
10 minute read
Serialisation: Headache or Opportunity?
from IPI Summer 2021
by Senglobal
The scourge of counterfeit drugs continues to threaten global health programmes. When it comes to dealing with the impact of counterfeit trade, there is an increasingly heavy burden placed upon healthcare systems, healthcare professionals, national medicine regulatory authorities, law enforcement agencies and criminal justice systems. To counter this growing threat, government bodies are enacting more robust and stricter regulations to control the genesis and proliferation of fake medicines.
Track-and-trace is an important aspect of serialisation and has long been recognised for its ability to protect against counterfeiters, as well as facilitating more effective recalls.
Despite the critical nature of governmentenforced initiatives to ensure the safety of consumers, as well as overall trust in the industry, many regulations are presenting real challenges to pharmaceutical manufacturers.
In this article we will examine three key questions: • Why is serialisation perceived as a headache by pharmaceutical companies? • How can we understand and address the challenges that arise from serialisation? • What are the opportunities for companies which effectively utilise this technology and what can be achieved by embracing serialisation?
What is Serialisation? Serialisation entails the encoding of each pharmaceutical product coming off a packaging line, with a unique identification code which can be traced and pinpointed at each stage in the supply chain. The unique identification code can be stored in an online database along with other valuable information about the product, such as manufacturer and batch details. This process enables complete monitoring and tracing of each product – from the packaging line right through to the patient.
Serialisation regulations vary between regions and countries, as well as being at different phases of implementation across the globe. To meet the demands of the country-specific deadlines, most global pharmaceutical companies should be trackand-trace and serialisation ready.
Why is Serialisation Needed? The main challenge we face in combatting counterfeit medicine is that counterfeiters are getting smarter. In today’s world, access to technology has become incredibly easy, so criminals and counterfeiters are able to keep up with ongoing changes and technological developments in the industry. Increasing numbers of internet pharmacies are also helping the fake medicines industry reach directly to the customer. Also, a lack of consumer awareness about counterfeit medicines is helping counterfeiters to expand their business.
Innovative and effective solutions have become essential to secure the supply chain and ensure safe products for consumers. Product authentication and implementing track-and-trace technology are two key aspects of ensuring supply chain integrity in the current climate.
A recent report by the UN Office on Drugs and Crime says “counterfeit goods and fraudulent medicines pose a serious risk to public health and safety”.1 We can also note the economic cost of counterfeit medicines for industry, government and society as a whole. Each year in the European Union alone it causes: • Loss of 4.4% of legitimate sales • Loss of €10.2 billion in revenue for the sector • Destruction of 90,900 direct and indirect jobs • Loss of €1.7 billion in government revenue (taxes and social contributions) 2
Establishing a robust, global system has far-reaching benefits for all stakeholders, from the pharmaceutical manufacturer to the end consumer. Track-and-trace will help overall control of the supply chain, coupled with providing brand protection for pharmaceutical companies. The technology improves trust in the product, due to supply chain visibility and data security between different stakeholders.
During the last 10 years, the track-andtrace industry has undergone vast change. Customers have moved from a reluctance to meet the regulation mandates, to utilising track-and-trace data for supply chain and production planning. Today, implementation is recognised as not just printing on cartons; businesses are now beginning to embrace the data management and security benefits from track-and-trace. The industry is moving from solely focusing on compliance, to creating real value for businesses and to consumer safety.
Why is Serialisation Considered to be a Headache? Although serialisation offers fair transparency and is a necessary requirement by regulatory bodies, it still presents a major challenge for the pharmaceutical industry.
Firstly, it is a long-term, substantial investment for individual companies. Secondly, it involves increased risk and complexity of current operations. Various bodies of evidence from early adopters of serialisation have demonstrated that productivity in terms of overall equipment effectiveness (OEE) has the potential to decrease. Serialisation demands tremendous changes to the entire IT structure, packaging and warehouse equipment and – most importantly – the data exchange system at each level of the value supply chain. For example, pharmaceutical companies in the EU have expressed concerns about the cost implications associated with the upgrading of pharmaceutical packaging lines to apply serialisation and tamper-verification features for the EUFMD.
Additionally, the changing regulatory frameworks, lack of uniform standards, and complex distribution networks make it difficult for pharmaceutical companies to cope with the overall implementation deadlines. Because of these challenges, pharmaceutical companies can be reluctant
to make changes to their processes or to invest in track-and-trace technology through their own initiative. Instead, they often only make changes to implement serialisation into their manufacturing, production and logistics as an obligation when governmental regulations are enforced.
Understanding and Addressing the Challenges As mentioned earlier, the implementation of serialisation will entail changing various business functions within the organisation, creating the need for collaboration among different departments. The production line, packaging, IT and engineering business units must work together to complete the line remodelling. It is also important to align the upstream and downstream trading partners to enable traceability of the products in the supply chain.
The addition of specific software and application components to the existing IT architecture of an organisation is one of the most critical aspects of implementing a serialisation and traceability system. Serialisation data is required to be fully integrated with centralised systems (at a corporate level), to allocate and manage serial numbers within the packaging processes. These systems also allow seamless data communication and storage to avoid any data duplication.
For ERP architecture level, organisations will require specialised software to retrieve and store all the necessary data in set databases. A dedicated on-site serialisation server will assess the complete production line from a track and trace perspective. The objective is to achieve accurate serial number commissioning on the production line, which does involve a significant investment of time and money.
Ensuring that serialisation and traceability are built into the supply chain is of the utmost importance. Once the products are serialised, the next step is to prepare and check diverse compliance data that can track the drug products as they are shipped, received, or analysed by operating facilities.
It is recommended that organisations seek enterprise-wide solutions that will eventually support serialisation datasharing throughout the internal supply chain, including trading partners. This involves integrating serialisation data with the enterprise resource planning (ERP) system and adding context or business data. It is this integration that enables product visibility from the point of manufacturer, to the patient.
There is no escaping the cost implications of serialisation for the pharmaceutical industry. Although there are low-cost serialisation solutions in the marketplace, these are not going to provide the required capability and benefits in the long-term. This would therefore represent a shortsighted investment. The critical parameter to evaluate serialisation is not cost, but value. Value, in turn, is defined as the combination of cost and benefit. It is the latter parameter that sometimes gets neglected. Ultimately, it is the value-proposition that should be the driver of the complete implementation strategy for any organisation.
What can be Achieved using Serialisation? Often, we are too caught up in the challenges of implementing change, instead of reviewing the value proposition(s). Innovation is essential for any industry, and in the case of serialisation within our sector, we cannot now go backwards, so it is critical we accept it and move forwards.
It is important to recognise and prepare for the challenges that come as a part of change. However, rather than viewing serialisation as a headache, it may be more beneficial to focus on the opportunities that will arise through integrating and investing in the various technologies that support serialisation. These include the following:
• Efficiency gains – Substantial efficiency gains can be expected in reducing manual processes for cross-party data validation and reconciliation and reducing repetition. • Brand enhancement – Improved trust in product provenance, and secure consumer confidence for quality, societal, and environmental impacts. • Revenue growth – Market penetration and new product/markets development. • Risk reduction – Reduced risk of counterfeit products and mitigated risk from lower-quality components. • Cost savings – Improved financing and credit rates due to greater transparency and certainty of movements of products and savings through streamlined operations. • Innovation drive – Leveraging innovation can increase efficiency and change outdated ways of working. • Product recall – Track-and-trace supports easy product recall with supply chain control.
What are the Future and Associated Opportunities? Businesses are under more pressure than ever to protect their products from counterfeiting. If a customer purchases a fake version of an authentic brand, or hears through the media that a particular product has been victim to counterfeiting, they can quickly become disillusioned with that brand. For any business trying to build a reputation in this era of online marketplaces, trust is arguably the single most important asset they can have. Without it, businesses could be leaving themselves exposed to unnecessary losses.
The track-and-trace industry is going through changes as a result of the Fourth Industrial Revolution. We foresee technologies like blockchain, IoT and machine learning playing key roles in securing the pharmaceutical supply chain from counterfeited goods.
In 10 years from now, track-and-trace will have become an integrated and essential part of any pharmaceutical business. It will soon be a must-have technology in complete production. Manufacturers will be interested in, and able to, monitor and track products at each point in the supply chain, 24/7. We can foresee track-andtrace expanding its reach downstream and upstream, accommodating tracking of the complete pharmaceutical process, from API/ molecular level, to actual consumption of product and consumer feedback.
In the future, our industry will not consider track-and-trace implementation as an obligation, but it will be appreciated as a key tool for the business to improve processes and quality guarantees for the consumer. The data captured throughout the pharmaceutical manufacturing process and the supply chain will be used for predictive quality improvement using traceability.
Improving Efficiencies and Creating Competitive Edge Serialisation presents many challenges for pharmaceutical businesses. Whilst reluctance to embrace serialisation is perhaps understandable, in the end it is neither productive nor beneficial. Given the inevitable acceleration of global regulatory requirements, as well as the myriad benefits serialisation can bring for
businesses, embracing change now will help organisations stay ahead.
Track-and-trace has long been recognised for its ability to protect against counterfeiters and facilitate more effective recalls. Today’s manufacturers are using it as a strategy to better observe and manage the entire ecosystem of their production facilities, and make smarter manufacturing a reality.
Track-and-trace is not just about creating a defence against counterfeiters and improving recalls. It is also about taking the opportunity to improve operations, quality, efficiency and consumer trust. All of which creates true competitive advantage.
REFERENCES
1. https://www.unodc.org/documents/treaties/ publications/19-00741_Guide_Falsified_ Medical_Products_ebook.pdf 2. https://euipo.europa.eu/tunnel-web/ secure/webdav/guest/document_library/ observatory/resources/research-and-studies/ ip_infringement/study9/pharmaceutical_ sector_en.pdf
OTHER SOURCES
• https://www.expresspharma.in/managementpharma/challenges-of-global-track-and-traceholistic-approach-common-solution/ • https://www.sciencedirect.com/science/ article/pii/S2405896319314314 • https://www.accenture.com/_acnmedia/ PDF-93/Accenture-Tracing-Supply-ChainBlockchain-Study-PoV.pdf • https://blog.matthews.com.au/how-trackand-trace-can-help-you-become-amanufacturer-of-the-future/#:~:text= Track%2Dand%2Dtrace%20helps%20increase, efficient%20for%20each%20production%20 centre
Gaurav Mohite
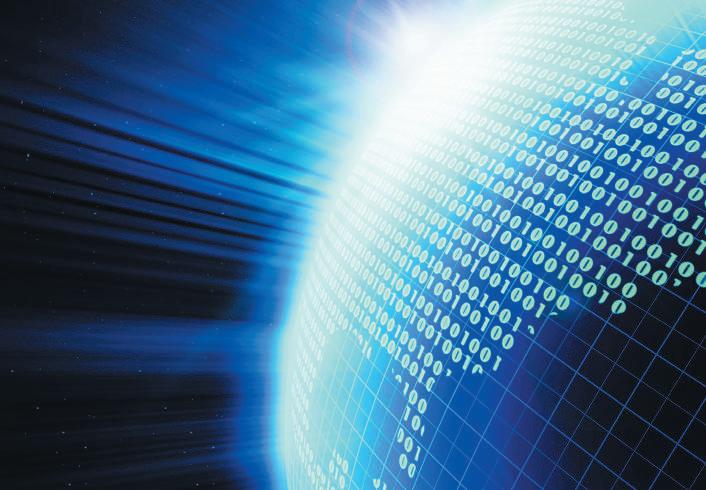
Mr. Gaurav Mohite, Product Manager at ACG Worldwide, has over 10 years of expertise in holistic Track and Trace solution for Pharmaceutical industry. He was part of complete Track & Trace implementation team across all the ACG implementation globally. He completed his master’s for Jamnalal Bajaj Institute of Management Studies (JBIMS) in marketing and bachelorette degree in Engineering. At the early stage of his professional career, he worked on vision inspection systems and Track & Trace applications as a developer and business analyst throughout the pharmaceutical industry. He is currently working as product manager and working for product marketing, strategy planning and technologic innovations.