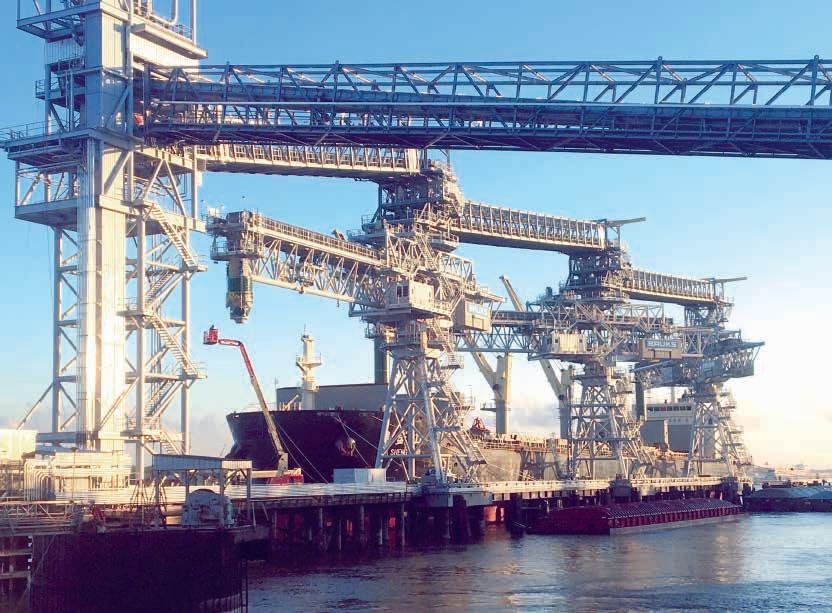
4 minute read
Dust-tight ship loading transforms southern USA grain export site
Grain handling can be a dusty business: ADM’s Ama facility left dust and spillage behind with the installation of enclosed ship loading systems from Bruks Siwertell; three years on and the site is setting new standards in effi ciency and environmental protection
TEXT Daniel Pace PHOTOS Bruks Siwertell
A LOT CAN HAPPEN IN A YEAR, and for one particular grain export site in Ama, Louisiana, USA, its ship loading and environmental protection capabilities were transformed. Owned and operated by one of the largest agribusinesses in the world, Archer Daniels Midland (ADM), in 2018, Bruks Siwertell completed the delivery and installation of three market-leading ship loaders.
ADM prides itself on the adoption of technology that enhances its ability to connect agricultural crops to world markets. It has a global footprint, but a firm operational infrastructure in the US. Headquartered in Chicago, ADM’s domestic operations comprise more than 160 ingredient manufacturing facilities and more than 300 crop procurement facilities, located across 29 US states.
Its scope includes grain elevators, ports and shipping terminals, which are used to store both raw agricultural materials and finished products. Many of ADM’s facilities are focused in the country’s major grain-producing states of Arkansas, Florida, Idaho, Illinois, Indiana, Iowa, Kansas, Kentucky, Louisiana, Michigan, Minnesota, Missouri, Montana, Nebraska, North Dakota, Ohio, Oklahoma, Oregon, South Dakota, Tennessee, Texas, Wisconsin, and Wyoming.
A terminal in the spotlight
ADM’s Ama, Louisiana, facility has been operational for decades and its equipment, which had once been fit-forpurpose, no longer was. “ADM recognized the need to replace its outdated and undersized ship loading technology,” explains Daniel Pace, Sales Manager, Bruks Siwertell.
DANIEL PACE, SALES MANAGER, BRUKS SIWERTELL
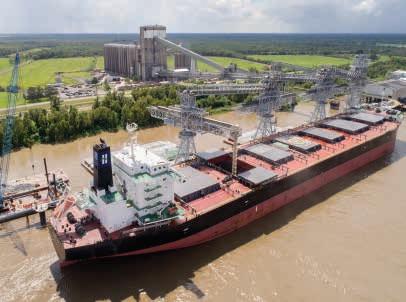
ADM’s Ama terminal features three pedestal-mounted, shuttling, slewing Bruks ship loaders
“The equipment had significant dust and spillage issues, as well as not meeting the company’s capacity needs,” continues Pace. “ADM wanted its ship loading system to be capable of accommodating post-Panamax sized vessels with enclosed conveyors, enclosed loading spouts and dust collection measures. Together these would provide the best possible dust control measures to protect the local environment.”
ADM was a new customer, and approached Bruks Siwertell for a solution following good references and seeing its technology working well and benefiting other operators in the agribulk business, but also wider afield for handling a range of dry bulk materials.
“We worked closely with ADM to establish its current needs, but we also considered the operational future of any installation, essentially to ensure long-term suitability and the potential capacity for growth as well,” he notes. “To maximize the effi ciency of a terminal it is important to tailor it to fit operational profiles, but as bulk terminal equipment lasts for decades it is also essential to ensure that there is flexibility in the system for some degree of change.”
Meeting customer needs
“Our ability to provide turn-key, tailored terminal solutions that are specially designed to meet specific customer needs, was a critical factor in ADM making that final
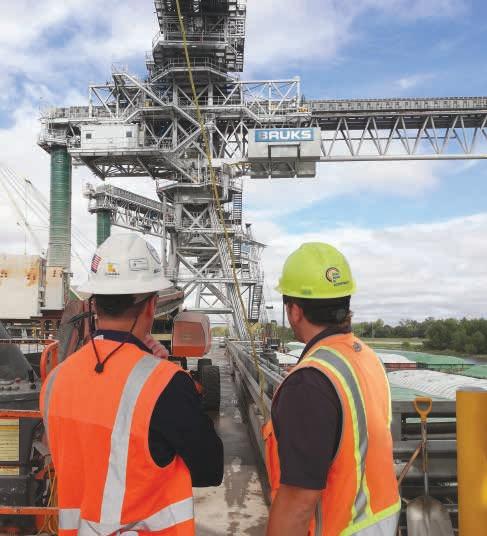
Each ship loader offers ADM a rated capacity of around 2,000t/h and can load post-Panamax sized vessels, up to 115,000 dwt and beam of 43m. They are in near-constant use and handle a broad range of grains including wheat, soya beans, milo, corn, meal, and dried distillers grains (DDGS).
Ongoing operational success
“The entire supply, installation and commissioning was undertaken in a year, and the results are impressive,” notes Pace. “ADM now has a system that offers completely enclosed dry bulk material handling, which not only eliminates waste from spillage, but crucially ensures that grain handling operations are dust free.
“The entire terminal has been vastly improved and now, three years on, ADM’s experience of our equipment speaks for itself. The ship loaders and conveyors are part of a flagship installation, setting grain handling standards in the US, and monthon-month, the Ama terminal continues to set new loading records,” he highlights.
An ability to provide turn-key, tailored terminal solutions was a critical factor in ADM Advances offer sustainability opting for Bruks Siwertell technology As operators replace outdated equipment, it should not only meet a company’s decision to adopt Bruks Siwertell technology,” explains capacity requirements, but also enhance environmental Pace. “Our US presence, and local 24/7 support, were protection. also extremely influential.”
ADM’s ultimate solution for the Ama terminal included three pedestal-mounted, shuttling, slewing ship loaders with completely enclosed loading conveyors, along with six totally enclosed belt conveyors to feed dry bulk material to the ship loaders. For this particular system, the operator requested spacious access platforms for easy maintenance. “We all have to be part of a sustainability drive, eliminating the unnecessary waste of cargo from spillage, and also protecting the environment from dust emissions. As dry bulk material handling equipment and technology advances, so too can our capabilities to significantly enhance the operational efficiency and sustainability of the terminals that rely on them.
The entire system was manufactured and pre-assembled into large, complete assemblies on the Harvey Canal and then carried on a barge to the terminal for final installation. It was commissioned in 2018 and has now been operational for almost three years. “We believe that ADM is one such operator; through its drive to improve the terminal equipment at Ama, the gains it achieved reached far beyond operational profitability, but have realized a wider accomplishment of significantly reducing its environmental impact as well,” Pace concludes.