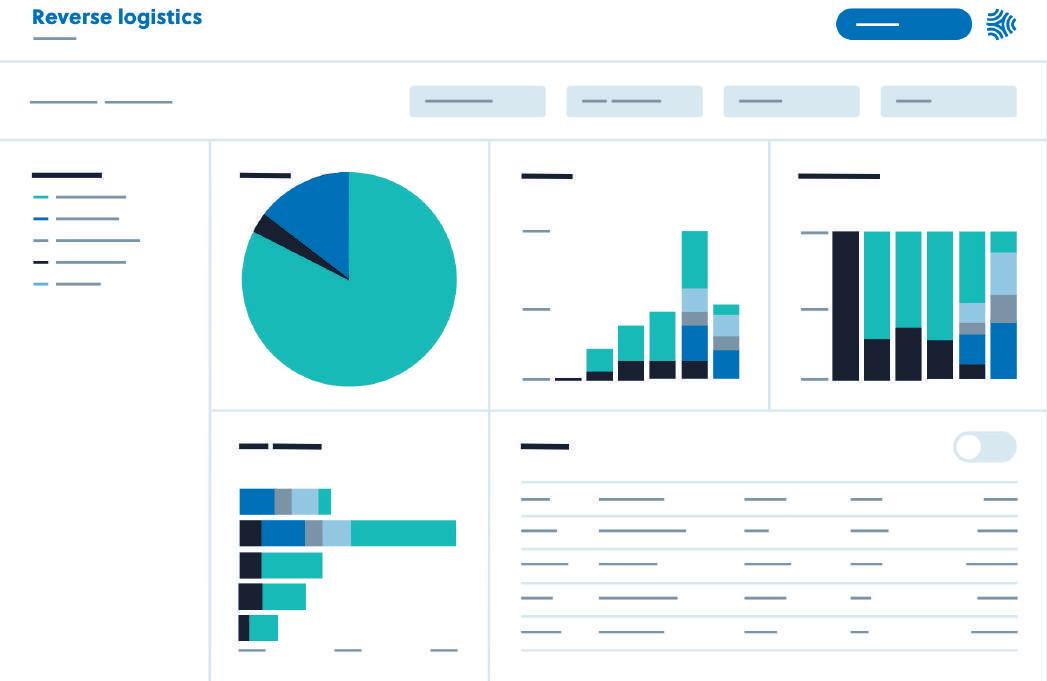
10 minute read
Lessons Learned from the COVID-19 Vaccine Cold Chain Control Tower
from IPI Summer 2021
by Senglobal
Lessons Learned from the COVID-19 Vaccine Cold Chain
Control Tower Supply chain visibility technology is proving its worth in the distribution of vaccines and has broader applications.
Now that COVID-19 vaccines have received regulatory approvals and vaccine manufacturers are producing a steady and increasing supply, the focus has shifted from manufacturing to distributing doses. Vaccine manufacturers have been working closely with cold chain distribution experts and technology providers to plan for monitoring and maintaining the cold chain to ensure the integrity of these crucial products. The vaccines that are currently in distribution must be transported and stored at temperatures ranging from refrigerated (2–8°C) to frozen (-20°C), or in a dry ice environment, with specific requirements, depending on the manufacturer and vaccine composition.
Pfizer and BioNTech's COVID-19 vaccine was authorised with stringent requirements of the currently authorised products, with storage between -80 °C and -60 °C. The vaccine is being shipped in thermal containers designed to hold dry ice for both shipping and temporary storage.
Many parties from all parts of the distribution chain — from developers of thermal packaging, IoT data loggers, and supply chain visibility data automation software systems, to dry ice and vial suppliers, airlines, and carriers — stepped up to prioritise vaccine distribution and solve one of the greatest logistical challenges we have seen.
Over the last several months, we have seen tremendous efforts across the COVID-19 vaccine distribution channel, with parties coming together to help solve a common goal for humanity. While we learned during the H1N1 outbreak more than one decade ago that digitally connecting and transforming the end-to-end would be paramount for future supply chains, this guiding principle has proven essential during the current pandemic.
With a significant global impact and human health at stake, manufacturers were tasked with rapid vaccine development, and distributing vaccines globally to regions with varying degrees of infrastructure and regulations. Gaining visibility from manufacture through last-mile delivery, and even onsite, has been critical to ensure vaccine integrity and help stakeholders make critical decisions as they are needed. Vaccine Cold Chain Challenges and Successes Aside from the rapid scientific development needed to develop an effective vaccine, manufacturers were tasked with gaining stakeholder engagement and buy-in on a level never previously seen. The urgency created by the pandemic and the rapid distribution required led to a change in the way systems and processes previously have worked. Ensuring regulatory compliance required team collaboration across large organisations, governments, and other external parties.
In a normal cold chain, pharmaceutical manufacturers must have rapid, accurate, and comprehensive capabilities in place to understand where products are and the condition they are in at all times. There are several risk factors in the cold and ultracold chain of COVID-19 vaccine distribution, and for most vaccines generally. First, vaccines must be stored at low and ultra-low temperatures, some of which must be kept at lower than the usual cold chain standard of 2–8°C. Any deviations in temperature during transport or storage can make the vaccine ineffective or even unsafe. Additionally, delays and losses of product in the supply chain can lead to critical vaccine shortages in areas that have been severely affected by the pandemic.
There are handoff points along the supply chain, and each one poses risks of temperature deviations, like pallets being split up or other incidents that can compromise the products' quality condition. Likewise, the receiving facility staff, including hospitals, clinics, and pharmacies, must review and understand all handling and storage instructions as well as the vaccine quality and safety conditions for each vaccine.
Some of the COVID-19 vaccines are shipping directly from the manufacturing site to receiving sites using a high-speed delivery model. This typically has involved air and road freight directly to receiving sites. To ensure the successful and rapid delivery of these sensitive products, shipping in high-volume, small parcel increments, realtime, actionable communication among stakeholders was needed. This requires connecting technology systems and activities to align people and processes and ensure vaccine integrity.
Many supply chains have traditionally used passive and limited use IoT data logger technologies that provide descriptive data, showing what happened after the fact. This delay in information is problematic because stakeholders cannot act on the data to prevent waste and loss. Vaccine integrity has never been more crucial as millions of COVID-19 treatments have already shipped, and potentially more than one billion will ship over the next 12–24 months.
Real-time, GSM-enabled IoT data logger technology and cloud-enabled analytics were designed to measure various scenarios that would require escalation in addition to temperature deviations and geolocation, which can detect if shipments are delayed, or products are split up or arrive at a wrong location. This technology is needed to support the rapid deployment of vaccine distribution on a global scale. Additionally, 24/7 monitoring and response services were required to respond to escalations and work with relevant parties to prevent vaccine product loss.
From a technology viewpoint, connecting people, processes, and stakeholders, both internally for manufacturers, and externally among its selected suppliers, carriers, and other stakeholders, has required a comprehensive mapping of new workflows and then building data and automation models to help streamline their efficiencies. For example, by integrating an enterprise resource planning (ERP) system with a real-time supply chain visibility software platform, carriers' own internal supply chain control tower system, and a quality management system, has connected and streamlined many value chain activities, spanning business, manufacturing, quality, and logistics.
The collaboration, alignment, processes, and data sharing across multiple internal and external stakeholders – such as carriers, manufacturers, governments, health systems, and others – integrating multiple control towers and implementing technology and service-enabled responsiveness has occurred over the last several months on a level never witnessed previously.
What the Cold Chain Control Tower Looks Like The cold chain control tower has evolved to support COVID-19 vaccine monitoring and broader cold chain applications. It provides real-time visibility for the end-to-end supply chain, analytics for decision support, responsiveness needed to prevent product waste, and efficiency to achieve economies of scale while supporting patient- and customer-centricity, cost reduction, and sustainability efforts.
Real-time Visibility The cold chain control tower is powered by real-time information enabled by GSMenabled IoT data loggers that continuously send shipment information to a cloud-based software platform, on product location, security, and quality. Notifications and alerts are automatically pushed to parties as they happen to improve transparency and enable proactive action to be taken to prevent product waste. Through integrations, data is pushed to internal and external parties, improving communication and alignment, in addition to patient- and customer-centricity.
Analytics Historically, supply chains have had only limited access to shipment data, knowing what has happened only at the end of a shipment, if at all. Many manufacturers do not have access to all shipment data, especially where manual upload from data loggers is needed. Real-time visibility and monitoring have made previous, retrospective processes and minimal data logging irrelevant. We can answer, 'What is happening right now?' so parties can act on critical information fast. Moving forward, supply chain stakeholders can leverage gathered business intelligence and data to predictively answer, 'What will happen?'
This data will enable businesses to execute planning in an entirely new way. For instance, if a product is shipped using a particular lane or packaging type during a specific time of year, prescriptive analytics can help people understand scenarios that are likely to occur. Information like this is crucial to prevent product waste and stock outages, as well as determine the best route or packaging material. These technologies include the integration of multiple systems and connect the physical and digital supply chains together.
Responsiveness The availability of real-time data poses a challenge in how to effectively respond to information as it happens. Today’s cold chain control tower solutions provide a greater level of responsiveness, working with manufacturers, logistics partners, and sites to proactively respond to escalations and alerts in real time in order to avert product loss. In addition to alerts that are triggered from the data delivered to the cloud software platform from the IoT devices to notify recipients of temperature deviations and other escalations that require review, solution providers are enhancing these notifications workflows with 24/7 monitoring and response services. These alerts notify carriers and sites directly if an escalation occurs and is not resolved so that product integrity isn't compromised. This level of responsiveness leads to product waste reduction throughout the supply chain.
Automation In addition to real-time visibility, a key benefit of an integrated cold chain control tower, is the data and workflow automation that becomes possible. This includes automatic shipment creation, where an enterprise resource planning system can automatically trigger a shipment

identification number and a customer email communication confirming their order and the order status. Automation also includes an exception-based quality release process, which can significantly reduce the number of hours manufacturers spend on retrieving and reviewing shipment data. By connecting IoT technology to cloud-enabled platforms in real-time, companies can define custom escalations and workflows in addition to communications that are triggered from the connected systems to deliver critical information to the right people promptly. Processes surrounding these new workflows will help companies save costs and conserve resources, while increasing their supply chain agility and responsiveness.
Measuring Success Companies leveraging the data provided by cold chain visibility technology can now quantify their improvements following their target goals and success metrics. For highvolume, small parcel shipments, some of these goals include avoiding temperature deviations as volume complexity increases and achieving end-to-end visibility of products, while achieving economies of scale and total cost reductions.
Beyond the vaccine supply chain, delivery performance metrics can include insights into deliveries such as countries and destination; product and packaging such as boxes and doses; deviations, such as alarms and alarm ratios, based on defined escalations; average time to delivery, per carrier; and product quality statuses such as average release time and successful delivery rate.
Many companies are shifting to reusable IoT data loggers and packaging to support their corporate sustainability objectives and are placing an added focus on measuring the quantities of boxes and loggers that are used and returned.
Together, these data and metrics, which can be shared with suppliers and carriers, are providing critical insights into supply chain performance and can be used to drive continuous improvements throughout.
Transformation Timeline COVID-19 vaccine distribution efforts have demonstrated the benefits of digital transformation throughout the cold chain. Global applications of control tower technology are becoming evident, including for direct-to-patient delivery models, clinical trials, and last-mile delivery.
The vaccine distribution efforts have also demonstrated the power of supply chain collaboration and pushing data to the right people, at the right time. This has enabled process optimisation that has impacted human health.
Pharmaceutical manufacturers and logistics providers can reap the benefits of digital transformation throughout their primary and secondary distribution models. While each rollout may vary, the initial phase generally includes achieving real-time visibility, intervention capabilities as they are needed, and fewer shipment rejections, while achieving a zero-touch release process, gaining trends analyses for decision support, and cost savings throughout.
The second phase may include achieving process streamlining and optimisation, predictive and prescriptive insights for whatif analyses and decision support, supplier analytics, data benchmarking, and reduced insurance premiums. The final phase may include process automation, network control, inventory reductions, and complete visibility, through the last mile.
Together, these transformations were previously not possible prior to the pandemic. Moving ahead, control tower technology is likely to fundamentally change the way the industry operates.
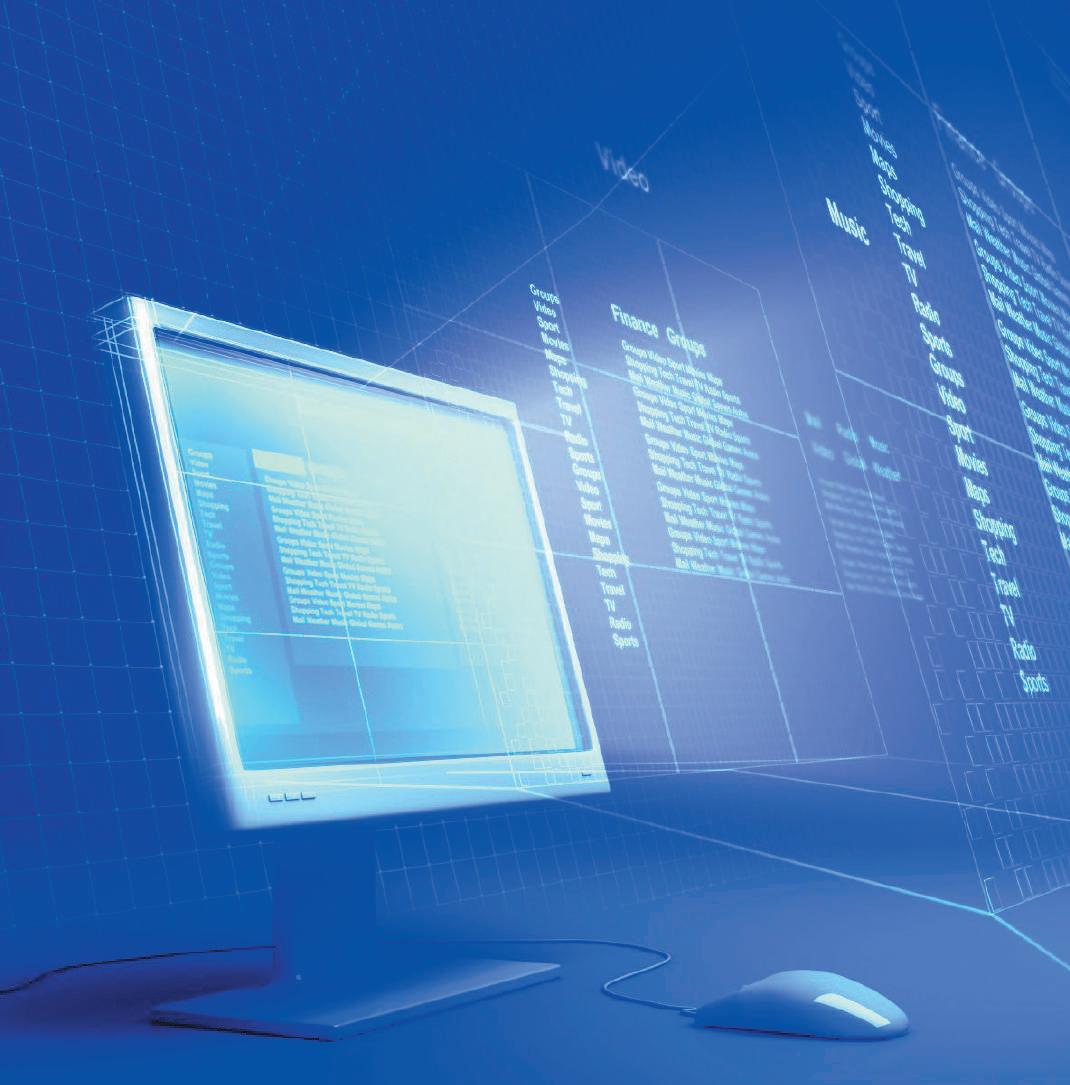
Conclusion The COVID-19 vaccine supply chain has demonstrated the value of data, automation, end-to-end visibility, and collaboration in ensuring quality and compliance, efficiency, waste reduction, and sustainability. Under normal circumstances, the new pharmaceutical distribution models currently in place would have taken years to accomplish, rather than only a few months. As companies consider their supply chains beyond the pandemic, they are increasingly focusing on achieving greater resiliency, agility, and responsiveness. Some companies have already begun making their supply chains more complex by recruiting additional suppliers. Others have started to integrate their supply chains more closely with their suppliers, logistics providers, and customers.
Resilience is required to meet trackand-trace, monitoring, regulatory, and licensing requirements. To achieve the level of sophistication needed, manufacturers are beginning to strategise and implement smarter solutions to deliver full digitisation to every part of their supply chain operations.
One thing we can likely agree on is that the pharmaceutical cold chain as we once knew it will likely never be the same again. Gisli Herjolfsson
Mr. Herjolfsson is Cofounder and CEO of Controlant, a technology company that is pioneering the development of next-generation supply chain visibility solutions for digitally connected pharmaceutical cold chains. He has driven the vision, culture, and growth of the company for the last 14 years.