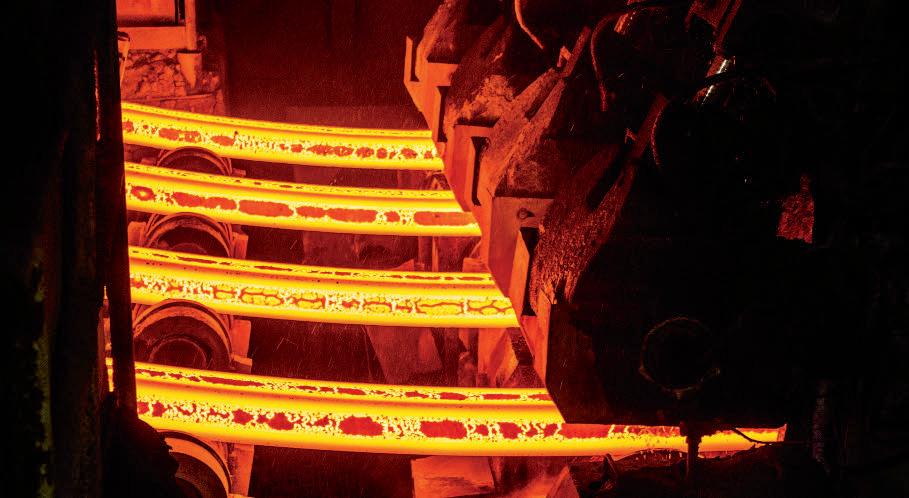
5 minute read
Advances in Springmaking Materials
By C. Richard Gordon
(Editor’s note: Rick Gordon’s article was developed as part of the overall theme of “Advances in Springmaking.” With so many developments to discuss, this is the first of several articles to come in future issues of Springs. Gordon will also discuss these advances as a part of his presentations during the 2021 SMI Metal Engineering eXpo.)
Advances in the production of springmaking materials over time have resulted in improvements in spring performance. Since the majority of springs are produced from carbon and alloy steels, production methods of these materials will be described here.
Production improvements have occurred in the areas of steelmaking, continuous casting, rod rolling, wire drawing and wire processing. Improvements in springmaking machine technology will be treated separately.
One important performance characteristic for springs subjected to cyclic loading is fatigue life. As the SMI technical committee looked at available spring fatigue data, it was discovered that spring fatigue data available from ASM International was developed prior to the publication of their “Metals Handbook, 8th edition” in 1961. More recent data was published by the Society of Automotive Engineers (SAE) in their 1997 publication, “Manual on Design and Application of Helical and Spiral Springs (HS-795).” The SAE manual data is included in the Advanced Spring Design software (ASD7).
These advances in springmaking materials motivated the SMI technical committee to explore the potential impact/improvements to historical fatigue life, assumptions that were based on decades-old wire production practices. This project is currently underway.
The improvements in steelmaking, rod rolling, wire drawing and wire processing technology will be briefly described below and are planned to be presented in detail in two technical sessions at the the 2021 SMI Metal Engineering eXpo in September.
Steelmaking and Continuous Casting
Improvements in steel manufacturing processes have yielded advancements in the purity of steel for higher-quality end-use products such as springs. Clean steel is produced by judiciously controlling parameters in melting, refining, degassing and casting operations.
As we look at the steel production process, there are two primary production methods used today: the integrated steelmaking process and the minimill process.
In the integrated steelmaking process, molten iron produced in a blast furnace is refined in an oxygen steel making furnace to produce steel. A typical furnace charge is 85 percent blast furnace iron and 15 percent scrap. The quality of the scrap is an important factor in the quality level of the steel being produced. Steel produced using the integrated steelmaking process can have very low levels of residual elements, which is desirable for high quality materials used to produce springs.
In the minimill process, steel is produced in an electric arc furnace where 100 percent steel scrap and scrap substitutes, such as direct reduced iron (DRI) pellets or briquettes, hot briquette iron (HBI), or pig iron, are melted. Scrap used in both processes is available in different quality levels, where residual elements such as copper, nickel, chromium and molybdenum vary by scrap type.
Historically, steel produced using the integrated process was preferred for high quality grades due to the low residual element composition (copper,
nickel, chromium) and low nitrogen levels produced. Minimills have been successful in producing high-quality spring grades by increasing the quantity of high-quality low residual scrap and scrap substitutes. In addition, improvements in slag practices and pouring techniques have enabled the production of steels with lower nitrogen levels.
Once the steel is refined in the furnace and the temperature and chemistry are determined, the batch or heat is poured or tapped into a ladle where materials are added to arrive at the desired end point chemical composition. In the past, steel was then poured into ingots or sent directly to the continuous caster. Sequencing of continuously cast heats was challenging at times, due to temperature variation. Today, the use of the ladle arc furnace has made it possible to produce over 90 percent of steel using continuous casting. A key process improvement making this possible for both types of steelmaking processes was the ladle arc furnace.
Often thought of as a secondary steelmaking process, ladle arc furnaces were installed between the primary melting furnace and the continuous caster. The ladle arc furnace includes electrodes for heating (temperature control), argon stirring via a porous plug for flotation of inclusions, alloy additions for fine tuning chemical composition, deoxidation and desulfurization capability.
In addition, some producers have installed vacuum degassing equipment for the removal of hydrogen, nitrogen and oxygen for production of the highest quality level products.
Also, at the continuous caster, improvements have been made to prevent reoxidation of the molten steel through the use of ceramic tubes between the ladle and the tundish and the tundish and the mold (ceramic entry nozzle pouring). Electromagnetic stirring in the mold is used to improve surface and internal structure and to minimize chemical segregation in the cast section, whether it be a bloom or billet. Some producers have installed additional electromagnetic stirring units below the mold to further improve uniformity of the cast section. These improvements in steel manufacturing processes in combination with advancements in the science of steel evaluation have resulted in significantly improved steel quality. The quality improvements include chemical composition uniformity, resulting in improved property uniformity and improved refining methods which raise the purity of steel. This high level of purity is what the industry refers to as clean steel. Clean steels contain limited nonmetallic inclusions in terms of size, shape, composition, distribution and frequency. As a result, clean steels are capable of outperforming other materials and excel in spring products. n
C. Richard (Rick) Gordon serves as SMI’s technical director. He has more than 45 years of experience in the steel and wire industries. You can contact him at: c.richard.gordon@gmail.com.
Mapes: quality that’s quality that’s never out of tune. never out of tune.
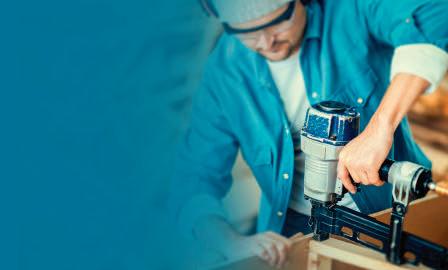
Choose Mapes Fine Music Choose Mapes Fine Music Wire for consistent quality. Wire for consistent quality. The high-performance wire high-performance wire for your demanding spring jobs. demanding spring jobs.
MAPES FINE MUSIC WIRE MAPES FINE MUSIC WIRE
Call for special wire needs and solutions, including restricted tensiles and size tolerances.
Wire diameter .063" – .006" / 1.6 mm – .15 mm
Coatings Phosphate, Tin Zinc, Tin Industry standards ASTM A228-18 JISG 3521 SWA, SWB ASTM A227-17 JISG 3522 SWPA, SWPB EN10270-1 Military specifications AMS 5112N Others, inquire
THE MAPES PIANO STRING COMPANY
P.O. BOX 700, ELIZABETHTON, TENNESSEE 37644 423-543-3195 • FAX 423-543-7738 www.mapeswire.com • info@mapeswire.com
ISO 9001:2015
certified QMS Your Preferred Supplier of Custom Springs from Design to Production
Beyond the Spring™
Helping you bring your industrial application or POP display to life
With innovative machinery, tooling and engineers, Vulcan Spring can deliver a spring solution for even the most challenging applications.
Contact us with questions or about a custom spring need today.
+1-215-721-1721 | VulcanSpring.com