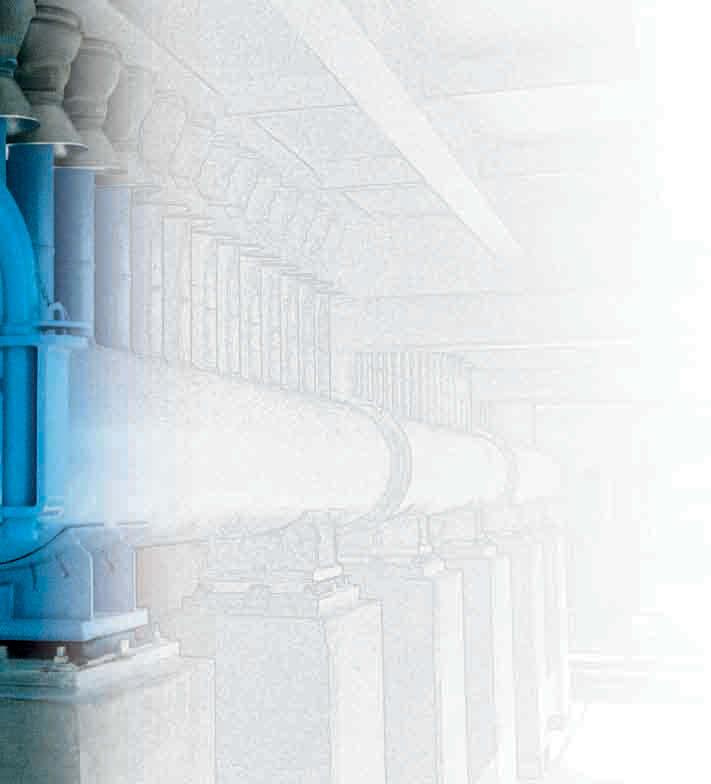
2 minute read
4.1 The primary ref ormer with a cold outlet manifold system
from Ammonia Production
by SheffieldMZ
The primary reformer with a cold outlet manifold system
Feed/steam
Advertisement
Furnace arch
Reformer tube The primary reformer is a furnace in which a multiplicity of tubes filled with catalyst are heated by burning fuel. The process gas temperature required at the outlet of the catalystfilled tubes is about 800°C at a pressure of approximately 45 bar. Inevitably, the service life of components such as the reformer tubes is limited. Material deterioration occurs through the combined effects of creep, alternating thermal and mechanical stresses, external and internal oxidation and carburisation.
Consequently, the furnace designer is faced with two main tasks:
Firstly, to minimise the number of components subject to wear and tear due to the combined eff ects of high temperatures and pr essures.
Secondly, to allow as smooth a nd safe an operation as possible.
The following main f eatures show Uhde’s approach to fulfilling the above requirements:
Top-firing for an optimum unif ormity of the tube skin temperature pr ofile.
Furnace bottom
Catalyst grid
Bellow
Gas conducting tube
Shop weld
Field weld
Carbon steel
Outlet manifold Skin temperature profile
Refractory
300 600 900 Skin temperature [° C] Small number of burners (in comparison with a side-fired ref ormer).
Internally-insulated cold outlet manifold sy stem made from carbon steel and loc ated externally under the reformer bot tom.
Internally-insulated ref ormer tube-to-manifold connection which operates at moder ate temperatures.
Each tube row is connected to a separate outlet manifold.
Advantages of the Uhde reformer:
No high-alloy outlet pigtails and /or outlet manifolds or risers which w ork at creep conditions.
Minimum number of components exposed to the severe pr ocess conditions.
Uniform temperatur e profile over the entire length of the reformer tube with the lo west possible peak tem perature, resulting in optimum utilisation of the ref ormer tube material.
No thermal expansion problems with the outlet manifold system. The slight remaining thermal expansions do no t have to be compensated by materials exposed to the severe pr ocess conditions. The design of very large single-box r eformers is possible.
The process g as outlet temperature is monitored for each tube row and is adjustable during oper ation for optimum reformer perf ormance and temperature uniformity.
Almost unlimited servic e life of the Uhde outlet manifold s ystem with no maintenance required other than painting.
Considerable operational allo wance of the outlet manifold system with r egard to process gas temperature and pr essure.
More than 60 reformers of this type have so far been designed and constructed since 1966. All have given excellent performance. The two largest units are equipped with 630 and 960 tubes, respectively.
Reformer tube-to-manifold connection with skin temperature profile


Fertiliser complex of AFC in Abu Qir (near Alexandria), Egypt. Capacities: 1,200 mtpd of ammonia 1,925 mtpd of urea 2,000 mtpd granulation unit