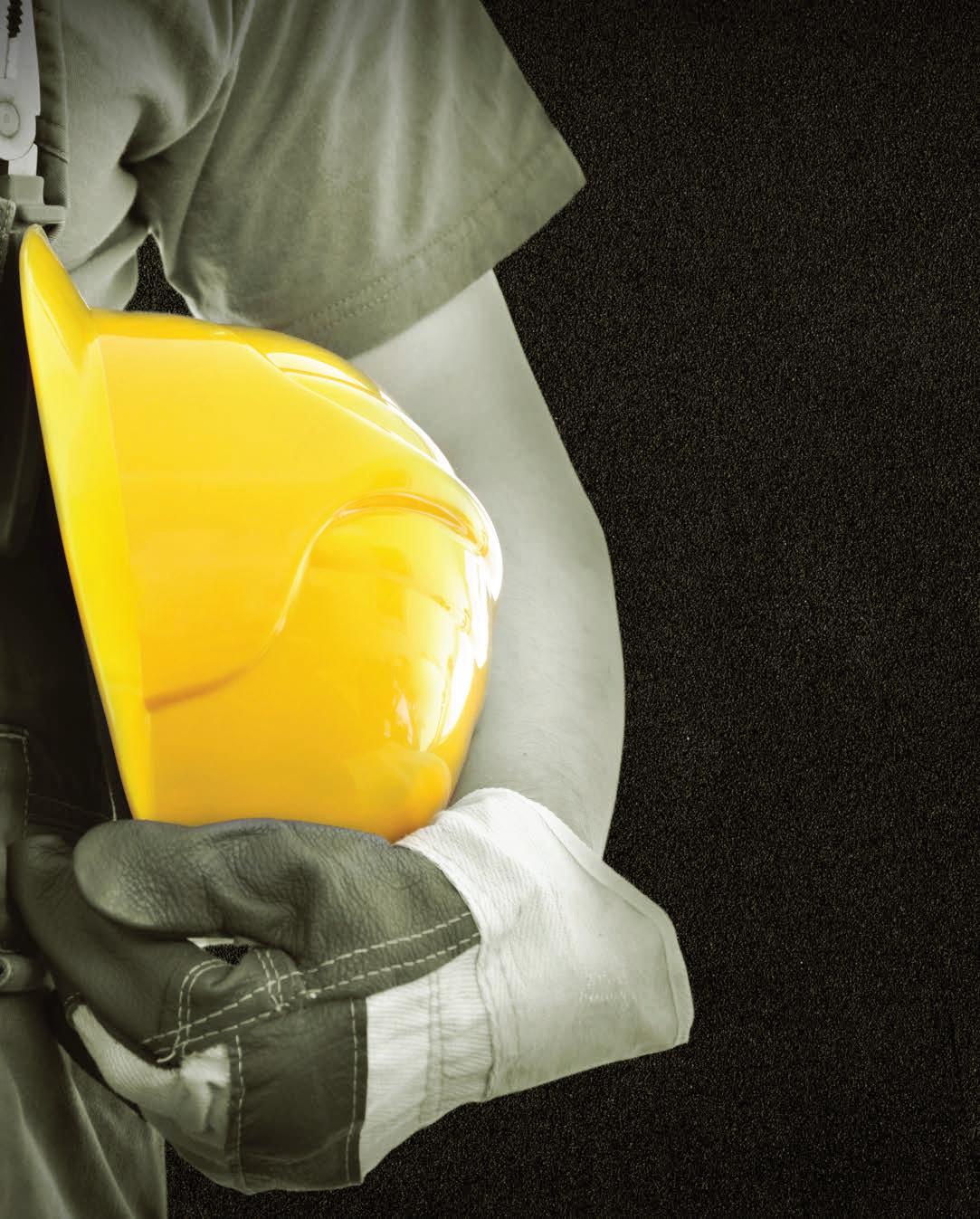
14 minute read
Safety First
orkplace safety refers to
the working environment
at a company and encompasses
all factors that impact the
safety, health and well-being
of employees. This can
include environmental
hazards, unsafe working
conditions or processes,
drug and alcohol addiction
and workplace violence.
By Gary McCoy
As this issue focuses on safety first, we have several articles for you to enjoy. First up is an interview with Dr. Laura Helmrich-Rhodes about the state of safety in manufacturing. Dr. Rhodes is well-known to Springs readers as an independent regulations compliance consultant for SMI and as a regular columnist. You can read “Safety First: An Interview with Dr. Laura Helmrich-Rhodes” on page 33.
Durkin goes on to say, “It does not take a lot of resources to make that message say, ‘safety first.’” Read Durkin’s article on page 37.
In her article “Pandemic Safety Strategies,” Annelise Mackiewicz at FENN/Torin discusses how the company has adapted measures to keep customers safe both now and in the future. You can read her article on page 36.
Finally, in Book Corner I review the book “Safely Working from the Ground Up” by David Shafer on page 57. Shafer takes a practical approach to workplace safety with a goal of “turning safety upside down.” His approach is to reject a top down approach to safety, and advocate for a program that endeavors to succeed from the ground up.
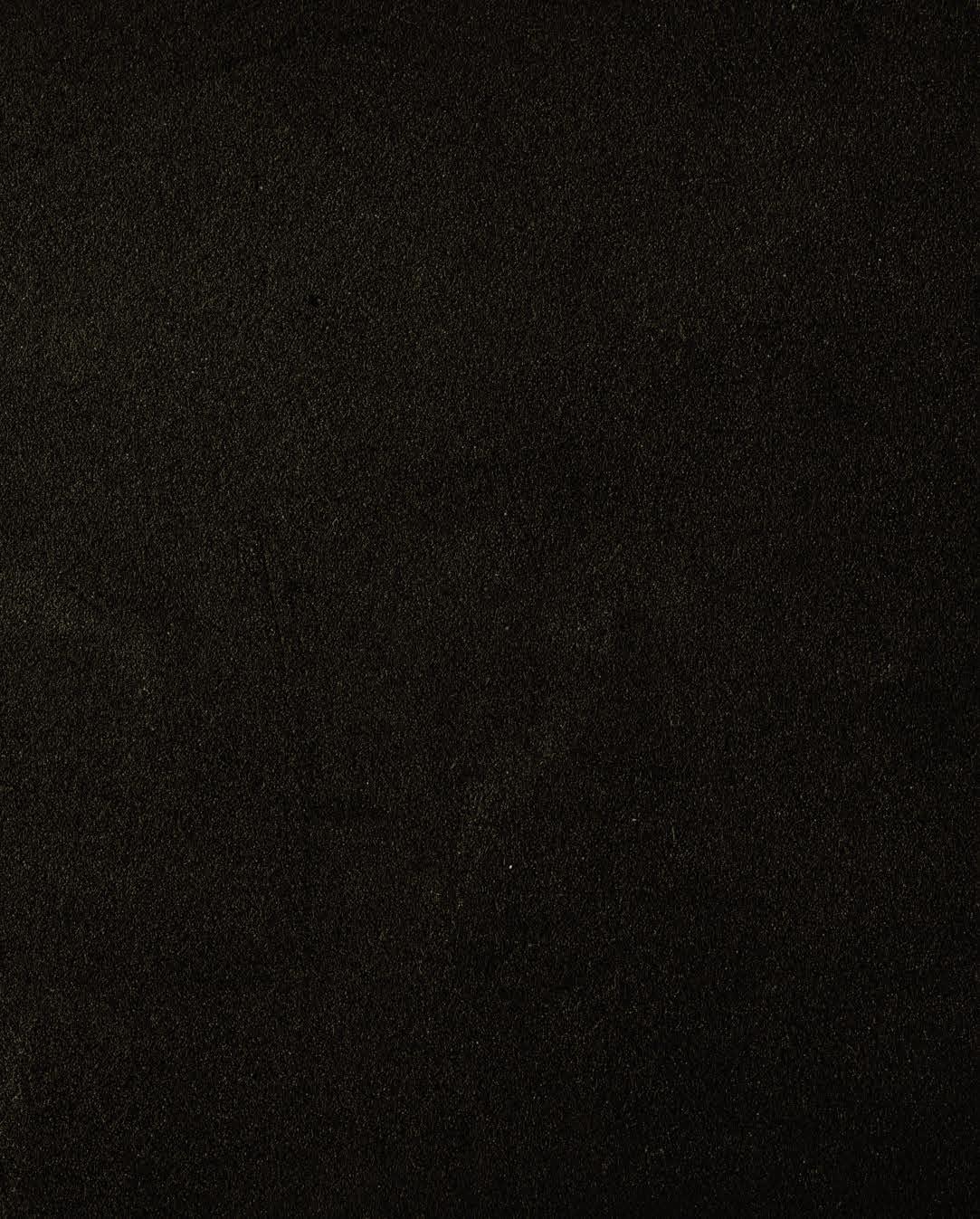
Workplace Safety: A Profile of Three Spring Companies
SMI members with safety programs at their manufacturing facilities try to juggle a delicate balance between production and profitability while keeping workers safe from dangers. I spoke with leaders at Iowa Spring and Stamping, Vulcan Spring and Manufacturing Co. and Plymouth Spring about the state of their safety program and how they are putting safety first.
Everyone at these three companies believe a safety program is a tremendous asset. They agree that a company’s most valuable asset is their employees, so putting safety first is a priority and a coveted company value.
Iowa Spring and Stamping, Adel, Iowa
Iowa Spring and Stamping is located in the heart of central Iowa, just 30 minutes west of the capitol city of Des Moines. Lorissa Moffitt is director of human resources at the company, a position she has held since 2012. Among her responsibilities is company safety.
Iowa Spring has a safety committee of 10 people that meets monthly. “What I love is that we all get together, our supervisors and our vice president of manufacturing, to address any issues or concerns,” explained Moffitt. “We address it right there and try to get it resolved. We have a list to make sure everything is completed.”
Moffitt explained that the size of the committee was reduced due to the pandemic. “I’m glad we continue to do this, only now on a smaller level.”
She said Iowa Spring is always trying to improve safety. “I don’t think anyone is perfect. The plant floor always has the best ideas when it comes to making safety improvements.”
Moffitt says they are always trying to improve things. In August 2021, Iowa Spring brought in SMI’s regulatory compliance consultant, Dr. Laura Helmrich-Rhodes, to complete a safety audit. “We did a walk through of the plant with her,” said Moffitt. “She was really impressed with the way we handle things.”
Moffitt said the next day Rhodes provided training that would be beneficial for supervisors. “The training helped the supervisors gain a different perspective on things,” explained Moffitt.
“We are always improving things out in the plant,” said Moffitt. “It’s manufacturing, so things are always changing. We have improved a lot since I’ve been here.”
The company now has gates around its wire reels and, among many things, they’ve also provided training on proper lifting.
Moffitt says every employee has annual safety training. “If we have any recordables or near misses, we will go over those.”
One of the things that Rhodes initiated at Iowa Spring is a program to help new employees with safety. “Most of the time, the people who come in here have never worked in spring manufacturing,” said Moffitt. “We made a list together of what we think is important when new employees come in here.”
Moffitt says they have a lot of temporary workers who come to work at Iowa Spring. “We have them wear a bright colored shirt so we can identify them. It helps us show them the different areas they need to know, such as walkway areas. When temps come in, we do a walk through with them and have them work with their supervisors on safety, as well.”
In addition, Moffitt said every temporary worker is assigned a mentor for advice and assistance.
She said up until COVID-19, Iowa Spring had its insurance carrier visit the plant to do a walk through to see how they can make improvements to its current system. “We’re here every day, so we sometimes don’t see it. We ask them to do it and it has always been very helpful,” said Moffitt.
The company has adjusted due to the pandemic, which has included investing in additional cleaning people. As a result, safety cleaning protocols have been implemented between shift changes and at the end of the day.
“One obvious thing with the pandemic is we have told our employees: ‘Don’t come to work if you are sick,’” explained Moffitt. “Sometimes you have to state the obvious.”
She said that Iowa Spring has made changes to its break room. Only 10 people are now allowed in at any time, and lunch breaks are taken at two different times. Plus, Moffitt said employees are now allowed to go to their vehicles for lunch.
Moffitt said meetings are now limited to 10 people. “Being a manufacturing company, our employees are already spread apart, so no one works side by side. So that helps quite a bit.”
In conclusion, Moffitt said, “We let our employees know all the time that safety is our No. 1 thing. If there is anything they question, they need to come to us. We will look at something so it is taken care of.”
Located 45 minutes north of the center of Philadelphia, Vulcan Spring and Manufacturing Co. was founded in 1967 by Alex Rankin.
“My father created an amazing base company with its foundation focused on constant force springs,” said second
generation owner Scott Rankin, who now runs the company and is a former SMI president.
“I got involved full time in 1983 and worked to help grow the company through sales and new versions of manufacturing. As I got more involved, I found a large gap between what we thought the Occupational Safety and Health Administration (OSHA) was asking for and what OSHA was actually asking for.”
Rankin said he made a call to OSHA to find out exactly what it was they had in mind for Vulcan Spring. “This turned into a long-term relationship with OSHA consultation and OSHA through their Safety and Health Achievement Recognition Program (SHARP) program,” explained Rankin.
“In 1990, I made my first call to OSHA and was put in touch with OSHA consultation. They visited Vulcan and started the process to work toward a SHARP certificate, showing that we were in compliance with OSHA standards for our business,” said Rankin.
Rankin says it took five years of hard work to get the company’s team ready for the SHARP certificate.
“After that, we have had yearly visits and many changes that kept us busy to keep current,” said Rankin. “This has gone on for more than 25 years, and we all work hard with our safety committee and OSHA consultation to meet the challenges each year. As time went on we had more time between visits but still worked to stay current with the ever-changing rules.”
Rankin is quick to point out that even with the SHARP certification, they have still experienced injuries.
“Our tally rate of no lost-time injuries has been reset many times, bringing us back to zero and letting us get more diligent with each issue,” explained Rankin. “We have gotten far better at finding why an accident happened and then making changes to try to guarantee that the same injury will not happen again. We work hard to keep our focus on safety at the forefront of all meetings and interactions with new and seasoned employees.”
Rankin went on to say, “I wish you could say having a safety committee and a safety program and an OSHA SHARP program would guarantee that no one gets hurt again, but unfortunately that’s not the real world we live in. There are people and people make mistakes. Things break.”
Rankin says the message of “safety first” is pretty blatant at Vulcan. “We have signs everywhere, and flags and stuff
like that we’ve gotten through the years with the OSHA program. When someone comes in the first day, there’s about 20 minutes of their onboarding devoted to safety.” And how important it is: “It’s what we do here,” said Rankin. “We have a quarterly meeting and sometimes monthly meetings; every meeting starts out with, ‘I’m proud of you guys for staying safe.’ And it always ends with: ‘I need you here and I can’t have you here if you’re injured. Just think and push forward on that.’” Rankin says he’s empowered employees to do something should they encounter an unsafe situation. “Anybody who is out in the factory is in charge of what happens there. If someone gets hurt we all take it personally, and we all work really hard to figure out ‘what, why and how,’ to make sure “ Your company’s safety culture is important to your customers, employees and it doesn’t happen again.” As a benefit to the company’s safety program, Rankin says he’s constantly upgrading machines and safety the entire business as a whole. An amaz- equipment and things such ing safety culture can positively impact as light curtains to something new. “If there’s a better way your business … Safety leaders in the to do it, I’ll do it,” explained everything for employees in ” organization must define what the culture is now and how they wish to transform it. — Lisa M. Buck, Workplace Safety Rankin. Rankin has also utilized the services of Laura HelmrichRhodes. “The biggest benefit of Laura is that she’s a different voice. She lays out a way they can understand and they can ask her questions.” Rankin says that’s important. “There are questions that they might not want to ask us because, ‘If Scott knows I don’t get this, it might be a problem.’ But they can ask her and if she doesn’t know the answer, she will get it.” Rankin says Rhodes is good at providing feedback, so “we know what might be missing and we can tie it into our next safety training session.” On the subject of the pandemic, Rankin says because they have a big factory, it was easy to practice social distancing and move tables away from each other in break room areas. He said they also retired some coiling machines that they were no longer using to create more distance in their coiling department. One of the important things that Vulcan upgraded was their ventilation system. Rankin says they changed all the air filters which made an immediate improvement to the air circulation system. “We have worked hard to get our air system to the highest point possible, in both the factory and in the office. From everything I had heard, if you can just move the air it’s got to be better.”
In regard to health protocols, Rankin said Vulcan changed its sick policy. “If someone feels sick we don’t want them coming to work. We don’t do testing here. We have a rapid testing facility right down the street. The main thing is I am asking employees to go see their doctor; I’m not going to play doctor at any point.”
On the subject of masks, Rankin says that once they were no longer mandatory, he made it strictly up to employees as to whether they want to wear a mask. “I’ve got a few people here who have worn a mask from day one and they still do. The majority of people don’t. If the person next to them is not feeling good or coughing, then they’ll put on a mask.”
As this issue of the magazine goes to press, the status of an OSHA mandate that any company with over 100 employees must have a fully vaccinated workforce or face fines was in limbo. Companies across the country sued to stop the mandate. Businesses would have had until Jan. 4, 2022, to require their indoor workers to be vaccinated against the coronavirus or get tested weekly. Violators could face fines of up to $14,000 per offense.
“As a fully vaccinated person, I do not understand how this can happen,” said Rankin, “and I am completely against this policy.” Rankin has more thoughts on the subject of vaccinations and the OSHA mandate that he’s happy to share with anyone who contacts him.
Plymouth Spring Co., Inc., Bristol, Connecticut
Plymouth Spring is located in the hotbed of New England spring manufacturing in Bristol, Connecticut, just 30 minutes southeast of Connecticut’s capitol city of Hartford.
Company president David DeVoe says Plymouth Spring has a safety committee that consists of one person from the seven departments that make up the company. “The committee also has a management representative, but it’s not me,” explained DeVoe. “I want employees to feel free to share things openly and to help make changes going forward.”
DeVoe says when there is a safety issue to address, it is presented to him for a response.
“Safety is a big deal here,” said DeVoe. It has been more than 3½ years since Plymouth Spring had a lost-time injury.
“We see the value in having large aisles so that people can move around safely here,” explained DeVoe. “We have many safety items within the plant, such as eye wash stations, heart monitors, etc. and we work with an occupational safety consultant to make sure we have everything employees need.”
DeVoe says having Laura Helmrich-Rhodes visit Plymouth Spring on a regular basis is a way for the company to add value.
“She will go to the shop to inspect and make recommendations,” explained DeVoe. “We do try to change it up each year and utilize Laura in different ways with training for our workers.”
DeVoe recognizes the expense of bringing Laura to Bristol, “but having her into our plant each year has helped lower our workers’ compensation insurance rates, in addition to helping provide a safe environment for our employees to work.”
According to DeVoe, the lower rates came because the work Rhodes completed helped lower the modification factor, or MOD rate, for Plymouth Spring. A MOD rate contributes to how much companies pay each month in workers’ compensation premiums. It is partly determined by the industry classification in which a company operates and how many OSHA recordables it accumulates.
DeVoe says the savings are nice, “But the most important thing is we are doing the right thing to make employees safe.”
We believe safety is important. “Employees make us money and help us produce our products. They are our future, so we need to keep them safe.”
With 55 employees to take care of, DeVoe believes it’s a big value for employees to come work at a safe company.
With the pandemic, Plymouth changed its shifts so there is a ½ hour in between and the company has time to clean.
In addition to investing in disinfectants and cleaning, DeVoe says Plymouth Spring provided hazard pay for eight weeks during the early part of the pandemic to thank its employees for working.
More recently DeVoe says the company provides $200 to employees to get vaccinated. “We do not mandate vaccination, and 80 percent of our workforce has done so voluntarily. We believe safety goes both ways.”
Building a Safety Culture
All the companies featured in the issue have worked hard to build a safety culture.
In her book “Workplace Safety,” Lisa M. Buck explains the benefits of this value.
“Your company’s safety culture is important to your customers, employees and the entire business as a whole. An amazing safety culture can positively impact your business by driving engagement, reducing workers’ compensation claims/costs, and attracting the very best talent. Safety leaders in the organization must define what the culture is now and how they wish to transform it.”
The time to build this type of “safety first” culture at your company is now, and if built right the foundation will last for many years, even in the midst of a pandemic. n