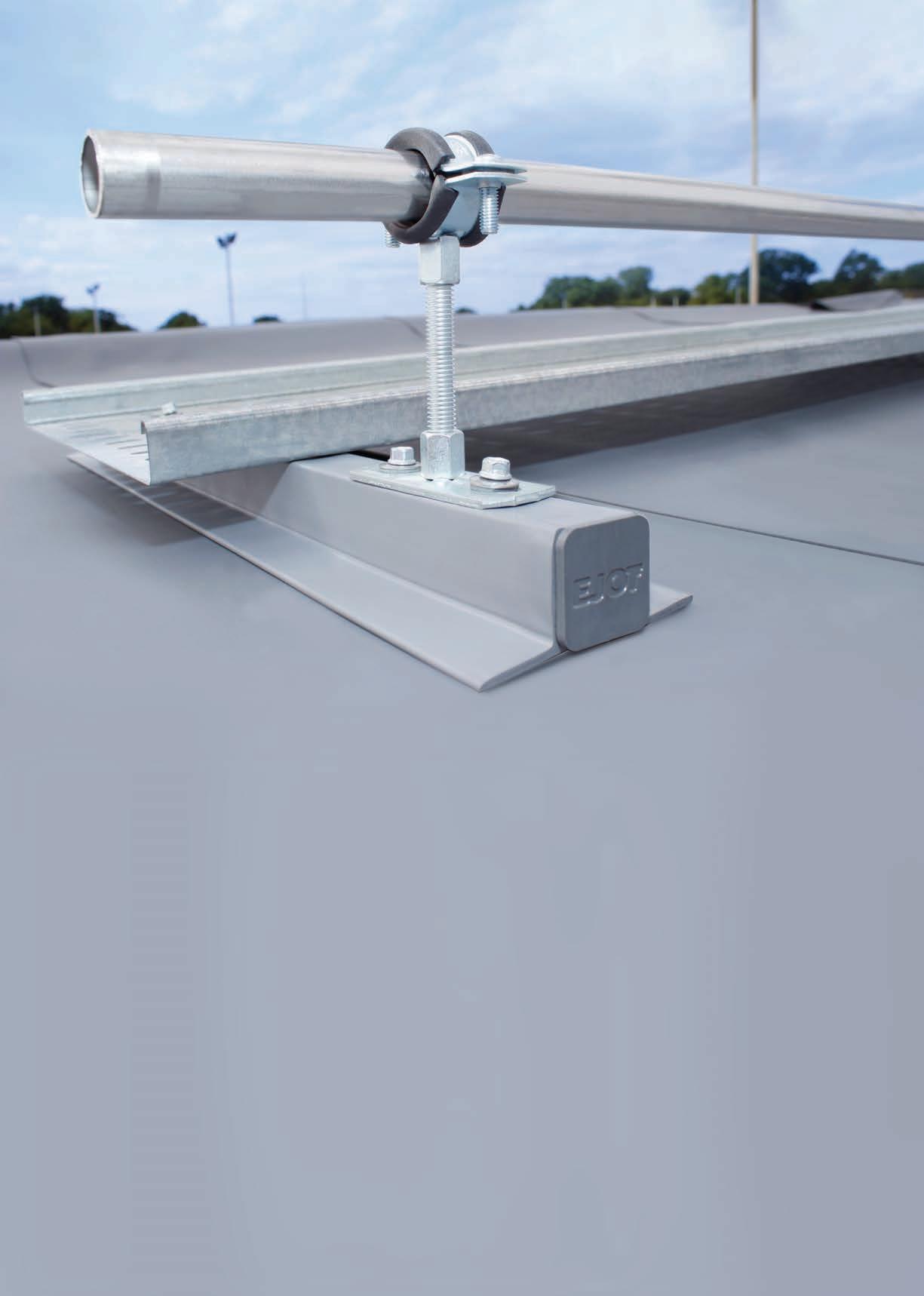
3 minute read
SUPPORTING SOLAR PV ADOPTION
How one innovative mechanical fixing system is supporting greater photovoltaic adoption without compromising flat roof performance
As energy efficiency and decarbonisation becomes increasingly important for the built environment, solar photovoltaic (PV) panels have become a familiar sight on buildings across the world. Although technological development in PV has largely focused on maximising the performance of panels and their associated electrical infrastructure to ensure the return on investment is attractive, innovation in how PV arrays are attached to buildings – especially when retrofitting – has also been critical.
One particular focus for PV attachment systems has been on flat roofs, which of course are commonplace on industrial, commercial, public sector and multioccupancy residential buildings. With this kind of roof, panels usually need to be positioned at an angle, so any attachment system effectively turns the flat roof into a pitched roof.
But, in an effort to make the building more sustainable through the installation of a rooftop PV array, sustainability could in fact be taking a backward step. This is because the performance and lifespan of the flat roof may inadvertently be reduced as a result of the way the PV panels are attached to the roof. The use of mechanical fixings can be problematic with flat roofing systems where a reinforced PVC membrane is incorporated to keep the building watertight and airtight. Inserting just one screw through this type of membrane can compromise its performance and invalidate the warranty.
As a result, we have seen the adoption of PV attachment systems which rely on ballast to hold them in place. But these are not without their drawbacks, especially the significant weight which they can add to the roof.
A combined fixing solution
One innovative mechanical fixing system from EJOT does, however, ensure the waterproof membrane remains complete, enabling the weight of the PV array to be spread across the roof area. Called EJObar, the product is a 2mm thick aluminium box section encapsulated in PVC which is hot air welded to the flat roof membrane to enable roofmounted elements to be mechanically fixed safely, unlike pointloaded alternative techniques.
EJObar was originally developed by EJOT’s UK R&D team alongside an OEM to provide a simple carrier system for flat roofs that eliminated workaround ‘rooftop’ solutions. Until it entered the market, it was not uncommon to see installers risk compromising the membrane integrity and safety in a variety of ‘makedo’ practices using everything from planks of wood to breeze blocks in an attempt to support rooftop ancillaries.
The hot air welding process is quick and delivers a secure fix with strong adhesion, making EJObar suitable for use with new and existing reinforced PVC single ply membrane roofs. It is approved for use by leading membrane manufacturers including Renolit, Soprema and Fatra, and 100% recyclable at the end of its long service life – another key factor in making the built environment more sustainable.

EJObar is designed to facilitate the use of mechanical fixings, in particular a class leading fastener from EJOT, the EJOFAST JF3 selfdrilling screw. This has a unique thread geometry that utilises displaced metal by driving it forward into the joint, with the added benefit of a piercepoint drill point which virtually eliminates the risk of ‘skating’. This reduces risk of an accidental tear to the membrane encapsulating EJObar.
The EJObar and EJOFAST JF3 combination ensures PV arrays can be attached to flat roofs with a system that is high strength and fast to install, with a quality end result easily achievable and virtually no swarf to clear. It offers assured structural integrity and a reliable design life, providing it has been correctly installed, which is important given the high wind loads the PV arrays can be subjected to.
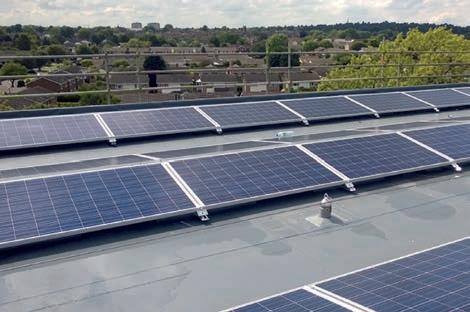
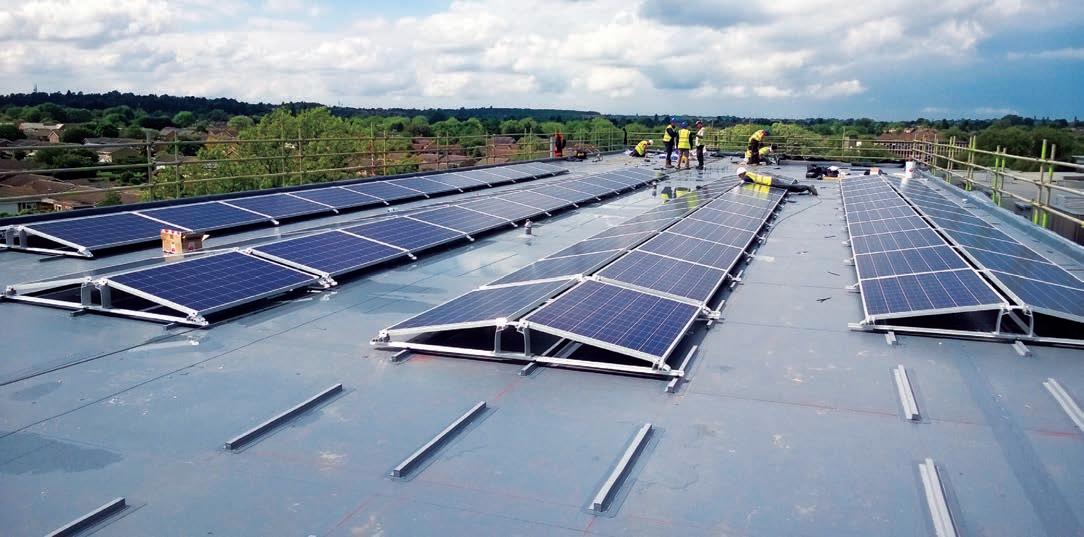
Unlocking new rooftop design potential www.ejot.co.uk
Such is the simplicity and versatility of EJObar that its application potential is growing continuously and globally, with most EJOT subsidiaries now selling the product to their local markets. From its M&E origins, the system is unlocking new potential to effectively address specific design challenges, including aesthetics as illustrated by one project in central London.
EJObar was specified by the architect redeveloping a building near Leicester Square to create a curved zinc façade for a penthouse apartment. A zinc strip system was fitted over a PVC singleply membrane, spanning two roof levels, arriving at the lower roof via a broad curve, providing durable protection from the elements with the benefit of concealed fixings.
Here, 3m EJObars were heat welded to the Bauder waterproofing membrane to create a fixing base for the concealed metal fixsystem, without penetrating the actual roofing membrane. Its uniformity, coupled with its strengthofweld attributes, contributed greatly to the maintained visual arc that flows from one roof level to the next.
Ultimately, wherever EJObar is used, it is extremely effective at expanding the weight distribution of rooftop elements, with simplicity, compatibility and cost effectiveness at the heart of the concept.