
5 minute read
INDUSTRY NEWS
Siemens Named a “Leader” in Industrial Internet-ofThings Software Platforms Q3 2021 Report
Siemens Digital Industries Software announced today that it has been named a “leader” in The Forrester Wave™: Industrial Internet-of-Things Software Platforms, Q3 2021 report. The report researches, analyzes and scores eight vendors against written and quantitative multi-dimensional criteria for Industrial IoT platforms, measuring current offering, strategy, and market presence. Forrester named Siemens as a “Leader”. According to the report, “MindSphere offers a comprehensive array of capabilities to simplify routine monitoring, management, and interaction with connected devices, even at scale. MindSphere is delivered, as a service, from Amazon Web Services (AWS), Azure, and (in China) Alibaba and can also be installed in other environments. Developer support and training are comprehensive and localized, and the vendor offers them in 13 languages.” Siemens received the highest possible scores in the support for digital industrial platform, execution roadmap and average deal size criteria and the highest score in the market presence category.
Tormach Outlines Its Machine Tool Right To Repair Policy
A recently released video on YouTube from Tormach, Inc. has generated a lot of industry buzz concerning the hot topic of ‘Right to Repair’. Tormach’s CEO, Daniel Rogge, talks about the company’s long-time philosophy of allowing customers to service their own Tormach machinery and equipment.
“Clearly this video has touched a nerve not only in the machine tool industry, but in the overall right to repair movement,” said Rogge. “We thought it was important to communicate that it is, and has always been, Tormach’s policy to not only allow owners to service their own equipment, but that we encourage and support this, at no cost to the user beyond replacement parts.”
One example of Tormach’s customer repair policy is, if a Tormach CNC machine requires a spindle replacement, users can buy the spindle directly from the website and replace it themselves, with technical support and documentation readily available from Tormach at no cost. Other machine tool companies not only charge for the part, but also require it be installed by a factory-authorized service person. This service fee typically costs thousands of dollars and in some cases, takes multiple weeks of downtime to schedule the service call. With the ability to repair one’s own machine, users not only save on cost, but can gain flexibility and autonomy in the process.
CONNECT WITH US ONLINE
Visit our website or connect with IMD on social media!
www.IndustrialMachineryDigest.com Mazak’s New MPower On-Demand Learning System Makes Training More Accessible to Manufacturers
As one of the key components within Mazak’s MPower customer support program, the company’s new online MPower On-Demand Learning (MODL) system further enhances training and makes essential courses easily accessible to today’s busy shops. Customers value the ability to improve productivity with in-depth knowledge of all aspects of their Mazak machine tools, but not all shop personnel can travel to in-person classes, and many shops are unable to afford the disruption of production shifts while operators attend off-site training sessions. MPower On-Demand Learning offers online instruction and virtual experiences that provide all the engagement of in-person instruction with the same standards of results. It also enables Mazak to customize its course offerings, and subject matter, to meet customer requests and adapt classes to suit learning levels. This ensures that shops always have access to exactly the right classes that will empower their teams to learn more and do more.
Global Shop Solutions Names John Davis Chief Technology Officer
Davis joined Global Shop Solutions in 2004, and over the past 17 years has served the company in many different capacities including analyst, programmer, and management. Most recently he led the R&D Infrastructure Team, and his excellent programming, networking, and all-around technical knowledge has played a critical role in shaping the company’s ERP software product.
“John has been instrumental in leading Global Shop Solutions technical strategy so our customers can take advantage of the benefits IoT brings to the manufacturing industry,” says Erika Klein, VP of R&D. “As CTO he will define the standards for the technical excellence we hold ourselves to.”
An experienced systems analyst in the computer software industry, Davis combines strong Visual Basic, Object Oriented Design, SQL, Perl, and C++ skills with a background in Computer Resource and Instructional Planning. He received his degree in Interdisciplinary
Studies with an emphasis in Computer Science, Business Information Systems, and Instructional Technology from Utah State University.
Acme Alliance Wins 2021 National Metalworking Reshoring Award
The 2021 award was presented on the FABTECH Main Stage at McCormick Place in Chicago by Harry Moser, Founder and President of the Reshoring Initiative. The award honors companies that have effectively reshored products, parts, or tooling made primarily by metal forming, fabricating, casting, or machining, including additive manufacturing. The award is made possible by the Reshoring Initiative, the Precision Metalforming Association (PMA), The Association For Manufacturing Technology (AMT), and the National Tooling and Machining Association (NTMA). SME generously provided the venue and audiovisual recording.
Mauri Mendes, President of Acme Alliance-Lovejoy Industries, said, “In our business model, we use our worldwide manufacturing footprint to produce and deliver products to the regions where they are assembled [and used] by our customers. We truly believe being close to our customers is the most important strategy. We are seeing many large organizations switching their strategy by reshoring their supply chain.” Matt Thavis, Director of Business Development, and JR Kinnett, General Manager, provided additional insight into Acme’s success.
Acme Alliance was chosen for several reasons, according to Moser. “Acme has a record of reshoring products for their customers. In one case, their reshoring fixed a quality problem and cut the customer’s inventory by 94 percent. Acme also has successful facilities in Brazil and China. By not shipping from those facilities to the U.S., Acme has proven that reshoring is not only possible but the right business choice.”
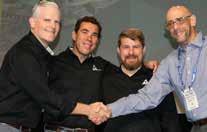
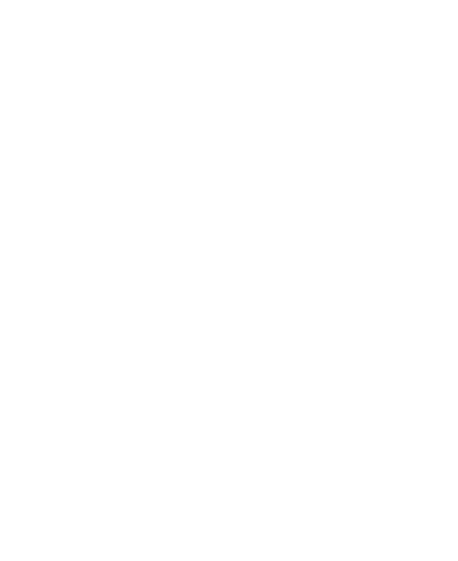

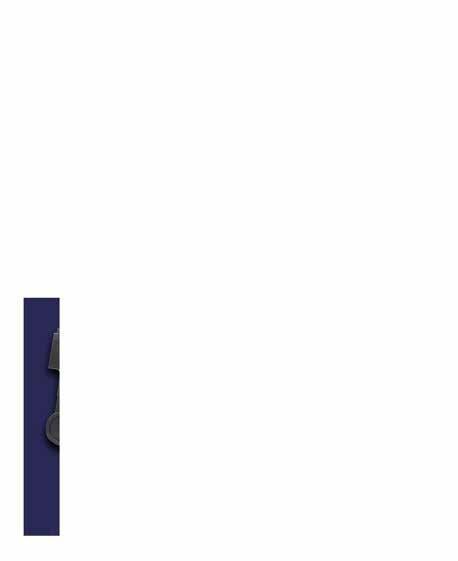
Z P U L L E R E
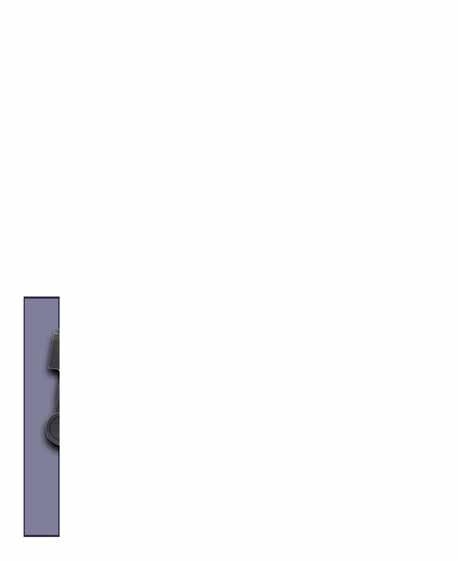
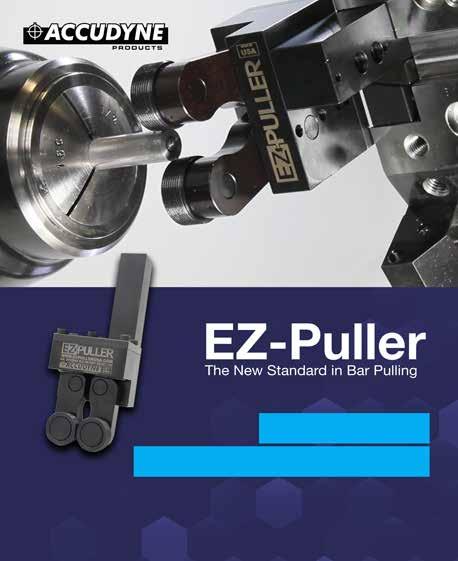
BARPULLING MadeEasyandEfficient
www.accudyneproducts.com Demand for New Vacuum Furnaces Continues at Ipsen
New equipment orders since the beginning of July have come from customers in ten states across the U.S., as well as four other countries—India, Japan, Mexico and Taiwan. Customers will be using the furnaces for processing a range of products including heat exchangers, jet engine components, fasteners and saw blades. Aerospace customers accounted for the majority of sales, but Ipsen also reports an increase in orders from emerging industries focused on electric vehicle production and additive manufacturing.
Many of these are long-standing customers who continue to purchase Ipsen equipment for the reliable service, quality products and technical expertise. Other customers cite process flexibility, turnkey solutions and adherence to industry standards as reasons for purchasing from Ipsen for the first time.
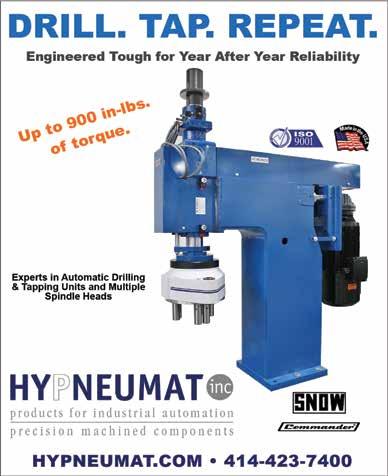