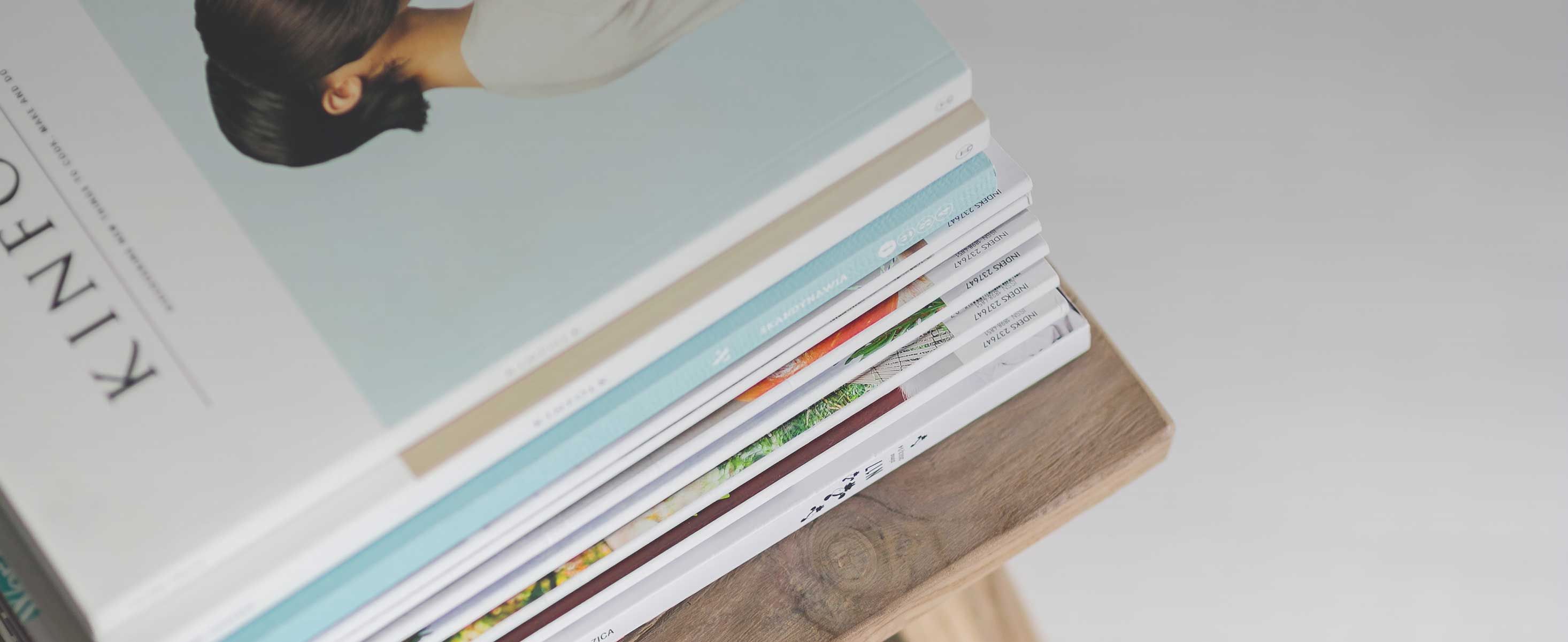
2 minute read
4.2 The secondary reformer
from Ammonia Production
by SheffieldMZ
Secondary reformer
Process air
Advertisement
Combustion zone
Water jacket
Catalyst
Refractory
Arch
Process gas
Process gas
CFD optimisation
The process gas leaving the primary reformer enters the secondary reformer at the bottom. The gas is routed through the central internal riser pipe into the combustion chamber at the top of the secondary reformer. Process air is introduced into this combustion chamber via nozzles, arranged at equal intervals round the circumference of the combustion chamber in two rows. The partially oxidised gas passes through the catalyst bed from top to bottom, the catalyst bed being supported by a ceramic arch. Finally, the gas leaves the secondary reformer through the outlet nozzle at the bottom. Particularly challenging areas in secondary reformer design include:
The transfer line fr om the primary reformer outlet to the secondary ref ormer.
The refrac tory lining including the ceramic arch which bears the c atalyst weight.
The burners.
Uhde’s answer to a safe and reliable secondary reformer comprises the following features:
A refrac tory-lined transfer line between the primary and secondary ref ormer which is only short as it is connected to the low er nozzle of the secondary reformer . Once in the secondary reformer, the gas passes through an centr al internal riser into the combustion chamber. This design eases duc ting and eliminates thermal stress between the tr ansfer line and the secondary r eformer.
A multi-layer r efractory lining with high-alumina bricks in the hot zones.
A ring-shaped ar ch made of high-alumina bricks that provides a highly stable suppor t for the catalyst. Due to the internal riser, the arch spans only half of the vessel diameter, r esulting in improved stability compar ed to other designs.
A multiple nozzle burner system comprised of nozzles equally distributed round the circumf erence of the combustion chamber at two levels.
Discharge of th e process gas from the central internal riser into the dome by rev ersing the flow direction. Air is added via a specific number of nozzles installed in the vessel wall at a defined angle, thus cr eating a vorte x flow in the combustion chamber. The vortex flow ensures optimised mixing of air and pr ocess gas. The flames do not come into contact with the vessel refrac tory or the central riser pipe.
A proprietary burner design, fir st applied in 1992, which avoids any metallic par ts coming into contact with the hot reacting pr ocess gas.
Since its introduction in 1968, the Uhde secondary reformer has proved to be a reliable item of equipment with a long service life.