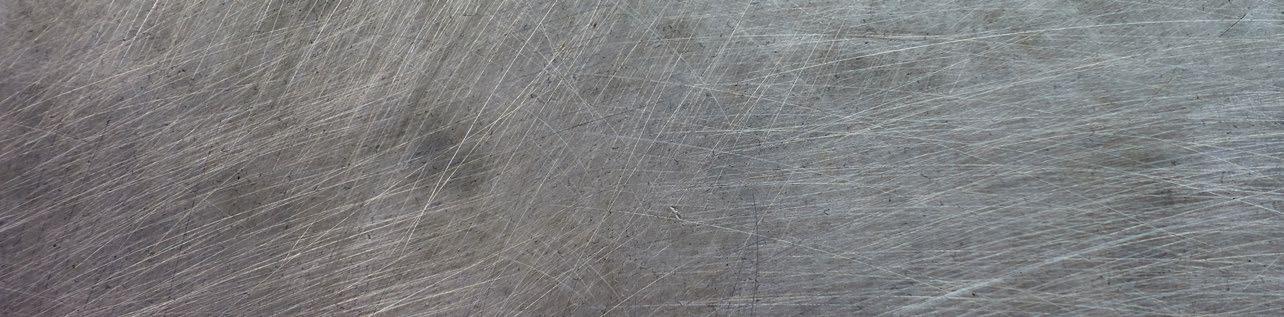
22 minute read
PrODuCT SHOWCaSE
Industrial Machinery Digest's Monthly Product Showcase features the latest from some of the manufacturing industry's top suppliers.
WANT TO BE FEATURED? Send your latest product information to editorial@indmacdig.com
ANCACrete polymer concrete base: a proven ANCA strength

It all begins with a solid base... and a secret recipe. What do tool and cutter grinders and buildings have in common? The importance of having a solid foundation. an essential component of achieving good accuracy and repeatability when grinding a cutting tool is the base. Having a stable foundation for a machine is paramount to achieving stable production. as part of anCa’s commitment to vertical integration, in the late 1980s Pat McCluskey decided to replace the bases that were then outsourced with an anCa designed and manufactured base.
McCluskey’s research was conducted primarily in Europe in conjunction with aachen university who had carried out some research in polymer concrete in machine tool applications. He worked with German and local consultants to develop anCa’s recipe for concrete base manufacture. The base molding technology they developed has since been an important part of the rigid anCa bases.
The first base was poured in late 1989. Further pouring and testing followed until everyone was fully satisfied. now called anCacrete, this technology would provide the best possible foundation for precision CnC grinders, reducing vibration and increasing the overall rigidity of the machine.
Since 1991 we have been using the polymer base technology which forms the stable foundation base of all anCa machines. Customers often ask us to explain the benefits of polymer concrete and we explain that polymer concrete by its very nature has a high thermal mass, so our bases are good at absorbing a lot of heat.
That means that throughout the production processes, their growth and contraction are very controlled and it takes a long time which means that the process is very, very stable. The second main part of polymer concrete is that when we designed the mix over 20 years ago, it was made to mimic the expansion thermal coefficients of cast iron very closely. This means that as our machines heat up and cool down, we can control the expansion and contraction of the machine – which in turn, gives us control over the production processes to make sure that the machine aligns to how we want it to react.
Between the large thermal mass, the very closely linked thermal expansion coefficient to cast iron and also the vibration absorbing characteristics, anCacrete significantly contributes to the overall rigidity of the machine. For our customers this translates into highly accurate tools with a superior surface finish.
This is the first in a series looking at the range of anCa technology that we have developed and refined over
the years so that we can offer the best in class to the market. at anCa we have fully embraced the benefits of vertical integration and are the only tool and cutter grinding machine company in the world that designs and manufactures the complete machine, including building the CnC, precision motors and spindles, and of course our anCacrete polymer concrete bases, in-house.
This means customers enjoy the benefits of a manufacturer that understands their product completely, stands behind the quality of every element, and is uniquely positioned to custom design both hardware and software to suit individual needs.
Optimising installation space and performance with thread-tapping screws
When it comes to fastening lightweight metals, the focus is on optimising installation space and on performance and cost optimisation.
When it comes to fastening lightweight metals, as well as a fastening needing to be reliable, the focus is on optimising installation space and on performance and cost optimisation. against this background a crucial point is the load-bearing capacity of the fastening.
It is precisely for such applications that arnold umformtechnik GmbH & Co. KG has developed Powertite. – a round thread-tapping screw with a trilobular tapping zone. This means that at the deformation point the screw has a slightly triangular cross-section (rounded edges) to reduce the tapping torque. The length of the tapping zone at 3 x p (p=thread pitch) is optimised for the installation space, allowing the forming energy created by the thread-tapping process to be distributed over several thread turns and giving optimal setting and centring of the screw. The round load-bearing cross-section has a defined overlap, the external diameter of the screw is always greater than the nominal diameter. This ensures a greater overlap of the screw’s thread edges and tapped nut thread. The combination of the trilobular shape in the tapping zone and the round cross-section in the load-bearing section achieves a significant improvement in thread-tapping screw fastenings. This is because firstly, the tapping torques are low and secondly, because the load capacity of the tapped nut thread is considerably greater.
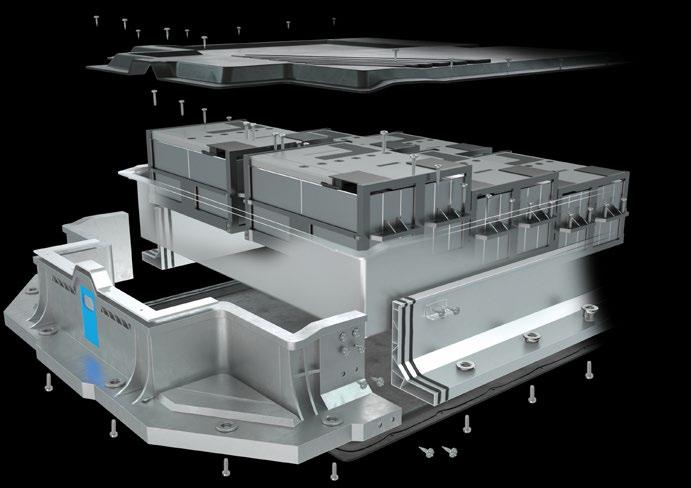
Major savings potential
There are many examples of applications for the thread-tapping Powertite screw. For example, applications in which maximum preload forces need to be achieved with plastically stressed assembly. and Powertite is also suitable for components into which only very short penetration depths can be made and high hole tolerances are necessary. Furthermore, in many cases it is possible to reduce weight by reducing the length of the screw and optimising the weight of the head.
Two specific examples illustrate how even a tiny screw can be a climate protector within a specific product. Since June 2022, a Powertite M7x40 has been implemented in a load transmission unit, currently still used in combination with combustion engines. With 13 screws in each transmission unit and a requirement for some 6 million screws per annum, by using Powertite in this unit alone there is a saving of around 19,400 kg in weight and a reduction in CO2 by 33.1 tonnes each year.
The saving is even greater in an e-motor transmission unit where 33 screws are used for each unit. Of the 50,000 vehicles planned each year, it is forecast that 30,000 will each be fitted with two e-motor transmission units. Projected over all 50,000 vehicles and the 80,000 transmissions needed the total number of screws required is around 2.64 million a year. Simply by using Powertite it is possible to achieve a weight-saving of some 8,519 kg and a carbon reduction of 33.1 tonnes each year in the manufacture of these vehicles.
Enhanced threadtapping technology
according to arnold umformtechnik, Powertite, with its perfect geometric fit, increases load-bearing capacity in the tapped nut thread by over 20 percent compared to screws with trilobular load-bearing cross-section. That creates a series of technical and commercial benefits: standardscompliant tapping torques, plastically stressed assembly even into conical cast core holes in al-Gd, a preload force similar to metric fastenings, and the possibility of larger core
hole tolerances to optimise lightweight metals casting. as well, assembly reliability is very good, and it can also be used in steel, aluminium and other lightweight metals. Furthermore, it is possible to make the screw fastening repeatedly and they can be replaced by metric screws if needed for servicing.
The main focus of Powertite applications lies on electromobility. This is especially true for lightweight metals, but it also applies when combined with cast components.
The product, which has already been patented, was launched on the market in October. as always, potential customers can access the complex product knowledge held by the Forchtenbergbased (south-west Germany) fastener manufacturer, as well as a full understanding of the product’s performance in the various applications and sectors. This is supplemented by the relevant calculation tools and wide-ranging manufacturing expertise. Together with its development partners in the vehicle manufacturing sector arnold umformtechnik has developed a completely new manufacturing process especially for Powertite.

Authentise announces Flows & FlowsAM
rebranded data-driven workflow management suite now available for additive and agile production environments. authentise (www.authentise.com), the leader in data-driven engineering & manufacturing workflow tools, today released its rebranded workflow management suite for both additive and non-additive applications.
Flows is the product of a decade of experience building data-driven solutions for the world’s most agile operations at Boeing, Danfoss, and ricoh, among others. Boeing’s time studies claimed that the system delivers up to 94% time savings and a 3x rOI within 8 months. Formerly known as the advanced Manufacturing Execution System (“aMES”), Flows incorporates many tools that stretch beyond the capabilities of a traditional Manufacturing Execution System, including real-time quoting, machine-data driven status updates, material genealogy, supplier management and more. These features are already used to manage post processing such as heat treatment, machining and more. With this release, authentise is announcing general availability of FlowsaM for operations primarily centred around additive manufacturing, and Flows for those that are not.
“We have long sought to use our experience in the additive sector to fuel digital manufacturing as a whole,” says andre Wegner, CEO of authentise. “additive has key advantages that make it a fertile sandbox, such as more data, less legacy, and focus on lot size 1. That ability to manage agile operations is increasingly in demand as the world moves to address recent supply chain failures. That is why we’ve chosen this point to release Flows and FlowsaM.”
Keith Perrin, VP of agile Manufacturing at authentise and formerly an executive managing Hexagon nexus, autodesk Fusion360, and Siemens Teamcenter added: “Since I joined the team 8 months ago it’s become increasingly clear that authentise has a ‘special sauce’ when it comes to handling production operations that require a high degree of flexibility. I know from experience that this is a big gap in the market, now more than ever. authentise’s ability to integrate machine data, 3rd party software tools, and human operations, into a contextual process is critical to meeting that need. The success we’ve seen with some of the world's most advanced agile engineering operations speak for themselves. I’m excited to bring this capability to other enterprises looking to deliver more flexible engineering, production and supply chains.” authentise FlowsaM (https://www.authentise.com/ flows-am) is available today. authentise Flows (www. authentise.com/flows) will be generally available in 2023. an early adopter programme is now open for customers with a particular interest in driving agile operations into their engineering and manufacturing operations and realising near triple digit productivity improvements.
Beckhoff Elevates XPlanar Functionality with Bumper ID and New Mover Variants
The adaptive automation system’s expanded features and mover variety further boost traceability and flexibility for wide-ranging applications
Beckhoff has once again created new possibilities in adaptive automation by expanding the functionality of the XPlanar “flying motion” system. now, on top of XPlanar’s impressive, field-proven capabilities, the solution can handle more products with even more flexibility through new mover identification, movers for two lanes of traffic on one tile, rectangular movers and mover coupling for higher payloads.
XPlanar now provides greater traceability through ID technology integrated into the mover bumper. The ID functionality enables unique identification of XPlanar movers by reading the mover’s individual serial number. The ID bumper is easy to mount or retrofit on movers already in the field, and it requires no additional hardware. This solution makes it possible to seamlessly track movers and the products they carry – even after system shutdown and restart. The bumper ID also eliminates the need for homing at system startup with appropriate programming. among the new XPlanar mover variants, the aPM4221 is now the second smallest model in the aPM4xxx family.
It supports payloads up to 1 kg and is ideal for handling small and medium-sized products with 140 mm center-to-center spacing. With dimensions of 127 x 127 mm, the aPM4221 allows two lanes of traffic to flow simultaneously across one row of XPlanar tiles. This enables a complete production cycle, including recirculation, with minimal footprint. The same applies to the aPM4230 rectangular mover, which measures 115 x 155 mm, for payloads of up to 0.8 kg. a third new variant is the aMP4350 rectangular mover, which measures 155 x 235 mm and supports payloads of up to 3 kg. By adding a second row of tiles to the XPlanar base, the aPM4350 rectangular mover enables up to three lanes of transport for longer products, further increasing adaptive automation capabilities.
The aPM4550 XPlanar mover is the largest version (235 x 235 mm) and can transport payloads up to 4.2 kg, making it the perfect device for handling larger, heavier products. More elaborate workpiece carriers and attached tooling can also help meet specific application requirements.
However, XPlanar can transport and position payloads weighing far more than 4.2 kg. using a simple adapter, several movers can be mechanically fixed together and the payload increases linearly. Coupling four aPM4550 movers would result in a new maximum payload of approximately 14.8 kg.
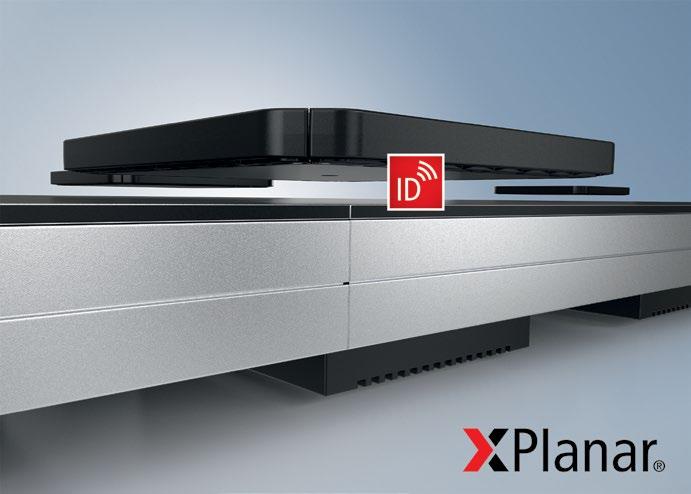
Our selection of Permanent and Electro magnet lifts cover a wide range of steel lifting applications. We also specialize in custom lift solutions designed specifically for your application. TOLL FREE 888.582.0822 imi@magnetics.com
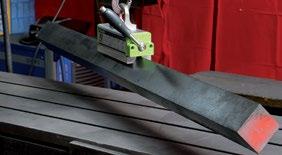

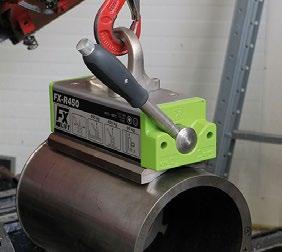
Industrial Magnetics Inc. 1385 M-75 S, Boyne City, MI 49712 PHONE: 1.231.582.3100 magnetics.com
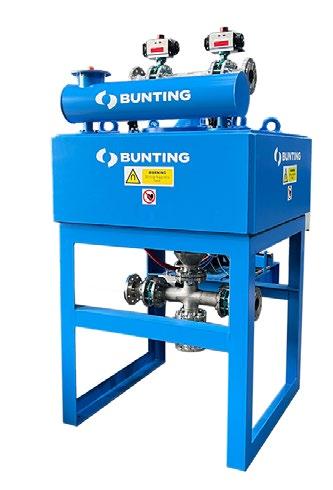
Electro Magnetic Filter for Ceramics Producer
Model HIF225-50 Electro Magnetic Filter a leading German ceramic manufacturer is cleaning ceramic glaze with a high-intensity Electro Magnetic Filter designed and manufactured by Bunting. The successful removal of fine magnetics reduces finished product rejects and increases surface brightness.
The Electro Magnetic Filter provides one of the most effective methods of removing problematic fine iron and paramagnetic minerals from ceramic slips and glazes. The separation efficiency of the technology is significantly better than permanent magnetic separators such as Liquid Pipeline Separators and Tube Magnet configurations. Electro Magnetic Filters consist of an electromagnetic coil positioned around a central hollow core containing a magnetic (400 series) stainless-steel matrix of various designs. The highly efficient computer designed coil generates a high intensity magnetic field that intensifies on the points of the matrix creating the magnetic force needed to separate paramagnetic particles from the slurry. The rectangular steel casing enclosing the magnetic coil intensifies the magnetic field into the hollow centre of the coil. Valves, mounted on the top and bottom of the Electro Magnetic Filter, close and open in a controlled timed sequence for product feed and discharge, as well as matrix cleaning using water and air.
In operation, ceramic glaze or slip feeds up through central canister packed with magnetic stainless-steel matrix. The magnetic field of the Electro Magnetic Filter intensifies on the sharp points of the matrix, enabling the capture of fine magnetic particles such as free iron and magnetic minerals.
This ceramics project in Germany required a large model HIF225-50 Electro Magnetic Filter, which generates a background magnetic field of approximately 6,500 gauss inside the central canister. The points of the matrix enhance the background magnetic field by up to four-times, with the 6,500 gauss models generating peak fields above 2-Tesla.
The ceramic glaze feeds up through the Electro Magnetic Filter for a period of approximately 60 minutes. On an automatic operation cycle, managed by a separate control panel, the valves system then stops the feed, diverting the glaze back into the feed tank, whilst the system goes through a cleaning cycle. This involves discharging the captured magnetics from the canister and cleaning of the matrix, which lasts for approximately two-minutes. The control enables adjustment of the sequence times to suit the processing of a wide variety of ceramic glazes. In this project, the HIF225-50 handles between 3-5 tons per hour of glaze with 64% solids. “If fine iron and magnetic minerals are not removed from ceramic glaze, they cause surface defects and discoloration,” explained Phil Tree, Bunting’s European Sales Manager. “In this project, we are working with one of the world’s leading ceramics manufacturers. They understand the necessity and benefits of automatically removing all magnetics, which is only possible with an Electro Magnetic Filter.” CERATIZIT MaxiMill 491 Features New Insert Size for Added Flexibility
For maximum productivity and machining application versatility, CEraTIZIT offers a wide range of tooling systems within its expansive Indexable Milling line of products that includes the company’s new MaxiMill 491. With eight usable cutting edges per newly expanded 9-mm insert size, a precise 90°profile and a durable nickel-coated tool body, the MaxiMill 491 system is extremely well suited for all shoulder and full-slot milling applications.
The MaxiMill 491 system provides exceptional ease of use, allowing users to quickly exchange inserts while the tool remains in the machine. This capability significantly reduces machine downtime while the precision-ground inserts deliver stable and smooth cutting thanks to CEraTIZIT’s state-of-the-art Dragonskin coating technology. Plus, the Dragonskin coating gives the inserts added strength for even the most demanding of machining conditions.
Configured with a positive insert geometry, the MaxiMill 491 ensures excellent surface quality and dramatically increases tool life. The tool’s eight usable insert cutting edges also provide a low price per edge for cost effectiveness.
CEraTIZIT initially launched the MaxiMill 491 in a 12-mm size with a nominal diameter range from 32 to 160 mm and a corner radius of 0.8 mm. The company extended the range with the addition of 1.2-mm, 1.6-mm and 2.0-mm corner radii. The new 9-mm insert size now brings even greater flexibility for all applications.
With this smaller size, more inserts can be mounted in the tools for even longer tool life and higher chip removal rates. The new size also reduces power consumption, making the MaxiMill 491 effective for use with lower power machine tools.
AM Coating: Innovative coatings for brake disks
A high-speed process to protect against corrosion and wear How can the protective layer be applied to the brake disk more quickly and more effectively? and how can it be made to stay on for longer? “The solution is intelligent coatings, as can be applied to brake disks using our aM coating system” says Dr. Géza Koscsák - the Head of additive Manufacturing at the CHIrOn Group. He has played a prominent role in developing the new system and reaching the decision to opt for the high-speed deposition welding process in his previous job as Head of advanced Development.
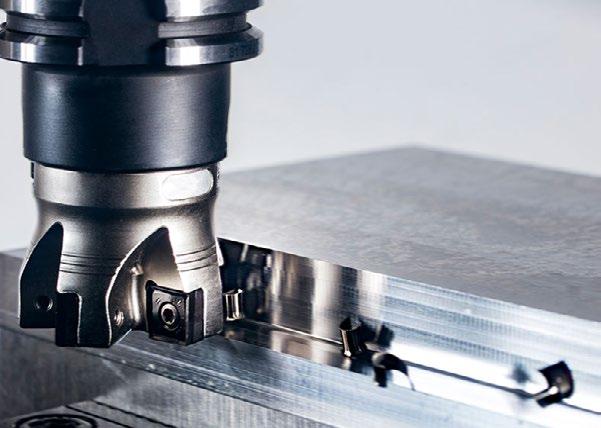
Innovative and productive process
Compared with the conventional LMD process, powder particles travel a longer distance before they are applied during high-speed laser material deposition. This means that they absorb more energy and melt in the laser beam, which enables a significantly faster coating speed. This process also has a clear advantage in comparison to thermal coating using high-velocity oxygen fuel spraying. aM coating's quicker speed and shorter process are two advantages with respect to the future Euro 7 standard, believes Dr. Koscsák. “When the standard comes – and it certainly will come – a production volume of 10 million brake disks annually will need to be managed, for the European vehicle brands alone. With a cycle time for conventional brake disks of around 30 seconds per disk, it's clear that the coating process needs to keep up” he adds.
In line with market requirements: aM Coating available in two versions » aM Coating TWIn is specifically designed for series production. The system works with two lasers for front and rear coating and the brake disks are transferred automatically. » aM Coating SInGLE is the ideal choice if you would like to test materials and material combinations in parallel with or before series production, to develop the application process or to manufacture small series. upon request, the team of experts at the
CHIrOn Group can provide support during process development, either at the customer premises or in
Tuttlingen. “We could install a base machine here,” says Dr. Koscsák, outlining a potential scenario, "where the customer's specialists can learn the process, run tests and set up the parameters with us ready for series production. Or, for a continuous and even more productive process, we can integrate a grinding machine and perfectly coordinate both systems."
Top-quality, firmly bonded application
about crack formation and durability? Project Manager Ernest Frombach says “We use high-speed laser material deposition to achieve improved adhesion through the firmly bonded connection. The layers are also thinner, down to tenths of a millimeter. This uses less material, and our powder management enables us to achieve a high degree of powder utilization. The powder and hard material layers are applied directly one after the other. By applying the first layer, the brake disk is tempered as it were, and we consistently achieve the best application quality for every brake disk without pores or cracks forming.”
More about the Chiron process at: www.chiron-group.com/ expertises/additive-manufacturing
AI-Powered, HD Mode for 3D Scanners
Exact Metrology: a Division of In-Place Machining Company and a comprehensive 3D metrology service provider and hardware sales company, has increased the capability of their artec 3D handheld scanners with the new HD mode. This artificial Intelligence-powered scanning technology provides ultra-sharp, clean and detail-rich scans for artec Leo and artec Eva.
Powered by artec 3D‘s aI neural engine, users can obtain sharp 3D scans with a resolution of up to 0.2 mm. Trained on hundreds of thousands of carefully selected samples, the engine’s neural network detects familiar patterns, surface details and shapes. This allows the 3D scanner to reconstruct a higher number of polygons per frame, resulting in 3D data that’s both denser and higher quality. now, the desired HD density can be selected from a standard 1X density up to 36X for Eva (~3 mln polygons per frame) and 64X for Leo (~5 mln polygons per frame). HD mode makes it possible to capture smaller, thinner elements with the 3D scanner while also considerably reducing noise. With these artec scanners, fine edges can be captured in high definition, faithful to their original shape. It’s easy to capture hard-to-reach areas
as the scans are reconstructed with every detail, giving users complete surface geometry.
Handheld Eva and Leo scanners can easily scan dark or shiny surfaces in high resolution and capture the full range of their geometries, without additional steps. using the artec aI engine, little to no noise in the raw scan data results in cleaner processed data and also saves time when producing the final 3D model. Once difficult to capture, now short hair, even separate strands, are fully within reach when scanning with HD mode. Furthermore, these scanners can capture a broad range of objects flawlessly and in high detail: from smaller, intricate parts such as thin pipes or valve handles, to larger objects with multiple high-detail sections, including car engines and skeletons. a perfect fit for reverse engineering and quality control due to clean, comprehensive data, scans can be easily fitted with primitive shapes and exported to the most popular CaD solutions for development.
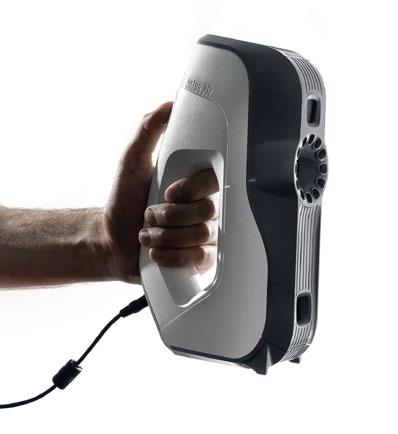
EXaIr’s VariBlast® Precision Safety air Gun has won the 2022 People’s Choice award from Professional Tool and Equipment news (PTEn). These safety air guns provide a focused blast of air capable of handling tough jobs with remarkable strength while minimizing air consumption and noise. This OSHa safe air gun employs an engineered, full finger, variable flow trigger able to produce varying force upon a target simply by pulling the trigger. The VariBlast is available with a standard, 12" or 20" extension which can also be outfitted with type 316 stainless steel or PEEK thermoplastic air nozzles for non-marring applications.
The 1/4 nPT VariBlast Precision Safety air Gun has a convenient hanger loop built into it. The air gun body is made of high impact acetal thermoplastic. The airflow that exits the nozzle can’t be blocked, assuring safe operation and meeting required OSHa standards 1910.242(b). a quiet 75 dBa noise level is well below the limits of the OSHa noise exposure standard 29 CFr 1910.95(a). a variety of other Super air nozzles with different force and flow values are available. all of EXaIr’s Safety air Gun product lines are CE compliant and use engineered air nozzles for high performance and safety. all are available with extension pipes and Chip Shields. Price starts at $88.00.
For more information, visit: www.exair.co/153-pten
Graco Launches QUANTM Pump
The new electricoperated double diaphragm pump for industrial and hygienic applications is a big leap forward in pump innovation
Graco Inc. (nySE: GGG), a leading manufacturer of fluid handling equipment, announces the release of the Company’s next generation electric-operated double diaphragm pump, QuanTM™. The QuanTM pump features a revolutionary new electric motor design that is up to 8X more efficient than a standard pneumatic pump.
The innovative QuanTM pump is suitable for nearly any fluid transfer application and offers a wide range of materials of construction to support multiple industrial and hygienic applications, including chemical processing, water treatment, paint manufacturing, food and beverage, pharmaceutical and more.
“The QuanTM pump isn’t a new twist on old technology. It’s an entirely innovative design that changes how pumps perform in factories and other installations around the world,” said Dan Purkat, Senior Product Marketing Manager. “We’re excited to have created an advanced, extremely efficient design that is lightweight and provides significantly lower lifetime costs than other pump technologies. The pump modernizes operations by greatly reducing energy cost. This empowers industrial manufacturers to protect and grow margins and measurably contribute to energy savings, compliance and environmental stewardship efforts.”
The breakthrough electric QuanTM pump is designed to be a highly reliable drop-in replacement for current pneumatic pumps or greenfield construction. This pump is built for harsh industrial or hygienic environments, yet its innovative and efficient design is lightweight and easy to maintain. With built-in controls and no gearbox, the pump also fits seamlessly into most fluid transfer applications. “Our new QuanTM pump is the perfect solution for upgrading your less-efficient air operated pumps,” said Jeffrey Shaffer, Senior Product Marketing Manager. “The same great self-priming, stalling, seal-less design with smooth, steady flow is a must-have for in-process applications, filling systems and hygienic applications. The powerful new FluxCoreTM motors and drives deliver up to eight times more continuous torque at low speeds than conventional motors, and the plug-and-play installation allows you to easily replace existing pumps without additional investment or infrastructure rework.”