
North America’s Manufacturing Resource for Industry Professionals Since 1986
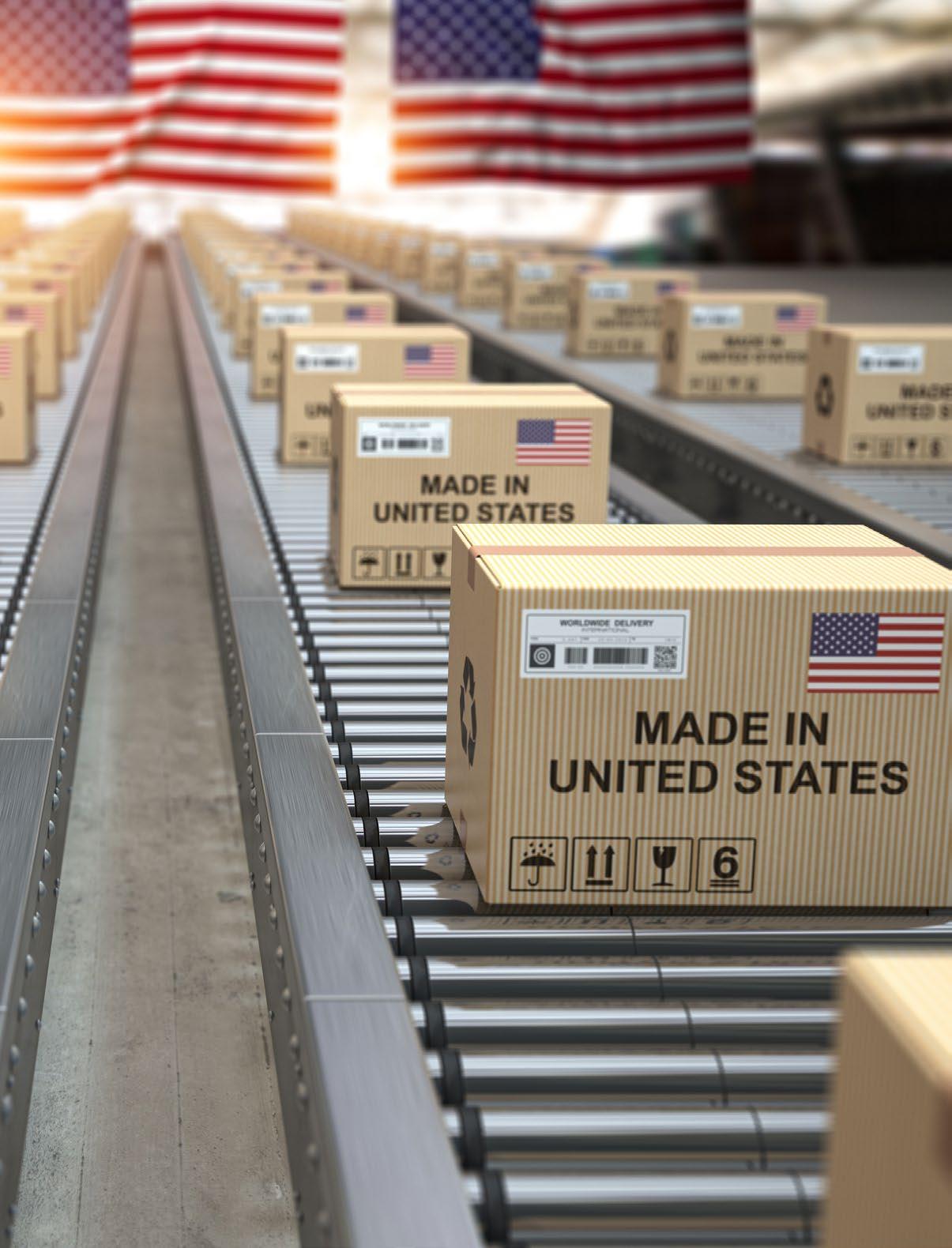
North America’s Manufacturing Resource for Industry Professionals Since 1986
in Advanced Cybersecurity Solutions in American Manufacturing
Innovations and Strategic Moves in American Manufacturing: Energy Efficiency, Relocations, Leadership, and Safety Initiatives
Innovations and Milestones: Shaping the Future of Manufacturing in America
Manufacturing Innovations Driving American Industry Forward
Industrial Automation: Advancing Manufacturing in America
Cutting-Edge Innovations in Manufacturing Technology
• American Made Ironworkers 45 to 150 Ton Models
• Circular Cold Saws Manual to Fully Automatic for Ferrous & Non-Ferrous
• Tube & Pipe Notchers Manual, Electric & Abrasive
North America’s Manufacturing Resource for Industry Professionals Since 1986
William C. Strickland III, Publisher william.strickland@indmacdig.com 800-366-0676 ext. 103 | Fax: 866-826-5918
Adrienne Gallender, Associate Publisher/Media Advisor
agallender@indmacdig.com 847-612-1572 | Fax: 847-559-2909
Brian Self, Associate Editor brian@indmacdig.com 800-366-0676 ext. 104 | Fax: 866-826-5918
Shane Bell, Creative Director sbell@indmacdig.com
lisa Hanschu, Sr. Account Executive lisa@indmacdig.com 785-965-9159 | Fax: 785-965-7199
William C. Strickland III, National Sales 205-903-9178 | fax 866-826-5918
Susan Strickland, Accounting susan@indmacdig.com 205-542-1098 | Fax: 866-826-5918
CIRCULATION & SUBSCRIPTIONS
IMD, 3590-B Hwy 31 South, Suite 233, Pelham, Al 35124 circulation@indmacdig.com | Fax: 866-826-5918
REPRINTS
To purchase article reprints please call 800-366-0676 ext. 103 or email wstrickland@indmacdig.com
As the manufacturing landscape in America continues to evolve, we are witnessing an era marked by remarkable innovation, strategic initiatives, and a relentless pursuit of efficiency and sustainability. In this special issue of Business 4.0, themed "Manufacturing in America," we delve into the transformative trends and cutting-edge technologies that are shaping the future of our industry.
One of the most significant developments is the integration of energy-efficient technologies and renewable energy sources. Companies across the nation are investing in solar, wind, and other renewable systems to power their operations, reducing reliance on fossil fuels and enhancing energy independence. This shift not only helps mitigate the risks associated with fluctuating energy prices but also underscores a commitment to environmental responsibility.
Advanced manufacturing technologies, such as additive manufacturing and digital twins, are revolutionizing the industry. These technologies allow for precise production with minimal material waste and enable manufacturers to optimize their processes through virtual simulations. Celebrating milestones like Mazak's 50th anniversary and Zimmermann's new FZG portal milling machine, it's clear that innovation continues to drive progress and maintain our competitive edge.
Workforce development remains a critical focus as we address significant labor shortages. Highlighting the achievements of companies like Kaiser Tool Company, we explore the causes, risks, and solutions related to this challenge. By investing in training and development programs, manufacturers are ensuring that the next generation of workers is well-equipped to meet the demands of modern manufacturing.
Cybersecurity is another vital area where advancements are making a profound impact. As manufacturing processes become increasingly digitalized, the threat of cyber-attacks looms larger. Siemens leads the way with innovative solutions like SIBERprotect™ and SINEC Security Guard, which safeguard industrial operations and ensure resilience against evolving cyber threats.
As we continue to navigate the complexities of the modern market, the stories and insights in this issue of Business 4.0 reflect the resilience, ingenuity, and forwardthinking mindset that define American manufacturing. Together, we are setting new standards in efficiency, sustainability, and innovation, ensuring a prosperous future for our industry.
Thank you for your continued support and engagement. We hope you find this issue both informative and inspiring.
Warm regards,
William Strickland Publisher, IMD
80 years of Innovation: AIRMATIC Celebrates Milestone Anniversary
AIRMATIC, a North American leader in industrial distribution, proudly marks its 80th anniversary, symbolizing eight decades of excellence in providing top-tier bulk materials handling products and services to customers worldwide. As a testament to its enduring legacy and commitment to sustainable excellence, the company is now proudly under fourth-generation management.
Established in 1944, AIRMATIC began as a Philadelphia-area air tool distributor and has since evolved into an accomplished and respected player in the agriculture, mining, construction, manufacturing, transportation, and energy production industries with an international footprint. The company's journey has been characterized by a pursuit of innovation, a dedication to customer satisfaction, and a focus on adapting to the ever-changing demands of the industrial landscape.
The fourth-generation leader, William J. “Billy” Dougherty III, brings a fresh perspective to the helm of AIRMATIC. His leadership is defined by a strategic vision that combines the wisdom of tradition with a dynamic approach to meet the challenges of a rapidly evolving global market.
"We are excited and proud to celebrate this significant milestone in our company's journey," remarked Billy Dougherty, Vice President and General Manager of AIRMATIC. "As we reflect on our achievements over the past 80 years, we are grateful for the trust our customers and suppliers have placed in us. looking ahead, we are committed to continue providing innovative solutions and services to our growing list of North American and international customers."
To commemorate its 80th anniversary, AIRMATIC has planned a series of community service events,
team-building exercises, and celebration events designed to express appreciation for the invaluable contributions of its employees.
With a comprehensive range of powder and bulk solids handling products and services, AIRMATIC remains at the forefront of its field. The 80th-anniversary activities serve as confirmation of the company's resilience, adaptability, and unwavering commitment to delivering value to its customers.
Toyota Material Handling (TMH) celebrates the 25th anniversary of its System of Active Stability (SAS) technology during National Forklift Safety Day. SAS is an innovative feature that helps prevent forklift tip-overs, significantly enhancing operator safety. Since its introduction, SAS has become a standard in the industry, demonstrating TMH’s commitment to safety and innovation.
TMH also highlights its Smart Environment Sensor Plus (SEnS+), which assists operators in identifying pedestrians or objects in their path. The company’s continuous efforts to improve safety standards have earned it recognition and
respect in the material handling industry. TMH’s leadership in promoting safety is evident in its comprehensive safety programs, operator training, and advanced technologies.
National Forklift Safety Day, sponsored by the Industrial Truck Association (ITA), is an annual event that educates customers, policymakers, and government officials about safe forklift use and proper operator training. With approximately 4.5 million forklift operators in the workforce, Toyota continues to emphasize the importance of continual safety education.
“Since its inception 11 years ago, National Forklift Safety Day has helped drive more discussion about making and keeping forklift safety a core part of every organization’s culture,” said Cesar Jimenez, Toyota Material Handling Vice President of Regulatory Affairs, Product Planning, and Product Assurance. “National Forklift Safety
Dynabrade's commitment to supporting the racing community with high-performance power tools, giving Junco Hollinger Racing a competitive edge by leveraging the power of the innovative equipment throughout the 2024 season.
"Dynabrade is excited to be an Official Partner of Juncos Hollinger Race Team in 2024," said Mike Saraf, VP of Global Sales at Dynabrade Power Tools. "Dynabrade has long prided ourselves on manufacturing the highest quality abrasive power tools in the industry, and this new partnership is a great opportunity for us to gain exposure on a platform as prestigious as the NTT INDyCAR Series, North America's premier open-wheel auto racing series."
E-Z lOK, a leading manufacturer of threaded inserts, will exhibit its products at IMTS 2024 in Chicago. The company will co-locate with its sister company TCI Precision Metals. The highlight of the show for E-Z lOK will be its new line of ultrasonic/heat-stake metal inserts and staking tools for plastics. These inserts are designed for OEM builds, retrofits, and injection molding, offering strong components with higher torque and pullout strength. E-Z lOK will also display its full line of threaded carbon inserts with factory-applied lOCTITE™ 204 adhesive coating. The company's products aim to provide durable and reliable solutions for a wide range of industrial applications.
Director of Sales & Marketing, Kyle lindsly-Roach and a team of E-Z lOK engineers will attend the show, displaying the full line of E-Z lOK products. Emphasis will be placed on the company’s threaded inserts for metal, wood, and plastic.
HEulE Precision Tools will feature their BSF tooling for automated high-volume back spot facing applications in IMTS booth #431364. It is ideal for counterbores up to 2.3 x diameter and ranging in size from 6.5mm to 20.5mm (0.256” to 0.807”). BSF tooling is available with three activation methods to suit any machining environment, including, (1) CNC machines with through-spindle coolant with at least 300 psi, (2) CNC machines with throughspindle air with at least 60 psi, and (3) a new manual version with easy collar locking/unlocking mechanism.
BSF tooling is designed for CNC machining and functions without an anti-rotation device, change of spindle direction, or contact mechanism, allowing components to be spot faced in the same direction as the bore is drilled. This saves the time and cost of turning the work piece, while allowing the spot-facing of difficult to reach areas like casting flanges, and bolt head faces. The simple swing mechanism combined with one of the three activation
methods yields optimal cutting performance, resulting in consistent spot facing and fewer scrapped parts. BSF tooling is stocked in the Cincinnati area warehouse for immediate shipment. They are ideal for gear housings, yokes, engine casings, and other parts in a wide range of materials.
The global manufacturing industry is expected to experience sluggish growth in 2024, with a slight contraction or stagnant growth anticipated for most economies. However, a recovery is projected for 2025, driven by improved economic conditions and increased consumer spending. China’s growth forecast has been revised down slightly due to economic challenges, but other territories are expected to see better-than-expected conditions by the end of 2025.
Despite these challenges, the global manufacturing outlook remains cautiously optimistic, with steady growth anticipated through 2028. The semiconductor industry has bounced back from a low point in 2023, boosting outlook for parts of South-Asia heavily reliant on the market sector, including Taiwan, Singapore, and South Korea. Dwindling
order books and the impact of the higher cost of living have constrained global demand, but there are signs of recovery in consumer spending and post-COVID supply chain problems have eased considerably.
Adrian lloyd, CEO at Interact Analysis, says, “The global outlook for manufacturing output is mixed to say the least. Our projections are holding but there are no clear signs of where recovery will come from and how strong it will be. As a result, we will be watching closely to see how constrained consumer spending in China, a strengthening uS economy and global events will affect conditions.
Plus One Robotics, a provider of AI vision software for robotic parcel handling, has been named “Overall Robotics Company of the year” by SupplyTech Breakthrough. The company’s AI vision software enhances robotic parcel induction and depalletization, reducing handling costs and improving throughput. Plus One Robotics’ innovative human-in-the-loop approach has streamlined logistics operations, making workplaces safer and more efficient.
The company recently launched InductOne, a dual-arm automated induction cell designed to increase throughput rates for parcel shippers. InductOne is designed for space-constrained areas, and its modular, configurable architecture integrates seamlessly with greenfield or brownfield facilities.
“Plus One Robotics has introduced a harmonious fusion of human expertise and robotic precision. logistics’ explosive growth, fueled by e-commerce, is evidenced by warehouses struggling to keep pace with increasing volumes and varieties of orders. This has led to inefficiencies, errors and rising costs,” said Bryan Vaughn, Managing Director of SupplyTech Breakthrough Awards.
“Plus One Robotics addresses these challenges with their cutting-edge solutions.”
Swiss tooling company REGO-FIX, inventor of the standardsetting ER collet, has partnered with Indianapolis-based Ed Carpenter Racing (ECR) to supply premium toolholding solutions for the IndyCar Series team’s machine shop.
For its precision machining operations, ECR will use REGO-FIX’s world-renowned ER collets and other related accessories, the powRgrip® toolholding system, and Multi line products that boost the accuracy of traditionalstyle tooling. ECR will use these productivity-enhancing solutions on its two new Hurco CNC machines – a TM10Mi lathe with live tooling capability and a high-speed, 5-axis VMX42HSRTi mill.
“REGO-FIX has a long history of innovation and dedication to detail that is necessary to deliver truly premium toolholding systems our customers have come to
trust for reliability and precision,” said Bill Obras, REGO-FIX general manager, Americas. “We’re proud to partner with an organization like ECR that is equally dedicated to excellence and has established itself admirably in a very competitive environment.”
TRuMPF Inc. Shows l aser and Arc Welding, 3D l aser Marking, and Additive Manufacturing Capabilities at IMTS 2024
In booth 433133 in the Additive Manufacturing pavilion at IMTS, TRuMPF Inc. will highlight the new TruPrint 2000. Introduced in February of 2024, TRuMPF's TruPrint 2000 now features a larger, square build plate and is designed for more productive, reliable, and high-quality 3D printing. Optimized for serial production, the new TruPrint 2000 offers greater productivity and quality for manufacturers, particularly in the tooling, dental, and medical technology industries.
In booth 135010 at IMTS, TRuMPF will show its automated arc welding, laser welding, and 3D laser marking technology. On display will be the TruArc Weld 1000 automated arc welding system for easy and affordable high-mix, low-volume production; the versatile, compact and fully-equipped Trul aser Station 7000 fiber laser welding system; and TruMark Station 7000 with a TruMark 6030 marking laser for high-performance 3D laser marking.
As the manufacturing landscape in America continues to evolve, the latest advancements and strategic initiatives are shaping the future of the industry. In this issue of Business 4.0, themed "Manufacturing in America," we explore key developments driving progress and innovation. From energy-efficient technologies and strategic relocations to personnel appointments and national safety campaigns, American manufacturers are setting new standards in efficiency, sustainability, and safety. This issue highlights significant contributions from leading companies like Bosch Rexroth, Dieffenbacher, Arnold, BIG DAISHOWA, Carlisle Fluid Technologies, and Combilift, showcasing their efforts to enhance manufacturing processes and ensure a competitive edge in the global market.
Bosch Rexroth and Dieffenbacher have partnered to develop an energy-efficient drive technology tailored specifically for Dieffenbacher's TailoredPress. This innovative drive system significantly reduces energy consumption while enhancing the precision and efficiency of pressing operations. By integrating Bosch Rexroth’s state-of-the-art hydraulic and control technology, the TailoredPress achieves higher performance with a reduced environmental impact. This collaboration exemplifies the shift towards sustainable manufacturing processes, meeting the growing demand for eco-friendly industrial solutions. The energy-efficient drive technology is expected to set new benchmarks in the industry, driving advancements in sustainable production methods.
The TailoredPress is designed to offer modularity, allowing manufacturers to customize the press to their specific needs. This flexibility is a key advantage, enabling companies to optimize their production processes without compromising on quality or efficiency. The press also features advanced automation capabilities, integrating seamlessly with existing production lines to enhance productivity. With these enhancements, manufacturers can achieve significant cost savings in energy and operational
expenses, making the TailoredPress a valuable investment for the future.
The partnership between Bosch Rexroth and Dieffenbacher highlights a broader trend in the industry towards the adoption of technologies that promote sustainability. As companies face increasing pressure
to reduce their carbon footprint and improve energy efficiency, collaborations like this one demonstrate how innovative solutions can help achieve these goals. The TailoredPress serves as a model for future developments in sustainable manufacturing, offering a pathway for other companies to follow in their quest for greener operations.
Arnold, a leading manufacturer in the industry, has announced the relocation of its Marengo operations to a new facility in Woodstock, Illinois. This move is part of Arnold's strategic plan to streamline operations, improve production capabilities, and better serve its customers. The new facility will feature advanced manufacturing technologies and processes that align with Arnold’s commitment to sustainability and operational efficiency. This relocation not only aims to enhance production capabilities but also to create a more sustainable and efficient working environment, supporting Arnold’s long-term growth and innovation strategy.
The new Woodstock facility is designed with sustainability in mind. It incorporates energy-efficient systems, including advanced HVAC and lighting solutions, to reduce the environmental impact of manufacturing operations. Arnold is also investing in renewable energy sources, such as solar panels, to power the facility. These initiatives are part of Arnold's broader commitment to reducing its carbon footprint and promoting sustainable manufacturing practices. The transition to the new facility is expected to be completed by the end of the year, with minimal disruption to current operations.
Arnold’s decision to relocate reflects the company's forward-thinking approach to business operations. By investing in a state-of-the-art facility, Arnold is positioning itself to better meet the needs of its customers and adapt to the evolving demands of the market. The new Woodstock facility will not only enhance production efficiency but also support the company’s efforts to innovate and develop new products. This move underscores Arnold's commitment to sustainability and its dedication to maintaining a competitive edge in the industry.
BIG DAISHOWA, a global leader in tooling systems, has announced several key personnel appointments aimed at bolstering its strategic initiatives and supporting its growth trajectory. Edgar Argueta has been appointed as the Sales Manager for the Southwest District, covering Southern California, Baja Peninsula, and Southeast Nevada. Argueta, who has been a manufacturer’s representative for the company for several years, brings a deep technical understanding of BIG DAISHOWA's product offerings and a strong commitment to customer satisfaction.
Glen James joins the company as a Sales Engineer for the Southwest District, covering Arizona and New Mexico. With over 20 years of experience in the aerospace, medical, and semiconductor industries, James’s background as a machinist and applications engineer will be invaluable in his new role.
Tom Burley has been appointed as a Sales Engineer for the Rocky Mountain District, which includes Colorado, utah, and Wyoming. Burley’s dedication to understanding each customer's unique needs and providing tailored solutions is expected to drive significant success for BIG DAISHOWA's business in the region.
Mike Herman, Vice President of Sales at BIG DAISHOWA, highlighted the importance of these appointments, noting that the experience, innovative thinking, and commitment to excellence that Argueta, James, and Burley bring align perfectly with the company’s vision for the future.
Carlisle Fluid Technologies has announced the appointment of Jeremy Renwand as a Technical Sales Specialist. Renwand brings extensive experience in fluid technologies and is expected to play a crucial role in expanding Carlisle’s market presence. His appointment is part of Carlisle’s broader strategy to enhance customer engagement and provide superior technical support. Renwand’s expertise will be instrumental in driving sales and supporting the company’s growth objectives, ensuring that Carlisle continues to deliver innovative fluid technology solutions to its customers.
Renwand will be responsible for managing key accounts and developing new business opportunities in North America. He will work closely with customers to understand their needs and provide tailored solutions that enhance their manufacturing processes. Renwand's appointment is part of Carlisle's ongoing efforts
to strengthen its sales team and expand its market reach. The company is also investing in new product development and marketing initiatives to support its growth strategy. Carlisle Fluid Technologies remains committed to providing high-quality products and services that meet the evolving needs of its customers.
The addition of Renwand to the team highlights Carlisle Fluid Technologies’ focus on building strong relationships with its customers. By prioritizing customer satisfaction and delivering exceptional technical support, the company aims to differentiate itself in a competitive market. Renwand’s experience and skills will be valuable assets as Carlisle continues to innovate and expand its product offerings.
Combilift has launched a national safety campaign titled " l ift your Standards by lowering your load" to promote forklift safety across various industries. The campaign focuses on educating operators about the importance of proper load handling techniques to prevent accidents and injuries. Combilift’s initiative includes training programs, safety guidelines, and awareness activities designed to enhance workplace safety. By advocating for better safety standards, Combilift aims to reduce the number
of forklift-related incidents and create safer working environments. This campaign underscores Combilift’s commitment to safety and its proactive approach to addressing industry challenges.
The campaign will include a series of webinars and in-person training sessions conducted nationwide. These sessions will cover key topics such as load stability, proper lifting techniques, and the importance of regular equipment maintenance. Combilift is also partnering with industry associations and safety organizations to promote the campaign and reach a wider audience. By raising awareness about forklift safety, Combilift hopes to create a culture of safety within the industry and reduce the number of accidents and injuries. The campaign is part of Combilift's broader commitment to promoting safety and sustainability in the workplace.
Combilift’s safety campaign is a timely and necessary initiative, given the prevalence of forkliftrelated accidents in many industries. By providing comprehensive training and resources, the company is taking a proactive stance to address this critical issue. The campaign not only aims to improve safety standards but also to foster a culture of responsibility and awareness among forklift operators. Through its efforts, Combilift is contributing to the overall well-being and safety of workers, reinforcing its position as a leader in the industry.
In this edition of "Talking Shop," we explore the latest advancements and significant milestones in American manufacturing. From TARuS enhancing clay milling performance with Siemens' SINuMERIK ONE to lK Metrology’s multi-sensor CMM retrofits, these innovations highlight the industry's commitment to precision and efficiency. Mazak's 50th anniversary celebration underscores decades of leadership and technological progress, while Zimmermann's new FZG portal milling machine sets a new benchmark in large-scale machining. These articles reflect the ongoing evolution of American manufacturing, showcasing how companies are leveraging cutting-edge technology to stay ahead in a competitive global market.
Sculpting the Future: TARUS Accelerates Its Clay Milling Machine Performance with SINUMERIK ONE TARuS, a prominent name in the automotive and aerospace industries, has significantly enhanced its clay milling machine performance with the integration of SINuMERIK ONE from Siemens.
The SINuMERIK ONE CNC system, known for its high-performance capabilities, has provided TARuS with the tools necessary to meet the increasing demands for precision and efficiency in design and prototyping processes.
SINuMERIK ONE is Siemens' latest and most advanced CNC system, designed to handle the most complex machining tasks with unparalleled accuracy. For TARuS, this means their clay milling machines can now deliver higher speeds and more precise cuts, significantly reducing the time required to create full-scale models and prototypes. This upgrade not only improves productivity but also enhances the quality of the final product, providing TARuS's clients with superior results.
The integration process involved extensive collaboration between TARuS and Siemens to ensure
seamless compatibility and optimal performance. Engineers from both companies worked together to fine-tune the system, ensuring that it met TARuS's specific requirements. The result is a state-of-the-art milling machine that sets new standards in the industry.
The SINuMERIK ONE system's advanced features, such as its digital twin capabilities, allow for virtual simulations of the machining process before any physical work is done. This capability enables TARuS to identify and address potential issues in the design phase, saving time and resources. By integrating this cutting-edge technology,
TARuS has positioned itself at the forefront of innovation in the automotive and aerospace sectors.
The enhanced clay milling machine offers TARuS a competitive edge in the market, allowing them to deliver faster turnaround times and higher quality prototypes. This advancement is particularly crucial in industries where time-to-market and product quality are critical factors. As a result, TARuS can better meet the demands of its clients and maintain its reputation for excellence.
The demand for multi-sensor inspection in manufacturing is on the rise, driven by the need for greater accuracy and efficiency in quality control processes. CMM (Coordinate Measuring Machine) controller retrofits have emerged as a cost-effective solution for manufacturers looking to upgrade their existing CMMs to handle multi-sensor inspection tasks.
One of the leading providers of CMM controller retrofits, lK Metrology, offers a range of retrofit solutions that enable manufacturers to integrate multiple sensors into their CMMs. These sensors can include touch probes, optical scanners, and laser scanners, providing a comprehensive inspection capability that enhances the accuracy and speed of quality checks.
The retrofit process involves upgrading the CMM's controller and software to support the new sensors. lK Metrology's retrofits are designed to be compatible with a wide range of CMM models, making it easy for manufacturers to enhance their inspection capabilities without investing in new equipment. The upgraded CMMs can perform a variety of inspection tasks, including dimensional measurement, surface scanning, and feature recognition, providing manufacturers with the flexibility to meet diverse quality control requirements.
The benefits of multi-sensor inspection are significant. By integrating multiple sensors into a single CMM, manufacturers can reduce the time and cost associated with performing separate inspections for different features.
This integrated approach also improves the accuracy of measurements, as the sensors can work together to provide a more comprehensive assessment of the part being inspected. As a result, manufacturers can achieve higher quality standards and reduce the risk of defects in their products.
Multi-sensor inspection capabilities are particularly valuable in industries such as aerospace, automotive, and medical device manufacturing, where precision and reliability are paramount. By adopting CMM controller retrofits, manufacturers can ensure that their quality control processes keep pace with the increasing complexity of modern manufacturing requirements. lK Metrology’s solutions offer a practical and effective way to enhance inspection capabilities, contributing to improved product quality and operational efficiency.
Mazak Corporation, a global leader in the manufacturing of machine tools, is celebrating its 50th anniversary of operations in Kentucky. Since establishing its North American headquarters in Florence, Kentucky, in 1974, Mazak has been at the forefront of innovation in the machine tool industry, contributing to advancements in manufacturing technology and supporting the growth of the local economy.
Over the past five decades, Mazak has expanded its operations in Kentucky, establishing a state-of-the-art manufacturing facility that produces a wide range of machine tools used in industries such as automotive, aerospace, and medical devices. The facility is equipped with advanced manufacturing technologies, including multi-tasking machines, CNC machining centers, and laser
cutting systems, enabling Mazak to deliver high-quality products that meet the evolving needs of its customers.
To commemorate this milestone, Mazak is hosting a series of events and activities throughout the year, including factory tours, technical seminars, and customer appreciation events. These celebrations provide an opportunity for Mazak to showcase its manufacturing capabilities and highlight its commitment to innovation and customer service.
Mazak's success in Kentucky can be attributed to its focus on continuous improvement and investment in new technologies. The company has consistently upgraded its manufacturing processes and equipment to stay ahead of industry trends and meet the demands of its customers. This commitment to innovation has enabled Mazak to maintain its position as a leader in the machine tool industry and contribute to the advancement of manufacturing technology.
As Mazak looks to the future, the company remains dedicated to supporting the growth of the manufacturing industry and contributing to the economic development of Kentucky. With a strong foundation built on 50 years of excellence, Mazak is well-positioned to continue its legacy of innovation and leadership in the years to come.
Zimmermann has unveiled its latest innovation, the FZG portal milling machine with a low rail gantry. This new machine is designed to provide unparalleled performance and precision in large-scale machining applications, making it an ideal solution for industries such as aerospace, automotive, and heavy machinery.
The FZG portal milling machine features a robust construction and advanced technology that ensures high rigidity and stability during machining operations. The low rail gantry design allows for greater flexibility and accessibility, enabling operators to perform complex machining tasks with ease. The machine is equipped with powerful spindle motors and high-precision linear guides, providing exceptional cutting performance and accuracy.
One of the key advantages of the FZG portal milling machine is its ability to handle large and heavy workpieces. The machine's spacious working area and high load capacity make it suitable for machining large components with complex geometries. Additionally, the machine's advanced control system and intuitive user interface ensure easy operation and precise control, enabling operators to achieve optimal machining results.
Zimmermann's FZG portal milling machine represents a significant advancement in large-scale machining technology. With its innovative design and cutting-edge features, the machine sets new standards for performance and precision, providing manufacturers with a powerful tool to enhance their production capabilities and meet the demands of modern manufacturing.
The introduction of the FZG portal milling machine demonstrates Zimmermann's commitment to innovation and excellence. By offering a machine that combines advanced technology with practical functionality, Zimmermann is helping manufacturers achieve new levels of efficiency and precision in their operations. This latest addition to their product lineup reinforces Zimmermann's position as a leader in the field of high-performance machining solutions.
In this edition of the "Safety and Maintenance" in IMD, we explore the latest advancements and technologies driving improvements in safety and productivity within American manufacturing. Highlighting innovative solutions such as lK Metrology's new measuring software, HEMCO rust-proof chemical-resistant island canopy hoods, the HEMCO Modul ab clean lab system, and Coxreels' enhanced vacuum reel options, these articles demonstrate how manufacturers are adopting cutting-edge technologies to maintain high safety standards and optimize operational efficiency. These developments underscore the industry's commitment to creating safer, more productive working environments, essential for maintaining the competitive edge of Manufacturing in America.
The latest release of lK Metrology's measuring software is set to revolutionize the manufacturing industry by enhancing both safety and productivity. The new software integrates advanced algorithms and real-time data processing to provide precise measurements, reducing the risk of errors and accidents on the production floor. With features such as automated reporting and compliance tracking, the software ensures that all safety protocols are met, thereby preventing potential hazards. The user-friendly interface and robust functionality make it an essential tool for manufacturers aiming to maintain high safety standards while optimizing their production processes.
lK Metrology's software is designed to be compatible with a wide range of measuring instruments, from handheld devices to complex coordinate measuring machines (CMMs). This compatibility ensures that manufacturers can easily integrate the software into their existing systems, maximizing its benefits without the need for significant investments in new equipment. The software also includes advanced data analysis tools that help identify trends and potential issues, allowing for proactive maintenance and continuous improvement of safety practices.
One of the standout features of this software is its automated reporting capability. This feature simplifies the documentation process, ensuring that all measurements and safety checks are recorded accurately and efficiently.
This not only enhances compliance with industry regulations but also provides valuable insights into the effectiveness of safety measures. By streamlining these processes, lK Metrology's software enables manufacturers to focus more on their core operations, improving overall productivity.
In addition to enhancing safety, the software's precision and efficiency contribute to increased productivity on the manufacturing floor. Accurate measurements reduce the need for rework and minimize downtime, allowing manufacturers to maintain high production rates. The real-time data processing capability ensures that any deviations from the norm are detected and addressed promptly, preventing small issues from escalating into major problems.
Overall, lK Metrology's improved measuring software represents a significant advancement in manufacturing technology. By promoting safety and productivity, it helps
manufacturers achieve higher standards of operation and ensures that they remain competitive in a rapidly evolving industry.
Island Canopy Hoods are essential for maintaining safe and efficient working environments in industries where corrosive vapors, heat, steam, and odors are prevalent. Manufactured from molded one-piece composite resin, these canopy hoods are lightweight yet robust, designed to collect and exhaust hazardous substances when mounted over areas with water baths, hot plates, or portable equipment. The glass smooth surfaces of the hoods provide superior chemical, corrosion, and heat resistance, ensuring long-lasting performance in harsh environments.
The design of these canopy hoods prioritizes both safety and functionality. Optional side panels prevent cross drafts and further improve airflow while providing a way to contain chemical spills. This feature is crucial in preventing the spread of hazardous substances, thereby protecting workers and maintaining a safe working environment. The lightweight construction of the hoods makes them easy to install and adjust, allowing for flexible use in various laboratory and industrial settings.
One of the key benefits of these canopy hoods is their ability to enhance workplace safety by effectively managing
hazardous fumes and vapors. The chemical-resistant materials used in their construction ensure that the hoods can withstand exposure to aggressive substances without degrading or compromising their protective properties. This durability is critical in environments where chemical spills and vapor release are common, as it helps maintain a safe and healthy work environment.
The Island Canopy Hoods can be customized with additional features such as integrated lighting and monitoring
systems. These enhancements provide users with a comprehensive solution for managing air quality and safety. By improving ventilation and reducing the risk of exposure to harmful substances, these hoods play a vital role in maintaining a safe and productive work environment.
HEMCO Rust Proof Chemical Resistant Island Canopy Hoods are an invaluable addition to any industrial or laboratory setting where hazardous substances are present. Their robust construction, superior chemical resistance, and customizable features ensure that they provide reliable protection and enhance overall safety and productivity.
The Modul ab, a state-of-the-art quality control room and clean lab solution, offers strict environmental control to meet the demanding requirements of various industrial applications. By incorporating HEPA filtration, the Modul ab regulates air quality to standards ranging from Class 1000 to Class 100000. This precise air quality control is essential for maintaining the integrity of sensitive processes in industries such as powder coating, food processing, seed production, and pharmaceutical manufacturing.
One of the standout features of the Modul ab is its ability to maintain precise temperature control. Optional modified cooling systems are available for lower temperature requirements, ensuring that the lab environment remains stable and suitable for critical operations. Additionally, humidity can be regulated with desiccant systems, which are available for applications requiring lower humidity levels. This level of control is crucial for processes that are sensitive to temperature and humidity fluctuations, as it helps prevent contamination and ensures consistent product quality.
The Modul ab's chemical-resistant modular construction provides flexibility and durability, allowing it to withstand exposure to harsh substances while maintaining structural integrity. This robustness is essential for environments where chemical spills and exposure to aggressive substances are common. The modular design also allows for easy customization and expansion, enabling users to create a controlled environment that meets their specific needs.
A variety of options are available for the Modu l ab, including a wide selection of doors, lighting, plumbing, electrical, and lab furniture systems that can be factory-installed. These features provide a comprehensive solution for creating a fully functional and efficient clean lab or quality control room. The ability to customize the lab environment to specific requirements ensures that it can support a wide range of applications and processes.
In addition to its advanced environmental controls, the Modu l ab offers a range of safety features designed to protect personnel and equipment. The integrated safety systems provide real-time monitoring and alerts for potential hazards, ensuring that any issues are detected and addressed promptly. This proactive approach to safety helps maintain a secure working environment and reduces the risk of accidents and contamination.
The Modul ab's ability to achieve strict environmental control and its robust construction make it an ideal choice for industrial applications that require high levels of cleanliness and safety. By providing a controlled environment that meets the specific needs of various processes, the Modul ab enhances productivity and ensures the integrity of critical operations.
Coxreels has expanded its V-100 Series product line with new models, including the V-112-735 and V-112H-735, designed for use with 35’ of 1 ¼” vacuum hose. These new models feature smaller frame sizes and an improved swivel design, making them more versatile and easier to handle. The enhancements to the V-100 Series Vacuum Reels focus on improving functionality and ease of use, ensuring that they meet the demanding requirements of commercial cleaning applications.
The V-112-735 and V-112H-735 models have been designed with a smaller frame size, featuring 12” diameter discs instead of the original 17” diameter discs. This compact design makes the reels more versatile and easier to handle, particularly in environments where space is limited. Despite the smaller size, the reels maintain the same high level of performance and durability that Coxreels is known for.
The improved swivel design is a key enhancement in the new models. This design allows for the connection of multiple hose sizes by using the inside and outside of the housing. The greater gradual taper of the swivel increases the number of compatible inlet hose cuffs, accommodating larger hoses up to 2.5” in diameter. This flexibility is particularly important as retail shop vacuums are coming with larger and larger hoses. The new swivel design also includes an enhanced O-ring sealing system, which ensures greater vacuum consistency and performance.
The hose used in these reels is super flexible and crush-proof, making it suitable for commercial cleaning applications. It is equipped with standard 1.5” threaded hose cuffs on both hose sizes, ensuring a secure and efficient connection. This durability is critical in commercial cleaning environments, where equipment is subject to frequent use and rough handling.
Coxreels' commitment to quality and innovation is evident in the design and construction of these new vacuum reels. The use of high-quality materials and precision engineering ensures that the reels can withstand the demands of daily use in challenging environments. By providing a reliable solution for managing vacuum hoses, Coxreels helps improve safety and efficiency in commercial cleaning operations.
Coxreels has remained steadfast and focused on manufacturing high-quality professional-grade hose, cord, and cable reels since 1923. Offering a full product line serving the industry in every channel and application, Coxreels takes great pride in designing, building, and supporting all of their products in the uSA.
The Manufacturing Showcase section in this issue highlights key advancements that are propelling American manufacturing to new heights. The rising global demand for forged parts is prompting u.S. manufacturers to rebuild and upgrade their equipment, ensuring the production of high-quality components. Dürr’s collaboration with Audi to enhance the top coat line for electric vehicles underscores the integration of cutting-edge technology, valuable for the u.S. automotive sector. Additionally, Majans' significant throughput increase, achieved through partnership with TNA Solutions, demonstrates the transformative impact of advanced packaging technology in the food industry. These stories collectively showcase the vital role of innovation in maintaining the competitiveness and growth of American manufacturing.
The global demand for forged parts continues to rise, driven by growth in industries such as automotive, aerospace, and heavy machinery. This surge has prompted manufacturers to rebuild and upgrade their forging equipment to meet the increasing demand for high-quality forged components. Rebuilding existing equipment offers a cost-effective solution to enhance production capabilities and extend the life of forging machinery.
Forging is a critical process in manufacturing, involving the shaping of metal using localized compressive forces. The resulting forged parts are known for their strength, durability, and reliability, making them essential in high-stress applications. However, the intense nature of the forging process can lead to significant wear and tear on equipment, necessitating regular maintenance and occasional rebuilds to maintain optimal performance.
To meet increased demand, forgers are seeking complete rebuilds from OEMs to ramp up production quickly.
in more consistent and higher-quality output.
Rebuilding forging equipment involves disassembling the machinery, inspecting and replacing worn components, and upgrading systems to incorporate the latest technologies. This process not only restores the equipment to its original specifications but can also improve efficiency and productivity. upgraded controls, enhanced automation, and better materials handling systems are among the improvements that can be made during a rebuild, resulting
Manufacturers are increasingly investing in advanced technologies to optimize their forging processes. For instance, integrating computerized control systems can provide precise monitoring and adjustments, ensuring that each forged part meets stringent quality standards. Additionally, implementing automation can reduce the reliance on manual labor, minimize errors, and increase overall production speed.
The benefits of rebuilding forging equipment are manifold. Enhanced efficiency and productivity lead to cost savings, while improved reliability and performance reduce downtime and maintenance costs. Furthermore, the ability
to produce higher-quality forged parts can open up new market opportunities and drive business growth.
The growing demand for forged parts is driving significant investments in rebuilding and upgrading forging equipment. By adopting advanced technologies and optimizing their processes, manufacturers can meet the rising demand for high-quality components while enhancing their operational efficiency and competitiveness.
Dürr has been selected to equip Audi’s top coat line for its electric vehicle production. This collaboration involves the installation of advanced painting robots and application technology designed to enhance the quality and efficiency of Audi’s production process. Dürr’s technology will enable Audi to achieve superior paint finishes while minimizing environmental impact. The new top coat line is part of Audi’s broader strategy to expand its electric vehicle lineup and enhance manufacturing capabilities.
The installation includes Dürr’s latest EcoBell3 atomizers, which are known for their precision and low material consumption. These atomizers ensure a high-quality finish with minimal waste, contributing to Audi’s sustainability goals. In addition to the painting robots, Dürr is providing advanced control systems that optimize the application process, ensuring consistent and efficient operation. This project highlights Dürr’s expertise in providing innovative solutions for the automotive industry and its commitment to supporting the production of environmentally friendly vehicles.
Dürr’s EcoBell3 atomizers are designed to deliver precise and uniform paint application, ensuring that every vehicle receives a flawless finish. The atomizers' low material consumption reduces paint waste, contributing to cost savings and environmental sustainability. The advanced control systems provided by Dürr enable real-time monitoring and adjustments, ensuring that the painting process is optimized for maximum efficiency and quality.
The new top coat line for Audi’s electric vehicles is equipped with the latest automation technology, enhancing the speed and precision of the painting process. This advanced technology ensures that Audi can meet the
high standards of quality expected by its customers while maintaining efficient and sustainable production practices.
Dürr’s collaboration with Audi to equip the top coat line for electric vehicles represents a significant step forward in automotive manufacturing. By integrating advanced painting technology and automation, Dürr is helping Audi achieve its goals of quality, efficiency, and sustainability in the production of electric vehicles.
Majans, a leading snack food manufacturer, has achieved a remarkable 140% increase in throughput within 12 months, thanks to its partnership with TNA Solutions. This collaboration involved the installation of TNA’s innovative ropac® 5 high-speed case packer, which has significantly enhanced Majans’ production capabilities. The ropac® 5 case packer is designed to handle high volumes with exceptional speed and precision, ensuring that products are packaged efficiently and accurately.
The increased throughput has enabled Majans to meet growing market demand and expand its product offerings. TNA’s technology has also improved operational efficiency, reducing downtime and maintenance costs. This success story underscores the importance of investing in advanced manufacturing solutions to drive growth and competitiveness in the food industry.
The ropac® 5 case packer from TNA Solutions is engineered to provide high-speed packaging capabilities, allowing Majans to significantly increase its production output. The case packer’s precision and reliability ensure that products are packaged consistently and with minimal waste, enhancing overall efficiency. This increased throughput has enabled Majans to respond more effectively to market demands and deliver products to customers more quickly.
In addition to improving production capabilities, the partnership with TNA Solutions has also brought operational efficiencies. The advanced technology of the ropac® 5 case packer reduces downtime and maintenance requirements, allowing Majans to maintain high levels of productivity. The system’s ease of use and reliability have also contributed to reduced operational costs, making it a valuable investment for the company.
Majans’ partnership with TNA Solutions demonstrates the significant impact that advanced manufacturing technologies can have on production capabilities and operational efficiency. By leveraging TNA’s innovative solutions, Majans has achieved impressive growth and enhanced its ability to meet market demands.
The partnership between Majans and TNA Solutions has resulted in a 140% increase in throughput within 12 months, highlighting the benefits of investing in advanced manufacturing technologies. This collaboration has enhanced Majans’ production capabilities, improved operational efficiency, and supported the company’s growth and competitiveness in the snack food industry.
As industrial automation continues to shape the future of manufacturing in America, companies like Fronius are leading the way with innovative solutions that enhance productivity, efficiency, and quality. This section explores how Fronius Welding Automation's cutting-edge technologies are transforming overlay welding processes, providing American manufacturers with the tools they need to stay competitive in a global market.
Fronius, based in Austria, is one of the world’s leading manufacturers of overlay welding systems and consistently introduces new innovations, such as the award-winning SpeedClad 2.0 process. Fronius Welding Automation offers complete systems and expert customer service from the initial planning stages through the entire service life of a welding system. This commitment ensures that users benefit from state-of-the-art technology for years to come, particularly in the competitive landscape of American manufacturing.
Fronius provides comprehensive support from planning, engineering, manufacturing, and commissioning to the
maintenance and servicing of overlay welding systems. All systems comply with international standards, ensuring safety and reliability. Technical commissioning by Fronius experts and preliminary acceptance by buyers, particularly from the oil and gas industry, take place at the production site in Steinhaus, Austria. The systems are then delivered, installed on-site, and accepted by international customers in the onshore and offshore sectors, including those in America. Fronius' comprehensive commissioning service includes expert training and process optimizations at the start of production, ensuring that American manufacturers can achieve peak performance and efficiency.
Every new overlay welding project at Fronius begins with feasibility studies and welding tests. Overlay welding is complex, with numerous factors influencing the result.
Welding tests are conducted under realistic conditions using the same materials and environmental conditions expected during live operations. This ensures the system delivers the desired results even under harsh conditions. Anton leithenmair, Head of Fronius Welding Automation, emphasizes the importance of realistic testing to meet customer requirements and achieve optimal welding results, a crucial aspect for maintaining high standards in American manufacturing.
With over forty years of experience, Fronius has developed application-based overlay welding systems tailored to customer needs. The Compact Cladding Cell (CCC) offers a compact, user-friendly solution for valve component cladding. The Endless Torch Rotation System (ETR) is ideal for larger, complex components, featuring an endlessly rotating welding head that enhances productivity and reduces setup times. Both systems incorporate advanced features such as 21-inch touch displays, real-time process visualization, and multi-user management, providing American manufacturers with versatile and efficient tools for various applications.
SpeedClad 2.0 sets new standards in overlay welding with its high deposition rate, impressive speed, and low
shielding gas consumption. It significantly improves the efficiency and cost-effectiveness of welding processes, earning the Excellence in Welding Award from the American Welding Society. The SpeedClad 2.0 process uses a 1.6 mm wire, increasing the welding speed and reducing argon gas consumption, making it an ideal choice for valve component welding in the American manufacturing industry.
Fronius also offers longitudinal and circumferential seam welding systems, robotic welding systems, and more. These solutions are designed to meet the diverse needs of metal processing companies. Fronius continues to innovate, with a focus on sustainability and reducing consumables. The company's commitment to customer support and technological advancement ensures that Fronius Welding Automation remains a leader in the field, benefiting American manufacturers by providing reliable and cutting-edge technology.
Fronius will showcase these innovations at the ADIPEC trade show in Abu Dhabi from November 4-7, 2024, Hall 14, Stand 14316. The Fronius team looks forward to demonstrating their cutting-edge solutions for cladding and 3D metal printing, which are highly relevant to American manufacturers seeking to enhance their operations.
The American manufacturing industry is currently facing a significant labor shortage, a challenge that has been exacerbated by the COVID-19 pandemic and the retirement of the baby boomer generation. This section delves into the causes, risks, and solutions related to this labor shortage and highlights the achievements of Kaiser Tool Company as it celebrates its 60th anniversary. understanding and addressing these workforce challenges are crucial for maintaining productivity, profitability, and operational efficiency in American manufacturing.
The manufacturing industry is currently facing a significant labor shortage, a challenge that has been exacerbated by the COVID-19 pandemic and the retirement of the baby boomer generation. This shortage poses substantial risks to productivity, profitability, and overall operational efficiency. understanding the underlying causes and developing effective solutions is crucial for industry leaders and risk managers.
Several factors contribute to the labor shortage in manufacturing:
» Aging Workforce: A significant portion of the manufacturing workforce comprises baby boomers who are now reaching retirement age. The departure of these experienced workers creates a gap that is difficult to fill with younger, less experienced employees.
» Perception of Manufacturing Jobs: Many young people view manufacturing jobs as outdated, low-paying, and lacking career advancement opportunities. This perception discourages them from pursuing careers in the industry.
» Skills Gap: The rapid advancement of technology in manufacturing requires workers with specialized skills. There is a growing mismatch between the skills required by modern manufacturing processes and the skills possessed by the available labor force.
» Economic Factors: Economic fluctuations, such as recessions and slowdowns, can lead to layoffs and reduced hiring in the manufacturing sector. This uncertainty makes it challenging to attract and retain workers.
The labor shortage in manufacturing introduces several risks that can affect overall operations:
» Workplace Injuries: With fewer workers available, existing employees may be required to work longer hours or take on additional responsibilities, increasing the risk of fatigue-related accidents and injuries.
» Product liability: A shortage of skilled workers can lead to quality control issues, resulting in defective products. This can expose manufacturers to significant product liability risks and damage their reputation.
» Property Damage: Inexperienced or overworked employees are more likely to make mistakes that could lead to equipment damage or operational disruptions.
» Production Delays: Insufficient staffing can cause production bottlenecks and delays, leading to missed deadlines and dissatisfied customers.
To address the labor shortage, manufacturers must implement comprehensive strategies that focus on attracting, retaining, and developing talent:
» Promote Manufacturing Careers: Manufacturers need to change the perception of manufacturing jobs by highlighting the industry's technological advancements, competitive salaries, and career growth opportunities. Outreach programs targeting schools and colleges can help attract young talent.
» Invest in Training and Development: Providing ongoing training and development programs can help bridge the skills gap. Manufacturers should offer apprenticeships, internships, and partnerships with educational institutions to equip workers with the necessary skills.
» Adopt Automation and Technology: leveraging automation and advanced manufacturing technologies can help mitigate the impact of the labor shortage. While technology cannot replace all human workers, it can enhance productivity and reduce the reliance on manual labor.
» Improve Working Conditions: Enhancing the work environment by offering flexible schedules, competitive benefits, and a focus on employee well-being can make manufacturing jobs more attractive.
» Retention Strategies: Implementing retention strategies, such as recognition programs, career development opportunities, and employee engagement initiatives, can help retain valuable employees and reduce turnover.
Kaiser Tool Company, a renowned name in the manufacturing industry, is celebrating its 60th anniversary. Since its founding, Kaiser Tool has been a pioneer in developing innovative cutting tools and solutions that have set new standards in the industry. The company’s commitment to quality, innovation, and customer service has been the cornerstone of its success and longevity.
Over the past six decades, Kaiser Tool has continuously adapted to the evolving needs of the manufacturing industry. The company has invested heavily in research and development, leading to the creation of cutting-edge products that enhance productivity and efficiency. Kaiser Tool’s comprehensive product portfolio includes a wide range of tooling solutions for various applications, from automotive to aerospace.
Kaiser Tool's success is largely attributed to its focus on innovation. The company has consistently introduced new technologies and products that address the changing demands of the manufacturing industry. For instance, Kaiser Tool has developed advanced cutting tools that provide superior precision and durability, enabling manufacturers to achieve higher quality standards and improved operational efficiency.
Quality has always been a top priority for Kaiser Tool. The company adheres to stringent quality control processes to ensure that its products meet the highest standards. This commitment to quality has earned Kaiser Tool a reputation for reliability and excellence, making it a trusted partner for manufacturers worldwide.
Customer service is another key aspect of Kaiser Tool’s success. The company works closely with its customers to understand their needs and provide tailored solutions that enhance their manufacturing processes. Kaiser Tool's dedicated customer support team is always ready to assist with technical inquiries, product recommendations, and after-sales service, ensuring that customers receive the best possible support.
To commemorate this milestone, Kaiser Tool is hosting a series of events, including technical seminars, factory tours, and customer appreciation days. These events aim to showcase the company’s rich history, technological advancements, and vision for the future. Kaiser Tool’s leadership attributes its success to a dedicated workforce, strong customer relationships, and an unwavering commitment to excellence.
looking ahead, Kaiser Tool plans to continue its legacy of innovation and quality. The company is exploring new technologies and expanding its product offerings to meet the evolving needs of the manufacturing industry. Kaiser Tool remains committed to supporting its customers and contributing to the advancement of manufacturing technology.
In the ever-evolving landscape of American manufacturing, staying ahead of technological advancements is crucial for maintaining competitiveness and operational efficiency. This section highlights the latest breakthroughs in manufacturing technology, showcasing how companies like ANCA, ABB, AMADA WElD TECH, and Thomson Industries are driving innovation. These new technologies are transforming precision grinding, automation, welding, 3D printing, and mechanical components, offering manufacturers the tools to enhance productivity and quality in their operations.
ANCA, a renowned manufacturer of CNC grinding machines, showcased its latest innovations at IMTS 2024, featuring the MicroX ulTRA grinding machine and AIMS Connect. These advanced solutions cater to the growing demand for precision and automation in the manufacturing industry.
The MicroX ulTRA grinding machine is designed for high-precision applications, offering unparalleled accuracy and repeatability. It features a robust design and advanced control systems that enable it to handle complex grinding tasks with ease. The machine's high-resolution feedback systems ensure tight tolerances, making it ideal for industries such as aerospace, medical devices, and precision engineering.
Equipped with ANCA's proprietary software, the MicroX ulTRA provides intuitive and powerful tools for programming and monitoring grinding operations. This software allows seamless integration with other manufacturing systems, facilitating a streamlined and efficient production process. The machine’s advanced spindle technology ensures smooth operation and superior surface finishes, enhancing the overall quality of the final products.
AIMS Connect is ANCA's comprehensive automation platform designed to enhance connectivity and efficiency in manufacturing operations. This platform integrates seamlessly with ANCA's grinding machines, providing real-time data and analytics to monitor and optimize production processes. It supports various automation solutions, including robotic loading and unloading, palletizing, and in-process measurement,
enabling manufacturers to achieve higher levels of productivity and quality.
The platform's user-friendly interface and robust functionality make it an essential tool for modern manufacturing environments. AIMS Connect helps manufacturers reduce downtime, improve process accuracy, and enhance overall operational efficiency, making it a valuable addition to any production facility.
ABB Robotics has introduced OmniCore, an intelligent automation platform designed to enhance business productivity and flexibility. OmniCore integrates AI, sensor, cloud, and edge computing systems, allowing for advanced and autonomous robotic applications. It increases robot
path accuracy, speed, and energy efficiency, making it suitable for various industries.
» Real-Time Data Processing and Analytics: OmniCore's advanced features include real-time data processing and analytics, enabling manufacturers to monitor and optimize their production processes continuously. This capability ensures that robots can learn and adapt to new tasks, improving their performance over time.
» Cloud Integration: The platform's cloud integration facilitates remote monitoring and maintenance, reducing downtime and enhancing overall productivity. This feature is particularly beneficial for large-scale manufacturing operations that require constant oversight and optimization.
safely alongside human operators. This feature is crucial in industries where complex and repetitive tasks require a combination of human dexterity and robotic precision.
» Collaborative Robotics: OmniCore supports collaborative robotics, allowing robots to work
By leveraging the capabilities of OmniCore, manufacturers can achieve higher levels of automation
and efficiency, driving growth and competitiveness in their operations.
AMADA WElD TECH, a leader in welding technology, has announced the release of the Wl-300A Precision laser Welding Workstations. These workstations are designed to provide high-precision welding capabilities for various applications, including medical devices, automotive components, and electronics.
» Advanced laser Technology: The Wl-300A workstations feature advanced laser technology that ensures precise and consistent welds, even in challenging materials and configurations. This capability is essential for industries that demand high-quality and reliable welding solutions.
» user-Friendly Control Systems: The workstations are equipped with AMADA WElD TECH's latest control systems, which allow easy programming and monitoring of welding operations. These systems include user-friendly interfaces and advanced data analysis tools that help operators achieve optimal welding results.
» Safety Features: Designed with safety in mind, the Wl-300A workstations include a range of safety features such as enclosed work areas, fume extraction systems, and safety interlocks. These features protect operators and ensure a safe working environment, making the workstations an ideal solution for manufacturers looking to enhance their welding capabilities and improve overall productivity.
With the launch of the ultiMaker Factor 4, a new and exciting engineering 3D printing material has been introduced: ultiMaker PPS CF (Polyphenylene Sulfide Carbon Fiber). Developed by a leading materials science company, PPS CF offers exceptional strength, heat resistance, and chemical resistance, making it ideal for a wide range of industrial applications.
Advantages of PPS CF
» Superior Mechanical Properties: PPS CF is engineered to provide high tensile strength and stiffness. The addition of carbon fiber reinforcement enhances these properties, making it an excellent choice for parts requiring durability and dimensional stability. The material’s stiffness and density give it a distinctive metallic sound, indicative of its well-defined molecular structure.
» High Temperature and Chemical Resistance: PPS CF offers excellent resistance to high temperatures and aggressive chemicals, ensuring long-term performance in challenging environments. This makes PPS CF suitable for applications in aerospace, automotive, and chemical
processing industries. Specifically designed for use with the ultiMaker Factor 4 and print core HT, PPS CF boasts a heat deflection temperature exceeding 230 °C post-printing, making it an exceptional choice for high-temperature applications.
» Compatibility with 3D Printing Technologies: PPS CF is compatible with industrial 3D printing technologies such as selective laser sintering (SlS) and fused
deposition modeling (FDM). This compatibility allows manufacturers to produce complex and high-precision parts with ease, reducing the need for traditional manufacturing processes.
» Extreme Durability: PPS CF is designed to withstand the harshest environments, offering exceptional chemical resistance, heat resistance, and dimensional stability. This high-performance material ensures that your industrial prototypes or functional end-use parts maintain their integrity over time, even under the most demanding conditions.
» Versatility and Performance: ultiMaker PPS CF offers a compelling alternative to traditional materials like steel and aluminum. This means that manufacturers can harness the advantages of additive manufacturing, including lightweighting, reduced waste, and complete design freedom. The result is a versatile, cost-effective solution that doesn't compromise on performance. PPS CF’s versatility and performance make it an ideal solution for producing functional prototypes, tooling, and end-use parts in various industries.
Thomson Industries has introduced a new line of miniature metric ball screws, designed to provide high load capacity
are ideal for applications where space is limited, but high performance is required, such as in medical devices, robotics, and aerospace components.
» High load Capacity and Precision: The miniature ball screws are engineered to handle high loads and provide exceptional accuracy, making them suitable for demanding applications. The advanced engineering and manufacturing techniques ensure consistent performance and reliability.
» Compact Design: The ball screws' compact design allows for easy integration into existing systems with limited space. This feature is particularly beneficial for industries that require miniaturized components without compromising on performance.
» Optimized Ball Recirculation Systems: The ball screws feature optimized ball recirculation systems that minimize friction and increase efficiency. This design ensures smooth operation and enhances the lifespan of the components.
» Versatile Mounting Options: Thomson's miniature metric ball screws are available in various sizes and configurations, providing versatile mounting options. The company's engineering team works closely with customers to provide tailored solutions that meet
As manufacturing processes in America become increasingly digitalized, the need for robust cybersecurity measures has never been more critical. Cyber threats pose significant risks to operational efficiency and data integrity, making it essential for manufacturers to adopt advanced cybersecurity solutions. Siemens is at the forefront of this effort, offering cutting-edge technologies like SIBERprotect™ and SINEC Security Guard to safeguard industrial operations. These innovative solutions are designed to protect critical infrastructure and production assets, ensuring resilience and security in the face of evolving cyber threats.
Siemens introduces SIBERprotect™, an advanced, real-time cyber-attack response solution designed to protect industrial OT systems. This innovative technology can respond to cyber-attacks within milliseconds, isolating and quarantining infected production equipment to facilitate faster resumption of normal operations.
Developed after years of technical development and operational design, SIBERprotect™ is aimed at protecting critical infrastructure and OT systems across various industrial sectors, including power plants, water treatment facilities, discrete manufacturing enterprises, military depots, data centers, and control stations. SIBERprotect™ integrates the SOAR (Security, Orchestration, Automation, Response) concept into cyber-physical systems with an OT-friendly and OT-managed approach.
SIBERprotect™ works with Siemens SCA l ANCE S industrial security appliances to securely isolate
OT systems after identifying credible cyber-attacks through top-tier threat detection technologies such as Intrusion Detection Systems, Next Generation Firewalls, Endpoint Solutions, Threat/Risk Intelligence, and other detection platforms enhanced with AI and machine learning capabilities. The system then initiates a rule-based response to protect selected equipment, allowing rapid assessment and remediation to prevent further contamination.
Key features of SIBERprotect™ include:
» Real-Time Response: Isolates infected equipment within milliseconds, facilitating quick remediation and resumption of normal operations.
» Multi-l ayered Protection: Integrates with existing security technologies to provide comprehensive protection.
» Detailed Situational Awareness: Provides operators with real-time alerts and critical information about threats, enabling immediate and effective response.
» Automation and Safety: Automatically activates emergency backup equipment and interfaces with legacy technologies to maintain operational continuity.
Chuck Tommey, a digital connectivity executive with Siemens, explains, “SIBERprotect™ represents a reimagining of how to implement SOAR, sending alerts directly to PlCs for instant action based on threat levels.”
SIBERprotect™ is part of Siemens’ “Defense In Depth” suite, compliant with IEC 62443, the international standard for industrial cybersecurity.
Siemens Xcelerator introduces SINEC Security Guard, a cloud-based software-as-a-service designed to improve cybersecurity on the shop floor by automatically identifying vulnerable production assets. This innovative tool allows users to map vulnerabilities to their OT assets, prioritize them, and engage in effective mitigation measures.
SINEC Security Guard offers automated vulnerability mapping and security management optimized for industrial operators in OT environments. The software can automatically assign known cybersecurity vulnerabilities to the production assets of industrial companies, enabling operators and automation experts to identify risks among their OT assets and receive risk-based threat analysis. The software then recommends and prioritizes mitigation measures, which can be planned and tracked using the tool’s integrated task management feature.
“With SINEC Security Guard, customers can focus their resources on the most urgent and relevant vulnerabilities while having full risk transparency in their factory,” says Dirk Didascalou, CTO of Siemens Digital Industries. “It provides a single pane of glass for security-relevant information in the OT area, taking into consideration the specific situation of the customer’s operational environment.”
SINEC Security Guard also supports connection to Microsoft Sentinel, Microsoft’s Security Information and Event Management (SIEM) solution. This integration allows SINEC Security Guard to send alerts for security events to Sentinel, enabling a comprehensive view of IT and OT cybersecurity and facilitating proactive threat detection, investigation, and response.
Key features of SINEC Security Guard include:
» Automated Vulnerability Mapping: Assigns known cybersecurity vulnerabilities to OT assets for risk-based analysis and mitigation.
» Integrated Task Management: Plans and tracks mitigation measures to ensure timely response to identified risks.
» Comprehensive IT and OT Security: Connects to Microsoft Sentinel for a unified approach to cybersecurity across IT and OT environments.
» Real-Time Network Monitoring: utilizes the SINEC Security Guard Sensor App for live information about
industrial networks, supporting signature-based network intrusion and attack detection.
SINEC Security Guard will be available for purchase in July 2024 on the Siemens Xcelerator Marketplace and the Siemens Digital Exchange.
To find out more information about SIbERprotect, please visit: usa.siemens.com/industrial-cybersecurity
Further details on the new SINEC Security g uard can be found at: www.usa.siemens.com/sinec-security-guard
SINEC Security Guard - Siemens uSA Siemens DCp, Disha patel
The American manufacturing landscape is undergoing significant transformations driven by technological advancements, sustainability initiatives, and strategic investments. This collection of articles provides an in-depth look at the latest industry trends and innovations that are shaping the future of manufacturing in the united States. From the rise of sustainable practices and AI integration to major expansion projects, these insights highlight how American manufacturers are adapting to meet the demands of a dynamic global market. By embracing these changes, the industry is poised to achieve greater efficiency, productivity, and environmental responsibility, securing its competitive edge in the years to come.
Sustainable manufacturing has become a critical focus for industries worldwide as businesses seek to balance economic growth with environmental responsibility. This trend is driven by increasing regulatory pressures, consumer demand for eco-friendly products, and the need to reduce operational costs through energy efficiency and waste reduction. Companies across various sectors are adopting innovative practices and technologies to minimize their environmental impact and improve sustainability.
One significant trend in sustainable manufacturing is the integration of renewable energy sources. Many manufacturers are investing in solar, wind, and other renewable energy systems to power their operations. This shift not only reduces reliance on fossil fuels but also helps companies mitigate the risks associated with fluctuating energy prices and regulatory changes. By generating their own clean energy, manufacturers can achieve greater energy independence and cost stability.
Another key trend is the implementation of circular economy principles. The circular economy aims to keep products, materials, and resources in use for as long as
possible, minimizing waste and environmental impact. Manufacturers are embracing this concept by designing products for durability, repairability, and recyclability. They are also developing innovative processes to recycle and repurpose waste materials, turning them into valuable resources for new products. This approach not only conserves natural resources but also opens up new revenue streams and reduces waste management costs.
Advanced manufacturing technologies, such as additive manufacturing (3D printing) and digital twins, are also playing a crucial role in promoting sustainability. Additive manufacturing allows for precise production with minimal material waste, enabling manufacturers to create complex
parts and components more efficiently. Digital twins, virtual replicas of physical assets, help optimize manufacturing processes by simulating different scenarios and identifying opportunities for energy and resource savings. These technologies enhance product design, production efficiency, and overall sustainability.
Sustainable supply chain practices are becoming increasingly important as manufacturers seek to reduce their environmental footprint. This includes sourcing materials from environmentally responsible suppliers, optimizing logistics to reduce transportation emissions, and implementing sustainable packaging solutions. Companies are also focusing on transparency and traceability in their supply chains, ensuring that their products are ethically and sustainably produced.
Toyota Material Handling has announced a nearly $100 million expansion project at its North American headquarters. This significant investment aims to enhance the company’s production capabilities and support its
long-term growth strategy. The expansion will include the addition of new manufacturing facilities and the implementation of advanced production technologies. This project reflects Toyota Material Handling’s commitment to innovation and its dedication to meeting the growing demand for material handling solutions.
The expanded headquarters will enable Toyota to better serve its customers and continue its leadership in the
AXIAL PISTON PUMPS… Oilgear open loop
axial piston pumps are offered in a variety of models and displacement sizes to match required performance. Models include both medium and high horsepower, medium and heavy duty, low viscosity pumps, plus a series of multiple fixed delivery pumps. Of the many industries Oilgear serves, a primary one is mobile and off-highway applications. Oilgear pumps are recognized for high performance in the toughest environments. Their heavy duty designs resist contamination as well as operating on low viscosity specialty fluids.
VARIABLE PUMPS…
Whatever the application, Oilgear has the ideal pump to fulfill the requirements.
MULTIPLE FIXED DELIVERY
CHECK VALVE PUMPS…
• High pressure to 15,000 psi
• Heavy duty construction
• High contamination tolerance
• Operation on low viscosity fluids
• Multiple deliveries up to three displacements from a single pump
industry. One of the key components of the expansion is the incorporation of advanced automation systems. These systems are designed to improve production efficiency, reduce operational costs, and enhance the quality of the company’s material handling equipment. By integrating cutting-edge technologies, such as robotics and IoT, Toyota aims to create a more agile and responsive manufacturing environment.
In addition to technological advancements, the expansion project emphasizes sustainability. Toyota is investing in renewable energy sources, energy-efficient building designs, and sustainable manufacturing practices to reduce its environmental footprint. The new facilities will feature solar panels, energy-efficient lighting, and advanced HVAC systems to minimize energy consumption. These initiatives align with Toyota’s global commitment to sustainability and environmental stewardship.
The expansion project is also expected to create hundreds of new jobs, contributing to the local economy and
supporting the growth of the manufacturing sector. Toyota is committed to fostering a diverse and inclusive workforce, providing employees with opportunities for career development and advancement. The company’s investment in training and education programs will ensure that its workforce is equipped with the skills needed to thrive in a technologically advanced manufacturing environment.
A recent study has found that 90% of manufacturers are now utilizing artificial intelligence (AI) in some capacity within their operations. This widespread adoption reflects the growing recognition of AI's potential to enhance productivity, efficiency, and innovation in manufacturing. AI technologies are being used to optimize various aspects of production, from predictive maintenance and quality control to supply chain management and product design.
Predictive maintenance is one of the most common applications of AI in manufacturing. By analyzing data
from sensors and equipment, AI algorithms can predict when machinery is likely to fail and schedule maintenance before a breakdown occurs. This proactive approach helps minimize downtime, reduce maintenance costs, and extend the lifespan of equipment. Manufacturers can also use AI to optimize production schedules, ensuring that resources are allocated efficiently and production targets are met.
AI-driven quality control systems are also becoming increasingly prevalent. These systems use machine learning algorithms to analyze images and data from production lines, identifying defects and anomalies in real-time. By detecting quality issues early in the production process, manufacturers can reduce waste, improve product quality, and enhance customer satisfaction. AI can also help identify patterns and trends in quality data, providing insights that can be used to refine processes and prevent future defects.
In supply chain management, AI is being used to enhance forecasting accuracy, optimize inventory levels, and improve demand planning. AI algorithms can analyze vast amounts of data from various sources, such as sales records, market trends, and weather patterns, to predict demand more accurately and adjust inventory
accordingly. This helps manufacturers reduce excess inventory, minimize stockouts, and improve overall supply chain efficiency.
The integration of AI into product design and development is also on the rise. AI-powered tools can analyze data from previous designs and customer feedback to generate new design concepts and optimize existing ones. This accelerates the design process and helps create products that better meet customer needs and preferences. Additionally, AI can be used to simulate and test product designs, identifying potential issues and improvements before physical prototypes are built.
The rise of sustainable manufacturing practices, the significant expansion projects like Toyota's $100M investment, and the widespread adoption of AI in manufacturing all highlight the dynamic and evolving nature of the industry. These trends are driving improvements in efficiency, productivity, and environmental responsibility, positioning manufacturers to better meet the challenges of the modern market. As businesses continue to innovate and adopt new technologies, the future of manufacturing looks promising, with a strong focus on sustainability and intelligent automation.
Industrial Machinery Digest's Monthly Product Showcase features the latest from some of the manufacturing industry's top suppliers.
WANT TO BE FEATURED? Send your latest product information to editorial@indmacdig.com
ABB l aunches
Next-Generation Robotics
Control Platform OmniCore
ABB Robotics introduced the OmniCore™ platform, an intelligent automation solution resulting from a $170 million investment. OmniCore enhances productivity and flexibility with faster, more precise, and sustainable automation. The platform's modular architecture integrates AI, sensor, cloud, and edge computing, enabling advanced robotic applications. OmniCore offers class-leading motion performance with path accuracy below 0.6mm and speeds up to 1,600mm/ sec. It allows robots to operate 25% faster and consume 20% less energy. The platform supports over 1,000 hardware and software features, providing extensive customization options for businesses in various industries. OmniCore replaces ABB's IRC5 controller, which will be phased out by June 2026. This new platform marks a significant leap forward in the field of robotics, showcasing ABB's commitment to innovation and sustainability in manufacturing. The OmniCore platform is expected to play a crucial role in the evolution of automated production lines, offering unparalleled flexibility and efficiency for a wide range of applications.
AMADA WElD TECH Announces the Release of the Wl-300A Precision l aser Welding Workstations
AMADA WElD TECH Inc. announced the Wl-300A precision laser welding workstations for continuous wave (CW) or quasi-continuous wave (QCW) fiber lasers, targeting battery manufacturing applications. The Wl-300A integrates laser, motion, cameras, and process monitoring in a CDRH Class 1 workstation. The compact design includes standard air-cooled CW or QCW fiber lasers and various options for rotary stages and viewing
systems. The workstation supports multiple welding types, including spot, spiral, wobble, and seam welding. The Wl-300A features user-friendly Windows 11 compatible software, easy CAD vector file importing, and a threaded hole pattern base plate for easy part fixturing. This workstation represents a significant advancement in laser welding technology, offering manufacturers in the battery sector enhanced precision and efficiency. The Wl-300A's versatility and advanced features make it a valuable addition to any production line, ensuring high-quality welds and improved operational productivity.
Arnold umformtechnik GmbH & Co. KG developed the Powertite fastener, a round self-tapping screw with a trilobular tapping zone for lightweight metals. The screw's design reduces tapping torque and increases load-bearing capacity, providing standards-compliant tapping torques and optimal assembly reliability. Powertite screws are suitable for applications requiring maximum clamping forces and high hole tolerances. The product is ideal for the electromobility sector, offering significant weight reduction and repeat fastening capabilities. Arnold umformtechnik plans to launch the patented Powertite screw in October, with extensive support and expertise available for customers in various industries. This innovation in fastening technology addresses the growing demand for efficient and reliable fasteners in the automotive and electronics industries, ensuring secure assemblies and enhanced performance.
Coxreels expanded its V-100 Series with the V-112-735 vacuum hose reel and the V-112H-735 model with hose. The new models feature smaller 12” diameter discs for use with 35’ of 1 ¼” vacuum hose. The series' swivel design now accommodates larger hose cuffs up to 2.5”, and an enhanced O-ring sealing system ensures greater vacuum consistency. The hose is crush-proof with a smooth
interior for commercial cleaning applications. Coxreels continues to manufacture high-quality hose, cord, and cable reels in the u.S., offering comprehensive support and products for various industry applications. These improvements in the V-100 Series vacuum reels highlight Coxreels' commitment to providing durable and efficient solutions for the cleaning and maintenance sectors, ensuring long-lasting performance and reliability.
E-Z lOK offers E-Z™ Knife brass and stainless steel threaded inserts for hardwoods like oak, cherry, and maple. These inserts prevent thread erosion and stripping during assembly or disassembly. Featuring a proprietary external "knife" thread, they ensure superior holding power and easy installation. Brass inserts are ideal for furniture and cabinetry, while stainless steel versions suit marine applications. E-Z™ Knife inserts provide a simple solution for adding machine threads to hardwoods and are not recommended for plywood. CAD files for these inserts are available on the E-Z lOK website. These threaded inserts represent a practical solution for enhancing the durability and functionality of wood-based projects, catering to a wide range of industrial and commercial applications.
Release Ball lock Pins from Fairlane Products
Offer Secure Holding
Fairlane Products offers T-shaped and l-shaped handle quick release ball lock pins, ideal for secure fastening and easy tool-less removal. Available in sizes ranging from 3/16" to 5/8" (metric versions from 5mm to 16mm), these pins ensure secure holding with positive-locking mechanisms. Handles are made from aluminum alloy or stainless steel, featuring
split rings for cable attachment. Fairlane Products also provides a wide range of workholding and positioning components, including rest pads, Swivots®, and clamping systems, ensuring reliable and efficient fastening solutions for various industrial applications. These quick release ball lock pins enhance the efficiency and safety of assembly and maintenance operations, offering robust and versatile solutions for industrial settings.
Fixtureworks introduced a larger flanged clamping module with 35kN clamping force for its 5-axis modular clamping systems. The system, designed for large workpieces and molds, offers 5-micron locating repeatability and easy tool access. The modular pull clamping system eliminates tool interference and increases efficiency. The new flanged module measures approximately 100 x 100 mm and is made from induction-hardened steel. Fixtureworks also offers various other modular clamping systems and workholding components, including retractable ball lock fasteners, pneumatic swing clamps, and adjustable torque handles, catering to diverse clamping applications. This expansion of Fixtureworks' product line demonstrates the company's commitment to providing innovative and reliable clamping solutions for complex machining operations.
IPG Introduces IMA Brand E-CO Flex
IPG® launched the IMA brand E-CO Flex SealMatic, a fully automated case sealer for FEFCO 201 cases, adjusting to case sizes automatically. using water-activated tape (WAT) technology, it seals cases at speeds up to 20 boxes per minute. The SealMatic can process a wide range of case sizes, automatically bypassing SIOC cases. Optional features include hazmat labeling, shipping label application, and quality inspection cameras. Its compact size allows seamless integration into existing layouts, offering advanced automation solutions for e-commerce and packaging industries. This innovation in case sealing technology addresses the increasing demand for efficient and flexible packaging solutions, ensuring high throughput and reliability.
Norstat offers the DNS Inclination Switch, featuring 4 independently adjustable switching outputs and a high-quality MEMS sensor unit. These switches provide fast visual feedback through a display with status and crosshair lEDs. The robust IP67 metal housing and encapsulated electronics make the DNS switch suitable for mobile machines, off-road systems, and EV charging stations. The switch offers a 4x PNP output signal with NO/NC function and is available with various adjustment ranges. Operating voltage is 9-30 VDC, with a protection rating of IP67, and operational temperatures from -25°C to +80°C. These features make the DNS Inclination Switch an ideal choice for applications requiring precise and reliable inclination measurement in harsh environments.
Norstat introduces the MBI Black series of industrial enclosures, combining modern design with technical performance for discreet installations. These enclosures, available with plain side walls or pre-formed metric knockouts, integrate seamlessly
into industrial environments. They feature foamed-in polyurethane gaskets, corrosion-free plastic cover screws, and various fastening options. MBI Black series boxes offer IP66 protection, IK08 impact resistance, and ul 90 V0 self-extinguishing properties. Suitable for hidden installations, these enclosures provide reliable and secure housing for industrial applications. The MBI Black series represents a blend of aesthetic design and robust functionality, catering to the needs of modern industrial settings.
Hommel + Keller Quick® Knurling and Marking Tools Now Available from Platinum Tooling in North America
Platinum Tooling, the North American importer of Hommel & Keller’s QuICK® knurling and marking tools, offers solutions for various industries including medical, aerospace, and automotive. QuICK® knurling tools support form and cut knurling for a wide range of workpiece diameters, including small tools for Swiss-type lathes. QuICK® marking tools enable rapid workpiece marking on diverse surfaces and geometries. The tools, known for precision and high-quality finishes, are ideal for applications requiring absolute precision and first-rate surface quality, such as medical instruments, automotive parts, and fitness equipment. These tools enhance manufacturing processes, ensuring high standards of quality and efficiency.
SAKOR Technologies Announces Dynamometer line for Testing Electric Motor Efficiency to Meet International Environmental Standards
SAKOR Technologies introduced a dynamometer line for testing electric motor efficiency in compliance with international standards such as IEC 60034-2-1 and IEEE 112B. The systems, capable of testing motors from 10 watts to over 3 megawatts, ensure high-accuracy efficiency measurement. Optimized to test a wide range of motor sizes, SAKOR’s dynamometers meet stringent data precision and accuracy requirements. These systems help engineers enhance energy efficiency and reduce fossil fuel consumption. SAKOR offers high-accuracy testing
solutions for various motor sizes, supporting the global effort to meet environmental standards. This product line demonstrates SAKOR's commitment to advancing motor efficiency and sustainability in engineering.
Thomson Miniature Metric Ball Screws Provide High load Capacity in a Small Footprint
Thomson Industries introduced miniature metric ball screws, offering high load capacity in a compact design. Featuring a unique multi-start ball return design, these screws maximize support for higher loads, providing precise, smooth, and quiet operation. Ideal for laboratory, medical, and space-constrained applications, Thomson's ball screws handle loads of up to 7.6 kN with repeatability of 0.05 mm. Available in various sizes and mounting options, they are constructed from carbon steel and can be customized with coatings such as thin dense chrome and black oxide. These ball screws address the demand for high-performance components in precision applications, ensuring reliability and accuracy.
Trim-lok Showcases Innovative All-in-One RV Slide Out Seal System and Patented Seamless Corner Installation in New Video
Trim-lok released a video showcasing its All-in-One RV Slide Out Seal System and patented seamless corner installation method. The comprehensive lineup includes
wipe seals, bottom pans, and wear bars, ensuring optimal performance for various RV slide-out configurations. The All-in-One Wipe Seal, installed with a patented seamless corner method, provides maximum watertightness, reducing the risk of water or air ingress. Trim-lok's innovative solutions streamline RV sealing, improving performance and minimizing installation time while maintaining quality. This product line highlights Trim-lok's dedication to providing effective and user-friendly sealing solutions for the RV industry.
PPS CF: The Newest Factor 4 Material for Industrial 3D Printing ultiMaker introduced PPS CF, an engineering 3D printing material for the ultiMaker Factor 4. PPS CF offers exceptional chemical resistance, heat resistance, and dimensional stability, making it ideal for high-temperature applications. The material's crystalline structure provides a unique metallic sound, indicating its durability. PPS CF is a suitable alternative to PEEK and metal, offering precision and reliability for industrial prototypes and functional end-use parts. The material ensures precise, smooth, and quiet operation, supporting additive manufacturing's advantages like lightweighting and reduced waste. This new material expands the capabilities of 3D printing, providing robust solutions for demanding industrial applications.
fulfillment with unprecedented speed and flexibility. The system uses TowerBots driven by AI to retrieve totes from a dense storage grid, enabling rapid multi-SKu order fulfillment. TowerBots move vertically and horizontally, allowing access to inventory stacked up to 75 totes high within seconds. The system's design supports high-density storage and fast order processing, suitable for urban distribution centers where space efficiency is crucial. urbx's innovative solution addresses the growing demand for rapid and efficient fulfillment operations. This system revolutionizes the logistics of retail fulfillment, ensuring high speed and accuracy in order processing.
urbx Introduces Robotic Inventory Storage and Retrieval System for Rapid Retail Fulfillment urbx launched a robotic inventory storage and retrieval system, enhancing e-commerce, retail, and grocery
Walter unveils the XTRA∙TEC® XT M5250 Helical Milling Cutter with BC System Inserts Walter introduced the XTRA∙TEC® XT M5250 helical milling cutter, offering high metal removal rates and process reliability. Available in various diameters, the cutter uses proven BC 1605 system inserts for full slotting, shoulder milling, and ramping. The SC 1105 inserts provide excellent operational smoothness, while the G51 geometry is ideal for long overhangs and vibration-prone applications. Walter's latest cutter generation features optimized insert pocket design, separate tool cooling, and high-performance cutting tool materials, ensuring reliable and efficient machining for aerospace, energy, and mechanical engineering applications. This new milling cutter addresses the need for high-performance machining tools, offering enhanced efficiency and reliability.
Quickly grind and remove welds, deburr rough edges, and polish hard-to-reach areas. American-made quality tools are precision designed and manufactured, allowing for fast and efficient production with less rework.
Experience the ease of working with Dynabrade with free on-site demonstrations, excellent customer service, and products that are in-stock and ready for immediate shipment.