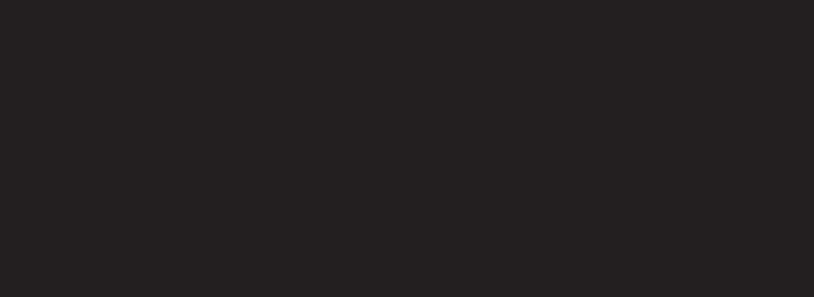
3 minute read
PERFORMANCE POLYMERS
HPP’s Project Coordinator, Megan Kitts explains how high performing polymer components fit into an ever-changing industry
High performance polymer fasteners are specialised plastics that have enhanced mechanical and thermal properties compared to standard polymers. One particular benefit offered by these fasteners is their lightweight properties. As polymerplastic fasteners are much lighter than metal fasteners, this makes them easy to handle and transport, while also reducing the weight of critical components in industries like aerospace and automotive for which weight reduction is vital.
One of the UK’s leading manufacturers and distributors of performance polymer fastening components, High Performance Polymer (HPP) stocks over one million polymer components used in multiple industries worldwide. These products play a key role in overcoming issues encountered with metallic or substandard polymer components, whether it be within the oil and gas, medical or automotive sectors.
One of the major issues that metallic screws can cause is galvanic corrosion, whereby when utilising two metals like aluminium and steel, one metal corrodes preferentially to another due to being exposed to a conductive solution such as water. Polymer components mitigate galvanic corrosion by insulating the metals while maintaining the performance necessary to keep up with the demand of the environment, whether this is high tensile or compressive strength, temperature or UV resistance.
As technology in industry advances, different characteristics are required within components to meet the project or product specification. Performance polymer components have a variety of favourable characteristics that ensure any project can continue as planned. One example of this is radio frequency (RF) transparency featured in PEEK. This characteristic has been proven to increase the range of remote electrical devices by reducing interference often found when using metal fasteners and componentry. HPP has provided a full PEEK solution for remote monitoring devices for oil pipelines that spanned large distances.
High performance polymer components have properties that far exceed the realms of what most people consider ‘plastic’ capable of. They can operate at high temperatures (360°C in some cases), have high tensile strength, are ultralow weight, have great insulting properties and chemical and corrosion resistance.
There are a multitude of polymer fasteners that specialise in meeting specific needs, so let’s look at some examples of HPP’s preferred polymer fastening components.

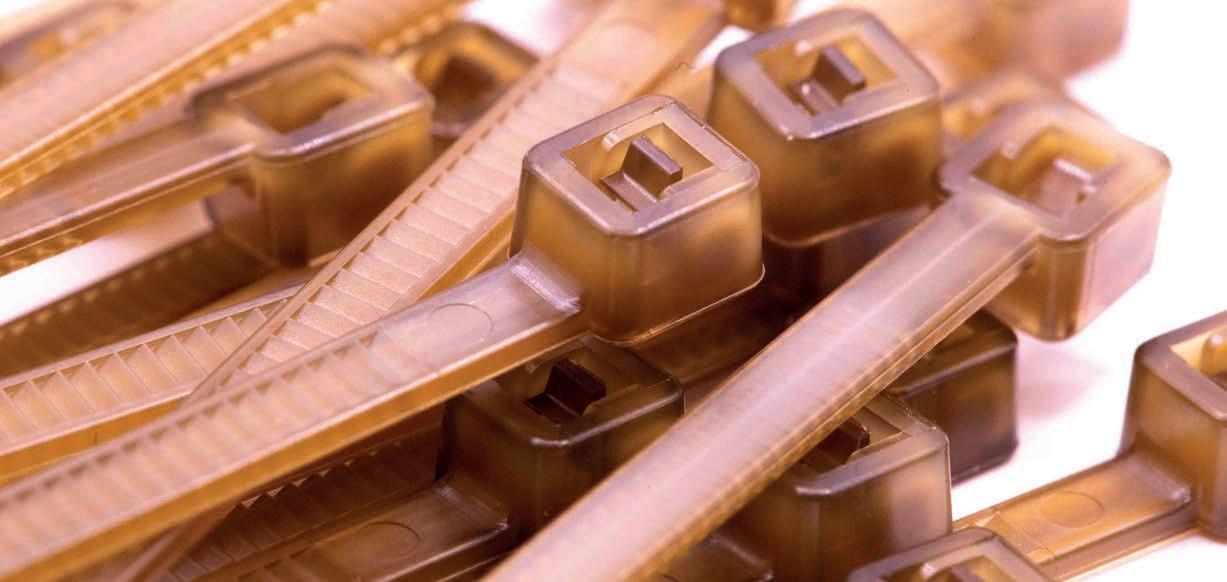
RENY
RENY is a high tensile strength Nylon. Its component property makeup is 50% glass fibre and 50% polyamide MXD6. When people think about a Nylon fastener, the first thing that comes to mind is a low strength, low quality and soft material that is inadequate for most industrial applications. RENY, however, is the opposite with a high tensile strength (285MPa), high bend strength (380MPa), and low tensile elongation at 2.1%.
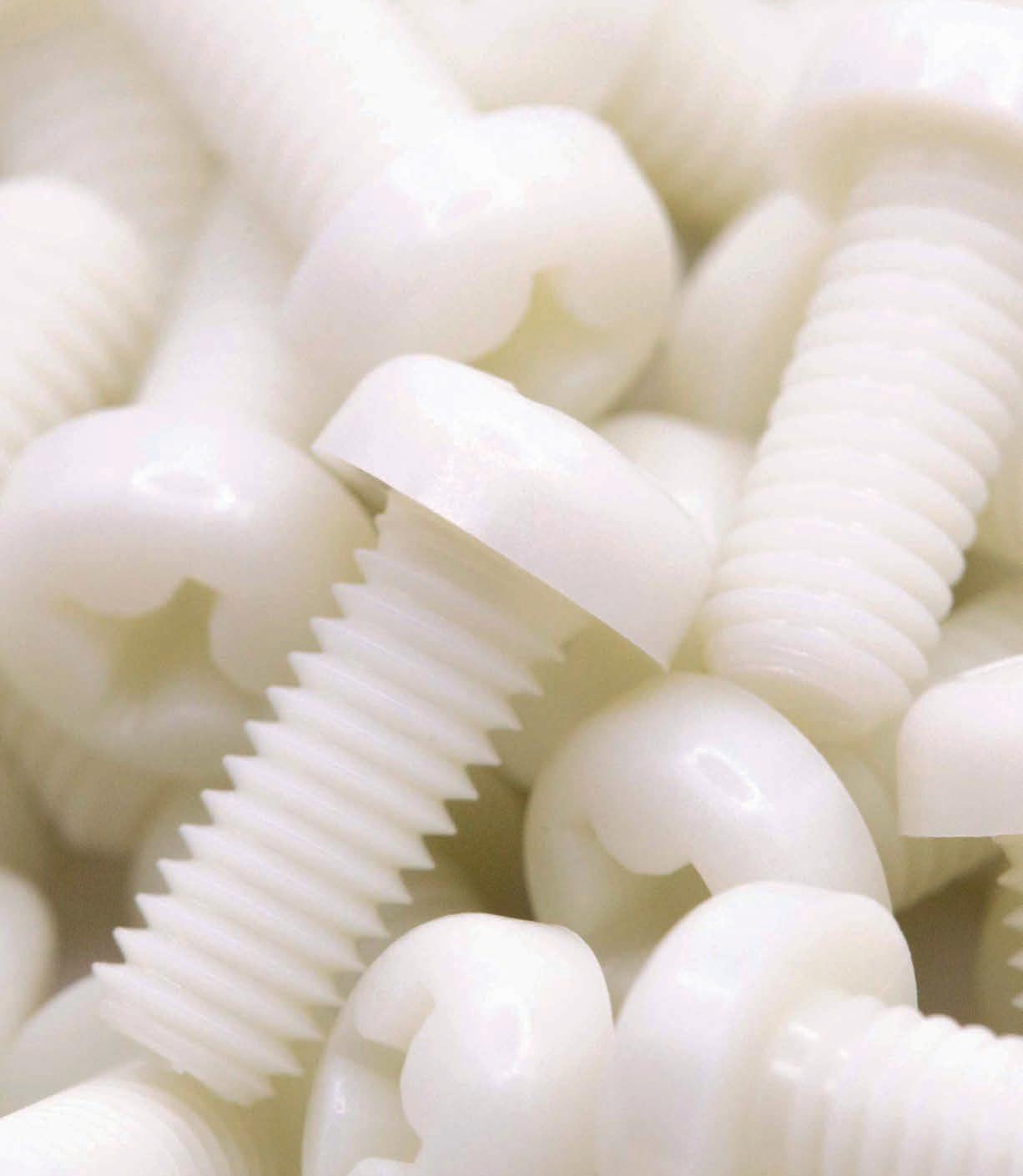
RENY fastening components are precisely manufactured to high tolerances and are particularly suited for applications that require high strength while encompassing the benefits of a polymer: insulating properties, chemical resistance, corrosion resistance and low thermal conductivity. Possible applications for RENY fasteners include flange bolting, robotics, automotive and aerospace applications.
Bespoke solutions
Offtheshelf polymer components are just one aspect of HPP’s operation; the company has vast experience in the engineering industry and offers bespoke component manufacture to a micron level of accuracy, which is particularly suited for life science and other niche applications. The firm also provides component and material consultancy to ensure the most appropriate material is used for a specific application.
This experience is embodied by the firm’s Director, Matthew HartleyJames, who worked as a mechanical engineer for a large scientific research facility for over seven years before launching HPP, often utilising PEEK and other performance polymer components for their radiation resistance, tensile strength and chemical compatibility.
As part of its offering, HPP ensures quality through a range of processes in line with its ISO 9001 certification. Raw material is traceable through to manufacture and all components are checked with high accuracy metrology equipment to ensure that they will meet the needs of any demanding environment.
While typical ‘plastic fasteners’ are thought of as an inferior and lowquality alternative, HPP’s polymer components are designed to meet the needs of the harshest environments and provide a dedicated solution to improving the reliability and functionality of products and devices used in industries worldwide.
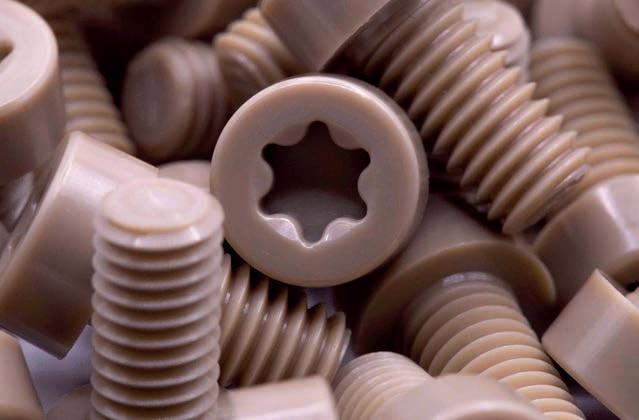
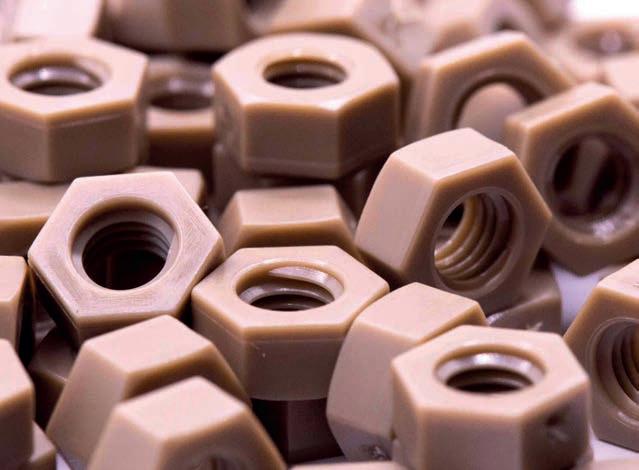
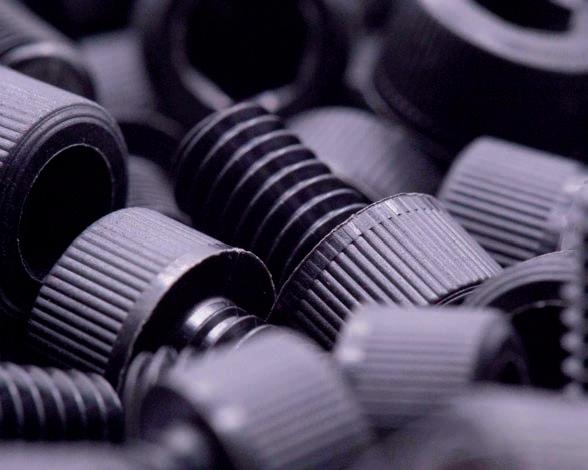
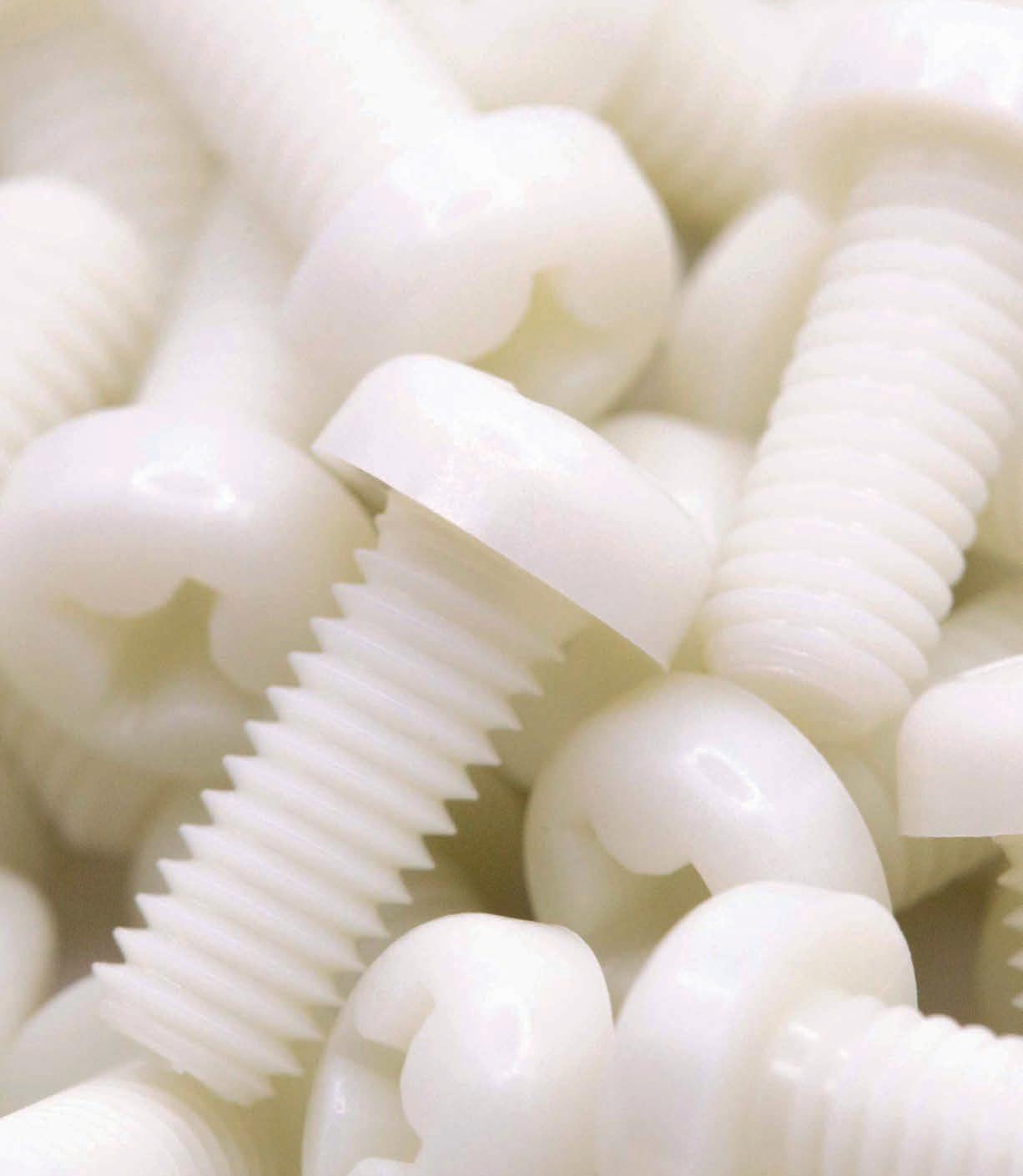
PEEK and PEEK GF30
Polyether Ether Ketone (PEEK) is a more commonly known high performing polymer material. It is one of the most versatile materials available for extreme applications and is used extensively in various industries from defence to oil and gas. PEEK is known for its ability to withstand high temperatures, exposure to a variety of chemicals and provide phenomenal insulating properties.
HPP uses Victrex 450G exclusively in all its standard PEEK components, with batch traceability and certificates of conformance available. If the specifications of PEEK are suitable for a particular application, but the tensile strength is too low, HPP offers a GF30 option. PEEK GF30 has a makeup of 70% PEEK and 30% glass fibre, drastically improving tensile and compressive strength while maintaining high temperature resistance and chemical resistance.
www.highperformancepolymer.co.uk
EJOT’s Application Engineers have access to prognosis and forecasting software that has proved pivotal for designers and can impact positively on prototype and testing budgets.
Bringing it together.