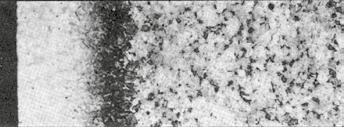
73 minute read
Doutor em Tratamento Térmico
Carbonitretação de Parafusos
DANIEL H. HERRING
Advertisement
+1 630-834-3017 dherring@heat-treat-doctor.com A carbonitretação de parafusos é de importância crítica para sua funcionalidade e um dos tratamentos térmicos de endurecimento mais comuns. Estudar como o processo funciona nesta aplicação ajudará a esclarecer todos os processos de carbonitretação. Vamos aprender mais.
A carbonitretação a gás é uma forma modificada do processo de cementação e não uma forma de nitretação. Neste processo, tanto o carbono (C) quanto o nitrogênio (N) são introduzidos na superfície do aço pela introdução de amônia (NH 3 ) e um gás enriquecedor de hidrocarbonetos na atmosfera do forno, a fim de adicionar nitrogênio à camada cementada à medida que está sendo produzida (Fig. 1).
0.8 O Processo de Carbonitretação
Normalmente, a carbonitretação é feita em uma temperatura mais baixa do que a cementação - 700-900°C - e por um tempo mais curto. Combine isso com o fato de que o nitrogênio inibe a difusão de carbono e o que geralmente resulta é um caso mais raso do que
Caso martensítico Núcleo
0.6
o típico para peças cementadas. Uma camada carbonitretada geralmente tem 0,075-0,75 mm de profundidade.
É importante notar que um contribuidor comum para profundidades não uniformes de revestimento é começar a adição de amônia antes que a carga seja estabilizada na temperatura. Esse erro geralmente ocorre em fornos descontínuos que iniciam as adições de gás assim que o setpoint se recupera ou em fornos contínuos onde as peças não estão em temperatura. É melhor introduzir um atraso de tempo para que toda a carga atinja a temperatura. Lembre-se também de que, quando termina a adição de amônia, começa a dessorção de nitrogênio.
A faixa de temperatura para carbonitretação não é arbitrária. A decomposição térmica da amônia é muito rápida em temperaturas de austenitização mais altas, o que limita a disponibilidade de nitrogênio. Uma estrutura quebradiça é formada em temperaturas mais baixas. Fornos operacionais abaixo de 760°C também podem representar uma preocupação de segurança.
A carbonitretação é conhecida por muitos nomes ao longo dos anos, incluindo “cianeto seco”, “cianeto a gás”, “nicarbonato” e “nitrocarbonetação” (Hoje, a nitrocarbonetação é usada para descrever outro tipo de processo de endurecimento.)
0.4
0.2
Nitrogênio Carbonitretação a 850˚C
Carbono
0 0 50 100 150 200
Distância da superfície, µm 250 Conteúdo de Nitrogênio da Camada
O nitrogênio no aço carbonitretado aumenta a temperabilidade e possibilita a formação de martensita em aços carbono simples e de baixa liga que inicialmente têm baixa temperabilidade. Os exemplos incluem SAE 1018, 12L14 e 1117 que podem ser transformados no caso em martensita devido à redução da taxa de resfriamento crítico necessária para transformar o aço. Os nitretos formados contribuem para
DOUTOR EM TRATAMENTO TÉRMICO
uma elevada dureza superficial.
Aços carbonitretados cobrem uma ampla seção transversal, incluindo aqueles nas séries SAE 10xx, 11xx, 12xx, 13xx, 15xx, 40xx, 41xx, 46xx, 51xx, 61xx, 86xx e 87xx. Teores de carbono de até cerca de 0,25% são típicos. Entretanto, teores de carbono tão altos quanto 0,50% nessas mesmas séries são carbonitretados para profundidades de camada de até cerca de 0,3 mm.
O nitrogênio - como o carbono, o manganês e o níquel - é um estabilizador da austenita. Portanto, a austenita retida é uma preocupação após a têmpera. A redução da porcentagem de amônia reduzirá a quantidade de austenita retida e deve ser feita se as reduções na dureza ou na resistência ao desgaste não puderem ser toleradas. Outra consequência do nitrogênio muito alto é a formação de vazios ou porosidade. Em geral, o teor de nitrogênio na superfície não deve ser superior a 0,40%.
Uma variação comum da carbonitretação é introduzir amônia próximo ao final do ciclo de cementação, normalmente 15-30 minutos antes de a carga ser temperada. Qualquer perda de temperabilidade que possa ocorrer devido à oxidação interna (ou intergranular) é parcialmente compensada pela absorção de nitrogênio.
Resistência ao Revenimento
Vários outros pontos devem ser mencionados. O nitrogênio na camada carbonitretada aumenta a resistência do aço ao amolecimento no revenimento, assim como alguns elementos de liga fazem. Além disso, quanto maior for o teor de nitrogênio, maior será a resistência ao amolecimento. É por isso que temperaturas de revenido mais altas de até 225°C são freqüentemente usadas em peças carbonitretadas.
A resistência ao revenido se manifesta em melhor resistência ao desgaste. As engrenagens carbonitretadas, por exemplo, freqüentemente exibem melhores propriedades de desgaste do que as engrenagens cementadas. Além disso, muitas peças de camada rasa e seção fina feitas de aço sem liga, como punções de corte e vinco, podem ser usadas sem revenimento.
A profundidade da camada é uma função do tempo na temperatura (Fig. 2). Os dados coletados na Fig. 2 mostram uma distribuição considerável e são representados como uma largura de banda, o que é explicado pelos autores originais [1] como “nada surpreendente devido às diferenças nas definições de profundidade de camada e métodos de medi-la, falta de conhecimento preciso do período de tempo durante o qual uma determinada parte está realmente na temperatura do
Profundidades da caixa, polegadas 0.036
0.032
0.028
0.024
0.060
0.016
0.012
0.008
0.004 1600-1625˚F
1550-1575˚F
1475-1525˚F
1425-1450˚F
0 0 1 2 3 Tempo, horas 4 5 6 7
Fig. 2. Profundidade do caso plotada contra o tempo para vários temperaturas (dados baseados em informações de cerca de 30 plantas) [2]
forno e o efeito da variação do tempo de aquecimento.”
Nitrogênio, % Carbono, % 1.1 1.0 0.9 0.8 0.7 0.6 0.5 0.4 0.3 0.2 0.1 0
0 Carbono Dureza
Nitrogênio
0.005 0.010 0.015 900
800
700
600
500
400 Dureza, V.P.M.
300
200 0.020
Tempo, horas
Fig. 5. Perfis de dureza, carbono e nitrogênio de um caso típico [3]
Durante a carbonitretação, o nitrogênio é adicionado na forma de amônia, uma vez que a dissociação, ou quebra, da amônia produzirá nitrogênio atômico (ou nascente) em oposição ao nitrogênio molecular. O nitrogênio atômico se combinará para formar o nitrogênio molecular, mas se a dissociação ocorrer na superfície do aço, o nitrogênio nascente pode se difundir no aço simultaneamente com o carbono (Fig. 3 online).
A carbonitretação é normalmente realizada na faixa de temperatura de 800-900˚C, mas temperaturas tão baixas
DOUTOR EM TRATAMENTO TÉRMICO
1.2 1.1 1.0 0.9 0.8 Composição, % 0.7 0.6 0.5 0.4 0.3 0.2 Carbono
7 NH 3
5 NH 3 15 NH 3 7 NH 3 4 NH 3 15 NH 3
Nitrogênio
0.1 0 0 0.005 0.010 0.015 0.020
Profundidade abaixo da superfície, polegadas Fig. 3. Efeito da concentração de amônia na caixa composição [3]
1.2 1.1 850˚ 1.0 0.9 Composição, % 0.8 0.7 0.6 0.5 0.4 800˚ 800˚ 900˚ Carbono 0.3 850˚ Nitrogênio 0.2 900˚ 0.1 0 0 0.005 0.010 0.015 0.020
Profundidade abaixo da superfície, polegadas Fig. 4. Efeito da temperatura na composição do case [3]
a)

b)
Fig. 6. Perfil de caixa de parafuso típico após carbonitretação de caixa rasa
quanto 700˚C são algumas vezes usadas de camada e microestrutura. (Fig. 4 online). A faixa ideal parece As razões para profundidades estar entre 845-870˚C. As taxas de de camada mais rasas em peças penetração são até 50% mais rápidas carbonitretadas incluem: do que a cementação. Por exemplo, a • A carbonitretação geralmente carbonitretação a 850˚C e a cementação é feita em temperaturas mais baixas a 900˚C produzem aproximadamente e por tempos mais curtos do que a a mesma profundidade de camada na cementação gasosa. mesma quantidade de tempo. • A adição de nitrogênio é menos
Uma vez que a carbonitretação é controlada do que a adição de carbono. normalmente feita em temperaturas Isso leva a um excesso de nitrogênio mais baixas e por tempos mais curtos no aço e, conseqüentemente, a altos do que a cementação gasosa, ela produz níveis de austenita retida. O aumento profundidades de camadas mais rasas, da porosidade pode ocorrer quando os porém mais duras (Fig. 5); geralmente tempos de ciclo são muito longos. não maior que cerca de 0,030 A carbonitretação, assim como a polegada no máximo. Os fixadores cementação, é usada principalmente carbonitretados são normalmente para produzir uma camada dura e montados (Fig. 6a) e gravados (Fig. 6b) resistente ao desgaste. Esta camada para revelar seu padrão de profundidade tem maior temperabilidade do que uma camada cementada. Conseqüentemente, a carbonitretação cria uma camada mais dura em aços de baixo carbono ou baixa liga.
As vantagens específicas da carbonitretação para fixadores em comparação com a cementação incluem: • Uma camada carbonitretada tem melhor temperabilidade do que uma camada cementada. Isso se deve à adição de nitrogênio na camada superficial. • Enriquecimento mais rápido em carbono, o que resulta em um tempo de tratamento mais curto em temperatura mais baixa • Melhor resistência ao desgaste e ao amolecimento (em temperaturas de serviço elevadas). • Melhores propriedades de fadiga (ou seja, limites de fadiga mais elevados) do que peças cementadas • Menor custo de operação devido às temperaturas mais baixas e tempos de ciclo mais curtos envolvidos
Resumo
A carbonitretação é uma excelente escolha para fixadores de baixo teor de carbono e materiais semelhantes que requerem uma camada uniforme, mas rasa, com boas propriedades de desgaste. Em geral, os tratadores térmicos que executam esses processos têm uma grande experiência e o know-how prático para controlar o tempo, a temperatura e as atmosferas do forno para atingir as propriedades e profundidades de camada exigidas.
A revisão da tradução desta coluna foi gentilmente feita por Shun Yoshida da Combustol Tratamento Térmico.
Referências Disponíveis Online
Novidades Indústria Negócios &
NOTÍCIAS
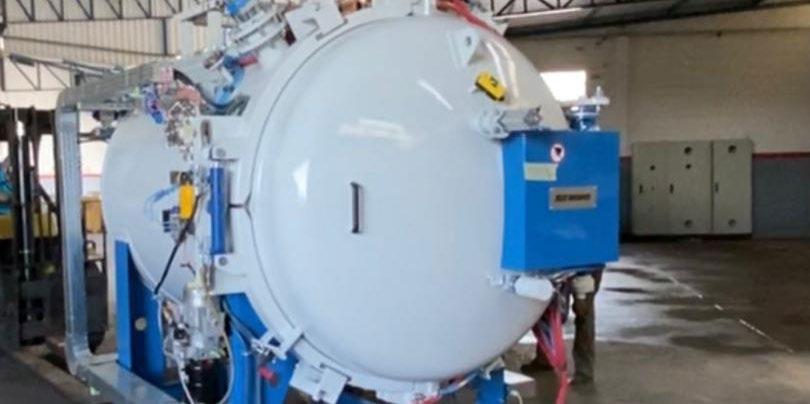
Combustol vende forno a vácuo da Seco Warwick para a Supertrat
A empresa Seco Warwick vendeu através da Combustol um forno a vácuo 600 x 600 x 900 mm de câmara, com 15 Bar de pressão de gás de resfriamento. Temperatura de 1300 ºC . O equipamento está em fase de instalação pela Combustol que dará todo o atendimento local ao cliente final, a empresa Supertrat de Santa Bárbara d’Oeste, interior do estado de São Paulo. O forno deverá estar em operação no primeiro trimestre de 2021.

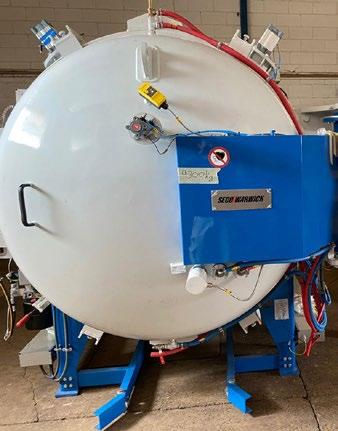
Novidades Indústria Negócios &
Forno a Vácuo para cerâmicas avançadas e metálicas
A TAV Vacuum Furnaces, representada pela LMTerm – Tecnologia em Processamento Térmico, conta com soluções inovadoras para o tratamento de cerâmicas avançadas e peças metálicas. Os projetos de fornos a vácuo são desenhados de acordo com a necessidade do cliente. Além disso, são sustentáveis: consomem energia quando há necessidade, não poluem o ar e nem a água.
O equipamento da imagem, por exemplo, chega a 2.200ºC, tem ø150x300mm, e foi o primeiro forno vertical instalado pela LMTerm, no início de 2017. O forno tem câmara de tungstênio, com pressão positiva de H2 e umidificação dos gases de processo. É aplicado para sinterização de cerâmicas translucidas e safira.
MAIS – Os projetos são sempre sob medida. Fornos desse tipo podem contar com sistema com bombeamento de grande dimensão que permite altos níveis de trabalho a vácuo; inovador sistema de refrigeração compacto que garante altos desempenhos de refrigeração; taxa de resfriamento rápido em todas as temperaturas, ciclos curtos.
Depois da entrega do equipamento, o alto know-how em aplicação que a equipe LMTerm tem permite que a empresa forneça treinamentos e pronta assistência tanto para manutenção de maquinário
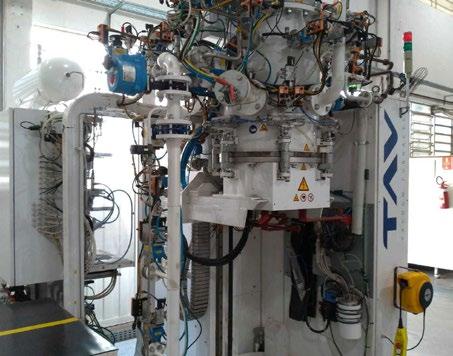
quanto para cada aspecto relacionado à tecnologia de processo.
A LMTerm é referência no segmento e se destaca no mercado nacional e também na América do Latina pela excelência no trabalho desenvolvido. www.tav-vacuumfurnaces.com www.lmterm.com.br
Combustol Fornos em parceria com a Seco Warick oferece forno VORTEX
A Combustol Fornos em contínua parceria com a empresa Seco Warwick acaba de fornecer um forno de recozimento de bobinas de alumínio com tecnologia VORTEX , de alta convecção. O processo consiste em promover o carregamento em baixa temperatura, cerca de 100°C , efetuar purga com Nitrogênio, para reduzir teor de oxigênio da câmara, para baixos valores e da ordem de apenas 0,4%, iniciando o aquecimento programado para homogeneidade da temperatura do metal. O equipamento é provido de recursos de adequação ambiental, com a operação de after burner para incineração dos voláteis desprendidos no processo de aquecimento, uma vez que a carga possui leves resíduos de óleo ao serem laminadas e evaporados no processo de tratamento térmico.
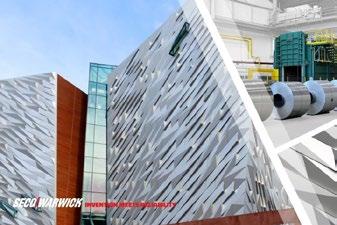
Novidades Indústria Negócios &
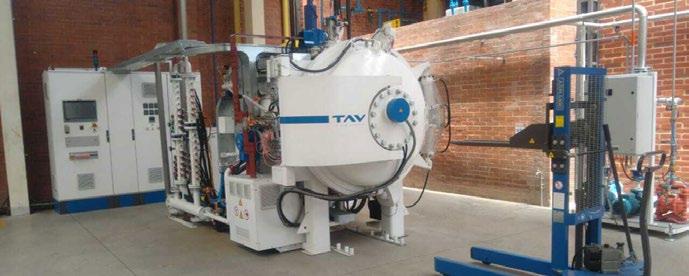
LMTerm inova e realiza montagem de forno de maneira inédita
Pandemia e fronteiras fechadas. Esse cenário fez empresa a LMTerm, especialista em tecnologia para tratamento térmico de São José dos Campos, sair do óbvio e se reinventar na montagem de um forno a vácuo na Colômbia. O equipamento chegou em fevereiro da Itália para Bogotá e aguardava a visita dos técnicos da empresa joseense para entrar em operação. O trabalho rendeu à empresa um
“Achamos que o fechamento das novo olhar sobre a instalação remota fronteiras seria passageiro, porém, de equipamentos. “Antes da pandemia, não foi o que aconteceu. Tivemos que era fora de cogitação fazer a instalação traçar uma estratégia para que o cliente dessa forma. Assim como todo o setor pudesse ser atendido”, disse o diretor da indústria, éramos extremamente da empresa, Luciano Micheletto, que protecionistas quanto a técnicas e destaca jamais ter cogitado realizar o algumas informações da instalação. A trabalho, repleto de detalhes e altamente crise nos fez ter um novo olhar. Além técnico, a quilômetros de distância. disso, já estamos estudando novas
Com a necessidade do cliente, tecnologias para ampliar o atendimento o administrador reuniu a equipe e remoto.” traçou uma estratégia para prestar o Segundo Luciano, a empresa já serviço de montagem do forno a vácuo. estuda o uso de ferramentas de realidade “Calculamos os riscos e dificuldades. O aumentada para que clientes no Chile, cliente contratou uma equipe que foi Argentina, México e em municípios capacitada pela LMTerm e, em 30 dias, brasileiros fora do Estado de São executamos todo o trabalho, sem falhas”, Paulo. “Dessa forma, conseguimos celebrou, destacando que tudo foi reduzir inclusive o custo das visitas concluído nesta segunda-feira (28). para atendimentos de Service Care e montagem de equipamentos.”
Para o cliente, a experiência foi positiva. “Estamos muito satisfeitos com o suporte de alta qualidade dado pela LMTerm para a montagem. A empresa nos deu informações técnicas claras e confiáveis. Tivemos uma comunicação ativa e direta que facilitou o entendimento da nossa equipe no local”, destacou o gerente de qualidade Fabian Gomez.
Segundo Fabian, o investimento no forno foi realizado para substituir os atuais processos de tratamento térmico. “Buscamos mais produtividade, elevados padrões de qualidade e tecnologia ecologicamente correta.”
Mais informações: www.LMTerm. com.br
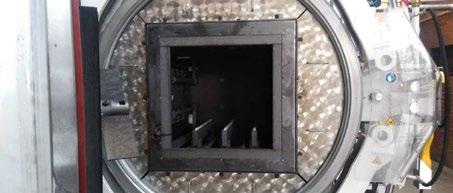
A Influência de Parâmetros de Revenimento na Microestrutura e Propriedades Mecânicas de Aços PM de Baixa Liga Tratados Termicamente (Parte 2)
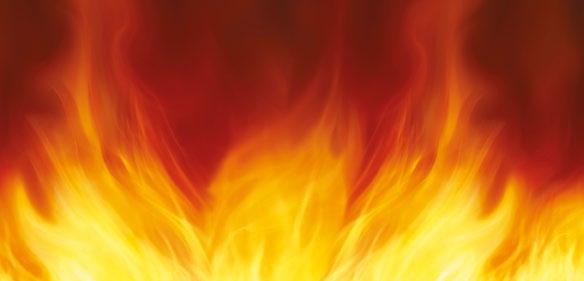
Amber Tims, Roland Warzel III and Bo Hu – North American Höganäs; Hollsopple, Pa. Bob Aleksivich – Vision Quality Components, Inc.; Clearfield, Pa., EUA
Revenimento é uma técnica de tratamento térmico usada para melhorar a resistência, ductilidade e resistência dos aços carbono temperados.
Para recapitular um pouco do que vimos na edição passada, estabelecemos os conceitos básicos e começamos a revisar o procedimento experimental e os resultados. Esses resultados são discutidos e resumidos aqui.
Discussão
A avaliação das propriedades mecânicas mostra que o sistema de material pré-ligado tem maior resistência à tração (~ 3%), limite de elasticidade (~ 5%) e dureza aparente (~ 6%) em todas as temperaturas de revenimento em comparação com o material ligado por sistema de difusão. O material ligado por difusão tem energia de impacto ligeiramente maior em comparação com o material pré-ligado. Esses resultados estão de acordo com os dados publicados do padrão MPIF 35 [1] . A resistência à tração de ambos os materiais permanece relativamente constante em temperaturas de revenido de 160-220°C. Um declínio acentuado na resistência à tração ocorre quando as temperaturas de revenido atingem além de 220°C, de
Tabela 4. Resumo das propriedades mecânicas
Procedimento de bombagem Propriedade
FLN2-4405 FD-0205
Resistência à tração
Resistência ao escoamento
Energia de impacto
160°C → 200°C 220°C → 275°C
160°C → 200°C 200°C → 250°C 250°C → 275°C
160°C → 200°C 200°C → 275°C
1% diminui 7% diminui
1% aumenta 8% aumenta 6% diminui
Constante 24% diminui 1% diminui 7% diminui
4% aumenta 5% aumenta 1% diminui
Constante 29% diminui
Dureza aparente
160°C → 275°C
18% diminui 21% diminui
Tensão da microdureza
160°C → 275°C
Tabela 5. Espécimes de efeito de massa
Amostra de tração
Área da seção transversal
Volume
160°C → 200°C 220°C → 275°C
160°C → 200°C 200°C → 250°C 250°C → 275°C
160°C → 200°C 200°C → 275°C
19% diminui 16% diminui
Disco de 40 mm de diâmetro
1,000 mm2
16,000 mm3 Disco de 100 mm de diâmetro
2,500 mm2
98,000 mm3
onde ambos os materiais mediram uma queda de 7% na resistência à tração de 220-275°C. Em contraste, a resistência ao escoamento aumenta constantemente à medida que as temperaturas de revenimento se aproximam de 230°C antes de cair novamente conforme as temperaturas vão além de 250°C.
A energia de impacto mostra uma diminuição constante em temperaturas de revenimento acima de 200°C para ambos os sistemas de materiais. Ambos os sistemas de materiais mostram uma diminuição linear na dureza aparente e microdureza ao longo de toda a faixa de temperatura de revenido. Com base neste estudo, as temperaturas de revenido ideais variam entre 220-250°C, onde ambos os materiais alcançam alta resistência
50 µm
à tração, mantendo boa resistência ao escoamento, energia de impacto, dureza aparente e microdureza. Um resumo das propriedades de cada sistema de material é mostrado na Tabela 4.
As microestruturas das amostras de tração revenidas a 200°C são mostradas na Figura 9. As microestruturas FLN2-4405 em cada temperatura de revenimento consistem em martensita com austenita rica em níquel onde o níquel estava presente. Os espécimes de tração FD-0205 também consistem em martensita com austenita rica em níquel, onde o níquel foi ligado por difusão.
Para entender como a massa de um componente afeta a microestrutura em cada temperatura de revenimento, um estudo foi conduzido usando
50 µm
dois corpos de prova de tamanho diferente fabricados com o material FLN2-4405. Para esta investigação, os discos foram tratados termicamente e revenidos usando os mesmos parâmetros dos corpos de prova submetidos a testes de propriedades mecânicas. A microestrutura da superfície e do núcleo foi avaliada nos discos e comparada com os corpos de prova de tração. As medições de cada amostra são mostradas na Tabela 5.
O processo de têmpera durante o tratamento térmico depende da transferência de calor para o meio de têmpera para resfriar rapidamente os componentes. O efeito de massa de um componente determinará a rapidez com que ele é resfriado, e várias taxas de resfriamento podem ser vistas nas diferentes seções do componente. Um componente com seções transversais
50 µm 50 µm
Sem revenido, superfície de disco de 40 mm
50 µm Sem revenido, superfície de disco de 100 mm
50 µm Sem revenimento, núcleo de disco de 40 mm
50 µm Sem revenimento, núcleo de disco de 100 mm
50 µm
220˚C, superfície de disco de 40 mm
50 µm 220˚C, superfície de disco de 100 mm
50 µm 220˚C, núcleo de disco de 40 mm
50 µm 220˚C, núcleo de disco de 100 mm
50 µm
275˚C, superfície de disco de 40 mm 275˚C, superfície de disco de 100 mm 275˚C, núcleo de disco de 40 mm 275˚C, núcleo de disco de 100 mm Fig. 10. Microestruturas em temperaturas de revenimento incremental dos discos FLN2-4405 de 40 mm de diâmetro e 100 mm de diâmetro retirados da superfície e do núcleo
105
100 Disco de 100 mm - revenido a 200˚C
95
Martensita % 90 85 80
75
70
0 1 2 3 4 5 6 7 8 9 10 11 12 13 14 Distância da superfície, mm Fig. 12. Análise de martensita por Microscópio Eletrônico de Varredura
pequenas resfriará mais rapidamente em comparação com seções transversais grandes. No mesmo aspecto, a camada de superfície externa de componentes maiores resfriará mais rápido do que o núcleo, resultando em variações na dureza e microestrutura quanto mais próximo do centro da peça.
As microestruturas do núcleo dos discos de 40 mm e 100 mm em diferentes temperaturas de revenimento após o tratamento térmico são mostradas na Fig. 10. Este estudo mostra que os discos de 40 mm foram capazes de alcançar uma microestrutura totalmente martensítica sem bainita observada no núcleo. Os discos de 100 mm têm uma superfície martensítica, mas a bainita foi observada dentro do núcleo após o tratamento térmico (~ 20%). A têmpera não tem efeito nas microestruturas.
Comparativamente, as microestruturas dos corpos de prova de tração com a seção transversal menor também desenvolveram uma microestrutura totalmente martensítica para ambos os sistemas de materiais. Todos os espécimes mostraram uma queda semelhante na microdureza da superfície ao núcleo devido ao alívio de tensões como resultado do revenido. Este estudo mostra que não há efeito de massa em componentes com área de seção transversal menor que 1.000 mm2, mas um efeito de massa é observado em componentes com área de seção transversal de 2.500 mm2. O efeito de massa se deve principalmente ao tratamento térmico e não ao revenimento.
A Fig. 11 mostra a porcentagem de mapeamento de fase da martensita em distâncias incrementais da superfície da peça até o núcleo em uma amostra de disco de 100 mm temperada a 200°C. O componente é 100% martensita na superfície da peça e 1 mm abaixo da superfície sem bainita observada. Uma pequena quantidade de bainita é observada e a porcentagem de martensita diminui ligeiramente a 2 mm abaixo da superfície. Uma grande quantidade de bainita está presente e a porcentagem de martensita cai significativamente a 3 mm abaixo da superfície. O núcleo do componente mede aproximadamente 80% de martensita.
A Fig. 12 mostra imagens tiradas por um microscópio eletrônico de varredura (SEM - Scanning Eléctron Microscope) para comparar as diferenças entre a martensita não temperada e a martensita temperada. A martensita não temperada consiste em agulhas grossas em forma de placa em toda a sua estrutura. Esta estrutura é o resultado de carbonetos sendo aprisionados na estrutura do cristal durante o tratamento térmico (têmpera), resultando em altas tensões internas em toda a estrutura.
À medida que a temperatura de revenimento aumenta, ocorrem alterações na microestrutura à medida que o carbono é precipitado para fora da rede cristalina. Os átomos se reorganizam e formam carbonetos esféricos dispersos na martensita. Essa alteração forma uma nova estrutura chamada “martensita temperada” e tem tensões internas mais baixas em comparação com a martensita não temperada. [5] A estrutura de martensita revenida suporta as propriedades mecânicas obtidas de forma que à medida que as temperaturas de revenimento aumentam, as tensões internas diminuem e a resistência, dureza aparente, energia
Sem temperatura
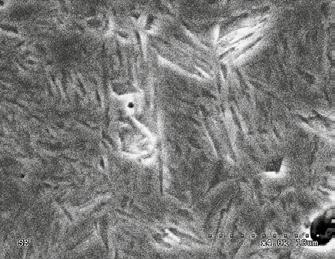

220˚C

275˚C
de impacto e microdureza também diminuem.
Inclinado para Trás
Rodas com pás inclinadas para trás (Fig. 3) estão entre os projetos mais eficientes para ventiladores que manuseiam correntes de ar mais sujas. Eles podem fornecer grandes volumes de gás com geração de pressão moderada e baixo ruído. Embora possam lidar com correntes de ar com partículas, não são adequados para partículas pegajosas. Seu design também não é adequado para temperaturas acima de 538°C. A aplicação mais comum para este projeto de roda (Fig. 4) no tratamento térmico é para resfriamento ou ventiladores de combustão.
Conclusões
Materiais
• O sistema de material pré-ligado tem maior resistência à tração final (~ 3%), resistência ao escoamento (~ 5%) e dureza aparente (~ 6%) em todas as temperaturas de revenimento em comparação com o sistema de material ligado por difusão. • O material ligado por difusão tem energia de impacto ligeiramente mais alta em comparação com o material pré-ligado.
Revenimento
• Um declínio acentuado na resistência à tração ocorre quando a temperatura de revenimento vai além de 220°C. Ambos os sistemas de materiais viram uma queda de 7% na resistência à tração acima desta temperatura. • A resistência ao escoamento aumenta conforme as temperaturas de revenimento se aproximam de 250°C, mas diminui acima dessa temperatura. • A energia de impacto de ambos os sistemas de materiais é semelhante na faixa de têmpera de 160-200°C. Conforme a temperatura de revenimento aumentou acima de 200°C, a energia de impacto de FLN2-4405 diminuiu 24%, enquanto a energia de impacto do material FD0205 diminuiu 29%. • Os níveis de dureza aparente diminuem linearmente com o aumento da temperatura de revenimento. O material FLN2-4405 exibiu níveis de dureza aparente mais elevados em todas as temperaturas de têmpera em comparação com o material FD-0205 ligado por difusão. • A microdureza das amostras de tração diminui linearmente com o aumento da temperatura de revenimento. Os níveis de microdureza de FLN2-4405 e FD0205 são semelhantes. • Com base neste estudo, as temperaturas de revenido ideais para obter a maior resistência à tração final, mantendo uma boa resistência ao escoamento, energia de impacto e níveis de dureza estão entre 220°C e 250°C.
Efeito de massa
• O estudo de efeito de massa das amostras FLN2-4405 mostra que a microdureza exibe uma diminuição linear conforme a temperatura de revenimento aumenta. A microdureza também diminui a cada incremento de 1 mm abaixo da superfície. • As amostras de disco de 40 mm foram capazes de atingir microestruturas totalmente martensíticas, enquanto as amostras de disco de 100 mm têm uma mistura de bainita e martensita dentro do núcleo. • Nenhum efeito de massa pode ser observado para o revenimento. Os efeitos de massa são vistos principalmente durante o tratamento térmico (têmpera). • A superfície das amostras de disco de 100 mm temperadas a 200°C é 100% martensita. Uma queda significativa no conteúdo de martensita é observada a 3 mm abaixo da superfície. O núcleo do componente é aproximadamente 80% de martensita. • A microestrutura das amostras de disco não revenidas consiste em agulhas de martensita em forma de placa. A martensita contém carbonetos esféricos dispersos típicos da martensita revenida na temperatura de revenido mais alta. • Os arranjos da microestrutura são consistentes com as propriedades mecânicas obtidas. À medida que a temperatura de revenimento aumenta, as tensões internas diminuem e a resistência, dureza aparente, energia de impacto e microdureza também diminuem.
Referências Online
PARA MAIS INFORMAÇÕES: Contate Amber
Tims, engenheira de serviço técnico, North American Höganäs Co. 111 Hoganas Way, Hollsopple, PA 15935, EUA; tel: +1 814- 479-3528; e-mail: amber.tims@hoganas. com; web: www.hoganas.com. Ambas as partes deste artigo vieram de Proceedings of the 2018 International Conference on Powder Metalurgy & Particulate Materials, June 17-20, 2018; Propriedades de material da categoria 10 - Página 755, Documento 122; Metal Powder Industries Federation Princeton, N.J., EUA.
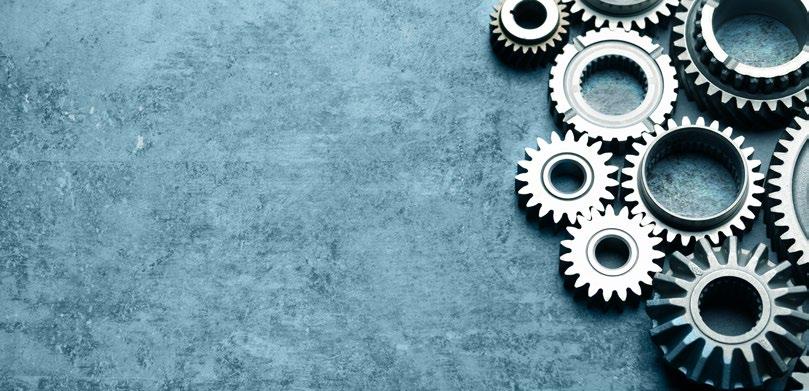
Como Maximizar a Confiabilidade e a Eficiência do Processo no Tratamento Térmico
Chris Ebeling – U.S. Bulk at Messer; Bridgewater, N.J., EUA A confiabilidade do processo é essencial para a produção de peças metálicas com tratamento térmico de alta qualidade. A confiabilidade pode ser melhorada por meio da vigilância e as respostas eficazes para a solução de problemas podem estender a vida útil para dar aos tratadores térmicos mais oportunidades de responder às demandas do mercado.
Alguns fornos podem se beneficiar de novas tecnologias de mistura de atmosfera que aumentam a transferência de temperatura e a reação da atmosfera com o material. Isso, por sua vez, encurta o ciclo de processamento para atingir maior rendimento do forno, ao mesmo tempo que melhora o processo e a qualidade das peças. Novas tecnologias de mistura também tornam possível eliminar os recirculadores do forno para melhorar ainda mais a confiabilidade do processo.
Uma Abordagem Geral
Embora o tratamento térmico seja um processo complexo, podemos simplificar a análise de confiabilidade examinando dois tipos gerais de alterações de superfície comumente encontradas quando os metais são aquecidos em fornos. Um é a oxidação / redução; a segunda é a cementação / descarbonetação, que se relaciona às reações dos gases com a superfície do metal que adicionam ou removem carbono do substrato.
A descarbonetação geralmente resulta em uma característica de material indesejável, enquanto as reações de oxidação / redução determinam a aparência da superfície do metal manufaturado. Quando os componentes de metal são endurecidos, a descarbonetação reduzirá a dureza da superfície do material e, portanto, diminuirá a vida operacional em condições de desgaste. A oxidação no forno, entretanto, é uma consequência indesejável quando os fornos e as atmosferas não são otimizados para controlar essas interações gasosas. Também existe uma correlação entre essas duas condições indesejáveis.
Essas questões podem ser resolvidas controlando as variáveis do forno de tratamento térmico, o processo e os equipamentos relacionados. Isso envolve um controle aprimorado das reações da atmosfera do forno e dos gases usados para criar as condições do forno. A otimização do forno usando certas tecnologias avançadas de controle de atmosfera leva a uma maior confiabilidade.
Confiabilidade
Com base no entendimento derivado da modelagem CFD, Existem mais de 100 parâmetros diferentes em um processo de tratamento térmico, mas talvez apenas 10 possam ser controlados ativamente pelos operadores. Parâmetros não controlados criam variações de processo que levam a resultados variáveis. Felizmente, a maioria das reações termoquímicas primárias pode ser analisada com os resultados previstos usando avançado controle de atmosfera para atingir a repetibilidade e melhorar a confiabilidade do processo.
A maioria das operações de tratamento térmico modernas usa ferramentas como modelos, analisadores e equipamentos de computador para manter o controle contínuo e fechado do processo. Isso permite que quaisquer problemas inesperados e esperados sejam detectados. Idealmente, os sistemas de controle podem responder a tempo para corrigir ou eliminar problemas ou, pelo menos, reduzir seu
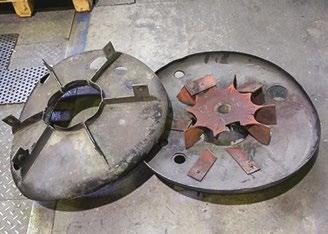
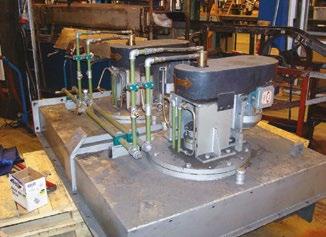
Fig. 1. A tecnologia de mistura de atmosfera HSGI pode substituir recirculadores, que são propensos à degradação térmica e sujeitos a reparos e substituições frequentes
impacto. No geral, esses sistemas de controle são projetados referência para detectar problemas, como quando um para fornecer confiabilidade. vazamento de ar aumenta o teor de oxigênio ou quando um
Atmosferas de fornos desempenham um papel imporvazamento de água aumenta a leitura do ponto de orvatante no processo de tratamento térmico em operações de lho. No entanto, a amostragem de gás limitada não pode fornos atmosféricos e de fornos a vácuo. Mesmo que esses ser usada para determinar a taxa de reações críticas, como processos de vácuo não empreguem gases atmosféricos, é redução, oxidação, cementação ou descarbonetação, etc. científica e praticamente impossível criar um verdadeiro vácuo onde não há espécies de gás. As moléculas de gás Circulação da Atmosfera estão sempre interagindo ou reagindo com a superfície do Na maioria dos fornos, a circulação tem três funções metal que está sendo tratado no gás pelas regras de difusão principais. Estes incluem: convecção para transferência efigás-sólido. Isso se deve ao equilíbrio de massa entre o ciente de calor; e aumentar os coeficientes de reação entre conteúdo da superfície metálica do gás e o gás livremente a atmosfera e a superfície, atualizando a composição do gás presente na atmosfera e suas reações entre si. próximo à superfície. A terceira é realizar as duas primeiras
A amostragem é principalmente o fator determinante funções de maneira uniforme. no controle do processo de uma atmosfera de forno. Na A maioria dos recirculadores de atmosfera não conprática, a amostra de gás é retirada do forno operando em segue realizar tudo isso ao mesmo tempo. Quando os condições atmosféricas. No entanto, isso representa apenas fornos equipados com ventiladores gigantes, como nos o espaço ao redor da sonda de gás, e não representa necesfornos vagoneta onde o alumínio é recozido, a circulação e, sariamente ou exatamente a condição completa da atmosportanto, a turbulência maciça não fornece uniformidade, fera do forno. Considere que a condição da atmosfera longe o que causa zonas de estagnação. Isso leva a problemas de da superfície metálica da peça é muito diferente da condiqualidade de superfície ao fornecer convecção de gás para ção da atmosfera nas proximidades da superfície devido ao permitir o aquecimento de grandes quantidades de material maior número de reações que ocorrem entre a atmosfera de alumínio. Na cementação gasosa, as operações do recire o metal. Também existem diferenças nos fluxos de gás culador atmosférico fornecem a mistura da atmosfera, mas e reações em outros espaços, como onde o gás reage com falham em fornecer uniformidade. Isso cria componentes os componentes do forno, bem como refratários ou mufla. não uniformes de falha de profundidade de camada para Portanto, para melhorar o controle e a confiabilidade da passar nas especificações de qualidade. atmosfera de um forno, a circulação da atmosfera deve ser Uniformidade é uma palavra-chave no tratamento empregada. térmico. Sem propriedades metalúrgicas uniformes, é quase
Nos casos em que não há mecanismo de circulação impossível produzir propriedades mecânicas uniformes, na atmosfera, as amostras de gás podem ser usadas como o que é uma falha em todo o propósito do tratamento
Fig. 2. Injetores de gás de alta velocidade podem ser instalados em fornos de tratamento térmico novos ou existentes e não requerem peças móveis dentro do forno
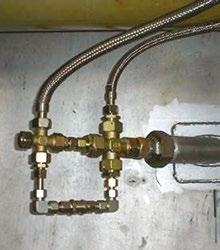
térmico. Em alguns casos, qualidades de superfície não uniformes, como oxidação, podem ser remediadas por decapagem com ácido, jato de areia ou outros métodos de limpeza manual. A variabilidade em processos termoquímicos, como cementação, no entanto, pode resultar em profundidade de camada irregular e efeitos metalúrgicos irreversíveis no substrato de metal que levam a taxas de refugo mais altas.
Alguns fornos podem se beneficiar de tecnologias de injeção de gás, como injeção de gás de alta velocidade (HSGI – High Speed Gas Injection), uma tecnologia patenteada desenvolvida pela Messer, onde o gás da atmosfera é injetado a partir de bicos especialmente projetados para criar fluxos supersônicos. HSGI é mais frequentemente usado sozinho.
Em fornos que usam recirculadores, o HSGI pode substituí-los completamente ou fornecer circulação suplementar se alguns estiverem inacessíveis. Ao modelar o uso e a colocação de vários bicos em um forno, é possível criar o mesmo efeito ou um efeito melhorado de quaisquer
Fig. 3. Melhorias na mistura e convecção da atmosfera podem ser modeladas para otimizar o projeto do sistema. Usando o software FLUENT de dinâmica de fluidos computacional (CFD - Computational Fluid Dynamics), essas imagens mostram as velocidades do gás em torno das bobinas dentro de um forno de tratamento térmico antes (à esquerda) e após a instalação da tecnologia Messer HSGI (à direita). A tecnologia de injeção de gás de alta velocidade (HSGI) melhora muito a mistura da atmosfera para maior qualidade e tempos de ciclo mais curtos (10-15%) em fornos de tratamento térmico
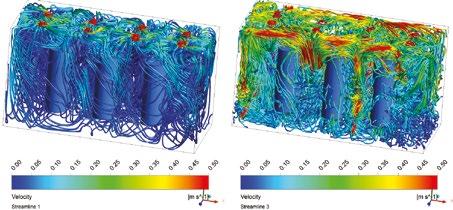
ventiladores existentes. A vantagem do HSGI é que ele cria uma distribuição de gás mais uniforme da atmosfera em todo o forno. Para aplicações de substituição, os bicos podem eliminar os custos de manutenção e funcionamento do recirculador.
A uniformidade melhorada levará a resultados de amostragem de gás mais consistentes em todo o forno, uma vez que a composição do gás em qualquer ponto deve agora exibir uma composição muito semelhante. Esta é a evidência da eficácia da controlabilidade e confiabilidade aprimoradas com tecnologias de controle de atmosfera.
A uniformidade da atmosfera também levará a uma melhor resposta do sistema de controle. Situações indesejadas podem ser corrigidas muito mais rápido quando a situação é comunicada ao sistema de controle mais cedo. O sistema de controle pode então executar ações corretivas para mudanças na composição do gás.
Por exemplo, o fluxo de gás na entrada do forno pode ser aumentado assim que detecta um aumento na concentração de oxigênio nas zonas de aquecimento. A concentração de hidrogênio em uma atmosfera de nitrogênio-hidrogênio para recozimento pode ser aumentada assim que detecta uma leitura de ponto de orvalho acima do normal, ou o fluxo geral pode ser aumentado assumindo que há um vazamento em algum lugar do forno. Compensar um vazamento aumentando a taxa de fluxo geral também pode melhorar a confiabilidade do sistema de controle. Isso deve ficar claro, pois manter uma atmosfera uniforme ajuda a eliminar atrasos na detecção de problemas que podem causar rejeições.
O HSGI pode substituir os ventiladores nos casos em que sua função principal é a circulação do gás na atmosfera do forno para facilitar as reações do gás. Ao substituir os ventiladores, todos os custos associados ao sistema podem ser eliminados e uma atmosfera muito mais uniforme pode ser alcançada. Isso obviamente leva a uma maior eficiência e qualidade consistente do produto. A uniformidade aprimorada pode aumentar a produtividade em até 25%,
reduzindo o tempo para compensar as reações de superfície não uniformes. Especificamente, o tempo de ciclo pode ser reduzido em fornos de poço para cementação. Além disso, o espaço de trabalho disponível pode ser aumentado devido à remoção de estruturas internas que suportam as operações do recirculador.
O HSGI também pode substituir ou complementar os recirculadores onde o objetivo principal é aumentar a convecção. Com bicos HSGI suficientes, efeitos de convecção equivalentes podem ser obtidos. Não há nenhum caso no tratamento térmico em que a uniformidade da atmosfera não seja importante. Portanto, o HSGI também pode ter como alvo áreas específicas onde a atmosfera é considerada estagnada. No recozimento de alumínio, por exemplo, a circulação de gás em torno das bordas das bobinas pode ser melhorada para auxiliar na remoção do lubrificante para eliminar a mancha nas bordas, reduzindo assim os tempos de ciclo.
A patenteada tecnologia HSGI tem um histórico comprovado em muitas operações de tratamento térmico e fornos. Ao fornecer uniformidade, melhora a confiabilidade do controle da atmosfera. Isso, por sua vez, aumenta a produtividade e a confiabilidade das atmosferas dos fornos e dos processos de tratamento térmico.
Uma abordagem de engenharia direta para melhorar a confiabilidade do processo é primeiro começar modelando a atmosfera e o forno existentes. Em seguida, projete um sistema de controle da atmosfera do forno que forneça os resultados desejados. Empregar tecnologias de ponta, como HSGI, sensores de oxigênio e métodos analíticos avançados, pode maximizar a eficiência e a confiabilidade do processo.
Este artigo foi revisado gentilmente pela Messer Gases Brasil (www. messer-br.com<http://www.messer-br.com>), representadas por Kati Torri, Carlos Kfouri e Gustavo Furigo.
PARA MAIS INFORMAÇÕES: O autor, Chris Ebeling, é vice-presidente executivo de Vendas e Marketing US Bulk na Messer em Bridgewater, NJ, EUA. Para obter assistência na solução de problemas de tratamento térmico ou obter mais informações sobre gases industriais e sistemas de controle de atmosfera para melhorar o desempenho, entre em contato com a Messer em tel: +1 800-755-9277 ou web:
www.messer-us.com.

Como Selecionar o Melhor Recirculador para o seu Processo
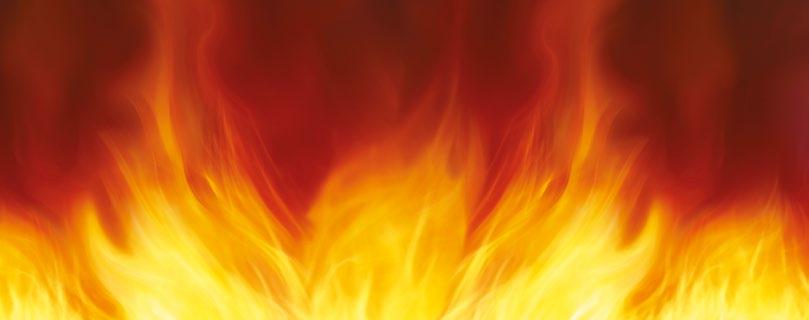
Eric S. Boltz and Aaron Saldanha – Howden Americas; Fairfield, Ohio, EUA
Os recirculadores são parte integrante do tratamento térmico com atmosfera, mas quais são os melhores projetos de recirculadores para um determinado processo?
Os recirculadores são parte integrante do tratamento térmico com atmosfera devido à necessidade de ter uma composição consistente da atmosfera na superfície da peça. Na verdade, como a interface da superfície atmosférica é onde estamos tentando manter - ou prevenir no caso de endurecimento neutro - uma reação química contínua, a agitação da atmosfera do forno é crítica. Mas qualquer pessoa que esteja no tratamento térmico por um tempo significativo ouviu muitas reclamações sobre o desempenho ou falha do recirculador. O desempenho insatisfatório ou falha geralmente é o resultado de uma combinação inadequada entre o processo e o projeto do recirculador. Quais são os melhores designs de recirculadores para um determinado processo? No final das contas, é principalmente sobre a roda.
Tipos de roda
Em linguagem de leque, o rotor do ventilador que move o ar ou uma mistura de gases é chamado de roda do ventilador. Existem muitos designs diferentes de rodas, mas cinco tipos básicos de rodas são encontrados dentro de fornos de tratamento térmico. Os nomes dos tipos descrevem as lâminas da roda. Eles são curvos para frente, axiais, inclinados para trás, radiais e com pontas radiais. Lâminas de aerofólio e lâminas curvadas para trás, que são o tipo mais eficiente de pás de ventilador, não são comumente usadas para esta aplicação devido à presença de impurezas na corrente de ar.
Curvado para a Frente
Rodas curvadas para frente (Fig. 1) são amplamente utilizadas em aplicações de tratamento térmico porque estão entre os designs mais silenciosos e podem ser construídas com materiais que permitem a implantação em temperaturas de até 1093°C. Geralmente, eles têm o menor tamanho de roda que você pode obter para um determinado requisito de fluxo de ar. Eles são adequados para criar pressão moderada e volumes de fluxo com eficiência relativamente baixa, mas requerem um alojamento para criar a aerodinâmica para o movimento adequado do gás. Como tal, os fornos que implantam rodas curvadas para frente frequentemente integram o alojamento da roda na parede ou teto do forno.
Projetos curvos para frente
Fig. 2. A série Howden Garden City Fan FF é um exemplo de uma roda de ventilador curvada para frente em alta temperatura
acumularão sujeira, entretanto, o que degradará o desempenho e poderá resultar em danos ao ventilador devido ao desequilíbrio resultante da roda. Isso limita os projetos curvos para frente para limpar processos como têmpera, recozimento e aplicações de homogeneização. Rodas curvadas para frente (Fig. 2) não são adequadas para cementação.

Inclinado para Trás
Rodas com pás inclinadas para trás (Fig. 3) estão entre os projetos mais eficientes para ventiladores que manuseiam correntes de ar mais sujas. Eles podem fornecer grandes volumes de gás com geração de pressão moderada e baixo ruído. Embora possam lidar com correntes de ar com partículas, não são adequados para partículas pegajosas. Seu design também não é adequado para temperaturas acima de 538°C. A aplicação mais comum para este projeto de roda (Fig. 4) no tratamento térmico é para resfriamento ou ventiladores de combustão.
Axial
As rodas axiais parecem hélices (Fig. 5). Elas podem empurrar volumes moderados a altos de gás enquanto criam pressão moderada, mas com eficiências mais baixas do que os ventiladores centrífugos. Eles são
Fig. 3. Rodas inclinadas para trás são eficientes e tolerantes a partículas não pegajosas, mas são limitadas a 538°C
tolerantes a partículas secas ou pegajosas, tornando-os adequados para processos mais sujos, como a cementação, e podem ser construídos para implantação em temperaturas de até 1093 ° C.
Muitos desses ventiladores axiais podem ser projetados para serem reversíveis por natureza. Ao alterar a direção de rotação da roda, a direção do fluxo de ar pode ser alterada. Este recurso (não disponível em ventiladores centrífugos) torna o ventilador axial uma opção atraente em muitos fornos para melhorar a circulação de ar.
Os ventiladores axiais geralmente são implantados sem qualquer caixa, embora isso reduza drasticamente sua eficiência e a pressão que podem criar. Para eliminar essa degradação de desempenho, alguns projetos usam um anel estático (Fig. 6) de material ao redor da lâmina para criar um efeito semelhante a um alojamento radial. A lacuna entre a ponta da lâmina e o anel estático é crítica para o desempenho do ventilador e precisa ser verificada durante a manutenção.
Radial
A roda de lâmina radial é freqüentemente chamada de desenho de roda de pás (Fig. 7). O design da roda de pás faz com que a roda solte sujeira - incluindo partículas pegajosas - conforme gira, tornando-a uma roda autolimpante. Isso o torna particularmente adequado para aplicações mais sujas, como a cementação.
O design também permite que essas rodas girem mais rápido do que outros designs, de modo que cobrem uma ampla gama de volumes e pressões. Sua eficiência é baixa, entretanto, e eles tendem a ser muito barulhentos, principalmente quando usados para criar pressões mais altas. As rodas de lâmina radial (Fig. 8) podem ser fabricadas para implantação em temperaturas de até 1093°C e podem acomodar revestimentos de lâmina para uso com partículas altamente abrasivas, como partículas de cerâmica. Eles são robustos o suficiente para serem usados até mesmo para mover mídia, como aparas de madeira.
Radial - Inclinado
Como o nome sugere, a lâmina com ponta radial (Fig. 9) tem características de lâmina curvada para trás, mas com a ponta da lâmina radial ao centro da roda. Isso permite que a roda seja mais eficiente e, ao mesmo tempo, lide com pequenas quantidades de partículas.
Selecionando a melhor roda do ventilador para o seu processo
É um procedimento direto para selecionar a melhor roda do ventilador para o seu forno. Essencialmente, deve-se caracterizar o ambiente dentro do qual o ventilador irá operar e a corrente de gás que o ventilador estará movendo. Os parâmetros críticos que será necessário definir são: • Em que faixa de temperatura este ventilador funcionará? • O processo contém partículas? Se sim, as partículas são pegajosas? • Que volume (CFM (Cubic Feet / Minute – Pés Cúbicos por Minuto)) de
Fig. 4. A série BF é um exemplo de uma roda de ventilador inclinada para trás
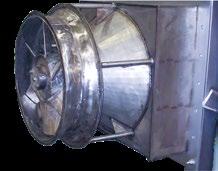
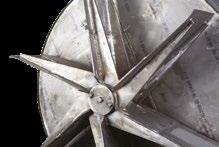
Fig. 5. As rodas de pás axiais são tolerantes a atmosferas mais sujas e podem suportar altas temperaturas, mas requerem um anel circunferencial ao redor do rotor para desenvolver pressões significativas
Fig. 6. A série PF-2 é um exemplo de ventilador de plugue axial usando um anel circunferencial estático para aumentar o desempenho do ventilador. Este ventilador é reversível por natureza

gás preciso mover e a que pressão? • Existem componentes do fluxo de gás que são corrosivos ou abrasivos? • É possível integrar uma carcaça para a roda do ventilador no teto ou parede do forno para criar a aerodinâmica correta, ou é necessário usar uma roda que não requeira carcaça? • Existem preocupações sobre eficiência ou som que devem ser abordadas?
Munido das respostas a essas perguntas, pode-se identificar o
Fig. 7. Rodas de lâmina radial são as mais robustas e tolerantes a sujeira graças ao seu design autolimpante. Adequado para altas temperaturas, suas principais desvantagens são eficiência e ruído
tipo de roda mais adequado para um determinado processo. Também é possível fornecer respostas a essas perguntas ao fornecedor de ventiladores, onde engenheiros de aplicação experientes podem fazer recomendações e fornecer um desenho para integração no projeto geral do forno.
Conclusões
Ventiladores em processos de tratamento térmico podem ser um ponto de frustração para muitos porque podem ser uma consideração tardia no projeto do forno em alguns casos. Não é comum ver um forno originalmente projetado para um processo reaproveitado para um processo diferente. Quando isso acontece, é possível que o volante original não seja adequado para o novo processo, caso em que o desempenho pode ser prejudicado até que o volante seja atualizado para atender às demandas da nova aplicação.
Por exemplo, se um forno for alterado de uma aplicação de particulado seco para uma aplicação de particulado pegajoso, a roda errada acumulará as partículas pegajosas, desenvolverá um desequilíbrio e, por fim, resultará em falha do ventilador e perda potencial de carga. Da mesma forma, o uso de uma roda que não forneça volume de fluxo ou pressão suficiente pode resultar em má circulação em torno da carga e degradação subsequente nas propriedades da superfície das peças tratadas.
Ao otimizar a seleção do ventilador para o processo em vez do forno, podese maximizar o desempenho e a vida útil. A intenção deste artigo é fornecer um guia para otimização, mas, na dúvida, seu fornecedor de ventiladores terá especialistas prontos para ajudá-lo.
PARA MAIS INFORMAÇÕES: Contate com Eric
S. Boltz, PhD, Garden City, Howden Americas, 2933 Symmes Rd. Fairfield, OH 45014, EUA; tel: +1-513-714-7075; e-mail: eric.boltz@ howden.com; web: www.howden.com.
Sistemas de Remoção de Lubrificantes na Sinterização: Revisão e Tecnologia mais Recente
Stephen L. Feldbauer – Abbott Furnace Company; St. Marys, Pa., EUA Quer um produto sinterizado seja produzido por meio de fabricação de aditivos binder-jet, moldagem por injeção de metal ou prensa e sinterização convencionais, a necessidade de remoção de lubrificante continua a ser um dos problemas mais comuns na sinterização.
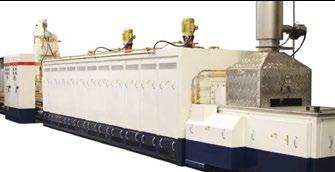
Como acontece com todas as tecnologias, novas técnicas de moldagem resultaram no desenvolvimento de novos lubrificantes. O resultado é a necessidade de ainda mais compreensão e desenvolvimento de processos na remoção de lubrificantes. Uma revisão das “velhas regras práticas”, soluções atuais e para onde a tecnologia de remoção de lubrificante está se dirigindo ajudará a traçar um roteiro para lidar com esse problema hoje e no futuro.
Pano de Fundo
Existem duas etapas comuns para o processo de fabricação de componentes de metal em pó (PM - Powder-Metal): moldar o pó na geometria de componente desejada e sinterizar o componente para desenvolver as propriedades de material desejadas. Em cada etapa, o lubrificante adicionado ao pó é uma consideração importante.
Durante a etapa de formação (por exemplo, compactação), a lubrificação é fornecida quando ela derrete e se move para as
Metano CH 4 Temperatura> 1012 ° F (550 ° C)
Hidro-carbono menor
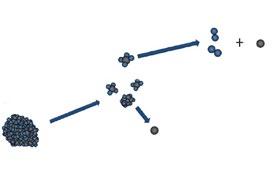
Etileno bis-estearamida Fuligem
Carbono
Hidrogênio (H 2 )
Temperatura> 500 ° F (260 ° C) Fig. 1. O Vulcan
superfícies da matriz. O lubrificante é necessário para a ejeção do compacto, evitando rachaduras do compacto e melhorando a vida útil da ferramenta. Infelizmente, o lubrificante que era tão necessário na etapa de modelagem deve ser removido do compacto de PM antes que as partículas possam se sinterizar.
O lubrificante que reveste cada partícula agora atua como uma barreira entre as partículas e pode dificultar o processo de sinterização. Portanto, o lubrificante deve ser removido do compacto nos estágios iniciais do processo de sinterização. A não remoção adequada do lubrificante pode resultar em vários problemas dentro da peça e do forno de sinterização.
O tipo mais comum de lubrificante usado no processo de PM convencional é o etileno bis-estearamida (EBS), também conhecido como Acrawax-C do Lonza Group. Este material é relatado como tendo um ponto de fusão de 140°C e um ponto de ebulição de 260°C. Pode-se concluir que o lubrificante deve derreter e ferver para fora do compacto no início do processo de sinterização, mas este não é o caso.
EBS foi observado [2,3] em função da temperatura. EBS não ferve a 260°C. Na verdade, ele permanece líquido a aproximadamente 540°C e então se dissocia totalmente em carbono e hidrogênio. O carbono sólido, ou fuligem, formado é a causa raiz dos problemas de remoção de lubrificante no processo de PM (Fig. 2, online). Variando em graus de severidade, a fuligem pode ser encontrada nas peças, nas peças e no forno (Fig. 3).
Outra observação importante informa que uma vez que o EBS derrete, o carbono começa a estar presente no líqui
do como um sólido até que toda a solução se torne carbono sólido. Isso foi explicado em um mecanismo proposto pela primeira vez em palestras por Levanduski, et.al. [1] da Abbott Furnace Company.
Como a maioria das cadeias de hidrocarbonetos, conforme o EBS é aquecido, ele começa a se decompor em cadeias menores de hidrocarbonetos. Eventualmente, ele se decomporá e se tornará o menor hidrocarboneto, o metano. Termodinamicamente, o metano não é mais estável quando atinge aproximadamente 550°C e se dissocia em carbono sólido e hidrogênio [2,3] .
Powell, et.al. [2,3] também observam que a densidade do compacto de PM desempenha um papel importante no processo de remoção de lubrificante. Conforme a tecnologia de compactação melhora para permitir a produção de compactos com uma densidade cada vez maior conforme compactado, o tempo necessário para que o EBS saia do compacto se torna mais longo (Fig. 4). Isso nos força a reconsiderar a regra prática de longa data que indica que 20 minutos foi adequado para a remoção de EBS.
Aqui vemos que a regra prática funcionaria bem para compactos de densidade mais baixa que eram comuns no passado. No entanto, esta não é mais uma regra válida. O tempo para o lubrificante sair do compacto, portanto o tempo para o compacto ser 140-540°C, deve aumentar com o desejo de pressionar para densidades verdes mais altas.
Há outra etapa importante nesse mecanismo [1] . Conforme o EBS se decompõe, ele não pode ser dividido em um número par de moléculas de metano. O resultado é o carbono sendo deixado para trás. Isso explica a presença de carbono no líquido da fusão [2,3] . Isso também aponta para outro aspecto- -chave do processo de remoção de lubrificante. O lubrificante sai do compacto como um líquido e então ferve para formar um vapor. No entanto, mesmo que todo o lubrificante líquido possa ser removido, ainda há carbono sólido que será deixado para trás conforme o EBS se dissocia.
Equipamentos e Auxiliares Para Remoção de Lubrificante
Ao longo dos anos, vários dispositivos e ferramentas de processamento foram desenvolvidos para auxiliar na remoção de lubrificante e tratar a presença de carbono. Os primeiros fornos de sinterização eram projetos de caixa única, onde o compacto era pré-aquecido e a remoção do lubrificante ocorria na frente da caixa aquecida. Determinou-se então que duas caixas aquecidas no forno ajudariam na remoção do lubrificante e permitiriam que a regra de ouro de 20 minutos na primeira caixa aquecida fosse mantida. Conforme a densidade dos compactos aumentava e as cargas de sinterização aumentavam, no entanto, isso não era suficiente para resolver todos os problemas de remoção de lubrificante.
O borbulhador foi o primeiro dispositivo adicionado aos fornos para auxiliar na remoção de lubrificantes e no combate à fuligem (Fig. 5). O conceito era fazer borbulhar nitrogênio na água. O nitrogênio pegaria a umidade e a carregaria para a seção de pré-aquecimento do forno. O local da injeção era normalmente colocado dois terços do caminho para a seção de pré-aquecimento (Fig. 6, online). Isso coincidia com o local onde a maioria dos produtos atingiria cerca de 650°C, porque podia ser visto no forno que era o local onde a fuligem começava a se formar e se acumular.
Para aumentar a capacidade do borbulhador, a água é então aquecida para acelerar a formação de vapor d’água e carregada para o forno. O grau de controle da bolha é limitado porque só se tem a temperatura da água e a vazão de nitrogênio como variáveis de ajuste. No entanto, os borbulhadores têm um bom desempenho para peças pequenas e médias e taxas de produção. Eles são capazes de produzir até aproximadamente 5 libras / hora de vapor d’água.
Infelizmente, a variabilidade no desempenho do borbulhador aumenta nas taxas de fluxo mais altas porque a grande quantidade de nitrogênio pode freqüentemente fazer com que o banho de água se torne instável e a água líquida seja captada pelo gás. Esta forma líquida da água causa picos na quantidade real de umidade que está sendo introduzida no forno.
Para resolver os problemas de controle do borbulhador, foi desenvolvido um dispositivo onde a água é jogada em um aquecedor para formar vapor. O vapor é então transportado por um fluxo de nitrogênio para o mesmo local de injeção do forno que o borbulhador. Estes são chamados de sistemas FAST (Furnace and Atmosphere Service Technology - Tecnologia de Serviço de Forno e de Atmosfera) (Fig. 8).
Como a variável de controle agora é a quantidade de água introduzida no aquecedor, o grau de controle é muito melhor. O fator limitante é o tamanho do aquecedor, que afeta a quantidade de vapor d’água que pode ser produzida. Os sistemas FAST são normalmente limitados a aproximadamente 2,5 libras / hora de vapor de água. Os sistemas funcionam bem para baixas taxas de produção e peças pequenas com menos lubrificante.
Para taxas de produção e peças grandes que requerem mais vapor de água para reagir com o lubrificante, foram desenvol-
Gramas de peso 14.75
14.70
14.65
14.60
14.55
14.50
14.45
14.40
14.35 Slug de meia polegada de diâmetro a 500 ºF

0 5 10 15 20 25 30 35 40 45 Time (minutos)
Fig. 4. Tempo para remover EBS vs. densidade [2] 6.2 g/cc 6.6 g/cc 7.0 g/cc
N2
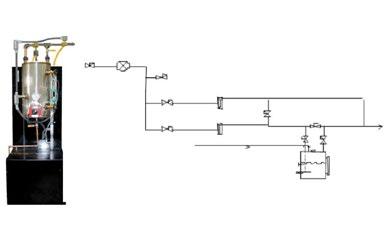
Water
Fig. 5. Borbulhador e esquema do encanamento
vidos sistemas que usam um queimador de gás para produzir a atmosfera. A proporção ar-combustível do queimador é ajustada para produzir a atmosfera contendo umidade usada para ajudar no processo de remoção do lubrificante. Um exemplo comum desta tecnologia é um processo de delubeamento de qualidade (QDP - Quality Delube Process , Fig. 9).
O gás do queimador é produzido em uma câmara acima do produto quando ele entra. O gás é então introduzido no produto no mesmo local da etapa de pré-aquecimento do processo que os outros métodos, aproximadamente 650°C.
Limitada apenas pelo tamanho do queimador selecionado, a quantidade de vapor d’água que esse tipo de sistema pode produzir é substancialmente maior do que outros sistemas. Devido à grande quantidade de umidade produzida, mesmo quando o queimador é reduzido para fogo baixo, este sistema não funciona bem para peças pequenas e cargas de produção leves. Essas cargas não transportam lubrificante produtor de carbono suficiente para reagir com a grande quantidade de umidade produzida. O resultado é uma oxidação das peças que é evidente por congelamento e descarbonetação.
O sistema é controlado por um termopar localizado na câmara de combustão superior. Como o queimador produz calor enquanto gera a atmosfera, a quantidade de umidade é diretamente influenciada pela temperatura da câmara. Esta é uma fonte de variabilidade.
Outra desvantagem significativa desse tipo de sistema é a manutenção. O desempenho do queimador mudará com o tempo. Isso requer uma pessoa com conhecimento em ajuste de queimador para fazer a manutenção rotineira do sistema.
Reconhecendo que o tempo para remover o lubrificante do compacto continuava a aumentar, as seções de pré-aquecimento do forno continuaram a se tornar mais longas e a tecnologia foi desenvolvida para aumentar o tempo em que o compacto está na faixa de temperatura ideal de remoção do lubrificante. Um deles, conhecido como Zona 0, é uma simples adição de um gargalo isolado à seção de pré-aquecimento do forno (Fig. 11, online). Os gases quentes que saem do forno passam sobre os componentes de entrada, os pré-aquecem e ajudam a iniciar a fusão do lubrificante mais cedo.
Uma outra adição a esta abordagem simples é adicionar a capacidade de injetar ar aquecido na Zona 0. O ar reage com o excesso de combustível da atmosfera do forno para produzir calor. Essa adição ao sistema é chamada de tecnologia de queimador de lubrificante (LBT - Lubricant Burner Technology).
Embora a Zona 0 e o LBT ajudem a diminuir o tempo de remoção do lubrificante, nenhuma das tecnologias fornece um meio de lidar com o carbono produzido durante a quebra da cadeia de hidrocarbonetos.
O Vulcan
A falta de controle é a desvantagem subjacente a todas as tecnologias desenvolvidas até o momento. A temperatura, o tempo, a composição da atmosfera de
N2
Vapor

Fig. 8. Sistema FAST e esquema de encanamento

Fig. 9. QDP e esquema de encanamento Gás
Ar
Fig. 12. O Vulcan
sinterização e a umidade para auxiliar na reação do carbono são frequentemente conectados diretamente ou limitados no grau de seu controle.
Um desenvolvimento recente enfoca a necessidade de um controle de processo melhor e independente. Este sistema é denominado Vulcan (Fig. 12). É uma

substituição direta das tecnologias de caixa de pré-aquecimento existentes.
Como a faixa de temperatura ideal para a remoção de lubrificante está entre 140-540°C, o aquecimento por radiação, como é usado em fornos convencionais, não é eficaz. O Vulcan usa aquecimento convectivo com ventiladores de velocidade variável para fornecer controle independente da taxa de aquecimento e do perfil de temperatura do compacto.
O tempo na faixa de temperatura ideal é controlado a 540°C ou menos pelo comprimento do sistema e o aquecimento em cada zona. Este tempo é ajustável para coincidir com a densidade de entrada do compacto, deixando para trás a regra prática.
A umidade também é independente de todas as outras variáveis. Com a capacidade de produzir de 0-12 libras / hora de vapor, o fluxo pode ser ajustado para fornecer o máximo ou o mínimo de umidade necessária para reagir com o carbono durante a decomposição do EBS. Isso dá ao mesmo sistema a capacidade de processar pequenas peças e cargas, bem como peças grandes e cargas pesadas.
Combinar a compreensão da remoção de lubrificante com o conhecimento do controle da atmosfera e do calor produziu um sistema que demonstrou funcionar em um nível ideal para uma ampla gama de níveis de produção e tamanhos de peças. Estudos de perda de peso demonstraram 100% de remoção de lubrificante para Interlube E e EBS sem oxidar ou descarbonetar o compacto.
Este artigo foi revisado gentilmente por Aparício Freitas da Combustol Fornos.
PARA MAIS INFORMAÇÕES: Contate Stephen
L. Feldbauer, Ph.D., diretor, Pesquisa e Desenvolvimento, Abbott Furnace Company, 1068 Trout Run Road, PO Box 967, St. Marys, PA 15857, EUA; tel: +1 814-781- 6355; e-mail: sfeldbauer@abbottfurnace.com; web: http://www.abbotturnace.com.
Modelamento e Aplicação de um Novo Tratamento Térmico para Refinamento de Microestruturas Bainíticas em um Aço de Baixo Carbono Resfriado Continuamente

Fig. 9. Microestrutura resultante do tratamento térmico de dois passes para a austenitização de 1200 °C. A figura (b) mostra a região delimitada de (a)
Pedro José de Castro, Thiago Marques Ivaniskia, Antonio Carlos de Figueiredo Silveira, Cristiano José Turra, Alexandre da Silva Rocha, Laboratório de Transformação Mecânica (LdTM), Universidade Federal do Rio Grande do Sul (UFRGS), Porto Alegre, Brasil
A crescente demanda em vista da eficiência energética no setor industrial exige que este setor apresente inovações tecnológicas e científicas continuamente. No setor de beneficiamento do aço, um dos caminhos em que a indústria e a academia vêm buscando melhorias é por meio da substituição de aços martensíticos, que demandam dispendiosos tratamentos térmicos posteriores visando ajustes de propriedades, alívio de tensões e correções de distorções. Uma das respostas a esse desafio é o emprego de aços bainíticos resfriados continuamente. Estes materiais visam atingir suas propriedades mecânicas de produto logo após seu processamento termomecânico, por meio de um resfriamento contínuo ao ar. O presente trabalho visou estudar a evolução microestrutural de um aço desta categoria em frente a um tratamento térmico baseado nos conceitos de uma nova classe comercial de aços, chamados “aços bainíticos nanoestruturados”. Para tanto, uma rota térmica que introduziu alta energia motriz no início da transformação bainítica foi desenvolvida. Além disso, buscou-se, por meio da simulação computacional, modelar a rota de resfriamento do corpo de prova, visando mapear as taxas de resfriamento ponto a ponto e obter maior controle do processo para futuras otimizações. Concluiu-se o contexto termodinâmico estabelecido pelo tratamento térmico de dois passes introduz uma matriz de bainita em ripas com maior dureza do que a matriz de bainita granular, que é presente no material em condição de recebimento.
A
tualmente há um grande interesse econômico e ambiental na substituição dos aços martensíticos por aços que obtenham propriedades mecânicas equivalentes ou superiores sem a utilização de tratamentos térmicos posteriores como o revenimento da microestrutura para ajuste de propriedades. Uma alternativa que está se consolidando para esta questão é a utilização de aços bainíticos. Esta classe de aços, que têm sido extensivamente investigadas nas últimas décadas
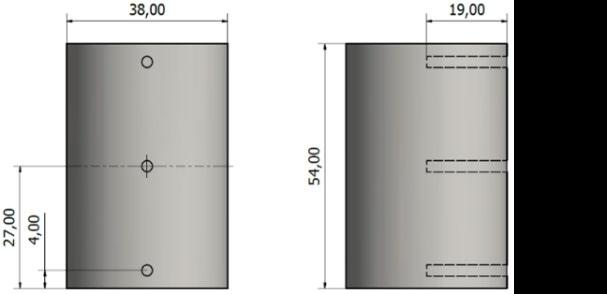
Fig. 2. Curvas de temperatura do núcleo e para as extremidades plotadas sobre o diagrama de resfriamento do aço utilizado

Fig. 3. Microestrutura do material na condição de recebimento. (b) exibe a área delimitado pelo retângulo em (a)
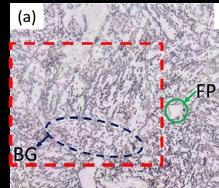

[1, 4] , oferece propriedades mecânicas formento da composição química e rotas ter
midáveis para uma vasta gama de composições químicas e rotas de processamento termomecânicos. Os aços bainíticos resfriados continuamente são uma das classes promissoras de novos materiais para a obtenção de propriedades finais a partir do tratamento termomecânico seguido por resfriamento continuo em ar [5, 7] . Com a utilização desta rota, descarta-se a necessidade do revenimento e de processamento posterior para correções das distorções que ocorreriam após o processo de têmpera. Além disso, para aços bainíticos resfriados continuamente com baixo teor de carbono, há a possibilidade de utilização dessas ligas para a soldagem sem grandes complicações [8,9] . Porém, mesmo com as qualidades das novas classes de aços bainíticos, existe uma lacuna entre as propriedades mecânicas oferecidas pelos aços martensíticos temperados e revenidos e os aços bainíticos [10,11] . Para tanto, faz-se necessário o aperfeiçoamomecânicas de processamento para estes novos materiais, visando fechar ou superar esta lacuna de propriedades.
A classe dos aços bainíticos nanoestruturados [12,13] , que é uma classe de aços de médio para alto carbono, é um exemplo de sucesso entre aplicação dos conceitos teóricos do design de ligas bainíticas e escala industrial. Estes materiais alcançam as maiores resistências a tração para a classe de aços bainíticos (aproximadamente 2500 Mpa) e, devido a sua rota de processamento, podem ser comercializados em uma vasta gama de diâmetros de barra [14,15] . O ponto chave destes materiais está no controle do desenvolvimento bainítico na nano escala. Isto é realizado com banhos isotérmicos em baixíssimas temperaturas que, devida a alta força motriz de transformação, refinam os feixes de bainita e, por conseguinte, as ilhas restantes de austenita retida. A bainita produzida por esse tipo de processamento apresenta morfologia acicular, agrupada em pacotes com direção de crescimento clara e, portanto, é denominada bainita em ripas (BR). Esse tipo de morfologia se destoa bastante dos aços processados por resfriamento ao ar, que apresentam uma morfologia sem direção de crescimento evidente, aparentemente aleatória, chamada bainita granular (BG). Porém, os aços nanoestruturados necessitam de tratamentos de altíssima duração, podendo chegar a tratamentos com duração de meses [12] , o que limita o ferramental disponível para sua produção. Nesse quesito, os aços de baixo carbono apresentam a clara vantagem, de maneira que a transformação bainítica cessa em questão de minutos.
Este trabalho tem como objetivo a aplicação e modelamento por simulação computacional de uma nova rota térmica em aços bainíticos de baixo teor de carbono resfriados ao ar. Para tanto, desenvolveu-se uma rota composta por um resfriamento contínuo em dois passos: o primeiro, em um meio de alta taxa de resfriamento e o segundo ao ar. O intuito disto, foi unir as qualidades de um resfriamento ao ar às vantagens de um tratamento térmico em baixas temperaturas, conferindo à bainita melhores propriedades mecânicas. O tratamento térmico foi acompanhado termopares distribuídos ao longo do corpo de prova. A partir dos dados gerados pelos termopares, se desenvolveu um modelo por simulação de elementos finitos do tratamento térmico empregado com o objetivo de avaliar a variação dos campos de temperatura ponto a ponto, o que permitiu calcular as taxas de resfriamento para toda a geometria do corpo de prova. Este trabalho está incorporado no escopo do projeto “Energy Efficient Manufacturing Chain for Advanced Bainitic Forging Steels Based on Thermo-Mechanical Processing”, vinculado ao programa Brazilian-German Collabora
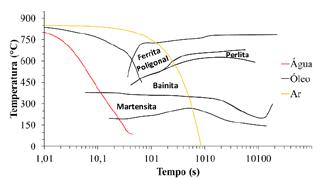
Fig. 4. Curvas de resfriamento obtidas pelo resfriamento em água, óleo e ar plotadas na CCT do aço estudado
Fig. 5. Curvas de resfriamento experimentais. As linhas horizontais representam o momento da retirada do banho líquido e da menor temperatura obtida para a base e o topo, respectivamente
tive Research Initiative on Smart Connected Manufacturing (BRAGECRIM), que visa estudar a viabilidade da aplicação de aços bainíticos ao processo de forjamento e posterior resfriamento contínuo, a fim de reduzir o consumo energético e reduzir o tamanho da cadeia de processos na fabricação de componentes mecânicos.
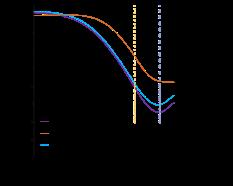
Composição química
No presente estudo foi utilizado o aço DIN 18MnCrSiMo6-4 (HSX 130) Swiss Steel, Suíça, cuja composição química é apresentada na Tabela 1.
Geometria dos corpos de prova e Resfriamento Contínuo em Dois Passos
O corpo de prova (CP) utilizado neste trabalho foi de tarugos cilíndricos simples, com geometria utilizada normalmente em tratamentos termomecânicos, como no caso de um forjamento. As dimensões do CP e as posições dos termopares utilizados são apresentadas na Fig. 1.
O primeiro passo para definição do tratamento térmico de dois passes foi a escolha de uma temperatura para início da transformação bainítica. A temperatura escolhida foi de 450°C, aproximadamente 70°C acima da linha da região de início de transformação martensítica (linha Ms) do aço em questão. Esta temperatura é baixa o suficiente para que se evite o campo de formação da ferrita poligonal e alta o suficiente para evitar o início da transformação martensítica. A rota térmica desenvolvida é ilustrada na Figura 1, plotada sobre o diagrama de transformação em resfriamento contínuo (contínuos cooling transformation curve, CCT) do aço utilizado. É importante notar que, devido a geometria do corpo de prova utilizado, há gradientes de temperaturas formados entre as regiões do núcleo e as regiões externas e, portanto, as transformações devem ocorrer em temperaturas diferentes. As curvas de resfriamento para as regiões do núcleo e extremidades esperadas são também ilustradas na Fig. 1.
Com base nas rotas térmicas desenvolvidas, foram então realizados tratamentos térmicos preliminares em óleo e água, visando encontrar o meio de resfriamento mais adequado. Os dados obtidos destes ensaios permitiram estimar o tempo necessário de permanência no banho líquido no primeiro passo de resfriamento, para que a transformação bainítica começasse no início do segundo passo. As temperaturas de austenitização empregadas foram de 1200°C e 1000°C, visando avaliar as variações morfológicas da bainita para diferentes tamanhos de grão austeníticos. O tempo de permanência em forno após o encharque foi de 20 minutos.
Simulação por Elementos Finitos
A partir dos dados coletados pelos termopares dispostos ao longo do corpo de prova, fez-se uma análise inversa por meio de simulação baseada em no método de elementos finitos (MEF) para obtenção dos coeficientes globais de troca térmica para cada meio de resfriamento utilizado. Considerou-se o corpo de prova como um sistema físico baseado nas equações constitutivas de troca de calor [16–18] . A Equação 1 representa a evolução de temperatura de um sistema, onde esta evolução é igual a competição entre condução interna de calor e sua dissipação de energia:
[1]
Onde ρ é a densidade do material c é o calor específico e k é a sua condutividade térmica. O valor de W ̇ é gerado por tensões plásticas que
Fig. 6. Valores das variáveis h,k e c para cada estágio do tratamento térmico para os dois casos simulados
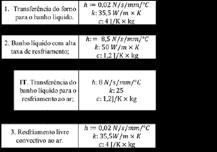
são dissipadas sob a forma de calor, no caso de materais que obecem a lei de Norton-Hoff. Estas, são definidas em termos de transferência de calor por radiação, condução e convecção, de acordo com as seguintes equações:
�� �� ��(�� 4 −�� 0 4 � =ℎ(��−�� 0 ) [2] [3]
O coeficiente ε é a emissividade do material, σ s é a constante de StefanBolzmann, T 0 é a temperatura do ambiente externo e T é a temperatura do corpo de prova. O valor de h representa o coeficiente global de transferência de calor por condução e convecção durante o processo de tratamento térmico, que varia de acordo com a condutividade térmica, k, do material e a sua temperatura. Partindo deste princípio, o modelamento do tratamento térmico foi dividido em múltiplos passos dependentes do coeficiente global de transferência de calor e a temperatura em que se encontra o corpo de prova. O tratamento térmico foi modelado pelo software DEFORM®. As condições de contorno utilizadas são apresentadas na Tabela 2. Neste trabalho, visando limitar sua extensão, só serão apresentadas as simulações para o tratamento térmico austenitizado a 1000°C.
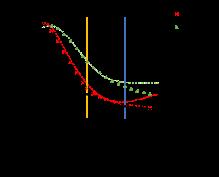
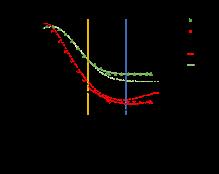
Fig. 7. Resultado comparativo das curvas de resfriamento experimentais comparadas com o modelo proposto. (a) simulação sem a etapa de IT (b) mostra o resultado com a utilização da etapa de IT. “Fit” é o nome atribuído às curvas de ajuste matemático
Fig. 8. Mapas de temperatura resultantes da simulação para (a) 11 segundos e (b) 20 segundos
Caracterização do Material em Estado de Recebimento
A microestrutura do material no estado de recebimento é apresentada na Fig. 3 com a sua respectiva dureza Vickers e taxa de resfriamento. Na Fig. 3 (b), é detalhada a região delimitada pelo retângulo em (a).
A partir da Fig. 3 se notam as principais características da bainita granular, que compõe a matriz do material no seu estado como recebido. Neste tipo microestrutura, a bainita ferrítica é revelada pelas regiões em branco permeada pelos constituintes MA como pequenas ilhas cinzas com formato irregular. As regiões com coloração mais escura são mais resistentes ao ataque químico, indicando provável maior teor de carbono [19] . Há também a presença de grãos de ferrita poligonal, em consequência da baixa taxa de resfriamento (aproximadamente 1°C/s) ao qual o material foi submetido durante sua produção.
Nesta microestrutura os contornos de grãos prévios são parcialmente mantidos, visivelmente na Fig. 3b. Isso se deve ao caráter ambíguo do mecanismo de crescimento da BG, que apresenta características de caráter difusional e adifusional [20,24] . Desta maneira, o mecanismo de crescimento
Fig. 10. - Microestrutura resultante do tratamento térmico de dois passes para a austenitização de 1200 °C. A figura (b) mostra a região delimitada de (a)
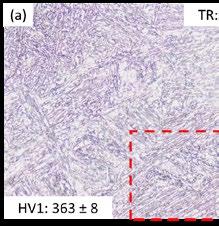
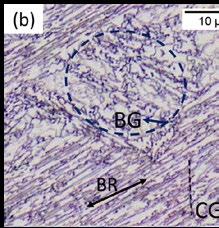
da BG ainda é alvo de incertezas no campo acadêmico, não ainda estando claro qual o mecanismo regente na formação desta microestrutura.
Tratamento Térmico de Dois Passes
A Fig. 4 mostra o resultado dos resfriamentos obtidos pelas têmperas preliminares plotadas na CCT do aço estudado comparadas com um resfriamento convencional para produção do aço, em convecção natural em ar (aproximadamente 1°C). Esta figura apresenta apenas a curva obtida pelo termopar localizado na base dos corpos de prova visto que esta é a região que apresentou maior taxa de resfriamento.
Como previsto, as regiões externas do corpo de prova perderam calor mais rapidamente que o núcleo. No momento que os corpos de prova alcançam a menor temperatura durante o resfriamento, aos 20 segundos, houve uma diferença de, aproximadamente, 40°C entre a base o topo, que é possivelmente resultado da direção do movimento do corpo de prova dentro do banho líquido o que cria uma camada de vapor responsável por isolar o corpo de prova heterogeneamente. No período da retirada do banho (11s) até a menor temperatura alcançada (20s), nota-se também que a taxa de resfriamento se mantém elevada, sugerindo que há uma transição gradual nos parâmetros de troca térmica durante a transição de meios. Após passar por este regime transitório, as extremidades do corpo de prova passam a ser aquecidas devido ao gradiente de temperatura entre o núcleo e as mesmas.
Modelamento por Simulação Numérica
O modelamento do tratamento térmico considerou inicialmente três etapas representantes do caminho do corpo de prova durante o tratamento térmico, este caminho inicial é aqui tratado como Caminho 1. Para cada etapa foi utilizado um coeficiente global de perda térmica, condutividade e calor específico referente à faixa de temperaturas em que se encontra o material. A Fig. 6 apresenta os diferentes valores de h,k e c utilizados para simulação de cada passo do tratamento térmico.
Pela análise posterior dos dados dos termopares, notou-se que a transição do meio líquido para o ar não resulta em uma variação abrupta do coeficiente de troca térmica do líquido para o ar. Este pode ser considerado como um período de “inércia térmica” (IT), resultando numa transição suave entre os meios de resfriamento. Para tanto, visando modelar esse comportamento, foi implementado um passo intermediário chamado de IT, que possui um coeficiente de transferência de calor intermediário, e diferentes valores de condutividade e calor específico, mostrados na Fig. 6 como um passo intermediário entre os passos 2 e 3 do caminho 1. Este segundo caminho é apresentado na Fig. 6, como caminho 2. A Fig. 7 apresenta as curvas modeladas sobrepostas aos resultados experimentais para as condições com (Fig. 7b) e sem (Fig. 7a) o período de inércia térmica. Para a curva com IT, devido à variação dos valores de entrada de condutividade térmica e do calor específico ao fim do primeiro e segundo passos no Caminho 2, foram calculados ajustes matemáticos para os dois seguintes passos, que são apresentados na Fig. 7.
Com base nos resultados da Fig. 7, nota-se a importância da
Tabela 1. Composição química do aço 18MnCrSiMo6-4, em porcentagem de massa
Elemento C Si Mn S Ni Cr Cu Mo Al Ti N Fe
Tabela 2 - Parâmetros utilizados na simulação computacional
Parâmetros da simulação
Número de elementos e nós
Temperatura de austenitização (°C) Emissividade (-) Temperatura Ambiente (°C) Tipo de Malha Solver Nós 6521 Elementos 28477
1000 e 1200 0,8-0,9 20 Tetragonal Newthon- Raphson
implementação de um passo intermediário para englobar a transição entre meios diferentes de resfriamento. Isto sugere que uma complexa interação térmica interna impede que ocorra uma transição abrupta entre os parâmetros da troca de calor do meio de maior taxa de resfriamento para o menor, o que deve ser considerado em tratamentos térmicos com variação na taxa de resfriamento.
Na Fig. 8 são apresentados os campos de temperatura resultantes da simulação para o momento de retirada do banho (Fig. 8a) e para o momento de menor temperatura para as regiões externas (Fig. 8b). Nota-se que as regiões externas do billet devem transformar para martensita devido à alta taxa de resfriamento proporcionada pela água.
Com com a evolução do campo de temperaturas é possível que ocorra o auto-revenimento desta martensita, o que assemelharia o tratamento em questão com a classe de aços temperados e auto revenidos (quench and self tempered - QST) [25,26] .Os campos de temperaturas também permitiram calcular a taxa de resfriamento média ponto a ponto, associando a microestrutura resultante com sua respectiva taxa de resfriamento. As taxas de resfriamento calculadas são apresentadas na seção 3.4.
Caracterização do Material Tratado Termicamente
Após a realização do tratamento térmico, devido ao novo contexto termodinâmico no qual ocorreu a transformação bainítica, houve uma mudança da matriz de bainita granular para bainita em ripas. Isso pode ser visualizado pela manutenção dos contornos de grãos prévios o que é uma característica de transformações adifusionais [22] . Outro fator responsável pela variação morfológica é a maior resistência mecânica da austenita em baixas temperaturas que é responsável pelo refino da espessura das ripas bainíticas [27,28] . Além disso, a alta taxa de resfriamento suprime a formação da ferrita poligonal, gerando uma microestrutura mais homogênea. A Fig. 9 mostra a microestrutura, microdureza e taxa de resfriamento resultantes da austenitização de 1000°C.
Para a condição de austenitização em 1200°C, houve um crescimento de grãos devido à alta temperatura, resultando em uma variação microestrutural notável. A Fig. 10 mostra os resultados microestruturas, de dureza e taxa de resfriamento para esta condição.
Caballero, et al, [21] analisaram a variação do tamanho de grão em tratamentos térmicos para produção de bainita granular. Em seu trabalho, foi concluído que grãos austeníticos prévios maiores devem favorecer a formação de bainita granular. Esse efeito pode ser visto na Fig. 10 (a e b), nas quais a identificação dos contornos de grãos é dificultada em relação a condição de grãos austeníticos menores, mostrado na Fig. 9, o que é atribuído ao caráter difusional da formação da bainita granular.
O aumento da dureza no material na condição tratada termicamente teve um aumento em média de, aproximadamente, 50 HV. Alguns autores [29,30] apontam que o mecanismo de aumento de resistência do em aços bainíticos é atribuído ao refinamento da espessura dos feixes bainíticos. No caso do tratamento térmico de dois passos, o refinamento é alcançado devido ao aumento da resistência mecânica da austenita, que dificulta o avanço da interface bainítica. As técnicas aqui utilizadas não são apropriadas para medição da espessura dos feixes bainíticos, más, a dificuldade de resolução da microestrutura do material tratado termicamente aponta para um refinamento microestrutural devido a maior quantidade de interfaces presente na Fig. 9 e Fig. 10 em relação ao material em condição de recebimento. Em relação a microdureza para as condições de maior e menor grãos austeníticos prévios, a condição com grão menor apresenta um pequeno aumento de microdureza, o que pode ser atribuído a maior quantidade de BR para esta condição.
Conclusões
As seguintes conclusões podem então ser sumarizadas: • O modelamento numérico do tratamento térmico de dois passes permitiu calcular as taxas de resfriamento ponto a ponto no corpo de prova, permitindo associar a taxa de resfriamento e microestrutura resultante; • O conceito de inércia térmica, baseada na transição entre meios de resfriamento com diferentes taxas de
resfriamento foi introduzido na simulação e permitiu uma maior aproximação com a curva obtida através dos experimentos físicos; • O tratamento térmico de dois passos suprime a formação de ferrita poligonal e introduz maiores volumes de bainita em ripas na microestrutura de um aço resfriado continuamente. Houve um aumento de dureza do material após o tratamento térmico, atribuído ao refinamento da espessura dos feixes de bainita.
Agradecimentos
Este trabalho foi realizado com suporte da CAPES (Programa BRAGECRIM, processo número 88881.142485/2017-01 - 1844/2017), Programa PROEX (Processo 88882.345785/2019-01) e CNPq (edital PQ 2018 processo 308773-7).
Referências
[1] Garcia-Mateo C, Paul G, Somani M, Porter D, Bracke L, Latz A, et al.
Transferring Nanoscale Bainite Concept to Lower C Contents: A Perspective. Metals (Basel) [Internet]. 2017 May 4;7(5):159. Available from: http://www.mdpi.com/2075-4701/7/5/159 [2] Rementeria R, Jimenez JA, Allain SYP, Geandier G, Poplawsky JD, Guo
W, et al. Quantitative assessment of carbon allocation anomalies in low temperature bainite. Acta Mater. 2017;133:333–45. [3] He SH, He BB, Zhu KY, Huang MX. On the correlation among dislocation density, lath thickness and yield stress of bainite. Acta Mater. 2017;135:382–9. [4] Takayama N, Miyamoto G, Furuhara T. Chemistry and three-dimensional morphology of martensite-austenite constituent in the bainite structure of low-carbon low-alloy steels. Acta Mater [Internet]. 2018;145:154–64. Available from: https://doi.org/10.1016/j.actamat.2017.11.036
[5] Buchmayr B. Critical assessment 22: Bainitic forging steels. Mater Sci
Technol (United Kingdom). 2016;32(6):517–22. [6] Sourmail T, Smanio V. Optimisation of the mechanical properties of air cooled bainitic steel components through tailoring of the transformation kinetics. Mater Sci Eng A [Internet]. 2013;582:257–61.
Available from: http://dx.doi.org/10.1016/j.msea.2013.06.040 [7] Xu Z bao, Hui W jun, Wang Z hua, Zhang Y jian, Zhao X ii, Zhao X ming. Mechanical properties of a microalloyed bainitic steel after hot forging and tempering. J Iron Steel Res Int. 2017; [8] Wang JP, Yang ZG, Bai BZ, Fang HS. Grain refinement and microstructural evolution of grain boundary allotriomorphic ferrite/granula
EXPERIÊNCIA QUE SUPERA 10 ANOS DE MERCADO Soluções completas e inovadoras em Equipamentos Industriais
Fornos a Vácuo Grafite e Fibras de Carbono Lavadora Industrial a Vácuo Service Care com Manutenção Preventiva/Preditiva e Corretiva Consultoria Técnica em Processamento Térmico Leak Test - Teste de Vazamento a Hélio
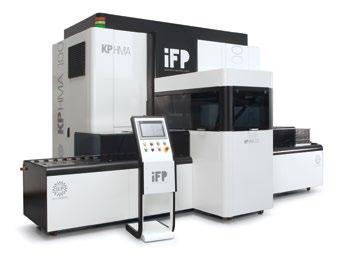
Equipamentos PVD/PECVD Fornos Industriais Peças de Reposição OEM e Customizadas Manutenção e Fabricação de Hot Zone / Câmaras Térmicas Serviços de Calibração Testes em Campo
+55 (12) 3021 4781 | www.LMTerm.com.br
bainite steel after prior austenite deformation. Mater Sci Eng A. 2004;369(1–2):112–8. [9] Zhang M, Wang YH, Zheng CL, Zhang FC, Wang TS. Effects of ausforming on isothermal bainite transformation behaviour and microstructural refinement in medium-carbon Si-Al-rich alloy steel.
Mater Des [Internet]. 2014;62:168–74. Available from: http://dx.doi. org/10.1016/j.matdes.2014.05.024 [10] Gomez G, Pérez T, Bhadeshia HKDH. Air cooled bainitic steels for strong, seamless pipes Part 1 – alloy design, kinetics and microstructure. Mater Sci Technol [Internet]. 2009;25(12):1501–7. Available from: http://www.tandfonline.com/doi/full/10.1179/174328408X388130 [11] Bhadeshia HKDH. Martensite and bainite in steels: Transformation mechanism & mechanical properties. J Phys IV JP. 1997;7(5). [12] Garcia-Mateo C, Caballero FG, Bhadeshia HKDH. Development of
Hard Bainite. ISIJ Int. 2003;43(8):1238–43. [13] Caballero FG, Bhadeshia HKDH, Mawella KJA, Jones DG, Brown
P. Very strong low temperature bainite. Mater Sci Technol. 2002;18(3):279–84. [14] Peet MJ, Bhadeshia HKDH. Surface relief due to bainite transformation at 473 K (200 °c). Metall Mater Trans A Phys Metall Mater Sci. 2011;42(11):3344–8. [15] Bhadeshia HKDH. Bainite in steels.Theory and Practice. IOM
Communications Ltd. 2015.
[16] Smoljan B. Numerical simulation of steel quenching. J Mater Eng
Perform. 2002;11(1):75–9. [17] Guo Z, Saunders N, Schille JP. Modelling phase transformations and material properties critical to simulation of heat treatment distortion in steels. Proc 17th IFHTSE Congr. 2008;2(2):753–6. [18] Sugianto A, Narazaki M, Kogawara M, Shirayori A, Kim SY, Kubota
S. Numerical simulation and experimental verification of carburizing-quenching process of SCr420H steel helical gear. J Mater Process
Technol. 2009; [19] Reisinger S, Ressel G, Eck S, Marsoner S. Differentiation of grain orientation with corrosive and colour etching on a granular bainitic steel. Micron [Internet]. 2017;99(April):67–73. Available from: http:// dx.doi.org/10.1016/j.micron.2017.04.002 [20] Josefsson B, Andrén H, Josefsson B, Microstructure HA, Granular
OF, Journal B. MICROSTRUCTURE OF GRANULAR BAINITE To cite this version : HAL Id : jpa-00228148. 1988;49. [21] Caballero FG, Roelofs H, Hasler S, Capdevila C, Chao J, Cornide
J, et al. Influence of bainite morphology on impact toughness of continuously cooled cementite free bainitic steels. Mater Sci Technol [Internet]. 2012;28(1):95–102. Available from: http://www.tandfonline.com/doi/full/10.1179/1743284710Y.0000000047
[22] Kang JS, Seol JB, Park CG. Three-dimensional characterization of bainitic microstructures in low-carbon high-strength low-alloy steel studied by electron backscatter diffraction. Mater Charact [Internet]. 2013;79:110–21. Available from: http://dx.doi.org/10.1016/j.matchar.2013.02.009
[23] Zajac S, Schwinn V, Tacke KH. Characterisation and Quantification of Complex Bainitic Microstructures in High and Ultra-High Strength
Linepipe Steels. Mater Sci Forum [Internet]. 2005;500–501:387–94.
Available from: http://www.scientific.net/MSF.500-501.387 [24] Peng K, Yang C, Fan C, Lin S. In situ observation and electron backscattered diffraction analysis of granular bainite in simulated heat-affected zone of high-strength low-alloy steel. Sci Technol Weld
Join. 2018;23(2):158–63. [25] Cadoni E, Dotta M, Forni D, Tesio N, Albertini C. Mechanical behaviour of quenched and self-tempered reinforcing steel in tension under high strain rate. Mater Des. 2013; [26] Isogawa S, Yoshida H, Hosoi Y, Tozawa Y. The Five Essentials of Pay for Performance. 1998;74:298–306. [27] Singh SB, Bhadeshia HKDH. Estimation of bainite plate-thickness in low-alloy steels. Mater Sci Eng A. 1998;245(1):72–9. [28] Caballero FG, Yen HW, Miller MK, Yang JR, Cornide J, Garcia-Mateo
C. Complementary use of transmission electron microscopy and atom probe tomography for the examination of plastic accommodation in nanocrystalline bainitic steels. Acta Mater [Internet]. 2011;59(15):6117–23. Available from: http://dx.doi.org/10.1016/j. actamat.2011.06.024
[29] Morales-Rivas L, Garcia-Mateo C, Sourmail T, Kuntz M, Rementeria
R, Caballero F. Ductility of Nanostructured Bainite. Metals (Basel). 2016;6(12):302. [30] Garcia-Mateo C, Jimenez JA, Lopez-Ezquerra B, Rementeria R, Morales-Rivas L, Kuntz M, et al. Analyzing the scale of the bainitic ferrite plates by XRD, SEM and TEM. Mater Charact. 2016;
Pedro José de Castro, Thiago Marques Ivaniski, Antonio Carlos de Figueiredo Silveira, Cristiano José Turra, Alexandre da Silva Rocha são do Laboratório de transformação mecânica (LdTM), Universidade Federal do Rio Grande do Sul (UFRGS), eles podem ser contatados no e-mail: pjdcastro73@gmail.com, antoniofigueiredosilveira@gmail.com, cristianojturra@gmail.com; thiagoivaniski@gmail.com.
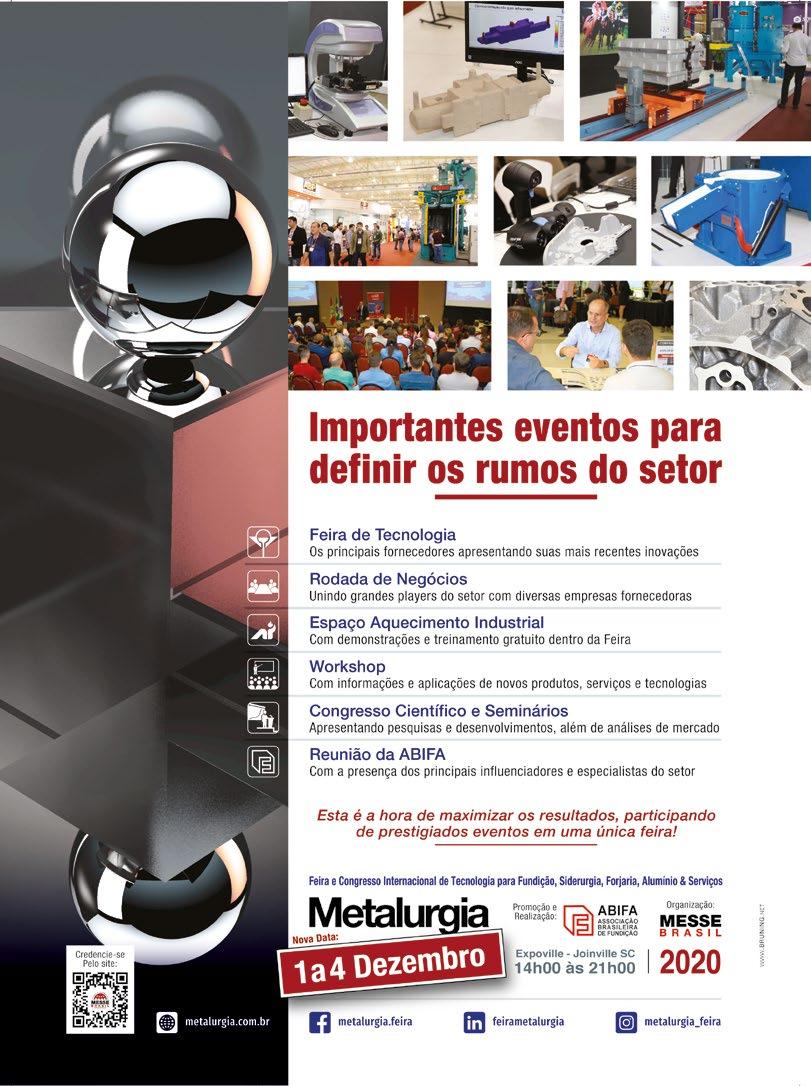
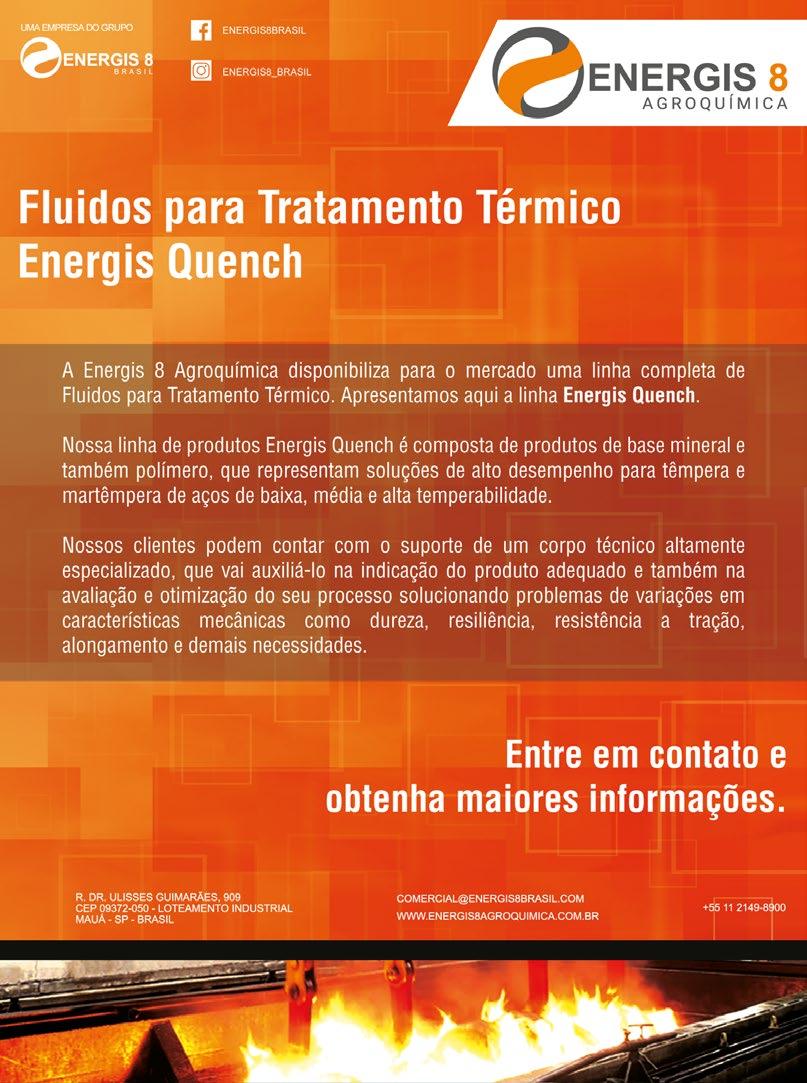