
10 minute read
Be Aware Safety Tips
Will OSHA Be Obama 2.0?
By Laura Helmrich-Rhodes, CSP, Ed.D.
It is no secret that the Democrats are considered more worker/ union friendly, and prefer regulations and citations over offering more employer compliance assistance. President Biden has been quoted as saying he will be the “strongest labor president.” As administrations change, one must wonder what the next era of the Occupational Safety and Health Administration (OSHA) will look like; specifically, what will be the inspection priorities and where will budget dollars be spent compared to a more conservative approach?
Top-Down Approach
The Trump administration did not nominate an assistant secretary of labor for OSHA during his term of office, relying instead on political appointments. Lauren Sweatt continued operations and stepped down in January.
As this article was being completed, it was announced that James Frederick, a former environmental health and safety (EHS) technical advisor for the United Steelworkers (USW), would become deputy assistant secretary at OSHA. Frederick will likely work under Marty Walsh, President Biden’s nominee for secretary of labor, who worked closely with MassOSH, labor unions and community groups and is a card-carrying union member from his younger days as a laborer (Industrial Safety and Hygiene News magazine, Jan. 14, 2021). Walsh is a past labor union president and a supporter of the “Protecting the Right to Organize Act,” a bill introduced by congressional Democrats in 2019 and reintroduced in February 2021.
An interesting twist, and an expansion of government operations, is an additional OSHA administrative role created during the first days of the Biden Administration. The “OSHA COVID-19 Advisory Board” includes Dr. David Michaels, former assistant secretary of labor for OSHA during the Obama administration. A highly educated epidemiologist with OSHA experience, Dr. Michaels is well qualified to fill this add-on to the bureaucracy.
Increased Regulatory Oversight?
Typically, when the administrations flip to a more liberal president, there is a call for the emphasis on increasing the number of regulations and employing more compliance officers. (Do you recall President Trump’s emphasis on eliminating two regulations for every one passed?) Such is the rallying cry in 2021 as well as increased OSHA regulations and enforcement.
What remains to be seen, at the writing of this article, is if there will be an OSHA Emergency Temporary Standard (ETS) for COVID-19 protections. Surely, with the addition of Dr. Michaels, it will happen quickly. EHS Daily Advisor predicts there “will be a National Emphasis Program (NEP) with increased whistleblower protection, and regulation by shaming.” That translates to OSHA media drawing widespread attention to serious/repeat violators.
OSHA has levied citations and issued large fines against employers for COVID-19 protection violations. Those initial actions have been well published in the media; however, the court cases or the success/failure of those cases have not been well published. Furthermore, most of those cited have been health care related and meatpacking entities. For OSHA to be more likely to prevail in court, a specific standard would serve them better than stretching current requirements (for example, a written respiratory protection program) or using the General Duty Clause of the Act to cite employers. Several U.S. senators have said the fines that have been issued have not been high enough and will not have an impact on protecting workers.
On that note, increased penalties were announced and went into effect Jan. 16, 2021. The maximum penalty for serious and other-than-serious violations is now $13,653 per violation, up from $13,494. The maximum penalty for a willful or repeat violation is now $136,532 per violation, up from $134,937. It is reported that penalties have risen 80 percent since 2016. Other changes include an increased effort to collect fines.
What to Expect with COVID and OSHA Compliance
Per OSHA, under certain limited conditions, the agency is authorized to set Emergency Temporary Standards (ETS) that take effect immediately and are in effect until superseded by a permanent standard. OSHA must determine that workers are in grave danger due to exposure to toxic substances or agents determined to be toxic or physically harmful or to new hazards, and that an emergency standard is needed to protect them. OSHA then publishes the ETS in the Federal Register, where it also serves as a proposed permanent standard. It is then subject to the usual
Laura Helmrich-Rhodes, CSP, Ed.D., is an independent regulations compliance consultant to the Spring Manufacturers Institute (SMI). A former member of PA/OSHA Consultation, she is an associate professor in the Safety Sciences Department at Indiana University of Pennsylvania where she teaches graduate and undergraduate classes on topics such as OSHA standards, safety communications, workers’ compensation and human relations. Rhodes is available for safety advice and information. Contact SMI at 630-495-8588 or laurahrhodes@gmail.com.
procedure for adopting a permanent standard, except that a final ruling should be made within six months. The validity of an ETS may be challenged in an appropriate U.S. Court of Appeals.
Perhaps a COVID-19 Protection ETS will be pushed through, forcing all employers covered by OSHA regulations to formalize protocols (remember, the term 'employer' has very broad coverage, ranging from low hazard employers such as real estate offices, up to private space exploration with many hazards!) with more specific requirements than are already in place for respiratory protection, personal protective equipment, infectious material, etc. Major corporations with robust safety programs probably won’t blink, but this will be particularly difficult for small employers to comply with the documentation requirements.
In the meantime, the best strategy is to look to the published federal “OSHA Guidance for COVID-19” and to the OSHA state plan states which have already enacted full regulations. Decide if your organization has addressed these items and areas where you need to improve. Several states have helpful websites that can be used as a framework for formal programs and even some sample employee training programs (see “My OSHA COVID-19 Compliance Check Up” on page 16).
Some may find of interest that the EHS Daily Advisor (Jan. 11, 2021) reported that California’s ETS was being challenged in a lawsuit filed by several employers. That outcome will be both informative to our readers and influential on a federal standard.
Will the Number of Compliance Officers Increase?
There is no doubt there is a need for more inspectors. The number of federal compliance officers has dwindled during the previous administrations to less than 800 in the field, and there are still highly hazardous operations, especially construction sites where workers are dying daily. A solid understanding of what injuries are occurring has still not evolved despite changes in recordkeeping.
The hiring of compliance officers to increase inspections will be the easy part for OSHA (though as of this writing, there are no posted openings for Federal OSHA compliance officers). They will find many qualified candidates; however, the normal extensive training needed before their deployment as officers will take some time, and likely more time than usual, due to COVID-limiting training opportunities for new inspectors. Inspectors are highly trained in not only the OSHA standards, but also policies and procedures such as investigating catastrophes, taking photos, preserving evidence, interviewing techniques, dealing with grieving families and exactly how to make a citation hold up in court, to name just a few topics!
The previous Democratic administration created the online, check the box, formal complaint form that significantly increased the obligations for compliance officers. This was a sudden change from the written, signed and mailed formal complaint letter. When you add the new electronic reporting of amputations,
loss of eye and hospitalization of one employee (versus three in a single incident) as triggers for on-site inspections, you can see that the current staff will be very busy.
Further complicating the matter is the protection of their own OSHA employees from contracting the virus. According to Safety and Health, a publication of the National Safety Council, the U.S. Department of Labor Office of the Inspector General is to conduct an audit of the protection of OSHA inspectors’ health during the pandemic.
Piling on the workload with the inclusion of increased whistleblower protection may slow the inspection process, too. Many citizens are unaware that OSHA handles twenty-some agencies’ whistleblower complaint investigations, in addition to workplace hazards. Some safety news outlets predict that the anti-retaliation protections will increase in the pandemic/infectious disease era, thus further increasing the OSHA office workload.
Expected Priorities
Historically, OSHA’s top priority for inspection is an “imminent danger,” a situation where workers face an immediate risk of death or serious physical harm. An example would be the report of workers in a trench without shoring, or on a roof without fall protection. A second priority goes to any fatality or “catastrophe,” which is an accident that requires hospitalization of one or more workers.
A third priority is employee complaints and referrals from other agencies. Lower inspection priorities include inspections targeted toward high hazard industries (National Emphasis Programs), planned inspections in other industries and, finally, follow-up inspections to determine whether previously cited violations have been abated. One can see that the lowest priority is the “follow-up;” however that may change under the Biden administration.
An annual report of OSHA and MSHA operations published in November called for “attention to confirming that abatement of hazards had occurred” (which translates to more follow-up inspections to check hazard correction/ abatement) and to “improve employer reporting of severe injury and illnesses” (which translates to increased emphasis on the prompt and correct recordkeeping/reporting of injuries and illnesses).
EHS Daily also predicts the following: Advancement of the Protecting America’s Worker Act, a legislative act reforming OSHA that would, among other things, increase civil penalties, expand the circumstances that would result in criminal charges for egregious workplace safety failures, and expand the rights of workers and survivors and their involvement in workplace safety cases.
OSHA's published Unified Regulatory Agenda has not been updated, but a labor driven group is getting press regarding their own agenda. The National Council for Occupational Safety and Health (COSH) has listed 1) Increased enforcement, 2) Strengthened anti-retaliation protections, 3) Increased worker participation, to name a few. The OSHA agenda continues to include items such
Stock Springs
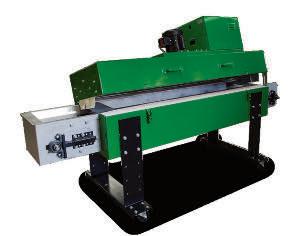
To Ship
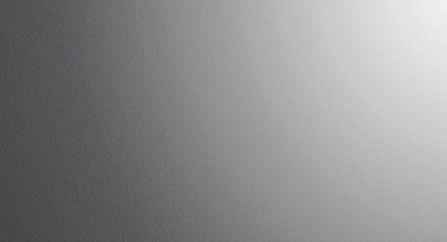
Your complete source for all your stock and custom spring needs
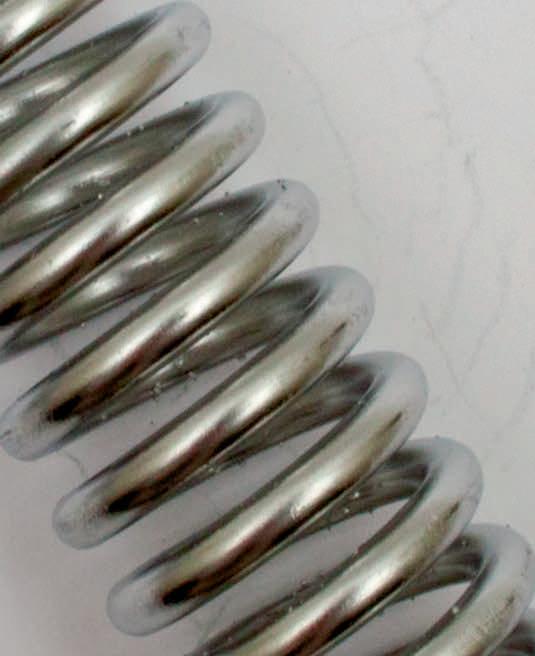
Ready Compression Springs Extension Springs Die Springs Torsion Springs
www.DiamondWire.com
1-800-424-0500
MADE IN USA
JN Machinery
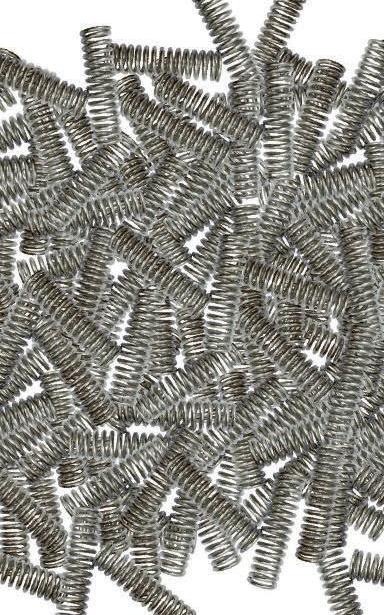
We’ve Got Stress Relieving Down to a Science!
JN-1060
Save space, time, money and improve quality with the efficiency of a JN Machinery oven! We can put our experience to work in your operation with an oven to fit your needs.
www.jnmachinery.com | 224.699.9161
TRC Coatings, a division of JN Machinery is now the leading coatings supplier to the spring industry, delivering systems and paint material ideal for corrosion protection and color-coding springs.
as lockout/tagout for modern machines, forklift design per ANSI, silica exposure prevention/ protection, and reducing beryllium exposures. For more information and to stay updated go to https:// www.osha.gov/laws-regs/unifiedagenda/ currentagenda
Conclusions
Under the current administration, employers need to be ready for a much higher likelihood of OSHA inspections, a greater emphasis on worker health and safety and an expanded reach of OSHA. It will take time to get new OSHA workforce addons ready, so employers should take this lag time as an opportunity to make sure all paperwork and mandated training programs have been completed/documented and increase diligence in all areas of safety and emergency preparedness. (See “Quick Pre-Inspection Check Up” below.) Will it be Obama 2.0? No, likely much more than we have seen in decades. n

OSHA Guidance Document Published February 2021
https://www.osha.gov/coronavirus/safework
CDC Guidance for Manufacturing
https://www.cdc.gov/coronavirus/2019-ncov/ community/guidance-manufacturing-workersemployers.html
Mask Selection and Employee Training Completed for COVID-19
https://www.lni.wa.gov/safety-health/ safety-topics/topics/coronavirus
Hazard Assessment Completed
https://www.osha.gov/coronavirus/hazards
Implemented Hierarchy of Controls per OSHA
• Eliminating the hazard by separating and sending home infected or potentially infected people from the workplace; • Implementing physical distancing in all communal work areas [includes remote work and telework]; • Installing barriers where physical distancing cannot be maintained; • Suppressing the spread of the hazard using face coverings; • Improving ventilation; • Using applicable PPE to protect workers from exposure; • Providing the supplies necessary for good hygiene practices; and • Performing routine cleaning and disinfection.
Quick Pre-Inspection Check Up
• Injury/illness records up to date and posted? • All mandated OSHA safety training up to date? • Lockout/tagout program and procedures up to date? • Hazard Communication Program up to date? • Forklift certified operators up to date? • Respiratory protection program up to date? • COVID protocols, per OSHA guidance, in place and documented? • Machine guards in place and enforced? • Electrical wiring appropriate and suitable for environment? • Emergency Action Plan up to date?