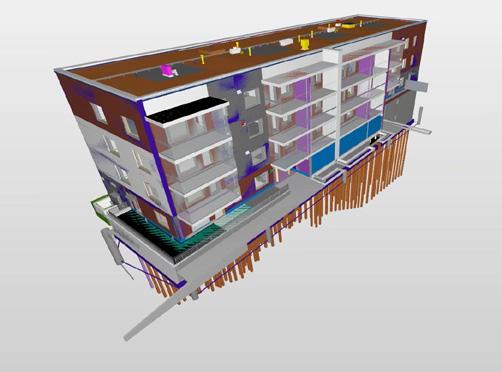
11 minute read
Customer Insights – Learning from others’ experiences
CUSTOMER INSIGHTS – L EA R N I N G F RO M OT H E RS ’ EXPERIENCES
Last December, we started a new webinar series called Customer Insights. The idea of the webinars is to share the experiences from our customers, how they use Solibri to find solutions to problems or challenges, improve quality, and increase efficiency. We wanted to offer a way for people to learn best practices and get ideas directly from other users. Here’s what we have learned so far.
Advertisement
JOIN OUR WEBINARS AT SOLIBRI.COM/CUSTOMERS TO VIEW CASES, VIDEOS AND STAY IN THE KNOW
D E M O H I G H L I G H T S
Viewing information in the different disciplines in the model to help seeing e.g. what the correct installation order is. Utilizing classifications with information takeoffs to help with site logistics and planning.
> VIEW THE FULL WEBINAR
Case Bonava Utilizing Solibri On-Site
Sampo Oksama shares experiences, use cases and needs Bonava have recognized in their construction sites in Finland.
Bonava is a leading residential development company in Northern Europe. Our speaker, Sampo Oksama from Bonava Finland, has over 10 years of experience from Building Information Modeling (BIM). His ambition is to challenge and revolutionize the construction industry with the help of BIM and digitalization.
“We did a pilot project on how BIM could be used more widely on-site. We gave a new tool – Solibri Site – for the site personnel for not only viewing the model, but also doing information takeoffs. BIM model is great for understanding what should be built. During the pilot we gained information on which on-site roles used the model: Site Engineers, Site Managers and Site Foremen all did. In my experience, the skills on-site for using this kind of tools has increased.
BIM models are used for communication every day – between site personnel and subcontractors. The people working at the construction are typically from different countries but understanding the BIM model does not require speaking the same language, so it helps communicating, for example, what should be done today. Our next steps are to continue and expand using the tool.”
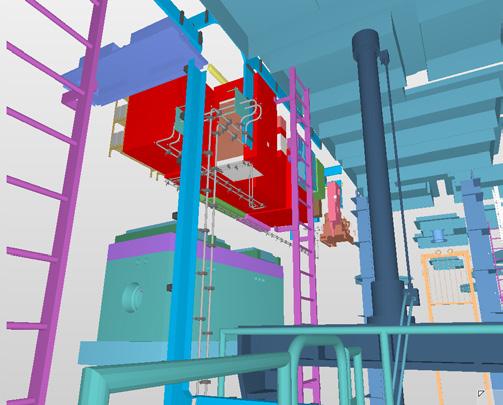
D E M O H I G H L I G H T S
Basic functionality of the COBie extension in Solibri and how to use it for structuring the data.
> VIEW THE FULL WEBINAR
Case Study Tideway – BIM Project of the Year 2019
Nigel Davies from Evolve Consultancy presents case Tideway, a major infrastructure project, and what choosing an Open BIM strategy has meant. The 2019 Construction Computing Awards chose it as the ‘BIM Project of the Year’.
Evolve is one of the UK’s premier BIM and design technology consultancies. Evolve Consultancy’s Director Nigel Davies has 20 years’ extensive experience within the AEC industry. He has unique insight and first-hand understanding of cutting-edge design and construction data production and exchange practices.
“Tideway is a large exercise to replace London’s sewers from the Victorian era. There are 24 work sites run by 3 Main Works Contractors. Construction started in 2016, and we are now about halfway through. We were involved already before 2016, looking at how the information should be delivered. We are talking about a huge amount of data, so right from the start we chose an open BIM approach for delivering the information. What is important is the structure of the data, not the tools used.
It is the Main Works Contractors respon sibility to validate everything, but we do spot checks on the information. We could not do this without Solibri – there is simply too much information to do it manually. So far, all the issues we have found can be easily resolved. Clearly, data is useless without validation and verification, and that is where Solibri steps in for us. If there is a clear logic, it is easy to automate it with Solibri.”
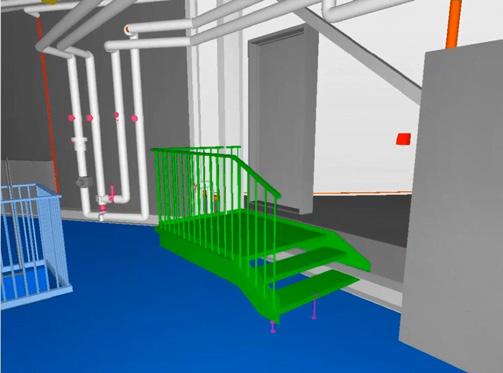
D E M O H I G H L I G H T S
Running checks in Solibri based on rulesets provided and communicating the issues. Saving Solibri resources and creating your own Solibri role.
> VIEW THE FULL WEBINAR
Case Copenhagen Airport Improving Quality and Communication
Michael Ørsted and Kenneth Passarge from Copenhagen Airport present how they have been able to improve the quality of projects and communication between different stakeholders, such as the Asset Managers. They also share how they have started to develop common rules with other major building owners in Denmark.
Copenhagen Airport is a building owner and operator in Denmark, and as an airport it is mid-sized with around 30 Million passengers yearly. The airport is open 24 hours a day, so the availability needs to maintain even if there are ongoing construction projects.
Michael Ørsted has been working at Copenhagen Airport for 12 years, and is the overall responsible for GIS, BIM and data to support building projects and daily maintenance. Michael Ørsted is the chairman of the Digitalization group within the Danish Building Owners’ organization.
Kenneth Passarge is responsible for BIM at Copenhagen Airport, and has been working with BIM for more than 10 years. Kenneth is securing that BIM is delivered timely and correct and is furthermore involved in the project of creating rulesets based on Denmark’s national regulations.
“We saw a lot of errors in our building projects, in many phases of the projects. Also, the communication about the demands was not working well. As the projects are getting more complex, the time consumed for the quality assurance was getting too high. For these reasons, we started a BIM initiative in 2016. We proved in the BIM initiative that we can save more than 4% on the project costs. This gave us a mandate to expand the usage of it.
We have aimed to translate our demands in HVAC, electrical, fire etc. into rules. We give everyone access to the rules. In our first project, our calculated savings were four times the investment. Our stakeholders have said the errors are reduced before the construction starts. The next step is to work with other Danish building owners to create a national rule system.”

D E M O H I G H L I G H T S
Using classifications to visualize installation schedule or to classify the model to different zones.
> VIEW THE FULL WEBINAR
Case Byggnadsekonomi I Didn’t See That Coming – BIM for Increased Productivity on Site
Johan Appelqvist and Jaakko Riekki from Byggnadsekonomi share some insight on how Solibri can be used for scheduling purposes and increased productivity on site.
Byggnadsekonomi is an award-winning total BIM consulting company in the Nordics. Johan Appelqvist is a professional scheduler and the CEO of Byggnadsekonomi. With more than 15 years of experience in BIM for production management, he is one of the pioneers in virtual construction and 5D solutions. At Byggnadsekonomi he has created unique and groundbreaking processes for BIM management.
Jaakko Riekki is BIM Specialist at Byggnadsekonomi. For the last 5 years he has been working onsite, implementing BIM based scheduling and Lean managing methods on major commercial projects in Helsinki region.
“We use Solibri full time – Office for quality checking and assurance, Site for quantity surveying, and Anywhere for communication with customers. We have about 30-40 active projects at the same time. We use visual way of planning together with the contractors. In addition, we use a more mathematical way in for example resource-based planning. This way we look for the most optimal way to build.
For this to work, we need to work with quality assurance. When you truly manage the development of your BIM model, you will have full traceability. To get quality assurance done, there are a lot of things you can do with Solibri: for example standard quality checking such as find missing elements, you can coordinate different models such as architectural vs structural, and make sure the model information is according to requirements. Solibri’s information takeoffs form a very good basis for schedule planning and optimization.”
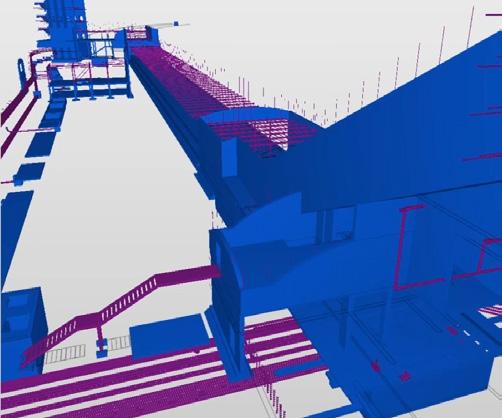
D E M O H I G H L I G H T S
Preparing carbon data in Excel and importing to Solibri. Utilizing classifications and information takeoff to visualize the numerical data in the model.
> VIEW THE FULL WEBINAR
Case Sweco Communicating Sustainability Aspects Using Value-driven Visualizations in Solibri
David Jirout shows how you can utilize cost and emission factors for coloring the model as a 3D heatmap to understand what parts of the design need to be revised from the sustainability perspective.
Sweco is Europe’s leading architecture and engineering consultancy, with projects in 70 countries annually throughout the world. David Jirout, Sustainability Coordinator for Sweco’s IT Consultants in Sweden, has his background in system development, BIM coordination and GIS. Merging his IT skills with knowledge gained in Sustainable Development program at Uppsala University, David’s job is about showing how IT and digitalization can be used to deliver measurable and tangible climate and general sustainability value in AEC projects.
“For me, Solibri has always been the first choice BIM tool that I have worked with as a BIM coordinator. But once we started to use it for visualizing carbon and cost at Sweco, it gained a new value. We have developed a service called BIM vision; its purpose is to help interpret carbon numbers. The idea basically is to simplify working with environmental questions. We connect carbon calculations with objects in Solibri. The model’s colors help you understand the carbon footprint – or costs – of your design.
Here’s an important message: if you are working in a big organization, it is very important that you have one really good integrated BIM manual that you distribute to all the projects, and that all the projects work with metadata in a similar way. Then you can create an extension for your organization that will work on some template, generic environmental data. Thus, no matter what IFC you open, you get all this carbon visualization work done with one click. Then we get insights, and upon insights we can act.”
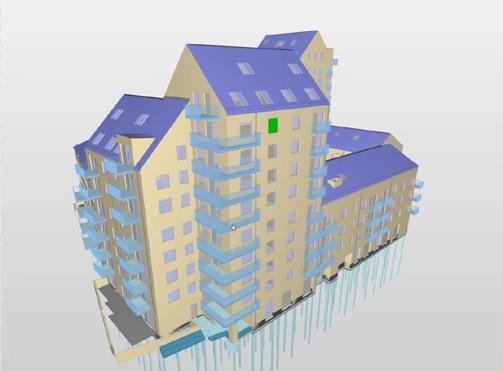
D E M O H I G H L I G H T S
Setting rules and utilizing information takeoffs to validate BIM requirements and help in construction planning.
> VIEW THE FULL WEBINAR
Case Skanska Achieving BIM Requirements
Joel Öman tells how to set BIM requirements, how models can be checked so that requirements can be achieved, and also how quantity take-offs and orders can be made directly from the model in Solibri.
Skanska is one of the world’s leading construction and project development companies, focused on selected home markets in the Nordic region, Europe and USA. Joel Öman works as a Digital Leader at Skanska in Sweden. He has almost 6 years of experience in BIM and digitalization in the building industry. In his work, Joel concentrates in creating more efficient ways of using software in order to save time and money in projects of all sizes.
“In Skanska, we have created documentation to achieve efficient design and obtain the necessary information in continuous phases of the project. Solibri is used for the validation of our requirements – we built a ruleset in Solibri that looks for the properties that are set in the documentation. We also use the powerful information takeoffs to capture quantities on for example materials we order from our suppliers. This way everybody from design to production is working on the same model.
We try to make the use of Solibri as versatile as possible. Many people working on-site don’t know how to use 3D models, this is quite new to them. So, we use it to extend knowledge of the project. We have got a lot of positive feedback from the Site Managers on how well built our models are. Our designers also want to produce something that is usable in the end, to feel pride in their work.”
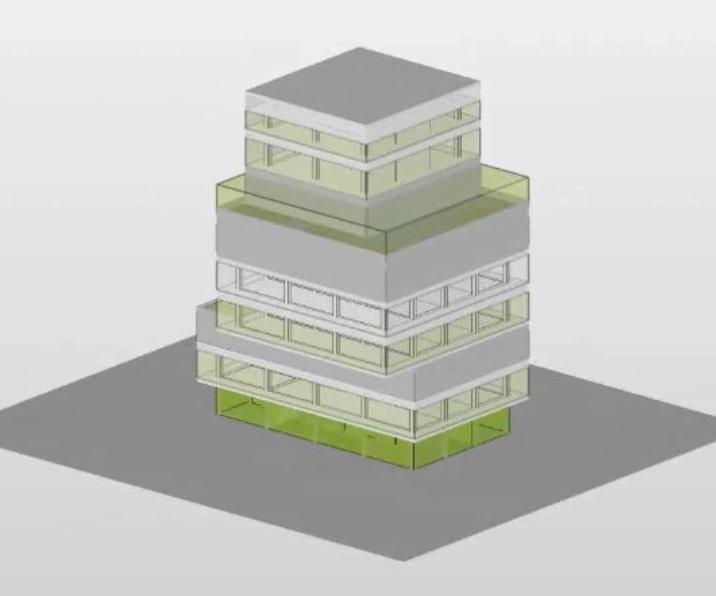
D E M O H I G H L I G H T S
What options to consider when exporting IFC files from authoring tools, such as Revit. Checking the IFC model properties in Solibri.
> VIEW THE FULL WEBINAR
Case Modelical Quality Beyond Clash Detection
Julio García and Sarai Zaballa from Modelical will be talking about quality assurance in residential projects.
Modelical, based in Madrid, is a modeloriented engineering company focused on project and process optimization for the building industry. Julio García is Modelical’s go-to guy for construction and 4D related matters. A Madrid Tech alumnus, Julio is a chartered quantity surveyor in Spain and has some extensive experience as site-work supervisor. Sarai is Modelical’s leading BIM consultant and Operations Officer. She has several years of experience in project design using BIM solutions and has conducted many Revit implementations and courses.
“Solibri is our preferred tool for coordina tion. Since Solibri is only using IFC models, it is important to have it clear how to export from Revit, ARCHICAD, Tekla or such. IFC files are very powerful, but only if they are configured and exported them correctly against the goals what you want to achieve. We have developed a tool to batch export IFC’s, because we have so many models that it would otherwise take too much time.
Solibri is not only clash detection for us. In Solibri we can go a bit forward, and check information in the models, and check relations between elements in the models, which we cannot do in other tools.”