


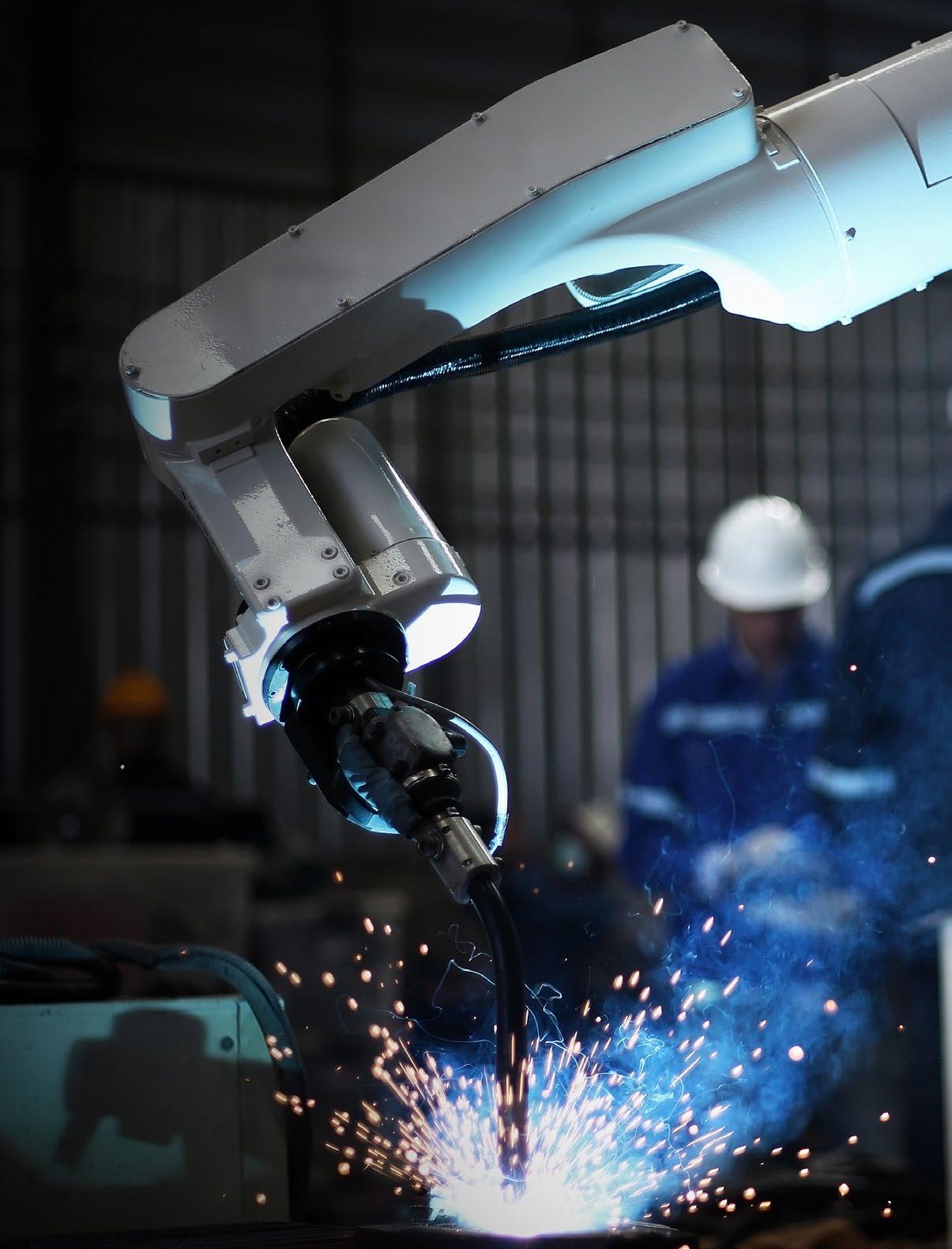
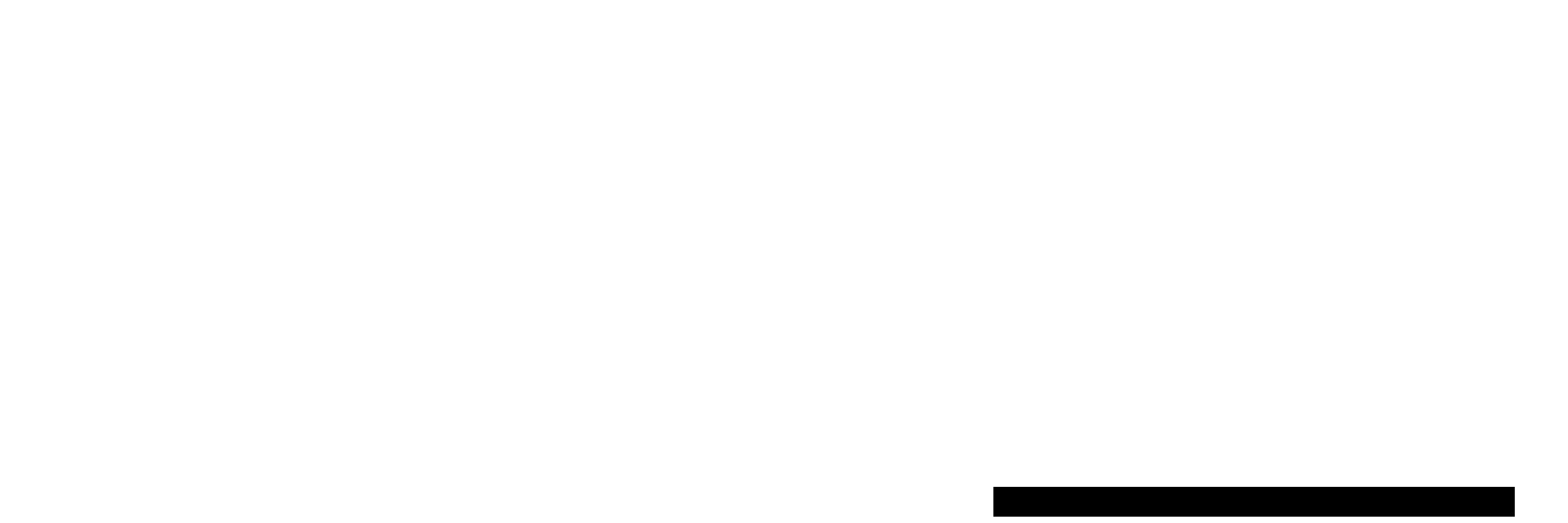
FUMEVAC’S ERGOBOOM maximizes weld fume gun usability
IVEC SYSTEMSTHE POWER OF
FUMEVAC’S FV-190 is a portable, continuous duty unit for weld fume extraction applications
Designed to get the most from your process ventilation equipment by monitoring fume exhaust and dust loads, then automatically adjusting the fan speed to provide optimum ventilation. IVEC gives you the power to cut costs, maximize resources and gain a competitive edge.
North America’s Manufacturing Resource for Industry Professionals Since 1986
William c. Strickland III, Publisher william.strickland@indmacdig.com 800-366-0676 ext. 103 | Fax: 866-826-5918
Adrienne Gallender, Associate Publisher/Media Advisor
agallender@indmacdig.com 847-612-1572 | Fax: 847-559-2909
brian Self, Associate editor brian@indmacdig.com 800-366-0676 ext. 104 | Fax: 866-826-5918
Shane bell, creative Director sbell@indmacdig.com
SALES
Lisa Hanschu, Sr. Account executive lisa@indmacdig.com 785-965-9159 | Fax: 785-965-7199
William c. Strickland III, National Sales 205-903-9178 | fax 866-826-5918
Susan Strickland, Accounting susan@indmacdig.com 205-542-1098 | Fax: 866-826-5918
CIRCULATION & SUBSCRIPTIONS
IMD, 3590-b Hwy 31 South, Suite 233, Pelham, AL 35124 circulation@indmacdig.com | Fax: 866-826-5918
REPRINTS to purchase article reprints please call 800-366-0676 ext. 103 or email wstrickland@indmacdig.com
3590-b Hwy 31 South PMb #233 Pelham, AL 35124
INDUSTRIAL MACHINERY DIGEST (ISSN 1542-5223) is published 12x per year by Source 360 Media. POSTMASTER: Please send change of address to INDUSTRIAL MACHINERY DIGEST, 3590-B US Hwy 31 South, PMB 233, Pelham, AL 35124. Printed in the U.S.A. SUBSCRIPTION POLICY: Individual subscriptions are available without charge in the U.S. to qualified individuals. Publisher reserves the right to reject nonqualified subscribers. One-year subscription to nonqualified individuals in the United States: $96.00. Single copies available (prepaid only) $20.00 each.
Welcome to the FAbtecH edition of Industrial Machinery Digest. FAbtecH, the world’s leading event for metal forming, fabricating, welding, and finishing, is just around the corner, promising an exceptional showcase of innovations that are set to shape the future of manufacturing. this year's event will emphasize key trends in automation, safety, connectivity, and precision, highlighting the industry’s relentless pursuit of efficiency and excellence.
At FAbtecH, AtI Industrial Automation will present the GbX 10 Gigabit ethernet Module, a breakthrough designed to optimize robotic tool changer performance in smart manufacturing environments. this high-speed module enhances communication between vision systems, inspection tools, and motion control systems, embodying the advancements in automation and connectivity that FAbtecH champions.
Fixtureworks is set to impress attendees with their new Heavy-Duty retractable ball-Lock Fasteners, engineered for quick-change applications. these fasteners deliver superior clamping and holding forces, enhancing efficiency and precision in industrial setups. their innovative design underscores the event’s focus on improving operational workflows and reliability.
In the realm of material handling, tAb Industries will showcase the tAb Wrapper tornado, an orbital stretch wrapper that secures long and awkward products without the need for custom pallets or crates. this solution not only enhances delivery safety but also streamlines logistics, demonstrating practical applications of advanced manufacturing technologies.
trUMPF will unveil the truMatic 5000, a fully automated punch-laser combination machine that integrates seamlessly into connected manufacturing cells, boosting productivity while minimizing energy consumption. Alongside, their truLaser Series 3000 bevel cut edition will demonstrate cutting-edge capabilities in bevel generation, reducing downstream processes and enhancing precision.
As FAbtecH approaches, Industrial Machinery Digest is excited to bring you in-depth coverage of these innovations and more. this issue delves into the technologies that will drive the future of manufacturing, providing you with the insights needed to stay ahead in this dynamic industry.
thank you for joining us in exploring the latest trends and technologies shaping the future of manufacturing. We hope you find this edition both informative and inspiring.
Warm regards,
William Strickland, Publisher, IMD
Industrial Machinery Digest's Industry News features the latest news and press releases from some of the industry's top companies.
WANT TO BE FEATURED? Send your press releases to editorial@indmacdig.com
3D Systems expands High Precision Investment casting Portfolio with Quickcast Air™
3D Systems (NYSe) has announced the launch of Quickcast Air™, an advanced tool designed to enhance their investment casting portfolio. this innovative software maximizes material removal from casting pattern interiors, leading to cleaner burnout processes and more efficient draining. customers utilizing Quickcast Air™ have reported up to a 50% reduction in material consumption and significant multi-hour decreases in build times. this advancement marks a pivotal shift in material efficiency, making Quickcast Air™ cost-competitive with traditional injection-molded wax patterns. the tool is integrated into 3D Systems’ 3D Sprint® software and is available via an annual subscription. It allows users to design casting patterns with fewer internal structures, resulting in less resin usage and easier resin drainage. Quickcast Air™ supports the creation of highly precise, complex geometric patterns, catering to industries such as aerospace, defense, and energy. As additive manufacturing continues to grow, projected to reach a $33.9 billion market by 2034, 3D Systems remains at the forefront, driving innovation and efficiency in investment casting. Patrick Dunne, VP of Advanced Applications, emphasized the company’s commitment to customer-centric innovation, enhancing design freedom and accelerating production timelines.
For More Information: www.3dsystems.com
equipment for battery and eV Manufacturing at the battery Show AMADA WeLD tecH is set to showcase its latest laser and resistance welding technologies at the battery Show from October 7-10, 2024, at Huntington Place in Detroit, Michigan.
Located in booth 3011, the company will display a range of cutting-edge equipment, including the WL-P300A Laser Processing Workstation, Ub-4000A Linear Dc Welding Power Supply paired with the tL-188b-eZ Weld Head, MAWA-300b Pulsed Micro tIG Welding Power Supply and torch, WM-200A IIot-ready Networked resistance Weld Monitor, and the MM-400b and MM-410b resistance Weld Monitors. these products are designed to meet the growing demands of battery and electric vehicle (eV) manufacturing, offering high precision, efficiency, and reliability. the WL-P300A workstation is optimized for various metals and is ideal for battery tab welding, while the Ub-4000A power supply ensures consistent welding conditions with advanced control features. the MAWA-300b and networked weld monitors enhance process reliability and traceability. AMADA WeLD tecH’s participation underscores its commitment to supporting the evolving needs of the battery and eV sectors with innovative welding solutions.
For More Information: www.amadaweldtech.com
AMADA WeLD tecH, Inc., a leader in welding, marking, cutting, micromachining, sealing, and bonding equipment, will present its advanced medical device manufacturing solutions at MD&M Minneapolis on October 16-17, 2024, at the Minneapolis convention center. Visitors can explore booth #3209 to discover a variety of welding and laser technologies tailored for the medical industry. Highlights include the WL-300A class 1 Laser Workstation, optimized for diverse metals and ideal for creating machine-readable marks and welding electrical components. Additionally,
ONE CARBIDE SAW DOES THE WORK OF FIVE CONVENTIONAL FACTORY BAND SAWS, WITHOUT SACRIFICING QUALITY
Cut 4 to 5 times faster than a conventional band saw with a clean surface finish that seldom requires a secondary operation. Standard features on all HYDMECH
CSNC-Series high production circular saws include:
• automatic bar loading magazine with adjustable incline
• mist fume exhaust system
• automatic lubrication system for all moving parts
• programmable part cut length and trim cut length
• automatic sorting of trim cuts, remnants, and cut parts
• automatic chip auger
• mist blade lubrication system
• remote diagnostic service
AMADA will demonstrate the Ub-1500A Low Power Linear Dc Micro Spot Welder with the SL-321A Light Force Motorized electromagnetic Weld Head, designed for precise micro-welds essential in medical device manufacturing. A live demonstration of the WM-200A IIot-ready Networked Weld Monitor will showcase its capability to collect high-resolution waveform data for process analysis and traceability. the exhibit will also feature the SIGMA® LS Laser Micromachining Subsystem, offering high-precision processing in a compact form. AMADA WeLD tecH aims to highlight its reliable and durable solutions that enhance efficiency and quality in medical device production.
For More Information: www.amadaweldtech.com
beckhoff
beckhoff Automation has inaugurated a new regional office in Greater Atlanta, specifically in Alpharetta, Georgia. Spanning over 5,000 square feet, this facility serves as a hub for local sales, support engineers, and regional training and seminar activities. the strategic location in Alpharetta, known as the “ technology city of the South,” positions beckhoff to leverage the area’s robust talent pool and proximity to over 600 tech companies. the office features a state-of-the-art training room to keep customers and employees abreast of the latest advancements in automation software, networking, and motion control. Additionally, a dedicated research and development room supports special projects and proof-of-concept validations, fostering collaboration across various industries. buck tanner, business Development Manager at beckhoff USA, highlighted that the new office underscores beckhoff’s commitment to expanding its market presence and enhancing customer support in the Southeast U.S. this expansion complements beckhoff’s recent openings and relocations in Los Angeles, chicago, and Austin, texas, further strengthening its nationwide footprint.
For More Information: www.beckhoff.com
combilift Wins two Major Accolades at UKMHA Archie Awards!
combilift has achieved significant recognition at the recent UK Materials Handling Association (UKMHA) Archie Awards held in birmingham on September 14th. the company secured two prestigious awards: ‘ergonomic Innovation of the Year’ for the combi-cb70e forklift and ‘Manufacturer Product Innovation of the Year’ for the combi Lc blade. the combi-cb70e, a 7-ton electric-powered multidirectional counterbalance forklift, was lauded for its ergonomic design, featuring an Auto Swivel Seat that reduces driver strain and a gas strut suspension system ensuring a smooth ride on uneven terrain. Its independent electric traction system enhances safety and precision when handling long, heavy loads. the combi Lc blade, designed in collaboration with Siemens Gamesa, addresses the logistical challenges of transporting large offshore wind turbine blades. this
innovation ensures unparalleled stability and safety, setting a new industry standard. Martin McVicar, ceO and co-Founder of combilift, expressed pride in winning these awards, highlighting the team’s dedication to pushing the boundaries of material handling solutions. these accolades reinforce combilift’s reputation as a leader in innovative and ergonomic material handling equipment.
For More Information: www.combilift.com
Guill Announces Guill tool europe
Guill tool, a global leader in extrusion tooling, has announced the expansion of its presence in the european market with the establishment of Guill tool europe. this new entity will offer a comprehensive range of Guill products, along with dedicated sales and engineering support across europe. Padraic Lunn will continue to represent Guill in the UK through Padraic Lunn enterprises Ltd, which provides extrusion machinery and consultancy services with a focus on tubing, wire, pipe, and profile applications. With over 60 years of expertise, Guill tool europe aims to deliver high-quality extrusion solutions, maintaining the company’s renowned standards across various applications, including regular extrusion, multilayered applications, jacketing, multi-lumen, rubber, and silicone. the expansion is supported by local sales representatives in each country, enabling Guill to establish a robust presence on the european continent. this strategic move underscores Guill’s commitment to supporting clients from concept design and engineering to manufacturing and process support, ensuring customers receive tailored solutions to meet their extrusion needs.
For More Information: www.guilltool.com
MAHLe Aftermarket Achieves Milestone in Operational efficiency with AutoStore empowered by Kardex
MAHLe Aftermarket has successfully implemented the AutoStore empowered by Kardex robotic cube storage system at its fulfillment center in Olive branch, Mississippi. Faced with a shift from large pallet orders to mixed-SKU single cartons
and experiencing storage constraints, MAHLe sought a high-density, scalable storage solution. the AutoStore system, featuring 42,000 bins, 7 ports, and 18 robots, along with a connected conveyor solution, has significantly increased storage capacity by up to four times and enhanced order fulfillment performance by up to ten times compared to traditional methods. this automation allows MAHLe to efficiently store more products in less space and ship small orders with greater speed and accuracy. the successful deployment was complemented by Kardex’s FulfillX software, which integrated seamlessly with MAHLe’s existing SAP Warehouse Management System. the project’s success has led MAHLe to expand the AutoStore solution to a second facility in Décines-charpieu, Lyon, France, and evaluate its applicability across other global locations. MAHLe Aftermarket praises Kardex for their hands-on support and end-to-end solution approach, which was pivotal in the project's smooth implementation and scalability for future growth.
For More Information: www.kardex.com
experience 'Flexible Sustainability' Showcased through a range of New Packaging Solutions by PAc Machinery at Pack expo International 2024 PAc Machinery is set to present its innovative concept of ‘Flexible Sustainability’ at Pack expo International 2024, held at Mccormick Place in chicago from November 3-6, 2024.
Located at booth S-2130, PAc Machinery will exhibit a variety of new packaging solutions designed to offer flexibility and sustainability. the theme emphasizes the ability to use both paper and plastic on the same machine, allowing companies to adapt to evolving regulations and consumer preferences without the need for additional machinery investments. Featured products include the FW 650SI Flow Wrapper, rollbag® r3200 and r3200XL Fulfillment Paper Automatic baggers, and the 6800cS-HS Side Sealer Shrink Wrap. these machines support curbside recyclable paper and plastic with up to 100% recycled resins, enabling environmentally friendly packaging options. Greg berguig, President of PAc Machinery, highlighted that these solutions provide companies with the ability to future-proof their packaging processes, ensuring compliance with stricter plastic regulations. Attendees will have the opportunity to witness high-quality packaging machinery in action and engage with PAc ’s packaging experts. PAc Machinery, with over 60 years in the industry, continues to focus on sustainable packaging innovations, offering comprehensive solutions to meet diverse packaging needs.
For More Information: www.pacmachinery.com
Sandvik coromant’s Stephanie chrystal Wins ANcA Female Machinist Award for Pioneering excellence in tool Grinding
Stephanie chrystal, a geometric grinding specialist at Sandvik coromant's Westminster Solid round tools Production Unit, has been honored with the AN c A Female Machinist Award. t his accolade recognizes her outstanding achievements in the tool and cutter grinding industry, highlighting her innovative problem-solving skills and dedication to excellence. Since joining Sandvik coromant through the acquisition of Precorp, Stephanie has been instrumental in expanding and training her team, growing from three operators in 2022 to nine in 2024. Her leadership has not only met but consistently surpassed production expectations, breaking records month after month. Gunnar Sterner, Production Unit Director, praised Stephanie's passion and commitment, while Veronica Messersmith, President of Americas for Sandvik coromant, commended her for inspiring excellence within the industry. t he AN c A Female Machinist Award underscores the importance of gender diversity and recognizes the significant contributions of female machinists like Stephanie in advancing the tool grinding field.
For More Information: www.sandvikcoromant.com
SMe Introduces “ready to Hire” to Deliver a Qualified talent Pipeline for Manufacturers
Amidst a persistent labor shortage, SMe has launched the “ready to Hire” program in partnership with cengage Group to address the manufacturing industry's need for a skilled workforce. this innovative program aims to build sustainable talent pipelines by providing manufacturers with access to pre-screened, pre-trained, and committed employees. recognizing the critical demand for entry-level roles trained in both technical and soft skills, ready to Hire streamlines the hiring process through a scalable, trainto-hire model. this approach allows employers to focus on team building and retention while SMe and cengage handle sourcing, screening, training, and onboarding. the program guarantees retention for referred candidates up to three months post-hire, enhancing long-term employee stability. targeted training programs include roles such as cNc machinist, welding technician, robotics technician, press operator, additive manufacturing, and electrical vehicle technician, with certifications like SMe’s certified Manufacturing Associate (cMfgA). ready to Hire leverages successful models from other industries, ensuring high-quality, consistent candidates ready to meet the evolving needs of the manufacturing sector.
For More Information: www.sme.org
By Aquant
You’re missing key details when you measure service KPIs in a vacuum. Instead, focus on a holistic view of your service organization. change the way you think about KPIs. Increase visibility into every corner of service. bridge the skills gap. Improve c S across the entire organization.
t he five KPIs service leaders need to measure, along with why we need to them differently and how to incorporate Service Intelligence Metrics into your data-driven service organization:
t he service industry has changed dramatically in recent years, and the way we measure success needs to change as well. Here are a few of the reasons why traditional KPIs are no longer enough:
» t he workforce is changing. t here is a labor shortage, and the skills gap between new recruits and retirees is widening. t his means that service organizations
need to find ways to measure the effectiveness of their workforce, not just their individual KPIs.
» customers are more demanding. today's customers expect fast, efficient, and personalized service. traditional KPIs, such as First t ime Fix rate (F tFr), don't take into account the customer's overall experience.
» technology is changing the game. New technologies, such as artificial intelligence and the Internet of t hings (Iot ), are giving us new ways to collect and analyze data. t his data can be used to develop more accurate and insightful KPIs.
Service Intelligence Metrics are a new generation of KPIs that are designed to provide a more holistic view of your service operation. t hey take into account not just the individual tasks that are performed, but also the impact of those tasks on the customer experience. Here are five examples of Service Intelligence Metrics:
» customer e xperience Index (cXI): t he cXI looks at
service from the customer's point of view. It considers factors such as quality of service, resolution time, and effort required.
» Mean time to Stability (Mtt S): Mtt S is a measure of how long it takes to resolve a customer issue for good. It takes into account all of the interactions between the customer and the service organization, not just the initial service call.
» cost per Successful resolution (cPS): cPS is a more accurate measure of service cost than traditional KPIs like cost per Work Order (cPWO). It takes into account all of the costs associated with resolving a customer issue, not just the cost of the initial service call.
» Mean time between events (Mtbe): Mtbe is a measure of the average time between customer interactions. It can be used to identify potential problems and areas for improvement.
» customer risk Score: t he customer risk Score is a data-driven way to assess the likelihood that a customer will experience a service issue in the future. t his information can be used to proactively address potential problems and prevent them from happening in the first place.
t he first step to implementing Service Intelligence Metrics is to identify the data you need to collect. t his data will come from a variety of sources, including your crM system, your service management system, and your customer satisfaction surveys.
Once you have collected your data, you can start to develop your Service Intelligence Metrics. t here is no one-size-fits-all approach to this, as the specific metrics you will need to track will vary depending on your industry and your business goals.
However, there are a few general tips to keep in mind:
» Focus on metrics that are actionable. t he goal of Service Intelligence Metrics is to help you improve your service operation, so make sure you are tracking metrics that you can actually do something about.
» Use a combination of quantitative and qualitative metrics. Quantitative metrics provide you with hard data that you can use to track your progress over time. Qualitative metrics can help you to understand the why behind the numbers.
» Don't get bogged down in too many metrics. It's important to track a few key metrics that are important to your business, rather than a bunch of vanity metrics that don't provide any real insights.
by following these tips, you can start to implement Service Intelligence Metrics and gain a more holistic view of your service operation. t his will help you to improve the customer experience, reduce costs, and achieve your business goals.
In the fast-paced world of industrial automation, safety is paramount. As machines become more complex and capable, the risks to human workers also increase. this is where companies like reer Safety come in.
Founded in torino, Italy, over 65 years ago, reer has a long history of providing safety solutions to industries around the world. Starting as a distributor, the company transitioned into manufacturing safety products and lighting. today, reer is a global leader in the field of industrial safety, offering a wide range of products designed to protect both workers and machines.
What sets reer apart from other safety companies is their application-based approach. Instead of offering a one-sizefits-all solution, reer takes a consultative approach to each application, tailoring their products to meet the specific needs of their customers. this ensures that the safety measures implemented are not only effective but also efficient and cost-effective.
the automation industry is constantly evolving, and reer is committed to staying ahead of the curve. by investing in research and development and collaborating with industry partners, reer is able to develop new products that meet the changing needs of their customers. For example, reer is currently working on a new light curtain designed for high-temperature environments.
reer's product line includes a variety of safety sensors and controllers, such as:
» Door switches
» Interlocks
» Light curtains
» Safety controllers
these products are designed to prevent accidents by detecting potential hazards and stopping machinery before harm can occur. For example, light curtains use laser beams to create a safe zone around machines. If a worker enters the zone, the machine automatically stops.
While collaborative robots (cobots) are designed to be safer than traditional industrial robots, they still pose risks. reer's safety solutions can be used to protect workers from potential hazards associated with cobots, such as sharp tooling or unexpected movements.
reer has formed partnerships with several leading companies in the automation industry, including Mechademic Industrial robotics, FANUc, and reiku. these partnerships allow reer to offer complete safety solutions to their customers.
reer's commitment to safety and innovation has been recognized by the industry. the company has exhibited at numerous trade shows, including IMtS, and has received positive feedback from customers and industry experts.
In the world of industrial automation, safety is a top priority. reer Safety is a company that is dedicated to protecting workers and machines. With their focus on applicationbased safety, innovative products, and strong partnerships, reer is well-positioned to be a leader in the field of industrial safety for years to come.
MEETS OR EXCEEDS ASME B30.26 REQUIREMENTS
SETTING NEW STANDARDS FOR SAFE LIFTING
• Now up to M1000 (UNC 4")
• Up to 30% higher WLL
• No more transverse loads
• No unexpected sagging of the load
• No more worst case!
DOWNLOAD THE ACP TURNADO BROCHURE HERE
Enclosed robotic laser parts cleaning systems are poised to safely remove rust and contamination as well as condition surfaces at dramatically higher volumes and at lower cost than conventional methods.
By Del Williams
today, advancements in industrial laser cleaning automation show great promise in boosting productivity and safety when rust and contaminant removal or surface preparation is required for higher volumes of components and equipment. Specifically, combining lasers and advanced robotics within enclosed workcells enables operators to efficiently and repeatedly clean components of different sizes, shapes, and materials on a level previously unattainable through manual methods.
“Automated laser cleaning systems are designed to cost-effectively clean high volumes of even the
largest format parts and equipment and can be tailored to suit the size and complexity of the parts, while eliminating concerns over operator safety,” says Wayne tupuola, ceO, Orlando, Florida-based Laser Photonics (NASDAQ: LAS e ), a leading global industrial developer of laser systems for cleaning and other material processing applications.
Industrial manufacturers frequently need to remove corrosion, grease, residue, and old coatings, or roughen the surface of metals prior to coating components and equipment. At times, contaminants or toxic substances need to be eliminated before further processing.
the challenge is that conventional methods like sandblasting, dry ice blasting, and chemical stripping are messy, time and labor intensive including preparation and cleanup, and require costly consumables. these methods can also pose risks to applicators and the environment so are scrutinized by regulators like OSHA and ePA.
As a much more efficient alternative, a laser cleaning robotic workcell usually consists of at least one laserwielding robot, controllers, and safety equipment in a custom, see-through enclosure. these collaborative robots, or cobots, excel at tasks like the laser cleaning of parts which involve repetition, freeing up employees to work on other activities.
the cleantech robotic cell from Laser Photonics, for example, utilizes a robotic arm that holds a “laser gun” with cleaning, roughening, and finishing capabilities. the robotic arm is programmable via a tablet/controller where the operator would input the coordinates for material processing. the cleaning laser can be replaced with a welding or cutting laser. If required, the workcell can be split into two sections – the robot cleans on one side, while an operator installs a part to be cleaned on the other side.
“ the operator can lay out several components for cleaning over the flatbed, set the cleaning coordinates, and leave the robot processing,” explains tupuola.
He points to advancements in laser technology that complement and expedite the efficient cleaning of such shapes.
“Dual axis laser technology enables the cleaning of target areas more effectively and quickly if they are complex and uneven,” adds tupuola. “Plus, our proprietary technologies allow the laser to move in various directions and clean hard-to-reach areas.”
Manufacturers of larger format components can find useful laser systems like Laser Photonics’ cleantech titan FX, which offers up to a 6’ x 12’ work envelope for automated laser cleaning, rust removal, and surface conditioning. this industrial, turnkey laser cleaning giant can operate as a standalone unit or be easily integrated into a production line environment.
“Large format automated laser cleaning systems can expedite the processing of [applications like] automotive tire rims, molds, oil and gas flanges, or even sheets for the hull of a ship or other vessel,” says tupuola. He notes that the size and configuration of the enclosures can be customized to accommodate the size and nature of the parts that require cleaning, with the lasers operating at a range of power levels.
Another significant benefit to such automation is improved operator and environment safety.
“For extra safety, our custom-tailored automated laser systems are enclosed in a class I safety workcell. We can also integrate dust and residue collection, as well as a fume extractor that captures vapors during the cleaning of toxic substances,” says tupuola.
this type of advanced laser cleaning equipment is designed to accommodate rigorous safety regulations. As
an example, Laser Photonics’ cleantech systems can help businesses achieve compliance with OSHA regulations and make environmentally responsible decisions in accordance with ePA’s waste management guidelines.
Abrasive sandblasting involves forcefully projecting a stream of abrasive particles onto a surface, usually with compressed air or steam. the silica sand used in abrasive blasting typically fractures into fine particles and becomes airborne, which can cause serious or fatal respiratory disease. Particles from the coatings, plating, anodizing, corrosion, and even lead paint being removed can also be inhaled. to avoid breathing in particulates, operators must wear full HePA suits when sandblasting.
With chemical stripping, harsh chemicals are used to strip metal-based objects of paint, rust, and other contaminants to bare metal – potentially exposing operators to corrosive acids and noxious chemical fumes. In addition, disposing of toxic chemicals is costly and closely regulated. Laser cleaning seeks to solve or minimize these issues.
Unlike conventional methods, the laser cleaning systems require no consumables other than electric power, minimal labor, and minimal maintenance. the longevity and low-maintenance design of these industrial-grade robotic laser cleaning systems further adds to their value, increasing rOI, and making replacement unnecessary for decades.
Programming the laser ablation procedure with a cobot workcell can be accomplished with a touchscreen. Generally, programming includes setting coordinates for the sample, ablation pattern, power output, and cleaning speed, according to tupuola.
“Installation and programming are needed, but once it’s set up, robotic cell cleaning is fast, precise, thorough, and controlled. So, it’s a very convenient, optimized process if the parts being cleaned are the same,” says tupuola.
tupuola adds that Laser Photonics is now working on integrating 3D scanners into the robotic workcell. this would automate the focusing of the laser and eliminate some of the programming now done by an operator.
While precision laser-based systems have been effectively used to remove rust, residues, contaminants, and paint, this approach commonly involves manual labor. Automated robotic laser cleaning systems provide manufacturers safer, easier, more eco-friendly options. to meet demand more efficiently, a growing number of manufacturers across a wide range of industries will increasingly turn to these laser systems to cost-effectively clean higher volumes of components with the control and speed required for decades to come.
For more information on laser cleaning solutions for surface preparation, contact Laser Photonics at (407) 804-1000 or visit www.laserphotonics.com.
ABOUT THE AUTHOR:
Del Williams is a technical writer based in torrance, california.
At IMtS 2024, brian Self of IMD’s Industry Insight podcast, interviewed Fredrik ryden, ceO of Olis robotics, to discuss the company's innovative video-based diagnostic system for robots and automation. this article dives deeper into the conversation, exploring how Olis empowers businesses of all sizes to optimize their automation processes.
Introducing Olis: Seeing is believing Olis robotics offers a unique approach to robot troubleshooting. Unlike traditional methods, which rely on log files and error codes that can be cryptic for non-experts, Olis leverages video alongside data. the system captures video recordings whenever an issue arises, synchronized with corresponding log files from all connected robot controllers, including the recently integrated rockwell Allen-bradley PLcs. this comprehensive data allows users
to not only see the problem but also understand the context in which it occurred.
Unlocking New Possibilities with PLc Integration
the integration with rockwell Allen-bradley PLcs represents a significant leap forward for Olis. Previously limited to individual robots, the system can now monitor entire automation cells encompassing multiple robots and PLcs. this opens doors for applications in various industries, including the automotive sector that wasn't previously well-served by Olis' technology.
Demystifying Data: Actionable Insights at Your Fingertips
Olis goes beyond simply capturing data. It empowers users to extract actionable insights. the system allows for historical data analysis, enabling proactive maintenance
by identifying trends that could lead to future problems. Users can configure alerts based on specific parameters, receiving notifications when cycle times increase unexpectedly or consumable resources start to dwindle.
One of the most significant advantages of Olis lies in its ability to facilitate remote troubleshooting. the system allows users to access critical data and live video feeds from anywhere with an internet connection. this is particularly valuable for small and medium-sized businesses (SMbs) that may lack in-house robot expertise. Olis enables them to connect with remote experts who can diagnose problems and guide them through solutions, eliminating the need for costly on-site visits.
Olis caters to a broad spectrum of users. For first-time robot adopters, the system provides invaluable training wheels. When unexpected issues arise, they can receive remote support, helping them understand the problem and troubleshoot effectively. this fosters a
learning environment where users gain confidence in operating their robots.
On the other end of the spectrum, Olis caters to high-stakes operations with significant downtime costs. t he system's ability to synchronize and present data from various sources enables rapid decisionmaking, minimizing downtime and safeguarding production schedules.
t he rise of lights-out manufacturing and automation in warehouses underscores the need for reliable remote monitoring solutions. Olis perfectly aligns with this trend. businesses can rest assured that their robots are functioning optimally, even during off-hours. early detection of problems prevents production delays and ensures on-time deliveries.
t he high turnover rate in the robotics industry poses a challenge for automation users. Olis offers a solution by providing access to a network of remote experts. even if a company lacks an in-house robot expert,
they can still leverage Olis to connect with qualified professionals when needed.
beyond the Interview: resources for the curious Interested in learning more about Olis robotics? t here are numerous resources are readily available.
» connect with Fredrik ryden on LinkedIn: Search for "Fredrik ryden ceO of Olis robotics" to connect directly with Fredrik.
» Visit the Olis robotics website: explore Olisrobotics. com to find detailed information about the system, its capabilities, and case studies.
» explore the Olis Youtube channel: Access the Olis Youtube channel directly from the website to watch informative videos showcasing the system in action.
Olis robotics is revolutionizing the way businesses approach robot troubleshooting and maintenance. by leveraging video-based diagnostics and facilitating remote support, Olis empowers users of all sizes to optimize their automation processes, unlock efficiencies, and achieve their production goals. As the industry continues to embrace automation, Olis is poised to play a pivotal role in ensuring its smooth and successful implementation.
Fronius is taking a revolutionary step in terms of sustainability and its use of resources by carrying out a certified life cycle assessment (LCA) for welding applications. Taking a holistic view of welding, from device manufacturing through customer use to end of life, yields insights into the key areas where we can reduce the carbon footprint. As pioneers in the industry, we are looking to address these areas in cooperation with our customers.
there’s no question that welding creates long-lasting bonds between metals. but how can we make this process one that will last by enhancing its sustainability in the customer’s application—in terms of the environmental impact? “For our customers, in addition to cost effectiveness, the carbon footprint of their production processes and components is becoming more and more important. that’s why we want to create added value for the users of our welding solutions, not only by further minimizing the carbon footprint of our devices, but also by helping companies to reduce their consumption of resources during welding,” emphasizes Harald Scherleitner, Global Director of Sales and Marketing, business Unit Perfect Welding, Fronius International GmbH.
t he discussion around sustainability is emotionally charged, but at Fronius, our approach to sustainability centers on the evidence. We start by bringing the facts to the table: “We examined two typical, real-world applications that our customers use when welding steel and aluminum, and had the analysis certified by the highly regarded Fraunhofer Institute,” explains David Schönmayr, team Leader for Product Sustainability at Fronius International GmbH. Fronius experts, together with partner to4to (together for tomorrow), meticulously assessed the environmental effects of the welding variables, such as material, energy, gas, and emissions using standardized methods as part of a life cycle analysis. based on this, we
can get a detailed picture of a welding machine—in this case the tPS/i 320 and tPS/i 400. t his comprehensive “cradle-to-grave” approach starts with the procurement of the raw materials, includes the production of the welding machines and transport, as well as years of use in industrial shifts, including wear parts, and also examines what happens when the welding machine has reached the end of its life cycle after a long service life.
translating the c arbon Footprint to 1 Meter of Weld every component and every welding application is individual and influenced by many factors, such as the base material, the seam geometry, and the welding parameters used. t hat’s why Fronius chose a framework that allows the results to be presented clearly so they’re easy to understand. “We translate the cO2 proportion of the relevant parameters over to 1 meter of weld, because it quickly shows us where our starting point should be,” Schönmayr explains. “For the cO2 proportion in use, we’ve based our calculations on the welds of robot series production with a typical duty cycle of eight years. We did this by referring to actual customer examples, which consisted of an automotive supplier that uses the tPS 400i in its robot configuration for steel welding and a vehicle manufacturer that welds with the tPS 320i cMt.”
In the life cycle of a Fronius tPS/i welding system, only around 0.5% of the total cO2 equivalents comes down to the production, repair, and disposal of the welding machine. t he rest is split between the filler metal, the shielding gas, and the energy consumed, which highlights the importance of making efficient use of these resources in particular.
“ t he good news is that at Fronius we have already been working for many years to keep our material and energy consumption during welding as low as possible. to this end, we have built up almost 75 years of know-how and developed innovative—and sometimes groundbreaking—technologies such as the first inverter welding machines ( transarc 500), the first digitally process-controlled tPS welding systems, and the revolutionary cMt (cold Metal transfer) welding process. When it comes to efficiency, we believe that digitalization continues to present tremendous potential,” affirms Scherleitner. by using the Weldcube Premium welding data management and analysis tool, many Fronius customers have already succeeded in optimizing their production—and thanks to the high quality of the results, they are now boosting their time and material savings as well.
economic benefits = environmental benefits Fronius wants to work together with its customers to tackle areas where cO2 can be reduced. High welding quality plays a central role here to ensure the materials are used as efficiently as possible, or in other words
“The TPSi 400 that we analyzed consists of 3,433 individual parts. We started by establishing the respective carbon footprint of these parts. Sometimes we even have to immerse them in an acid bath to determine minute quantities of gold, for example,” says David Schönmayr, who oversaw the life cycle analysis together with his team.
by avoiding wasting resources with rejects or rework. reproducible, high-quality welded joints protect both the bottom line and the environment, which is why taking a holistic view of production at component level ( tcOP—total cost of production) can have a huge impact. However, Fronius also has solutions that are very easy to implement, such as the OP t/i Gas digital gas controller, which can reduce shielding gas use by an average of 40%. If there are lots of short welds, the savings potential is even higher.
“Sustainability in joining is at the top of our agenda. Our experts in research and development follow the ‘Sustainability by Design’ approach. In this way, we create environmentally inspired innovations combined with our understanding of the challenges faced by our customers. However, the best way to save material, time, and money while gradually reducing the carbon footprint is by working together. Our Lc A is only the starting point for a series of tips that we’ll be sharing with our customers,” summarizes Scherleitner.
t he experts at Fronius can provide targeted support to help customers identify carbon savings potential in production, for example by using the OP t/i Gas digital gas controller or the Weld cube Premium monitoring and analysis tool.
By Julie Gowthorpe, PhD, RSW
“Sort it out on your own,” is no longer an option for businesses when employees are in conflict. Management goals commonly include maintaining harmonious work environments that make employees happy and motivated, but how do you achieve this when people don’t get along? As teams grow and turnover happens, a variety of personalities and experiences become part of the landscape. In other words, conflict between people is inevitable. How do you, the manager, approach disputes between employees?
the answer lies in realizing how people perceive conflict with others is influenced by many factors including personality, and associatively what they have experienced throughout their lifetime. When you look at your business is there someone who struggles with others? Perhaps you’ve notice that what they expect from others is different than what they deliver? Until you think about who you are managing and then, what they have coped with throughout their lives, you will be unprepared. this is because how people interpret interactions, and conflict, depends on what they experienced in the past—before they met their coworker.
Is your business manufacturing, professional service, or retail? No industry is exempt. Jennifer managed a large coffee chain store. taught to pay attention to dynamics, she observed how employees interacted and communicated. When two employees, ted and Arlene, who often travelled to work together, became embroiled in a dispute over tips, Jennifer quickly intervened, reminding them of their friendship. Jennifer saw the ineffectiveness of this approach, noticing how ted ignored Arlene while Arlene made jokes about ted to another barista. Jennifer worried customers felt the tension. When district manager, Lee, stopped into the café for a check-in, she immediately noted the friction. Lee met the employees independently and then jointly. Jennifer watched ted and Arlene return to work, smiling and having light conversation.
What did Lee do differently than Jennifer?
5 Steps to resolve conflict between employees translates into:
1. Identify the anxiety that blocks resolution. Lee put this into action by talking with the employees about
who they are, before she waded into the issue at hand. She learned that ted had been exploited as an adolescent by people he trusted. Lee realized that relationships made ted feel vulnerable, so she reassured him that Arlene and the company cared for him and there was no intent to harm him. Lee also learned that Arlene was a single parent to two children and feared being unable to provide financially. Lee reassured Arlene that the tip situation would be resolved so she would not experience financial distress. She reaffirmed that work is a safe place.
2. think like your employee.
this effort can be proactive, so when conflict arises, you already know your employees. Ask questions like: What do weekends look like for you? Are they busy with obligations or do you get downtime? Ask these questions with curiosity, not as though you are filling out a questionnaire! this genuine interest builds trust so that when you intervene in an employee dispute, they see that you care about their overall wellbeing.
When conflict happens, effective intervention is directed by empathy. How does your employee think about things based upon what you know about them and their life? For example, Lee knew that Arlene worried about income so her intervention considered how Arlene needed to feel safe and secure that finances would not be jeopardized.
3. cool your jets before taking off into problem solving.
Let’s face it, most managers, owners and leaders find dealing with conflict between employees uncomfortable. this prompts a reactive response, whereby we want the conflict resolved, and fast! Unfortunately, this approach leaves people feeling unheard, dissatisfied and vulnerable to further conflict. Instead, slow down. When your reaction is to quell your own anxiety with a quick solution, like separating them, and solving what they are upset about rather than why it’s placing a tiny band-Aid on a gaping wound. Like Lee, take time to meet with them individually. consider whether the experience has made them feel unvalued or unsafe (physically, emotionally, or financially) and what would need to happen to lower this anxiety.
4. Keep the relational Goal Paramount.
When you are meeting individually with the employee, don’t lose sight of the goal is to heal the relationship between the employees. Unless they can work in complete silos, it is helpful to think of this relationship as a necessary elastic cord that must be flexible and intact for the relationship to work. even if you can establish distance between the two, keep in mind that unresolved conflict can ripple across teams, like smoke from forest fires. Like Lee, shift from individual meetings to sitting together. As the manager, take the lead with a calm, assertive and compassionate tone. reiterate that you understand each of their experiences and the purpose now is to find ground for resolution. Start by highlighting the positives you have heard and that you are pleased with the effort they have made to engage professionally.
5. Set a collaborative direction.
In your joint meeting, summarize what you heard from both employees and highlight the things that were the same. For example, “Jill, you mentioned that you have always worked well with Mark and Mark, you complemented Jill about her creativity. While this disagreement has been serious, let’s not minimize the many hours and interactions that have been successful.” even with resolution, reinforce the collaborative direction of the company. If Mark felt angered by having
to take calls for Jill when she took lengthy lunches, and Jill felt Mark’s tone was condescending, demonstrate your commitment to maintaining collaboration. For example, “I understand you can be great workmates. to address this problem, we have created a schedule for phone coverage that does not always rely on Mark and will be sending out a reminder to the team that lunches are within designated times.” In other words, make sure you close the loop!
Julie Gowthorpe, PhD, rSW, is a leading authority in the field of relationships. renowned for her expertise in simplifying complex concepts, she shares this through a thriving private practice and a weekly radio broadcast, Dr. Gowthorpe speaks candidly with intimate and large groups. She transforms the lives of individuals and business teams, and in her forthcoming book, I Hate People, continues her mission to foster stronger, healthier connections. Visit www.gowthorpetherapists.com for more information.
In the ever-evolving landscape of industrial automation, Siemens continues to lead the charge with innovative solutions that drive productivity, sustainability, and security. recently showcased at IMtS 2024 in chicago, Siemens introduced the latest addition to its esteemed SINUMerIK cNc family—the SINUMerIK 828D controller. tailored specifically for the compact and mid-range machine tool market, the SINUMerIK 828D promises to redefine manufacturing processes with its cutting-edge hardware and digital twin capabilities.
A Leap Forward in cNc technology the SINUMerIK 828D controller stands out with its newly designed Panel Processing Units (PPUs)—PPU271.5, PPU270.5, PPU290.5, and PPU272.5—and a revamped Machine control Panel (McP). these enhancements offer a broad spectrum of functions and options aimed at boosting the productivity, sustainability, and efficiency of manufacturing operations.
One of the standout features of the SINUMerIK 828D is the introduction of run MyVirtual Machine—a game-changer for cNc programming. Available through a software upgrade to version 5.24, this digital twin technology allows operators to create, validate, and optimize Nc programs within a virtual environment. by mirroring the real cNc machine, run MyVirtual Machine enables:
» reduced Setup time: Manufacturers can decrease setup time by up to 20%, streamlining the transition from programming to production.
» Minimized Production risks: early detection of potential collisions and errors through detailed visualization of machine operations ensures safer and more reliable manufacturing processes.
» enhanced training: New employees can train using the virtual model, reducing machine downtime and preventing damage from operational or programming mistakes.
the redesigned SINUMerIK 828D McP aligns seamlessly with the new generation of PPUs, offering an intuitive and
user-friendly interface. Key features include:
» Larger Screens: Available in 12.1-inch and 15.6-inch sizes, the new McPs provide enhanced visibility and control.
» Mechanical Keys: robust mechanical keys ensure durability and ease of use in demanding industrial environments.
» customizable Interfaces: With create MyHMI/3GL, users can tailor the interface to suit specific machine applications, further enhancing operational efficiency.
Siemens has prioritized connectivity and security in the SINUMerIK 828D, addressing the modern demands of industrial automation:
» X120 Interface: this new interface facilitates seamless connections to external devices such as the SINUMerIK Ht (Handheld terminal) 10 and edge devices, broadening the scope of machining applications and boosting overall productivity.
» energy efficiency Analysis: the ctrl-e key combination offers comprehensive analysis functions, making energy consumption transparent and promoting
sustainable manufacturing practices.
» cybersecurity Features: enhanced security functions, including security archives, user management, and certificate storage, protect against manipulation and product piracy, ensuring the integrity and reliability of manufacturing operations.
the SINUMerIK 828D's versatile capabilities extend its applicability beyond traditional manufacturing sectors. With enhanced PLc integration, Siemens has expanded its reach into industries such as power and energy, electronics and 5G, and automotive manufacturing. this expansion underscores Siemens' commitment to providing flexible and scalable solutions that meet the diverse needs of modern industries.
Siemens continues to champion the digital transformation of manufacturing through its Digital enterprise portfolio. b y integrating real and digital worlds, Siemens empowers businesses to optimize their entire value chain, from design and production to maintenance and beyond. t he SINUM er IK 828D is a testament to this vision, offering manufacturers the tools they need to achieve greater flexibility, productivity, and sustainability in their operations.
the unveiling of the SINUMerIK 828D cNc controller marks a significant milestone in Siemens' ongoing mission to revolutionize industrial automation. by combining advanced hardware, digital twin technology, and robust security features, the SINUMerIK 828D equips manufacturers with the tools necessary to navigate the complexities of modern production environments. As industries continue to embrace digitalization, Siemens remains at the forefront, delivering solutions that drive efficiency, sustainability, and innovation.
For more information on the SINUMerIK 828D and other Siemens Digital Industries offerings, visit Siemens Digital Industries.
Siemens Digital Industries (DI) is a global leader in automation and digitalization, dedicated to driving the digital transformation across process and discrete industries. With a comprehensive portfolio tailored to the specific needs of each sector, Siemens DI supports businesses of all sizes in integrating and digitalizing their operations to enhance productivity and flexibility. Headquartered in Nuremberg, Germany, Siemens DI employs around 75,000 professionals worldwide, continuously innovating to incorporate futureready technologies into its offerings.
The model making and mold construction company Erglis counts on a compact and scaled-down version of the FZU22 by F. Zimmermann. The 5-axis-portal milling machine efficiently processes a multitude of plastic components.
being able to accept orders quickly while remaining flexible is a crucial factor in making the A. erglis GmbH competitive. to achieve this, the model making and mold construction company relies on Zimmermann portal milling machines for more than 28 years. the machine fleet continues to grow with the capacities of orders and was recently complemented by a compact and dynamic FZU22. A. erglis is using this system, which is reduced to its essentials, exclusively for processing composites and plastic parts.
“What makes us so competitive?” – rainer eckelt does not have to think long. “We are able to react very swiftly when it comes to client orders and are thus able to deliver quickly.” A crucial factor that is extremely important for his clients, but especially to those in the motorsports sector. Mr. eckelt is an executive manager of the A. erglis GmbH in Heilbronn, Germany . the company, specializing in model making and mold construction, was founded in 1965 by Arnold erglis. It was taken over by Josef eckelt in 1979, who then passed on the company to his son reiner in 2003. the team, consisting of over 30 employees, is constructing molds, models and prototypes according to client’s specifications and requirements. Following this process, specialists are programming the data for the Nc-milling machines. “because we are offering construction as well as manufacturing from one single provider, we guarantee flawless compatibility”, assures eckelt. the materials used are epoxy resin, ureol, various plastics, aluminum and steel, amongst others.
“Oftentimes we receive an order on Monday, asking for delivery on Friday”, explains eckert. “ this can be positive molds, but also direct machining tools for the sidepods or the front spoiler of a car.” the executive manager usually declares these especially urgent projects a top priority for himself. “If I open an e-mail in the evening then it is almost always difficult to catch any sleep at night. After all, the end client does not want to fall behind on race day.” Seriously? At least to some extent. “Not a lot of suppliers offer such service”, says the executive manager. to ensure this kind of speed, the model making and mold construction company also relies on its excellent network which is able to quickly supply the needed materials in the necessary quantity.
currently, the order books for the upcoming months are well-filled. besides motorsports, other clients are primarily operating in the automotive, as well as the aerospace sector. but especially in the Formula 1 racing series, speed is not only crucial on the racetrack.
It’s
every order is different, there can be parts with complex shapes, but also simple parts, unique parts or parts demanded at large quantity – the size also varies significantly. “We are, for example, able to manufacture
small components economically by using large machines with interchangeable plates, whereas we would not be able to manufacture large components on small machines.”, says eckelt. Due to this, the machine fleet has adapted to the order situation in recent years. the major share of systems is produced by Zimmermann. “We already knew about the Swabian company from model construction. In 1997 we got the first portal milling machine – a FZ30”, Mr. eckelt remembers. back then he was already working in the family business, while his father was still leading the company. “We liked the regional proximity, because fast service is a very important factor”, he says. In addition, we quickly established a relationship of mutual trust with rudolf Gänzle, the director and executive manager at F. Zimmermann GmbH in Germany at the time. “ the contract was not signed, but sealed by a handshake as usual in this time”, says Mr. eckelt with a smile.
For the first portal system the company built a new hall, which continued to fill up. Since the FZ30 was not designed for aluminum, but for plastics, a FZ37 was added in 2002 and another one of the same model four years later. Afterward, Zimmerman exchanged the first FZ30 with a new one, providing larger workspaces. A FZ33 compact followed, allowing quick and complete processing of aluminum and composite parts from all five sides – furthermore it enables the company to finish steel and cast components with high dynamics and in simultaneous operation. two machines from a market competitor are also running during the two-shift operation of the company. “We always selected the systems by the size of their workspaces and the technologies, which are continuously developed further by Zimmermann”, eckelt explains. Of importance are short processing times and high precision, to avoid reworking the components, as well as a very high availability of the systems.
efficiently plastic milling
At the beginning of March, rainer eckelt expanded the machine fleet again. “We spent one or two years searching for an economical portal system, which we can exclusively use for composites and plastics, while not having to invest
• Machines can be mounted in any orientation
• The sealed ink system allows discontinuous operations with immediate start-up of comparable previous impressions
• Machines can be modified or made to order for your particular marking application
more than a million.” the FZ30 with interchangeable plate system had become too slow for him in the meantime, due to its setup times paired with the multitude of components. Alongside factors like reliability and efficiency, the price played a particularly important role. He looked at different machines, also from competitors. Of course, there had been discussions with Zimmermann and with rudolf Gänzle, who is still closely connected to the A. erglis GmbH.
the initial plan included a FZU32. the compact five-axis-portal milling machine specifically processes aluminum, but also fiber-reinforced composites, plastics and ureol. the centrally guided portal is rigid and less vulnerable in adverse environmental conditions due to the thermo-symmetrical design. “We liked the machine, but it was too much for our limited demands, also regarding the price”, explains eckelt. but Gänzle did not give up. the executive manager of erglis was then able to take a look at a FZU22 at another model making and mold construction company – “it is basically a base, or economy version of its bigger sister machine”, describes Sandra bayer teixeira, marketing manager at Zimmermann Germany. eckelt: “We were also able to talk to the operator and even mill a test part.” the result was compelling due to its high precision and the quality of its surface finish.
When the other company decided to purchase another FZU22, it became clear to eckelt that he would make the right decision when buying this product family. the
construction space measures 1,800 x 3,000 x 1,250 millimeters. the standard equipment includes, amongst other things, a 12- or 24-position tool changer. the specifically developed, dynamic 5-axis-milling head c2 with fork head and the 15kW spindle is well suited, even for hard-to-reach areas,
due to its geometry. It is equipped with a two-sided bearing pivot axis, which is made of cast.
Adapted to specific requirements
rainer eckert continued to construct his very own design for the machine. this way the FZU22 was equipped, for example, with a double-acting zero-point clamping system, to be able have two interchangeable plates installed at the same time. the dust extraction was manufactured independently, while the air-conditioned hall is sufficient for cooling.
“We refrained from using anything we do not need, which makes the machine even more efficient”, says the executive manager. Sandra bayer teixeira compares this to a car: “If I do not add seat heating or a rain sensor as equipment components, the price becomes more attractive and the chance that such a sensor will cause problems in the vehicle diminishes. I will reliably get from A to b.”
easy transport, easy installation
“ t he nice part about such a compact system: transportation is quite uncomplicated”, says the marketing manager from Zimmermann. It took only a few months for the machine to be built and delivered. Sandra bayer teixeira:” We did not have to disassemble our lightweight machine when loading it on a truck and a crane was able to lift it into the hall.”
the tools for the FZU recently arrived from Heilbronn. the machine is not working at full capacity yet, but this will change in the upcoming weeks. It has already shown what it can do. reiner eckelt is presenting a small, complex model of a racecar, which has been shaped from the full: the milling of undercuts and of the small edges is actually quite challenging. the compact FZU22 mastered this without problems. rainer eckelt is satisfied and also positively surprised, by just how fast the minimally equipped machine was able to complete the first orders – many small parts made of plastic – within one clamping process.
Enhance the Safety, Storage & Efficiency of your logistics with Combilift
Combilift’s range of multidirectional forklifts, pedestrian reach trucks, straddle carriers and container loaders will allow you to maximize the capacity, improve efficiency and enhance the safety of your facility. Contact Us Today
To find out how Combilift can help you unlock every inch of your storage space.
Source: Pressmaster/MotionArray
By Scott Ryan
In any manufacturing environment, the bill of materials (bOM) generated by engineering lays the foundation for the processes for the rest of the company. the bOM has a direct impact on quoting, purchasing and material planning, scheduling, production management and tracking, and so on.
Particularly for engineering-heavy industrial equipment environments, these bOMs often have a very complex structure with multiple levels or layers of subassemblies. While the drawings in a cAD or design program handle this easily and natively, the way the full bOM for a top level, finished product is structured in an erP/MrP system has significant impact on the production of the actual product. Production managers and shop floor workers have to navigate the complexities of a multi-level bOM in real-time as they keep to a production schedule and can get frustrated or overwhelmed dealing with an extraneous amount of paperwork or unnecessary data.
building a bridge between engineering and production is crucial to maximizing quality without sacrificing efficiency.
the first decision is how to structure the bill of materials within the business system used to run operations, typically an enterprise resource planning (erP) system, and then determine whether to stick to the complex, hierarchical, sub-bOM (or subassembly) structure or to ‘flatten’ the bOM into a single-layered product.
take the process of building a custom conveyor system as an example. You could either:
» create a single bOM that includes the entire system, such as the frame, motor, and belts.
» Or divide it into subassemblies for the frame, motor, and belts, each of which is managed and produced separately before integrating during final assembly.
A flexible, manufacturing-focused er P will allow for either approach and should provide options for simplifying production even with the complex, multilevel structure.
either approach results in a functional product that effectively drives inventory, captures cost, and meets specifications. but, often a multi-level bOMs requires the ability to manage suborders and planning for each of the subassemblies, and your production plan and goals must be considered.
If a subassembly must be built discreetly (for traceability purposes), is overbuilt or purchased from a subcontract manufacturer, then the best practice is to maintain the subassembly breakout in a hierarchical bOM. If a subassembly is shared amongst other products in your mix, it is often more efficient to ‘overbuild’ or ‘batch’ build these subassemblies separately, maintaining some kind of safety stock, or building to a consolidated demand through material requirements planning (MrP).
If you are responsible for all production, and these subassemblies are unique to the top level, you will need to consider the implications of the complexity in production. Your production process may be most efficient by processing a flat bOM on a single work order that captures all raw material/component demand and labor for the entire product.
Once the bill of materials is structured within your erP system, the process of initiating production begins when a work order is issued. A manufacturing erP system will be capable of recognizing the relationships between subassemblies and the top-level bOM and should provide practical tools to streamline production workflows based on these connections.
A robust erP, such as cetec erP, also offers manufacturers several options for handling subassemblies, ensuring that production planning aligns with operational efficiency and material availability. typically, manufacturers can choose from the following options when managing sub-bOMs:
1. create Suborders - discrete suborders under the parent order
this option triggers a work order for each subassembly, linking it to the parent work order. this would typically include tools for maintaining full oversight of the production stages for the entire project, allowing for real-time visibility and adjustments to the schedule and production status. this is particularly beneficial when all manufacturing is in-house and subject to complex, dynamic scheduling needs or traceability requirements.
2. Do Not create Suborder - defers material planning downstream to an MrP
In cases where subassemblies are outsourced or frequently used across different products, this option allows manufacturers to bypass the creation of additional work orders. the subassembly is treated as a purchased component, simplifying the overall work order structure and allowing production planners to handle demand through MrP processes to consolidate demand for the subassembly and create a work order (or purchase order) only if necessary. this option minimizes disruptions by ensuring that purchased parts are available when needed without triggering unnecessary internal builds.
3. Phantom bOMs - flattens the bOM structure into a single work order Phantom bOMs (or phantom assemblies) serve as a valuable solution when subassemblies are logically
Figure 2: Example of a "Related Orders" screen within Cetec ERP with added notes, showing all suborders for the subassemblies of a parent or top level BOM. This shows the status for each level along with the ability to dynamically reschedule any or all portions of the project. (Source: Cetec ERP)
required by engineering for labor and/or materials but present unnecessary complexity during production. t his option effectively combines the components, labor, and documents of a subassembly directly into the top-level bOM, treating the subassembly as part of the main product without generating separate work orders. by using phantom bOMs, manufacturers can maintain structured product hierarchies while simplifying the production flow.
to further optimize your production, your erP system should be able to automate these decisions regarding subassembly builds based on real-time inventory levels. If sufficient stock is available for a particular subassembly, the system can automatically opt to not build, preventing unnecessary production orders. conversely, when stock is low or unavailable, the system should be configurable to allow the switch to create suborders based on the determined shortage for the top-level by calculating the required quantities for production. this level of automation reduces manual intervention, ensuring that production schedules are not derailed by stock shortages or excess. this approach also guarantees that subassemblies are created or bypassed based on material availability, which not only streamlines production but also optimizes resource allocation, minimizing production delays and material waste.
Phantom bOMs offer a powerful alternative when standard subassembly structures create bottlenecks in production. by integrating subassemblies directly into the top-level bOM without generating separate work orders,
manufacturers can simplify workflows without sacrificing structure or traceability.
consider a scenario where a manufacturer is building an industrial HVAc system that includes several subassemblies such as the compressor, evaporator coil, and blower assembly. Instead of creating separate work orders for each of these components, a phantom bOM allows the manufacturer to group them into the main system’s bOM. the production team can then issue a single work order for the entire HVAc system, which includes all necessary materials for these subassemblies. this approach saves time, minimizes administrative overhead, streamlines the workflow, and ensures that production continues without unnecessary delays or interruptions.
Phantom bOMs preserve the logical relationships defined by engineers while providing the production team with a more straightforward, efficient method for assembling complex products. this flexibility is especially
valuable in industries with high complexity, such as aerospace, medical devices, and automotive manufacturing, where product variations and customizations are frequent.
Phantom bOMs offer several practical benefits that can significantly transform production efficiency:
» reducing Administrative Load: by consolidating work orders, production workers are no longer overwhelmed by an excessive amount of paperwork related to multiple subassemblies. this streamlining allows teams to focus on actual assembly rather than administrative tasks.
» Improving Material and Workflow coordination: Phantom bOMs eliminate the need for sequential builds, enabling the assembly team to work on subassemblies as part of the main build process. this eliminates unnecessary stops in the workflow, keeping production moving at a faster, more efficient pace.
» enhancing Flexibility in the Production Line: by allowing subassemblies to be built along with the top-level assembly, phantom bOMs provide production teams with greater flexibility in scheduling and task prioritization. this adaptability is particularly important in environments where lead times are tight, or product variations are frequent.
Manufacturing companies often find themselves trying to reconcile the detailed, structured approach required by engineering with the need for speed and efficiency on the production floor. Multi-level bOMs are essential for maintaining the integrity of complex product designs, but
if not carefully managed, they can lead to slowdowns and inefficiencies in production.
by embracing best practices in bOM structuring, such as automating build decisions and utilizing phantom bOMs, manufacturers can keep both engineering and production teams aligned. A modern erP system that supports these strategies will enable businesses to maintain detailed product structures while keeping production streamlined and flexible.
With the right tools and strategies, it's possible to retain engineering precision without bogging down production with unnecessary work orders and administrative tasks. Ultimately, the goal is to ensure that complex products are built with the highest quality while keeping production lean and efficient.
An integrated erP system is essential for bridging the gap between engineering and production, providing the structure and control needed for complex builds while simplifying workflows for production teams.
In the end, it's about creating a manufacturing environment where both engineering and production can thrive, working in harmony to deliver profitable products that meet both quality standards and market demand.
For More Information:
Scott Ryan, Sr. Consultant Cetec ERP, LLC
Ph. 512-299-9170 ext. 116
E-mail: scott@cetecerp.com
Website: www.cetecerp.com
LinkedIn: https://www.linkedin.com/company/cetec-erp-llc/
AtI Industrial Automation Introduces a High-Speed ethernet Module to enhance robotic tool changer Performance
AtI Industrial Automation (AtI) has unveiled the G bX 10 Gigabit tool changer ethernet Module, designed to optimize robotic tool changer performance in smart manufacturing environments. t his advanced module facilitates high-speed, safe, and reliable data transmission, enhancing communication between vision systems, inspection tools, metrology devices, motion control, and fieldbus systems. Key features include plug-and-play M12 8-pin X-code connectors that eliminate the need for stripping, crimping, or soldering, thereby saving integration time. t he module also offers configurable cable exit options at -90°, 0°, and +90° radial positions, allowing users to optimize cable routing and reduce strain. engineered for longevity, the G bX module can handle up to one million mating cycles, making it ideal for demanding industries such as automotive, aerospace, and testing. Additionally, it boasts broad compatibility with AtI’s Standard and Heavy Duty tool changers, as well as Utility couplers, promoting module standardization across various applications. AtI’s latest innovation underscores their
commitment to enhancing automation efficiency and reliability in advanced manufacturing settings.
For More Information: www.ati-ia.com
Available Now: AZcO’s SUr SIZetM Sheeter FGW 1650 For Unwinding, Slitting and cutting AZcO corp announces the availability of the SUr SIZetM Sheeter FGW 1650, a versatile and customizable cutting assembly designed for precise unwinding, slitting, and cutting of various flexible materials including films, foils, nonwovens, and paper. t his heavy-duty sheeter features a rugged anodized frame with stainless steel covers and an air shaft supported by safety chucks for quick roll changes, ensuring continuous operation and minimal downtime. Key components include rotary shear blades for clean cuts, ground urethane rollers for efficient material handling, and a hardened steel blade for consistent performance. t he FGW 1650 boasts a modular “building block” design, allowing seamless integration of additional features such as rewinds, sensors, light towers, and web-guiding systems to meet specific operational needs. technical specifications highlight a maximum cut width of 1,650 mm, servo motor drive system, and a color touchscreen for easy setup and monitoring. AZcO’s SUr SIZetM Sheeter FGW 1650 is ideal for industries requiring high precision and reliability in their cutting processes, enhancing overall productivity and operational efficiency.
For More Information: www.azcocorp.com
coxreels Offers New Options for the challenger Series reels coxreels® is excited to introduce new roller bracket assemblies for its challenger Series reels, enhancing hose guidance during extension and retraction. Specifically designed for the compact challenger platform, these roller brackets are available in a 4-way upper roller format and accommodate various drum sizes: 8” and 12.5” wide drums for 12” disk models, and 8”, 12.5”, and 18” wide drums for 17” disk models. t hese assemblies improve hose management, ensuring smooth operation and reducing wear and tear on the hoses. coxreels®, established in 1923, continues to uphold its reputation for manufacturing high-quality, professional-grade hose, cord, and cable reels in the USA. t he new roller bracket assemblies are compatible with other models like the 1125-Series and 1175-Series, promoting standardization and ease of integration across different reel types. Manufacturers can enhance their material handling efficiency with these robust, reliable solutions designed to meet diverse industrial needs. For
more details or to request a brochure, contact coxreels® customer Service or visit their website.
For More Information: www.coxreels.com
Dillon Manufacturing introduces its new extra-long hard jaws, designed to extend the reach of big bore chucks and facilitate the machining of smaller diameter materials with enhanced precision. crafted from durable 8620 steel, these hard jaws are compatible with 8” to 15” power chucks and offer multiple length options to cater to specific machining requirements. t he extra-long design enables faster setups and reduces downtime, significantly improving shop efficiency and productivity.
Ideal for handling challenging smalldiameter part machining, Dillon’s hard jaws provide exceptional center reach and versatility, making them a
valuable addition to any machining operation. In addition to hard jaws, Dillon Manufacturing offers a comprehensive range of workholding solutions, including chuck jaws, vises, soft jaws, collet pad systems, and more, all available through their nationwide network of industrial distributors. Application engineers are available to assist customers in selecting the best products to meet their specific needs, ensuring optimal performance and reliability in various industrial applications.
For More Information: www.dillonmfg.com
e XAIr’s New Mobile App enhances User experience
e XAIr has launched its latest Ar Mobile App, available on both Apple and Google Play Stores, to provide an interactive and enhanced user experience for customers. t he e XAIr Ar (Augmented reality) Mobile App allows users to browse and place 3D models of e XAIr products directly into their work environments, ensuring a perfect fit for their specific applications. t his innovative tool expedites the solution-finding process by enabling users to select product sizes, performance requirements, and visualize them in real-time before making a purchase. Additionally, the app includes a library of conversion calculators, assisting users with on-the-go problemsolving and computations. t he Ar Mobile App reflects
e XAIr ’s commitment to offering advanced tools that add significant value to customers, helping them select the right Intelligent compressed Air ® products to improve their processes. Alongside the app, e XAIr com provides a comprehensive Knowledge base with resources such as product videos, performance data, c AD files, installation guides, air savings calculators, case studies, and an extensive application database with over a thousand solutions.
For More Information: www.exair.co
Fixtureworks Introduces New Heavy-Duty retractable ball-Lock Fasteners
Fixtureworks expands its One-touch Fastener lineup with the introduction of heavy-duty retractable ball-lock fasteners, delivering high clamping forces up to 450 lb (2000N) and holding forces up to 1120 lb (5000N). t hese new fasteners are engineered for quick-change applications requiring frequent fixture insertion and removal, providing positive locking without tools. t he retractable pin feature allows the fastener to slide off the base safely, making them ideal for slide and door applications. t hese fasteners are compatible with the Q c W e S receptacle and are available in stainless steel, ensuring durability and reliability. In addition to the new heavy-duty Q c W e SA fasteners, Fixtureworks offers a wide range of retractable clamping solutions, including the Q ct H-series with cam-locking systems. t hese fasteners replace traditional nut-and-bolt assemblies, enabling operators to lock and unlock plates, panels, covers, and machine components effortlessly.
Fixtureworks’ comprehensive product line also includes various workholding supports, pneumatic clamps, and fixturing accessories, all designed to enhance efficiency and precision in industrial applications.
For More Information: www.fixtureworks.com
GF Machining Solutions introduces the MILL P 800 U S, a full 5-axis milling machine designed for scalability and seamless automation integration to meet growing production demands. t he MILL P 800 U S features a compact design with a reduced footprint, making it ideal for flexible manufacturing environments. A key innovation is the relocation of the electrical cabinet to the left side of the machine, allowing robots to load workpieces directly from the rear, eliminating the need for a pallet changer and reducing cell footprint. t his design enhances operator ergonomics and safety by freeing up the machine’s front area for easier access. t he machine is built with a twin-ballscrew drive and twin-linear
scale gantry system, ensuring synchronized movements and reducing wear, thereby increasing longevity and precision. t he Steptec spindle offers a maximum speed of 20,000 rpm and a torque rating of 120Nm, suitable for a wide range of applications. Additional features include the Operator Support System (OSS), Machine Spindle Protection (MSP), Automatic Machine c alibration (AM c), and the econoWatt energy-saving function. t hese enhancements ensure high performance, reliability, and energy efficiency, positioning the MILL P 800 U S as a versatile solution for both roughing and finishing operations in advanced manufacturing settings.
For More Information: www.gfms.com
HeMcO introduces the Digital Airflow Monitor, a cutting-edge device designed to continuously monitor the face velocity airflow of fume hoods, ensuring workplace
safety and compliance. Featuring a clear digital display, the monitor shows airflow velocity in meters per second (m/sec) or feet per minute (FPM) and includes an audible alarm that alerts users to unsafe conditions. t he device offers push-button calibration for easy setup and maintenance, and it comes equipped with three programmable input/output relays for customizable integration with existing safety and automation systems. Available for both factory and field installation, the Digital Airflow Monitor provides a reliable solution for industries requiring precise airflow management, such as laboratories and manufacturing facilities. Its robust design ensures durability and consistent performance, making it an essential tool for maintaining optimal safety standards in environments where airflow control is critical.
For More Information: www.hemcocorp.com
KUKA introduces the KMP 600P compact Mobile Platform, a versatile autonomous mobile robot (AMr) designed specifically for confined production environments. As part of KUKA's high-performance P-series, the KMP 600P offers a payload capacity of up to 600 kilograms, making it suitable for various industries aiming to enhance production and intralogistics efficiency. t his compact platform utilizes differential drive technology, enabling it to move forward, backward, turn on the spot, and navigate tight curves with precision—ideal for spaces with limited maneuverability. t he KMP 600P is VDA 5050-compatible, facilitating seamless integration into diverse fleet management systems, and features inductive charging
for continuous 24/7 operation, thereby extending battery life. certified with international ce and UL standards, the platform ensures maximum safety and easy maintenance. Its modular design allows for quick component replacements, minimizing downtime. Additionally, the user-friendly KUKA.AMr Fleet software enables effortless commissioning and rapid workflow optimization without requiring programming expertise. Julian Stockschlaeder, Head of AMr business Development at KUKA, emphasizes that the KMP 600P expands KUKA’s AMr portfolio, supporting their growth as a leader in the AMr market.
For More Information: www.kuka.com
ModuleWorks is set to release its GPU-accelerated simulation feature, enhancing material removal simulations by leveraging the high processing speed of workstation GPUs. expected to be available for testing with the ModuleWorks 2024.12 software release, this new feature dramatically increases simulation speed, achieving up to ten times faster performance compared to traditional cPU-based methods. As machining processes become more complex, requiring precise and accurate simulations, ModuleWorks addresses the common compromise between speed and quality. by utilizing GPU architecture,
QUALITY FEATURES… Sheffer cylinders are designed not only for exceptional performance, but for fast and easy installation and parts replacement to minimize downtime. STUDDED ROD ENDS: Sheffer’s design virtually eliminates breakage by outing stress away from a common weak point. SEPARATE ROD BEARING: On most Sheffer cylinders, the hydrodynamic “flooded bearing” greatly reduces wear and extends part life. SLIPPER PISTON SEAL AND BEARING: Standard on all hydraulic cylinders. Teflon surfaces provide excellent lubrication, reduce heat and friction. FOUR FULL WRENCH FLATS: Designed to avoid damage to the rod surface during installation or replacement. CHAMFERED TUBE ENDS: When replacing seals, the chamfer compresses the seal into the piston, minimizes seal damage.
HYDRAULIC CYLINDERS… The Hydraulic line consists of three series. The MH and HH models feature interchangeable dimensions with ANSI, NFPA, and JIC. MH: Medium-Duty, Bores to 8’’, 800 to 2,000 PSI, 20 standard mountings. HH: Heavy-Duty, Bores to 24’’, 3,000 working PSI, 22 standard mountings. UH: Ultra High Pressure, Bores to 14’’, 5,000 PSI, 8 standard mountings.
PNEUMATIC CYLINDERS… The Pneumatic line consists of four series. The MA and A models feature interchangeable dimensions with ANSI, NFPA, and JIC. MA: Medium-Duty, Bores to 8’’, 200 PSI, 14 standard mountings. A: Heavy-Duty, Bores to 14’’, 250 PSI, 20 standard mountings. AA: Light-Duty Aluminum, Bores to 2.5’’, 200 PSI, universal mount, kits available. C20: Cast Iron, Bores to 10’’, 200 PSI, 5 standard mountings.
the accelerated simulation can handle large-scale scenarios with over a million toolpath points, providing detailed and high-fidelity simulations without sacrificing speed. this integration allows cAM systems to adopt GPU-accelerated simulations seamlessly, maintaining the comprehensive feature set of ModuleWorks’ cutting simulation products while significantly boosting productivity. Additionally, the GPU-accelerated simulation supports efficient process planning, optimization, and verification, enabling engineers to iterate and refine machining operations rapidly. Dr.-Ing. Sven Odendahl, Principal Product Manager at ModuleWorks, emphasized that this advancement allows users to maintain high-quality standards while meeting tight deadlines. the GPU-accelerated simulation represents a significant leap in simulation technology, empowering manufacturers to enhance their operational efficiency and precision.
For More Information: www.moduleworks.com
For emergency Stop Norstat introduces the SAFeLINe SL4, a robust stainless steel rope pull switch designed to provide constant emergency
stop access in industrial settings where physical guarding is impractical. constructed from 316 stainless steel, the SAFeLINe SL4 is highly durable and resistant to corrosion, making it ideal for harsh environments and applications with strict hygiene requirements. this versatile grabwire system enhances safety and operational efficiency by allowing emergency stops to be initiated from any point along a rope that can span up to 75 meters. the system features simple tension monitoring through built-in indicators and an intuitive reset mechanism, minimizing downtime after an emergency stop. Additionally, the SAFeLINe SL4 includes a mushroom head e-Stop button and offers four sets of contacts (2Nc/2NO or 3Nc/1NO), ensuring comprehensive emergency stop capabilities. With a protection rating of IP69K and operating temperatures ranging from -25°c to +80°c, the SAFeLINe SL4 meets stringent safety standards and adapts to various industrial applications. by reducing the need for multiple emergency stop switches, this innovative solution streamlines safety protocols and enhances workplace safety, making it an essential addition to any facility requiring reliable emergency stop access without the constraints of physical guarding.
For More Information: www.norstat.com
betenbender Manufacturing, Inc — www.betenbender.com
bUrr KING — www.burrking.com
www.clamprite.com
combilift, USA — www.combilift.com
cosen Saws, USA — www.cosensaws.com
cOXreeLS — www.cOXreeLS.com
Experience the most comprehensive showcase of sheet metal manufacturing processes under one roof at FABTECH 2024, North America’s preeminent event for metal forming, fabricating, welding, and finishing. Discover innovation, find inspiration, and make connections that will impact your career or business.
THE LEADER IN INNOVATIVE SURFACE FINISHING SOLUTIONS
+ Durable, American Made air tools are ideal for rapid material removal, deburring, finishing and polishing.
+ Straight-Line, Right Angle and 7° Offset models offered in front and rear exhaust configurations.
+ Tools available in horsepowers ranging from 0.3 hp to 3 hp, with speeds from 3,200 RPM to 100,000 RPM.