regulatory affairs across all sectors – from medicines and combination products to medical devices and IVDs. We work with our members internationally to enable and promote excellence across the healthcare regulatory profession. “The platform has worked very well and given the challenges of speakers and delegates all being remote, I think that the speaker discussions and responding to delegate questions has been done well.”
— 2020 TOPRA Symposium attendee
we are still nowhere close to closing this funding disparity. UNICEF estimates that an additional 2 billion dollars is needed to help the 92 poorest countries who are in need of fridges, expenses for vaccinators, health worker training, fuel for trucks and more.
Finally, the last challenge is resistance – both from wealthier countries not willing to share their doses, and ‘vaccine hesitancy’ with people cautious to receive the vaccine. Individual countries are doing one-to-one deals with pharmaceutical companies, further putting strain on the supply chain. Alongside this, richer countries find themselves with an over-supply of available doses, which could be shared with countries in need – and worse, some of these vaccines are even being wasted.
This ‘vaccine hesitancy’ is something that must also be addressed, as though evidence supports vaccines saving lives, fear outweighs the life-saving potential. This is partly driven due to misinformation, so much so that the UN launched the ‘Verified’ campaign – aiming to educate and fight distorted information and messages – to become a source of trusted truth. This is the ultimate hurdle; it's one thing to ensure a country has enough supply of vaccines; it's another question convincing a population to take it. In the US, this is presenting a major problem, where vaccine uptake has become divided along political lines. We need to make sure that we have an exclusively medical public discourse and we continue to promote the critical importance of vaccines long after the pandemic has subsided.
Infrastructure problems, coupled with export controls, patent issues, intellectual property laws, and vaccine hesitancy present multiple challenges in getting the vaccines to those in need.
Over the past year, there have been a number of innovations in the pharmaceutical industry, especially when it comes to the supply chain. For example, there are now innovative containers that can maintain a stable internal temperature in extreme conditions from as low as -30°C to as high as 70°C. This year even saw the launch of deep-frozen containers that are able to cool to -80°C while maximising aircraft capacity utilisation, mitigating the traditional capacity limitations caused by the use of dry ice by making energy transfer more efficient.
Combating spoilage rates is important, not only in the current pandemic, but generally across the pharmaceutical industry. The industry accepts up to 12%, meaning a standard shipment of vaccines, similar to that which any COVID-19 vaccine would travel in, would be around 100,000 vials. The standard spoilage would mean that 12,000 vials would not be viable upon arrival. Innovations in the industry have brought this double-digit number down to almost zero.
This is a revolutionary improvement, as each of these vials will save lives and help stop the continued impact of the pandemic. Being able to deliver the vaccines to countries around the world in the first instance, be they rich or poor, with spoilage rates approaching zero per cent, will be the key to containing the spread and preventing further infections and deaths until we can eliminate the virus once and for all.
However, it’s not only innovation in the industry that is important. It is the partnerships across the industries that are pivotal in not only improving the supply chain, but helping to ensure medicines make it to where they need to go. Partnerships with airlines and shipping companies are paramount here. The likes of Qatar, Saudia Cargo, KLM Airfrance Martinair Cargo, Korean Air, LOT, and Virgin Atlantic cover almost all corners of the world, and make shipping these life-saving medicines a smoother process.
Furthermore, collaboration within the entire pharma supply chain is needed to maximise these airline and shipping company partnerships, allowing for fast and efficient distribution of vaccines. An

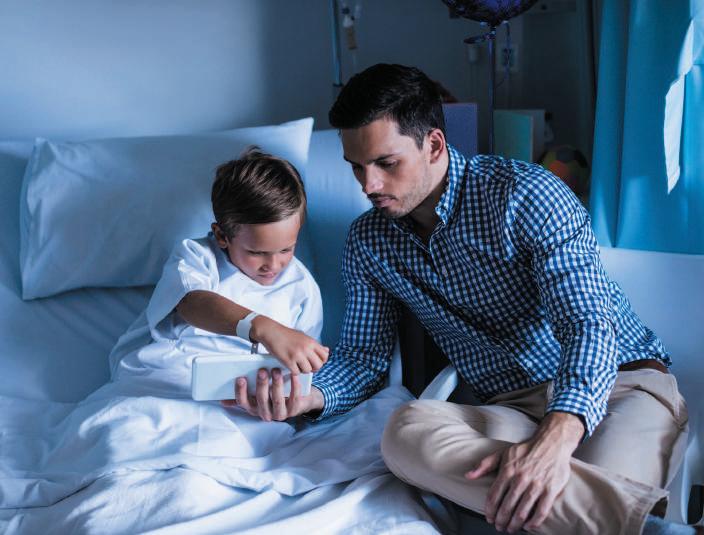

example is the Hope Consortium – a UAEbased public-private partnership offering a unique end-to-end supply chain solution capable of delivering large quantities of COVID-19 vaccines – from production to patients in emerging markets.
As I’ve mentioned, necessity is the mother of invention and we have been down this road before. The Spanish Flu brought about the early stages of DNA understanding, the plague during 1665 resulted in Newton’s theories on the concepts of gravity, and the Second World War prompted the invention of the first computer. I would like to hope that COVID-19 will be looked upon as a revolutionary time for the pharmaceutical industry, with innovations across the full expanse of the supply chain – though we still have a way to go. The pandemic has taught us that in a globalised world, diseases can spread faster than ever before. This also means that future pandemics will never be isolated to single countries – if there’s a lesson to be learned in the international community, it's that isolationist policies will not work. We need the international cooperation we have seen in the last year and a half to remain, in order to protect everyone from whatever comes next. Time will tell, but in any event lessons will be learned from this pandemic and past mistakes and ultimately impact our response to future pandemics – hopefully for the better.
In summary, technology has gone a long way towards contributing towards a healthier planet – but we are neither out of the woods nor all the way there just yet. We have seen rapid innovation arise to help fight against the pandemic, from vaccines to deep-frozen storage containers to an overhaul of the healthcare industry around the world. We are just witnessing the tip of the iceberg, so to speak, with more to follow as we continue to live in this ‘current normal’. Using these innovations and adaptations, we must now ensure that anyone, anywhere receives access to these vaccines. Not only do we have infrastructure hurdles to jump, but also financial, political and resourcing obstacles to overcome first. It is great to witness that progress is moving in the right direction, and as necessity and global need increase as we hopefully edge nearer and nearer to the end of the pandemic – with new technology constantly being developed to meet our new way of living and working, we are on track to becoming not just a healthier planet but a fairer, more just one.
Richard Ettl
Richard Ettl, the CEO of SkyCell, holds a Bachelor of Arts in Management from the University of Fribourg and attended the Executive Leadership Program at Harvard University and the Stanford University Graduate School of Business. Prior to founding SkyCell, Richard worked for Bobst SA in the company's production and logistics team. SkyCell is based on a strong set of values – innovation, reliability and sustainability – and has become the third largest pharma container provider within seven years. Richard helped establish the Institute for Value-Based Entrepreneurship (IVE) in Switzerland, which to date has offered business plan creation courses to more than 2500 students.
Foodmek Celebrates 50 Years with Growth Plan Success
Scottish bespoke engineering company Foodmek is celebrating both its 50th birthday and the continued success of its ambitious Scottish Enterprisebacked growth plan, which includes entry into the pharmaceuticals manufacturing engineering markets.
Thanks to the quality of the products and service delivered by its highly-skilled, dedicated workforce, the company, based in Tayport – just across the River Tay from Dundee – which designs, makes and installs engineering solutions for the pharmaceuticals, food, drink and cosmetic industries is enjoying a renaissance since its growth plan received the first tranche of £500,000 Scottish Loan Scheme funding from Scottish Enterprise in November 2019. It enabled Foodmek to invest in new equipment, innovation and extra highlytrained engineers in its design office and factory. This has allowed a dedicated focus on research & development.
Apprentices The funding also allowed it to recruit and train more staff through Graduate, Modern and Foundation Apprenticeships in collaboration with the University of Dundee – a core part of its strategy to prepare for the retirement of its most experienced staff, many of whom have long service of many decades. In fact, its longest-served staff member, Jim Carson, is 78, and still working after clocking up 42 years to date!
Foodmek now employs six design staff and is hiring two more Modern Apprentices to add to the pair recruited last year. Overall, eight people joined Foodmek last year, with five more planned this year.
That investment in people has helped Foodmek bounce back strongly from a decrease in orders caused by the COVID-19 lockdowns around the world.
Pharmaceuticals Market The global pandemic, however, helped Foodmek gain momentum in the international pharmaceutical market – part of its growth plan.
Between May last year and January this year it delivered 25 high-specification
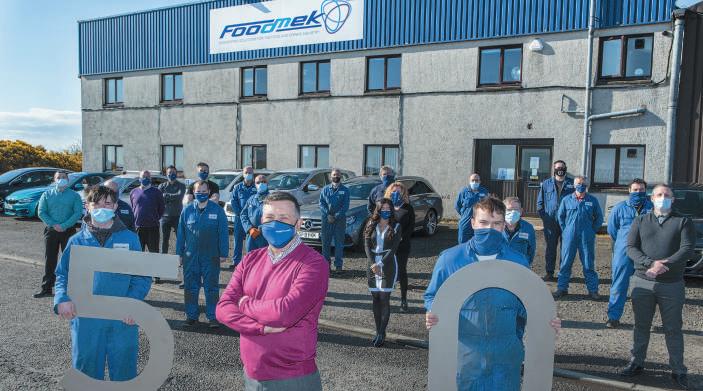
Foodmek MD Scot Kelly (centre), apprentices (left) Cameron Bell and (right) Lewis Ritchie with a stainless steel ‘50’ join staff members in marking 50 years in business.
200-litre stainless steel vessels over four orders to a global manufacturer of COVID-19 PCR test kits – for the production of the fluids required.
The client was so impressed with the high quality of the vessels it is currently in discussions about its next order. Foodmek is also working on a vessel for a veterinary medicine manufacturer and several large tanks for a bioengineering company.
Turnover Up 13% Despite Lockdowns That market entry success helped Foodmek grow in its 2020–21 financial year, despite the effects of the global pandemic on economies around the world. “During the end of our fiscal year ending May 2020, we saw an impact of the global pandemic,” revealed Managing Director, Scot Kelly. “However, in the fiscal year ending May 2021 we’ve seen a 13% increase in our turnover and are projecting a further 33% increase during our next fiscal year. This has also seen our headcount increase from 32 to 43 over the last two years. “Thanks to our success in the financial year to May 2021, we met all the requirements from Scottish Enterprise to draw down the second tranche of our Scottish Loan Scheme loan.
Investment “This has enabled us to invest in a new ERP system, which will transform our enterprise planning capability. A six-figure capital investment has also been made in upgrading our manufacturing equipment.”
Funding from the Energy Saving Trust has also enabled Foodmek to buy a Kia e-Niro electric pool car for customer visits – part of Foodmek’s net zero sustainability strategy.
‘Healthy’ Order Book Orders from existing and new customers have also driven Foodmek’s progress. Further orders are expected soon, adding to its “healthy” order book.
In line with its ethos, Foodmek plans to keep using its success to invest in the local community – through employability talks to local schools, engaging with community groups and a publicly-accessible defibrillator.
Foodmek believes that continuing to invest in people, machinery and new technologies is the blueprint for another successful 50 years. That’s begun already – it’s a Finalist for Engineering Company of the Year in the Scottish Business Insider Made in Scotland Awards.
For more information about Foodmek, go to http://bit.ly/Foodmek50Years
About Foodmek Foodmek Ltd provides design, manufacturing and installation engineering solutions to the pharmaceuticals, food, drink and cosmetic industries.
It supplies some of the largest food processing plants in the UK, as well as pharmaceuticals manufacturers and major cosmetics brands, and has exported to more than 20 countries since its foundation in 1971.

Some of the COVID-19 test kit vessels made by Foodmek.
Foodmek manufactures processing machinery for liquids – from conveyors, filling machines and cooking / mixing vessels to access platforms, pasteurising and cleaning equipment.
Biotechnology As well as the food industry, it also works with the biotechnology, cosmetics and other industries which benefit from using bespoke high-specification machinery.
Foodmek has been working closely with some of the UK’s leaders in biotechnology – providing them with cooking and mixing vessels tailored to comply with the increasing demands of the pharmaceutical industry’s regulations and requirements.
Modern pharmaceutical processes require incredibly sophisticated techniques and precise control to ensure the end product is as accurate as possible, something few equipment manufacturers can guarantee.
Consistent Foodmek’s 200- and 400-litre steamjacketed tanks are popular among its clients for their consistent, hygienic, robust and precise mixing and cooking. These are designed to the client’s individual needs to ensure end-product consistency.
It can make these larger if required – with a vast range of mixing options. It works with each client to make sure it gets the perfect vessel for its requirements.
Foodmek designs can be tailored to meet specific requirements of production output as well as overcome space constraints.
Highly Durable The company, based at Tayport, Fife, manufactures highly-durable products which adhere to established quality assurance standards.
During installation, Foodmek engineers work to provide its customers with optimal productivity while keeping production downtime to a minimum.
Foodmek offers a wide range of services, including full refurbishment of its equipment and stainless steel fabrication. Foodmek is Safe Contractor-certified, and ISO9001 and EN1090 certified.
Scottish Business Pledge In 2019, Foodmek committed to its staff with the Scottish Business Pledge, which includes: 1. Paying the real Living Wage 2. No inappropriate use of zero hours contracts 3. Action to address the gender pay gap 4. Environmental impact 5. Investing in a skilled and diverse workforce 6. Workforce engagement 7. Innovation 8. Internationalisation 9. Support our community 10. Prompt payment
Foodmek is a member of Scotland Food & Drink, Fife Chamber of Commerce and Dundee & Angus Chamber of Commerce.
For more about Foodmek’s work with the biotechnology sector, go to http://bit.ly/ FoodmekBiotech
For enquiries, call Business Development Manager, Ross Waite on 07943 024881. LinkedIn – linkedin.com/company/ foodmek-limited/ Twitter – twitter.com/FoodmekLtd Facebook – facebook.com/ Foodmek-157904604603674/ Instagram – instagram.com/foodmek_ltd YouTube – youtube.com/channel/ UCdN7FlFYoK2nZwNmVHKyFFw
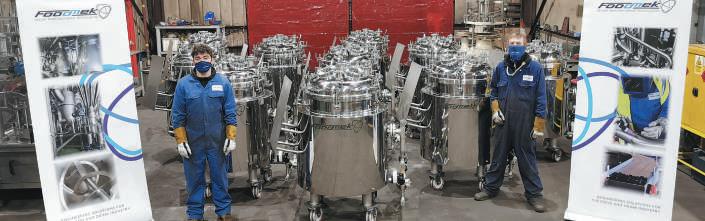
Scot Kelly
This month marks four years since Scot Kelly arrived at Foodmek to take up the position of Managing Director. He brought with him almost two decades of experience in precision manufacturing with global players to the firm with a long history of high-quality engineering and big brand clients. With a BSc in mechanical engineering from the University of Strathclyde and a DMS in management studies from Edinburgh Napier University, Scot became Global Commodity Director for NCR, based in Dundee, in August 2000. In 2002, he became its Director of Manufacturing – responsible for manufacturing assembly of ATMs, particularly low-volume, high-feature machines and new product introduction. In July 2008, Scot moved on to GE. There he spent just over two years as Fulfilment & Productivity Manager with GE Drilling & Production Systems, before moving to GE Oil & Gas to take up the role of D&P Engineering Planning Leader. In January 2012, Scot became the Subsea Engineering Operations Manager, based in Aberdeen. Scot’s final role at GE Oil & Gas was as Subsea Services Site Leader, based in Montrose, starting in July 2013. Before taking on the leadership of Foodmek, Scot was the Interim Project Manager at ATMRC Ltd.