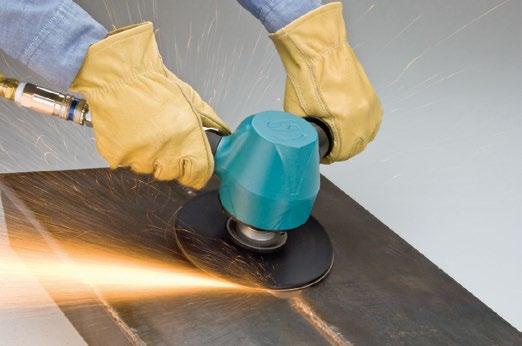
28 minute read
DESIGNED FOR PEAK EFFICIENCY
WE LISTEN. WE OBSERVE. WE OPTIMIZE.
WE LISTEN. WE OBSERVE. WE OPTIMIZE.
n Tools available in horsepowers ranging from .3 hp to 3 hp, with speeds ranging n Durable, American made air tools are ideal for rapid material removal, deburring, finishing and polishing. n Durable, American made air tools are ideal for rapid material removal, deburring, finishing and polishing. n Straight-Line, Right Angle and 7° Offset models offered in front and rear exhaust configurations. n Straight-Line, Right Angle and 7° Offset models offered in front and rear exhaust configurations. n Tools available in horsepowers ranging from .3 hp to 3 hp, with speeds ranging from 3,200 RPM to 100,000 RPM. n Tools available in horsepowers ranging from .3 hp to 3 hp, with speeds ranging from 3,200 RPM to 100,000 RPM. in Business 4.0 this month we discuss our industrial Machinery Digest industry X Blueprinting Workshop. These Workshops enable iMD to bring to your location our perspectives on the industry 4.0 evolution, trends in advanced manufacturing and machinery, access to our network of experts, facilitated examination of current state of operations, and next generation visioning for change in the form of a Workshop intended to yield actionable strategies for a digital operations transformation program. in Safety and Maintenance, our guest contributor Chris Kolb is Vice-president of Sales for Aerobotix, an innovative leader in robotic solutions for the aerospace and defense industries headquartered in Huntsville, Al. Chris looks at how robots can be used for handling toxic materials such as hexavalent chromium.
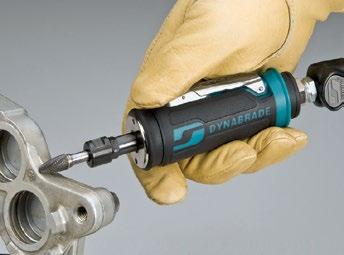


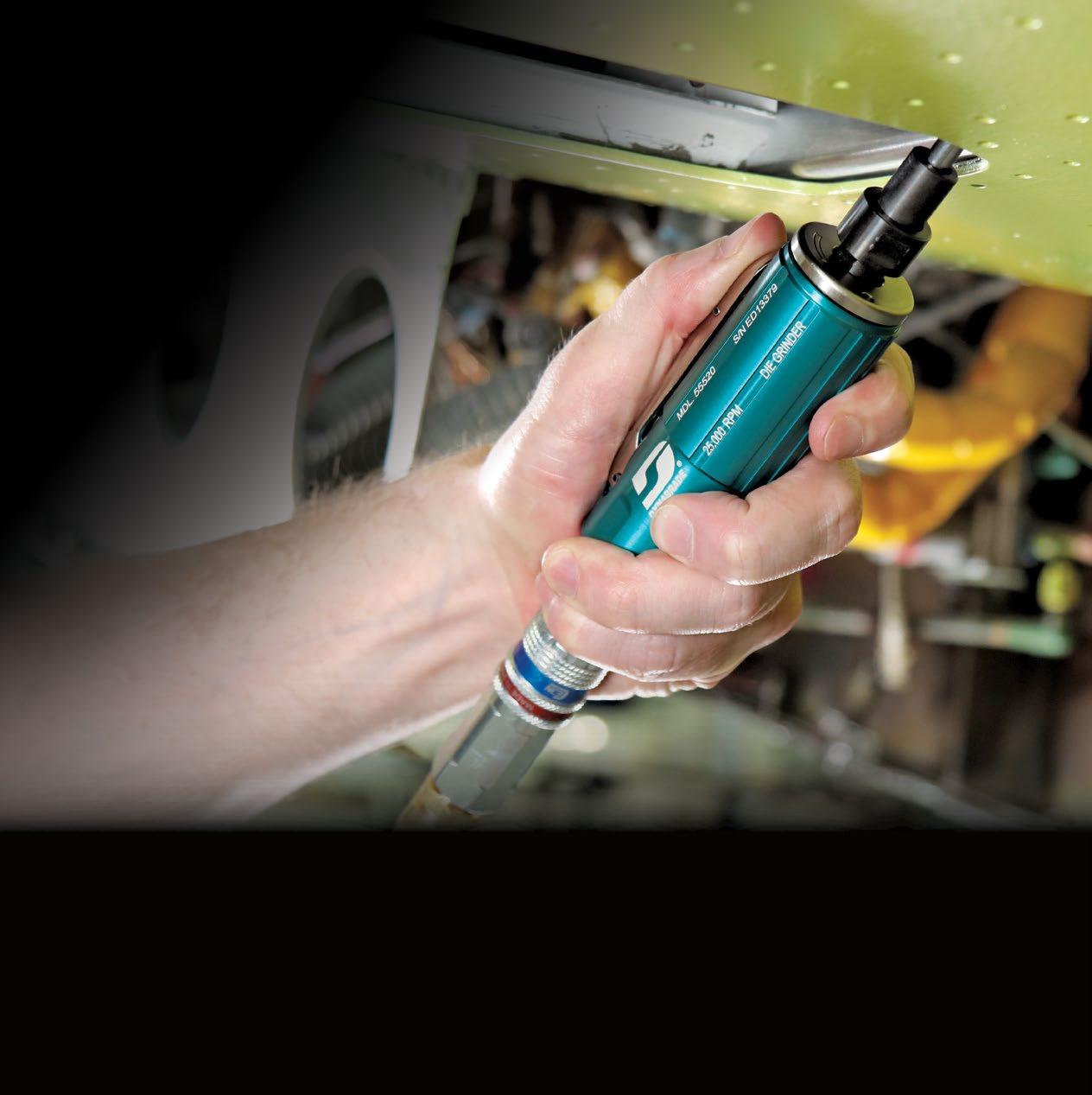
Contact us for a Free Tool Demonstration!
Contact us for a Free Tool Demonstration!
Q1 just wrapped up, and by the time you are reading this we will be well beyond the starting line for Q2.
The shininess from the new year has probably become a bit less reflective. Now is the time though to double down and refocus on leveraging your assets - in terms of people and technology and knowledge. We hope to provide you with some insight that will get you rolling again.
Our 1Q23 Quarterly issue focused on robotics has hit the digital racks, and we are accelerating toward more industry 4.0 insight with this edition for April.
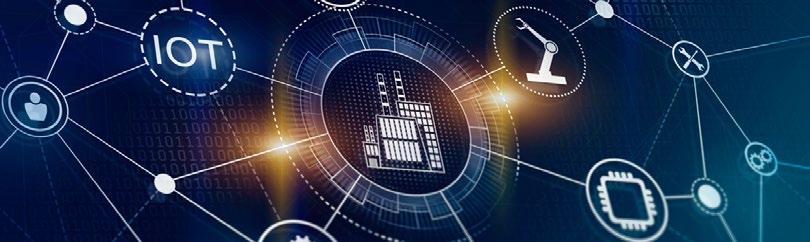
Talking Shop is a bit different in format this month. We highlight a Digitalization and Modernization Workshop in Michigan conducted by Executives from Schuler Group and Schuler North America in which they take a deep dive into their Smart press Shop. From VDp to lasers this is a working example of industry 4.0 in action. The backplane is Schuler’s Digital Suite for what they coin Forming Technology 4.0.

We feature some of the advances being made by Siemens in our News and industry insight sections. These include the new intralogistics vertical, as well as the Siemens Xcelerator platform. lasers are seemingly underutilized, but expanding rapidly due to their lower maintenance costs and high effectiveness in areas like cutting, marking, welding, and for instance cleaning. in our Schuler overview, lasers play a role. However, we also feature a contributed piece on how lasers can be used to clean surfaces in our industrial Automation section this month. We take a deeper dive on laser technology - how lasers work, a timeline on discoveries and the differences between fiber lasers and CO2 lasers, and some ideas on capabilities in our article from process called “The laser - our Modern lightsaber.”
Our Workforce Development section features The Smart Factory @ Wichita, in which industry leaders such as Deloitte, Amazon Web Services, infor, SAp, Dragos, Siemens, and Wichita State University have come together to build a working factory that features operating industry 4.0 use cases. This isn’t an idea on a wipe board, but rather a brick and mortar (well, really a metal and concrete and wind power and solar power and glass and digital and robotic and advanced net zero emissions) masterpiece. The factory provides among other things, a place for Wichita State students to experience first hand the impact of industry 4.0 on manufacturing.
Other industry news and several product showcases that have been curated by our staff will round out this edition. Hope you made it to proMat 2023 - ping me (trey@indmacdig.com) with your Workshop questions.
Keep building.
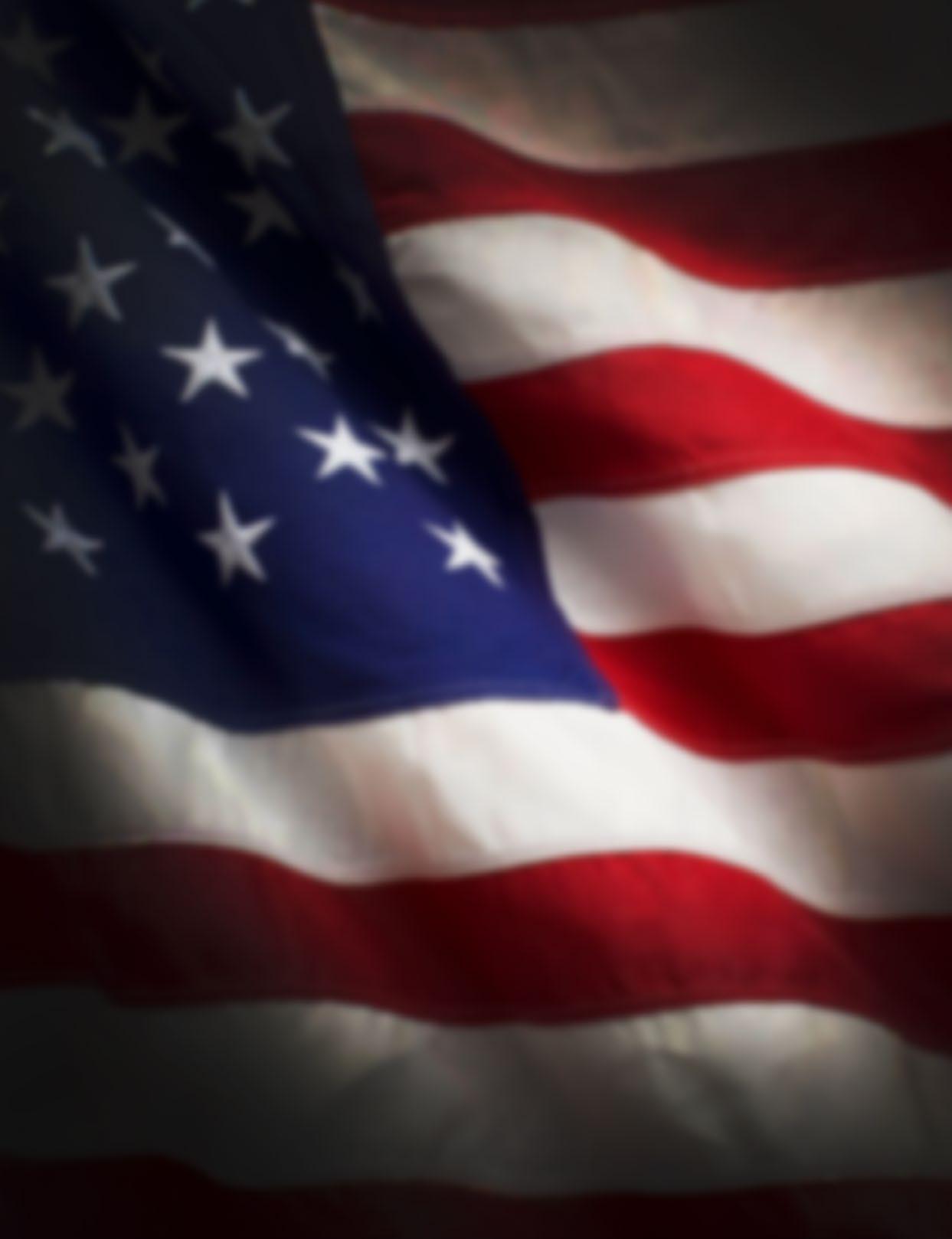
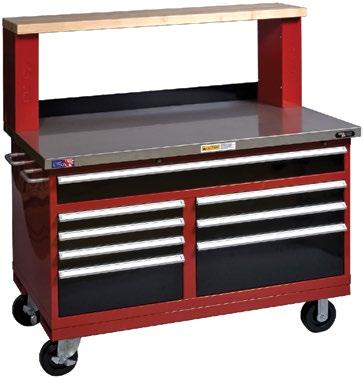
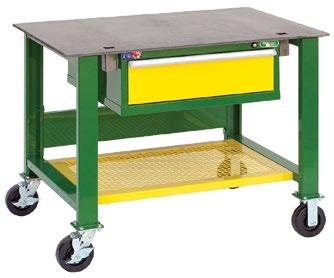

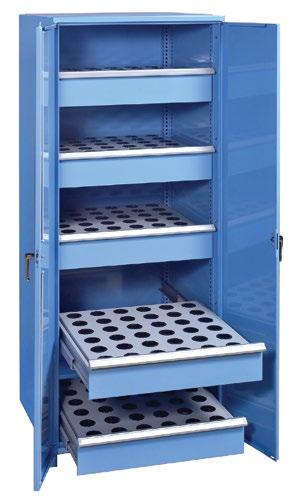

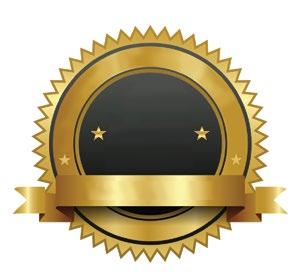
#Interoperability
Siemens to showcase TIA Portal v18
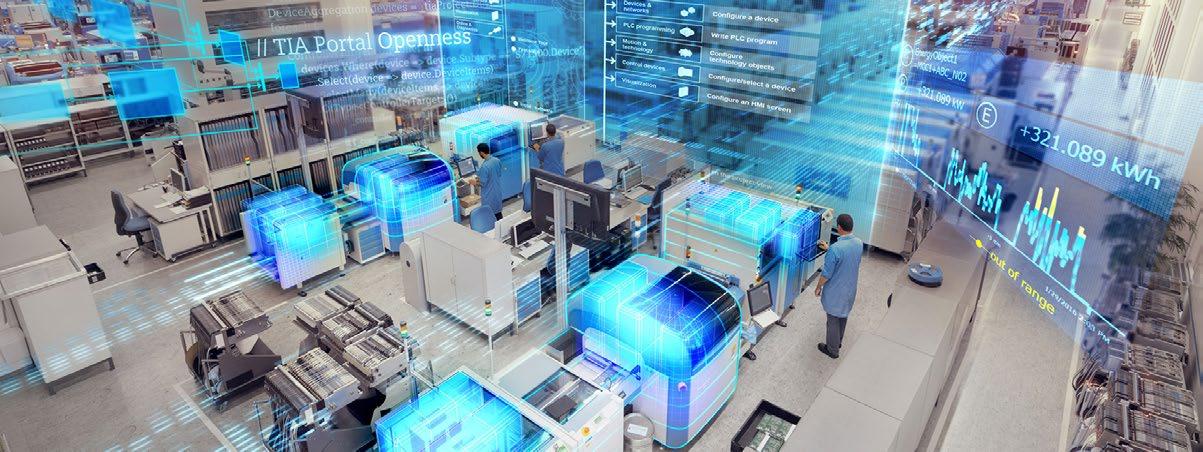
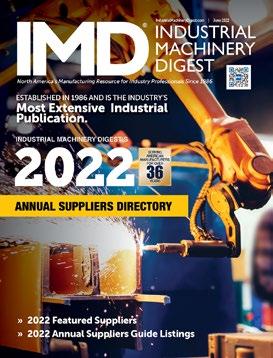
The new version of TiA portal boosts engineering efficiency with optimized functionalities for multi-user engineering, allowing users to work in teams and parallel on projects and build and manage shared libraries. in addition, access rights can be assigned individually or by group, making collaboration more flexible.
Siemens is expanding the TiA portal, an all-in-one engineering ecosystem with iT-oriented workflows, by integrating Simatic Automation Xpansion (Simatic AX). This integration provides iT professionals with a familiar development environment based on Visual Studio Code and version control via Gitl ab. Object-oriented libraries can be created in Structured Text and integrated. OT and iT users can use the engineering platform without reskilling. This development is a decisive step towards iT/OT integration and counters the growing need for more skilled workers in the OT world. Simatic AX is available as a cloudbased service, allowing projects to be easily downloaded and updated at any time and place.

Version 18 of TiA portal also offers simple and holistic engineering of 5D/6D kinematics, enabling motion control functions across six interpolating axes. This flexibility allows companies to expand, convert, or modify production facilities - without interfering with running systems. The scope for TiA portal and Simatic controllers has also been further extended, with the Simatic S7-1500 and the Simatic ET 200Sp providing higher computing and communication performance and supporting r 1 redundancy. This functionality ensures the maximum availability of applications and helps solve future automation challenges. in addition, the r 1 redundancy can be quickly and flexibly integrated into existing networks with no programming effort, making it one of the most straightforward solutions on the market that can be used in various applications - factory automation, logistics, or infrastructure. The new hardware also supports the latest security standards, with the Version 18 release focusing on state-of-the-art security improvements. in short, TiA portal version 18 offers even more efficient and flexible automation engineering thanks to enhanced team-collaboration functionalities, iT/OT integration, the advanced engineering of kinematics, and maximum availability through r 1 redundancy. As a result, it's a tool well-suited for industrial companies looking for efficient automation engineering that can be quickly modified to meet new requirements, shorten time-tomarket, counterbalance the lack of skilled workers, and most importantly, always remain competitive.
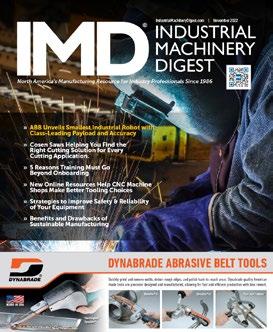
#Lasers
TRUMPF Inc. Breaks Ground on New Smart Factory Production Expansion
Groundbreaking ceremony in Farmington, Connecticut marks the beginning of construction // Expansion will house sheet metal production and Smart Factory to manufacture TrUMpF inc. laser cutting, bending and welding machinery
TrUMpF inc. has begun work on expanding its local manufacture and sheet metal assembly of fabricating machine tools in Farmington, Connecticut. The North American subsidiary of the high-tech TrUMpF Group will add 55,800 square feet to its production building for the manufacture of laser cutting, bending and welding machinery. The project is part of ongoing recovery efforts related to damage sustained after a plane crashed into the production building in September of 2021. TrUMpF will invest an estimated $40 million into the project which will include a Smart Factory that demonstrates advanced automated and connected precision sheet metal production.
Construction on the project has begun and is expected to be completed by May of 2024. The building was designed by renowned architectural firms Barkow leibinger and Tecton Architects. More than 620 of TrUMpF’s approximately 1,500 North American employees work in Connecticut.
The Connecticut Smart Factory project will become TrUMpF’s fourth Smart Factory worldwide and second in the United States. TrUMpF inc. opened its first U.S. Smart Factory just outside Chicago in 2017. in the past five years, more than 8,000 manufacturers have visited the working model of connected manufacturing and TrUMpF has helped create approximately thirty other Smart Factory projects for large OEMs and smaller manufacturers across the United States. in 2022, more than 2,000 people visited TrUMpF in Connecticut for technology demonstrations or training, and more are expected to visit once the new Smart Factory is complete.
The privately held global TrUMpF Group, which celebrates its 100th anniversary this year, opened the North American subsidiary in 1969 and began manufacturing in Connecticut in 1974. Dedicated to meeting customer demand for proximity, TrUMpF inc. also maintains additional offices in California, illinois and Michigan.
Find out more about T rUMpF at www.trumpf.com
#DigitalTwin
Siemens presents software for Real-Time Locating System (RTLS)

“Location Intelligence” software expands SIMATIC RTLS location platform to include the Digital Twin of performance and warehouse location intelligence will also provide manufacturers with a digital twin of warehouse logistics. Warehouse content can be easily visualized with real-time maps or a custom-built dashboard to implement and support FiFO or liFO concepts. it can even enable a “pick by light process” by using signal lights or lEDs of the transponder that trigger a visual notification if a work order remains immobile and needs to be moved to the next production step. in addition, the combination of location and business information leads to transparent processes: searches are reduced to a minimum because the positions of all relevant objects on various terminals are visualized in real time. Bottlenecks or deviations from the production schedule can be avoided, workflow anomalies identified, paperless order information retrieved, and material flow and order status assessed. At the same time, previously untapped potential for optimization in the factory can be identified through real-time analyses and rapid decision-making.
Siemens “ location intelligence” software expands the SiMATiC rTl S (real-Time locating System) locating platform to include the digital twin of performance and warehouse. The web-based software analyzes and visualizes dynamic data, processes events, and can be addressed directly from local Erp (Enterprise resource planning) or MES (Manufacturing Execution System) systems. The intelligence acquired based on position data provides the user with a comprehensive overview of material flow, order information or possible problem areas.
The transponder iD is linked to the existing order data. Depending upon the process step and order status, order information can then be displayed on the SiMATiC rTlS epaper transponders, providing a paperless solution. location intelligence also offers users the opportunity to track individual workpieces or the entire order in real time. When the order iD is entered, the real-time positions of linked transponders are shown on the customer’s digital card.
With a real-time locating technology, warehouse space can be utilized efficiently, the correct goods in the right amount at the right time will be made accessible for manufacturing, shipping and distribution while increasing delivery accuracy and processes quality.
#IoT
Accelerating the digital transformation of the machine tool industry with Siemens Xcelerator
» Siemens Xcelerator includes selected portfolio of ioT-enabled hardware,
» software and digital offerings for the machine tool industry
» Software applications for cloud, edge and customer servers with numerous innovations for the machine tool business
» First partner applications based upon industrial Edge for Machine Tools, the open ecosystem for ioT
Siemens demonstrates how the enormous potential for optimizing machine tools can be utilized, thanks to the continuous analysis of production data. With the open digital business platform Siemens Xcelerator, ioT-enabled hardware and software, the company demonstrates how the physical world can be connected to the digital world. Such a portfolio accelerates digital transformation and enables flexible and sustainable action both in the building of machine tools and in use.
Apps for the machine tool business with Siemens Xcelerator
Siemens recently launched an open, digital business platform called Xcelerator. By doing so, the company seeks to enable customers of all sizes in the fields of industry, buildings, power generation, public utilities and mobility to accelerate their digital transformation and increase value creation. The business platform makes digital transformation easier, faster and scalable. it comprises three cornerstones — a curated portfolio of internet of things (ioT) enabled hardware, software and digital services from across Siemens and certified third-parties; a growing ecosystem of partners; and an evolving marketplace to facilitate interactions and transactions between customers, partners, and developers.
With applications such as Manage Myresources / Tools, Manage Myresources /programs, Analyze Myperformance /OEE, Manage MyMachines, Manage MyMachines /remote and Analyze MyMachine /Condition, as well as the industrial Edge for Machine Tools platform, Siemens also provides offerings for machine tools via Siemens Xcelerator, both for the machine builder and CNC machine users.
Numerous innovations for machine tool apps in the area of work preparation, Siemens is presenting several innovations at iMTS in Chicago this year for the applications Manage Myresources /Tools, Manage Myresources /programs and Analyze Myperformance /OEE.
The apps provide intelligent resource management that allows production orders to be prepared smoothly by providing the right tools and NC programs. A central solution at the manufacturing level manages real instances of tools, tool locations and programs for parts production, using the data from the CNC. Workflows in machining environments are optimized, tool circulation and tool inventory are efficiently organized.
The utilization of production capacities can be improved by analyzing overall equipment effectiveness (OEE). All three applications offer innovations, for example, with broader connectivity even for CNC machines that are not equipped with Siemens SiNUMEriK CNC, a significant development. This means nothing stands in the way of a shopfloor-wide connection of machines to resource management. in addition, Manage Myresources /Tools can now provide further valuable insights into tool usage, such as the duration of the different life phases for certain tool types.
Also new is the possibility of more efficient tool planning with reservation of tools for a machine or production order or as a standard tool. With the help of unloading lists for balancing, the planning of tool requirements will become even more efficient in the future.
For Manage Myresources /programs, additional use cases can now be covered by the possibility to add additional file types such as drawings to NC packages. in Analyze Myperformance /OEE, machine status can now be configured individually. in addition, the app provides detailed insights into workpiece statistics and production progress.
For the monitoring of CNC machines during operation, Siemens is also presenting innovations for the already available apps Manage MyMachines, Manage MyMachines / remote and Analyze MyMachine / Condition at iMTS. These apps analyze the data generated during workpiece machining, which can then be used to improve maintenance planning. Unexpected changes, for example, in machining performance or vibration, indicate disturbed processes. in the new version of Manage MyMachines, it is now possible to examine reports of technical faults even more closely. Also new is the now seamless transition between the two apps Manage MyMachines and Manage MyMachines /remote, which further improves the user-friendliness and efficiency of service calls. Manage MyMachines is now also available with broader connectivity, which supports machine controllers from other manufacturers.
Open Siemens Industrial Edge for the Machine Tool ecosystem
Siemens openness to partners is demonstrated by the i ndustrial Edge for Machine Tools ecosystem. Based upon the Siemens Edge p latform, Schunk, the global manufacturer of gripping systems and clamping technology, developed its iTendo Service. By combining sensor data from the tool tip and data from the NC, Schunk wants to help machine tool operators improve the machining process and prevent tool breakage.
Siemens will accelerate digitalization for a sustainable tomorrow by demonstrating how the enormous potential for machine tool optimization can be utilized, thanks to the continuous analysis of production data.
#Robotics ABB to expand Robotics factory in US
investment of $20 million will increase production at its existing Auburn Hills facility and strengthen ABB’s US leadership
Newly expanded, highly automated facility will create new jobs in the state of Michigan
Expansion featuring the latest in automated and advanced manufacturing processes to open November 2023
Today, ABB strengthened its commitment to one of its largest customer markets – the US –with construction starting on the expansion of its existing North American robotics headquarters and manufacturing facility in Auburn Hills, Michigan. The project is expected to be completed in November 2023 and represents an investment of $20 million. The expansion will create 72 highly skilled new jobs in the area and is supported by a $450,000 Michigan Business Development program performance-based grant.
Adding to the $14 billion ABB has already invested in the US since 2010, the latest investment in its robotics headquarters and factory will benefit customers in the Americas, particularly those in growth sectors including electric vehicles, healthcare, packaging and logistics. With the expansion set to significantly increase the factory’s production capacity, it responds to the increased demand for automation from 70 percent of US businesses looking to bring production closer to home, as revealed by ABB robotics’ survey of 1,610 executives in the US and
Europe in June 2022.
ABB robotics moved into the 538,000-square-foot building in 1993 and opened the manufacturing plant in 2015, becoming the first global industrial robotics company to fully commit to a North American robotics production footprint. The expansion and increased use of automation in the factory will create new jobs, supporting the ABB robotics packaging & logistics Headquarters in Atlanta, Georgia and the robotics lifesciences and Healthcare Hub located at the Texas Medical Center in Houston, Texas. ABB already has a workforce of approximately 350 employees at Auburn Hills.
ABB’s footprint in the US is more than 20,000 employees over more than 40 sites nationally.
“The expanded facility will feature the most advanced technology available, with Ai-enabled robots and smart digital manufacturing systems supporting the production and manufacture of state-of-the-art customer solutions,” said John Bubnikovich, ABB United States robotics Division president. “Almost every aspect of the site will be upgraded to enrich our efforts to attract, retain and nurture the best automation talent, while creating a US manufacturing hub and headquarters befitting of a global leader in automation.”
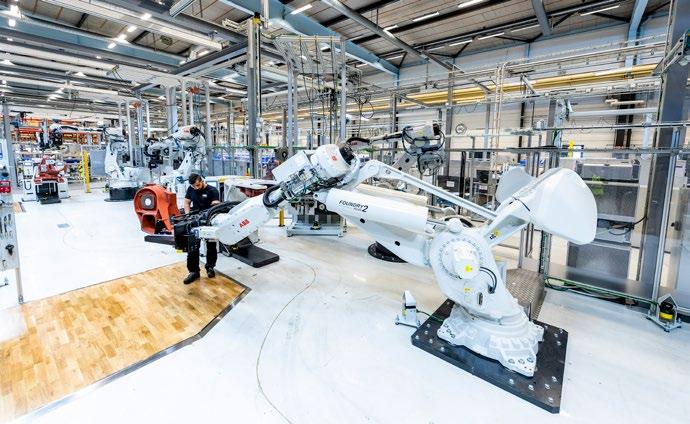
This investment will see the latest digital and automation technologies implemented to manufacture next-generation robots in the US, for the Americas, streamlining the delivery process and reducing lead times. Close to 90 percent of robots delivered to customers in the US, Canada, Mexico and South America will soon be made in Auburn Hills. The plant will utilize flexible, modular production cells that are digitally connected and networked, and served by intelligent autonomous mobile robots. Ai-powered robotic systems will take on tasks such as screw driving, assembling and material handling, relieving people from these tasks and enabling more rewarding work.

ABB is a technology leader in electrification and automation, enabling a more sustainable and resourceefficient future. The company’s solutions connect engineering know-how and software to optimize how things are manufactured, moved, powered and operated. Building on more than 130 years of excellence, ABB’s ~105,000 employees are committed to driving innovations that accelerate industrial transformation. www.abb.com
Hypertherm Associates announces Sofos Robotics Co. as new authorized partner for Robotmaster offline programming software
Hypertherm Associates, a U.S.-based manufacturer of industrial cutting systems and software, today announced a new partnership for its robotmaster ® offline programming software for robots. As an authorized partner, Sofos robotics Co. will include robotmaster as part of the robotic systems they offer when end users require an easy-to-use and powerful robot programming solution.
“Sofos robotics is a great partner. Not only are they experts and power users of the robotmaster offline programming software, but they also have years of experience in robotic system sales and integration,” said Cory A. John, robotmaster software sales manager. “Finding someone who can marry the two worlds together the way Sofos robotics can is like hitting the jackpot. i have heard nothing but great things from the customers who get the pleasure to work with the team at Sofos robotics.”
Sofos robotics uses robotmaster to perform robotic system engineering including cell design, reach and feasibility studies, as well as for their programming services.
“ robotmaster is a game-changer for our clients who are looking for a programming solution that is easy to use and allows them to program complex tasks with ease,” said John Huster, Sofos robotics president. “By using robotmaster, our clients drastically reduce programming time and costs, especially in small batch production runs. Ultimately, by pairing robotmaster with our robotic systems, we are able to deliver a complete solution for our clients.” robotmaster, a Hypertherm Associates brand, is an offline programming software for robots that helps manufacturers maximize productivity on production runs of all sizes. robotmaster makes programming parts of any complexity quick and easy as a result of its integrated CAD/ CAM functionality. This intuitive and powerful solution is designed with process experts in mind reducing the need for programming and robotic expertise. learn more at www.robotmaster.com.
Sofos robotics was founded by Mark Walstrom and John Huster in January 2019. located in Ham l ake, Minnesota, they provide automation and robotic integration services to help their customers maximize efficiency in their production processes.
Hypertherm Associates is a U.S.-based manufacturer of industrial cutting products and software. its products, including Hypertherm plasma and OMAX waterjet systems, are used by companies around the world to build ships, airplanes, and railcars; construct steel buildings, fabricate heavy equipment, erect wind turbines, and more. in addition to cutting systems, the company creates CNCs, and software trusted for performance and reliability that result in increased productivity and profitability for hundreds of thousands of businesses. Founded in 1968,
• Heavy Gauge Steel Design learn more at www.HyperthermAssociates.com.
• Press Bed bolted on, not welded, to prevent distortion.
• Large press bed to accommodate a variety of tooling other than just punching.
• Pump, motor, valve and reservoir are all easily accessible for maintenance.
• Large rectangular tubes used at base of machine to give safe, instant portability.
Hypertherm Associates is a 100 percent Associate-owned company, employing approximately 2,000 Associates, with operations and partner representation worldwide.
Scott Wisotzke Joins
New Scale Robotics as Director of Sales
New Scale Technologies has appointed Scott Wisotzke as Director of Sales for its New Scale robotics division, expanding the division’s sales team to capture opportunities in the fast-growing market for automated metrology in high-mix, small batch manufacturing.
Scott has more than 25 years of experience in sales, sales leadership, and business development in the manufacturing and machining industries. Over 13 years with Transcat, a distributor of test, measurement, and calibration equipment and services, he held positions of increasing responsibility including Director of Field Sales for North America. He was most recently with NYMAT Machine Tool Corp. and has additional experience with tool distributor Alltite, Fluke process instruments, ElectriCom, and Newark Electronics. He has served in the US Marine Corps active duty and reserves. He has a Bachelor’s Degree in Management from St. John Fisher College.
SprutCAM Tech announces support for FIRST® Robotics Competition teams worldwide
FrC teams from different countries that have mastered SprutCAM X are already participating in this robotics competition.
FirST® robotics Competition (FrC), organized by the global robotics community FirST (For inspiration and recognition of Science and Technology), combines the excitement of sports with the rigor of science and technology. FrC teams (ages 14-18) design, program, and build a robot using a standard set of parts and a common set of rules to compete in a themed head-to-head challenge.
The main vector of SprutCAM X software development is to become the world's #1 solution by implementing the Offline programming of industrial robots (Olp) technology in the product. Olp makes it possible to run a new machining program on a robot in just a few hours, whereas the same task takes several days with traditional online programming. The development of its global educational program, including support for initiatives such as the
FirST® robotics Competition, is an important part of SprutCAM Tech's strategy.
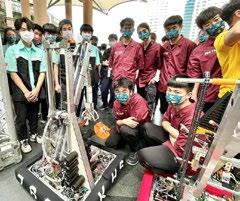
#AdditiveManufacturing
Velo3D Announces the 2023 “Proof is in the Printing” Roadshow Tour Across Eight U.S. Cities
The series of events highlights how engineers can achieve repeatable outcomes in real-world environments and qualify parts for production
Velo3D, inc. (NYSE: VlD), a leading metal additive manufacturing technology company for mission-critical parts, today announced its 2023 roadshow, the proof is in the printing Additive Manufacturing Tour, which will visit eight cities across the U.S. The tour builds on Velo3D’s previous roadshow series that brought together more than 400 engineers around the U.S. to learn about how metal additive manufacturing can help them transform their businesses.
Velo3D piloted its roadshow program in 2021. Each roadshow is a half-day event that includes presentations from Velo3D leadership team members, partners, and customers.
By attending, engineers can hear how their peers are utilizing metal additive manufacturing to produce parts and qualify them for use by utilizing the Velo3D fully integrated additive manufacturing solution. presentations will also discuss how to optimize the additive manufacturing process to produce more performant parts and increase throughput.
Tour dates have been scheduled for the following cities:
» phoenix, AZ: March 29, 2023
» Denver, CO: April 27, 2023
» Houston, TX: May 17, 2023
» Jupiter, Fl: June 15, 2023
» long Beach, CA: August 17, 2023
» Detroit, Mi: September 20, 2023
» Fremont, CA: October 19, 2023
» Cincinnati, OH: November 2023
Dates will be announced for roadshow events in Europe and Asia. Velo3D’s distribution partner GoEngineer will also host a roadshow in Albuquerque, NM.
" if you have struggled to go into production with high- quality, additively manufactured metal parts, this roadshow lays down the groundwork to speed up and simplify the process," said Josh Brown, GoEngineer Director of Metal AM. “Attendees will leave with a clear understanding of how to utilize metal additive manufacturing for their mission-critical parts and qualify them for production use.”
Engineers interested in attending one of the shows on the tour can visit velo3d.com/roadshows to register or email info@velo3d.com.
HII Receives Additive Manufacturing Approval from Naval Sea Systems Command
Global all-domain defense partner Hii (NYSE: Hii) announced today that its Newport News Shipbuilding division recently received approval as a vendor to provide some additive manufacturing components to Naval Sea Systems (NAVSEA) platforms.
The certification enables NNS to use additive manufacturing, or 3D printing, to fabricate pipefittings or other potential components for use on aircraft carriers, submarines and other NAVSEA platforms.
“ innovation is driving our business transformation at Newport News Shipbuilding,” NNS Vice president of Engineering and Design Dave Bolcar said. “Our continued advances in additive manufacturing are revolutionizing naval engineering and shipbuilding. This will continue to propel our progress in efficiency, safety and affordability as we remain steadfast in our mission to deliver the critical ships our Navy needs to protect peace around the world.” in 2018, NAVSEA approved the technical standards for 3D printing after extensive collaboration with Hii and industry partners that involved the rigorous printing of test parts and materials, extensive development of an engineered test program and publishing of the results.
The first 3D-printed metal part, a piping assembly, was delivered to the U.S. Navy for installation on the NNS-built USS Harry S. Truman (CVN 75) in January 2019. Since then, NNS has received approval for several other metal 3D-printed parts on U.S. Navy ships of varying criticality.
This most recent certification is for stainless steel (316/316l grade) additively manufactured pipefittings. NNS is also pursuing approvals that will enable broader use and implementation of additive manufacturing across the naval enterprise. The highly digitized process could lead to cost savings and reduced production schedules for naval ships.
NNS is the only builder and refueler of nuclear-powered U.S. Navy aircraft carriers and one of just two shipyards building nuclearpowered submarines for the Navy.
Additive Manufacturing Users Group Awards Two Scholarships
Dr. les Kalman and Brent Griffith to be recognized at the 2023 AMUG Conference
The Additive Manufacturing Users Group (AMUG) today announced the recipients of its scholarships. Dr. les Kalman, Assistant professor in restorative dentistry at Western University (london, Ontario, Canada), has been awarded the randy Stevens Scholarship for educators in additive manufacturing. Brent Griffith, p.E., is pursuing a Master of Engineering in Additive Manufacturing and Design through penn State University (State College, pennsylvania) and has been awarded the Guy E. Bourdeau Scholarship for students in additive manufacturing.
Online at www.amug.com.
Desktop Metal Qualifies Copper Alloy C18150 on the Production System™ with Sandvik Additive Manufacturing and Top Five Global Automaker
» Also known as chromium zirconium copper, C18150 is a high-strength, high-conductivity copper alloy commonly used in thermal transfer applications, such as electrical connectors, welding electrodes, as well as other electrical and electronic components
» A global automaker is now testing a unique 3D printed part design, which is being developed for a future production application, in C18150 using Sandvik’s Osprey ® metal powder
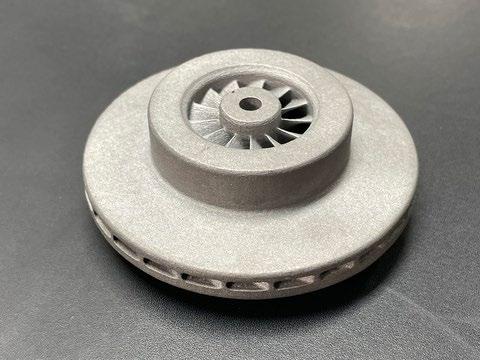
» Desktop Metal and Sandvik Additive Manufacturing will discuss details of this joint automotive project during a presentation at AMUG 2023, held March 19-23 in Chicago
» With the addition of C18150, Desktop Metal now offers a world-leading 23 metal materials on its binder jet 3D printing systems, which includes the Shop System™, p roduction System™, and X-Series platforms learn more about Desktop Metal and our #TeamDM brands at www.desktopmetal.com. the p-1, for research and development of binder jetting projects for serial production, and the p-50, the world’s fastest metal binder jet system, offering the lowest cost per part, with SpJ technology. production System users interested in working with titanium should consult their Desktop Metal sales representative on hardware and binder requirements. learn more at desktopmetal.com/materials.
Desktop Metal, inc. (NYSE: DM), a global leader in additive manufacturing technologies for mass production, in collaboration with Sandvik Additive Manufacturing, a world-leading producer of gas atomized metal powders, and a top five global automotive manufacturer, today announced that copper alloy C18150 has been DM Qualified for binder jet 3D printing on the production System™.
Sandvik Osprey developed and provided C18150 powder that routinely delivered as-sintered densities of 98-99% when printed on the p-1, allowing the automaker to deliver a unique component design that is targeted for high-volume production on the production System™ p-50 after additional development.
Chromium zirconium copper offers a combination of strength, conductivity, and corrosion resistance that makes it suitable for a wide range of industrial and commercial applications. it’s also able to withstand service temperatures up to 500°C, making it ideal for certain applications in the automotive industry.
TriTech Titanium parts llC, which is iSO 9001:2015 certified, uses metal injection molding (MiM), investment casting, and now, binder jet 3D printing on the Desktop Metal production System p-1 to produce titanium parts. The company is a spin-off of AmeriTi Manufacturing Co., which was founded in 1984 and sold last year to Kymera international.
SFM Technology Create the First Helicopter
Desktop Metal and TriTech Titanium Parts Qualify Titanium Alloy Ti64 for Binder Jet 3D Printing on the Production System™
» Detroit-based TriTech is an experienced manufacturer of titanium parts for the commercial and industrial markets, including aerospace, marine, and automotive
» Ti64 is a popular material because of its excellent strength-to-weight ratio, corrosion resistance, and biocompatibility
» Binder jetting of Ti64 simplifies production of complex titanium parts, which can be challenging and expensive to fabricate using traditional manufacturing methods
Desktop Metal, inc. (NYSE: DM), a global leader in additive manufacturing technologies for mass production, in collaboration with Detroit-based TriTech Titanium parts llC, today announced that Ti64 has been customer-qualified for binder jet 3D printing on the production System™.
The production System platform features high-speed Single pass Jetting (SpJ) technology on two models:
Main Rotor Blade Restraint Cradle
With 3D Printing Technology
Urgently requested to provide cradles for helicopters, SFM Technology turned directly to the Bigrep prO
For the aerospace and defense giant leonardo - tasked by the Ministry of Defence to provide AgustaWestland AW101s for the royal Navy - they found that their pre-existing main rotor blade restraint cradles were not living up to their standard. leonardo turned to SFM Technology and their AeroAdditive section to provide a solution. The result was the first main rotor blade restraint cradle – measuring 900 x 230 x 160mm - created with 3D printing.
3d Printing Provides The Solution
As a solution had to be found very quickly, SFM turned immediately to the possibilities of additive manufacturing. As Mr. Wilson says, "This is quite a long process, so we had a look at many aspects of 3D printing. We must look at cost, efficiency, and of course, the size, which pushed us to Bigrep. Eventually, we looked at the Bigrep prO as we had to look at a production 3D printer, which i believe the Bigrep prO can provide. The machine is used as a production machine, so every rotor blade restraint cradle will be going to the end customer."
3d Printing More Versatile Than Traditional Methods
in the aerospace industry, lightweight yet strong parts are essential. SFM Technology found through stress-testing that their 3D-printed printed parts performed better than original, non-printed parts. By using Hi-Temp CF – a carbon fiber reinforced material with versatile, high-strength properties – the blades have a powerful resistance to wear and tear as well as any external pressure.
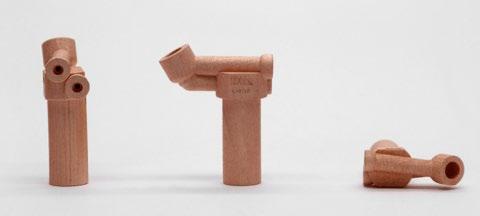
SFM Technology are now looking to use the Bigrep prO as a batch 3D printer, able to sequence production and create improved results across the board. it is likely that more aerospace designers will see the benefits of 3D printing and look to adopt it in due course.
Find more information at: www.sfmtechnology.org. uk/ Find out more at www.bigrep.com
Sintavia to Develop Additive Manufacturing Facility for the U.S. Navy
partnership with Bechtel plant Machinery, inc. will enhance adoption of additive technology across multiple nuclear platforms
Sintavia, llC, a designer and additive manufacturer of complex mechanical systems and components for the Aerospace & Defense industry, announced today that it had been awarded a contract from Bechtel plant Machinery, inc. (“BpMi ”) to develop a dedicated additive manufacturing facility in support of the United States Naval Nuclear propulsion program. The new, vertically integrated facility will develop and additively manufacture advanced nuclear propulsion systems for both in-production and in-development submarine programs of the United States Navy, including the next generation nuclear-powered attack submarine.
The new facility, located in Hollywood, Florida, is expected to come online in the second quarter of 2023.
For more information visit http://www.sintavia.com.
From Spaceflight to Industry Insight: Additive Manufacturing Keynote Speakers Announced for RAPID + TCT 2023
Daily keynote presentations and 170 technical presentations highlight impact, innovation and more as the largest AM event in
North America returns May 2 - 4 in Chicago
The most accredited leaders and experts in additive manufacturing (AM) will gather to educate and innovate at r ApiD + TCT 2023, North America’s largest and most influential AM event in North America as it returns to Chicago’s McCormick place, May 2 - 4. Each day will kick off with a keynote speaker presentation featuring leading authorities and iconic innovators in AM covering topics like AM applications in space, scaling digital manufacturing spaces, and a panel discussion taking a pulse on AM’s challenges and what the future holds.
The three-day event, produced by SME and rapid News publications, owner of the TCT Group, will bring together thousands of AM experts and students from around the world, feature hundreds of exhibitors, as well as two thought-leadership panels across a swath of industries including healthcare, automotive, aerospace, defense and more.
Visionary keynote speakers and topics include:
» Building and Scaling an industrial Digital Manufacturing System: Tuesday, May 2Kevin Czinger founder, lead inventor and CEO of Divergent Technologies will discuss the architecture and elements of the Divergent Adaptive System (DAp S™), its benefits and the business model for localizing sustainable manufacturing on a global scale.
» Additive Manufacture for Space: past, present, Future: Wednesday, May 3Omar Mireles, phD, Additive Manufacturing r&D engineer at NASA Marshall Space Flight Center, will discuss how AM enables tech, decreases the cost of rocket engine manufacturing, increases design flexibility, provides access to new materials and more.
» AM industry Outlook: Opportunities and Challenges: Thursday, May 4 Terry Wohlers, head of Advisory Services and Market intelligence, ASTM international
» robert ‘Bob’ Willig, executive director & CEO of SME
» Chris Ciuca, vice president of programs at SAE international in addition to keynote presentations, r ApiD + TCT 2023 will feature almost 170 technical presentations, evaluated and selected by a team of world-class experts, covering AM trends across industries including healthcare, aerospace, defense, automotive, design for additive manufacturing, economics, r&D, supply chains, metrology and more. Topics range from tips on getting started with large-format 3D printing in consumer-goods industries to the impact of micro 3D printing on prototyping and designs in healthcare. registration is now open to attend the premier destination for technology providers and industry leaders worldwide.
» Wohlers, Willig and Ciuca will join the winner of the AM industry Achievement Award, which will be announced during the event, for a panel discussion discussing challenges and opportunities in AM.
To learn more about what r ApiD + TCT 2023 has to offer, visit www.rapid3devent.com and keep up to date with all things AM by following us @r ApiD_Event on Twitter and linkedin.
#AdvancedFuelCells
Advent Technologies Announces Opening of R&D and Manufacturing Facility in Charlestown, MA
Advent Technologies Holdings, inc. (NASDAQ: ADN) (“Advent” or the “Company”), an innovation-driven leader in the fuel cell and hydrogen technology sectors, is pleased to announce the opening of its new state-of-the-art research and development and manufacturing facility at Hood park in Charlestown, MA. The new facility represents a significant investment in Advent's future growth and will enable the Company to accelerate its efforts to scale-up and deliver on the increasing global demand for electrochemical components in the clean energy sector.
Advent's Hood park facility is situated in the center of Boston's thriving innovation and r&D community and boasts a total area of approximately twenty one thousand square feet. The new facility brings together Advent's corporate office staff, who were previously based at 200 Clarendon Street in downtown Boston, and the Company's research and development team, which was based at Greentown l abs in Somerville, Massachusetts. By integrating these two teams under one roof, Advent aims to streamline its operations and foster a more collaborative and innovative work environment.
Advent's newly opened site offers an array of state-ofthe-art equipment and facilities, including:
» modern coating machines to support the seamless transition from prototypes to initial production runs for advanced membranes and electrodes for both fuel cells and low-cost hydrogen production;
» a fully analytical facility dedicated to quality control, failure analysis, and improving product lifetime;
» fuel cell and electrolyzer test stations for statistical process control and development of next-generation membrane electrode assembly (MEA) materials, and,
» a mechanical engineering lab for developing automated assembly processes for MEAs and stacks.
Advent's Hood park facility will be producing a range of innovative products, including the ion-pair Advent MEA, which is currently under development as part of the Company's joint development program with the U.S. Department of Energy's los Alamos National l aboratory, Brookhaven National l aboratory, and National renewable Energy l aboratory.
With the ion-pair MEA technology, Advent is looking to revolutionize the global MEA market by producing fuel cells that can last at least three times longer and deliver double the power density of its previous systems. These next-generation pEM-based fuel cells would be capable of consistently operating at more than 100°C for over 20,000 hours, making them an ideal choice for heavy-duty mobility applications. The move to the Hood park facility will enable Advent to significantly expand the production capacity of the ion-pair Advent MEA in-line with its growth plan.
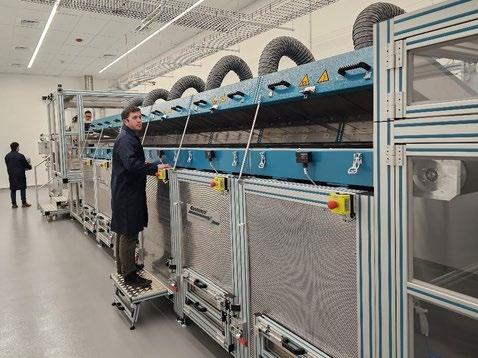
Dr. Vasilis Gregoriou, Chairman and Chief Executive Officer of Advent Technologies, stated, "Today is a significant achievement for the entire Advent team worldwide. Undoubtedly, 2022 was a year of tremendous progress in the clean energy sector, leading to an unprecedented surge in interest in fuel cell products and electrochemistry components. Over the past two years, we have been dedicated to completing our new state-of-the-art r &D and manufacturing facility. The move to Hood p ark is perfectly timed and marks a major step forward for Advent's goal of becoming a leader in the hydrogen industry. We are excited about expanding our production capacity and growing our team to meet the increasing global demand for our innovative products.”
Dr. Emory De Castro, Chief Technology Officer of Advent Technologies, added: "Advent's new facility at the Hood park campus is a major milestone in the Company’s quest to accelerate the global transition to a net-zero carbon future. By providing clean and sustainable power from hydrogen fuels, Advent is helping to replace polluting diesel generators and combustion engines with environmentally friendly alternatives. in addition to supporting Advent's growth in the U.S. market, the new facility is also expected to create numerous job opportunities for young professionals, including material scientists and fuel cell engineers based in Massachusetts. The proximity of Hood park to top research universities will enable Advent to tap into a rich pool of intellectual talent and further enhance its innovative efforts, solidifying its position as a leader in the electrochemistry components industry.”
For more information, visit www.advent.energy.