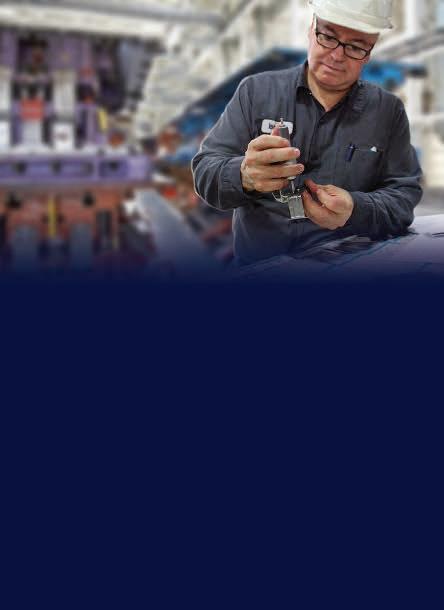
10 minute read
Be Aware Safety Tips
Have You Heard About Be Aware Safety Tips OSHA’s Hearing Conservation Requirements?
By Laura Helmrich-Rhodes, CSP, Ed.D.
There are many written programs required by the Occupational Safety and Health Administration (OSHA) and a formal, written, hearing conservation program (HCP) is one of them. During my on-site safety audits, I have found the HCP is often missing. This is not surprising, considering in 2019 OSHA issued 168 citations for just the written program portion of the HCP standard to manufacturing companies. More citations were issued for other parts of that same standard (see graph on page 16). Protecting employee hearing is built on engineering controls and the implementation of a well written program.
Many spring manufacturing companies, or portions of the manufacturing buildings, are operating at a time weighted average (TWA) of 85 decibels (dB) over an eight hour day. This is called the “action level,” according to OSHA. This is when employers must make hearing protection available at no cost to its employees. Usage does not have to be enforced at this level. It is up to the employee to decide; however, everyone exposed to 85 dB must be included in the formal HCP as described in detail below. When noise levels hit 90 dB TWA, over an eight hour day, hearing protection must be worn and fully enforced.
Noise Monitoring
In order to determine if exposures are at or above this level, it may be necessary to measure or monitor the actual noise levels in the workplace and to estimate the noise exposure or "dose" received by employees during the workday. Noise monitoring or measuring must be conducted only when exposures are at or above 85 dB. Factors which suggest that noise exposures in the workplace may be at this level include employee complaints about the loudness of noise, indications that employees are losing their hearing, or noisy conditions which make normal conversation difficult (see Informational Appendix in Helpful Links on page 17).
There are two types of monitoring necessary. One is an area survey that measures the noise around equipment and is usually reported as a map, similar to a topographical map, with sound level readings noted in the various areas of the plant. This only tells us what noise is present. It does not tell us the
Laura Helmrich-Rhodes, CSP, Ed.D., is an independent regulations compliance consultant to the Spring Manufacturers Institute (SMI). A former member of PA/OSHA Consultation, she is an associate professor in the Safety Sciences Department at Indiana University of Pennsylvania where she teaches graduate and undergraduate classes on topics such as OSHA standards, safety communications, workers’ compensation and human relations. Rhodes is available for safety advice and information. Contact SMI at 630-495-8588 or laurahrhodes@gmail.com. dose of noise each employee is experiencing in a workday. This measurement method is generally referred to as "area" noise monitoring. These are helpful in determining where signs should be posted and which departments should have more extensive testing to determine what the employees are experiencing. To determine employee exposures, personal dosimeters must be used. A dosimeter is a device attached to the employee’s clothing, usually near the shoulder, with a sturdy clip. The device measures the noise levels while they carry out their daily tasks. It then averages the noise exposure over the workday. The results are analyzed and a dose is determined. These tests should be done by a trained professional. Preferably, a certified industrial hygienist (CIH) should take the readings or overseeing those who do the tests. The CIH is specially educated and trained in employee health concerns and the operation of monitoring equipment. Their expertise in these devices is paramount, since they must be calibrated prior to use. Also, strict adherence to the manufacturer’s recommendations needs to be followed to assure accuracy. Both CIH and certified safety professionals (CSPs) would be able to make valuable recommendations for the elimination of noise through engineering and administrative controls too. Your workers’ compensation carrier may conduct these tests for little or no cost and have CIHs and CSPs on staff. If testing was done in the past and no hazard found, it is likely those readings have changed. Production has significantly increased in some spring and wireforming companies, and therefore it is highly recommended that new results be obtained to assure employees are being properly protected. If machinery has been added or reconfigured, then re-monitor. Many companies choose to re-monitor periodically (once every year or two) to ensure that all exposed employees are included in their hearing conservation programs (see Informational Appendix).
Written Program: The Nuts and Bolts
It is not enough to download a sample written program and stick it in a binder. The written program is meant to be a living document that actually assures that important events happen. For example, who will be purchasing the correct hearing protection, with the correct noise reduction rating (NRR)? Who will conduct training and where will employees go to have annual audiometric testing? These are just a few key elements. All written safety and health programs should outline the responsibilities, authorities and accountabilities of everyone dedicated to help prevent employee noise-induced hearing loss.
Most written programs are to be reviewed annually to assure they are working. OSHA’s “Recommended Practices for Safety and Health Programs” suggest three steps in assuring programs work as expected. First, monitor the performance and progress; verify the program is implemented and operating; and last, correct the program shortcomings and identify opportunities to
improve it. An entire eTool has been created to assist businesses in the best practices for all safety programs and a page dedicated to Hearing Conservation (see Helpful Links on page 17).
One important questionSprings readers may have is: “Who is responsible for temporary employees?” OSHA has an initiative to protect temporary workers and issued a statement on this question.
“The host employer will usually have the primary responsibility for determining noise exposure levels, implementing and maintaining engineering, administrative and work practice controls, providing appropriate hearing protection, and maintaining a hearing conservation program in accordance with all requirements of the standard for the workplace.”
Audiometric Testing
Exposure to high levels of noise can cause permanent hearing loss. OSHA considers a hearing loss to have occurred when a worker experiences a standard threshold shift (STS). An STS is a change in the worker’s hearing threshold when compared to the worker’s baseline audiogram. Short-term exposure to loud noise can also cause a temporary change in hearing. Exposed workers may develop a short-term partial hearing loss, referred to as a temporary threshold shift (TTS) or may develop a ringing in the ears, called tinnitus. These short-term health effects may go away within a few minutes or hours after leaving the noisy area. However, repeated short-term exposures to loud noise can lead to permanent tinnitus and/or hearing loss (OSHA, Bulletin #9).
If employees are exposed to noise greater than 85dB TWA (this is determined by personal dosimetry), then audiometric testing must occur within six months of their first exposure then annually to determine if STS are occurring.
The Right PPE
Not all hearing protection (plugs or muffs, for example) are made the same. This is definitely a case of “buyer beware.” First, be certain purchases are made from reputable suppliers. The CIH should recommend a particular NRR to be purchased. It is best to provide a variety of hearing protection to assure employees are comfortable and will wear them for the entire workday.
Occupational Health and Environmental Control [1910.94 – .98]
CFR1910. 29
95(c)(1)
95(g)(1)
95(d)(1)
95(k)(1)
95(g)(6)
OCCUPATIONAL NOISE – HEARING CONSERVATION PROGRAM
168
OCCUPATIONAL NOISE – ESTABLISH & MAINTAIN AUDIOMETRIC TESTING PROGRAM
76
OCCUPATIONAL NOISE – DEVELOP & IMPLEMENT MONITORING PROGRAM
71
OCCUPATIONAL NOISE – EMPLOYER SHALL TRAIN EACH EMPLOYEE
65
OCCUPATIONAL NOISE – ANNUAL AUDIOGRAM FOR EACH EMPLOYEE
45
Number of Serious Violations – FY2019
The NRR was developed by the Environmental Protection Agency (EPA). According to an EPA regulation, the NRR must be shown on the hearing protector package, so make certain this is on the package when purchasing. The concept is that the NRR attenuates the noise to a TWA of 85dB. There are calculations that are necessary to confirm you have the right PPE and those can be found in the Helpful Links on page 17. This underscores the importance of using a qualified CIH and audiologist.
Recordkeeping
According to OSHA, employers must record a work-related Standard Threshold Shift on the OSHA log. 1904.10(a)
Basic requirement. If an employee’ s hearing test (audiogram) reveals that the employee has experienced a work-related Standard Threshold Shift (STS) in hearing in one or both ears, and the employee’ s total hearing level is 25 decibels (dB) or more above audiometric zero (averaged at 2000, 3000, and 4000 Hz) in the same ear(s) as the STS, you must record the case on the OSHA 300 Log.
We can all agree that it is important to eliminate all injuries and illnesses in the workplace as they impact the OSHA incident
Hearing Conservation Checklist
❑✔Monitoring noise levels (personal and area samples) using a
Certified Industrial Hygienist or qualified person ❑✔Notify employees of hazardous noise levels, including access to the OSHA regulation ❑✔Allow employees the ability to observe noise monitoring ❑✔Maintain a written audiometric testing program, conduct baseline and annual audiograms of those in the high noise areas ❑✔Post signs near areas of high noise ❑✔Provide and consistently enforce the use of hearing protectors when engineering and administrative controls do not control the noise ❑✔Develop and implement a training program ❑✔Provide access to information and training materials ❑✔Assure audiograms are reviewed by a qualified audiologist and results are shared with employees ❑✔Maintain accurate records, including recording any work-related STS ❑✔Continue to reduce work area noise through planning processes and the purchase of future equipment ❑✔Annually review the program and document continuous improvement efforts
rate and even the workers’ compensation experience modification rates (EMR), since some states provide compensation for noise-induced hearing loss. By including the STS on the OSHA log, employers are sometimes surprised how significantly their incident rate can jump, especially if they don’t normally have an OSHA recordable incident. High incident rates can trigger OSHA inspections under the current OSHA administration. The key is to prevent any injury or illness, like hearing loss, from occurring to keep those numbers approaching zero.
Another important question readers may have is: “How long does an employer have to maintain medical records?” This question is addressed specifically in the OSHA standards.
Helpful Links
Federal OSHA Noise Regulation: https://www.osha.gov/ laws-regs/regulations/standardnumber/1910/1910.95 Safety Program Best Practices: https://www.osha.gov/ safety-management/program-evaluation Hearing Conservation Booklet: https://www.osha.gov/ sites/default/files/publications/osha3074.pdf Informational Appendix to the Federal OSHA Noise Standard: https://www.osha.gov/laws-regs/regulations/ standardnumber/1910/1910.95AppG Choosing the Right Hearing Protection Appendix B of the OSHA Standard: https://www.osha.gov/laws-regs/ regulations/standardnumber/1910/1910.95AppB The basic answer is 30 years past the last date of employment, in other words, a very long time! For more information on all medical records, see the link in the Helpful Links below.
Conclusion
It is not enough to have a written program in a 3-ring binder on a shelf. There is science and engineering, as well as human behavior, which impact a fully functioning program that prevents employees from permanent hearing loss and OSHA recordable events. When all the time, money and effort go into these protections, certainly we are convinced of the importance of consistent enforcement and continuous improvements. n
Questions About Hearing Conservation: https://www. osha.gov/laws-regs/standardinterpretations/1994-05-09-0 NIOSH Preventing Noise Exposures: https://www.cdc. gov/niosh/topics/noise/ Temporary Worker Initiative: Noise Exposure and Hearing Conservation Bulletin #9: https://www.osha. gov/sites/default/files/publications/OSHA3953.pdf Federal OSHA Medical Recordkeeping Regulation: https://www.osha.gov/laws-regs/regulations/ standardnumber/1910/1910.1020
It’s your world. Shape it as you please.
In the hands of skilled craftsmen, our steel becomes the parts, components and products that make the world turn. For over 65 years, fabricators and manufacturers big and small have trusted Admiral Steel to help them leave their mark on the world. For any size order from 10 lbs. to 10,000, you get first-class quality, on-time delivery, and personalized service from Admiral. Contact us for a quote today!
Admiralsteel.com
ISO 9001 REGISTERED
4152 West 123rd Street Alsip, Illinois 60803-1869 Ph: 800-323-7055 Fax: 708-388-9317 email: sales@admiralsteel.com
Admiral is a registered trademark of Admiral Steel LLC. Alsip, Illinois. Reg. No. 2430959. All rights reserved.
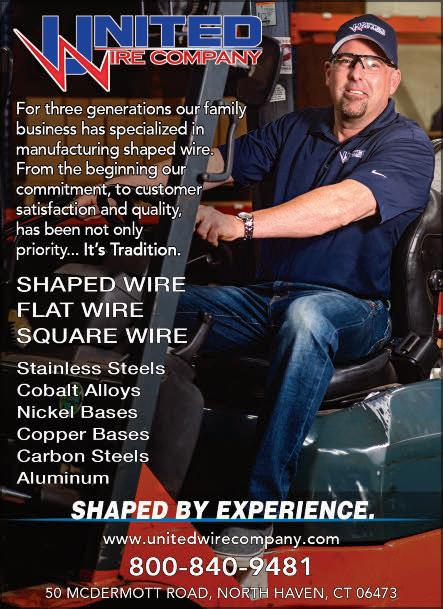