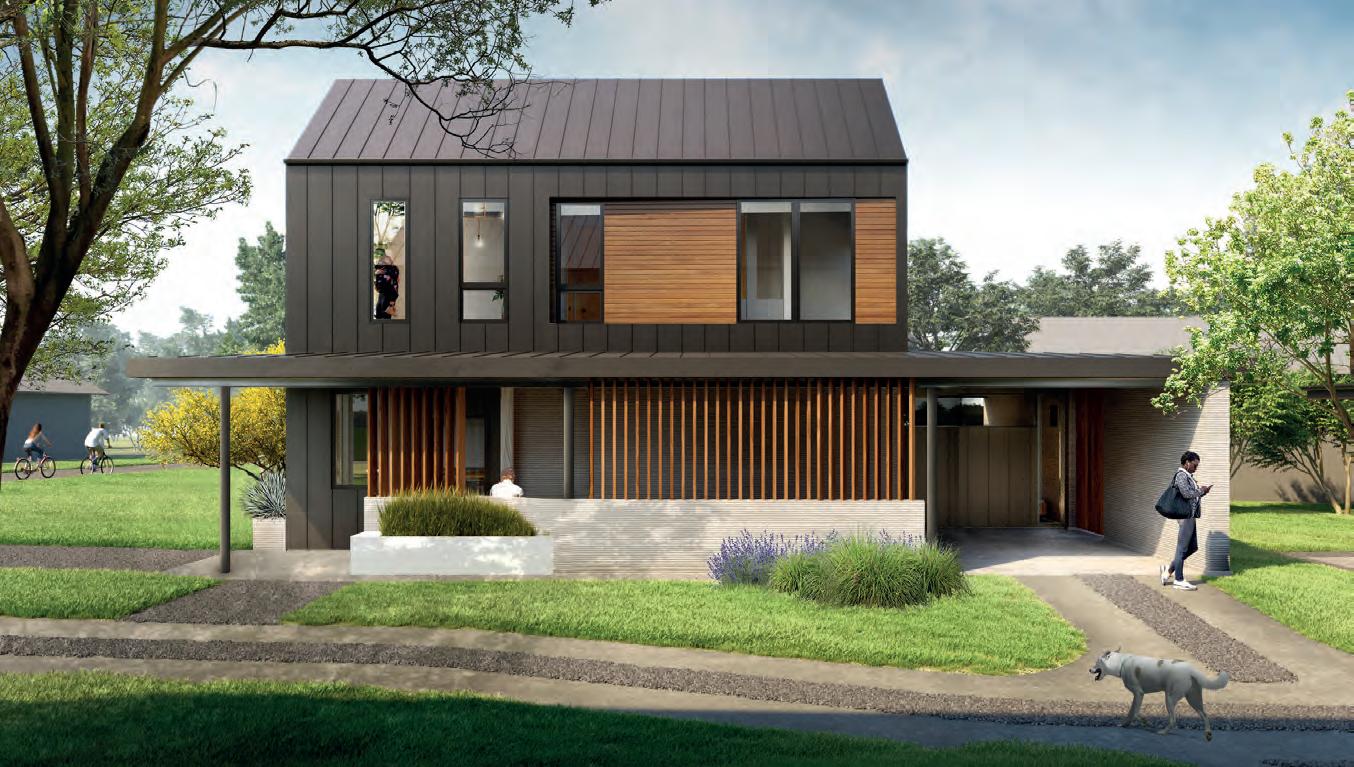
4 minute read
East 17th St Residences
Photo: © Logan Architecture
A multi-home mainstream housing development, designed by Logan Architecture for developer 3Strands, leverages ICON’s proprietary 3D printing technology to construct two to four bedroom homes in Austin, Texas. This is America’s first series of 3D-printed sustainable homes for sale.
Advertisement
The Kansas City developer, 3Strands, announced that the next evolution of homebuilding has launched with the company’s first multi-home project: America’s first 3D printed homes for sale.
Partnering with Austin-based construction technology company, ICON, the 3Strands mainstream housing development leverages ICON’s proprietary 3D printing construction technology, software and advanced materials to deliver the two to four bedroom homes located in Austin, Texas, one of the fastest-growing cities in America.
“We want to change the way we build, own and how we live in community together,” said Gary O’Dell, Co-founder and CEO. “This project represents a big step forward, pushing the boundaries of new technologies, such as 3D-printed homes.”
The one-of-a-kind homes designed by Logan Architecture for developer, 3Strands, are the latest homebuilding project using ICON’s Vulcan construction system to deliver sustainable, resilient and beautiful housing. The first floor of these highly energy efficient homes were 3D printed using ICON’s advanced material that is stronger and longer-lasting than traditional building materials. 3D printing
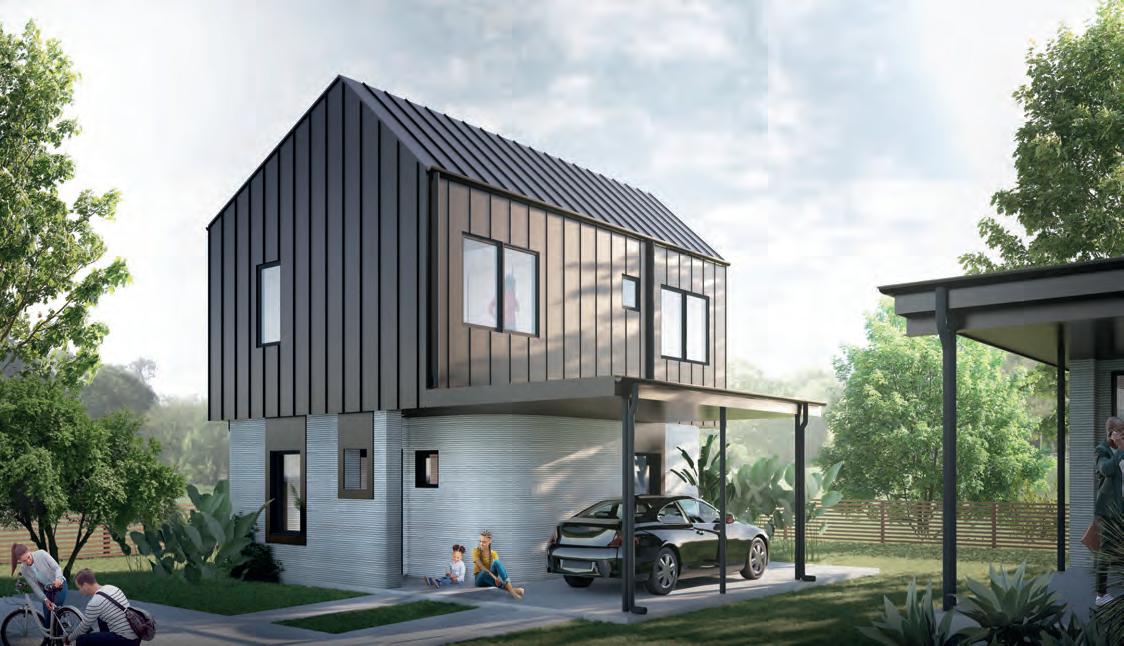
Photo: © Logan Architecture
technology provides safer, more resilient homes that are designed to withstand fire, flood, wind and other natural disasters better than conventionally built homes and that can be built in a matter of weeks. To date, ICON has delivered two dozen 3D-printed homes across central Texas and in Mexico and this marks the first mainstream housing project for the startup.
“ICON has delivered better homes at a better value across a variety of cost-centers than conventional construction, including materials, time to market, and labour,” continued O’Dell. “The East 17th St Residences represent the future of homebuilding for the mass market and illustrate what is possible with this technology.”
“We were delighted when 3Strands approached ICON to deliver their first mainstream housing development,” said Jason Ballard, co-founder and CEO of ICON.
“There is an extreme lack of housing that has left us with problems around supply, sustainability, resiliency, affordability and design options. With ICON’s 3D printing technology, we anticipate more high-velocity progress in the years ahead to help bring housing and construction into the modern world and in-line with humanity’s highest hopes.”
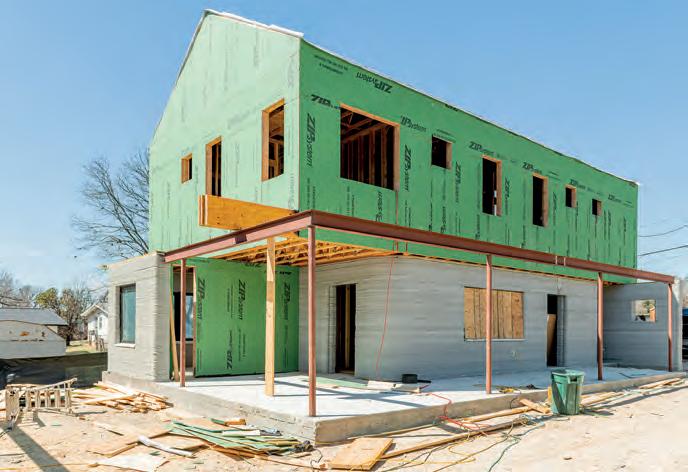

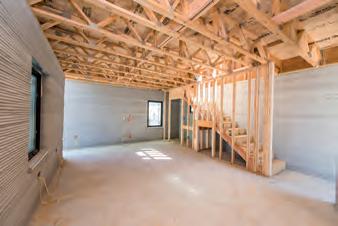
Photos: © ICON
Nestled in the fast-growing East Austin neighborhood, the homes feature large covered front porches, extensive front yards, covered parking, open concept floor plans, bespoke interior design, vaulted master bedrooms, large Northfacing windows, high performance HVAC, secluded office/bedrooms, and minimalist architectural aesthetic.
Each of the four homes took about 5-7 days of printing – that is less than a week per home for the print portion only. The resilient material used to 3D-print the homes is a proprietary cementitious material called Lavacrete and is more durable than traditional construction materials.
A ustin-based designer Claire Zinnecker joined the project to design the interiors’ finishes and fixture selection. Her approach for these spaces was a modernized West Texas design with a simplified palette featuring natural woods, similar metal finishes and earthy tile colours.
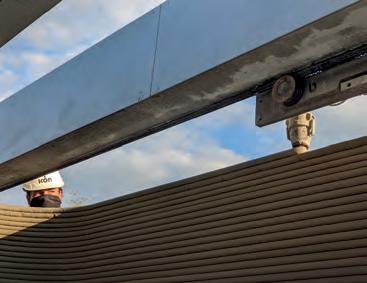
Photos: © ICON
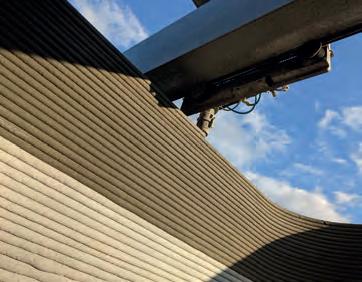
PROJECT DATA
Project Name: East 17th St Residences Location: Austin, Texas, USA Type: Two- to four-bedroom, 1,000 – 2,000 square feet homes Developer: 3STRANDS Architectural Firm: Logan Architecture 3D Printing Construction Technology: ICON Completion: 2021
Interview with Andrew Logan, AIA, Principal, Logan Architecture, PLLC
SEAB: Give us a brief overview of the East 17th St Residences project.
ANDREW: East 17th is the first market rate 3D printed project in the US. We worked closely with the developer (3Strands) and ICON to create a project that would highlight ICON’s technology and have mass appeal to the average home buyer in Austin.
SEAB: Compared to conventional construction, what advantages did 3D printing technology offer to this project?
ANDREW: 3D printing offers endless flexibility in plan and on this project, it allowed us to have radiused walls to soften the building base corners and allow the building to respond to user circulation within the site and within each building.
SEAB: What were some of the issues and limitations that you faced when using 3D printing technology for this project?
ANDREW: The most common challenge we face with 3D printing in Austin is the added wall thickness required for insulation and proper structural support. This added thickness must be counted as a part of our buildable area per city code, and thus reduces the size of buildings that an individual site might be able to yield.
SEAB: How closely did you work with the 3D concrete printer specialist to realise this project?
ANDREW: Very closely. The design of these buildings was a highly iterative process with ICON.
SEAB: In your opinion, what kind of future do you see for 3D printed buildings?
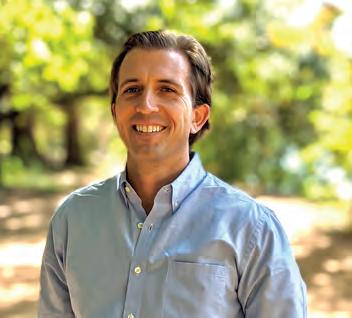
Andrew Logan. Photo: © Logan Architecture
ANDREW: Eventually, I think 3D printed concrete and other mineral based printing will replace all other methods of masonry construction that are commonly used today.