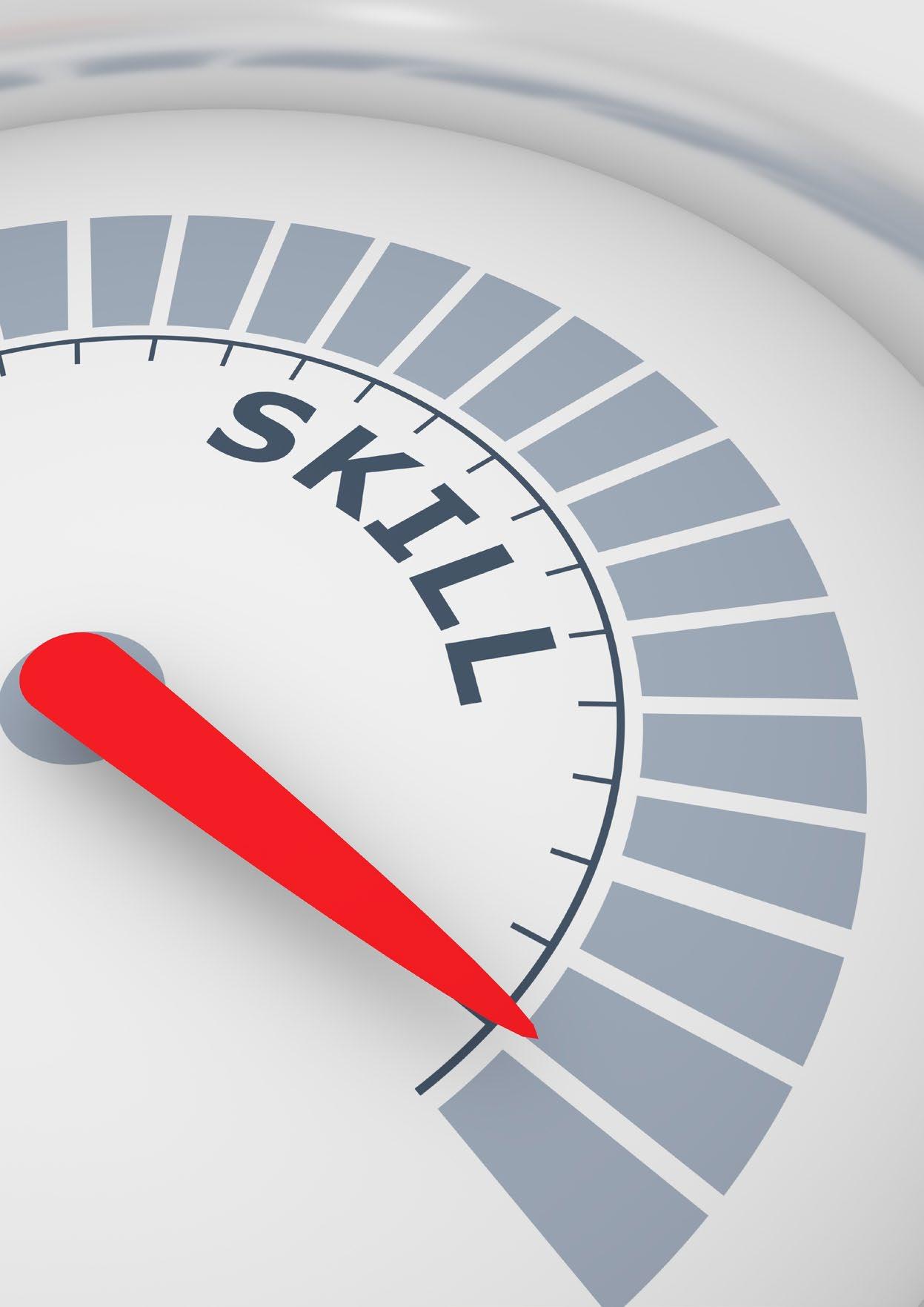
7 minute read
WORKFORCE DEVELOPMENT
Technical Skill Assessments: A Tool for Managers, Machinists, and More
By: Tony Glockler, CEO and Cofounder of SolidProfessor
The industrial manufacturing sphere is facing many exciting opportunities for innovation and digital transformation thanks to Industry 4.0. Many sectors — from heavy equipment and machinery to mold, tool, and die — will be growing significantly over the next decade. The industry is slated to create several million jobs, encompassing skilled production roles such as CNC machinists and programmers as well as engineers, scientists, and researchers.
However, all of this growth and opportunity comes with some major hurdles, one of which is the significant shortage of skilled workers. This skilled labor gap has the potential to leave millions of new jobs unfilled and is already causing hiring delays in the industry.
One way that organizations are tackling this challenge is by hiring outside of their typical job requirements. This often means focusing less on technical skills and instead hiring for skills such as logic troubleshooting, spatial visualization, critical thinking, and most importantly, a willingness to learn.
Organizations must then take a more active role in providing training resources and opportunities to help workers get their technical and software skills up to par. Employers are offering more apprenticeships, coordinating on-the-job training, and providing access to tools like online learning platforms.
With the need to upskill employees quickly, tools like skill assessments are incredibly helpful for both employers and potential candidates. Skill assessments for technical skills like CAD and CAM software can be used in a number of different ways to aid in the hiring process and build an effective training program for manufacturing workers.
What Are Skill Assessments and How Do They Work? Skill assessments test an individual’s proficiency in specific competencies. Unlike resumes and in-person interviews, skill assessments offer an objective and standardized method for measuring skills. The assessments provide clear scores, ratings, and analyses that highlight strengths and weaknesses.
Technical skill assessment scores are one of the most important inputs when conducting a skills gap analysis. In a skills gap analysis, you can compare these scores to help determine where gaps exist between existing and required skill levels, and even between different employees on a team.
Many online learning platforms offer skill assessments for technical skills including CAD and CAM software. Some platforms will even aggregate team results and/or break down the assessment scores by separate skill sets. For example, an online SOLIDWORKS skill assessment might give you scores in Drawing, Assemblies, and more in addition to an overall score so you can get a clearer understanding of individual competencies as well as overall results.
TheBestTool Cabinet You Will EverBuy 1 0 0 % M A D E I N T H E U S A
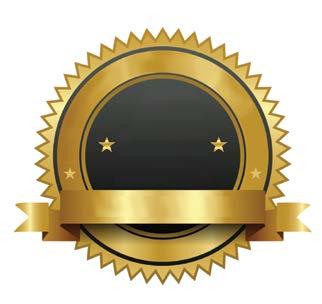

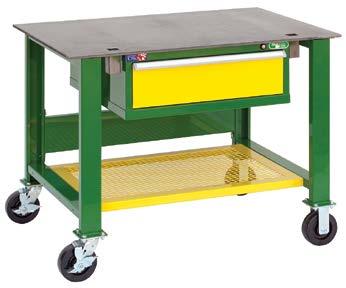
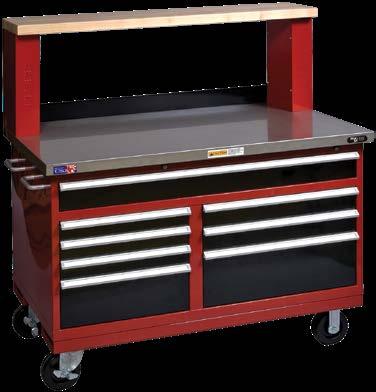
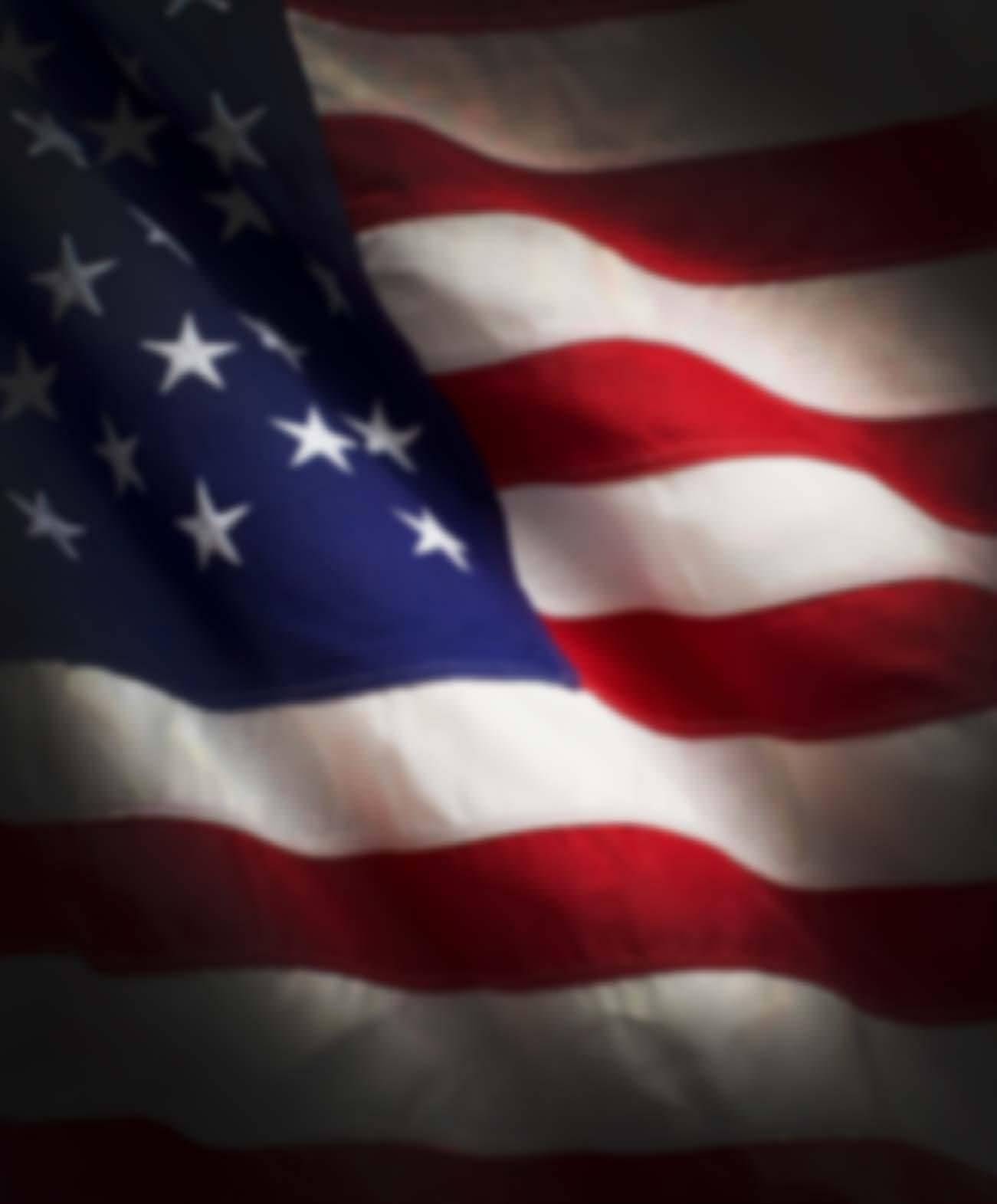
GUARANTEED I N E V E R Y W A Y
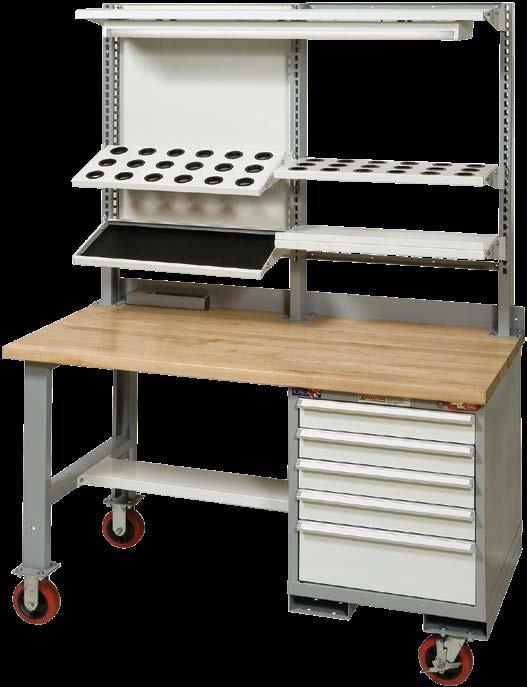

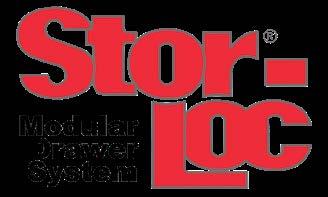
WWW.STORLOC.COM • 1-800-STORLOC 1-800-786-7562 MADE BY AMERICAN CRAFTSMEN IN THE USA sales@storloc.com
CLOSING IN ON THE MANUFACTURING The Manufacturing Sector’s Skills and Labor Shortage
The U.S. manufacturing industry needs to fill more than 4 million jobs over the next decade, but 2.4 million of these jobs could go unfilled.
2.4 million unfilled positions over the next decade
The National Association of Manufacturers estimates that this labor shortage could result in a loss of $2.4 trillion in GDP.
THE SHORTAGE OF MANUFACTURING LABOR IS DIRECTLY TIED TO A SHORTAGE OF SKILLS.
84%
84% of manufacturing executives agree there is a shortage of skilled workers in their industry.
Manufacturers’ top challenges are: Finding skilled new hires (99%) Upskilling the incoming workforce (92%)
IN-DEMAND SKILLED ROLES: CNC machinists CNC programmers Manufacturing engineers Mechanical engineers Quality engineers Design engineers
49%
49% of respondents say their company has not begun assessing their manufacturing employees’ current skills against skills they will require in the future
54%
54% don’t currently budget for employee development
88%
88% say their company is below average when it comes to offering outside resources to upgrade the skill sets of employees
In order to build a future-proof workforce that’s ready for Industry 4.0, manufacturing and engineering teams need to close the skills gap and change up their hiring process.
CLOSE THE GAP WITH:
APPRENTICESHIPS ONLINE LEARNING HIRING FLEXIBILITY
LEARN MORE AT www.solidprofessor.com/mfg-skills-gap
CONTACT: team@solidprofessor.com +1 (619) 269-8684
Sources: Reliable Plant. U.S. Manufacturing Faces a 2-million Worker Shortage. | PBS. Manufacturers say their worker shortage is getting worse. Here’s why. November 2018. | Tooling U-SME. 2018 Manufacturing Workforce Report. 2018. Deloitte. 2018 Deloitte and The Manufacturing Institute skills gap and future of work study. 2018.
How Should Managers Use Technical Skill Assessments? Technical skill assessments are highly useful for machine shop managers and engineering managers for a number of different applications. They can play a critical role in the hiring process. Managers might require job candidates to complete a CAD or CAM skill assessment to see if their skills match up with the organization’s needs. Or, if managers are trying alternative hiring approaches in order to expand their pool of applicants, skill assessments can be taken after candidates are hired in order to establish a baseline for key skills and then determine the best strategy for on-the-job training.
Uses for skill assessments don’t stop there. Skill assessments are valuable for all employees regardless of experience level or job title. Technical skill gaps are common on engineering design and skilled production teams and can slow down workflows without teams even realizing they exist.
In these instances, managers can use skill assessments to get a quantified view of their team’s proficiency. This makes it much simpler to identify inefficiencies, pitfalls, and hidden skill gaps. This then enables managers to implement training programs to address those skill gaps, saving time and boosting productivity.
22 | IMD APRIL 2020 Plus, skill assessments can be repeated— managers that have their teams take the same skill assessments annually or even quarterly will have the best insight into their employees’ skill improvement and the effectiveness of their training program.
How Should Machinists, Drafters, and Designers Use Technical Skill Assessments? Technical skill assessments are a powerful management tool, but they can be just as useful for professional machinists, drafters, and designers that are looking to prove their software skills or qualify for a new position.
Taking a skill assessment as an individual is a great way to gain an understanding of your technical strengths and weaknesses. For example, if you’re training for an industry-recognized credential or software certification, try a related skill assessment as a form of pre-test. If you’re applying for a new role, especially if you’re an entry-level employee or switching industries, take a skill assessment and see how your skills stack up against the job requirements. When using an online testing tool, your results should make it very clear which areas you need to improve in order to achieve the position you want.
Take the skill assessment again and see how you perform once
you feel confident in your abilities. A high test score on a skill assessment is a great metric to add to your resume. For example, sharing that you received 90 percent on a SOLIDWORKS Advanced assessment is an impressive way to communicate to potential employers that you know how to work efficiently in the software.
The same advantages apply for experienced workers—even if you’re not on the job hunt. Taking a technical skill assessment can give you a confidence boost by proving what you really know. Your results will also help you pinpoint areas where you might be struggling. That way, you can save time by training only on what you really need to learn. And while high scores are great for resumes, they can also be valuable proof points if you’re trying to cinch that next raise or promotion! To learn more Information: Take SolidProfessor’s free SOLIDWORKS skill assessment and get customized training recommendations by visiting www.solidprofessor. com/skills-analyzer. An example of group skill assessment results via SolidProfessor Skills Analyzer

MACHINE TOOL ACCESSORIES, MAINTENANCE SUPPLIES & PARTS
413-323-9041
JHL-35F
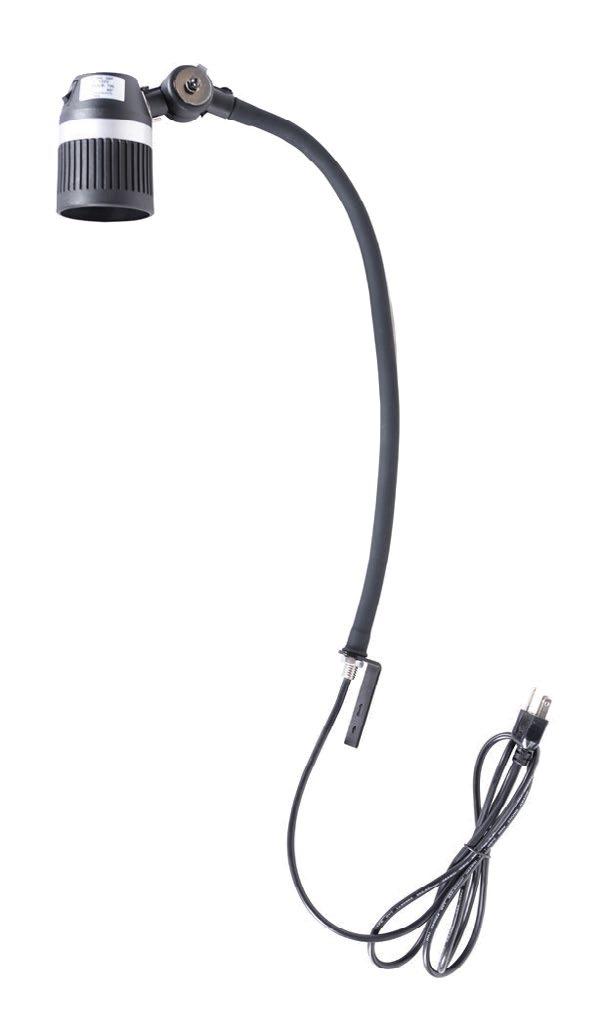
SALE $51
JARRER LED TASK/WORK LIGHT
• 7 watt high quality LED • 770 lumen • Flexible goose neck: 24” • Head permits swiveling to any direction or fixed securely at a position • Comes with a 6 ft. 120V grounded plug cord • LED light for Bridgeport style milling machines, lathes, drill presses and any work bench, etc. JHL-35F-AC120V
• Can be adapted to many other applications • 120 Volts • On/Off switch • Up to 50,000 hours life • Flexible goose neck keeps the light where you need it • Double shade design permits fast heat dissipation • Energy savings
Important Information! It is a very bright LED light for work benches, milling machines, lathes, drill presses, etc.It can also be adapted to fit other machines and applications. Just tap 2 holes anywhere it’s convenient and mount. The LED will be much cooler than Halogens and use less than 1/4 of the electricity.