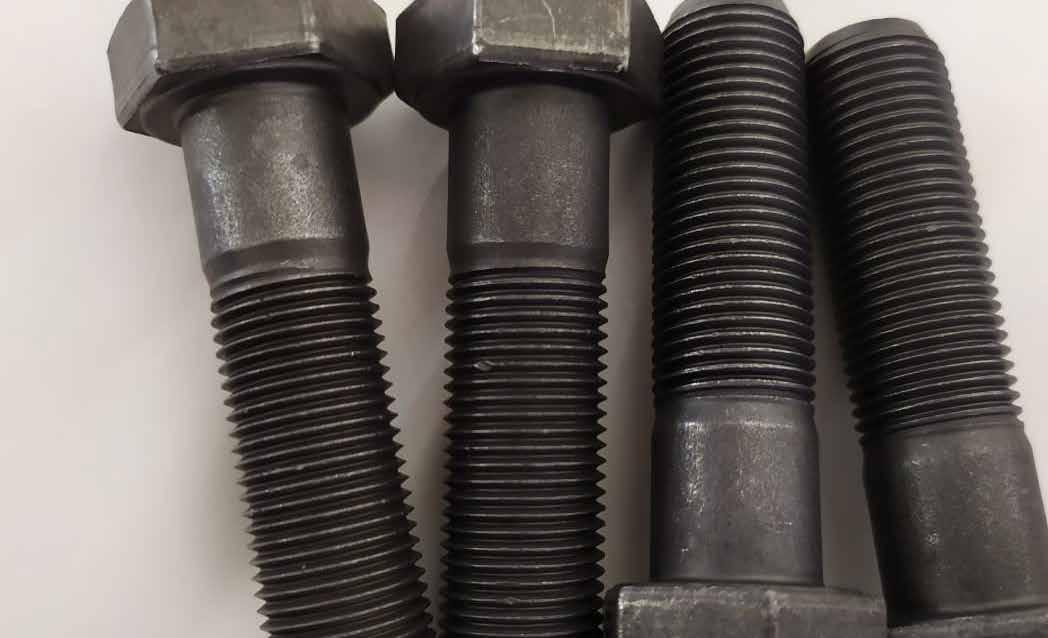
20 minute read
Refratários
Estudo da Influência da Ferrita Delta em Parafusos Tratados Termicamente na Resistência ao Torque
Leandro José de Almeida , Fernando Suzumura Kawata, Rafael Neves de Almeida, Lucelio Siqueira – Meritor O processo de Fabricação do parafuso tem como fluxo após vergalhão trefilado na usina, a conformação mecânica em dois estágios, sendo cabeça e corpo, assim como a região da rosca sendo conformada por usinagem, o processo num todo também consiste na utilização do fosfato de manganês para auxiliar no processo de conformação, desde o processo de trefilação dos vergalhões na Usina até o processo de conformação final dos parafusos. Para que os parafusos consigam atingir a resistência necessária para suportar carregamentos de torção, impacto e tração se faz necessário o tratamento térmico de Tempera e Revenimento. Antes do parafuso entrar no forno de Tratamento Térmico é extremamente importante que ocorra a desfosfatização, para garantir que o Fósforo residual presente na superfície do parafuso não difunda para o interior da peça e forme uma fase rica em Fósforo, com baixa resistência denominada Ferrita Delta. Com esse trabalho poderemos concluir se realmente a fase Ferrita Delta reduz a vida em fadiga com análise da Curva S-N e reduz também a resistência ao torque. A fase Ferrita Delta não somente é caracterizada pela análise microscópica, como também no MEV via EDS com a comprovação do elemento Fósforo, com isso vamos expor o parafuso a concentrações diferentes de fosfato de manganês em um mesmo tempo de forno na tempera e também com tempos de forno na temperas distintos em uma mesma concentração de fosfato de manganês. Assim vamos entender qual a variável que mais difunde a Ferrita Delta e após essa constatação, estudar não somente a fragilização devido a fase Ferrita Delta, mais também a relação de percentual/profundidade de Difusão de Ferrita Delta X resistência ao Torque.
Advertisement
Sabemos que uma falha de componentes em veículos pode originar um risco potencial ao condutor sofrer um acidente, para o próprio condutor ou terceiros. Parafusos para tal aplicação requer alta resistência quando utilizados em diferenciais de caminhões, e sofrem altas solicitações mecânicas, que se faz necessário processos de fabricação especialmente para obtenção de propriedades para que possam suportar esses esforços, aumentando sua resistência ao torque e a fadiga.
Históricos de falha de campo e linha mostram que o problema que tais parafusos apresentavam uma camada branca na superfície, camada com grande dureza e fragilidade. Analisando essa camada se concluiu que ela surgiu em função da presença residual de fósforo proveniente do processo de fosfatização de manganês, difundindo no aço durante o tratamento térmico de tempera.
A fosfatização de manganês é necessário, pois serve de ancoradouro agindo como um lubrificantes e outros redutores de atrito, facilitando assim, o processo de conformação mecânica a frio de trefilação entre outros. Se expormos o parafuso no fosfato de manganês, haverá a formação da fase frágil conforme Cioto et al. (2008), responsável pela falha prematura do parafuso quando observada em campo ou em processo de linha de montagem.
Com o já dito, objetivo deste Artigo é mostrar o efeito prejudicial da Ferrita Delta quando em solicitação mecânica, mostrando sua influência quando relacionado ao limite de resistência ao Torque em função do percentual e/ou volume de Ferrita Delta.



Gráfico 1. Diagrama TTT do aço SAE 9254, fonte: Tarim e Peres (2004)
Gráfico 2. Esboço do processo de tempera e revenimento utilizado nesse trabalho para Difusão da Ferrita Delta
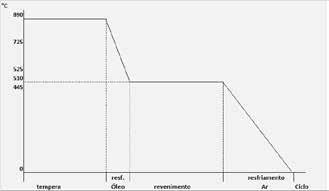
Fig. 2. Forno Tipo Mufla, com tanque de óleo para resfriamento

Referência Bibliográfica
Durante o processo de conformação mecânica algumas variáveis são de extrema importância, podemos considerar o Ishikawa para entender essas variáveis, algumas estão ligadas ao processo, como lubrificação, assim como também àqueles relacionados ao
Fig. 3. Preparação do corpo de prova para análise Metalográfica
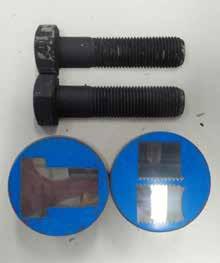
material como à qualidade da matéria prima, por exemplo, microestrutura do aço a ser conformado, propriedades mecânicas, etc. Se o material não estiver adequado a aplicação, isso pode levar a problemas como nucleação e propagação de trincas, redução de vida útil e fragilização no parafuso. Os processos de trefilação de vergalhões, extrusão a frio, forjamento a frio, etc. Estas operações que envolvem deformação a frio, em uma condição em que a transferência de calor e massa seja baixa, faz com que estas operações requerem uma boa lubrificação da superfície a ser deformada, sendo possível através da aplicação do fosfato na usina seguido da adição de sabão em processos de extrusão e trefilação. Sabões de trefila são reativos de estearatos alcalinos transformam a camada de fosfato de zinco em um estearato de zinco de alto poder lubrificante que adere à superfície.
O fluxo de conformação mecânica consiste de forjamento a frio e laminação de rosca, o parafuso estudado é de classe de dureza superiores a 22HRC e portanto, necessitam de serem submetidos ao tratamento térmico de têmpera resfriada em óleo e revenimento ao ar, porém, quando exposto ao fosfato e se obtiver resíduos de fosfato, o material após tempera acarretará a formação da fase delta (ferrita delta, Fe3P ou fosfeto de ferro), como mostrado na figura X, caracterizada como uma camada branca.
Em temperatura próxima de 723°C e durante a austenitização, o fósforo residual presente na peça conformada pode difundir para o interior do metal, formando essa fase frágil rica em fósforo. Em processos de fabricação de parafusos, para evitar a formação da camada branca é recomendada a remoção do fosfato com um tratamento de desfosfatização (desengraxante alcalino) antes do tratamento térmico de têmpera, principalmente em atmosferas descontroladas.
A fase estudada rica em fósforo difundida na superfície dos parafusos, apresenta alta dureza, por volta 45
Fig. 4. Amostra 1 - 1 minuto de exposição

Fig. 5. Amostra 2 - 2 minutos de exposição

Fig. 7. Amostra 4 - 4 minutos de exposição
HRC, com profundidades variadas, quanto mais resíduo maior a difusão e uniformidade da camada, reduzindo assim a resistência ao torque e a fadiga.

Materiais e Métodos
Inicialmente utilizamos parafusos classe 12.9 na liga SAE 4140, onde fizemos a exposição dos mesmos em banho de fosfato em diferentes concentrações.
Tratamento Térmico
A tempera do material foi realizada com resfriamento em óleo para analisar microscopicamente a relação do
Fig. 6. Amostra 3 - 3 minutos de exposição
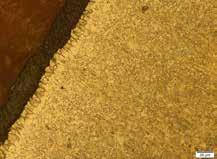
Fig. 8. Amoatra 5 - 5 minutos de exposição
tempo de exposição do fosfato X percentual e/ou profundidade de difusão da Ferrita Delta. Temperamos as peças conforme Diagrama abaixo, porém, dentro do faixa de transformação de Ferrita Delta.
Para o processo de Tempera e Revenimento, utilizamos um forno tipo Mufla.
Análises Microscópicas das Amostras de 1 a 6 minutos de Exposição em Banho de Fosfato de Manganês
Para as análises metalográficas, fizemos a preparação do corpo de prova com corte em cut of, seccionando o parafuso longitudinalmente, embutimento com termofixo baquelite em embutidora, desbaste em lixa #120, #400, #600, polimento em politriz com pasta de diamante e ataque químico com nital 2 a 5%.
Para caracterização da microestrutura, utilizamos um microscópio ótico Olympus, com objetiva de 50X e ocular 10X (500X).
Observado presença de Ferrita Delta uniforme e dispersa na Superfície do material, ataque nital 2%, estrutura Martensítica, aumento 500X (Fig. 4).
Observado presença de Ferrita Delta dispersa, porém de forma mais uniforme na Superfície do material, ataque nital 2%, estrutura Martensítica, aumento 500X (Fig. 5).
Observado presença de Ferrita Delta dispersa, porém de forma mais uniforme na Superfície do material, ataque nital 2%, estrutura Martensítica, aumento 500X (Fig. 6).
Observado presença de Ferrita Delta dispersa, porém de forma mais uniforme na Superfície do material, ataque nital 2%, estrutura Martensítica, aumento 500X (Fig. 7)
Observado presença de Ferrita Delta dispersa, porém de forma mais uniforme na Superfície do material, ataque nital 2%, estrutura Martensítica, aumento 500X (Fig. 8).
Dureza encontrada nos testes, conforme Curva de Gauss (Gráfico 3, 4, 5, 6 e Fig. 9)
Teste Mecânico
Após expor os parafusos em tempos diferentes de fosfato de 1 a 6 minutos e tratar termicamente para a difusão da
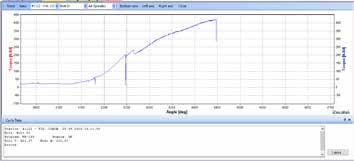
Gráfico 3. Dureza após tempera para amostras expostas em tempos diferentes no banho de fosfato de manganês


Gráfico. 4. 1 minuto de exposição no fosfato (condição de maior torque)
Ferrita Delta, testamos o torque.

Análise de Microscopia Eletrônica de Varredura (MEV)
Analisamos no MEV a camada de Ferrita Delta para comprovação da difusão do fosforo, mostrando que se trata realmente da Ferrita Delta e não de uma descarbonetação.
Conclusão
Os teste iniciais mostraram que existe uma redução de resistência ao torque quando exposto a tempos de fosfato maiores, ou seja, quanto mais uniforme a camada difundida a resistência ao torque tende a cair.
A resistência quando comparado entre 1 e 5 minutos caiu 56%, mudando também a curva de escoamento. Observamos também que existe um limite máximo de difusão do fosfato, acima de 5 minutos provavelmente a difusão se mantenha e a tendência seja a mesma na relação ao torque, se tornando um ponto de saturação da Ferrita Delta difundida no parafuso.
Sugestões para Trabalhos
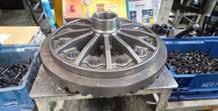


Gráfico. 5. 5 minutos de exposição no fosfato (condição de menor torque) Fig. 10. Superfície com presença de Ferrita Delta
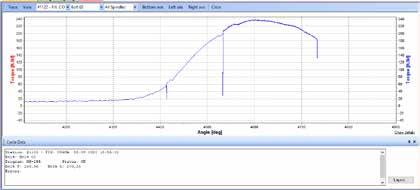
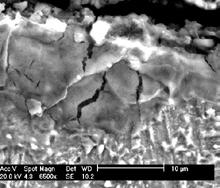
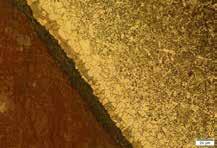
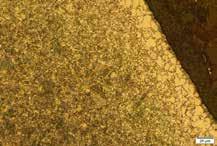
Gráfico. 6. Gráfico comparativo, torque x tempo de fosfato, imagens microestrutural mostrando a relação do tempo de exposição ao fosfato com a uniformidade da camada de difusão da ferrita delta
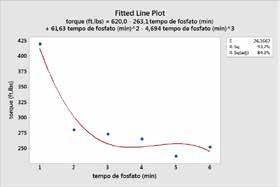
Futuros:
Para trabalhos futuros sugerimos fazer um comparativo, porém, indo mais a fundos nas propriedades mecânicas, avaliando também, o limite de resistência a tração e a vida em fadiga.
Referências
[1] CALLISTER, W.D. Materials science and engineering an introduction. 7thed. New
York: John Wiley, 2007. p.290-300. [2] CIOTO, R.; COLLARES, A.R.; ZUFFO,
C.H. The Effect of delta ferrita on the fatigue behavior of high resistance threaded fastener. Warrendale: SAE, 2008.
(Paper SAE 2008-36-0063E). [3] FORSYTH, P.J.E. A Two stage process of fatigue crack growth. In: CRACK PROPA-
GATION SYMPOSIUM, 1961, Cranfield.
Proceedings… Cranfield: Cranfield College of Aeronautics, 1961. v.1, p.76-94. [4] PANOSSIAN, Z. Fosfatização dos metais ferrosos. São Paulo: ABM, 2007. p.5080. [5] COLPAERT, H.; COSTA, A.L.S. Metalografia dos produtos siderúrgicos comuns. 4.ed. São Paulo: Edgard Blücher, 2008. p.409-416. [6] SURESH, S. Fatigue of materials.
Cambridge: Cambridge University Press,
Fig. 18. Cristais de fosfato na superfície da peça e EDS para caracterização da presença de fósforo, Aumento 700x

1991. TARIN, P.; PEREZ, J. Stecal 3.0. Materials Park: ASM International, 2004
Agradecimentos a Isac Ponciano, Técnico em Metalurgia. Metaltork, Cortesia dos Parafusos. Meritor, Dos testes e análises.
PARA MAIS INFORMAÇÕES: Contate Leandro
José de Almeida, Engenheiro Metalúrgico. Fernando Suzumura Kawata, Supervisor Qualidade. Rafael Neves de Almeida, Tecnólogo em Metalurgia.
Comparando o Isolamento de Manta de Grafite de Forno a Vácuo - PAN vs. Rayon

Reàl J. Fradette and William R. Jones – Solar Manufacturing, Inc.; Souderton, Pensilvânia, EUA
Amaioria dos fornos a vácuo atualmente ativos no mundo do tratamento térmico incorporam alguma forma de, ou combinação de, isolamento de manta de grafite, com revestimento interno de folha ou placa na construção de zona quente do forno. A manta de grafite usada em fornos de alta temperatura é à base de PAN ou de Rayon. O grafite PAN (poliacrilonitrila) é o mais usado, pois é aproximadamente 20% mais barato do que o isolamento à base de Rayon. A Solar Manufacturing conduziu recentemente testes de cada material para conservação de energia e desempenho do ciclo, a fim de determinar os benefícios de cada tipo de manta quando usado em fornos a vácuo. Este artigo apresenta nossas descobertas.
Performance Térmica
Os testes foram realizados para avaliar a eficiência térmica relativa dos dois materiais de manta de grafite usando um de nossos fornos de laboratório. Este forno vertical possui isolamento todo de grafite e uma zona quente utilizável medindo 30 cm de profundidade x 45 cm de altura. Modificações foram feitas no forno, incluindo uma extensão superior, que fornece espaço suficiente para variar a espessura da cobertura da zona quente superior. Isso também permitiu espaço suficiente para a colocação do termopar.
Duas tampas da câmara superior foram criadas, uma com quatro
Tabela 1. Efeito do tipo de manta na perda de calor para a parede fria do forno a vácuo Tipo de Manta Manter 955˚C Manter 1093˚C Manter 1233˚C
Manta de grafite PAN Manta de grafite Rayon Melhoria térmica Rayon vs. PAN 254˚C 235˚C 6.93% 301˚C 284˚C 5.22% 348˚C 324˚C 6.52%
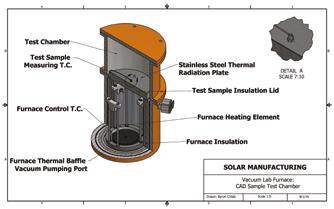
camadas de manta PAN de 1,27
Parede da câmara externa Parede da câmara interna
‘A’ ‘B’
Transferência de aquecimento
Elementos de aquecimento Refrigeração a água
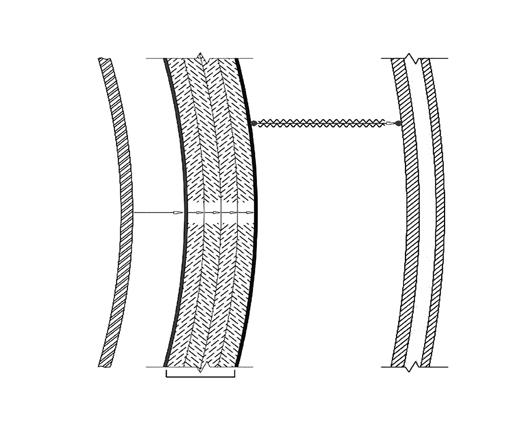
Desenvolvimento de anel (aço inoxidável 304)
Face quente (0,090” grafite)
Manta de grafite (4 camadas) Fig. 2. Superfícies de radiação em um forno a vácuo resfriado a água
Tabela 2. Perdas de energia em temperaturas de manutenção
Manta de grafite da zona quente Grafite PAN Perda a 955˚C
25.56 kW Perda a 1093˚C
37.85 kW Perda a 1233˚C
53.50 kW
Grafite Rayon Melhoria - Rayon sobre PAN (porcentagem) 21.50 kW
15.88% 33.06 kW
12.65% 45.05 kW
15.79%
Tabela 3. Propriedades químicas e físicas de produtos de feltro para isolamento de forno a vácuo
Propriedades
Densidade aparente (g / cm3) Manta de grafite PAN
0.10 Manta de grafite Rayon 0.08
Conteúdo de carbono (%)
Conteúdo de cinzas (%) Temperatura do processo (˚C) >99.5
0.05
2400 >99.9
<0.01
2500
Tabela 4. . Medições de “α-case” (alpha-case) para o teste de
contaminação por umidade
Tipo de isolamento
Isolamento de manta PAN Profundidade da alpha-case (polegada x 10-2)
.319
Isolamento de manta Rayon Zona quente totalmente metálica .250
.216
cm e outra com quatro camadas de manta Rayon de 1,27 cm. Um termopar foi acoplado a ambas as tampas em aço inoxidável da câmara, simulando a temperatura de irradiação no anel de suporte externo de um forno padrão (Fig. 2, ponto A).
A Tabela 1 mostra as temperaturas relativas registradas em cada uma das tampas de grafite quando mantidas em temperaturas elevadas. A tabela ilustra a eficiência térmica superior do Rayon em relação ao PAN em aproximadamente 6%. Nossos resultados representariam o ponto A na Fig. 2 irradiando para o ponto B da parede da câmara.
Embora isso destaque uma melhoria na temperatura da superfície radiante em um pequeno arranjo de teste, a importância de diminuir a temperatura da superfície radiante A torna-se aparente ao usar um forno a vácuo de produção típico com um tamanho de zona quente de 92 cm de largura x 92 cm de altura x 122 cm de profundidade e aplicando dados da Lei de Stefan-Boltzmann para Radiação (Equação 1).
O segredo é que a temperatura da superfície radiante seja elevada à quarta potência. Pode-se calcular a perda de energia geral esperada em cada temperatura de retenção (Tabela 2) para comparar as perdas de energia para cada pacote de isolamento. Com base nos dados de teste, o pacote de isolamento Rayon é termicamente mais eficiente em termos de energia do que o PAN em aproximadamente 15%.
P = θσ A (T4 - T c 4) [1]
• P = potência irradiada líquida • θ = Emissividade da superfície radiante (usado 0,55 para SS) • σ = Constante de Stefan - 5,6703x10-8 watt / m2K4 • A = A área de superfície radiante • T = Temperatura da superfície radiante (graus Kelvin) do anel de suporte • T c = temperatura da superfície circundante (graus Kelvin) da parede da câmara
De acordo com esses dados, a manta Rayon também tem um desempenho muito melhor do que o PAN ao executar ciclos com longos patamares em temperaturas elevadas.
Desempenho do Ciclo
A eficiência térmica é importante. No entanto, no processamento a vácuo, deve-se também considerar o efeito geral de um projeto de isolamento no tempo de ciclo e nos contaminantes residuais que podem afetar a pureza da peça. Se um projeto requer um bombeamento extensivo que estende os tempos de ciclo gerais, isso pode ser prejudicial ao custo de execução do processo.
Mais importante, se o projeto de isolamento libera gases residuais indesejados durante o processo de tratamento térmico, ele pode contaminar certos metais, resultando em contaminantes de superfície indesejados.
1.OE-03 Vácuo nível (torr) Pan felt Rayon felt
1.OE-04 Vácuo nível (torr)

1.OE-05 0 200 400 600 800 100 1200 1400 Tempo (seg.)
Fig. 3. Teste de bombeamento de comparação
Uma revisão das propriedades da manta de grafite PAN para a manta de grafite Rayon sugere que cada pacote de isolamento pode ter um impacto diferente no desempenho do bombeamento, devido às diferenças na densidade e no conteúdo de cinzas (Tabela 3).
Para testes de desempenho, fabricamos 10 peças de 34 cm de diâmetro de PAN e materiais de manta de Rayon. Também substituímos a tampa padrão de outro forno de laboratório semelhante ao forno mostrado na Fig. 1 por uma configuração de 10 camadas de cada tipo de manta para simular a área de superfície efetiva da manta em um forno de produção maior. Antes do teste, todas as amostras de manta foram submetidas a um processo de cozimento em vácuo profundo até uma temperatura de 1315˚C e mantidas por uma hora. As amostras resfriadas no forno foram colocadas em sacos selados separados para minimizar quaisquer efeitos devido à umidade.
Os testes foram conduzidos em um forno com uma zona quente totalmente metálica usando a mesma peça de extensão, conforme mostrado na Fig. 1. A utilização de uma zona quente totalmente metálica para esses testes garantiu que qualquer contaminação e problemas de bombeamento fossem o resultado das peças de cobertura de teste de manta somente e não do uso de manta em um forno de laboratório padrão todo de grafite. Conforme mencionado anteriormente, cada pilha de tampas de 10 peças de PAN ou manta de grafite Rayon foi apoiada em uma placa de molibdênio. O seguinte ciclo de tratamento térmico a vácuo foi executado para cada teste. 1. Registre a temperatura ambiente, umidade e ponto de orvalho antes de iniciar o ciclo. 2. Bombeie o forno para atingir 5 x 10-5 Torr. 3. Rampa a 10˚C por hora para atingir 1232˚C.
3
2 Nível de vácuo x 10-5 2.5 1.5 1 Pan 0.5 Rayon Moly 0 5 15 25 35 45 55 65 75 85 Tempo (seg.)
Fig. 4. Curva de desempenho de vácuo
4. Segure a 1232˚C por 30 minutos. 5. Resfriamento estático de nitrogênio a -5 polegadas HG a 54˚C. 6. Remova a tampa de isolamento e deixe-o em ar ambiente por 60 minutos. 7. Registre a temperatura ambiente, umidade e ponto de orvalho. 8. Coloque a tampa de grafite de volta no forno. 9. Bombeie para 1 x 10-5 Torr e registre o tempo de bombeamento. 10. Aterre e descarregue o forno.
Um registro completo do nível de vácuo alcançado e o tempo geral para atingir o vácuo registrado é mostrado na Fig. 3. Embora não seja aparente que as curvas no gráfico mostrem uma diferença significativa no tempo de bombeamento ao calcular a taxa de bombeamento, se encontra uma melhoria de aproximadamente 20% no desempenho do vácuo para Rayon em comparação com PAN.
Teste Revisado de PAN/ Rayon
Ao trabalhar com fornos a vácuo isolados com manta, a captação de umidade pode se tornar uma fonte importante de contaminação por oxigênio. Para fins de teste, cada pilha de manta foi deixada na atmosfera da fábrica por 1012 horas antes de ser colocada no forno. Conforme descrito abaixo, o ciclo do forno para cada pilha foi executado com uma peça de teste de titânio limpo incluída no forno. Após cada execução, a análise da “α-case” (alpha-case) por meio de avaliação metalúrgica determinou o nível de contaminação da captação de umidade para o isolamento PAN e Rayon em comparação com uma zona quente totalmente metálica limpa.
O ciclo do processo para esses testes foi o seguinte: 1. Registre a temperatura, umidade e ponto de orvalho antes de carregar o forno. 2. Adicione a extensão do forno. 3. Coloque a peça de teste de titânio no forno. 4. Coloque a tampa modificada com 10 camadas de PAN (ou Rayon). 5. Registre qual manta está em execução. 6. Feche o forno e inicie o ciclo. 7. Bombeie para 5 x 10-5 Torr antes de iniciar o aquecimento. 8. Aqueça a 15˚C / minuto a 955˚C e mantenha por uma hora. 9. Registre o desempenho de vácuo / temperatura ao longo do ciclo. 10. Encha com nitrogênio e resfrie o forno à temperatura de sua abertura. 11. Remova a tampa de grafite e a peça de teste de titânio, identificando-a como o teste PAN ou Rayon.
Quando comparados com a zona quente padrão totalmente metálica, os níveis de vácuo para cada pacote de isolamento (Fig. 4) mostram níveis de vácuo menos eficazes, indicando a presença de mais gás residual. Devemos observar que a umidade e o ponto de orvalho eram consideravelmente mais altos na data do teste Rayon do que na data do teste PAN. Com este fato em evidência, o resultado na Fig. 4 indica que o isolamento PAN é muito mais sensível à captação de umidade do que a manta à base de Rayon.
As medições de “α-case” resultantes (Tabela 4) também apoiam esta conclusão, considerando que a amostra de titânio usada no teste de isolamento Rayon produziu um resultado de “α-case” semelhante à zona quente totalmente metálica, embora a pilha de manta Rayon sofreu umidade mais severa do que amostras de teste PAN.
Vantagens / desvantagens de trabalhar com esses materiais de feltro Três coisas ficaram imediatamente evidentes ao trabalhar com a manta de grafite PAN. 1) O material desfiou ao ser cortado, deixando bordas irregulares. 2) O material estava muito sujo de manusear. 3) O material não tinha espessura uniforme, dificultando o empilhamento.
A manta de grafite Rayon era o oposto completo. 1) Era fácil de cortar no tamanho certo e não desfiava nas bordas. 2) Era muito mais limpo de manusear. 3) Era muito mais liso e estava bem horizontal e empilhado.
Com base nisso, Rayon é a manta preferida do ponto de vista da fabricação.
Conclusões
A Solar Manufacturing determinou que a manta Rayon será o isolamento selecionado em seus projetos de fornos futuros com base nas seguintes conclusões. • A manta de grafite Rayon, quando usada corretamente, pode ser até 20-30% mais eficiente em termos de energia quando comparada à manta de grafite PAN. Esta pode ser uma vantagem definitiva para os fornos com ciclos de processo que requerem longos períodos de espera em temperaturas elevadas. • A manta de grafite PAN tem mais conteúdo de cinzas do que a manta Rayon, o que pode afetar os resultados da superfície do produto. • A manta de grafite Rayon demonstrou características de liberação de gás mais baixas do que a manta PAN, resultando em níveis de vácuo melhores e mais rápidos. • A manta de grafite PAN teve um efeito mais drástico em uma amostra de titânio em relação à formação indesejada de “α-case” do que a processada com a manta de grafite Rayon. • A manta de grafite Rayon tem um preço aproximadamente 20% mais alto do que a manta de grafite PAN, portanto, a economia é uma consideração em um projeto de zona quente de forno a vácuo. • A Solar Manufacturing padronizou a manta Rayon para menor consumo de energia e melhor desempenho de vácuo.
Citações Disponíveis Online
PARA MAIS INFORMAÇÕES: Contate Reàl J. Fradette, consultor técnico sênior, Solar Manufacturing, Inc., 1969 Clearview Rd., Souderton, PA 18964, EUA; tel: +1-267-384-5040; real@solaratm. com; web: www.solaratm.com.