
4 minute read
TALKING SHOP
feaTURinG:
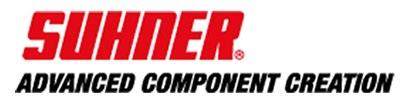
Suhner OWS, Orbital Sander.
TALKING SHOP WITH: Mike Ricketts — Western Midwest Regional Manager — SUHNER Machining
How would you describe your company's primary business?
Helping manufacturers with their success—critical metal component machining needs that include drilling, milling, honing, chamfering, reaming, cutting, and tapping into steel, aluminum, alloys, fiber glass, foam and other materials.
In brief, what is your history with the company?
I bring almost 23 years of industrial automation experience to the table. I have been with SUHNER nearly five years as their Western Midwest Regional Manager for the Machining Division based out of the Chicagoland area. I have developed relationships with companies ranging from Fortune 50 companies all the way down to local contract manufacturers in main industrial verticals (i.e., Large and Small Commercial Trailers, Automotive, Aerospace and Foundries to name a few).

How has your company changed through the years?
SUHNER has become much more focused to the needs of their customers globally as well as regionally. Our goal is to support our customers manufacturing needs quickly and easily with our ‘care’ programs (stocking MRO supplies on-site and providing support).
What are interesting applications of your products?
Over the last few years, SUHNER has helped the Trailer Industry with their manufacturing needs.
What critical issues are often overlooked by your clients that they have or might encounter?
One of the primary issues overlooked often is what type tooling our client would need to be using and how to incorporate it within the spindle application. We can’t stress enough the need to get a tooling expert involved early in the project to recommend proper tooling for the application.
What are the key advantages you provide to small-to-medium manufacturers?
Some of the key advantages we offer is our local representation. SUHNER offers engineering, technical support, and a complete service center here in the U.S. What are you excited to bring manufacturing professionals in 2022?
Because of the rising needs of the market and our customers, SUHNER has launched a range of Robot end-effectors for material removal and polishing.
For more information, visit www.suhner-machining.com/en/
The sUHneR RoboTools for fully automated manufacturing
For stationary machining applications, SUHNER products already represent the first choice. However, in cases where the cutting tool must be moved towards the work piece, insufficient or not, many practical solutions are readily available. This gap is now being closed by the SUHNER robot machine tool program. One option is to bring the work piece towards a standard stationary SUHNER machining unit. Today, SUHNER offers the possibility to adapt and guide the tool by the robot.
As a specialist in automation processes, machining units, handheld power tools and abrasives, SUHNER has expanded its wide product range with special tools that can be mounted directly to the robot arm and ready for continuous industrial use. In short, SUHNER has multiplied the capabilities of the robot to now include surface finishing. The application range is enormous.
Change of the abrasives
Abrasives typically have a short life cycle. A patented, simple quick change of abrasives system (dispose and reload) was added to the program to simplify the change of abrasives.
This quick change for abrasive system from SUHNER, for example, allows the use of different abrasives in sequence to achieve a desired surface finish. An automated abrasive change increases the flexibility and eliminates unproductive production hours.
Servo motor driven angle grinders
Today, most robot guided grinding and polishing machine tools are operated by air. Often, considering a 24-hour operating environment, these machines reach their limits. Frequent service interruptions, plus extremely high air consumption add to energy cost that also will affect profitability. In addition, air driven tools drop in speed when under load which can contribute to an adverse effect to the surface finish. Depending on surface quality requirements, the rotation of the grinding or polishing tool often requires clock and counter clock rotation which an air driven tool can’t accomplish.
All of these critical requirements can be met with the newly designed servo driven tools from SUHNER either in standard or orbital design version. Lightweight and powerful servo motors are used to obtain high speeds up to 9,500RPM made for continuous operation. All grinding tools are made with an M14 spindle to enable the use of standard, commercially available grinding discs.
For more information, visit https://www.SUHNER.com/en/robotics/
LIKE YOUR BIG VMC’S APPRENTICE
CNC MILLS | CNC LATHES | CNC PLASMA TABLES | CNC ROUTERS | AUTOMATIC FEED BANDSAWS
Prototype. Run second operations. Perform short-run production.
With its compact size, the 1100MX sneaks into unexpected places. With servo motors and a BT30 spindle, it’s built to mill anything. Set it up and start making chips and cutting parts. At Tormach, we help people make things. Our 1100MX runs on our intuitive and easy-to-use CNC controller, PathPilot®. For a lot of our users, PathPilot is a dealmaker. Start cutting for $21,450, or deck it out with an optional ATC and PathPilot Operator Console. What do Tormach owners love about Tormach?
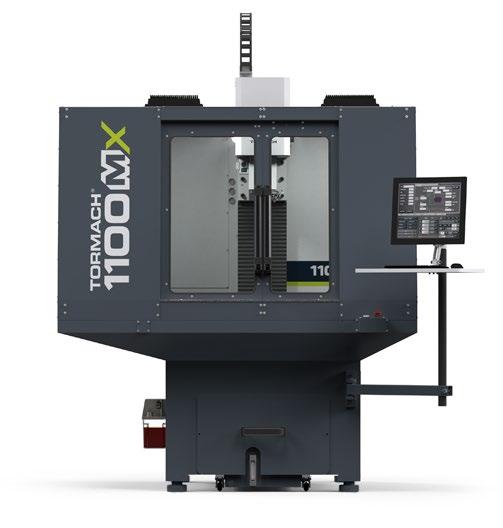
• Maintain your right to update, upgrade, and upkeep. • Buy-what-you-need, upgrade-as-you-go modular equipment. • Experienced machinists make up our USA-based
Tech Support crew.