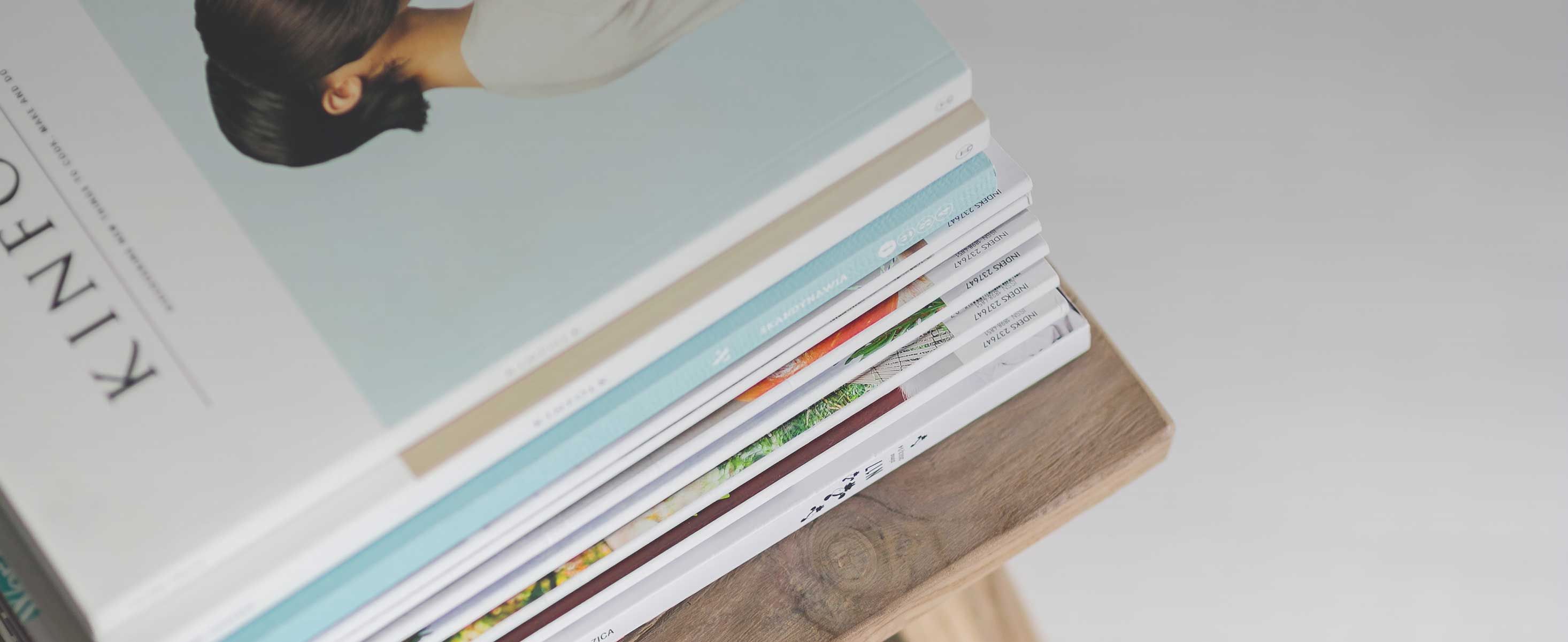
7 minute read
Be Aware Safety Tips
A Fresh Start
By Laura Helmrich-Rhodes, CSP, Ed.D.
One of the great benefits I have found of being a full-time academic, is that a new semester begins in the fall and again in the spring. This is a nice way to live, with at least two fresh starts every year; a chance to evaluate, take stock, make changes and maybe even start a new exercise routine! Is it time to step back and look at and evaluate your company safety program as a new season approaches? As the fire, workers’ compensation and general liability insurance December policy deadlines have come and gone, it is always a good time to make a fresh start. Whether you have an established safety, health and environmental program or have decided it is time to formalize your employee safety efforts, the Occupational Safety and Health Administration (OSHA) has provided an excellent resource on their website called “Recommended Practices for Safety and Health Programs.” Within this helpful website it lists “Ten Ways to Get Your Program Started.” Let’s look at these 10 items as they impact the spring industry and how to use them to start anew.
Establish Safety and Health as a Core Value and Lead by Example
The first two elements, establishing safety and health as a core value and leading by example, need to be discussed together. There is no doubt that a safety culture begins with the owner(s) of the company. Written mission statements and policies are only as good as the leadership team implementing them. Those at the helm need to make decisions everyday with safety as a key question. Accepting jobs that exceed the capability of the workforce, equipment or time constraints, purchasing equipment that is properly safeguarded (machine guarding and hazardous energy shut down) and setting aside funds for higher level training for those in hazardous positions, such as maintenance and forklift operators, are all decisions that should have safety as a high-level consideration.
Leading by example goes way beyond owners and managers wearing appropriate protective equipment on the shop floor. Leading everyone to make decisions with safety in mind creates a culture of safety. When every employee truly believes they have the authority to stop work when they see an imminent danger and that management cares about them beyond profitability,
Laura Helmrich-Rhodes, CSP, Ed.D., is an independent regulations compliance consultant to the Spring Manufacturers Institute (SMI). A former member of PA/OSHA Consultation, she is an associate professor in the Safety Sciences Department at Indiana University of Pennsylvania where she teaches graduate and undergraduate classes on topics such as OSHA standards, safety communications, workers’ compensation and human relations. Rhodes is available for safety advice and information. Contact SMI at 630-460-8588 or laurahrhodes@gmail.com. then safety is a core value. As the old saying goes: “More is caught than taught!” Employees know when key decisions are made that overlooked safety considerations.
Established and communicated values will help attract and maintain a younger workforce. Youth want to know that organizations are committed to sustainability, environmental protection and the greater good. Showcasing your company’s commitment to safety and the environment might help hire and maintain a loyal workforce.
Implement a Reporting System
Creating a meaningful incident reporting system, where there is a follow-up system to prevent reoccurrence, is a critical element of a safety program. The best strategy is to identify near-miss events so that no one is injured, or property damaged. Behaviorbased safety programs work on reinforcing the positive work methods to avoid errors, damaged goods and injury to your workers. The key is that employees know they are free to report injuries and illnesses without fear of retaliation.
Beyond assuring employees that repeat events will not occur, collecting and synthesizing meaningful data regarding safety is a great way to elevate the importance in a company. Losses, potential losses, supervisor completed inspections, returned defective materials and work orders with safety as priority are all examples of little nuggets, that when analyzed for trends, can be used to continuously improve operations. Safety data should be a part of every senior management meeting so that your overall program stays fresh.
Provide Training
There are many federal OSHA requirements for safety training and there may be state requirements as well. For example, Pennsylvania requires annual training for hazardous chemical right to know (Hazard Communication), but federal OSHA has different times that re-training must occur. Commitment to training goes beyond the annual safety training I provide to SMI member companies (summer training dates are being scheduled).
Professional growth can help prevent workers from leaving. Create a training plan for all employees so that they improve and master job tasks and can move on to greater challenges. Grow supervisors and managers by providing in-house training, send others to advanced courses and conduct monthly, meaningful toolbox talks to keep employees interested in safety topics at work and at home.
Conduct Inspections
Inspections should be done at a variety of times, depending on the operational hazards and the depth of the safety culture. Some standards have specific inspection times. For example, forklifts must be inspected daily before each shift. Those inspection forms
need to be available to the OSHA inspector, if a forklift accident occurs. Rigging (includes, but is not limited to, synthetic and chain slings) used for material handling also have specific inspection times, as well as any fall protection.
Every employee should have inspection obligations for their work area, including the office staff and quality control labs. No one should be exempt. Everyone should know the extent of their authority to change it and/or who to notify if it is beyond their authority. The bottom line is that hazards should not be present until the next monthly inspection takes place and waiting for “someone” to fix it.
Collect Hazard Control Ideas and Implement Hazard Controls
I have found that employees are excellent resources for both hazard identification and new ideas for cost effective controls. Employees work with the equipment/process daily, meet deadlines and quotas, use a variety of raw material and experience failures. It is likely your employees have put a lot of thought into ways to improve both efficiency and safety.
Management is overlooking a vast pool of knowledge when they don’t ask employees for ideas. I have found that the employees “in the trenches” can have much better ideas than some engineers. By teaming skilled employees’ ideas with in-house or consulting engineers, problems can be solved and improved processes can be created while reducing/eliminating hazards.
This discussion could lead to the hot issue of “Quiet Quitting.” Employees who are offended or feel unheard are only going to do the minimum for the organization. Their loyalty is waning. Engaging employees and their ideas and acting on them help employees feel part of the team and the company’s overall mission. Of course, not every suggestion must be implemented. Gather them, recognize them and implement the ones that move the organization forward.
Address Emergencies
When I look back at the emergencies that were included in the first Emergency Action Plan (EAP) I created in the early 1980s, I am horrified by the expansion needed today. All emergencies that are possible need to be included in the Emergency Action Plan (EAP). Often overlooked is the required Fire Prevention Plan that accompanies the EAP. The federal requirements for employers over 10 employees in a calendar year are greater than very small companies; nonetheless, unfortunate events hit even very small factories. The key is to have a plan, publish and practice it. Consider inviting local emergency management and law enforcement to conduct drills and demonstrations at company facilities. The better they know the facility layout, location of shut-offs, hazardous chemicals and employee muster points, the more effective they will be when an emergency arises.
Seek Input on Workplace Changes and Make Improvements
Before changing operations or equipment, be sure to get employee input so that any safety or health issues can be addressed before implementing. Create a list of safety questions that purchasing managers must ask. Do a pre-purchase machine guarding study and obtain the lockout shut down procedures before the purchase. When planning any construction or making agreements with contractors, include safety in the bid process as well as a review of their safety program to assure they are not creating new hazard for your employees.
Take the beginning of a new year as a time to make a fresh start. Set aside time to review safety and health issues, goals, mission statements and measure how the company is doing in meeting/exceeding those goals. Act on the items employees bring to you as sincere concerns. By doing these things you can make a fresh start toward deepening the culture of safety so that it becomes a part of the fabric of your day-to-day operations. n
Helpful Resources
Recommended Practices for Safety and Health Programs: How Do I Get Started? Downloadable booklet also available in Spanish https://www.osha.gov/safety-management/ getting-started American Red Cross Ready Rating: Assess your Company’s Level of Preparedness https://www.readyrating.org OSHA Emergency Preparedness Safety Topics Page https://www.osha.gov/emergency-preparedness Machine Guarding eTool https://www.osha.gov/etools/machine-guarding/ standards
Leading a Culture of Safety: A Blueprint for Success For health care but easily applied to any business venture https://www.osha.gov/sites/default/files/Leading_a_ Culture_of_Safety-A_Blueprint_for_Success.pdf
1. Establish safety and health as a core value. 2. Lead by example. 3. Implement a reporting system. 4. Provide training. 5. Conduct inspections. 6. Collect hazard control ideas.
7. Implement hazard controls. 8. Address emergencies. 9. Seek input on workplace changes. 10. Make improvements.