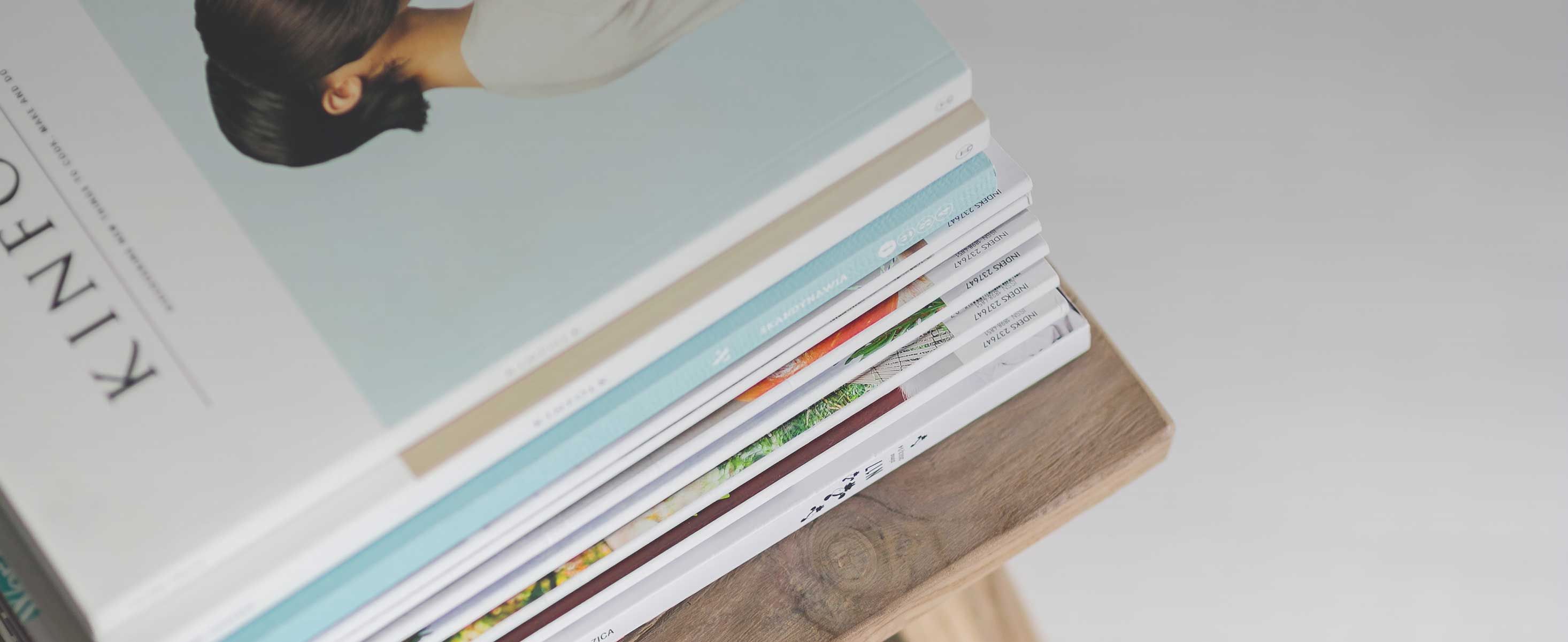
3 minute read
Making the digital manufacturing process concrete
The UK’s Explore Industrial Park, conceived and owned by Laing O’Rourke, is the most automated concrete products facility in Europe. For Laing O’Rourke, the Solibri software has been crucial for checking the quality of incoming data, and an essential tool for streamlining the design and ensuring everything works before it takes a physical form.
C O N S T R U C T I O N ’ S D I G I TA L MANUFACTURING REVOLUTION— I N T R O D U C I N G E X P L O R E INDUSTRIAL PARK
Advertisement
For centuries, the way we construct our world has remained largely unchanged. But now, particularly because of new technologies, we are witnessing the rise of automation, increasing productivity on production lines, while digital design information is helping to streamline processes and increase accuracy.
The shift into “offsite manufacturing” can be clearly witnessed at the UK’s Explore Industrial Park, which is concceived and owned by Laing O’Rourke – a global general contractor. Explore has manufactured concrete elements for some of the UK’s most impressive projects, including London’s Leadenhall skyscraper and Terminal 2 at Heathrow.
For the major projects at Explore, such as Manchester Airport’s Transformation Programme and Liverpool’s new specialist cancer hospital, it is critical that the digital data is accurate. Errors in production can slow the overall progress of projects, affect other activities out on the construction site and mess up the factory’s work schedule, costing time and money.
T H E I M P O R TA N C E O F D I G I TA L D ATA A N D H OW I T ’ S E N S U R E D W I T H SOLIBRI
When a project lands at Explore, Laing O’Rourke considers if there are elements that can be fabricated off-site. The process of Laing O’Rourke’s concrete manufacturing is highly automated, all the way from the distribution of concrete across the factory, the pouring of that concrete and the process of curing it.
To ensure the accuracy of their digital information, the team use Solibri Office to validate its contents.
“You’re able to streamline the design in the best way possible and ensure that everything works before it’s tangible in any way, shape or form. So, for us, it’s very key that we get the models and all our theoretical understanding of the entire structure spot on before it gets near the floor or sites.” Rehan Aneksha, the Design
Team Leader at Laing O’Rourke, explains.
“Having a safe system that is able to carry out these checks for us eliminates the possibility of human error and uncertainty, giving us a much better outcome in the way that the product is built. Information not being right has impacts to every single facet of the system. If you think about not just the safety and economy of the whole thing, it’s the environmental impact as well.”
With the help of Solibri’s software, the teams can seamlessly engage with and see the data, throughout the designers to those working in the field. Run on digital data, Laing O’Rourke’s use of Solibri during design, manufacture and final assembly is key to ensuring that the process runs smoothly, underpinning the success of countless projects.
“We look at ourselves as any other factory. We are trying to be the best we can be by looking at industries that are fundamentally ahead of the game in the way they produce things. So, we’re not trying to just be the best construction concrete facility we can be, we’re actually trying to be the best manufacturing company we can be.”
RIINA KEURULAINEN
RIINA KEURULAINEN
Product Marketing Manager at Solibri