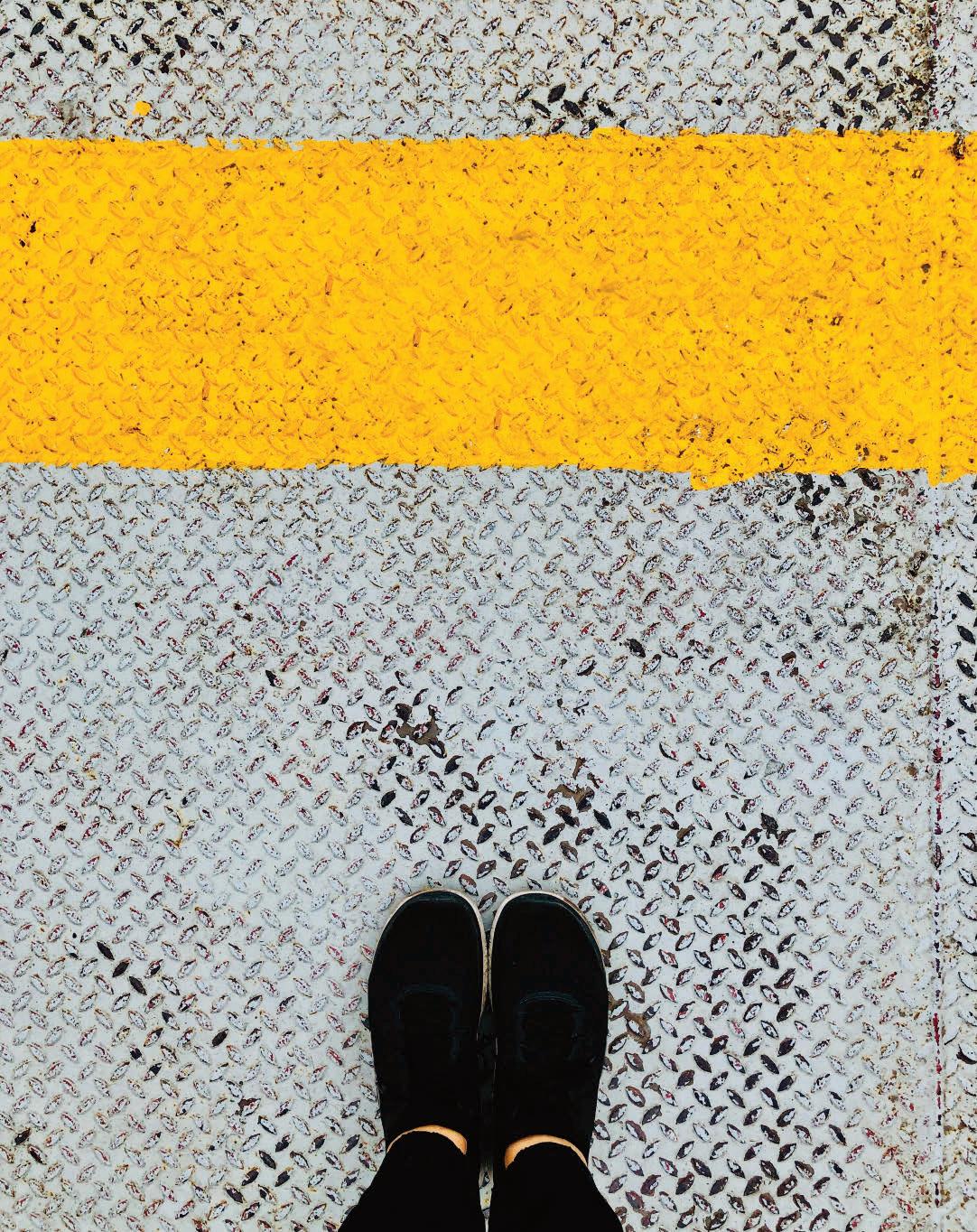
10 minute read
Safety First: An Interview with Dr. Laura Helmrich-Rhodes
SAFETY FIRST
An Interview with Dr. Laura Helmrich-Rhodes
By Gary McCoy
s this issue focuses on workplace safety, in this interview I review the landscape of today’s manufacturing environment with Dr. Laura Helmrich-Rhodes. Dr. Rhodes is well known toA A
Springs readers due to her role as an independent regulations compliance consultant for SMI and as a regular columnist. Dr. Rhodes has worked with SMI since Oct. 1, 2014, conducting safety audits, training classes and webinars. Safety audits are offered to SMI members as a means to prepare for Occupational
Safety and Health Administration (OSHA) inspections. Participating members have lowered incidents of lost-time injuries, lowered workers’ compensation costs and avoided large fines from government regulatory agencies. In addition to her work with SMI, she is a board-certified safety professional in Comprehensive Practice (CSP) and is an associate professor in the Safety Sciences department at
Indiana University of Pennsylvania. She continues to be active in private consulting through
Safety Geeks, LLC. In her free time, Dr. Rhodes enjoys travel, fly fishing, backpacking, tent camping and any outdoor fun. Dr. Rhodes earned her doctorate from the University of Pittsburgh, where her dissertation focused on the intersection of human resources and safety professions and the need for human resource professionals to gain graduate safety education. She holds a bachelor’s in safety sciences and a master’s degree in industrial and labor relations. On the following page is an edited version of my recent Q&A with Dr. Rhodes conducted via Zoom.
How has the practice of safety science changed in the last 30 years?
During my career, one of the important developments in the profession has been the addition of ‘environmental’ to the work of what the safety professional does. So now you’ll see the acronyms like EHS, environmental health and safety, or SHE, which is safety, health and environmental.
The work of the safety pro has really expanded. When I first started in this business, most of the time the safety director was somebody who had gotten hurt, or it was a maintenance person. Typically, it wasn’t a degreed safety professional. We are now seeing people who are academically prepared to be in this role.
We’re starting to see them more at the C-suite level. At my university we have graduates that are vice presidents of safety for large organizations. We have safety professionals that have become plant managers, along with people that have board of directors’ positions in major corporations.
The safety profession has been viewed differently over the past 10 to 20 years and it’s professionalized to a greater extent. When we have this conversation, we have to include the influence of major disasters.
Within the last 20 to 30 years, we have witnessed major tragedies like Imperial Sugar, which has brought about greater attention to dust explosions which impact the spring industry. The Bhopal and Texas City explosions brought more awareness for process safety and the importance of redundancy. Plus, workplace violence incidents have risen to the point where we now have to lock our doors and have a policy for visitors. All these tragedies have impacted the whole safety process.
If we look ahead, data is the future. Perception surveys, leading indicator data and inspection data help identify system inefficiencies and identify risk. I think that’s probably where the greatest change is going to happen in the future.
What benefits can a company see that places a high priority on workplace safety?
At the academic level, we are trying to develop good research in this area. For years, we have said, ‘We’re increasing productivity. We’re decreasing inefficiency.’ Which is true.
I don’t think we have come far enough on real, science-based research into the benefits. Anecdotally we do see increased efficiency and profitability and we have better employee engagement. I see a lot of benefits to it that need to be measured, so that we have more research beyond anecdotal evidence.
A lot of people only think of OSHA compliance as workplace safety. Why is that a shortsighted view?
The reality is that you could comply with every OSHA standard and someone still could be seriously hurt, or even killed. Even in this industry, we’ve had several near misses and catastrophic events. Creating a decision-making culture within individual spring manufacturing plants is better than using avoidance of OSHA as the goal.
If we look at OSHA compliance, sadly there is a segment of people who feel that fines are just a cost of doing business. The reality is that we can’t put a price on a person’s life or on their vigor. I’ve worked with a lot of companies who have had tragic events and it wouldn’t matter how much we fined that company. The heart hurt is far greater than any fine that they would experience.
It sounds like a mindset change, is what you’re talking about?
Yes, absolutely.
What permanent changes in workplace safety do you foresee as a result of the current pandemic?
There is definitely going to be a change in infectious disease prevention. We’re already hearing that from OSHA and the most respected epidemiologists. We have practices and OSHA regulations in place that are preventing infectious disease, and I think we’re going to see that carried out no matter what happens with COVID-19.
One of the things that I think is cool about this is, if you talk to a fourth grader, they know what the hierarchy of controls is (a globally recognized system for controlling hazards through five tiers of strategies, from elimination to prevention). They know that personal protective equipment is not the best strategy, but they have to use it. We can distance ourselves from people or we can put up a guard. My thought is that there might be employees that eventually come into your workplace that are going to have a much better understanding of the hierarchy of controls just because they’ve lived it. I see a greater hazard awareness for the next generation.
The other thing that I think will change, that is probably here to stay, is insurance loss control surveys. Employers used to have somebody come from the insurance company, sometimes every year or once every two years, to do a walkthrough of their facility. That has changed a lot during the pandemic to phone surveys or even FaceTime, where you carry a phone through your facility to show the loss control representative different areas of your business. I’m guessing that this type of approach is a lot less costly for the insurance company.
The downside of this trend for spring companies is the loss of the opportunity to talk to a safety professional. Many of our graduates ended up going to work for insurance companies in loss control. If your company does not have a full-time safety professional, traditionally the insurance company has provided you with an opportunity to have a face-to-face helper in your facility.
I’m a little concerned that spring companies might have to ask for more help from their insurance companies, and they deserve it. They’re paying a premium and they might have to be more vocal in asking for help.
What are successful companies doing to promote workplace safety?
From my perspective the recipe is really simple: you have to assign responsibility, accountability and authority. In other words, who’s going to do what, how are you going to measure what gets done and how will you allow individuals to make decisions?
There’s a safety maturity curve where you want your organization to move from a compliance framework to a proactive risk management standpoint. It starts with a written plan to assess risk, and then to the adoption of effective controls. Finally, you have to go back to make sure that they’re still working.
I don’t think that a lot of people understand that OSHA wants you to have these written programs. It’s not because they just want you to have something on paper. From a safety professional standpoint, you want that piece of paper to come alive.
For instance, here are some questions to consider. When you look at lockout/tagout, who’s going to be in charge? Who’s going to handle the training? How often is that training going to happen? How are we going to document that training? Who gets the last word on this? What’s the enforcement policy? Will we accept people working on live equipment? What is tolerable? How much authority do people have?
You put all this on paper, and then you go back annually to make sure it’s working.
Many SMI companies already hold regulatory compliance certifications. Why should they consider achieving the ISO 45001 international standard for occupational health and safety?
This is something that I’m actually very excited to try to push with SMI members who are already ISO 14001 or 9000 certified. That’s because they are already familiar with the ISO structure and understand the importance of that framework. They have procedures in place and are used to the concept of continuous improvement and have seen the benefit of it.
What this standard does is put safety into that same mindset of the ISO ‘plan–do–check–act’ cycle. It involves taking the safety ideas and making procedures for those and putting them in a similar format that has already worked before.
It’s a good way to put it all together, and it engages people.
What should a company do that is faced with an OSHA investigation?
It starts with having a written plan to follow for any type of inspector that might come on site to your facility. People need to know their responsibilities, accountabilities and authorities. Who’s going to greet them? Does that person know that they need to ask for the credentials of the OSHA inspector?
Inspectors are not offended when you ask for their credentials. We are in an era of workplace violence. I have stories to tell about imposters that have come to the door. You also want to make sure the inspectors are observing COVID-19 protocols.
Other considerations come from a planning standpoint. Where are you going to allow them to work? Do you have a
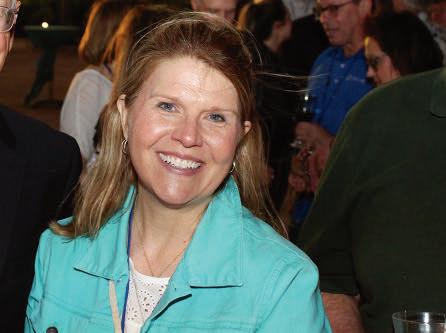
Dr. Laura Helmrich-Rhodes
conference room where there’s no other materials in that area that they would have access to?
Employers need to understand their rights and how inspections can vary. There’s a process for a formal complaint. There’s a process for them coming for a national emphasis program visit. There are different things that happen in an opening conference with OSHA, so you need to understand your rights. There are many things I can do to help SMI members before, during and after the inspection. If anybody’s involved in an inspection or wants to get themselves ready, I’m more than happy to help them.
I’ve discussed OSHA inspections in webinars and previous issues of Springs.
I think the key advice on preventing inspections from happening is to have some way for your employees to share their concerns with management. You definitely need to follow up with employees so that they know that you’re reacting to their concerns. If you can keep the potential for employee complaints down, you’re going to reduce the possibility that OSHA shows up to inspect your manufacturing facility.
What are some of the services you provide to SMI members?
I’ve been working with SMI for seven years and I primarily conduct safety audits and employee training. I also have been doing four free webinars per year for SMI members and at a nominal cost for non-members.
If you were to hire someone who has 30 years of experience, a doctorate and is a board-certified safety professional, it would be much more than the $1,000 that SMI charges for a safety audit. Employee training for SMI members is another $800 if you also book an audit.
Training is my greatest strength because it is part of what I teach at the university in how to make meaningful safety training sessions, how to keep adults engaged and, most importantly, how they can retain that information.
I believe SMI members get the best deal for safety audits and training that you could find anywhere.n