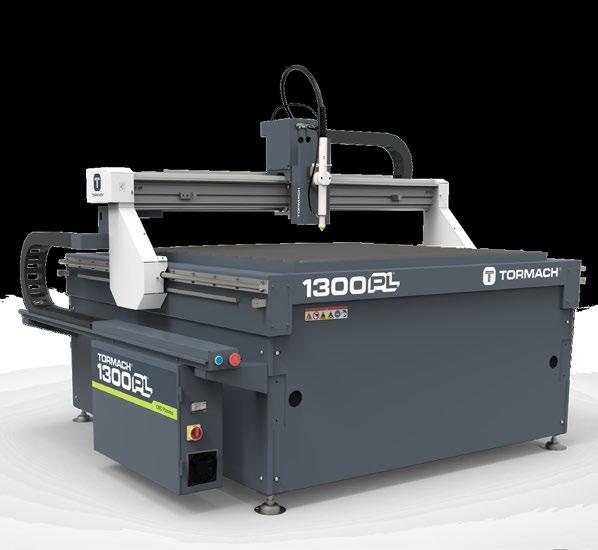
5 minute read
DID YOU KNOW TORMACH SELLS PLASMA TABLES?
Premium features make better parts.
• Closed-loop servo motors for reliable accuracy
• Floating head with Digital Torch Height Control that help make cuts to uneven surfaces like corrugated metal
• Standard breakaway torch holder with collision detection to minimize machine damage if things go wrong
• Minimized run times with fast rapids (1,000 in./min., 400 in./min. cuts) and acceleration (30 in./sec.²)
• Integrated water table mounted on sliding rails, ideal for cutting pipes and larger parts
• The only plasma table built with PathPilot, Tormach’s award-winning CNC controller, and access to PathPilot HUB, Tormach’s browser-based version of PathPilot to complete the design of FabLab, a new in-space manufacturing system. FabLab is expected to be tested onboard the International Space Station (ISS) and serve as a precursor for a rtemis missions to the Moon and Mars. The multi-material 3D printer will allow N a S a crews in deep space to manufacture tools and components on demand using materials such as metal, plastic, ceramics and electronics, enabling a sustainable human presence on and around the Moon, Mars, and beyond.
“FabLab is a solution for some of the key logistics challenges with sustained human deep space exploration aboard the Lunar Gateway and on the Moon and Mars,” said Redwire Executive Vice President John Vellinger. “a stronauts won’t need to pack their spacecraft with every tool or part they may need millions of miles from Earth. Make it, don’t take it.”
In 2017, Redwire was selected to prototype FabLab through N a S a’s Next Space Technologies for Exploration Partnerships program. This latest contract will see the FabLab design fully matured to spaceflight-ready status. a n anticipated follow-on contract will support the construction of a FabLab unit and its test aboard the ISS in low-Earth orbit (LEO). Testing FabLab on the ISS will be an important step toward building versions for use at destinations beyond LEO, such as N a S a’s Gateway. With FabLab technology, crews on the Moon, Mars, and in deep space will be able to manufacture critical assets, such as tools, replacement parts, and printed circuit boards on demand.
“Having an integrated capability for on-demand manufacturing and repair of components and systems during space missions will be integral for sustainable exploration missions,” said Jim Reuter, associate administrator for N a S a Space Technology Mission Directorate programs. “This is a rapidly-evolving, disruptive area in which N a S a wants to continue working with industry and academia to develop these technologies through collaborative mechanisms such as this one.”
FabLab leverages Redwire’s leadership in in-space manufacturing. Redwire’s a dditive Manufacturing Facility ( a MF), the first permanent commercial manufacturing platform to operate in LEO, has manufactured over 200 tools, parts, and assets onboard the ISS. a MF’s versatility and durability have made it a reliable resource for government and commercial customers since its activation in 2016. Building on this expertise, Redwire is continuing to develop new capabilities that will leverage in-space manufacturing for unprecedented applications to meet future space exploration goals.
For more information, please visit redwirespace.com
a BB invests $170 million in the U.S.
» Investment reflects increased customer demand for electrification and automation products
» Wisconsin greenfield facility for drives and services demonstrates continued commitment to U.S. customers and workforce
» Inflation Reduction act supports company’s continued investment in creating more secure supply chain and strengthening local manufacturing a BB is accelerating its growth strategy in the United States by investing approximately $170 million and creating highly skilled jobs in manufacturing, innovation and distribution operations. a BB is committed to growing in the U.S. by investing in its electrification and automation businesses that meet increased demand from industry-leading customers, while supporting the clean energy transition and the trend towards reshoring of production. This commitment is highlighted by today’s pouring of the concrete foundations for a greenfield drives and services facility in New Berlin, Wisconsin. The U.S. is a BB’s largest market, comprising 24 percent of the company’s annual revenue. a BB technology touches every sector of the economy, from transportation to utilities to buildings. Recently passed legislation like the Inflation Reduction a ct, CHIPS a ct, and Infrastructure Investment and Jobs a ct, gives a BB confidence to invest in manufacturing capacity, distribution systems and technology innovation to bring products and services closer to customers.
Investment projects underway across the U.S. include:
» New Berlin, Wisconsin: Opening of Drives and Services manufacturing facility will increase U.S. production capacity of industrial electric drives and provide additional customer services. The business manufactures a wide range of aC variable frequency drives and controls which reduce energy consumption in buildings and industrial applications in the U.S. market. The nearly $100 million greenfield investment is expected to be completed in late 2024 and is replacing a neighboring existing facility, which employs approximately 720 workers. Some 100 new jobs will be added over the next three years.
» Memphis, Tennessee: Investing $3 million in the opening of an Installation Products Research & Development Lab and Innovation Center to accelerate development of new products. a BB remains the seventh-largest private employer in Memphis.
» atlanta, Georgia: Opening of packaging and logistics facility for end-to-end robotic automation solutions in warehouse and distribution, retail, and logistics industries. This $2 million investment will open in 2023 and create approximately 15 jobs.
» a lbuquerque, New Mexico: Previously announced $40 million investment in a new facility to manufacture Elastimold, the leading brand for underground cable accessories, to support strengthening a more sustainable U.S. electrical grid. It underpins a BB’s commitment to improve reliability and resilience of the U.S. infrastructure and assure greater safety for a merican consumers, businesses, and communities. The investment will create 55 new jobs and will be completed by 2024.
» auburn Hills, Michigan: Previously announced expansion of North american robotics headquarters and manufacturing facility as more customers turn to automation to build resilience while improving efficiency and flexibility as part of the near and reshoring of production. The $20 million investment will create 72 jobs and be completed by the end of 2023.
» Lehigh Valley, Pennsylvania: Previously announced opening of Installation Products Division Northeast Distribution Center in 2023. This more than $4 million investment will create more than 100 jobs and further regionalize aBB’s global supply chain to help reduce delivery times of high-demand electrification products to contractors by up to 50 percent.
» Columbia, South Carolina: Previously announced opening of electric vehicle charger manufacturing facility to build up to 10,000 chargers per year, ranging from 20kW to 180kW in power, to support operators building the national charging infrastructure. aBB E-mobility’s investment will create over 100 jobs.
“The Inflation Reduction act is triggering investment in clean energy and supporting businesses that can produce technology locally,” said Michael Gray, U.S. Country Holding Officer of aBB. “More than ever before, aBB is designing and producing products domestically to serve our U.S. customers, as they move toward more sustainable electric power generation, clean energy manufacturing, electric transportation, and industrial efficiency including carbon capture and storage, as well as methane reduction.”
The U.S. federal government projects real gross domestic product to increase 2.5 percent in 2023, average 2 percent annual growth between 2024-2028, and grow 2.3 percent per year during 2029-2032. This projected GDP growth, combined with an estimated global EV infrastructure investment of more than $1 trillion by 2040, gives aBB the confidence to continue investing. aBB projects 25 percent of global EV infrastructure investment will take place in the U.S.
Since 2010, aBB has invested $14 billion in U.S. plant expansions, operational improvements, state-of-the-art equipment, products, and people, making it the company’s largest market. With approximately 20,000 employees in more than 40 manufacturing and distribution facilities, aBB is investing, growing and serving customers across america through industries that create jobs, encourage innovation and achieve a more productive, sustainable future.
For more information: www.abb.com