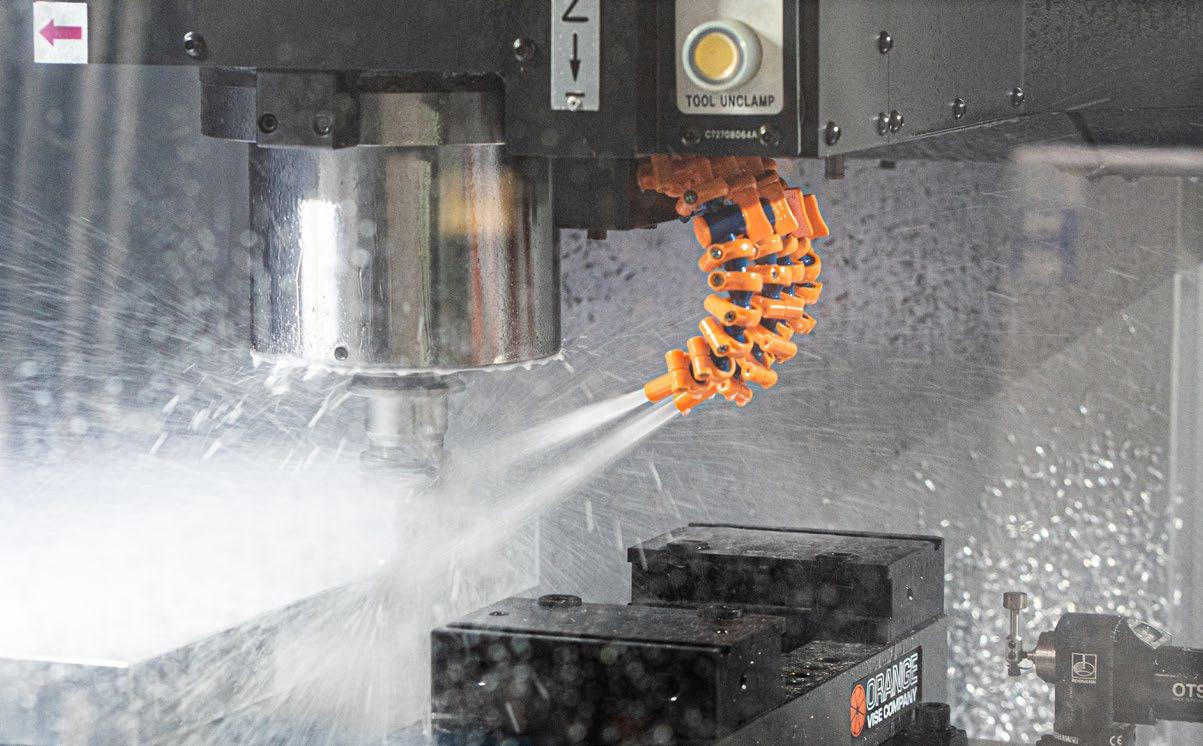
9 minute read
WORKFORCE DEVELOPMENT
The Cutting Edge of Aerospace Machining: Ensuring Parts are Precise and Reliable for Critical Applications
from rapid prototyping and design for manufacturing before the first part is machined, to adaptable and scalable manufacturing and state-of-the-art metrology & inspection throughout the process
For the aerospace industry, the “cutting edge” of parts machining goes far beyond having the latest CNC equipment and accessories. It also means engaging at the earliest stages of the process using the latest in design for manufacturing (DFM), simulation and process verification processes prior to cutting the first part. It is then critically important to have flexibility and adaptability to make changes and scale production when needed with the ability and commitment to inspect with the most precise tools throughout the process. The goal of this approach is to give customers the knowledge that when machining begins, the parts are going to be 100% right, with zero defects, the first time and every time. Delivering this level of peace of mind is critical in the aerospace industry. There is, after all, so much at stake in aerospace and defense where parts are critical to performance and safety. Whether operating in the air, sent into space, or used on the battlefield, the reliability of how parts function is essential to success.
Typically, when a potential customer is looking for a machine shop to make a complex part, they are looking for the latest equipment and current certifications including ASQ, ISO 9001 and AS9100. There is a tremendous benefit, however, for a customer to look beyond these prerequisites for a machine shop that will work with them from the design phases through manufacturing to predict and resolve failures before they happen. The ability to predict when failures could occur requires proactive communication and early engagement with an expert machine shop.
Design For Manufacturing – The Ability To Adapt Early
A Design for Manufacturing process enables the machine shop to anticipate possible complications and limitations in the machining process upfront.
“With Design for Manufacturing, the goal is to make the product manufacturable in an efficient and cost-effective way and that starts with reviewing the parts and discussing the specifications openly,” says Tony Doan, CEO of San Jose, California-based Halcyon Manufacturing, an advanced ITAR Registered and AS9100/ISO9001- Certified manufacturing shop for complex parts serving Greater Silicon Valley. “The aerospace and defense industry needs a cutting-edge machine shop that has both the expertise and the desire to guide their customers on how to achieve better machined products at a better price.”
This analysis and feedback are part of an ongoing manufacturing collaboration between an aerospace client and their contract machining partner well before production starts from the inception of a project through prototyping.
Halcyon applies the Design for Manufacturing protocol across a wide spectrum of metal machining from bar grade 6061 aluminum, brass, copper, titanium, stainless steel, and plastics. The company also works with quartz, ceramic, graft, titanium, and a variety of steels and serves customers in the aerospace, home defense, automotive, medical, and semi-conductor sectors.
“When you can use the latest simulation and process verification technologies prior to cutting the first chip of metal or plastic, then when you start manufacturing, you know that the parts are going to be 100% right the first time, every time,” says Doan.
Rapid prototyping
Rapid prototyping removes financial and time risk by providing a cost-effective way to test a full range of designs and materials. With rapid prototyping, many iterations of a part may never make it to production, which can save aerospace and defense contractors time and money.
“If we understand how the part needs to function, we can 3D print the item in plastic, run it through a few tests, and then proceed – rather than rush to machine parts out of expensive material in the prototype phase,” explains Doan, who adds that in addition to initial prototyping, 3D printing can be used to create workholding and fixtures.
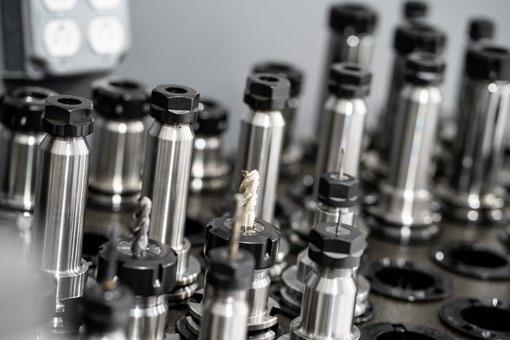
Adaptability And Scalability In Production
Aerospace and defense clients operate in highly dynamic markets and the need for changes to part specifications and the quantity of parts is high. Cutting-edge aerospace machine shops must therefore be adaptable and flexible for any design changes. They also must be capable of scaling up production to “lights out” manufacturing if needed without compromising the accuracy of the machining.
“While capacity is certainly important, the overall size of a machine shop is not the most important criterion,” says Doan. “Aerospace and defense companies certainly need manufacturing scale, but they also require adaptability as complex manufacturing designs evolve and change. For a machine shop to be an effective partner, they need to be nimble.”
Inspecting Quality Upfront
Finally, to complement the machining capabilities and nimbleness, a shop must have state-of-the art metrology equipment for advanced inspections guided by a proactive zero-defect mindset.
“It’s not about making parts and sorting out the bad ones and shipping the good ones,” says Doan. “You need a machine shop committed to not making the bad parts at all.”
“To produce the most precise parts, you must be able to inspect more than the finished goods,” he adds. “A machine shop should be inspecting in real-time such things as the set-ups and the speed throughout the process which enables data to be captured for statistical predictive process control.”
At Halcyon, automated coordinate measuring machines (CMMs) perform process inspections and produce first article reports. Halcyon also uses a digital multimeter (DMM) with scanning capability that can take thousands of data points during a scan of a complex curved surface. This results in very precise and accurate repeatable product evaluations.
Forging A Partnership
Aviation, defense, and other sectors that rely on machine shops to produce precision parts to extremely tight tolerances with consistency should look beyond the basic certifications and CNC capabilities for those with the expertise to optimize the manufacturing process before any items are manufactured and adjust as needed after. With this level of flexibility, and by ensuring a zero-defect approach at every stage of the process, OEMs and defense contractors can proceed with certainty that the parts they are receiving are of the highest reliability and without unnecessary additional costs for their most critical applications.
8 Questions for Better Plasma Cut Parts
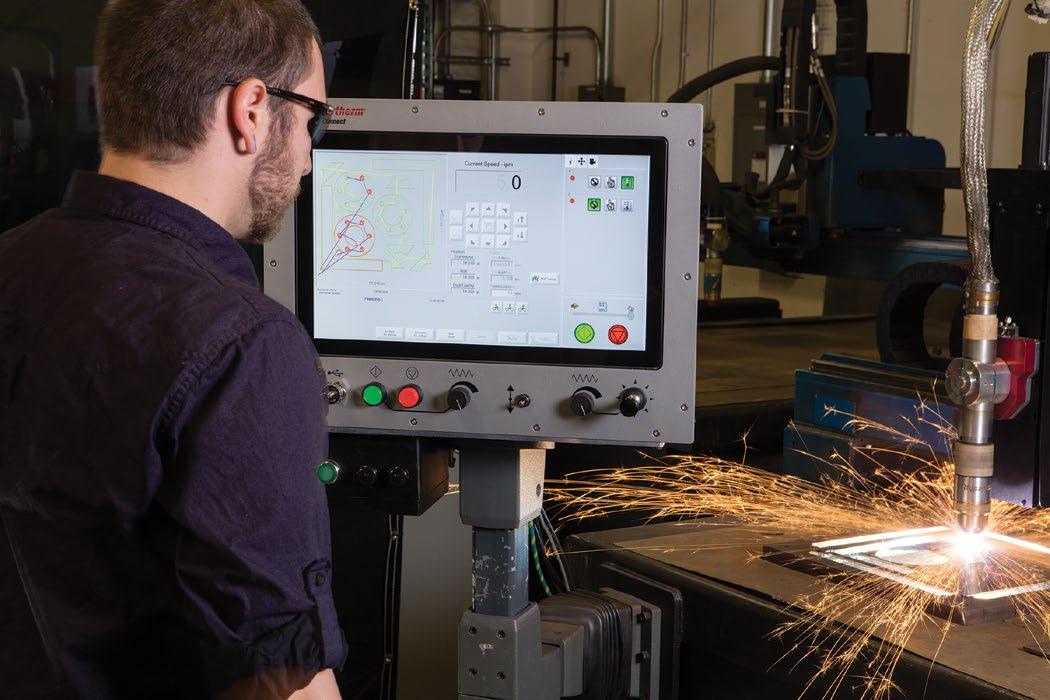
By: Michelle Avila, Hypertherm Inc. Communications Manager
Questions about cut quality and consumable life are common when cutting with plasma. How’s my cut quality? Are my consumables lasting long enough? Is there anything I can do to improve my productivity? Unfortunately, there isn’t one simple answer to the above questions because so many factors impact the outcome you will see. Although Hypertherm’s Technical Service Team is happy to help you troubleshoot issues, customers can often achieve the same results by asking the following eight questions.
1. Are You Cutting in The Right Direction?
With standard consumables, the plasma arc spins clockwise as the torch moves forward into the cut. This means the squarest cut angles will be on the right side of the arc. To benefit from this, cut contour shapes in a clockwise direction and holes and other internal features in a counter-clockwise direction. 2. Are You Following the Cut Charts?
Sounds like a simple question, right? Still, we often come across customers using the wrong settings. Look at your owner’s manual. Refer to the cut charts and make sure you are using the
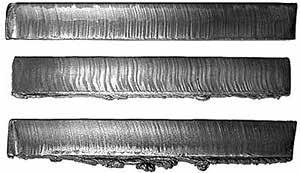
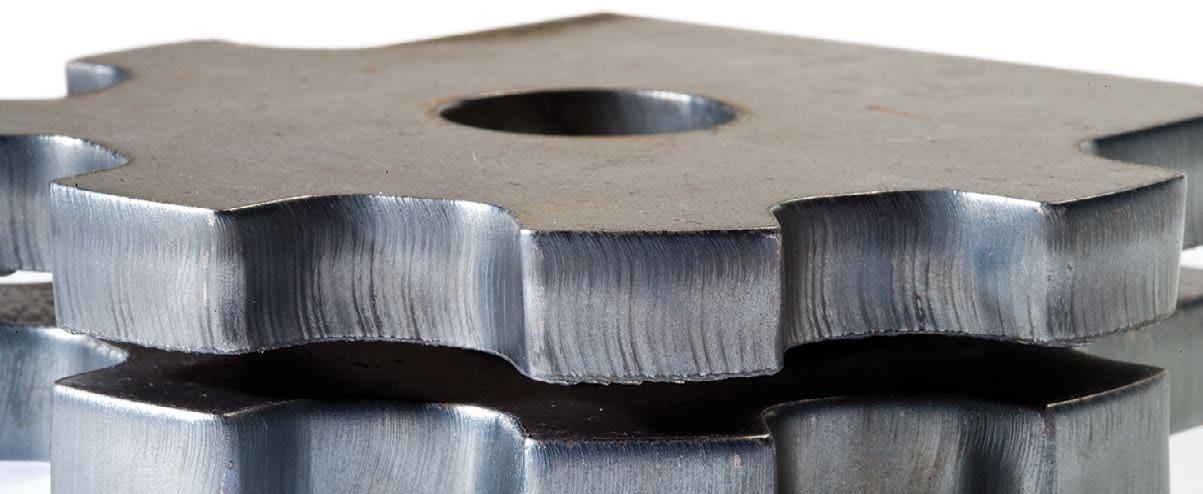
settings listed for the material type, material thickness, desired cut quality, and speed you want. The cut charts will tell you what consumables to use, what plasma and shield gas you need, and give you the appropriate gas pressure (or flow rates), torchto-work distance, arc voltage, and cutting speed.
3. Are You Using Good Consumables?
Any type of imperfection on your consumable parts can impact system performance so you want to regularly inspect your consumables and replace if needed. Though less common, we also sometimes discover customers who have accidentally put the wrong consumables into the torch. If you continue to have cut quality issues, we suggest double checking the laser-etched part numbers found on each consumable with the numbers in your owner’s manual.
4. Is Your Torch Square to The Workpiece?
Torches can sometimes get knocked out of alignment. If you find that you need to adjust your torch, check to make sure your table and workpiece are level and that your table slats are not covered in dross. Keep in mind that if the metal plate you plan to cut is bent or warped, it might be impossible to square the torch.
5. Are you holding the right torch to work distance?
Sometimes referred to as a “stand-off,” you’ll want to ensure your torch isn’t too close or far from the workpiece as this will cause angled and rounded cut edges. In addition, if the torch is too close, metal spatter blowing back onto the torch can seriously damage your torch and nozzle. Lastly, don’t forget to routinely adjust the torch to work distance as your consumables wear.
6. Are you cutting at the right speed?
Dross is a great visual clue that lets you know if your cut speed is too fast or too slow. Low-speed dross is the bubbly or globular molten material that collects at the bottom of the cut edge. This kind of dross is easy to remove and flakes off the plate. To eliminate it on future parts, cut faster. On the contrary, high-speed dross causes a thinner bead of molten metal to collect at the bottom of the cut. To fix this, slow down your cutting speed so the arc has time to catch-up with the torch.
7. How is your air or gas quality?
If using an air plasma, make sure your air is clean and dry. The same applies to your gas when using an oxygen or multi-gas system. Always use pure, high-quality gas and the appropriately sized regulators and gas lines. If a manual purge is required, confirm that the purging cycle was completed. Check to see if gas is leaking or flow is restricted. Ask your gas distributor for help if needed.
8. Does your table need a tune-up?
Is the table cutting at the specified speed? Is the torch secured tightly to the table gantry? How is your table motion? Is it vibrating? Often, plasma cutting issues have nothing to do with the plasma itself and instead are caused by poor motion or other table issues. If you’ve run through the preceding seven questions and are still having issues, it might be time to reach out to your table manufacturer.
ABOUT HYPERTHERM
Hypertherm engineers and manufactures industrial cutting products used by companies around the world to build ships, airplanes, and railcars, construct steel buildings, manufacture heavy equipment, and more. Its products include cutting systems, CNCs, and software trusted for performance and reliability that result in increased productivity and profitability for hundreds of thousands of businesses. Founded in 1968 and based in New Hampshire, Hypertherm is a 100 percent Associate owned company, employing more than 1,800 Associates, with operations and partner representation worldwide.