
10 minute read
Moldando Inovações Futuras com Forjamento Radial
B k G
C E
Advertisement
I
A K
F D
Fig. 1. O mecanismo biela-manivela pode ser descrito como uma “haste deslizante com manivela e ranhura”. De W. J. M. Rankine, A Manual of Machinery and Millwork (um manual de máquinas e trituradores) (ed. 6, Londres, 1887, p. 169)
pelas matrizes. Isso difere substancialmente do forjamento radial, durante o qual altas forças são transferidas via superfície de contato peça/ matriz e o movimento senoidal radial atua na peça. Nas máquinas de forjamento radial, a rotação da peça é realizada de maneira controlada e otimizada de forma direta por um acionamento rotativo oscilante do manipulador, o que leva a um processo mais confiável e robusto.
Mais Sobre Forjamento Radial
O engenheiro austríaco Bruno Kralowetz cunhou o termo "forjamento radial". A empresa que ele fundou foi a GFM, que é a abreviação alemã de “empresa para tecnologia de fabricação e construção de máquinas” (Gesellschaft für Fertigungstechnik und Maschinenbau).
As primeiras máquinas possuíam três martelos e o material passava verticalmente pela máquina. O princípio de operação (mostrado como fluxo horizontal de material) e uma imagem da segunda máquina de forjamento radial construída são mostrados nas Figs. 2a e b, respectivamente.
Quase um século após a invenção do forjamento radial, as mais avançadas máquinas de forjamento radial se apóiam nos seguintes princípios básicos: acionamento por eixo excêntrico, mecanismo biela-manivela para converter movimento rotativo em movimento linear e o arranjo radial de vários martelos. O método pertence ao grupo de processos conhecidos com “forjamento em matriz aberta”. Nesta perspectiva, é um processo de forjamento incremental com curso e energia limitados.
Em um acionamento normal de virabrequim, a força é fornecida até um determinado ângulo, mas esse não é o caso da máquina de forjamento radial GFM. Na máquina da GFM grandes volantes são usados para reduzir a potência necessária do acionamento e transformar uma máquina força limitada (relacionada com a restrição do ângulo),
Fig. 2. a) Princípio do forjamento radial; b) Primeiro tipo de máquina de forjamento radial (versão vertical, 1948)
em uma máquina de energia limitada.
Do processo incremental derivam diretamente benefícios tais como reduzida necessidade de potência, ferramentas versáteis e um processo controlado. Juntamente com esses benefícios, a utilização da tecnologia CNC para controle do processo permite alcançar as vantagens do processo de forjamento de precisão para vários tipos de formas de seção transversal, tais como redonda, quadrada, retangular, hexagonal ou octogonal.
Forjamento Radial de Última Geração
Os bem conhecidos tipos de máquinas SX ainda são amplamente utilizados em todo o mundo. Ao longo das décadas, no entanto, benefícios adicionais foram alcançados através de diferentes tipos de máquinas. A tecnologia evoluiu de simples modelamento superficial para forjamento massivo profundo. Essas características divergem e se tornam mais
Tópico
Baixa força de forjamento Pouca ou nenhuma formação de carepa Forjabilidade Baixo risco de defeitos
Baixo custo de usinagem Peças com massa até Tolerâncias internas e externas de acordo com DIN/ISSO 286 Rugosidade (Rz) interna e externa Tensão de escoamento (T, grade) Deformação logarítmica - (T, grade) alongamento (redução em área)
Forjamento a quente
+++
11000kg
IT9-11 IT11-12
20-50µm >50-150µm approx. 20-30%
φ ≤2,7 15:1 (93%)
Forjamento semiquente
++
50kg
IT9-10 IT10-11
5-15µm >10-30µm approx. 20-50%
φ ≤1,6 5:1 (80%)
Forjamento a frio
30kg
IT7-9 IT9-10
2-5µm >3-10µm
100%
φ ≤0,7 2:1 (50%)
a

a
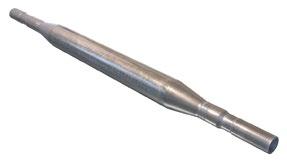
b Visão detalhada
Bloco deslizante
Eixo excêntrico
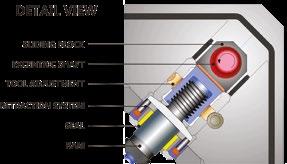
Ferramenta de ajuste
Sistema de retração Selo Ram
Fig. 3. a) Pequena forjadora radial automotiva SKK; b) Corte através de uma máquina de forjar do tipo SKK (projeto real)
específicas. O tipo de máquina mais vendido para forjamento a frio e semiquente é a máquina SKK com ajuste mecânico (Figs. 3a e 3b). Esse processo confiável e robusto atinge a mais alta precisão. Este tipo de máquina foi desenvolvido especificamente para as exigências da indústria automotiva. Com o uso de um mandril flutuante é economicamente viável a obtenção de eixos vazados com precisão interna incomparável. Eixos de acionamento (Fig. 4a) e eixos de transmissão automática (Fig. 4b) são aplicações típicas de sucesso.
As máquinas podem processar diferentes materiais em diferentes temperaturas de conformação e, assim, oferecer uma flexibilidade inigualável. As propriedades mais importantes das diferentes faixas de temperatura estão resumidas na Tabela 1.
Uma célula de produção típica para forjamento semiquente é mostrada na Figura 5.
O tipo RF (Radial Forging) é o estado da arte do forjamento radial há 20 anos. Neste sistema, o ajuste do ferramental no diâmetro é feito hidraulicamente por meio de um cilindro. Esse tipo de máquina fornece potência suficiente e a capacidade de deformar o material profundamente até a linha central da peça, permitindo um interior consolidado e minimizando a taxa geral de redução. Uma vantagem é o curto tempo de contato com as ferramentas. Isso é de importância crucial para peças de material altamente ligados ou superligas e é especialmente verdadeiro para seções transversais pequenas e peças mais longas.
b
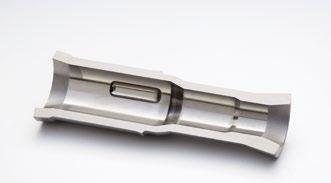
Fig. 4. a) Eixo tubular monobloco (eixo lateral); b) Eixo vazado em caixas de transmissão modernas
A expansão dos limites técnicos foi suportada pelo recurso de avanço por passes. Com este tipo de máquina, mais material pode ser deformado por passe, minimizando o tempo de contato com a ferramenta e, assim, o resfriamento da peça. A obtenção de um forjado com grão finos e fibramento compacto é possível pela combinação de recursos da máquina e tecnologia de processos e ferramentas.
As modernas ferramentas de simulação baseadas no FEA (Finite Element Analysis) permitem a otimização dos processos sem a realização de experimentos demorados e dispendiosos. A sofisticada, mas fácil de usar ferramenta de software FEA é integrada ao controle das modernas máquinas de RF. Rotinas inteligentes permitem a execução de simulações rápidas apesar da complexidade numérica e iteratividade dos cálculos. As ferramentas de simulação fornecem indicadores de porosidade, desenvolvimento da rede de carbonetos e bandeamento.
Limites Tecnológicos
Para precisão ou acuidade geométrica, apenas pequenas melhorias adicionais são esperadas. Os limites que serão e precisam ser mais avançados são a deformabilidade de vários tipos de materiais. A deformabilidade intrínseca é uma propriedade do material em si. No entanto, novas máquinas de forjamento radial expandem os limites de deformabilidade pela utilização de estados vantajosos de tensão durante o forjamento. A conformação da peça por todos os lados, combinada com geometrias de ferramentas e sequência de passes otimizadas,
Fig. 5. Célula de produção moderna para forjamento radial semiquente de eixos
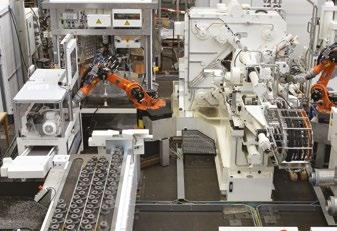
permite o forjamento, inclusive, de materiais suscetíveis a trincas. Essa é uma das vantagens mais importantes em relação a processos alternativos, como o forjamento convencional em matriz aberta e a laminação.
Baixos Custos Operacionais e Sustentabilidade
Comparado ao forjamento em matriz aberta, o processo requer significativamente menos potência e menos energia elétrica (até cerca de 50%). Isso se deve em parte a um acionamento elétrico direto, que evita a baixa eficiência energética de acionamentos hidráulicos e, em parte, ao efeito de balanceamento do volante. Essas vantagens mantêm as despesas operacionais baixas e, portanto, representam uma tecnologia ambientalmente amigável e sustentável.
Futuro do Forjamento Radial
As tendências do forjamento radial estão claramente definidas. Os eixos do rotor para motores elétricos estão agora aparecendo no mercado automotivo. Seu design típico parece se basear nas capacidades da tecnologia de forjamento radial. A melhor abordagem é um processo de forjamento semiquente. Imagens de eixos de rotores EV típicos são mostradas na Fig. 6. À medida que o número de veículos elétricos aumentar, o forjamento radial tornar-se-á o principal processo de fabricação para produção desse tipo de eixo.
Outro tópico são os novos e emergentes tipos de aço e superligas. O potencial do aço e das superligas ainda não foi totalmente explorado. Centenas de engenheiros de materiais estão projetando novas classes de materiais metálicos que sejam competitivas contra o avanço de materiais compósitos. O design de peças com o menor peso possível exige maior capacidade de carga mecânica e às vezes térmica. A deformabilidade limitada, característica das novas classes de materiais (aços altamente ligados e superligas), está direcionando as melhores práticas para o forjamento radial.
Juntamente com a máquina, tecnologias modernas como servo controles, motores de torque e sistemas sofisticados de acionamento dominam o desenvolvimento. Para aumentar a produtividade e a confiabilidade do processo, as limitações das ferramentas devem ser abordadas. Classes de materiais aprimoradas, revestimentos sofisticados, lubrificantes ecológicos e conceitos de resfriamento interno bem projetados são o verdadeiro foco para o desenvolvimento do processo.
Conclusão
O forjamento radial encontrou seu nicho em várias peças ocas de forma complexa e sua capacidade de forjar aços altamente ligados e superligas. O processo oferece alguns benefícios interessantes que se tornarão ainda mais importantes e difundidos devido a exigências emergentes de material, rendimento, confiabilidade e propriedades do material.
Este artigo foi gentilemente traduzido pelo Dr. Eng. Alberto Brito e Prof. Lírio Shaefer da Universidade Federal do Rio Grande do Sul.
O co-author Brad Fair é vice presidente da American GFM Corporation, Chesapeake, Va. Ele pode ser contatado em @agfm.com or 757-487-2442. O co-author Robert Koppensteiner é diretor geral da GFM GmbH, Austria. Ele pode ser contadado em koppensteiner@gfm.at. O co-author Martin Auer é diretor da Forging Technologies at GFM GmbH, Austria. Ele pode ser contatado em auer@gfm.at.
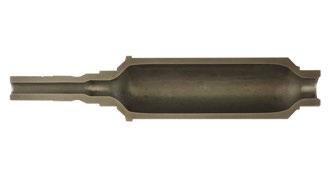
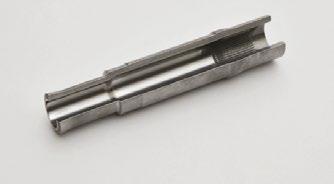
>>> Lubrificantes Influência de um Lubrificante Utilizado em Processos de Conformação Mecânica na Taxa de Desgaste de um Aço em Diferentes Patamares de Rugosidade

Luana De Lucca de Costa, André Rosiak, Lirio Schaeffer, Laboratório de Transformação Mecânica - LdTM , UFRS - Porto Alegre, RS - Brasil
Os lubrificantes são elementos muitas vezes indispensáveis nos processos de conformação mecânica e seu custo é relativamente baixo quando comparado ao valor final do componente produzido pelo processo. Além disso, os lubrificantes possuem uma importante função no processo, evitando o contato metal-metal entre o billet e o ferramental e minimizando danos causados pelo desgaste. A rugosidade superficial é uma particularidade que exerce influência no contato entre as protuberâncias superficiais (billet x ferramental). Em interações superficiais, conhecer as características topográficas é necessário para compreender os fenômenos tribológicos que atuam durante o contato superficial. A análise das características da superfície também são informações fundamentais para o entendimento dos mecanismos de desgaste. Tendo esta informação como premissa, o presente trabalho visa avaliar a variação da taxa de desgaste de um par de material metal-metal (SAE 4140 e DIN100Cr6), avaliando o desempenho do lubrificante em diferentes níveis de rugosidade superficial entre as amostras, através da utilização de um dispositivo para ensaios tribológicos pino-sobre-disco, avaliando assim a perda de massa das amostras após o ensaio.
O
presente trabalho tem como objetivo avaliar a influência dos lubrificantes identificados como: “Lubrificante 1”, “Lubrificante 2” e “Lubrificante 3” (comumente utilizados nos processos de conformação mecânica a frio) no desgaste durante uma interação entre superfícies do tipo metal-metal de um par de material, constituído pelos aços SAE4140 e DIN100Cr6, sob influência de diferentes patamares de rugosidade superficial (Nível C, Nível B e Nível A), através de um dispositivo para ensaios tribológicos do tipo pino-sobre-disco (Fig. 1). Esta prática visa elaborar uma avaliação tribológica preliminar oferecendo uma melhor compreensão

do comportamento do lubrificante perante o nível de rugosidade superficial dos corpos de prova ensaiados. Essa metodologia procura contribuir para a adequada seleção de lubrificante em casos que um determinado patamar de rugosidade é conhecido.
Determinação do Desgaste por Mudança de Massa
A mudança de massa é medida como a diferença entre a massa da amostra registada antes e depois do ensaio tribológico. Da mesma forma como todos os detritos provenientes do ensaio devem ser coletados e reservados para análises posteriores [2] .
Resultados confiáveis através da técnica