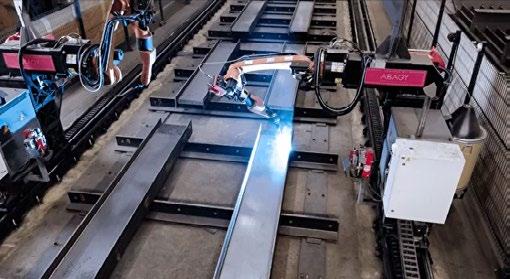
10 minute read
InDuSTry nEWS
industrial Machinery Digest's industry news features the latest news and press releases from some of the industry's top companies.
WANT TO BE FEATURED? Send your press releases to editorial@indmacdig.com
Will welding robots replace welders? Results of polls and experiments.
robotic company aBaGy and the welder community Weld.Com, which unites thousands of welders in the uS, conducted a joint experiment. as a result, one of the welders was able to operate a robot without special training on the same day. austin Hargett (aka Dr. Weldz), a welder with 14 years of experience and one of the members of Weld.com, tested the aBaGy solution for robot control. He defined welding parameters and put the robot to work without any special knowledge in robotics.
“Welding machines are changing. Technology is changing. My job is a constant evolution. as a welder, I believe that I need to learn something new every day. and I agree with aBaGy that robots can be a new effective tool for welders. I’m really impressed with how simple and easy it was to get the robot up and running.”, – austin Hargett said. also, a poll was conducted among the welding community. Out of 1500 voters, 43% think robots present a great opportunity for better efficiency.
Dmitry Golitsyn, co-founder and CTO at aBaGy, explains: “Every single day we hear from manufacturers that they can’t find people. according to american Welding Society research, more than 40% of welders are over 45 years old. To address this welder shortage, we can help people who are already in the industry become more productive with new technology”.
Kate Degai, CMO at aBaGy, said: “There’s a prevailing preconception that robots will replace people. This is exactly what hinders the development of robotics. It is impossible to install robots if there are no people inside the factory who are ready to work with them and feel that this helps them to increase their own efficiency. Therefore, we are open to a dialogue with the welding community”.
Seven Schools Awarded Welding Workforce Grants to Enhance Their Welding Education Programs
The aWS Foundation is dedicated to increasing the welding workforce by providing grant funding to secondary, post-secondary and welder training facilities that seek to enhance and improve their welding education programs. Grant funding of up to $25,000 per location is awarded for facilities to make improvements, invest in capital items such as welding or metalworking equipment, or purchase/upgrade computers or computer-based training systems.
The following seven schools were recently awarded the Welding Workforce Grant: » Bend Senior High School — Bend, Or » Bridgerland Technical College — Logan, uT » Colonial Career and Technology
Center—new Oxford, Pa

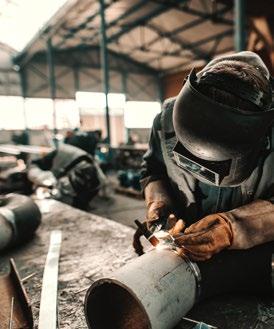
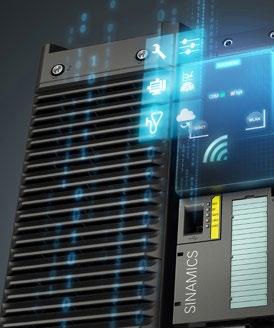
IndustrialMachineryDigest.com October 2021 IndustrialMachineryDigest.com March 2019
IMPACTING
the DROP ZONE
Wildeck Provides Increased Safety for Moving Palletized Loads
IndustrialMachineryDigest.com June 2021
GETTING BACK TO WORK!!
» Front range Community College—Fort Collins, CO » Lynnes Welding Training—ramsey, Mn » reIgnite Hope—Gardena, Ca » Wallace Community College—Dothan, aL
“as the need for skilled welders continues to increase, helping educational facilities such as these seven locations is more important than ever,” said Monica Pfarr, Executive Director of the aWS Foundation. “We are pleased to support the expansion of their welding programs, their commitment to the welding industry and their dedication to cultivating the next generation of welding technicians and professionals.”
Welding is among the most crucial and essential skilled trades that impact everyday life, yet the number of skilled welding technicians and professionals continues to decrease. The american Welding Society through the aWS Foundation supports programs to ensure the growth and development of the welding industry through research and educational opportunities. In 2022, the aWS Foundation awarded more than $2.5 million in grants and scholarships to support welding education.
For more information, visit aws.org/foundation.
Wesley Maine Joins Beckhoff USA as Business Development Leader
Maine will create strategic business opportunities in the Great Lakes region, drawing on three decades of industry experience
Beckhoff automation recently added Wesley Maine to its rapidly growing team as Business Development Leader in the Great Lakes region. Maine brings deep experience in application engineering, sales and management roles across the automation industry. In this role, he will develop new sales opportunities with current customers and prospects throughout Ohio, Michigan, Indiana and Kentucky to further accelerate Beckhoff market share growth. Based out of the company’s Cincinnati-area office, he reports to Don Shanklin, regional Director – Sales and Process.
“Wes has everything you look for in a business development professional. He is an exciting addition, and we are thrilled to have him on the Beckhoff uSa team,” Shanklin said. “Wes is in a great position to leverage his deep experience in sales process, team selling and new customer development – along with enthusiasm for our market-leading automation technologies – to help us drive growth in the Great Lakes region and across the company.”
Maine spent the first 10 years of his career in manufacturing and engineering roles at Mitsubishi Electric automotive and aTS automation, Inc. He then worked as a regional sales manager for B&r Industrial automation for seven years and a sales engineer at Motor Systems, Inc. for four years. after that, Maine joined Mitsubishi Electric automation for 12 years, most recently serving as regional Sales Manager.
“as a market-leading, family-run, global business that actively encourages employees to help shape its future, I am thrilled to join Beckhoff,” Maine said. “My 10 years of manufacturing experience and 20 years as a sales engineer provide a solid foundation for me to spearhead new technical sales activities at Beckhoff. My primary goal is to help customers think differently about automation so they can lead in their respective industries.”
Maine earned a Bachelor of Science in electrical engineering from the university of Dayton.
BWP, LiCAP, and Siemens Establish Strategic Partnership for Mass Production of Dry Electrode Manufacturing Equipment
Strategic partnership will drive cost-effective and sustainable dry electrode manufacturing towards mass production by 2023.
BW Papersystems (BWP), a division of Barry-Wehmiller, is a capital equipment manufacturer for multiple industries; and is experienced in the successful merging of technologies to develop new solutions that create value for their customers. LiCaP Technologies, Inc. (LiCaP) is a developer of cost-effective and sustainable dry electrode manufacturing solutions for lithium-ion battery and solidstate battery technologies. Siemens is a global innovator focusing on digitalization, electrification and automation for the process and manufacturing industries. Today the companies are proud to announce that they have entered a strategic partnership to manufacture and commercialize innovative dry electrode manufacturing systems for the battery cell industry.
BW Papersystems has a people-centric focus in a way that pursues business growth and creates value. BW Papersystems, LiCaP and Siemens are all companies with technology – that together – fills a product line gap, diversifies the industry, and enhances a new market. rising demand for batteries comes with a huge jump in demand for battery cell manufacturing equipment. Today most incumbent battery cell manufacturing suppliers are based in asia, already operating at more than 95 percent capacity. Moreover, they may prioritize orders from established customers (mostly leading incumbent cell manufacturers) over those from new market entrants from Europe and the united States. as a result, north american and European battery cell manufacturing companies and EV OEMs are likely to face a bottleneck in equipment supply that will place their planned start of production at risk.
The strategic partnership between BW Papersystems, LiCaP and Siemens will make the north american and European Gigafactories more competitive through industrialization of LiCaP’s cost-effective and sustainable activated Dry Electrode™ technology. as a crucial manufacturing partner, Siemens will be integral in scaling production for both companies.
“For LiCaP, it was important that BW Papersystems and Siemens, as our manufacturing partners, already
have the expertise and know-how in areas that are critical to successful commercialization of our activated Dry Electrode™ technology. This is why we partnered up with them and have no doubt they can build manufacturing equipment for our electrode manufacturing process at much greater speed compared to any other company,” says Martin Zea, VP of Operations at LiCaP.
For more information, visit bwpapersystems.com.
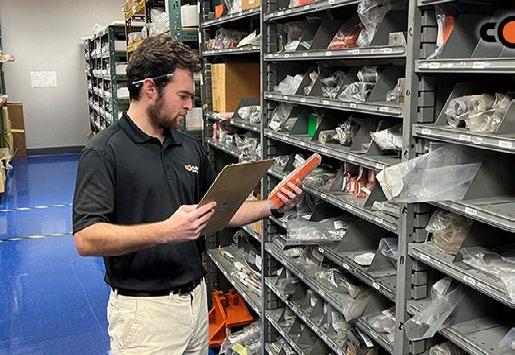
Cosen Saws Support for Machine Parts
Cosen Saws is prepared with a strong stock of replacement parts at their Charlotte, nC headquarters.
Since Cosen Saws beginning in 1976, Cosen has grown and evolved to meet customer’s needs. The commitment to the needs of customers has never changed. In an effort to be proactive, the Cosen Saws parts department is constantly reviewing the parts inventory and processes to ensure that the best customer experience can be offered as well as maintaining a sufficient inventory of parts for repair. no matter how large or small the parts order is, Cosen promises to give the attention and service each and every customerdeserves.
Cosen Saws parts department spans over 3,500 square feet. This includes a comprehensive inventory of replacement band saw parts that are always ready to ship as soon as you need them. With the importance of uptime and proper maintenance of band saw machines, Cosen does their best to keep inventory up to date for all machines including common and uncommon parts in order to make sure the parts you need for your machine are always available. This ensures the best customer experience and makes sure saws are always up and running.
Cosen Saws parts department is always available to assist you during working hours, Monday through Friday from 8:00 aM to 5:00 PM EST. They can help to figure out which parts you may need, place orders for those parts, and check on any current orders. also if you are unsure of which parts you need, the Cosen team will work to help identify the correct match. From there, that part can be reordered or quoted and put on record in case it is ever needed again.
Cosen Saws stands behind their products and for that reason also assure quality customer service and support for as long as you have your machine.
For more information, visit www.coensaws.coms
Datanomix and Vallen Partner to Bring Real-Time Factory Analytics to Industrial Manufacturers
Vallen adds Datanomix production monitoring software to its Metalworking Solutions Business portfolio
Datanomix, maker of the industry’s only automated Production Intelligence™ software platform, announced a partnership with Vallen to offer the Datanomix software solution to its wide range of manufacturing customers. Datanomix is well known for its no Operator Input™ approach to production monitoring. The partnership enables Vallen to offer the Datanomix solution to industrial customers seeking improvements as part of Industry 4.0 and industrial automation initiatives.
“We are excited to welcome Vallen into the Datanomix Partners Program,” said John Joseph, CEO of Datanomix. “It’s clear that selling new technology to manufacturing customers requires a deep and successful history of selling value-added solutions. Vallen is a respected brand in the industrial market. They can now have conversations about adding a new layer of value by introducing our LIVE production intelligence software to the portfolio of solutions.” as part of the reseller program, Datanomix will train Vallen’s Metalworking customer-facing team on selling, installing, and supporting its customers, with comprehensive information on the Datanomix platform and its benefits for precision manufacturers.
“Several machine monitoring companies are selling basic utilization services to manufacturers today. We carefully evaluated the contenders and selected Datanomix for its true real-time job insights and ability to translate job performance to business impact. This aligns with Vallen’s mission of creating value for our customers,” said Chuck Delph, CEO of Vallen. “The information presented by Datanomix accelerates time to information, shortens corrective action cycles, and directly impacts decision-making at exactly the right time. as Vallen focuses on innovation and our leadership position in metalworking solutions, we are truly excited to be offering Datanomix to our customers.”
The Datanomix solution automates the collection and analysis of manufacturing data and delivers deep insights into production performance, both in real-time and over time. Designed for growth-oriented precision manufacturers, the Datanomix platform delivers industryleading innovation of manufacturing productivity with no Operator Input™ without burdening the end user with cumbersome analysis or data crunching.