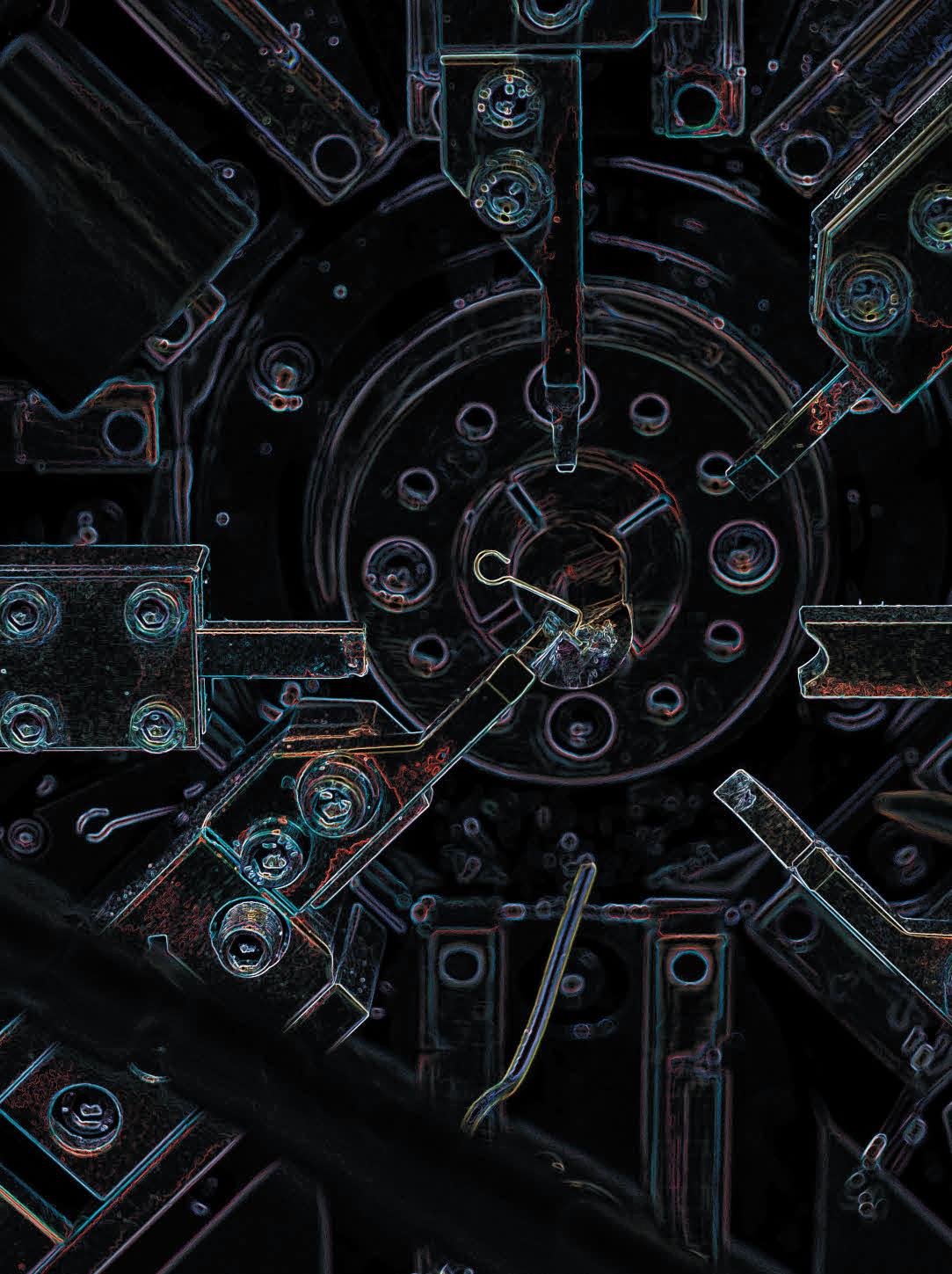
10 minute read
Advances in Springmaking
by Gary McCoy
Looking back on advancements in the spring industry over the past 50 years, it is not an overstatement to brand it as “revolutionary,” especially with machinery improvements dominating the landscape.
In the last two decades, advancements have primarily centered around digital technology, both in the office and on the shop floor. This article explores some of the changes that have taken place to advance the spring industry forward.
Articles that are also part of the advancement theme includes a focus on the area of robotics. You can read more about “Collaborative Robots on The Rise” on page 27. You will also find "Five Manaufacturing Trends to Watch" on page 32, that offers a glimpse of broader manufacturing trends that may impact springmakers.
On the materials side, C. Richard Gordon looks at “Advancements in Springmaking Materials” on page 30.
Finally, our Flashback article on page 35 is a reprint of a President’s Message from A. H. “Pete” Peterson, SMI president from 1993-1995, from the Oct. 1994 issue of Springs. Peterson makes the convincing argument that management techniques should be considered in any discussion of technology breakthroughs. This area is not covered in this issue of Springs, but it is a point worth pondering in any discussion about advancements.
Historical Perspective
Dan Sebastian, (aka “The Dean of Springs”) was a student intern at Associated Spring in the summers of 1968 and 1969, as he worked toward earning a degree in metallurgy and material science at Lehigh University. After graduation in February 1970, he started working full time for the company.
Sebastian, a former SMI president and current technical consultant to the association, remembers when the Barnes Group bought its first mainframe computer with a scientific package attached. “It was the first time we were able to use computers to do linear regression analysis to confirm the data we were producing,” said Sebastian.
Before that, Sebastian said, you had to allot 20 minutes to use a pad of paper and a slide rule in order to make the same calculations. This later evolved to using a Texas Instrument scientific calculator, and finally culminating in the usage of personal computers with ever increasing speeds.
Spring Design
Over the years, SMI has developed spring design booklets and manuals and offered numerous training programs, all of which continue today. In addition, numerous articles in Springs have been devoted to the subject.
Former SMI president Chuck Pepka at Renton Coil was instrumental in bringing the first spring design software package to use among SMI members.
“It was a great program, but it could not handle complicated simultaneous equations,” explained Sebastian.
SMI later discovered TK Solver™ from Universal Technical Systems, Inc. (UTS), which had the ability to readily solve simultaneous equations. The program could dramatically reduce design hours, production costs and speed time to market.
A partnership between UTS and SMI resulted in Advanced Spring Design (ASD) software that combines engineering expertise with customized calculations to help users design quality springs. “With things like ASD and overall computer speed improvements during the last 20 years, the industry has experienced a digital revolution,” explained Sebastian. “Technology has allowed us to plug into AutoCAD design programs making it easier than ever to design springs.”
“With things like ASD and overall computer speed improvements during the last 20 years, the industry has experienced a digital revolution,” explained Sebastian. “Technology has allowed us to plug into AutoCAD design programs, making it easier than ever to design springs.”
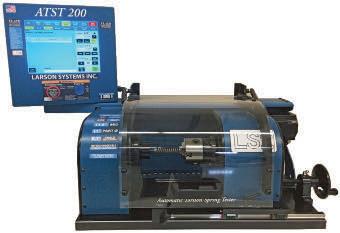
Machinery Improvements
The introduction of computer numerical control (CNC) coilers in the late 70s helped bring automation to the spring industry. CNC machines are operated by computers executing pre-programmed sequences of controlled commands. CNC machines are essentially the opposite of “old-school” mechanical coilers, which are manually controlled by hand wheels or levers, or mechanically automated by cams alone.
Sebastian says the early CNC coilers utilized electrical stepping motors to provide greater precision compared to a regular DC motor. A stepping motor is able to break down a complete revolution into a couple of equal steps to make it suitable for operations where precise and small movements are needed.
Sebastian says the late 80s introduced hydraulic servo control technology to work in tandem with the stepping motor. He says the evolution of the servo motor provided the ability to achieve more horsepower and torque.
“The first CNC machines were all coiling machines, but with the advent of technology in the early 90s you could apply the same servo control improvements for forming machines,” explained Sebastian. “Things have just gotten better from there as technology has improved.”
Further developments came with the introduction of multi-axis coiling and forming machines. This type of machining was originally performed mechanically on large complex machines that operated on several axes, which were controlled individually via levers that rested on cam plates. The cam plates offered the ability to control the tooling device, the table in which the part is secured, as well as rotating the tooling or part within the machine. Due to the size and complexity of the machine, it took extensive amounts of time to set them up for production.
When multi-axis CNC machines were introduced they provided a faster, more efficient method to coil and form parts. Today’s coiling machines come with 2-12 axes, and forming machines can handle 2 to 16 axes.
Multi-axis machines provide increased speed and higher quality parts.
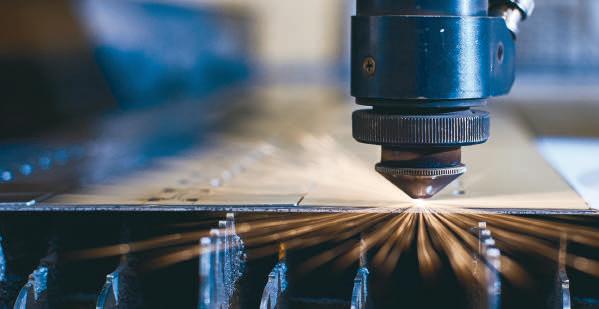
©iStockphoto.com/ sandsun
Looking Back, Looking Forward
Al Mangels is president of Brooklyn-based Lee Spring. When reflecting back upon his 38-year career in the spring industry, he provided his list of 20 advances (in alphabetical order) that have impacted springmaking.
“The biggest changes have been in the application of digital technology, both on the factory floor and in the office,” explained Mangels. “If I had to pick between these two, I’d say that at this point, digital office technology has had a larger effect than digital manufacturing technology. That’s only because I feel that, for the office, it is more advanced; digital manufacturing technology in our industry is not yet quite as advanced as it is in other manufacturing industries.”
As Mangels looks forward to additional advances he expects that robotics/automation will be the next biggest change.
“Although it will be challenging in the spring industry, due to the nature of our products,” said Mangels. He explains that generally it is more difficult to automate springs than other products, such as machined parts or plastic injection molded parts.
“Additive manufacturing is another area, but the extra-high strength of most spring materials also makes that difficult,” he said. “Other more esoteric technologies are nanotechnology and graphene.”
1. Additive manufacturing (3D printing) 2. Automatic length gauges with sorting devices for coiling machines 3. Automatic setting, testing and sorting machines 4. Bar coded packaging, and accompanying systems 5. CAD drawing software 6. Ceramic/diamond type grinding abrasives 7. CNC controlled downfeed grinding machines 8. CNC wire EDM machines 9. Computerized vision inspection systems 10. Computerized spring design programs
11. Conveyorized stress relieving ovens 12. Digital (load cell equipped) load testing machines 13. Digital office systems (networks, email, faxes, etc.) 14. Environmentally friendly cleaning and finishing chemicals 15. Industrial robots/cobots 16. Laser cutting machines 17. Laser probing devices 18. Multi-axis CNC coiling machines 19. Multi-axis CNC wireforming (slide forming) machines 20. Vibratory bowl feeders
“What once required multiple setups now can be executed in only a few, if not one setup, reducing steps and decreasing the opportunity for error,” said Sebastian.
Not to be forgotten is the beloved fourslide machine, which is used for the high-volume manufacturing of smallstamped components. Recent years have seen the introduction of servodriven fourslide machinery, promising quicker tooling changes and higher productivity versus the traditional mechanically-driven machine.
Other production accessories have also improved, such as inline conveyor ovens for stress relieving, spiral ovens, box ovens, part collectors, payoff reels, grinding machines, to name just a few.
Vision Systems
The introduction of vision systems technology to spring coiling and forming machines came on the scene in the past 10 years. “It allows us to make physical adjustments to the part as it is being produced on a three-dimensional scale,” explained Sebastian.
Essentially the vision control system on board the machine takes pictures to make real-time adjustments to make sure the part is being produced within set tolerances. Using this technology on the machine leads to a reduction in waste, because fewer parts are scrapped that are out of tolerance. It also provides consistency in part production and better quality.
Stand-alone vision inspection systems are also being deployed in the quality department of springmakers for final inspections to meet quality standards, such as ISO9000. It is also used to provide customers with performance and inspection testing results.
Environmental Changes
Spring manufacturers have worked hard to curtail the amount of waste produced. Sebastian said initially going “green” was more of an economic decision, such as installing more efficient furnaces (as a result of energy price hikes). Later, he said, springmakers realized the benefits to the environment by utilizing earth-friendly cleaning and finishing chemicals and providing scrap materials for recycling. “It used to be if you wanted a good spring coiler you looked for the person who worked on their car all the time. Today you look for the kid who’s the best at video games.”
3D Printing
The introduction of additive manufacturing (3D printing) to the spring industry has primarily involved using it for small lots and prototypes.
Sebastian says one of the problems with using 3D printing for mechanical components is a metallurgical gap. “The actual raw materials you use for a 3D printer are not the same metallurgically strong materials that springmakers work with,” he explained. “Imagine making a spring with a thousand little pieces versus one solid piece of wire. So far there hasn’t been a revolution yet that helps break that barrier.”
Until improvements come about, the use of 3D printing in the spring industry will be limited.
ERP Systems
Owing to improvements in the front office, enterprise resource planning (ERP) software has greatly improved in the past 20 years and is now primarily cloud-based. Software packages provide manufacturers with systems for quoting, shop management, scheduling, inventory, accounting, quality control, customer relationship management (CRM) and much more. Spring manufacturers benefit from real-time inventory accuracy, improved on-time delivery, lower administrative costs, increased sales and improved customer service.
Daily production schedules, productivity scorecards and other reporting capabilities have made ERP systems a valuable management tool.
As a result of new ERP systems and other changes within the office, many have or are in the process of moving toward a paperless environment.
Conclusion
There are numerous other developments that have moved the spring industry forward. The ones listed in this article are some of the most important. See Al Mangels reflections in a related article on page 25.
Sebastian points out that one of the benefits of advancements in the spring industry is to help bridge the skills gap.
“It’s changed the way we recruit people and how the people we hire do their work,” explained Sebastian. “It used to be if you wanted a good spring coiler you looked for the person who worked on their car all the time. Today you look for the kid who’s the best at video games.”
Another change that advancements have brought about is how capital is invested. “With sophisticated technology comes a higher price,” explained Sebastian. “You have to make sophisticated decisions as to which machine you are going to buy and the money that’s involved in it.”
He says the decision comes down to how the machine will increase the speed of your operations, the quality, or both. “Therefore, your throughput goes up and you get more return on your investment for what you spend.”
Sebastian says overall quality has increased because of the changes.
“When you marry the quality measurement techniques that are available with the available equipment we have now, the products are much better than they ever were,” said Sebastian. “Why? Because we’ve taken out the greatest element of error, which is the human being. You still need a human being to make sure the computer is doing the right thing. But when the computer functions properly and makes all the adjustments in an intelligent fashion, everyone wins.”
With the fourth industrial revolution (Industry 4.0) upon us, who knows what the next 50 years will entail, as robots, automation, artificial intelligence, the Internet of Things (IoT) and smart manufacturing gain a foothold in the industry. n