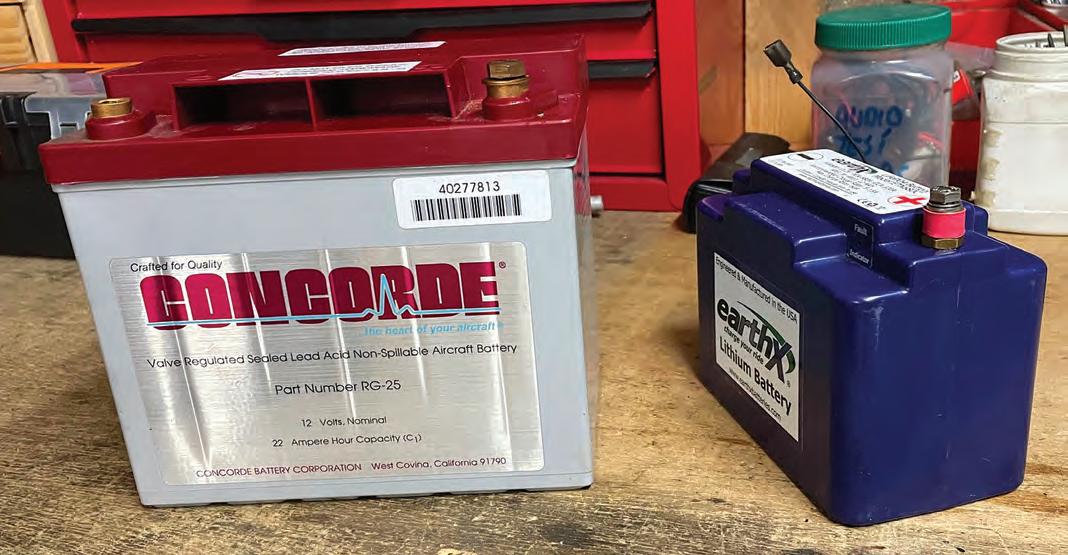
19 minute read
BATTERIES
Take charge…
Ian Fraser explains how to check and look after your battery, and what to consider when deciding to replace leadacid with lithium…
Batteries are one of those components that many of us take for granted and most of us are totally reliant upon them for starting our aircraft. But how do we know if they are up to the job? Manufacturers suggest life expectancy of a normal aircraft battery could be five to seven years, and although some users wait until the starter begins to falter before replacing the battery, others change them regularly as a matter of normal service routine.
Some of us now permanently connect smart chargers, which the ‘charger’s champions’ say can double the life of a battery. I have heard reports of aircraft battery lives of between two and 20 years, but who really knows how long you can expect your battery to be reliable for? I don’t think anyone does.
So, is there a practical, simple engineering means of deciding if and when your battery needs replacing?
The short answer to that is, yes.
However, if we do decide the battery needs to be replaced, do we really need another 12kg lead brick?
That’s a fair chunk out of our useful load after all, and technology has improved such that a much smaller lithium battery can provide adequate current to start even a large engine. With the reducing electrical load for other electrical equipment, suitable batteries are Above The old Concorde lead-acid battery and the new EarthX lithium-Iron. available today that weigh less than 20% of the original, which could be a saving of 10kg.
Before we look at smaller, lighter batteries it is key to appreciate exactly what an aircraft battery needs to do and with how much power it needs to do it – and that is it must not only start the engine, it must also provide an adequate source of electricity in the event of an alternator failure.
Starting requirements
To explain starting and its battery requirements, I will split the process into two parts: getting the starter itself and the engine moving; and then the normal cranking of the engine.
Getting the starter and engine moving, or ‘breakaway’ as the specialists refer to it, initially requires a massive burst of current, e.g., for a Lycoming O-320 some 200-300 amps. This current then reduces as the starter gets up to speed. Once it is moving at the normal turning or cranking speed (about 60 engine rpm or two blades per second), that current should drop to between 80-120 amps. If the engine is labouring during the starting process due to cold weather or a fault, it never gets to that sweet cranking speed and is actually placing a higher demand on the battery than if it were cranking normally.
Voltage drop
The ability of a battery to provide these high currents is known as it’s Pulse Crank Amps (PCA) or peak power rating, and for the cranking phase Cold Cranking Amps (CCA) or 15 second power rating. While it is possible to measure the battery’s ability to deliver these currents with a battery test set or ammeter, it’s expensive and messy and there is a much easier way to do it.
An ‘off-load’ lead acid battery’s fully charged voltage is about 12.5v. But the voltage measured while delivering high currents is a good indicator of its health. Its own internal resistance will result in a drop of a volt or so between the battery terminals when under cranking load, but on its own this is not unhealthy. If, however, during starting (from fully charged) the voltage drops below, say 10v, or panel lights noticeably dim, it indicates a potential battery problem.
But the key to effective starter cranking is the voltage at the starter. For my RV’s starter, (a B&C), it recommends a minimum voltage of 9v while cranking, so that is where we should actually measure it. Why would the voltage at the battery and starter be different? Poor or loose terminals (including engine earthing), dirty solenoids or even under specified cable (too long and/or thin) can impact the voltage that gets to the starter. This reduces starter efficiency, but such problems are often misdiagnosed as battery faults.
My RV has four feet of 4 AWG (heavy duty) cable from the battery to the starter and back, including ground cables. That’s short by many aircraft’s standards but alone accounts for ¼ volt drop at cranking currents due to its resistance, even if everything else is working perfectly. Longer or thin cables equate to more resistance and less volts (Ohm’s law). If the battery itself is OK (greater than 10v while cranking) but the engine cranks too slowly, then that is your next port of call.
So, you can quite easily check your battery’s adequacy to start the aircraft by measuring the voltage at the starter, but for how long or how many times will it do it? Below The set up to carry out a capacity test on your battery.
Bottom Check the voltage drop at the starter motor. Storage capacity
The second health consideration is storage capacity, amp / hours, which is important for both starting and electrical back-up. Remaining charge or capacity (what it actually has left, not what is written on the side) is important to the battery’s long-term effectiveness. As you use a battery (without a charger or alternator) its voltage gradually reduces until it comes to a point where it no longer has enough voltage for the devices it is supplying (typically between 8-10v, see device manuals). It is measured by the time it takes the battery voltage to drop from a fully charged 12.5v to 10v while supplying a known current. Over time, due to use, lack of use, or indeed misuse, the number of amp / hours a fully charged battery can supply decreases, and eventually no amount of charging (by any means) will sustain its capacity.
To determine the remaining capacity there is a simple test. From when fully charged, drain the battery with a test load until it reaches 10v, measure the time to do that and you can calculate the amp hours used. I use a 55W (4.5amps) car headlamp as my load (it is representative of my RV’s essential equipment load). When new, I would expect my Concorde 22AH RG25 battery to last for just under five hours (22/4.5). However, if its capacity has deteriorated, it will take significantly less than that. At four hours it is time to consider a change.
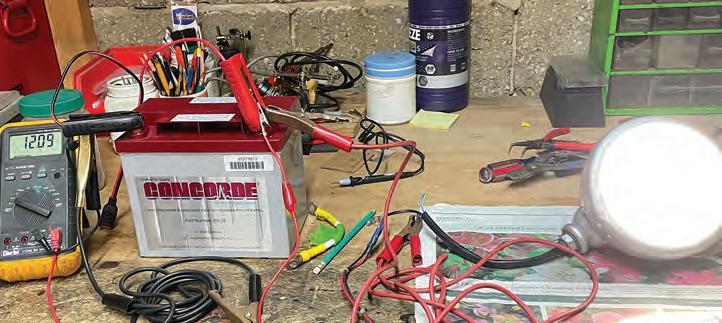

When to renew…
The Concorde (lead acid battery) maintenance schedule says that if it fails the above test with less than 19-amp hours, before you condemn it, give it a conditioning charge and test it again, it may recover. Some smart chargers have a conditioning charge mode to do just this.
Battery capacity deteriorates with age and lack of use, which is mostly why they die, but at what point does it become a liability or safety risk? The normal criteria is to change it when it drops to less than 80% of its original storage capacity – the rationale behind that is not the actual 80%, but below 80% the deterioration accelerates, and in less than a year’s time your battery could let you down.
Lead acid batteries also self-discharge, even if not connected. If not recharged regularly through use or maintenance, they eventually flatten themselves to a level that permanently damages them and their capacity. A regular charger is fine to recharge a battery but, once charged, leaving it connected can do more harm than good.
Smart ‘float’ charging
Many of us now use ‘smart’ battery chargers (e.g. CTEC / Optima) on our aircraft to overcome this. They charge the battery as normal, but once they detect that it is charged, revert to the so-called ‘float’ mode, which preserves the battery and charge, supposedly without damage.
While these devices definitely pay for themselves in extended battery life and with prompt, reliable starting, they can also mask impending failure until it is potentially serious. With a smart charger, the battery is always topped up so a defective battery with say, only 20% capacity left, could still achieve a good burst of cranking, and thus comfortably start an aircraft, before suddenly giving up the ghost. You may never spot this while the alternator is working until it fails completely during a backup or restart role (e.g. for the return flight). I have seen this happen on my classic vehicles. The worn-out ‘float charged’ battery starts the engine easily – once – but after that I have experienced them neither accepting nor holding a normal charge and not even running the lights. The battery was dead and had no indication that it had a problem! So, if you are using a smart / float charger, checking battery capacity routinely is doubly important for your safety.
With nothing more than a voltmeter, watch and headlight bulb, you can determine the health of your battery and starter system and take the guesswork and speculation out of the equation.
Below A smart charger is a good idea for lead-acid but can also mask problems. Considering new technology…
During this year’s annual inspection, lockdown restrictions prompted me to look carefully at alternatives for my RV-6’s battery. Measurements of my 12-year-old Concorde RG25 showed that, while within spec, it was close to the 80% capacity point, so I decided to make the change to lithium.
Lithium battery technology was discovered in the US in 1980 and the first practical lithium batteries were developed by the Japanese in 1985 for phones and handheld computers.
The technology, known as lithium ion, supersedes several old technologies, including the heavy lead-acid batteries we use in aircraft. It achieves a power (storage capacity) to weight reduction over the then current technologies of some 60-70%, plus there are other electrical characteristics that make its stored electricity more usable. Unfortunately, the electrolyte they originally used allowed internal short circuits to develop, resulting in some disastrous fires. Subsequently, better chemistry has evolved with lithium iron phosphate (LiFePO) now being dominant, offering a much safer solution. However, there is still a lot of energy stored in a small volume and out of control loads or internal faults could result in overheating. This is now managed by built-in electronics and is the safe lithium battery technology today, a complex but reliable package of chemistry and electronics.
Small lithium batteries can now provide enough current to start quite large engines and several have been developed for motor racing. It was only a matter of time before those batteries came to the attention of aircraft homebuilders.
Lithium batteries have several quite different characteristics to those of lead acid and the LAA, having considered the safety implications, now has a (no fee) Standard Modification, SM14337 in place for upgrading your aircraft battery. Read it carefully as it contains a number of constraints and requirements which you must consider in your upgrade.
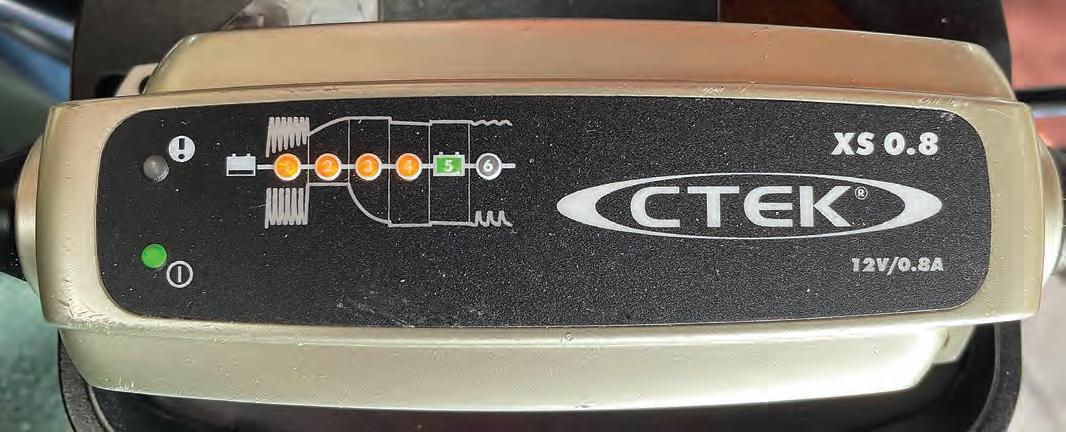
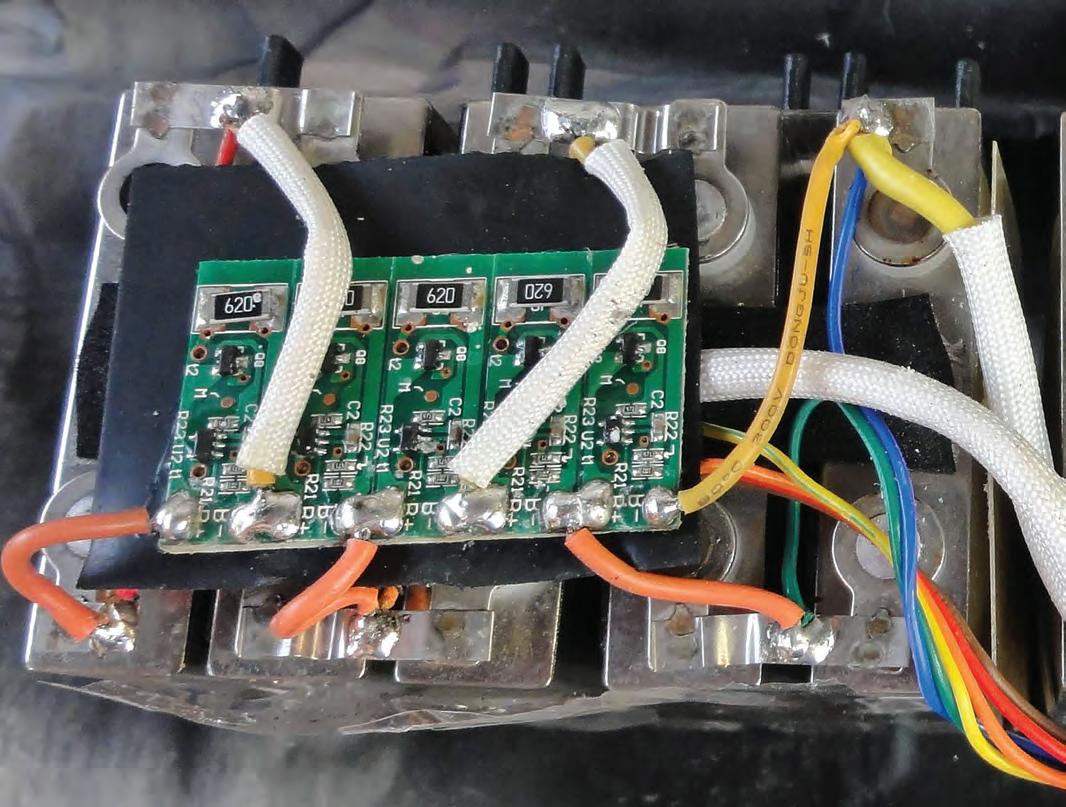
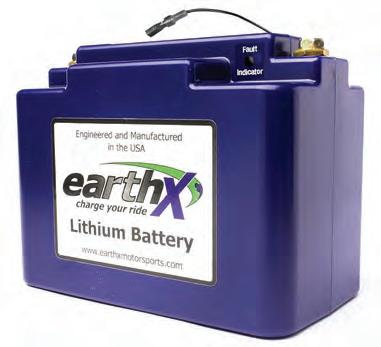
In its document, the LAA also published a list of acceptable lithium iron batteries, but be careful here, all they are ‘approving’ is the safety of carriage and connection of the battery in your aircraft, not saying it is either suitable or fit for purpose, that is your call. The modification must be approved by your Inspector before you fly, so it is best to get him / her involved from the beginning. I chose an EarthX ETX680C for my RV, for reasons discussed later. Could lithium be an option for your aircraft?
The key considerations…
First and foremost, weight and balance. One of the requirements of the Standard Mod is to use the original mounting position. If the original battery was close to the C of G, as on the RV-6, then the 10kg or so weight reduction will not move it far and it shouldn’t exceed any limits. But if, for example, you have an RV-8 where the battery is some distance from the C of G, it may move it out of limits for some load cases. As part of the standard mod, you must demonstrate that it is still within acceptable limits. If you need to move the battery, it becomes slightly more complex – you can, but you must go through the full LAA modification approval process.
The next, and key question, is will it start your aircraft? To select the battery, you can of course calculate or measure the demands of the starter, but
Above A dismantled Lithium battery, note the internal electronics.
Left Ian’s replacement EarthX ETX680C battery weighs less than two kg.
Below A graph showing the EarthX voltage drop over time.

it’s much easier to match or better the peak and cranking capability of your current battery. As a general rule of thumb, a lithium battery with just 30% of the capacity of a lead acid one will provide the same cranking power. My 0-320 was not a problem for any of the candidate batteries.
Then you need to consider capacity or amp-hours (ah). The graph shows the capacity of the EarthX lithium 12ah battery. From full charge, its output is reasonably constant, delivering 13v at six amps for two hours, 12a for one etc. It can even deliver high cranking current (100 amps or more) for much more of its capacity cycle than a lead acid battery, providing many more starts than you might expect. This is sometimes referred to in adverts as a ‘lead acid equivalence’.
Don’t be misled, it works for starting, but the same capacity oddity is not true for the alternator failure back-up function. That must be calculated properly and planned for. An important aspect of lithium batteries to be aware of is that when they run out of charge, they do so suddenly. No warning and no more electrical power! Your calculations must consider that.
Alternator back-up
Alternator back-up is about continuing to run your essential electrical and electronic equipment in the event of an alternator failure. The LAA talk about 30 minutes and ‘load shedding’ to achieve it. I believe 30 minutes is far too little for touring. If your alternator fails, you need to get somewhere with reasonable accommodation and a chance of fixing it, not just the nearest airfield. Load shedding is a method for reducing the electrical and electronics functions in use to those essential to complete the flight safely, e.g. flight and engine instruments, Comm, perhaps Intercom and Nav but, no lights, music, autopilot, Comm Box 2, transponder, or USB devices etc. The electrical load page from my RV-6 handbook shows the plan by highlighting in colour the criticality of the functions. It is based on average, not peak consumption, as that is what happens in real life.
The minimum essential equipment requires 2-2.5 amps. To complete a typical touring flight of three hours, I need about 7.5 amp / hours of power. I added enough for a couple of engine starts, (250a/10 secs) plus a bit for flaps and fuel pump and the total to complete a flight under load-shed conditions is about 8.5ah.
Bearing in mind battery lifetime capacity degradation (-20%) the smaller candidate batteries available would be pushing my luck but a 12ah EarthX battery gives me enough margin to complete a touring flight comfortably. It is important to document the load shedding plan where it can be accessed in an emergency.
Below An electrical load sheet for the RV’s electrical requirements.
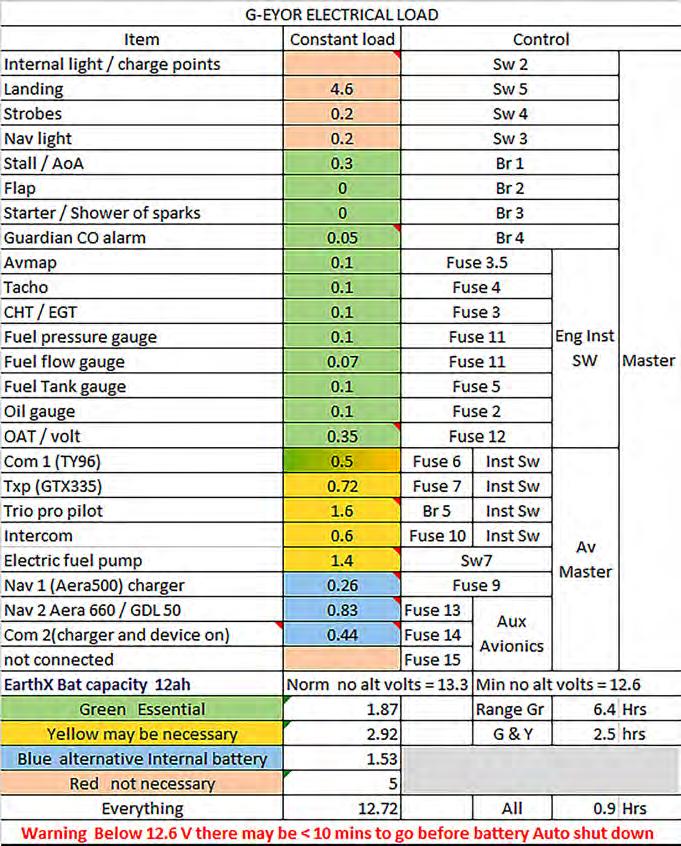
Electrical design
Once you have selected a suitable battery you have several electrical and mechanical considerations. Probably the most significant of these is over-voltage protection, something we should all have (do we?). Over-voltage is an electrical problem that can occur if the alternator’s field winding or regulator fails and the alternator outputs a much higher voltage (greater than 15v) than some of the aircraft’s electronics are designed to tolerate. Uncontrolled, it could damage your avionics and instruments and thus your wallet. In the normal world this might be called a ‘surge’, and reports of it in aircraft are surprisingly common.
Over-voltage can happen regardless of your battery type but all lithium battery manufacturers concur that lithium cells can be damaged by exposure to over-voltage, hence concern about over-voltage protection (OVP). Surprisingly, many aircraft don’t have OVP, but most that do use a system called a ‘crowbar’ to provide it. This device, sometimes part of the regulator, sometimes separate, works in conjunction with a circuit breaker in the alternator field (charge enable) line. If the crowbar (a bit of electronics) detects over-voltage, it simply connects the alternator field wire to ground, and the alternator field circuit breaker should be tripped. A relic of the Jurassic period of aviation, there should be many better ways of doing it today, but there doesn’t seem to be.
Disconnecting the field should automatically disable the alternator and you are safe to continue with your flight on battery power. Those of you who have attended the LAA electrical course may recall Nick’s fascinating demonstration of just how fickle circuit breakers can be and there are several searching questions to answer on the subject of OVP, but they are beyond the scope of this article.
The aircraft voltage being in normal range is an
important flight safety parameter and, to ensure that you know, the LAA insist that you have a voltmeter visible to the pilot, and also the ability to fully isolate the alternator field and output. In my case, my charging circuitry was already compliant and most of my devices are OK up to 33v anyway (I already fried those that weren’t with an earlier unprotected alternator over-voltage fault). If you don’t have OVP and a voltmeter, then you may have some thinking, wiring and other changes to do.
One of the points in favour of the EarthX battery is that it seems to be more sophisticated than the rest in terms of its built-in battery management system (BMS). The BMS monitors many aspects of battery performance and manages, reports (via a status indicator) or safeguards both you and the battery. In the case of an over-voltage condition, it blocks charging, protecting the battery regardless of the effectiveness of the crowbar. It also manages cell balance, an important battery life thing and, if you manage to discharge the battery, it switches it off before any permanent damage can be done. Whether that is a benefit or an overcomplication remains to be seen, but to me it seems a clever and useful system.
Mechanical installation
Another reason for choosing EarthX was that its physical size fitted my existing carrier quite well. The LAA document implies that you can use packing to locate the new battery, but I would be very cautious in doing so. For their small size, lithium batteries can produce a lot of heat, and wrapping them in packing will not help cooling.
The installation in the RV-6 was quite simple. The carrier for the existing battery unbolts and can be removed for modification. I just added the battery manufacturer’s standard ventilated mounting bracket to the carrier and left off the original battery cover (for cooling). One cable needed replacing to do a neat job and the terminals must be covered with insulating sleeves. An EarthX battery has a fault indicator light connection, so this was added to the panel and wired in.
While in the battery area, it is worthwhile considering adding a socket to the exterior of the aircraft to charge and monitor the battery. Mine connects to the battery positive terminal via a (7amp) fuse and to the starter terminal so I can make all the measurements described earlier.
Pre-flight, in-flight checks and continued airworthiness
The essential thing is to know and monitor the important voltages. Adequately charged, but offcharge you should see greater than 13v on your voltmeter, if it is below 12.6v it is too flat and could quit imminently (see the graph). During flight, charging should be between 14 and 14.4v*. More and it is over-voltage, less and it may not be charging effectively. Although in an emergency, any charger will charge one, lead acid chargers can damage the battery. Optimal charging requires a specialist Lithium battery charger which deals with their foibles so for long and reliable battery life, it is better to use one of those.
Lead acid batteries can self-discharge by up to 30% capacity per month, hence they benefit from a top up with a float charger. Lithium batteries normally discharge at 3% or less per month so float charging is much less important. In fact, rather than benefit the battery, it seems that the specialist chargers just ‘do no harm’ if left connected. If you do let your battery go flat, the BMS may switch it off to protect it from itself. And the catch here is that some lithium batteries, once they have switched off, don’t naturally restart or take a charge, they need to be ‘bump started’ to recover them. The latest smart chargers have a button to do this. See the battery or charger manual.
Of the batteries available on the LAA’s list that I could find out enough about, the EarthX seemed to be the one most specifically aimed at the aviation market, and after carefully comparing the essential parameters, it was the one I chose. Installation in my RV-6 only really took a day’s work, and it has performed perfectly since. Multiple starting has been fine, and the battery voltage has stayed at the expected level without float charging. The weight change has made no discernable difference to empty flight characteristics. As with much of this ‘invisible’ equipment, the issues by which it may really be judged (reliability) hopefully may never occur, and so far, so good. I will open a thread in Hangar Chat so if anyone has any experiences, they would like to share, please do it there.
Below It’s worth installing an easy access charge / monitoring point for whatever battery type you have installed.
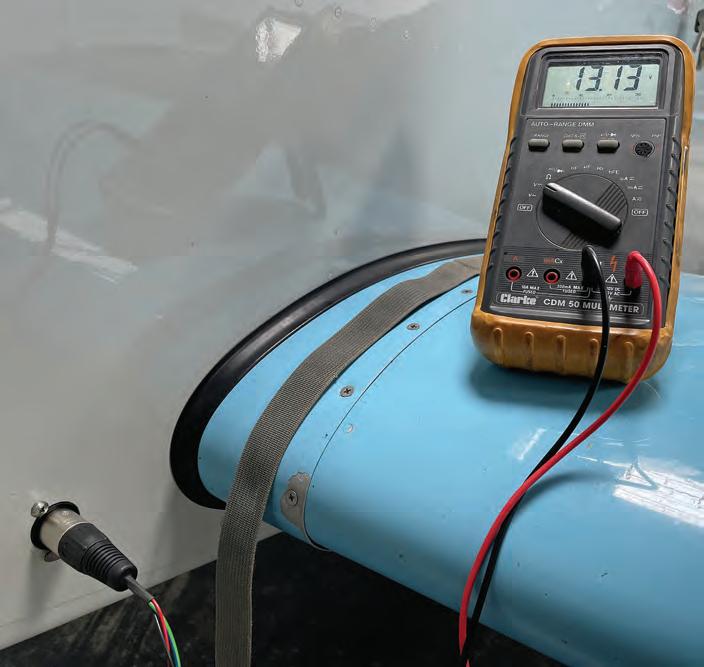
* Check all these values for your specific battery. Note: I have been deliberately vague about some values because they are often unique to an individual set of components, and manufacturers data can also be inconsistent. The values I have suggested will put you in the right ballpark, but the best way is to measure and record the key values when everything is working. You then have an aircraft / equipment specific set of values to compare against later to judge battery health. ■