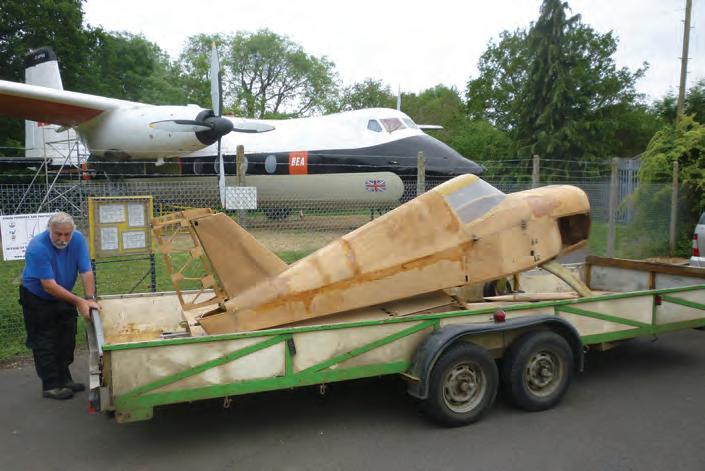
4 minute read
LETTERS
We are always pleased to receive your letters and feedback. Please email the editor at bfjjodel@talktalk.net
Above Alan Turney delivers the uncompleted JG3 to the Museum of Berkshire Aviation
Racer donation
The Museum of Berkshire Aviation has recently acquired a ‘Midget Racer JG3’ donated courtesy of Steve Slater and the LAA. The aeroplane was designed and entered for the Rollason Midget Racer Competition in the early 1960s, the two winning entries of which were the Luton Group Beta, in first place, and the Taylor Titch in second.
Our aeroplane, the Goodwin JG3, designed and built by C J Goodwin, was never completed, but was later acquired by David Kent, who undertook further work but it remained incomplete.
It is believed there was an instruction to burn it, however, as David Kent did not wish it to meet such a fate, it was secreted away. There was a pile of wood remaining and this was set on fire, so the aircraft was thought to have been destroyed! More recently the aircraft was donated to the LAA by David’s son Mike.
Francis Donaldson (LAA) has been helpful in providing info about JG3 and believes he has some more documentation he can let us have.
Alan Turney (Midland Aeroplane Company) kindly delivered JG3 to our museum on Monday 7 June (above).
If anyone has any further information about JG3, we would love to hear from them.
Regards, Dave Scott (Museum of Berkshire Aviation).
Cylinder Conundrum…
Hi Brian. Ruth Kelly’s really helpful article in the July edition seemed to miss out on one of the most useful features of the leak-down test: that, when a cylinder is leaking, it’s easy to pin down the source of the leak. Listening to the exhaust pipe (exhaust valve leak), the air cleaner (inlet valve) and crankcase breather (piston/rings/bore) gives a real clue as to where to look deeper.
After many years of coping with a sometimes-awkward C90, and eventually fitting four new cylinder kits (huge thanks Adams) we learned a few things. One is that leaking exhaust valves are only ignored for so long – they don’t get better. Removing a valve cover and tapping a leaking valve will often restore a good seal if it’s merely a carbon deposit. Also, that the engine can perform nearly 100% (as shown during check flight climb test) with leak-down pressures somewhat below 40psi!
Kind regards, Dave Smith.
…and again
Dear Editor. This was an excellent article and a very useful introduction to a very valuable check of engine condition. It does, however, require the aircraft owner to beg/borrow/steal a differential test set, or suggest to his/her patient partner that it would make a great Christmas present.
I would like to suggest that there are a couple of further procedures that may reveal a little more about the condition of the engine.
If the test set shows a leak-down pressure of 60 psi or less, I have always regarded it is then the time for investigation. Carrying out the test while the engine is hot often gives better results than when the engine is cold.
Pressure will be lost either due to a worn/damaged exhaust valve, leakage past the piston rings, or because of a damaged cylinder (as was the case in Ruth Kelly’s article).
With the test set connected, a leakage past the exhaust valve may be heard by sticking an ear (carefully) over the open end of the appropriate exhaust pipe (not when it is hot of course!). If the valve is worn/ damaged, then you will hear the sound of air leaking past the valve. The noise level will give some idea of the severity of the problem.
Exhaust valves live a pretty tough life whereas inlet valves rarely give trouble.
If exhaust pipes are joined, then leakage may still be detected by listening at the final open end.
Leakage past worn or damaged piston rings may be heard by listening to the open end of the crankcase breather, as air passes the rings and enters the crankcase to vent via the breather. As before the seriousness of the problem may be indicated by the level of sound.
A damaged cylinder may not be so easily detected but a low reading and an excessive level of sound may call for the cylinder to be pulled in any case.
A final note of caution. The cylinders on most Lycoming and Continental engines are quite large and applying 80 psi will generate a very strong rotational force. It is strongly recommended that one person hangs on to the prop at TDC, keeping out of the propeller arc, while the other carries out the check.
Kind regards, Mike Powell.
Editor’s note: Thank you, Dave and Mike, for the additional information on the leak down, which I know many members have for years relied on as the benchmark for cylinder condition. My concern – not that I’m losing sleep over it – is that since the 1980s, Continental, and many independent engineers, have brought the test into question as the sole arbiter of cylinder diagnosis. They maintain that air leaking past the piston or a valve, does not necessarily mean they are defective.
They recommend that a borescope, which these days can be purchased at reasonable cost, gives a far more accurate picture of a cylinder’s health.
I would certainly welcome an article on borescope use and understanding of the indicators that removal of the cylinder really is necessary. ■