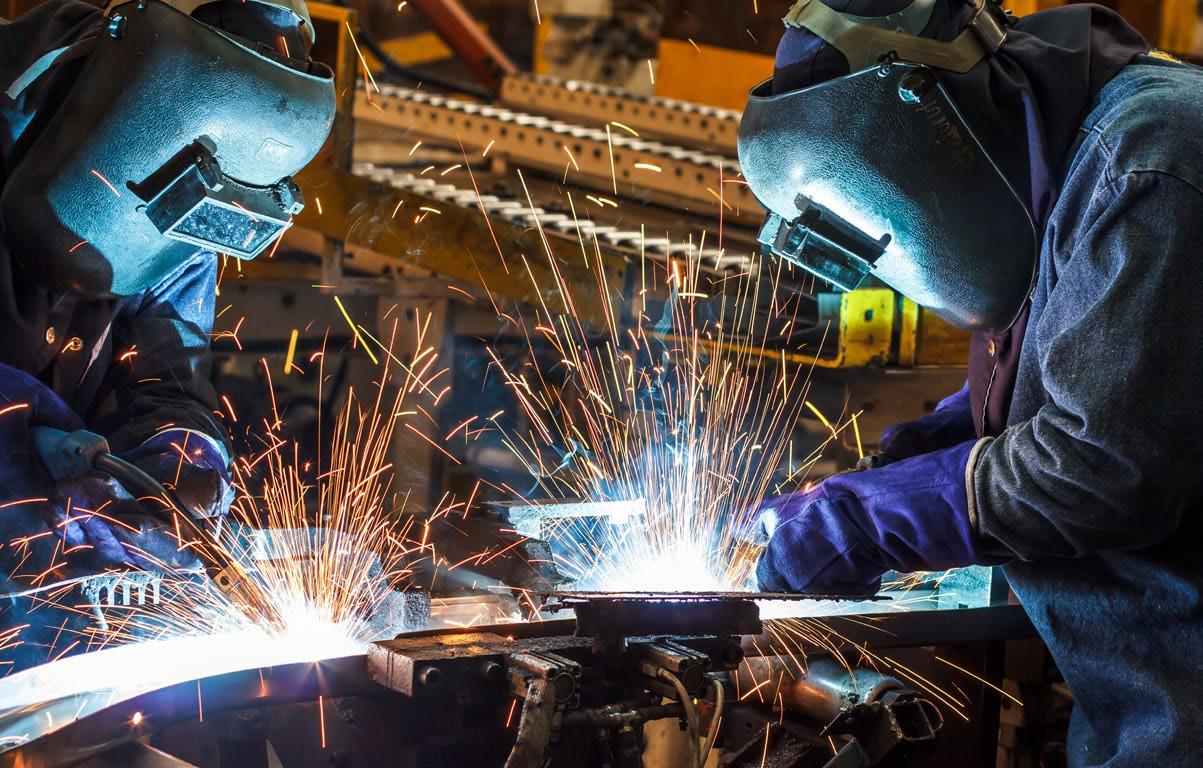
7 minute read
SAFeTY & mAINTeNANCe
Major Safety Issues for the Metalworking and Machining Industry
Common Dangers in the shop and How to keep it safe, starting with strong safety Culture
By Lori Culpepper
Noise and distractions from machines. Welding fumes and chemical emissions. Heavy materials to lift and move. The potential hazards related to the metalworking and machining industry create a long list of major safety concerns. SafeStart has been serving clients with solutions to increase personal safety awareness and skills for 25 years. According to the company, every employee’s reaction in any situation is primarily dependent on the adequacy of their training, company culture, their state of mind, and the safety of the working environment. They say that a company that is not investing in removing or mitigating existing hazards or providing protection against hazards that cannot be removed is failing its workforce. According to optimum Safety management, a company that partners with clients to achieve best practices in workplace safety management, those who manage metal fabrication facilities or other similar manufacturing facilities must have a thorough understanding of the unique industrial safety risks and how to combat them. It’s not optional since workers’ lives and well-being are at stake.
However, with the metalworking and machining industry, it’s difficult to develop elevated standards of safety because the work occurring on the floor is very high-risk. It’s important to know what the major safety issues of the industry are and best practices for dealing with them.
Dangers of Handling Materials and Tools
According to Thomas, a Xometry Company, a data, platform, and technology company that has become a leading resource for the industrial marketplace, material handling is a frequent cause of injury in the workplace. With
metal as the main component of many operations, workers must often lift heavy material. When proper lifting methods are not followed, injuries may occur.
Sustained exposure to vibration, engaging in work that requires awkward posture, and continual repetitive motions can also lead to impairments. excess metal pieces can lead to minor and major cuts or scrapes, and flying shards or sparks can also be hazardous. In welding shops, workers may face the risk of inhaling fumes and other emissions from lubricants or chemicals, which can pose a risk particularly in spaces with inadequate exhaust or poor ventilation.
Inadequate Guards and Other Protective Measures
employee exposure to unguarded or inadequately guarded machines is prevalent in many workplaces, according to the occupational Safety and Health Administration (oSHA). because of this, workers who operate and maintain machinery suffer approximately 18,000 amputations, lacerations, crushing injuries, and abrasions per year; and there are more than 800 deaths each year related to inadequately guarded machines.
Thomas says that access to many areas and equipment should be prohibited in a metal fabrication shop and other types of machining facilities. Guardrails or other barriers should be used to prevent accidental entry. but poorly maintained or non-existent guards are among the most common causes of barrier-related injuries. For example, guarding mechanisms are important in preventing a worker's fingers from entering the metal trapping space of a cutting guillotine. If these safety guards are improperly installed, there is an increased chance of hand injury or finger loss.
According to optimum Safety management, most violations involve the requirements for design and construction. Lockout/Tagout violations are also common, as well as safety violations related to machinery. Some of the most dangerous machinery includes mechanical power presses, mechanical power-transmission apparatus, abrasive wheel machinery, woodworking machinery, and hand and portable power tools and equipment.
Personal protective equipment (PPe) is another important area to consider, and employers should determine what exactly is needed so that each individual employee can safely carry out each task required of them. In the metal fabrication industry, for example, common risks that can be mitigated by protective equipment include metal fume inhalation, airborne silica, molten metals, chemicals, heat, and falling hazards. These hazards may require equipment for respiratory protection, eye and face protection, hand protection, foot protection, and more.
Ultimately, SafeStart says that the working environment must be as free from hazards as possible, and all required guards should be installed and functioning. Guards and PPe should be inspected and checked regularly.
28
Machines for any job or budget • Superior PLATINUM Warranties
Plate Rolls
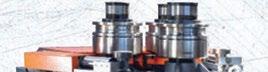
20 Ga to 6” Capacities, 80 Models, 3D CNC Options
Angle Rolls
1” to 10” Capacities, 30 Models, CNC Options
Section Bending Machines
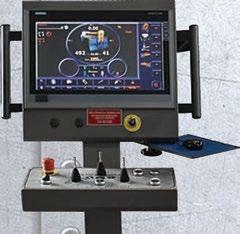
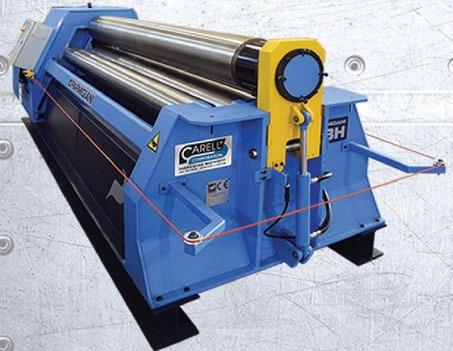
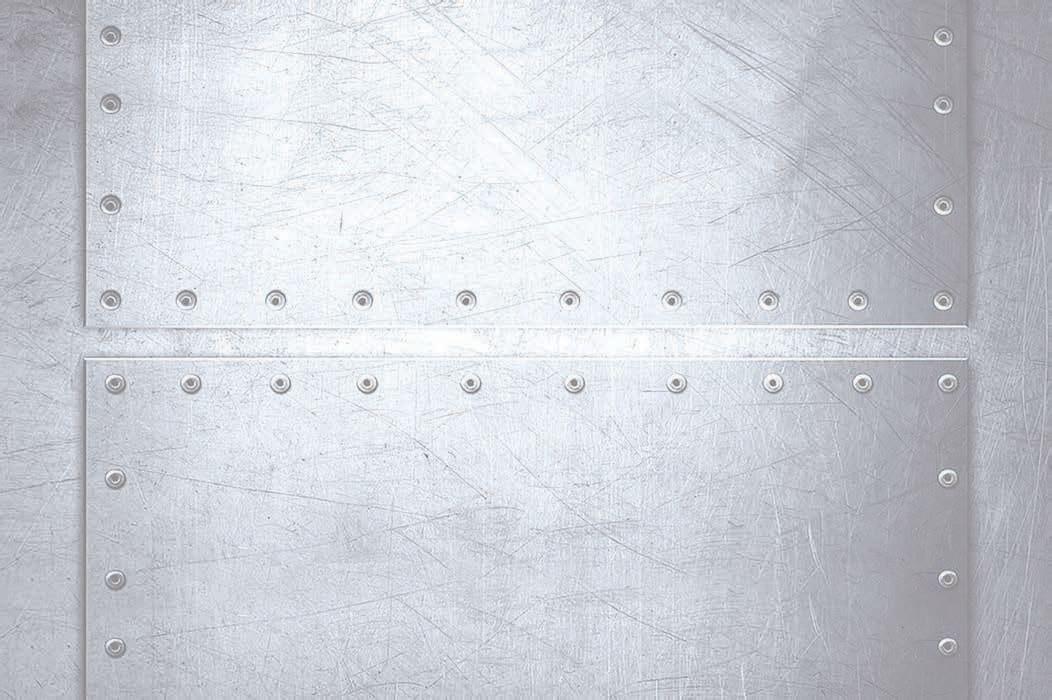

Visit us at Booth B9041 1" to 4" Capacities, 15 Models, Bar Twist, Scroll & CNC Options
MEMBER
November 8-10, 2022 in Atlanta
Visit Us Online or Call: (251) 937-0947 sales@carellcorp.com • www.carellcorp.com sales@eaglebendingmachines.com • www.eaglebendingmachines.com
Thomas says that one reason why metal fabrication can be so hazardous is that there is the potential for inattentiveness due to noise or other distractions. This can result in a loss of concentration, leading to accidents.
Additionally, when employees feel rushed, frustrated, or fatigued, or if they’ve gotten used to taking shortcuts with their work, their chances of sustaining an injury increase substantially, according to SafeStart. The problem often surrounds the fact that a lot of the materials in the metal fabrication industry require manual handling, and the work conditions can be demanding. but when employees exhibit personal awareness of their physical surroundings and they are in a good state of mind, they are less likely to be injured on the job.
Lack of Consistent Training and Focus on Safety Culture
Safety training should start at the beginning of each employee’s time with the company, and they should immediately see a commitment to regular training updates, according to SafeStart. No subject is too small to discuss, but it’s difficult to implement a safety program without having buy-in from everyone at the organization, from those working on the floor to upper management. managers must lead the way by always following safety protocols and attending all safety training sessions. A successful program should instill a sense of accountability in workers and allow for a judgment-free way of addressing employee concerns. The goal is for everyone to understand, accept, and believe in the value of safety practices and standards.
Keeping Your Metalworking or Machining Shop Safe
optimum says that the most effective method of keeping your metal fabrication shop safe is three-pronged: 1. Identification – To make your shop a safe workplace, conduct a thorough safety assessment to identify risks that need prevention. These risks are unique to your shop. 2. Prevention – once you’ve completed your safety assessment, come up with a prevention plan and implement the preventative measures for the risks that need to be addressed. This may work well using procedural steps within each risk area. 3. Safety culture – A transformative safety culture is needed to continually and successfully keep your employees healthy and safe.
Thomas offers additional best practices for the prevention of injuries, including the advice to always adhere to strict safety protocols. managers should also consider the following for workplace safety in metalworking and machining shops: » If appropriate, install adjustable workstations that can accommodate different tasks and employees » Limit or control exposure to harmful materials » ensure that workspaces are uncluttered with a smart layout that reduces contact with dangerous areas or equipment » Pay special attention to personal surroundings and physical exertions required by employees » ensure the proper use of forklifts or cranes to unload heavy raw materials » Have appropriate training regarding effective lifting methods » Use trolleys to transport materials between stages of the fabrication process » make sure ventilation systems work properly and provide PPe as needed » regularly inspect any potentially hazardous piece of machinery to ensure necessary safety measures are in place » Select hand tools based on the suitability of their design » maintain a brightly lit workplace and avoid extreme temperatures in the shop
While the inherent dangers related to the metalworking and machining industry cannot be removed completely, focusing on safety from the shop floor all the way up to management is the best way to prevent injuries, protect workers’ health and safety, and keep your shop running as smoothly and efficiently as possible.
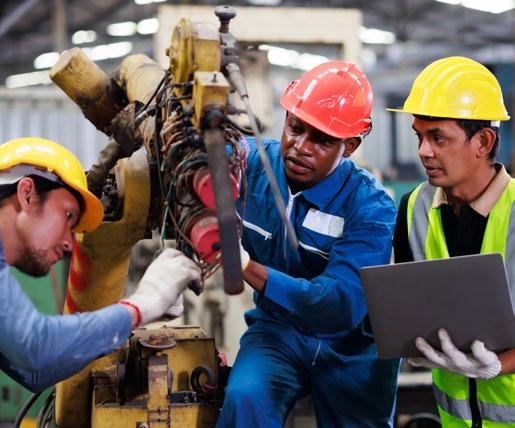
SOURCES:
https://www.optimumsafetymanagement.com/blog/metalfabrication-safety-how-to-keep-the-shop-safe/
https://safestart.com/news/4-major-safety-issues-metalfabrication-industry/
https://www.thomasnet.com/articles/custom-manufacturingfabricating/metal-fabrication-injuries/