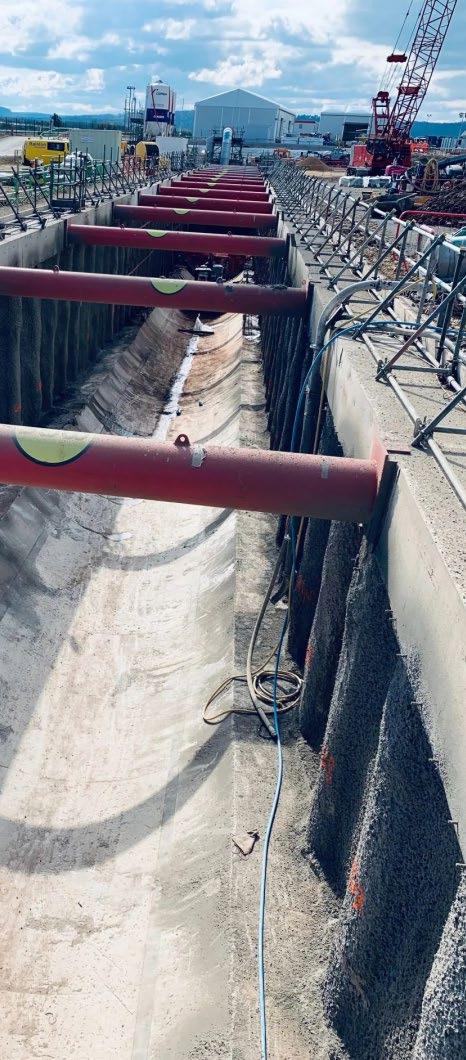
5 minute read
Resuming the Cut Task: Woodsmith Shaft Boring Roadheaders
SPECIAL FOCUS
Polyhalite Sirius Minerals Projects, North Yorkshire (England)
Resuming the Cut Task: Woodsmith Shaft Boring Roadheaders
The Woodsmith project in north Yorkshire has been on the radar for several reasons, making it one of the most closely watched shaft sinking projects in the industry at the moment.
It is a project that has lately changed hands, to start with. The 10 Mt/y project, which was initially managed by Sirius Minerals, was acquired by Anglo American in 2020. This acquisition resulted in a new perspective on the entire project execution phase.
The principal shaft sinking contractor, DMC Mining, was relieved of its responsibilities by Anglo American as a result of the ownership transition and reevaluation of plans
created by Sirius, a considerably smaller firm that was influenced by different investor demands and operational practices. The project's intended use of Herrenknecht's Shaft Boring Roadheader (SBR) technology is another reason to keep an eye on it.
The second generation of the technology, SBR 2.0, was put to the test in Belarus at the Slavkaliy-owned Nezhinsky potash project after making its debut at the Jansen potash project in Saskatchewan, Canada, where it excavated two blind shafts with diameters of 8 to 11 m down to a level of about 1,000 m deep. DMC served as the contractor for this project. Under the direction of the contractor Redpath Deilmann, it ultimately broke shaft sinking records while working on a project to sink two 8 m diameter shafts (one to 750-m depth and one to 697-m depth).
With its expertise in automated tunneling, Herrenknecht created the SBR for the automated sinking of blind shafts in soft to medium rock. According to the business, the SBR offers better safety performance compared to traditional shaft sinking methods while also attaining higher advance rates. It is based on the tried-and-true technology of the Herrenknecht Vertical Shaft Sinking Machine.
The SBR is a suspended shaft sinking machine that stands 60 meters tall and has 12 work decks and two service platforms. A partial-face cutting technique is used to extract rock carefully with a telescopic, boom-mounted cutting head.
The cutting head operates in cycles, beginning each cut from the center of the shaft to the shaft wall and repeating this process until a layer of material is removed. 1-m intervals of excavation are followed by SBR lowering sequences.
As opposed to the traditional drill and blast approach, the SBR was chosen for Woodsmith by Sirius because of its advantages in terms of enhancing safety and schedule. By abandoning the use of explosives and implementing this system, the corporation would be able to achieve a number of operational goals while also implementing a method of work that was safer and more predictable. The SBR eliminates the need for a linear procedure and enables work to be done as the shaft is being sunk, minimizing damage to exposed host rock and increasing safety while reducing downtime. As excavation progresses, workers can construct shaft lining and tubbing on work decks above the cutting head while waste rock is being removed by a pneumatic mucking system.
According to the Sirius plan, the third generation of technology will sink production and service shafts with a 6.75-m diameter to depths of 1,594 m and 1,565 m, respectively, at Woodsmith. This technology builds on the first two deployments. It includes, among other things, the addition of two retractable robotic probes to test and grout the ground ahead for safer excavation and an additional control cabin on the surface for more remote operation.
Four triple sheaved winches from SMS SIEMAG, as well as conveyors owned by Herrenknecht's H + E Logistik GmbH, are among the support equipment used for these SBRs. The "first cut" with the SBR in the service shaft was confirmed by former Anglo American Chief Executive Mark Cutifani in July of that year, marking the start of construction on the shaft.
This progress was made even though the company was still working on a thorough technical study of Woodsmith to guarantee the technical and financial soundness of the entire design. The development of the underground mining area, the sinking of the two main shafts, and the adjustments needed to accommodate both increased production capacity and the more effective and scalable mining method of using only continuous miners are all given particular attention in this review, according to Anglo American.
Since the first cut was made in July 2021, however, Anglo American and Redpath Deilmann—which is now in charge of the sinking project as shaft sinking contractor—have been reviewing the current plans for sinking with the SBRs, making minor hardware changes to the machines, and making sure all staff is properly trained to make the process easier to complete. The materials transport system (MTS) shaft's drill-and-blast sinking is another project that the Redpath Group is working on.
In the past, Woodsmith has considered a number of different shaft sinking rates, and Anglo American is presently striving to develop the best option for the plant-based on technical requirements.
Compared to the first two SBR operations carried out to this point, the sinking at Woodsmith provides a unique problem. To start, unlike what happened in Canada and Belarus, Woodsmith is not anticipated to experience ground freezing. Even though it takes a long time and is only used to freeze the unstable water-bearing layers near the shaft, this method can improve rock homogeneity and help maintain cutting rates.
Another level at Woodsmith to take into account is the MTS level, where lateral development work will be done around the 360-meter level to connect the production shaft with this level, from which polyhalite ore will be delivered by a 37-kilometer tunnel to Wilton near the port. This means that while the MTS level connection is being formed, vertical cutting and loading may be stopped.
The engineering work Anglo American is performing at Woodsmith will take into account all of these variables, as well as the success of previous SBR work. However, in terms of the SBR, there are indications that work on the service shaft may resume soon, with plans to begin sinking in the production shaft by the end of the year. www.skillings.net | 37