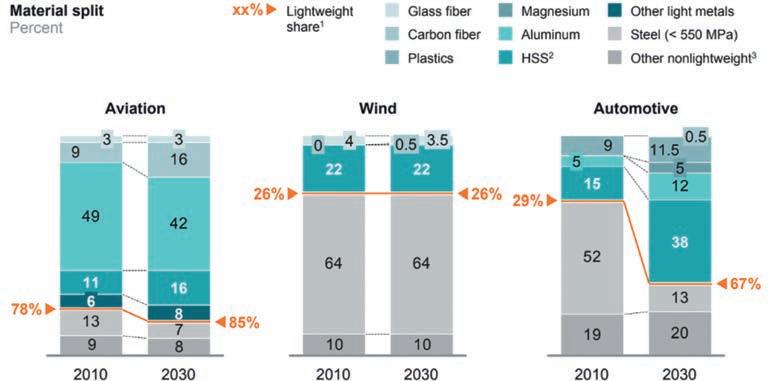
2 minute read
LEVEL UP WITH LIGHTWEIGHTING
How is the growing demand for lighter products affecting fastener materials and designs?
Lightweight materials and product design has long been an important consideration within many industries, from automotive and aviation to renewable energy and rail. In line with global trends towards reducing CO2 emissions and improving resource efficiency, the need for lighter and more efficient parts is becoming increasingly vital.
In light of this, the lightweighting of fastener designs is also evolving. Joining lightweight materials can present numerous challenges, from different panel thicknesses and retention requirements to corrosion and the need to reduce the complexity of fastening interfaces. As such, new fastener designs must meet the desired performance and reliability standards unique to each industry, prompting the need to develop more suitable mechanically and chemically compatible solutions.
Market demands
While an important factor for many industries, such as aerospace and electronics, lightweighting is particularly imperative for the automotive industry, as the weight of a part has a substantial impact on vehicle autonomy, fuel consumption and CO2 emissions. According to a recent report by McKinsey & Company, expected changes in materials use are likely to have the most significant impact on this sector with the rise of carbon fibre application and lighter metals such as aluminium and highstrength steel.
The rise of electric vehicles (EVs) is also accelerating the demand for lightweight fastening solutions. With added weight of batteries and associated electronics systems, the efficiency of these vehicles relies heavily on developing lighter parts.
Types of lightweighting
Lightweighting can be achieved through several different means. Direct lightweighting is where the fastener itself is made lighter than a traditional fastener might be. To accomplish this, manufacturers can opt to use a lighter weight material for the fastener, but must weigh this against the potential loss of other desirable mechanical properties like strength and resilience. Another way of achieving direct weight savings is to develop lightweight designs, such as the ‘lightening holes’ drilled out in aerospace applications to reduce mass without compromising on structural integrity.
Other ways to achieve weight savings is to utilise fasteners that possess improved technology that provides better or equal performance than a traditional fastener. New and innovative technologies can often provide performance improvements over older, more traditional fastening technologies, or can act as an enabling technology for revolutionary fastener and component designs.
Material choice matters
When developing lightweight fasteners for any industry, structural integrity and durability are paramount. To ensure this, any new component design must include specific design and validation processes to ensure it performs as intended in any given application.
Material choice is a big part of this, as performance can vary hugely depending on the chosen application and surrounding environmental conditions, while cost can often be another factor. Currently, there is an ongoing trend in the fastener industry of moving away from heavier steel materials and towards lighter alternatives such as aluminium, carbon fibre, nylon, plastic, titanium and multimaterial assemblies. These types of materials are allowing engineers to shed weight from fasteners without compromising their strength, durability or reliability. Meanwhile, new advances in manufacturing technologies and processes are enabling more innovative multimaterial assembly solutions, which can help to not only reduce weight but also to lower production costs.
In short, fasteners play an important role in lightweighting for a myriad of applications across different industries. Engineers and designers are continually developing new ideas and technologies to make parts lighter, some of which cannot be realised until a new fastening technology or design is developed to complement it. As such, lighter and more optimised fasteners are an integral part of lightweighting efforts across industry as it looks to reduce CO2 emissions and optimise efficiency.