
9 minute read
Prevention is the Pre dictive Cure! bulk handling in mining
SPECIAL FOCUS
Prevention is the Predictive Cure!
bulk handling in mining
Maintenance, repair, and operations (MRO) specialists require a comprehensive plan with a foundation founded on worker safety to effectively manage high-tonnage conveyor systems.
Understanding the benefits and drawbacks of reactive maintenance (RM), preventive maintenance (PM), and predictive maintenance (PdM) is necessary to create a strategy with objectives like minimizing unscheduled downtime, improving safety, increasing efficiency, and lowering overall operating costs to get a better return on investment (ROI).
Repairs made as needed
Many businesses still use their conveyors in what is known as reactive maintenance, which entails fixing whatever fails.
Components are allowed to continue operating until they malfunction, which causes unplanned, expensive, and disruptive system downtime. Unplanned production halts, ancillary equipment damage (when a damaged component harms something else), overtime, and emergency service charges are some of the expenses associated with this strategy.
Other drawbacks include uncontrolled budgets, potential safety risks, and a reduced asset life expectancy since components are not kept in the best possible operating condition. Furthermore, when under pressure to resume operation as soon as possible, technicians oftentimes take more chances and make more errors. Figures estimate 50% of all conveyor repair efforts in the typical North American facility use
this tactic, despite the obvious drawbacks of this approach. Budget is the apparent factor: Reactive maintenance involves less personnel, less preparation, and a smaller initial outlay. However, such a tactic results in inadequate planning, monitoring, and system management.
Preventive maintenance has taken over
Due to the shortcomings of reactive maintenance, a more preventive strategy has evolved to reduce failures that necessitate unscheduled shutdowns for repairs. Norms are frequently determined by length of service or business hours.
Performing routine maintenance on equipment to lower the likelihood of failure has been a component of PM virtually since the invention of the wheel. The same strategy is used by customers to prolong engine life when they bring their automobile in for routine oil changes.
Shifting millions of tons of rock, aggregate, and sand in erratic weather conditions puts a constant strain on bulk handling equipment and may result in dust emissions, spillage, and carryback. PM extends component life, boosts output, enhances overall effectiveness, and lowers maintenance costs. A successful PM schedule also needs to be adhered to strictly and updated frequently.
Some businesses handle this internally, while others discover that specialized service providers provide a higher return on their maintenance investment by relying on the knowledge and planned maintenance from industry specialists so their personnel can concentrate on essential tasks.
The PM method to conveyor maintenance often assumes that each component has a typical equipment life based on prior similar uses and circumstances. It may also assume that each component is triggered by time, metered inspection, or common signs (mistracking, spillage, etc.). The PM estimates the appropriate time to retire, replace, or repair pertinent parts prior to the anticipated failure point based on observation and experience. As a result, there is generally more safety, a more effective system, less leakage, and better overall system control.

The price of maintenance in advance
Calculating cost estimations based on the rate of failure derived from data of similar applications remains mostly theoretical because equipment life estimates frequently do not take into account performance in a range of service circumstances.
Given the environment, application, and operation schedule, PM is typically little more than a best-guess estimate (among several other variables).
However, a major problem with PM is that some parts will undoubtedly need servicing more frequently than necessary, increasing expenses, while others won't, resulting in subpar performance at best and catastrophic failures at worst. The ability to undertake maintenance on bulk handling systems is further influenced by the parts' accessibility, the equipment's age, the availability of skilled staff, and the rules governing each procedure.
There may be cool-down and ramp-up times needed for operations like coal-fired boilers, cement production, and smelting plants. These intervals might last days on either end of the maintenance work and add to the safety concerns (personal protective equipment, confined space entry, exposure limits, etc.).
Preventing future problems
To more precisely predict failure, predictive maintenance (PdM) closely analyses equipment performance while it is in use. It employs software and sensors to gather data over time, aggregate the facts, and use an algorithm to produce a useful result that is made available to stakeholders.
This kind of data-driven system gives service technicians and operations staff much more comprehensive, accurate, and usable information when used in conjunction with routine physical inspections.
SPECIAL FOCUS
As part of a managed service arrangement, certain component manufacturers provide structured conveyor inspections and belt-cleaning maintenance. Their monitoring systems can track component deterioration and inform the service professional and/or operations staff of impending servicing needs through wifi or mobile phone. In stance of not so desired conditions, the system will also transmit a notification via a mobile app, giving service professionals and plant operators access to real-time data. Some modern systems can even automatically change the tension of a belt cleaning.
When traveling to and from the equipment that has to be fixed and recording information in their reports, highly skilled service professionals add another set of eyes to the conveyors.
They frequently spot issues that general maintenance employees overlook or have grown accustomed to ignoring since they see so many varied applications. With factory-direct managed service, the provider is in charge of maintenance, freeing up the team to concentrate on other tasks.
PdM is based on the actual state of the equipment, as opposed to PM, which is decided by an average or predicted life statistic. When a possible problem is identified through predictive analysis, also known as "condition-based maintenance," a repair can be planned to have the least amount of an impact on production.
Benefits from a more automated, analytics-based system include improved system performance and component life, a decrease in the requirement for visual examination, and a reduction in guesswork. This method saves time and lessens possible risks for conveyor systems that can be miles long and, in some cases, traverse treacherous terrain, even though it does not entirely eliminate the need for manual inspections and maintenance.
The use of predictive maintenance
Data collection and storage are the primary tasks in a predictive maintenance program before moving on to analysis. Adding new sites of measurement used to be a laborintensive and expensive process, but wireless equipment have significantly lowered these expenses.
Some bulk material handlers are realizing that each important component can and should be monitored and studied to maximize performance as a result of more easily accessible data collecting, storage, and analytics choices. Additionally, data from sensors can be broadcast to mobile apps in the field through cloud-based software.
Although the initial capital investment for these systems may seem high, cloud-based technology might help offset some of the early expenses.
Extended equipment life, more accurate budget forecasting, more dependable maintenance scheduling, improved productivity, and higher worker efficiency all contribute to a quick return on investment.
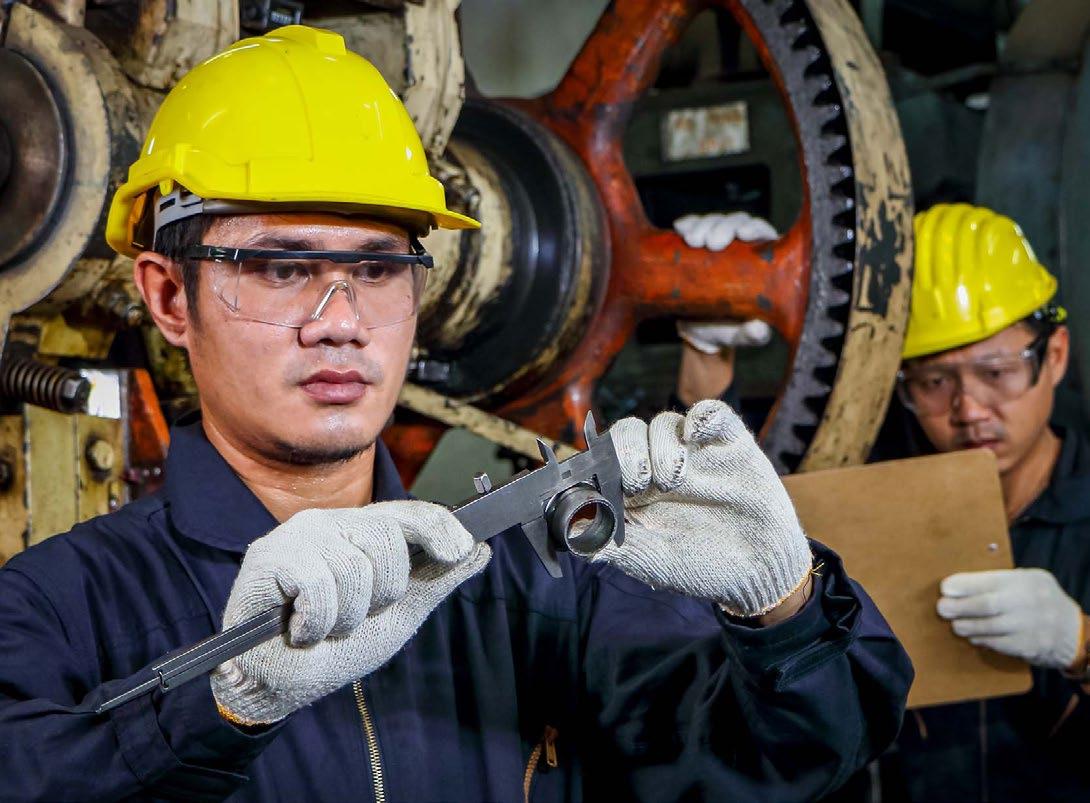
Computer learning
Machine learning adapts maintenance requirements to the operation and service environment, fed by all prior input, in contrast to preventative maintenance (PM), which depends on wear life defined by the manufacturer and/or operator observations.
The advantage is a customized experience that gives the impression that equipment is speaking to decision-makers directly about what it requires.
A belt cleaner position indicator, which monitors the blade and tracks and reports its remaining service life, is a recently marketed example. The user-friendly tool collects information on primary belt cleaners continually and alerts factory-trained service professionals and/or plant operations staff when re-tensioning or replacement is necessary or when abnormal situations
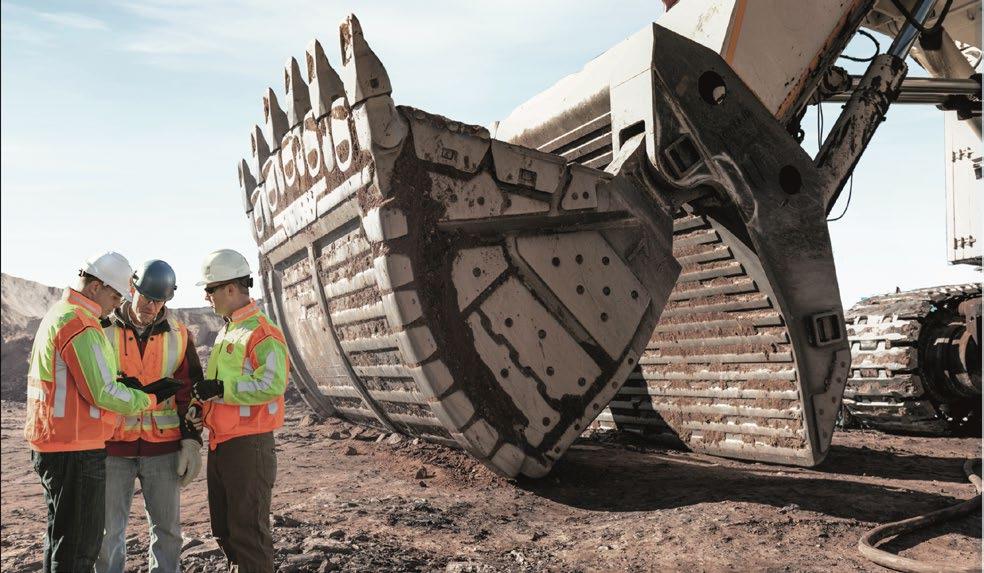
arise. Information on any networked cleaner may be instantly accessed by managers and service professionals using a mobile device or wifi.
The gadget increases efficiency and safety by reducing worker exposure to moving conveyors and delivering crucial real-time intelligence. By making precise information readily available, service employees may deliver and install replacement of worn parts during planned outages, simplifying maintenance planning.
The indicator maximizes the blade's usable surface area by relying on real operating conditions rather than human judgment to monitor blade wear and tension for the best cleaning performance. It also reports with confidence when a blade is getting close to the end of its useful life. A patent-pending device that combines the position indicator with an automated belt cleaner tensioner advances the technique.
This innovative powered assembly includes sensors that continuously check the pressure on the blades and change the assembly's position to maintain the best possible cleaning tension. The requirement for maintenance staff to manually re-tension each cleaner has been eliminated.
Instead, the chores are carried out automatically, cutting down on maintenance time while increasing each cleaner's useful space.
This elevates the idea of preventative maintenance to a new level by prioritizing real-time profitability and over-optimizing for a process parameter or other statistic.
Utilizing PdM and PM's combined power
Predictive maintenance is superior to preventive maintenance in many ways, but historically it has been difficult or prohibitively expensive to use it on all but essential parts. Additional parts and systems will probably join a plant's conveyor maintenance program as data collecting, storage, and analysis grow simpler and more affordable.
When they are brought on by random, anomalous overloads or a human mistake, unexpected failure events in bulk material handling systems operating in challenging operating environments can be challenging to foresee. Therefore, maintenance personnel must be able to respond to unexpected failures in some way. Managed service providers might make use of unscheduled downtime for equipment maintenance or upgrades.
In addition, some service providers are assisting clients with limited access to their facilities during the Covid-19 pandemic by remotely training maintenance staff to properly maintain their conveyor systems and providing instructions on preventive maintenance, inspections, and blade replacement options. Factory-direct technicians maintain regular check-ins and constant communication with management to ensure optimal performance.
Human labor will always be required to plan and implement solutions with the aim of a successful and economical maintenance schedule, just as data will always depend on human experience to be properly used. The optimal strategy is to take advantage of both PM and PdM benefits.
Because unscheduled downtime, prematurely degraded wear parts, and unnecessary labor have such a serious impact on the cost of operation, applying both methods to a maintenance strategy maximizes the effectiveness of both.