CREATING VALUE IN WAREHOUSE AUTOMATION www.geekplus.com | www.imhx.net INTERVIEW | CASE STUDIES | SHOWCASE

www.imhx.net
Simon has worked for Geek+ since 2019. He has been part of the distribution, logistics and supply chain sectors for over 30 years, having worked for large systems integrators, warehouse storage companies and also ran his own national distribution centre for over 10 years. He leverages this extensive supply chain experience in his current role and strongly believes that using AI and robotics in the next 10 years will dramatically change how we view automation in the warehouse environment. SHD Logistics Editor James Burman speaks to Simon Houghton, Head of Sales and Marketing UK&I at Geek+, about how the company has developed in recent years, and what it now offers to customers.
www.geekplus.com
James Burman (JB): Why, in 2022 is technology so important in the warehouse? Simon Houghton (SH): I think it’s so important because of the VUCA economy (volatility, uncertainty, complexity, and ambiguity). These things that make up the VUCA economy are present in warehouse environments, and it makes it exactly the environment where an AMR (Autonomous Mobile Robot)type solution is key. They can be used to tackle the rising cost of energy and labour – even the lack of labour – all while increasing efficiency. It’s also a considerably lower capital cost compared with traditional automation, has a much shorter implementation period, and is ultimately more scalable and flexible. These elements make AMRs the perfect solution in a VUCA environment.
INTERVIEW ‘It’s all about continual improvement’ Former
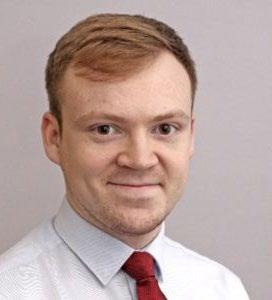
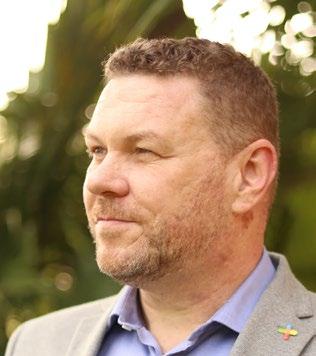
www.geekplus.com
www.imhx.net JB: How would you say Geek+ has changed as a business over the last five years? JB: How does Geek+ approach research & development for its products? INTERVIEW
Simon Houghton (SH): That’s a question! When I joined the business even three and a half years ago, we were just over 600 people and now we’re over 1500. In fact, there were only three of us working in the UK, and there wasn’t an office back then. Now, we have got an extended team of more than 150 people across the country (including resellers), working in sales, engineers, and support, all of whom are actively knowledgeable about Geek+'s solutions. That’s people; but in terms of technology, we’ve changed so much, too. Traditionally, we were known for shelf-to-person solutions, but that's changed considerably, particularly when it comes to tote-toperson solutions and much faster, taller picking systems. We’ve now got robots which will pick totes 8m high. We’ve got very densely packed mobile racks with 3.7m shelves, which are presented to an automatic station, gathering up to 650 totes an hour. That’s the solution known as PopPick We’ve also introduced a 4 way shuttle solution, which is a multilevel storage and retrieval system with upper level storage and ground level picking technology. The new solution augments warehouse throughput, storage capacity, and operational flexibility with optimal cost effectiveness. It’s the perfect solution for businesses who demand both high storage capacity and picking efficiency. These are just some of the technological developments we’ve made. It has been an incredible five years. Simon Houghton (SH): R&D is a huge part of our business. We’ve got I think - between 800 and 900 patents filed already on our solutions. To give you a further sense of importance, of the 1500+ people working at Geek+, we’ve got over 50% R&D professionals globally We’ve got ex-rocket scientists and professors of mathematics in our team. They are developing both mechanical and software improvements for our solutions. We use existing data to formulate the algorithms for the AI element of the software; it’s continually learning from previous processes, looking to optimise the stock management in the warehouse wherever it can. It’s considering where to locate that stock and basically adapt to the most efficient route to it, providing the most efficient storage facility Researchpossible. and development is key. The solutions don’t stop coming! It’s all about continual improvement, and that’s how we approach it.
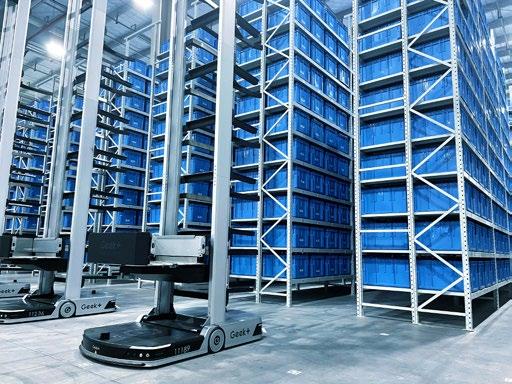
JB: What’s Geek+ future development plan in UK?
Simon Houghton (SH): This year, we opened our UK headquarters and robotics innovation centre in Liverpool. There are demos of a variety of Geek+ robots, including the P800 picking robot, RoboShuttle, and the sorting robot S20C. We’ve got a whole team there with sales, solutions, project management, engineering and customer service. Our partners, clients, or anybody who wishes to visit is welcome to see our AMRs. The team would be happy to show people around and answer any questions about how Geek+ can help them automate their operations. Our goal is to continue to empower our local partners and we expect to soon have even more successful projects in the UK. We also plan to introduce new cutting edge products to the UK market for even better efficiency and accuracy in smart warehouse operations.
www.geekplus.com
INTERVIEW www.imhx.net
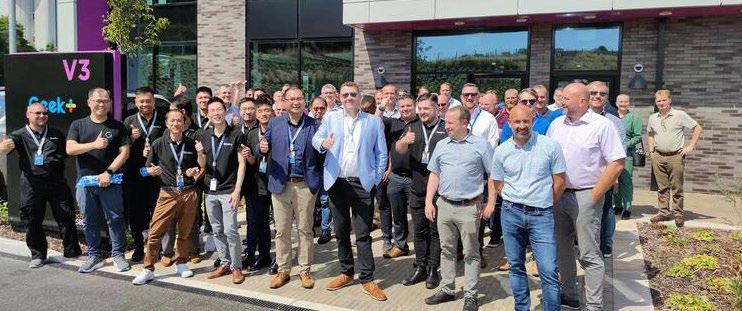
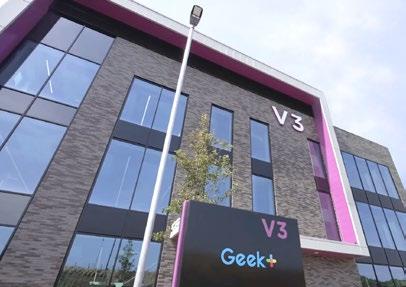
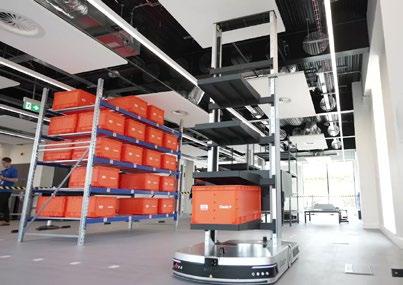
CASE STUDY
Paack, a fast-growing transport and parcel company, has the vision to optimise delivery times to make a valuable contribution to the e-commerce market. To cope with their large and expanding business, they decided to adopt Geek+ warehouse automation solutions in their new Madrid distribution centre The distribution centre covers more than 27,000 square metres and is one of the facilities that handle the distribution of parcels bound for over 80 cities in Spain, the UK, France, and Portugal, serving over 100 international companies all over Europe. This project is the largest autonomous mobile robot (AMR) project in Europe and the company’s first to handle both last-mile delivery and cross-docking operations. Paack launch Europe’s largest autonomous mobile robot project www.geekplus.com
Why does Paack want to adopt warehouse automation?
www.imhx.net
Geek+ and

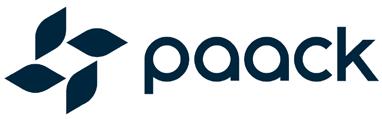
Geek+ has achieved a significant improvement in warehouse efficiency and operation accuracy is created in Paack’s warehouse. The Geek+ robots are sorting around 10,000 parcels per hour for distribution to up to 190 different destinations. Despite the number of parcels, the Geek+ robots achieve 99.99% accuracy in order fulfilment. Black Friday is one of the most significant events in the e-commerce industry. On Black Friday 2021, there were more than 100,000 orders processed during the first 2 days of the shopping season. The flexibility of Geek+’s solutions allows businesses like Paack to react to such sudden changes in demand to deliver exceptional services during peak periods.
www.imhx.net www.geekplus.com
What Geek+ solution has Paack adopted? 230 Geek+ S20C sorting robots and 32 Geek+ P800 picking robots are working in Paack’s distribution centre The distribution centre is divided into two sections: a mezzanine level for sorting, and a picking section on the ground floor Sorting robots move parcels via chutes to racks on the ground floor, where picking robots move the parcels to the operators. All robots are powered by strong algorithms which monitor robot traffic and balance the task of each robot to achieve maximum efficiency.
Watch the case video
What are the results and benefits of using the Geek+ solution?
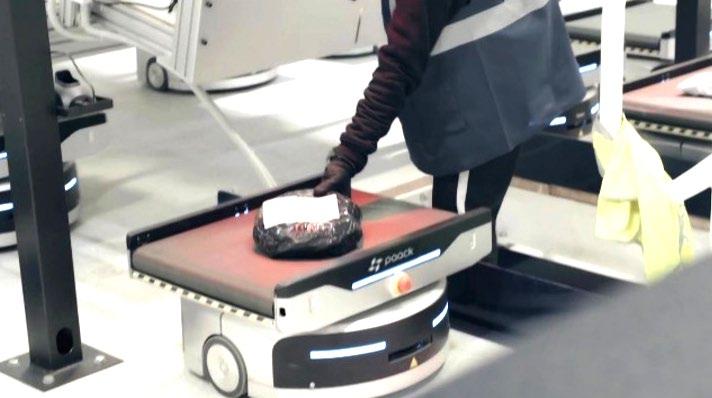
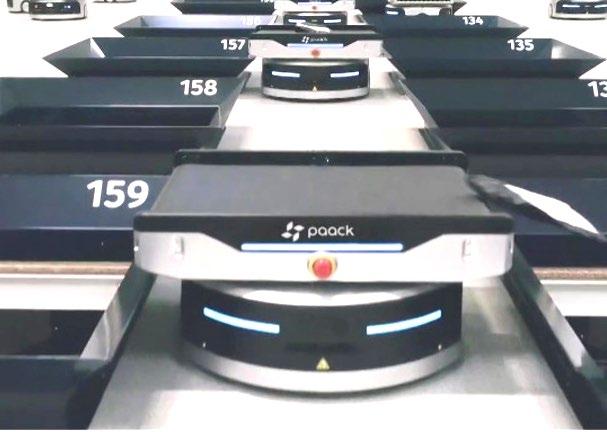
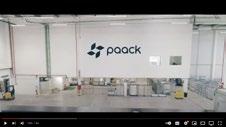
www.imhx.net
SHOWCASE PopPick - The next-gen
picking solution Geek+ discusses the benefits of its intelligent goods-to-person solution, PopPick. With the repercussions of supply chain disruptions, warehouse automation is a common strategy for companies around the world to take precautions and avert any potential knock-on effects from threatening the stability of their supply networks. Research has shown that the demand for warehouse automation is ever increasing, and the size of the warehouse automation market in the United Kingdom is expected to reach 3.9 billion U.S. dollars by 2025.* To fulfill the rising needs of the UK market, Geek+, the global AMR leader, continues to introduce cutting-edge warehouse automation technology to the country.
www.geekplus.com

*Source:
www.imhx.net www.geekplus.com
SHOWCASE
Visit Stand 5F50 to see the live demo of this revolutionary solution. Statista
Geek+ recently launched a ground-breaking goods-to-person solution, PopPick. In warehouse settings, Geek+ picking robots carry movable racks from storage locations to PopPick workstations. The target totes, which are already stored on the movable racks, are picked automatically by the station and presented to the operator for easy picking. As an all-in-one solution, PopPick creatively combines picking and storage of totes, shelves, and pallets and provides the warehouse with high storage capacity, high throughput, and great flexibility.
The PopPick station can handle piece picking, whole tote picking, and pallet picking with small, medium, and large goods. This high compatibility makes it easily adaptable to different industries, including retail, apparel, pharmaceuticals, 3PL, cosmetics, e- commerce, manufacturing, books, 3C, etc. Geek+ will showcase the PopPick solution at IMHX 2022.
This is the industry’s first dual-armed picking station, which means that the PopPick workstation has two picking points to select individual totes and present them to human pickers. This advanced technology increases the warehouse picking efficiency to up to 650 totes per hour and boosts throughput capacity by a factor of two.
In a warehouse, every inch counts. Every warehouse owner tries to increase space utilisation by maximising the storage capacity. PopPick provides high-density storage with 12 columns of totes stored in rows that have only 20mm gaps between totes. Similar to other Geek+ smart warehouse solutions, the PopPick solution is also powered by artificial intelligence and algorithms. Its dynamic slotting supports automatic unmanned operations based on order forecasts analysed during idle time. With totes arranged in the optimal position, the PopPick hit rate reaches 10 totes per move
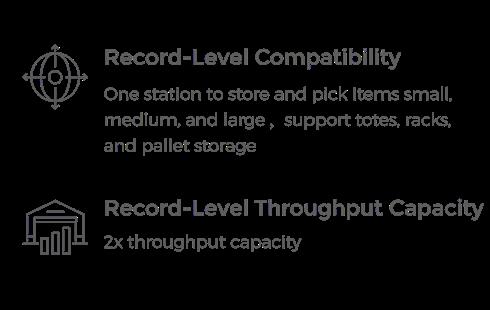
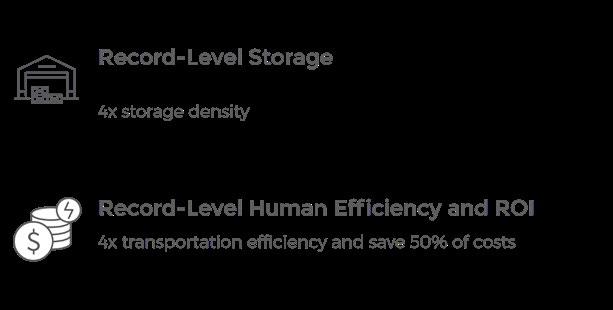
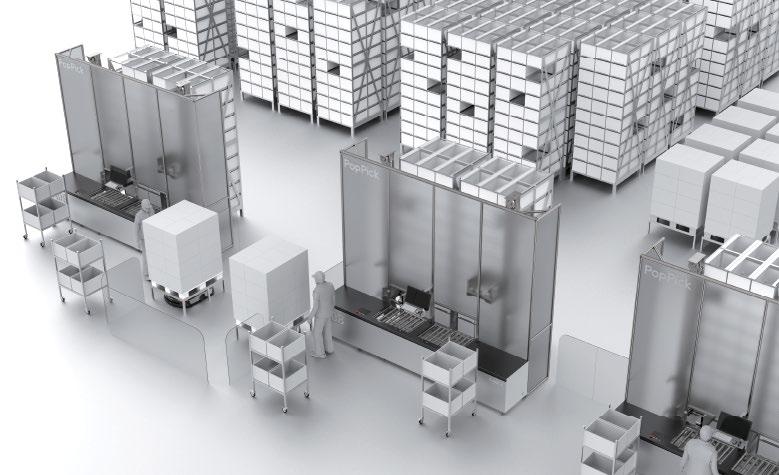
Asda Logistics Services adopted Geek+’s sorting robots to increase operational efficiencies. Here’s why. What Geek+ solution has ASDA adopted? Sixty sorting robots were deployed into Asda’s South Elmsall, West Yorkshire distribution centre. The project was implemented by AMH Material Handling, a provider of material handling solutions, and Geek+. Integrating S20C robots into the existing ALS sorting system provided Asda with the ability to respond to rapid changes in order volume and continue to provide excellent services during periods of peak demand.
www.imhx.net
www.geekplus.com CASE STUDY
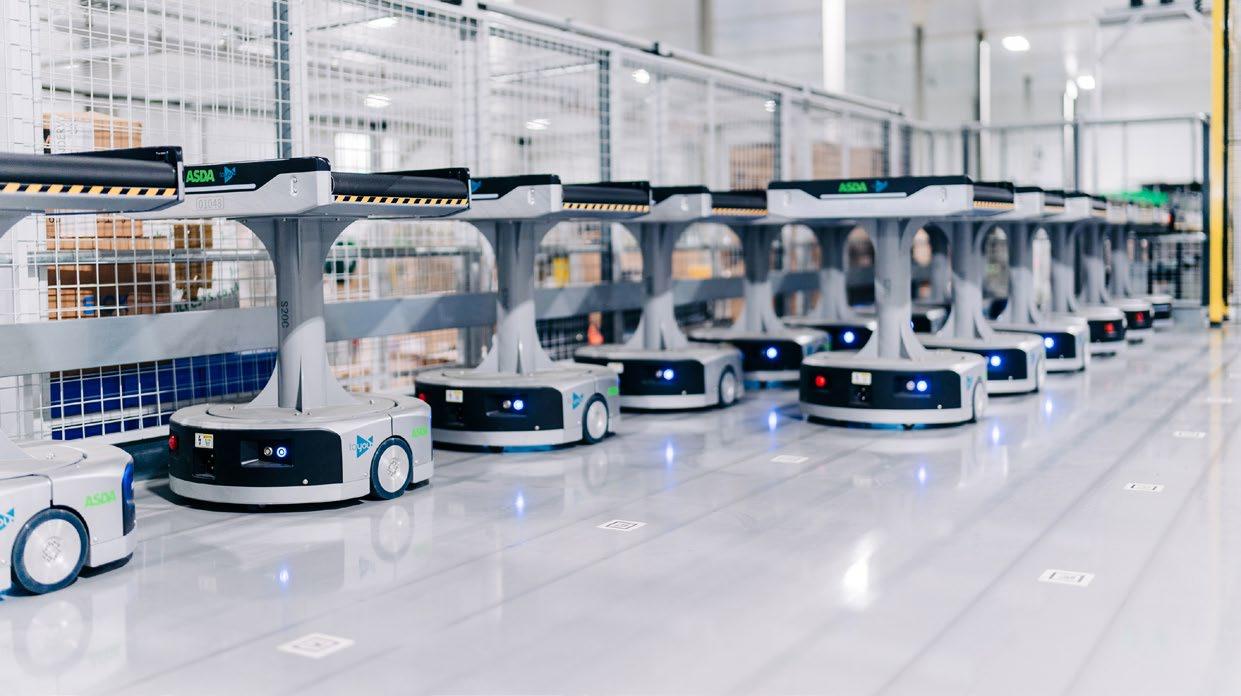
Asda is able to achieve 99.99% sorting accuracy thanks to the Geek+ solution. It allows them to provide excellent service during peak periods and respond to rapid changes in forwarding and reversed order volume. With this efficient and accurate solution, Asda, AMH & Geek+ won the Supply Chain Excellence Innovation Award 2021. “We’re pleased to be one of the first retailers in the UK to pioneer the Geek+ S20C robots in our National Sortation Centre, working in collaboration with partners at Geek+ and AMH. The robots work alongside our colleagues, enabling us to drive greater efficiencies at times of peak demand, which has helped to boost the number of parcels we’re now able to sort through our Asda toyou service.” - Jon Parry, Vice President of Asda Logistics Services (ALS) at Asda.
Watchwww.geekplus.comthecasevideo
Why did Asda want to adopt warehouse automation?
Asda was searching for an automation solution which would allow it to develop additional e-commerce capacity and improve its toyou service for online sales during the lockdown, in order to keep operations running while respecting social distancing.
What are the results and benefits of using the Geek+ solution?
www.imhx.net
With the pandemic causing a change in customer behaviour and an uplift in the number of purchases made online, Asda noticed that the demand for parcel collection and returns services had grown. At the same time, Asda’s toyou distribution service has expanded the number of retailers it supports. Over 100 are now available via the service, which has seen it process 65% more returns.
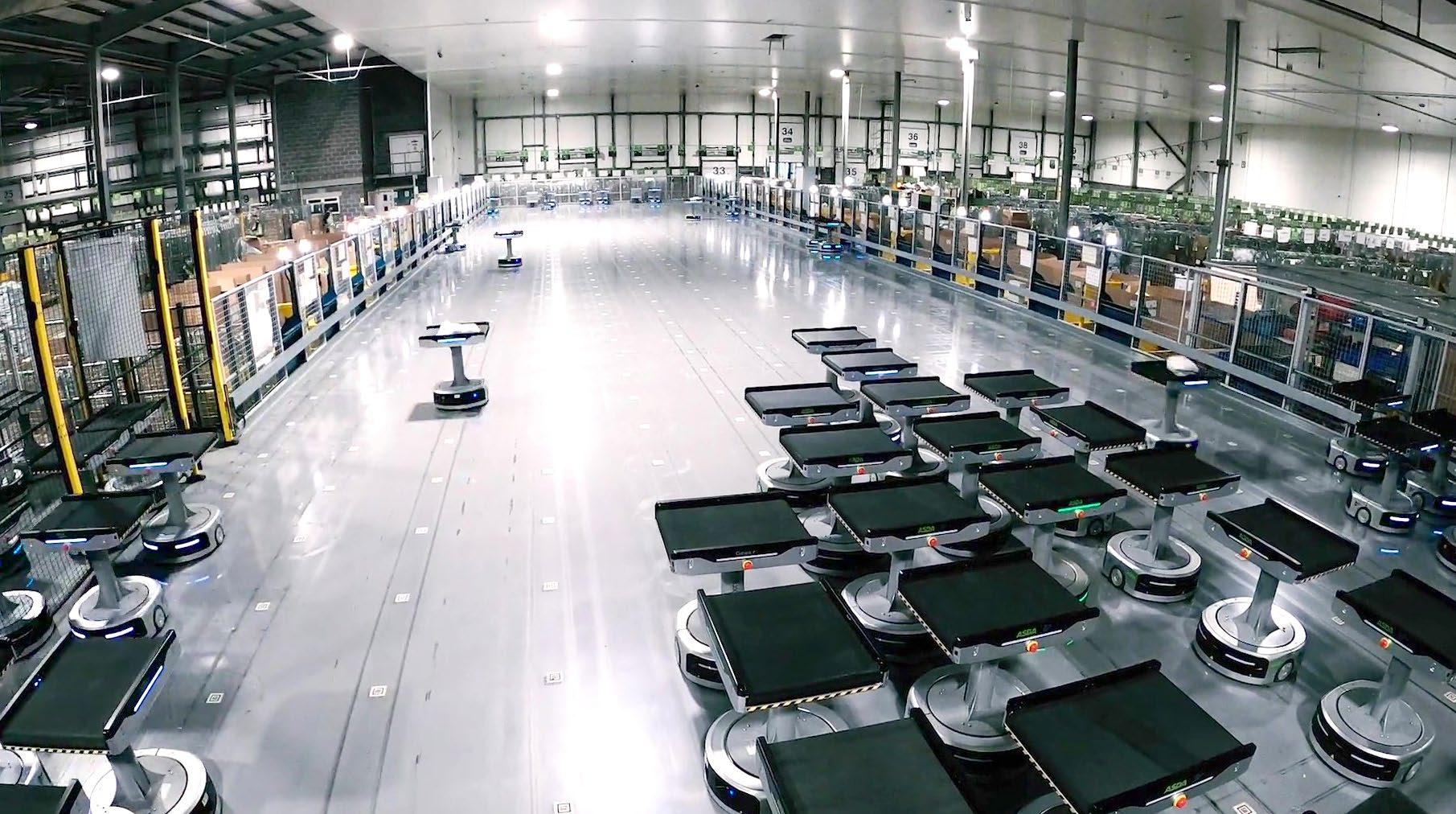
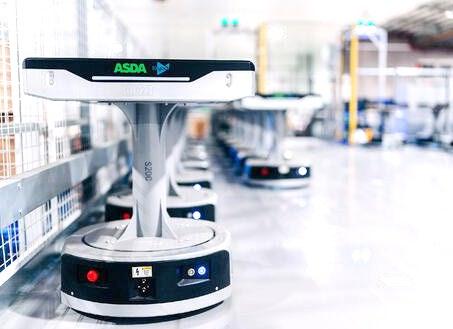
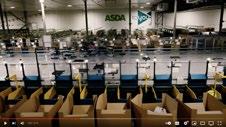
In Siemens’s warehouse, there are more than 200,000 SKUs, which makes the inbound, storage, and distribution of raw materials quite complicated. Siemens started to consider automation after they experienced a surge in demand for customized equipment, putting a strain on an already complex production process subject to inefficient storage of raw materials, labour-intensive material handling, and low visibility of the production process. After evaluating several automation solutions, the company chose the Geek+’s solution to create a more dynamic and efficient production process. They expect to be more competitive and able to cope with their fast growth after adopting automation.
www.imhx.net Geek+ streamlines Siemens’s operations with a one-stop robotic solution
www.geekplus.com CASE STUDY
Why does Siemens want to adopt warehouse automation?
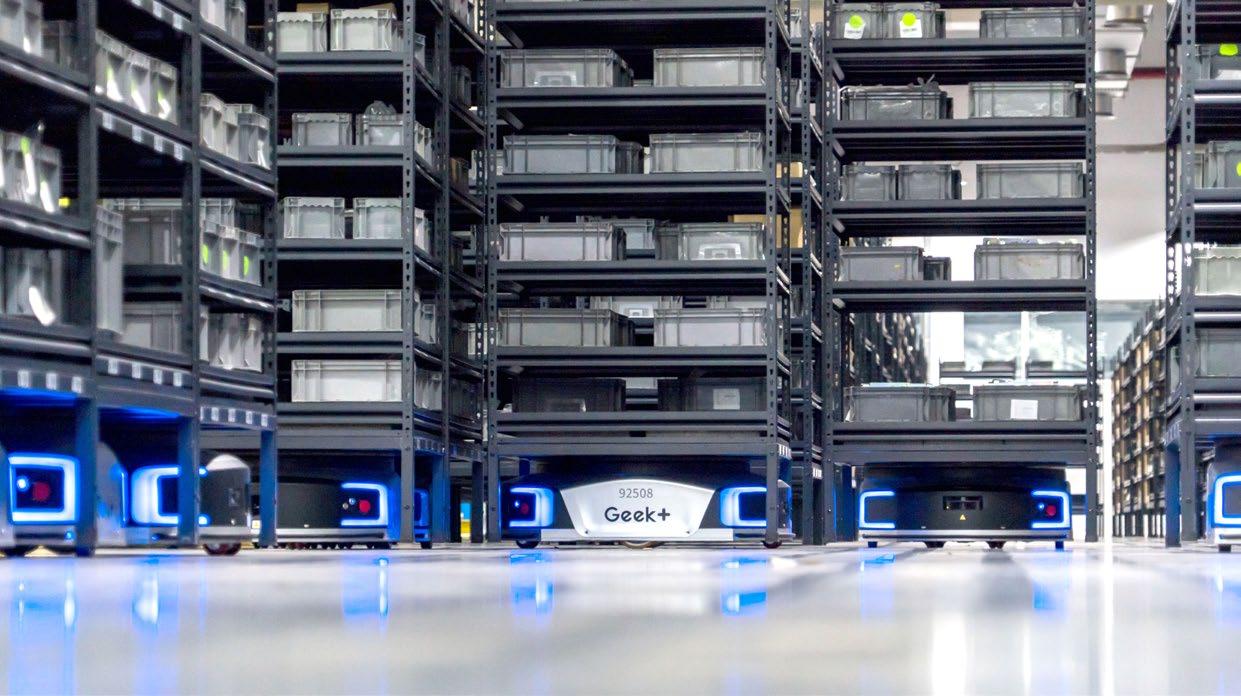
Geek+ has a full range of robots capable of fulfilling the needs of different parts of the whole material handling process at Siemens. In this project, Siemens applied four types of AI-driven logistics robots, including P800 goods-to-person robots, RS2 bin-to-person robots, four-way shuttles, and M1000 heavy-load handling robots. Through the seamless collaboration of Geek+ robots, Siemens has consolidated the process for receiving raw materials, quality checking, storing, outbound collection, and transportation of raw materials from storage to the production line. What are the results and benefits of using the Geek+ solution?
With digitalised automation, Siemens’s material handling processes have become transparent and traceable. The real-time information of goods is visualised with a dashboard, which makes management easier. With artificial intelligence and advanced algorithms, the inventory is rearranged according to usage frequency. This helps to make the picking process even faster. Further positive outcomes include 2-3 times more storage capacity, 99.99% accurate operations, 2.5 times greater storage efficiency, outbound collection process improved by 2.15 times, and 30% less manual labour needed.
www.imhx.net
What Geek+ solution is used in Siemens’s warehouse?
Watchwww.geekplus.comthecasevideo
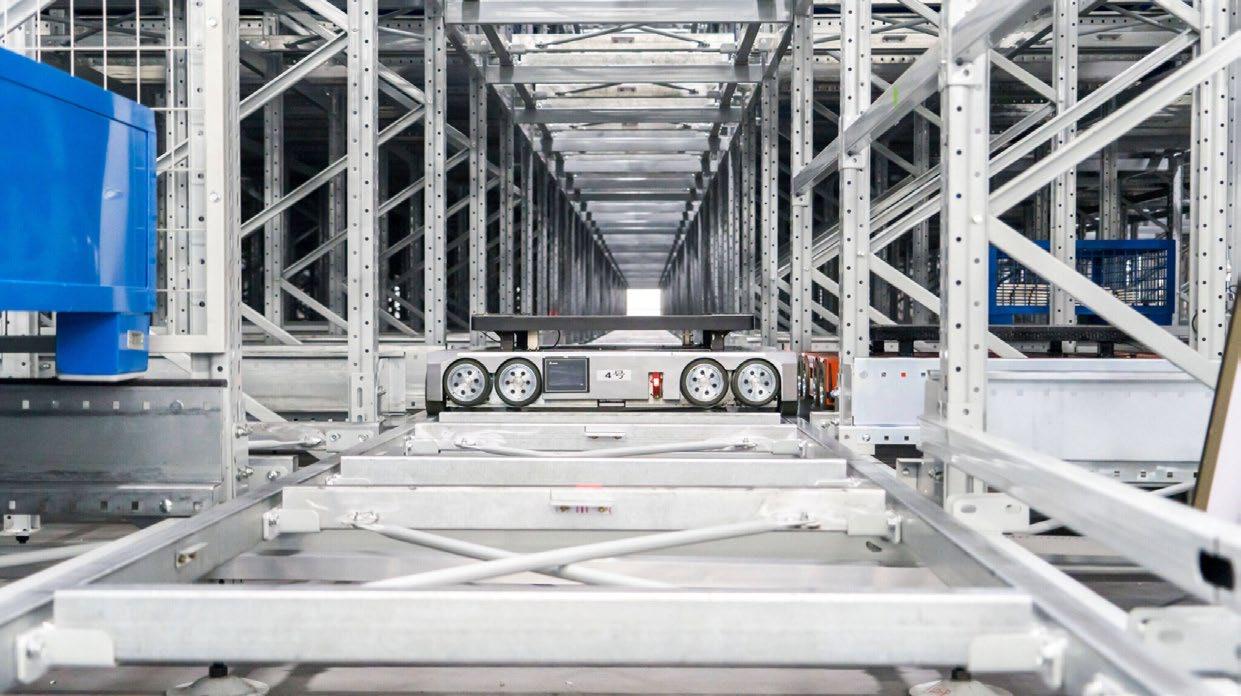
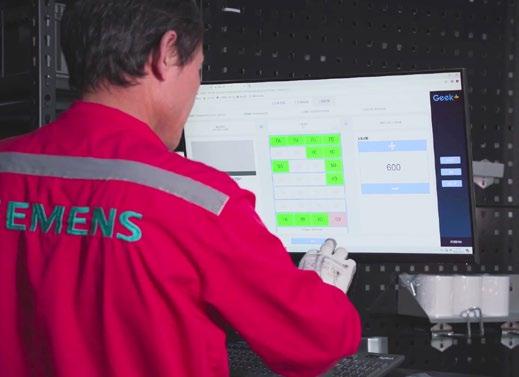

V3, Keckwick Lane, Sci-Tech, Daresbury Warrington, United Kingdom | Geekplus UK Limited +44 0800 048 7268www.geekplus.com sales@geekplus.com

#IMHX REGISTER NOW! TO BOOK YOUR FREE TICKET, VISIT IMHX.NET It’s been a long three years, but the wait is finally over. Get set for the UK’s must-attend intralogistics event of the year… IMHX 2022 | 6 -8 September | Live at the NEC Birmingham! LAST CHANCE FOR TICKETS TO THE UK’S PREMIER LOGISTICS EVENT! FREE TO ATTEND & NOW FREE PARKING!
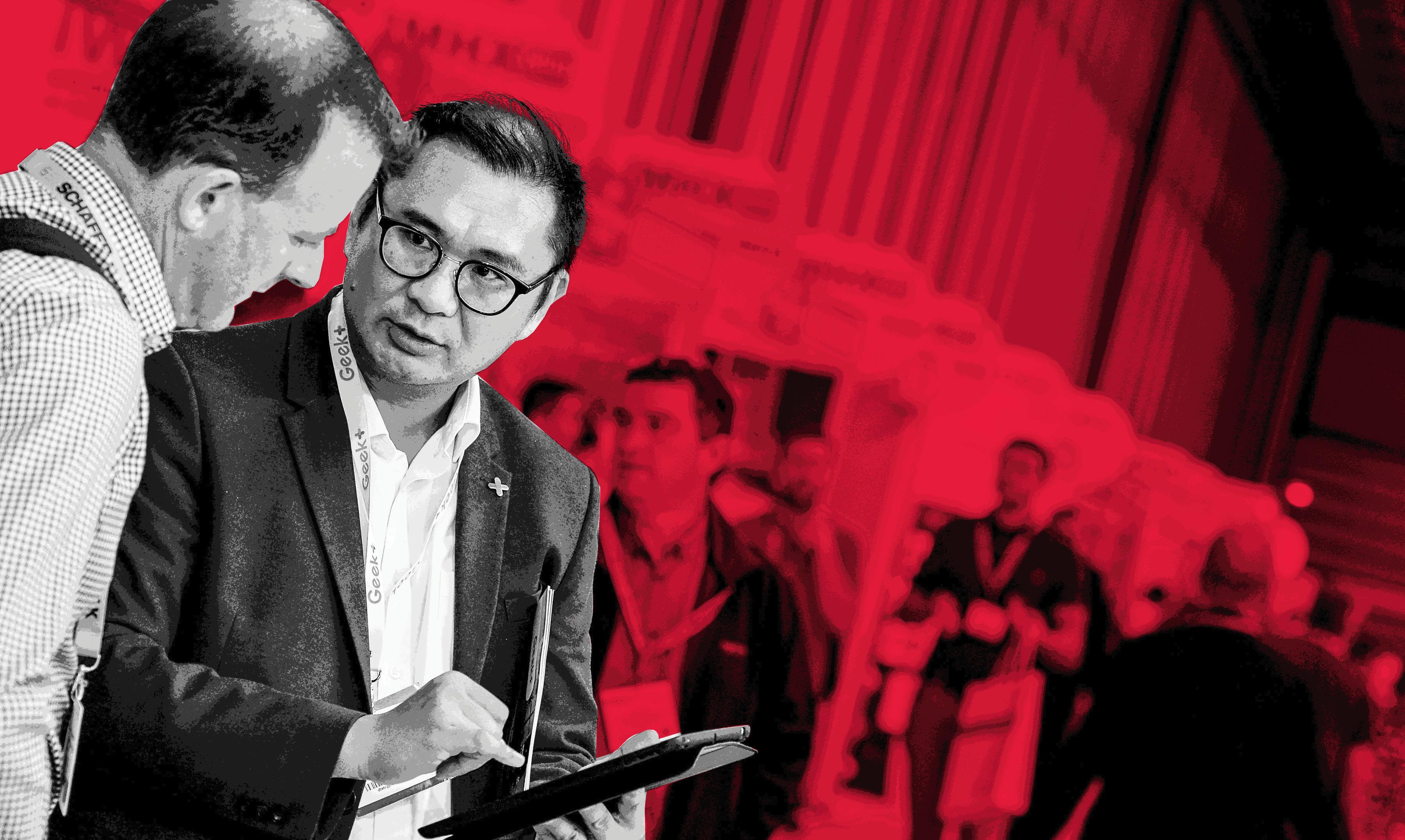