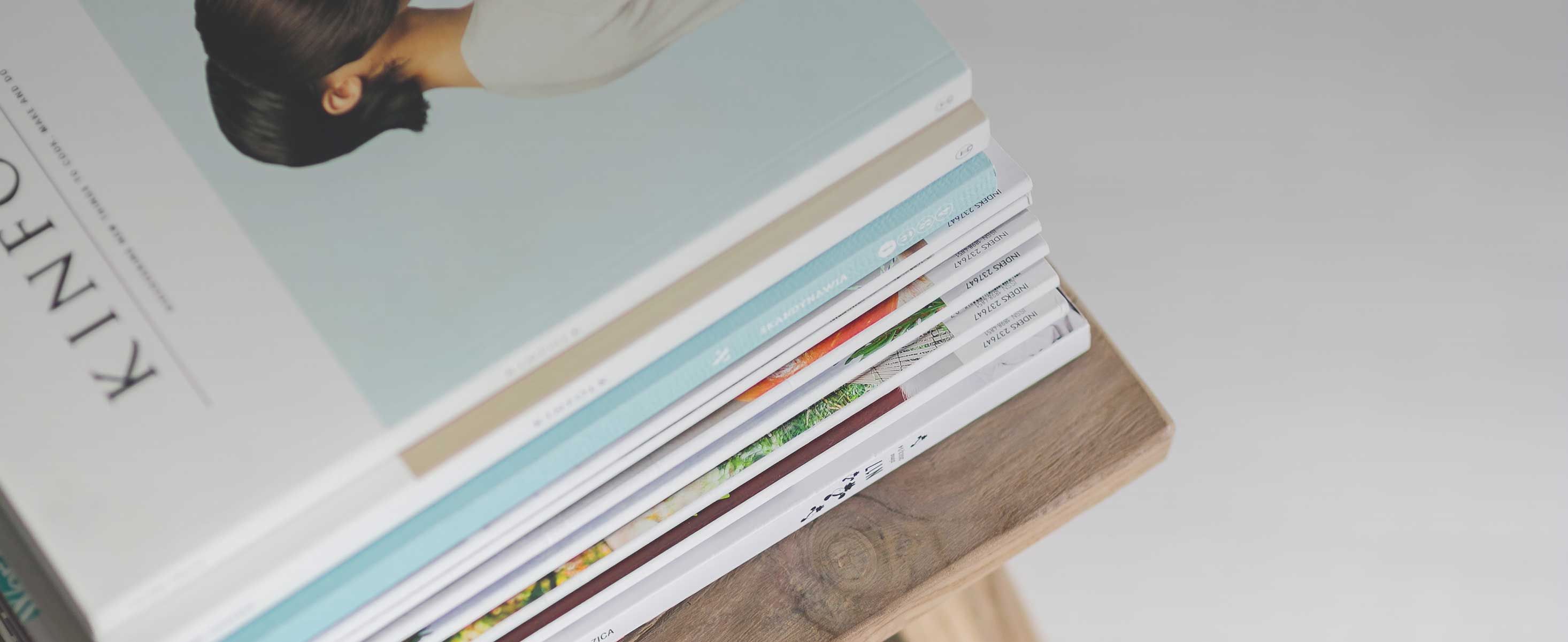
8 minute read
Letters
We are always pleased to receive your letters, photos of your flying, and your feedback. Please email the editor at ed.hicks@laa.uk.com
Avgas 100LL Dear Steve,

We have been discussing the recent alarmist article in the Daily Telegraph (Ed – on 100LL), and the academic paper from the University of Kent upon which it was based.
As you probably know, Ian (Fraser) flies an RV-6 with a Lycoming O-320, which runs well on UL91. Ruth (Kelly) flies an RV-8 with a 200hp high-compression IO-360, which has not been approved to use unleaded fuel, and so uses 100LL. Both aircraft are based at Henstridge. We are both engineers, and enjoy discussing technical issues and putting forward articles and items for discussion.
Having reviewed the original academic paper we can see that there are flaws in its data: where there are deficiencies in the sources, the authors have erred on the side of higher risk in a number of key areas (underestimating both the proportion of GA aircraft that are able to use unleaded fuel, for example, and the availability ofUL91 and the use of mogas).
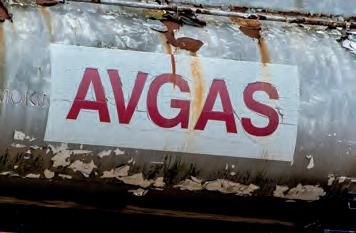
However, we agree that doing nothing is not an option. While the UK remains the only manufacturer of TEL, we do not refine avgas in the UK, and our main source – France –will presumably be ceasing production in 2025. The possibility of a lead-free replacement for 100LL from the USA is tantalising, but likely to be very expensive.
What to do? It seems to us that there are two options: change the fuel, or change the engines. We assume that there is little that can be done to expedite the appearance of 100UL. But perhaps more could be done towards getting approval for Ruth’s engine – and others like it – to use unleaded fuel?
Both the Lycoming 320 and 360 series have high and low compression variants. For the 320s, both variants are approved to use unleaded fuel. On the face of it there should be nothing to prevent the high-compression 360 running on unleaded fuel, except perhaps when leaned at full throttle. After all, the engine components are all essentially identical to those in engines approved for UL91.
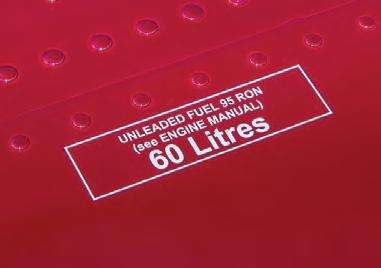
Is there an opportunity here for the LAA to sponsor some academic research and testing to examine the problem, and establish whether or not it may be feasible for more engines to use UL91 than are currently approved? The issue, of course, is preventing detonation. Leaning limitations, ignition timing, rpm limits and octane-increasing additives are all possible areas for investigation – all successfully applied in the car world following the demise of five-star petrol. It may be that relatively simple interventions could solve or at least alleviate the problem. We just need to base these on some solid research and testing. It would also enable us to report that something is being done. Ruth Kelly & Ian Fraser.
Steve Slater, CEO, replies: I share your concern and I have been working with Malcolm Bird at AOPA and the DfT on this for a while, although prior to the Telegraph article their focus on it diminished after Grant Shapps and Robert Court moved on from their ministerial positions.
The Telegraph article, despite, as far as I am concerned, its several inaccuracies has actually worked in our favour in focusing attention on the challenge. I am trying to set up a meeting with DfT, AOPA, fuel and engines suppliers to look again at the options available and the options for assistance in funding. The next LAA Board Meeting is at the end of January, and I am copying in our chairman and the chair of the Airworthiness oversight group as I anticipate a discussion of possible actions at that meeting.
Learning the lessons, moving forward
Dear Editor,
Harry Cook’s letter (January 2023 Light Aviation) makes some very pertinent points. I too had seen no expression of contrition on the part of those responsible for the loss of members’ funds until the Chairman’s contribution to Straight and Level in the January edition of Light Aviation
However, it is to the LAA’s credit that Harry’s letter was published. It was obviously influential in eliciting the welcome if overdue apology.
The establishment of a forum, which will enable members to engage with the Board, is a positive development. My hope is that in the course of discussions, nothing will be off limits and that both members and the Board will engage constructively in this process.
Two other suggestions for the Board’s consideration:
Externally accredited Quality Systems, such as those already established within Engineering Services, are appropriate and beneficial to customer focused services in general. Consideration should be given to extending the system to encompass the whole of the LAA activities. Such a system would have included financial security procedures which would have minimised the likelihood of successful fraudulent activities.
Secondly, the LAA website shows that the organisation employs 19 staff with service delivery roles and 12 directors. Of these 12, five have no stated role other than that of ‘director’. In both public and private sector organisations, in addition to their strategic leadership roles, directors generally have clearly specified particular responsibilities for the oversight of key corporate goals, organisational governance and service delivery. This often requires an ability and a willingness to act as an independent voice and a ‘critical friend’ within their organisation.
If the LAA is to fully and permanently learn the lessons of this debacle, all directors should be required to make significant individual contributions to the corporate governance, development and growth of the LAA.
Regards,
Dr Chris Callicott.
As reported, the Board has reviewed fully our processes in line with the recommendations of the Panel Review and will consider what additional quality systems or reviews may be appropriate to implement.
LAA directors are expected to make significant individual contribution to the functioning of the Association based on the considerable experience and skills they bring to the Board and upon which they were elected by members. The main standing committees are chaired by directors and we will look to report on their activities over the year and at the AGM.
Fees increase Ed,
The January issue announced increases in membership and permit fees as a means of ‘balancing the books for 2023’, but failed to shed any light on the reasoning behind the proposed changes. Presentation of 2022 income and expenditure in percentage terms rather than actuals is unhelpful, but when engineering income is declared, but engineering outgoings are not, an appropriate justification or otherwise of the proposed increases in membership and permit fees relative to other engineering fees is impossible. My experience of mod and repair charges leads me to the conclusion that these must be subsidised by other charges. The suggestion that an increase in initial fee from £60 to £145 would pose ‘a serious safety risk in discouraging owners from making applications and drive work underground’ is offensive and insulting to those engaged in repair or modification of their aircraft. The extent to which any such risk exists is more likely driven by an engineering function which cannot respond in a timely and effective manner to those applications which are made.
Every operator, builder or restorer of a permit aircraft has a huge interest in an appropriately staffed, responsive and effective engineering function. We are told that existing staff in Engineering struggle to provide a satisfactory service and that the Association faces problems of recruitment and retention of staff. We are not told what an appropriate staffing level is considered to be nor what an appropriate budget would be to attain this level. Without this information any changes in engineering fees are a sticking plaster solution to these issues. One hopes that the Board has done the necessary homework.
There are frequent references from our CEO and Chairman to openness and transparency – features notably lacking in the past. If the management was to share meaningful information on projected staffing and proper costing of the various engineering activities it may find the membership are much less timid in addressing any necessary changes in fees than they have been so far. Malcolm Rogan.
PS: In my past business life reporting 9.9 % of expenditure (in this case approx £150,000) as ‘other’ would never be considered acceptable. It suggests something hidden. We should be told.
Steve Slater replies: Malcolm is welcome to raise these points, but I am a bit surprised that he claims that we are not transparent. The presentation in last month’s magazine, as well as presentations at the AGM and our annual detail run down in Light Aviation in the middle of each year gives us a much higher level of sharing accounts information than most other associations. We’ve been sharing this information with members since 2015.
Of course, the limitations of space do mean we can’t break down all the details, but in answer to his query on miscellaneous expenses, these include extra freelance resources for training, engineering support, quality management etc., bank and credit card charges, asset depreciation, board expenses, donations to outside bodies such as Royal Aero Club and GASCo, costs for advocacy on airfield protection and airspace, and irrecoverable VAT, to name just some. These are all, of course, properly accounted for and budgeted – there’s simply no room to show them on a small pie chart!
Woodcomp propeller bolts

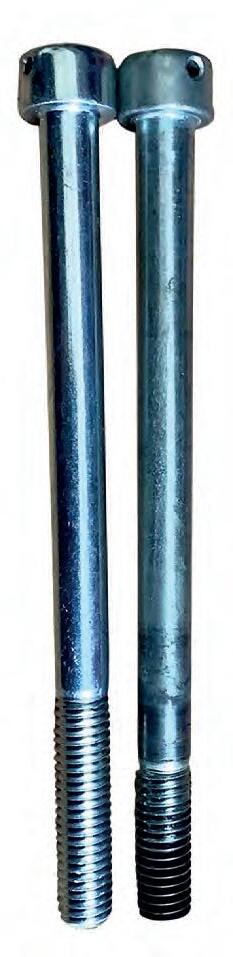
I would like to offer some background to the section attributed to me, regarding propeller mounting bolts in the Engineering Matters section in the January edition.
In August last year while replacing the gearbox on my 912ul I decided it would be a good time to also replace the mounting bolts on my Woodcomp Klassic which had been in use for several years.
When the new bolts arrived I was surprised to see that while they were of the same type and length as the original bolts supplied by Woodcomp, the threaded length was much greater, such that the plain shank no longer passed into the engine drive plate.
This meant that the shear load at the drive plate/prop boss interface was being taken on the much weaker thread root diameter instead of the full plain shank diameter.
My engineering qualifications include materials and stress analysis and I was always aware that setting up a shear possibility in this way was bad engineering practice and I could see no engineering
Left Woodcomp propeller bolts. Also see the update in Engineering Matters on page 26 justification for the change. Therefore I rejected the bolts and returned them to the UK agent for Woodcomp. rejected using plate
I was also aware of the incidents in the past where Shadow aircraft using Rotax 582/ Precision props had suffered loss of the propeller, when the bolts sheared having been fitted with the shear plane load on the threads in a similar, although not identical, manner in that the bolts were threaded into the drive plate and locked with a stiffnut.
Again, I had occasion to oversee the replacement of mounting bolts in a Rotax 503/Ivoprop set-up where a previous owner had fitted bolts such that the plain shank did not pass through the spacer and resulted in the threads bearing on the engine drive plate, and the wear on the threads at that point was so significant that vibration was being experienced. Replacing these with the correct length of bolt immediately solved the problem.
I contacted Woodcomp Cz directly, firstly to ask why it had changed the bolts to the shorter plain shank version, but also to see if I could be supplied with the original specification bolts.
Its response was: ‘This fact has no effect on the safety of installing the propeller on the engine, as the screw is under tension and the torque is transmitted by friction between the engine flange and the propeller head’. It made no mention as to why it had changed from the original specification.
While their statement is true in theory, in practice there are many reasons to doubt the friction grip as being adequate at all times, For example if the torque is measured at the bolt head and not at the nuts then the friction between the bolt and the holes may significantly affect the result. Again if the bolts are torqued up, say, in winter, will there be the same grip in a high temperature summer?
And of course there is the simple human mistake of using the wrong torque setting or procedure. The bolts themselves may then be carrying some of the load and are in shear. Is it worth the risk?
I put these points to Woodcomp Cz and they have indicated that they understand my concerns, and will source and supply me with the original specification bolts.
It will be interesting to hear what others make of this issue. Keep up the good magazine, well worth the monthly read.
Dave Whitelaw, LAA Inspector and BMAA Senior Inspector.