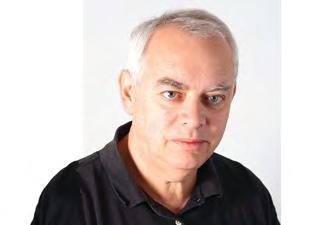
15 minute read
PROJECT NEWS
Projects which inspire others to build their own aircraft Compiled by Mike Slaughter
Project News
Thus far, or at least to mid-January anyway, the weather has been very mild and most conducive to project tasks in the workshop. However, in the UK at this time of year, mild equals wet and I know many newly finished projects have suffered from waterlogging delaying those early test flights.
I am very fortunate to have a generous double garage to go and fettle in, but recently I realised it is not the space it once was. Decades of domestic storage, one aeroplane too many, not to mention a growing collection of tools and materials, have turned it into the inverse of the Tardis. Over time, the art of keeping the place tidy has improved to a point where although it has multiplied, the ‘stuff’ is condensed into the same volume. Now though, a task cannot be commenced without moving ‘stuff’ from A to B and perhaps subsequently from B to C. Stuff has to go and I need to see the brick walls again. Less would definitely be more – space!
Clearly, I should consider myself lucky and just get on and de-clutter, Graeme Bird has managed to complete and spray his project in a space less than seven feet wide. Originally begun in 1995, it's another Europa project that has come out of the shadows and rapidly progressed to flying stage – progress can be rapid when you have built one before. You can read his story below. It’s a common dream to one day build and fly one’s own aircraft, often the catalyst being the construction of balsa flying models when younger. David Lawry initially satisfied that itch assembling a Jabiru nearly 20 years ago, but considering that to be a full-size Airfix model, he has now gone on to plans build a lovely little Luciole, almost now satisfying the building itch.
Andrew Beggin not only needed to satisfy that building urge, he also needs to get on and complete the training for his licence to fly the very capable Sling 2 that he has now finished. I think he is finding his PA-28 training aircraft to be in a different league to the modern ‘starship’ he has created.
To get in touch with Project News, and tell your story, report a milestone or just to send a picture, email: projectnews@laaarchive.org.uk. Please share your story!
G-PATS (PFA 247-12888) Europa
By Graeme Bird
Iacquired the project, a Classic 80hp Monowheel, from the original owner in December 2018 and the Permit to Test was issued at the beginning of December 2019. Rather unfortunately, the original local owner was unable to continue the build due to illness, but I was able to finish the aircraft with his continued involvement, mostly in the form of visits coinciding with inspections. However, there were challenges charting specifics of the project’s history due to elapsed time and his condition. The flying surfaces were all constructed but still required finishing and preparation for painting. The fuselage had been joined but some remedial work was required internally, rather fiddly with the two halves already mated! It also needed to be fully prepared for painting. So, the tasks were to bring her up to mod standard, finish filling and sanding, paint, interior, cowlings, doors and glazing. Then on to the firewall forward, fuel system, wiring, dash and instrumentation. At the beginning of my involvement, no single phase of the build had been completely finished.
One overriding focus was to bring the project back to the build book, with the addition of numerous but only standard mods in order to smooth the paperwork burden and final LAA release to flight. The goal of the instrument fit has been simplicity and reliability with conventional engine dials, pitot and static instruments. A battery-backed Garmin G5 provides an EFIS and Attitude Indicator, a Garmin AERA 600 is the main GPS unit with an iPad for SkyDemon moving map and a traffic feed from PilotAware. An obsession on fuel state is shown by the inclusion of sight tube, tank gauge and differential flow computer. The interior is painted with Nextel suede paint and upholstery is simple shaped and covered Dynafoam seat and back cushions.
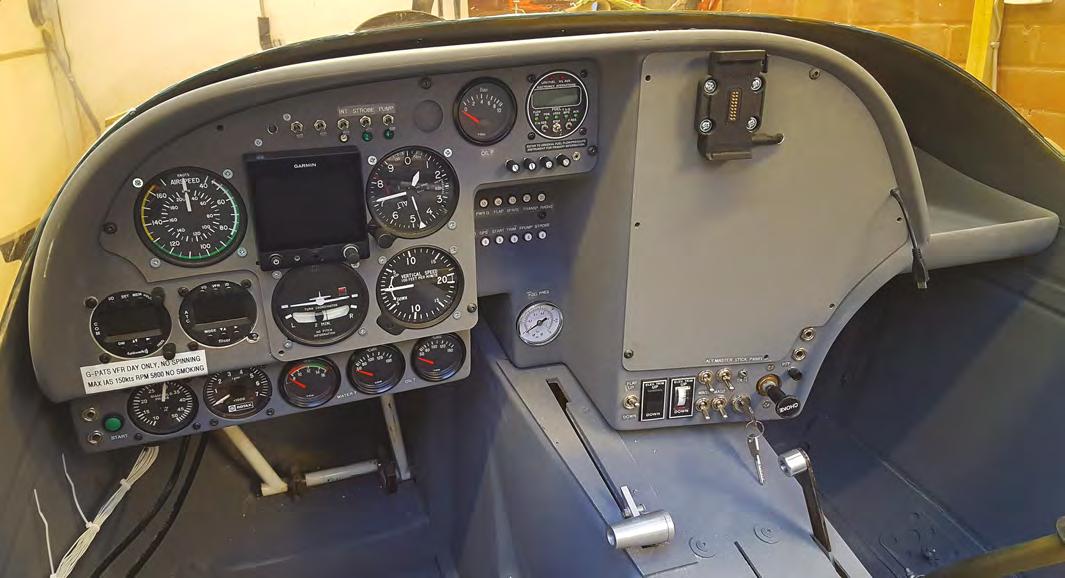

Above The dash finished and installed into the aircraft. Photo: Graeme Bird
Left A beautiful winged creature emerges from its cocoon workshop. Photo: Graeme Bird
Below It can be seen here just how little space there was in the lean-to as Graeme’s wife Carol helps attach the registration. Photo: Graeme Bird
Possibly the most unusual aspect of this project has been the restricted workspace. My primary workshop has been a lean-to down the side of our house. It measures only 2.1m x 6.2m and doubles as a spray booth. A trailer on the drive was used for storage of parts that were not being worked on. The driveway also hosted several trial assemblies of the airframe and the odd engine run. The neighbours haven't minded the unusual outlook, but I have only just learned that one of their dogs did loudly object to the engine tests. This is my second Mono Europa project and I have flown 400 hours in my previous example, completed in 2011. I couldn’t keep both aircraft and have agreed the sale of Tango Sierra once the full permit has been issued, allowing the future owner to be involved in the checking, weighing, paperwork and flight-testing process. He should then have detailed knowledge of the aircraft and systems that he will be taking on.
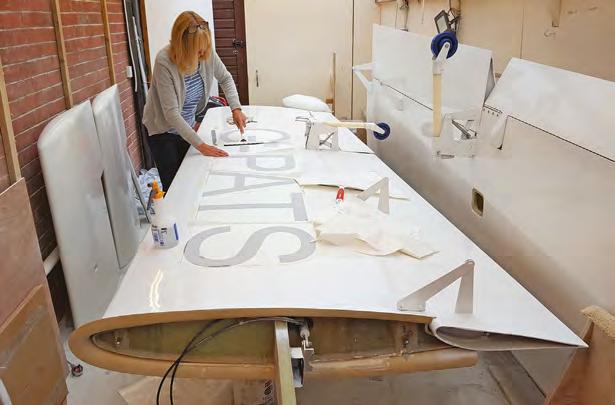
G-LHAB (LAA 399-15401) Sling 2
By Leila and Andrew Beggin
It was going to be an RV-12, but then Tim Hardy’s article in the LA magazine made me think again. That boyhood dream of… one day I’m going to build my own aeroplane, was within reach but the choice had to be right, and there would be no second chances. It was not easy; the Sling 2’s aluminium construction, good range and fuel economy with the Rotax 912iS, as well as the aeroplane’s track record around the world, meant it ticked important boxes. Moreover, it looks pretty good too. My pilot brother, Keith, happened to be in Jo’burg, home of the manufacturers, at the right time. We contacted TAF (The
Airplane Factory) and after a trial flight he gave the Sling the ‘thumbs up’. I made the order.
Leila: the builder’s wife: What a relief! In my view the Sling was, and still is, the best-looking aeroplane in its class. Call me shallow, but as a mere prospective passenger, that counts for a lot. While waiting for the first kit, I did some boring but essential prepping, which included installing nine LED strip lights in our double garage and adding insulation to the doors at each end. At 6.5m in length, the garage was able to accommodate the fuselage and engine once mounted, with a bit to spare for working/walking round. Multiple layers of clothing and an electric heater meant I could keep going in winter. The empennage was delivered in May 2016. The kit was carefully packaged in a wooden crate, the parts were well-labelled, and the instruction manual was clear, which was also the case for most of the kits that Below Alpha Bravo ready and waiting for that first test flight. Photo: Andrew Beggin
Top right Starboard wing under construction in the TAF special jigs, beefy looking main spar and location in front for the fuel tank. Photo: Andrew Beggin
Below right Nice interior, the panel lights up for the first time. Photo: Andrew Beggin followed. Most importantly of all, parts were matchdrilled precisely and the kit fitted together beautifully. For corrosion resistance I chose to use a Deoxidene wash followed by Alocrom treatment of all internal surfaces, and JC5A between all mating surfaces and on every rivet. Use of zinc chromate requires care and use of the correct PPE but has helped in achieving a relatively good empty weight. Only time will tell in relation to corrosion resistance.
There is perhaps room for an LAA course on corrosion protection but the LAA courses I attended on working with aluminium, Rotax engines, and electrical systems all proved extremely valuable during the build.
Feeling pretty sure that eventually I would end up with an aeroplane to be proud of kept me going, as inevitably there were setbacks, some of which took up considerable time and effort to resolve. One such was the delivery of the wrong engine mount, something that only became obvious once the engine itself was mounted and the cowling refused to fit.
Leila: There were definitely difficult times. Luckily, I’d been one of the novice builders in the 7-Day Build of a Sling 4 at the LAA Rally in 2016. That experience helped me immensely in my role as ‘builder support’. I couldn’t offer practical advice but at least I could be a sensible sounding board. But in the end, it’s the builder who has to find the drive to persevere.
The actual build turned out to be the easy part; around 15,500 rivets later you have your aircraft. The real challenges come with fitting the engine and the
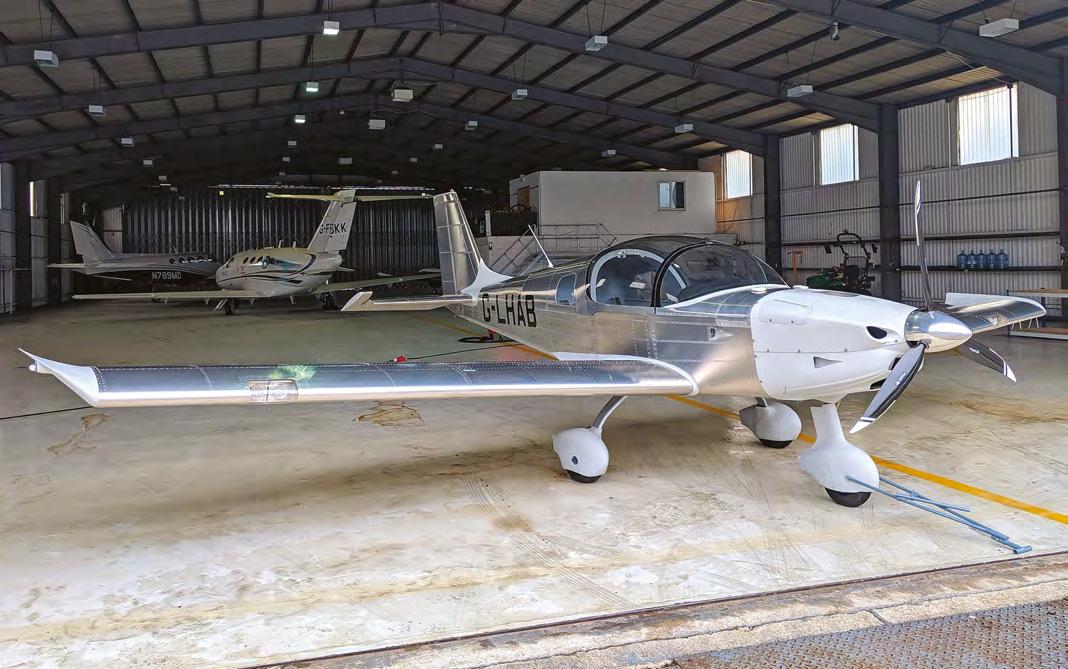
electronics. The Garmin glass panel was pre-wired by TAF but still came with a bewildering array of wires, each of which had to be found the right home. I am hoping that it can be cleared for night and IFR operation in due course. A key milestone was the first engine ground test in December 2018. G-LHAB, was tied to an apple tree in the garden and with barely a turn of its Airmaster constant speed prop, the engine started first time! Another milestone came in February 2019 when the excellent Paul Ponsonby moved her to London Oxford Airport (Kidlington).
By the end of the day four of us (Leila, my wife, Keith and my other brother, Graham) had put both wings on – G-LHAB looked the business.
A number of weeks were spent getting everything ready for the final inspection. Some issues were then encountered in the application for the permit to test relating to the use of the Rotax 912 iS engine. It was the first Sling 2 in the UK with this engine, although a Sling 2 used for training in South Africa was the first aircraft to reach 2,000 hours on a 912 iS. Finally, on 5 October 2019, after some 1,500 man-hours, G-LHAB took her maiden flight in the capable hands of Tim and fulfilled that young boy’s dream. Thank you for all your invaluable help to Leila, my inspector Antonia Gigg, Keith, Tim and the engineering team at the LAA. Now, I just need to finish getting my licence!
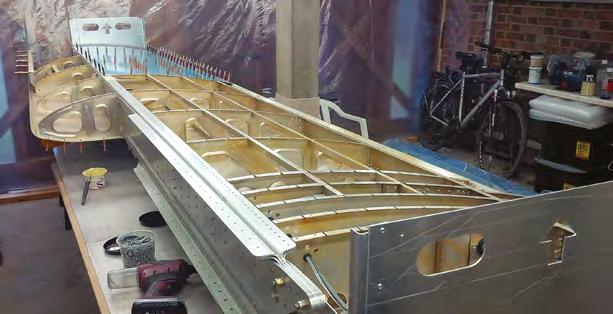

G-CKTD (LAA 371-15021) Colomban MC-30 Luciole
By David Lawry
This is a project that probably became inevitable in the 1950s when I discovered KeiI Kraft, and resumed 60 years later when I thought I needed a retirement project (which turned into a spare time project). At the turn of the 20th century, I put together a Below On 30 December 2019 she was all finished and ready for test flying. Photo: David Lawry Jabiru kit which I still fly and love. However, the sense of building was limited as it only felt like putting together a big Airfix kit, so I still needed to build an aeroplane. Then Brian Hope wrote a couple of articles about the Luciole in LA magazine and the fuse was lit. And

Richard Teverson exhibited his partly built Luciole at the Rally for a couple of years and fanned the flames. About 10 of us bought sets of plans (24 full-size sheets and four or five manuals in French) at the same time and we co-operated in buying and making parts and jigs etc. G-CKTD is the fifth example completed in the UK, with a couple of projects still being actively worked on.
For those that don’t know it. The Luciole is a design by Frenchman Michel Colomban as a minimum aeroplane, in France it is a ULM (Ultra Léger Motorisé – a microlight), the goal being minimum power, maximum economy but a good performance, and built mainly from wood. With an empty weight of 100kg, and a max weight of 200kg, the Luciole will cruise at 100mph for as long as your backside can stand it, and all on less than five litres per hour. As for construction, I’m told that this design needs more attention to precision manufacture than most – I never expected to be planning up strips of wood and measuring them with a micrometer!
Carbon fibre top boom
The wings (a separate one each side) are each built on a spar the depth of the wing and about 30mm thick, which features a substantial pultruded carbon fibre top boom and a slightly lighter one at the bottom, both being supported by spruce and beech caps and ply webs. The spars are extended inboard and overlap across the bottom of the fuselage, to which they are affixed by two pins, allowing the wings to de-rig very easily. The ribs are cut from 10mm closed cell PVC foam and, thank heavens, they are all the same. There is a trailing edge spar of 1.5mm ply with 9mm spruce booms, which supports the ailerons and the flaps, which occupy about 2/3 of the span. The whole of this structure is bonded into the wing skin of 1.2mm ply, pre-formed to fit around it.
The fuselage is a pretty standard wooden construction, with a bit of added interest in that the two sides and the bottom have a combined convex and concave shape to them and have to be built on a specialty shaped table. In addition, the top longeron, which is basically 10mm square spruce, is laminated to 10mm x 30mm in the forward section and is further reinforced with carbon fibre. There are three frames made from sheet aluminium bonded into the fuselage to take the wing and undercarriage loads. The engine is perhaps not of the type that first comes to mind when you think of aircraft. It is a Briggs and Stratton (no laughing now) Vee twin stationary engine, modified in simple terms to remove the governors and add a carburettor heat system. The power is about 26hp and the max rpm is 3,600. The engine installation is unusual and appears complex in order to give compliance and cope with the unusual (to us) vibration characteristics of the Vee twin – a phenomenon that causes Harley Davidson riders’ hands to tingle, making them fear they have developed Parkinson’s disease. The prop is custom designed for the aircraft, carbon fibre with ground adjustable blades.
Instrumentation on this aircraft is to the design and is the minimum possible.
Trial assembly
The biggest challenge for me, though not for everyone else, was the canopy which although it looks blown at first sight, is from a flat panel of PET with a moulded carbon fibre cap, all riveted and glued to a framework of curved aluminium tubes. Every time I went for a trial assembly, it went together in a slightly different way but, in the end, it was spit or bust and it seems to fit the aircraft OK.
Now, after several years of pleasurable problem solving, therapeutic cutting, shaping and gluing, I’m left with a mild case of post-natal depression, even though I probably have the prospect of many hours of debugging to come. One of the pleasurable facets of the project has been the number of exceptionally impressive and talented people from a variety of backgrounds that I have met along the way. Many that I’m still in contact with, and all who share this common interest. They will not recognise this themselves, because they don’t think they are exceptionally impressive and talented. All I need now is the weather to fly off the test schedule!
New Projects
If your aircraft has been featured in the New Projects list, please let Project News know of your progress at: projectnews@laa-archive.org.uk
n Eurofox 912iS (LAA 376-15678) 18/12/2019
Cleared To Fly
If your aircraft has featured recently in the magazine and has subsequently completed its maiden flight, Project News would like to hear from you at: projectnews@laa-archive.org.uk
n G-CISF Quad City Challenger II (LAA 177-14783) 03/12/2019 Mr Simon Beddus, 35 Grove Lane, Ipswich, IP4 1NX n G-CLCM Mission M108 (LAA 370-15559) 17/12/2019 Mr D M Griffiths, Bryn Haul, ‘Dinas’, Pwllheli, Gwynedd, LL53 8UB n Sherwood Ranger-ST (LAA 237B-15675) 04/12/2019 Mr J Corrall, 4 Park Avenue, St Ives, Cambridgeshire, PE27 5JW n Zenair CH 750 (LAA 381-15677) 09/12/2019 Name and Address held by LAA Engineering n Mission M108 (LAA 370-15676) 06/12/2019 Name and Address held by LAA Engineering
Vivienne and Laurence Soutter, 2 Hyde Barton Churchill Way, Northam Bideford EX39 1NX and Karen Shern, 45 Felbridge Close, East Grinstead, RH19 2BN n G-TOPP Van’s RV-10 (LAA 339-15289) 02/12/2019 Mr Stephen Coles, Church Farm, Walton Road, Wavendon, Milton Keynes, MK17 8LY and Mr David Topp, Keyes Burrow, Lillingstone Lovell, Buckingham, MK18 5AY n G-AKPI Auster 5 (s/n 1088) 17/12/2019 Name and Address held by LAA Engineering n G-PATS Europa (PFA 247-12888) 02/12/2019 Name and Address held by LAA Engineering n G-RVFT Van’s RV-8 (s/n 82253) 03/12/2019 Name and Address held by LAA Engineering n G-SLNG Sling 4 (LAA 400-15477) 20/12/2019 Name and Address held by LAA Engineering
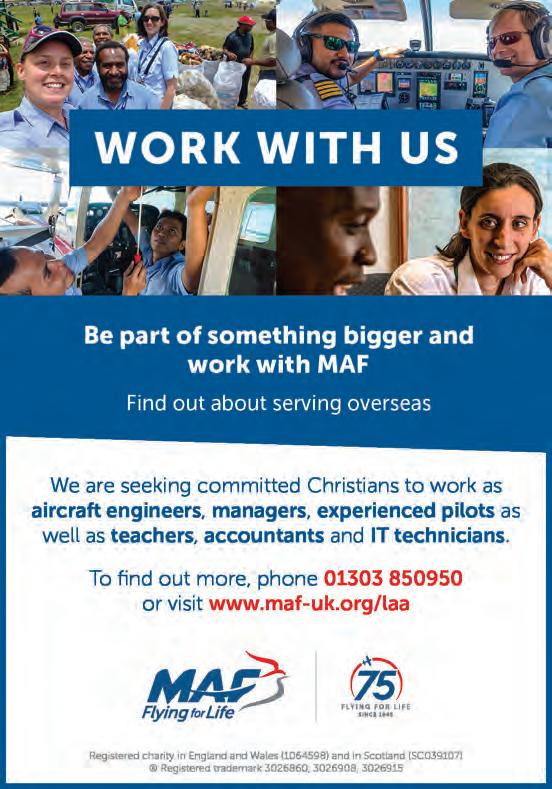
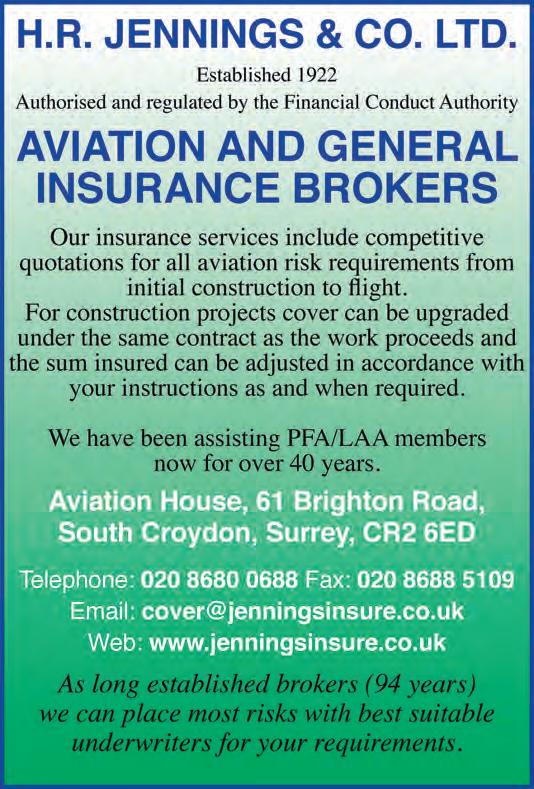
