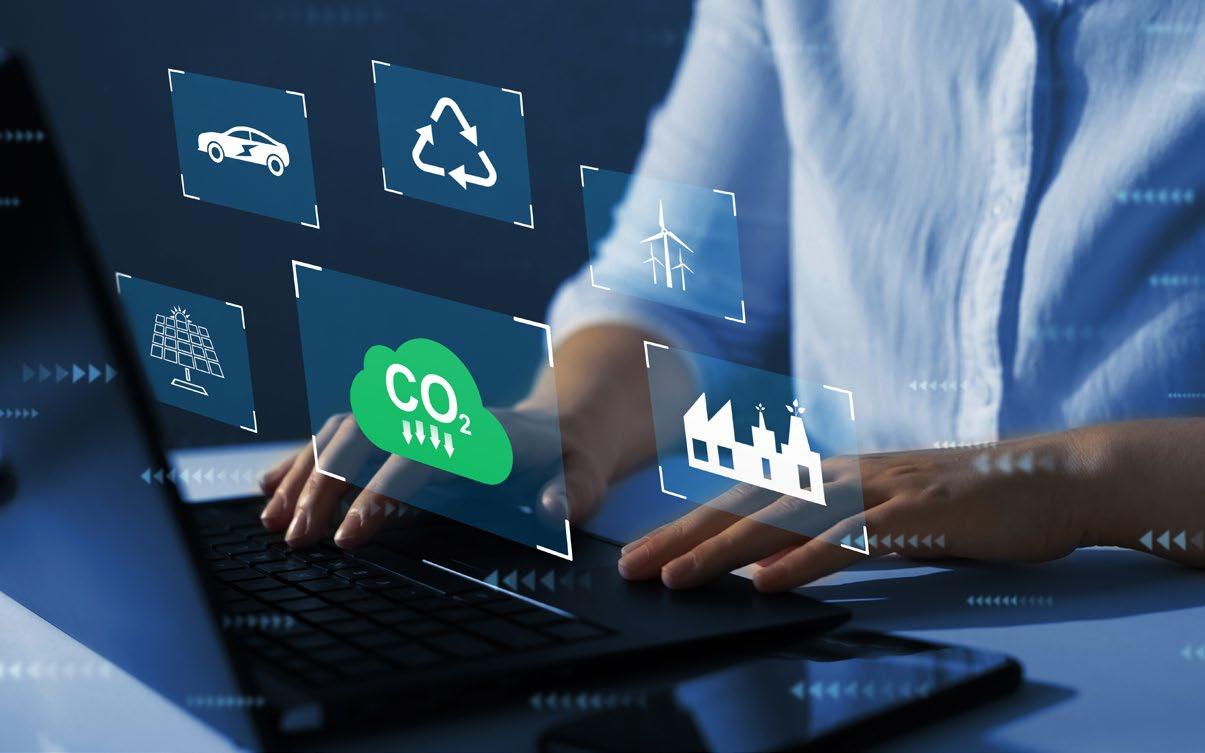
10 minute read
INDUSTrY INSIGHTS
what exactly is sustainable Manufacturing, and How Do we Move forward with it?
By Lori Culpepper
According to the definition given by the U.S. environmental Protection Agency (ePA), sustainable manufacturing is “the creation of manufactured products through economically-sound processes that minimize negative environmental impacts while conserving energy and natural resources.” It also enhances employee, community, and product safety. The ePA says that an increasing number of manufacturers are realizing substantial financial and environmental benefits from sustainable business practices. but how sustainable is it really, why is it necessary, and how practical is it for small-to-medium size manufacturers?
Why Sustainable Manufacturing Is Important
When we talk about environmental impacts, we are referring to several resources, such as energy, material, solids, air, and water. According to the U.S. energy Information Administration’s International energy outlook 2019, the manufacturing sector consumes around 40% of global energy. This is more than 80% of the world’s industrial energy use, making it the largest energy consumer within the sector. more specifically, machining processes such as turning, grinding, milling, and reaming contribute to a significant fraction of this energy use. machining has a large environmental footprint due to energy and resource use since it involves the process of removing or cutting away material. Turning, the removal process of material from a rotating/cylindrical workpiece is the most prevalently used and significant machining technique. It uses a considerably larger amount of energy than other machining operations.
According to Nabil Nasr, associate provost and director of the Golisano Institute for Sustainability at rochester Institute of Technology and Ceo of the remade Institute, experts say that if we continue along the path we’re on, greenhouse gas emission will likely increase by 43% by 2060. but by implementing effective sustainability measures across the globe, we could reduce greenhouse gas emissions by a significant percentage, possibly as much as 90%.
Benefits of Sustainable Manufacturing for Small-toMedium Size Manufacturers and Others
While it may have started with big business, sustainable manufacturing has evolved to include benefits for newer manufacturers, start-ups, and other small-to-medium size companies. These often have more flexible business models and they may rely less on long-established methods or ways of doing things. This allows for opportunities to innovate and change quickly when it comes to sustainable practices.
In fact, a growing number of companies are treating sustainability as an important objective in their strategy and operations to increase growth and global competitiveness, according to the ePA. Companies engaged in sustainability efforts include those of all sizes, ages, and sectors. In many cases, their efforts are having significant results, and they are seeing key benefits such as: » Increasing operational efficiency by reducing costs and waste » responding to or reaching new customers and increasing competitive advantage » Protecting and strengthening sales as well as brand and reputation » building public trust » building long-term business viability and success » responding to regulatory constraints and opportunities » Lowering resource and production costs » Lowering regulatory compliance costs » Increasing access to financing and capital » Finding it easier to hire and retain employees
Disadvantages of Sustainable Manufacturing
one of the biggest considerations that can be difficult, especially for small-to-medium size manufacturers, is the transition to achieve more sustainability. While it should ultimately save the business money, it can cost a significant amount in the short term. The transition typically requires not only the implementation of new manufacturing processes, but also the ability to design and build the technology and machinery needed to support the new sustainable practices. However, in some areas, there may be tax benefits available that can help offset the costs of the transition.
The switch to sustainability can also lead to higher costs in the production process or elsewhere in the facility. A manufacturer who changes suppliers to buy only sustainably made products will likely have to pay a premium price. The higher costs must be passed on to customers or it will mean a smaller profit margin for the manufacturier.
The Way Forward for Sustainable Manufacturing Methods
The ePA says there are several ways in which companies can progress further on the path to sustainability: » Address sustainability in a coordinated, integrated and formal manner, rather than in an ad hoc, unconnected, and informal manner » Focus on increased competitiveness and revenues rather than primarily focusing on cost-cutting, risk reduction, and improved efficiency » Use innovation, scenario planning, and strategic analysis to go beyond compliance » Integrate sustainability across business functions » Focus more on the long term » Work collaboratively with external stakeholders
While Nasr has seen instances where the indicators were there and businesses identified approaches to increase sustainability, manufacturers don’t always follow through with the plans. but because there’s been so much progress in learning about the right path forward, he continues to be optimistic about moving in the right direction for sustainability.
SOURCES:
» https://www.epa.gov/sustainability/sustainable-manufacturing » https://www.eia.gov/outlooks/ieo/pdf/ieo2019.pdf » https://theconversation.com/how-sustainablemanufacturing-could-help-reduce-the-environmentalimpact-of-industry-185672 » https://www.oecd.org/innovation/green/toolkit/ aboutsustainablemanufacturingandthetoolkit.htm » https://smallbusiness.chron.com/advantages-disadvantagesgreen-manufacturing-businesses-22312.html
AGRO-HYTOS
HYDRAULIC PRODUCTS
FILTRATION… The range of filter solutions implemented at Argo-Hytos extends from fixed-position industrial plants to highly mobile applications, primarily tailored to individual customer requirements. As a result of their vast experience with custom applications over a wide variety of sectors, Argo-Hytos offers a comprehensive range of innovation standard solutions: Suction Filters; Return and Return-Suction Filters; Pressure/ High Pressure Filters; Filling and Ventilating Filters; Filter Accessories; Sensor Technology. FLUID AND MOTION CONTROL…
DIRECTIONAL CONTROL VALVES D02/D03/D05/D07/D08: Argo-Hytos DC and dual frequency AC coils can be rotated to locate connectors to your need. DIN, Deutsch Flying Leads and Wire Box Connection are available as standard Manual Override. Full line of Sandwich Controls.
FIVE SERIES OF VALVES RATE TO 5000 PSI: RPE3-04, providing 8.0 GPM; RPE3-06, providing 21.0 GPM; RPE4-10, providing 37.0 GPM; RPE4-16, providing 80.0 GPM; RPE4-25, providing 160.0 GPM GEAR PUMPS: Argo-Hytos gear pumps provide high reliability, high volumetric efficiency, and low noise levels over the entire operating range. THREE SERIES: GP1-P, maximum pressures from 2300-4350 flows 1.0 gpm; GP1-T, maximum pressures from 1700-4200, flows 1.0 to 17.0 gpm; GP1-Q, maximum pressures from 2900-4500, flows 7.1 to 42.8 gpm.
7355 N. Lawndale Ave., PO Box 6, Skokie, IL 60076 PHONE: 847-676-2910 FAX: 847-676-0365
ON EXHIBIT
industrial Machinery Digest's on exhibit features the latest news and press releases from companies exhibiting at the leading trade shows across north america.
WANT TO BE FEATURED? Send your press releases to editorial@indmacdig.com
NOVEMBER 8-10, 2022
Georgia World Congress Center, GA
FAbTeCH provides a convenient ‘one-stop shop’ venue where you can meet with world-class suppliers, see the latest industry products and developments, and find the tools to improve productivity, increase profits and discover new solutions to all of your metal forming, fabricating, welding and finishing needs. www.fabtechexpo.com
Cosen Saws can help find the right cutting solutions for your application at FABTECH 2022.
Cosen Saws is one of the world’s leading band saw manufacturers with a diverse product line and a sales and service network covering all of North America. Cosen’s band saws deliver exceptional quality at a competitive price. Whether you are looking for an everyday saw that can help automate your workflow or just a small band saw to keep in the shop for one off cuts, with Cosen Saws 140+ reliable and dependable options are all configurable to help provide the best cutting solutions possible. Cosen Saws will be exhibiting at booth b8629. During FAbTeCH, Cosen Saws will have a variety of different band saws including manual, vertical, and automatic saws on display. Cosen Saws experts will provide live demonstration on the machines and available to answer any questions you might have on finding your ideal cutting solution no matter the industry.
CINCINNATI at FABTECH 2022: Think It. Design It. Make It., Taking you from the digital part to the physical part
Leading machine tool manufacturer to unveil the industry’s newest cobotic welding technology at the show.
We’re living in a digital world, and CINCINNATI® Incorporated (CI) puts digital innovation on full display at FAbTeCH 2022 (November 8-10, Atlanta, GA). Attendees can visit CI in booth b7909 in Hall b of the Georgia World Congress Center, to explore some of the latest metal fabricating equipment and software solutions – including the industry’s newest cobotic welding technology. Additionally, CI service representatives will be available to discuss the company’s aftermarket options including training, machine upgrades, and more. marketing manager, Nikki Stenzel explained that the event offers a unique opportunity to witness CI’s integrated design to part manufacturing environment.
“With its extensive collection of fabricators, machinery, software, and service providers, FAbTeCH is North America’s premier metal fabrication event. And we’re excited to show the industry what CINCINNATI is all about,” said Stenzel. “Attendees will have an opportunity to see our encompass by CI software suite followed by bending and welding demonstrations as we take a part from 3D design through all phases of manufacturing. Needless to
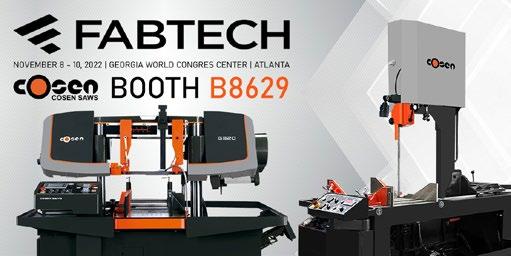
say, anyone looking to enhance shop floor efficiency through automation should make it a point to see what CINCINNATI has to offer.”
Encompass by CI Software
CINCINNATI’s encompass software is dedicated to helping operators tackle projects with greater speed and quality. And today, using digital twins, one moves from the digital part to the physical part accurately and efficiently.
The encompass by CINCINNATI suite includes: » Design: From 3D models, accurately import geometry and identify the correct flat blank. » Nest: Amplify your ability to nest your laser parts with software automation and create optimized machine code to make your Cincinnati laser (and most other lasers) operate at top performance. » bend: Supercharge your offline press brake programming with advanced software automation. » Schedule: Take the stress out of scheduling by automatically scheduling multiple jobs across multiple shifts and multiple CI lasers. » Automate: Advanced software for
robot-tended press brake bending cells. Feature-rich simulation capability ensures collision-free solutions and the generation of efficient programs for both the robot and the press brake. » Analyze: Get real-time and historical insight into the productivity of all your CI machines anywhere, from any device with CIberDash.
Press Brake
Nobody does press brakes like CINCINNATI, and our Autoform line combines precision forming with leading-edge features and control technology. The 60-ton Autoform+ with 6-Axis backgage provides all the benefits of a hydraulic press brake in a smaller footprint and will be our featured press brake at the show.
Cobotic Welding
FAbTeCH attendees will be among the first to experience the industry’s newest cobotic welding technology. A cobot, or collaborative robot, is a robot intended for direct human-robot interaction within a shared space. Simple to use and easy to program, the CINCINNATI Cobotic Welding cell is the first of its kind for TIG welding. With a working range of 2400 mm x 1200 mm (approx. 4’ x 8’) the automated system is suitable for large or small production batches. The cell is compact, easily repositioned, and contains advanced adjustable safety devices including the continuous robot elbow monitoring.
New Line of 1.3 Hp Air Tools from Dynabrade Feature Right Angle Grinders and Sanders New Line of 1.3 Hp Air Tools from Dynabrade Feature Right Angle Grinders and Sanders
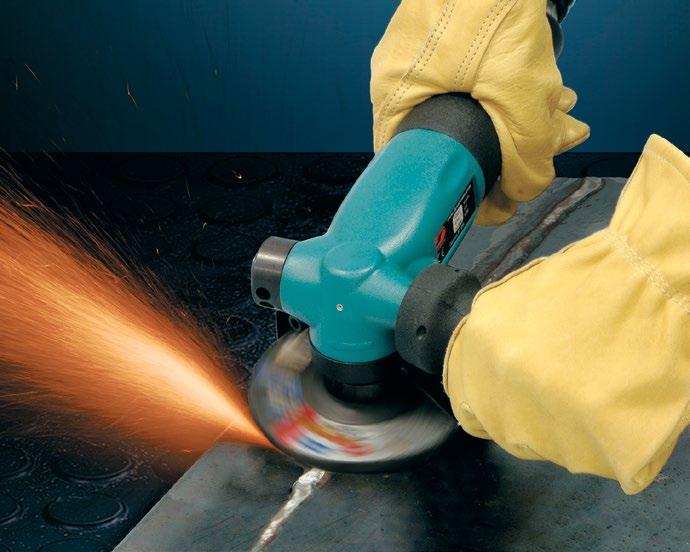
Dynabrade is proud to introduce a new line of 1.3 HP Air tools. These new high quality air tools are available as a rightAngle Disc Sander and a right-Angle Depressed Center Wheel Grinder.
Available in 4”, 4-1/2” and 5” diameters, the tools are excellent for fast stock removal, metal clean up prior to welding, removal of weld beads and various material removal applications. The Depressed Center Wheel Grinder is available in either 12,000 or 13,500 rPm. The grinder is ideal for use with Type 27 Grinding Wheels. The 1.3 Hp Disc Sander, available in 12,000 rPm is for use with a wide variety of coated abrasives.
The tools feature a governor assembly for maintaining rPm under load. Also included is a safety-lock throttle to prevent accidental start-up and a Spindle Lock for fast, easy abrasive/wheel change. A Two-Position Side Handle for left or right-hand use is included. This vibration-dampening handle also reduces vibration to the operator’s hand. This line of air tools was also designed with a Wick Lubrication System, which extends gear life when the tool is properly lubricated with gear oil. Also included is a 360° rotational exhaust for directing the exhaust away from the operator. The Depressed Center Wheel Grinder also includes a safety guard and wheel flange kit. 3/8”-24 and 5/8”-11 spindle models are offered. made in the U.S.A.
ESAB Launches InduSuite: A Brand-Agnostic Workflow Software Portfolio Solution for Robotic, Welding, and Cutting Operations