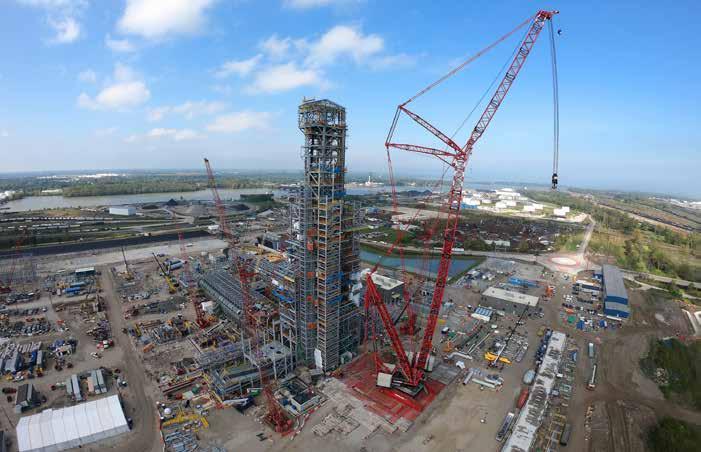
27 minute read
International Industry
Erection of the 457-foot furnace reactor tower for HBI project at Cleveland-Cliffs.
Cleveland-Cliffs details new HBI facility
Advertisement
US iron ore producer Cleveland-Cliffs has revealed additional information regar ding the status of the company‘s new hot-briquetted iron (HBI) facility under construction in Toledo, Ohio. CEO Lou renco Goncalves confirmed that Cleveland-Cliffs‘ new HBI plant is scheduled to begin production in the first half of the year. The company plans to price its HBI using US pig iron imports as a point of reference, with the goal to eventually re place imports with a US-made product.
Trade restrictions by WTO members continue at historically high levels. Between mid-October 2018 and mid-October 2019, the trade coverage of import-restrictive measures implemented by members was estimated at $747 billion. This is the hig hest trade coverage recorded since October 2012 and represents an increase of 27% compared to the figure recorded in the previous annual overview ($ 588 billion). WTO’s report notes that new trade restrictions and increasing trade tensions added to the uncertainty surrounding in ternational trade and the world economy. The main sectors targeted by the new import restrictions were mineral and fuel oils (17.7%), machinery and mecha nical appliances (13%), electrical machinery and parts thereof (11.7%) and precious metals (6%).
thyssenkrupp considers sale of plantbuilding activities
thyssenkrupp has started testing the waters for a potential sale of its Plant Technology unit. „We have started ad dressing the market, sending comprehensive information kits to parties interested,“ said CFO Johannes Dietsch at a conference call, noting that the kit re quires a declaration of confidentiality from the receiver. Group CEO Martina Merz pointed out that the group is trying several options simultaneaously „We have learned thinking in different scenarios. This may be confusing to observers, but for us the result is best when we ave more than one option, as the successful sale of Elevator Technolo gy has shown,“ she said. The unit builds coking plants for steelmakers, for exam ple for ArcelorMittal’s Tubarão works in Brazil. Other activities are plants and services for the cement, chemicals and fertiliser industries, as well as materials conveying machinery for the mining industry. In the last fiscal year, it achieved a revenue of €2.8 billion.
Liberty Steel lines up €2 billion in European
Liberty Steel has announced plans to invest €2 billion in its Continental Europe business, following its acquisition of the plants last summer. In doing that, the group puts „ a clear focus on carbon neu trality by 2030,” said Sanjeev Gupta, Executive Chairman of Liberty Steel parent GFG Alliance. The expenditure will cover the Romanian unit Liberty Galaţi with a €1 billion investment programme over ten years for major upgrades to its casters, rolling mills and coating lines, as well as plans to install an Electric Arc Furnace (EAF) to significantly reduce emissions and its dependency on imported natural resources, the group says. At Ostrava in the Czech Republic, a €750 million 10- year investment programme will allow the business to install new hybrid steelmaking technology - a first in Europe – and start a major modernisation of its rol ling mills. Liberty also plans a €100m investment at its Liege-Dudelange works, Source: Business Wire
to improve the quality, performance and output of galvanised steel products.
Swiss group proposes setting up steel plant in Andhra Pradesh
Swiss commodity trading group IMR Metallurgical Resources has proposed to invest in the construction of a major steel plant in YSR Kadapa district in the Indian state of Andhra Pradesh. This was disclo sed to information service Steelguru by the representatives of IMR Metallurgical who held discussions with the state’s chief minister Y.S. Jaganmohan Reddy. The chief minister said that there would be scope for improving industrialisation in YSR Kadapa district once the proposed steel plant comes up and added that the government was ready to provide all the basic infrastructure facilities. The chief minister said Krishnapatnam port, rail way connectivity and highways were readily available for transportation purposes.
Hebei plans multi-billiondollars steel projects
The northern Chinese province of Hebei has planned new steel projects worth 65.2 billion yuan ($9.4 billion). According to official government documents, pro jects to build new steel equipment include the relocation projects of Handan Iron &
Steel, Tianzhu Steel, and Huaxi Special Steel. They also include equipment up grade schemes for Xinhui Metallurgy, Jingye Steel and Xinji Aosen. Hebei Iron and Steel‘s (HBIS) Laoting base second phase project and Tangshan Yanyang Steel‘s cold rolled sheet project will also start construction this year. Hebei has furthermore established a special finan cing vehicle worth 50 billion yuan ($7.1 billion) to help get the local economy up and running again after being hit by coronavirus disruptions.
Severstal plans to invest approximately 110.5 billion rubles in 2020, focusing on the key areas of the Company’s updated strategy as disclosed during its Capital Mar kets Day in November 2019. However, as previously announced, should the market situation become less favourable, the com pany maintains the flexibility to reduce the volume by 30-40%, by postponing those projects that are the lowest priority, it says. The most significant projects in 2020 will be the construction of the new blast furnace #3 (expected to commence operations in 2020), the coking battery #11 (to be launched at full capacity in 2022, replacing batteries #8 and #9) and the flat steel production development programme, aimed at improving the company’s product mix.
Celsa begins construction of rolling mill in France Celsa Group has laid the first stone of the new rolling mill to be developed at the Celsa France facilities, located in the municipalities of Coucau and Tarnos, within the new Aquitaine re gion. The current Boucau-Tarnos steel mill „will go from making steel billets to making finshed products thus in creasing its competitiveness and profitability“, says Celsa’s president Francesc Rubiralta. The project will also enable the steelmaker to improve its presence in the French and Bene lux markets, he adds. The planned investment for the launch is estimated at around $67 million.
Outokumpu reviews its long products business
Outokumpu has initiated a strategic review of business area Long Prodcuts as part of its „process to determine opti mal long-term business mix“, the company says in a short statement. For this purpose Outokumpu will investigate multiple options regarding the busi ness area‘s future including opportunities for consolidation within the stainless long products markets. The strategic review is expected to be finalised at some point during the year 2020.
MPT International / March 2020 Outokumpu‘s Long Products business area had net sales of 707 million US-Dollars in 2019.

Aerial view on Nucor Steel Berkeley

Nucor receives tax breaks for facility expansion
US steel producer Nucor has received initial approval for tax breaks by Berkely County Council‘s Committee on Finance for a prospective expansion of $300 million to its local steel operations. The proposed agreement between the county and Nucor would slash the company‘s property tax rate at the facility by 4.5 percentage points from a 10.5 % rate to a reduced rate of 6 %, the newsletter Kallanish Steel reports. It further writes that Berkeley County is currently in competition with three other unnamed Nucor locations for a tentative expansi on. The proposed tax agreement includes information about Nucor‘s prospective plan for its Berkley facility, which includes a 250 million US-Dollars invest ment for equipment upgrades and a 40 million US-Dollars investment for cons truction. If approved by both parties, the expansion is expected to create an additional 50 jobs at Nucor within a five-year time period.
African Industries to launch integrated steelworks
Lagos-based African Industries plans to comission by end-2020 phase 1 of its prospective direct-reduced iron-based steelworks in Kaduna State. This infor mation comes from a Nigerian Investment Promotion Commission note. The coal-based DRI plant will be fed by iron ore beneficiated and pelletized at the same site. In recent years African Indus tries has acquired mining leases for iron ore in Kaduna. It expects to mine 5.4 million tonnes/year of the raw mate rial to feed its DRI plant. The firm will also construct a 36MW captive power plant that will generate power from the waste heat recovered from the integra ted steelworks. African Industries produces billet, rebar, wire rod, angles, BRC mesh and nails, exporting some output to other West African nations.
US-Steel unveils 2020 spending budget
US-Steel (USS) has unveiled the company‘s total capital spending budget for 2020. In a press release USS announced expected spending for the year to be ab out $875 million. Half of that is slated for strategic investment projects. In an conference call CEO David Burritt said the highest priority for USS is the com pletion of the second phase of expansion to its jointly owned Big River facility, which is projected for completion later this year. The expansion will cost an es timated $1.2 billion and intends to double hot-rolled steel production to 3.3 million short tons per year. Following this, USS will prioritise $175 million in upgrades to the endless casting and rol ling equipment at the company‘s Mon Valley facility in Pennsylvania. The pro ject of third highest priority is upgrades to the company‘s hot strip mill in Gary, Indiana, later this year.
Myanmar steelmakers seek investment
Myanmar’s finance and industry ministries are searching for foreign investors to revive a local steel mill in Mandalay province, the steel newslet ter Kallanish notes. The No. 1 Steel Mill in Myingyan is estimated to have 1.8 million tonnes per year steel capa city from two EAFs. In addition, the No. 2 Steel Mill in Pang Pet is also planning to attract foreign invest ments. A spokesman from the heavy industrial department says that near ly $53 million will be needed to complete the construction of the mill and then start operations. The govern ment is willing to consider different investment models such as public-pri vate partnership or the possibility of selling some production lines. The two mills were in the middle of a ma
jor upgrade when these projects were cancelled due to a budget review in 2017.
thyssenkrupp specifies investment volume in steel
thyssenkrupp AG has come up with tangible figures about the investments it intends in its steel operations. The group plans to spend some €500 milli on per year on a regular basis, plus an additional €800 million over the next six years, The German conglomerate used to invest €470m per year in its steel division. „The details of the spen dings are currently being worked out,“ its CFO Johannes Dietsch said, and emphasised that „each investment is meant to make an operation profitable by itself and independent from others.“ The group has just successfully sold its Elevetor Technology division, a deal from which it will receive €17 billion. It announced that details for internal investment will be revealed in May.
Steel Dynamics acquires Mexican recycler Zimmer Steel Dynamics, Inc. (SDI)today announced that as part of its raw material procurement strategy to support its new Texas f lat roll steel mill, the company has entered into a definiti ve agreement to acquire 100% of the equity interest of Zimmer, S.A. de C.V. („Zimmer“). Zimmer is head quartered in Monterrey, Mexico and operates a ferrous and nonferrous scrap metals recycling business. Zim mer‘s primary operations are comprised of six scrap processing facilities strategically positioned near high-volume industrial scrap sources located throughout Central and Northern Mexico. The company also operates several third-party scrap processing locations. These combi ned facilities currently ship approximately 500,000 tonnes of scrap annually and have an estimated annual processing capability of approximately 2 million tonnes.
GFG Alliance acquires Adhunik Metaliks to create Greensteel facility GFG Alliance, the parent group of Liberty Steel, has completed the strategic acquisi tion of Adhunik Metaliks Ltd (Adhunik) and Zion Steel Ltd (Zion) in cash deal worth $60 million. The transaction marks GFG’s entry into India.– one of the world’s fastest growing steel markets. GFG Alli ance says it will introduce its Greensteel model to revive the plants – combining steel recycling with low carbon and rene wable power sources – to create a more sustainable, competitive operation serving local markets. Adhunik is an integrated steel plant located at Chadrihariharpur near Rourkela in Odisha. The plant has both blast furnace and Electric Arc Furnace steel making capability with 0.5 million tonnes per annum capacity, and a 34MW captive power plant. Adhunik along with Zion Steel, its associated steel rolling faci lity, has a combined rolling capacity of 400k tonnes per annum. The sites produce products for the automotive, energy, engineering and oil & gas sectors.
Steel’s Premier Technology Event
4–7 May 2020 / Cleveland, Ohio, USA
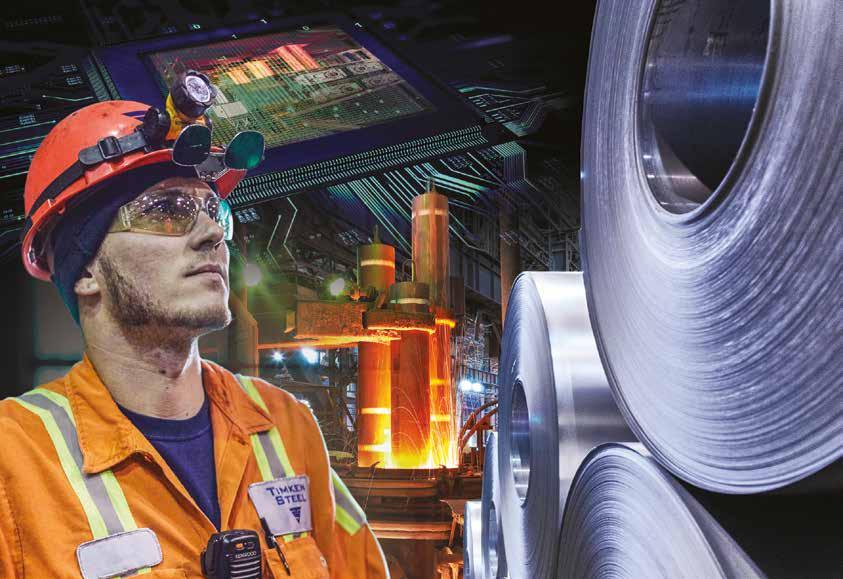
The Iron & Steel Technology Conference and Exposition
Americas CANADA ArcelorMittal Dofasco (AMD) has awarded SMS group the contract to supply a replacement 320-tonne KOBM converter and gear drive for its steel making plant in Hamilton, ON, Canada. The converter at ArcelorMittal Dofasco is considered the largest basic oxygen converter in North America. The pro ject goals are to replace the existing equipment, which is approaching its end of life, with new equipment incor porating the latest technological developments. One featured technology is the unique SMS group electro-hydraulic torque compensator, which is a system that actively reduces the resultant for ces generated by highly dynamic bottom blown converters. This will reduce the dynamic loading on the entire sys tem, with resulting increases in availability and life. The complete converter replacement is scheduled for the se cond quarter of 2021.
Automazioni Industriali Capita nio (AIC) has successfully commissioned the major rolling mill automation upgrade project at Gerdau’s plant in Selkirk, Canada. The scope of the project included the complete rolling mill automation starting from the reheating furnace exit until the cooling bed, including the rougher area, pendulum shear, continuous mill composed by 14 stands and 2 start/stop shears, inter mediate and dividing shears, a full complete cooling bed entry conveyor, braking slide and cooling bed. Strate gical motor drives were also replaced at site together with the automation upgrade to increase the production capacity of the mill. The first part of
Stopper-rod control system at US Steel
the upgrade has been commissioned and the second part of the upgrade is foreseen for the summer 2020 outage.
USA Danieli Centro Cranes will provide two EOT charging cranes with lifting capacity of 310(430)/100/25 short tons to North Star BlueScope Steel, Delta, OH. Danieli is supplying a meltshop pro ject featuring EAF and LF furnaces and fume treatment plant there. The customdesigned cranes will satisfy the local CMAA Specification 70 standards, and fo resees a 16-wheel bridge with end truck equalizing configuration. The arrange ment of bridge drives is an A4-type with “open” kinematic scheme (motor-gear box-external brake-wheel).Both cranes will be equipped with a regenerative sys tem that recovers the braking energy of all the movements. The first crane will be fully commissioned by July 2020 in line with the plant erection schedule, and the second crane will be started up by the end of October.
After successful installation and com missioning of Danieli mould-level and

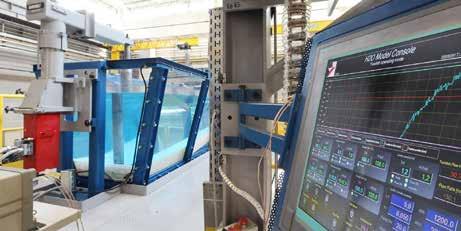
stopper-rod control packages on four strands, US Steel proceeds to revamp a third slab caster. At the end of 2016 US Steel entrusted Danieli to replace the stopper-rod control system together with the mould-level control sensors and automation at its Great Lakes Works and Gary Works. Both plants, which operate one double-strand slab caster and two single-strand slab casters (A-Line and B-Line), improved the cas ting process stability after the installation, the plantbuilder says Hy-Power electrohydraulic stopper actuator to re gulate the steel flow, eddy-current double-coil sensor for a precise measurement of the mould level, and Q-Level+ automation package for a fine control of the entire system (picture top).
Automazioni Industriali Capitanio (AIC) was chosen by Chicago Heights Steel to perform rolling mill upgrade with electrical and automation (E&A) supply in Chicago Heights (IL, USA) that allows the plant to improve the diagno stics and the flexibility of the automation system, to reduce the time to identify problems and their solutions, to decrea se unscheduled downtime and the maintenance cost. The scope of supply includes new drives, automation & HMI control system for the rolling mill, start ing rougher group and going through the bars takeout on the cooling beds. Asia CHINA
Shougang Jingtang successfully commissioned the new hot-dip gal vanizing line supplied by SMS group. The new line is especially equipped to produce high-strength grades with ten sile strengths of up to 1,350 MPa. The capacity is 360,000 tonnes per year of Photos: Danieli; SMS group
hot-dip galvanized steel strip, which will be used mainly in the automotive industry to produce structural parts and car body shells for lightweight cars. The first coil was produced on Novem ber 13, 2019. Right after the start-up Shougang Jingtang was able to produce 1,000 tonnes of sellable galvanized ma terial. A second campaign of 5,000 tonnes was produced in December 2019. The new hot-dip galvanizing line is the sixth strip processing line SMS group installed for Shougang Jingtang on Cao feidian Island, a man-made island offshore the Chinese province of Hebei.
Beihai Chengde Stainless Steel Co. (Beihai Chengde) achieved their full reduction program on their new Power X-HI 3-stand mill on HRAPL#5, excee ding 60 % reduction on 304 grades with white coil process, 55 % on series 200 black coil process. Subsequently, Beihai Chengde awarded Primetals Technolo gies with the Preliminary Acceptance certificate for the TCM only six months after rolling mill start-up. The 3-stand continuous tandem cold mill (TCM) was supplied to the Beihai plant in Guangxi Province. The rolling mill has a rated capacity of 600,000 tons of cold strip per year and is designed to produce 300 and 200 series steels as white and black coils. It is the first application of a Pow er X-HI mill for the direct processing of stainless black coils. The new mill relie ves the hot rolling mill and allows additional thickness reduction. The mill has been in operation since mid-2019.
Shandong Iron & Steel Group Co. Ltd., Rizhao, China, has awarded SMS group the final acceptance certificate, following the successful commissioning of its new continuous caster for ul trawide slabs. The single-strand caster is designed for an annual production of 1.5 million tonnes of steel slabs with widths of up to 3,250 millimeters and a thickness of 150 millimeters. This means the casting machine is able to cast the widest slabs in the world. It processes structural steels, and micro and low-alloy steel grades. Peritectic grades make up more than 45 percent of the overall production output. The slabs are hot charged to the Steckel mill which rolls them down to sheet and hot strip. Shandong Iron & Steel also orde red latest quality-enhancing digitalization solutions for the casting machine. The digital alignment assistant HD LASr (High Definition Laser Aligning System
The first slab produced on the new continuous casting line at Shandong
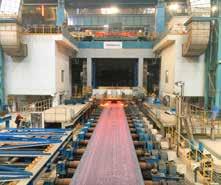
remote) developed by SMS group gua rantees, for example, that the shapes and segments are perfectly aligned.
Paul Wurth has been awarded with or ders for the supply and engineering of Sopreco Single Oven Pressure Con trol Systems for two top charging coke oven batteries. They are intended to be part of the new coke making plant of Xi angtan Iron & Steel in Xiangtan, Hunan province, in Central China. Each battery counts 50 coke ovens with a height of 7.3 meters equipped with Sopreco, Paul Wurth’s solution for individual oven pressure control and coke oven bat tery emission control. This is the second cokemaking technology project for Paul Wurth in China. The contractor Shan dong Province Metallurgical Engineering Co. Ltd (SDM), with whom Paul Wurth had concluded a cooperation agreement back in 2013, issued the orders. Based on this cooperation, top charging batteries of Jumbo type have been commissioned at Rizhao Iron & Steel in 2017/18.
Guangdong Shaoguan Iron & Steel, a unit of Baosteel group, has selected Friedrich Kocks for the supply of a RSB 370++ /4 in 5.0 design for its 490.000 t/a bar mill line. Shaoguan in tends to further expand and strengthen ist share in the SBQ sector for high qua lity engineering steels for the automotive industry. The RSB 370++/4 will produce straight bars step less in a range between Ø 17 to 80mm with a very clo se tolerance level and excellent surface onto the cooling bed. The RSB 5.0 will be located as a finishing unit after the roughing and intermediate mill, consis ting of 20 stands in H/V arrangement. Further Kocks scope of supply is a roll shop for offline stand and guide prepa ration as well as supervision for erection and commissioning. The start-up of the new RSB® is scheduled for 2021.
News in brief Hilco Industrial Acquisitions has purchased the rebar mill from Posco SS Vina, Vietnam, which was delivered by Danieli in 2015. It consists of a walking beam furnace, 18 roll stands and cold plate shears. The Vietnamese company intends to concentrate its remaining section mill on the manufacture of section products such as H-beams in the future. In December last year it was announced that the Japanese Yamato Kogyo Group had acquired a 49 percent stake in Posco SS Vina.
Primetals Technologies has received the Final Acceptance Certificate (FAC) for the modernized rolling mill for long products at JSW Steel Ltd. in Salem, India. The core of the modernization project was the new reversing roughing group with Red Ring stands, which enables to increase the size of the blooms to be processed to 220 mm. This consequently enables to extend the range of rolled products, both in terms of size and grade. With a high rigidity, the Red Ring stands also improve the rolling quality, with consequent reduction of defects and increase of metallic yield.
Automazioni Industriali Capitanio (AIC) was contracted to perform the revamping of the reheating furnace Level 1 combustion control system for the CMC Steel Florida mill in Jacksonville. One of the targets of this project is to reduce gas consumption and scale at the reheating furnace area.
UHT has received an order for a Granshot metal granulation unit to voestalpine Böhler Edelstahl. The granulation unit will be integrated in voestalpine Böhler Edelstahl’s new special steel plant project in Kapfenberg, Austria. Granshot metal granulation converts liquid metal into granules by rapid solidification in water. UHT will deliver a complete plant, including process engineering and automation.
INDIA
Primetals Technologies has commissioned a new Level 2 system at Jindal Stainless on AOD converter No. 1. In itia experiences in operation have shown that production processes would now be much more stable. The core of this level 2 process automation is a dy namic process model, which should enable both a preliminary calculation and an online simulation of the process. Ac cording to Primetals, errors could be avoided by pre-calculating the casts, as the feed materials can be prepared in good time. A further advantage of the modernization would also be a „Digital Twin“ through which all important pro cess data would be collected. This data can then be used for further optimizati on or new development.
JAPAN
The Techint-subsidiary Tenova was awarded a contract for the supply of a Consteel EAF (Electric Arc Furnace) for Nippon Steel Corporation. This new EAF is the first one for the Nippon Steel Group in Japan - and it will be in stalled at their Hirohata works. Production is targeted to start in the first half of the 2022 financial year. With this new installation, Hirohata plant wants to save about 400,000 tonnes per year of CO 2 emissions. According to Tenova, its exclusive Consteel technology is the only fully proven industrial process that continuously heats and feeds metallic charge into the EAF, while simulta neously keeping gaseous emissions under control.
SOUTH KOREA Andritz has received an order from South Korean Hyundai Steel for the supply of process equipment for Furna

ce 1 in the continuous galvanizing line at the Dangjin mill. The so-called „Selas DFF“ (Direct Fired Furnace) will elimina te current problems such as soot formation and cracks in the burner nozzle. The order also includes the engineering, supervision and commissioning. The project is scheduled to be completed in the fourth quarter of the year.
TAIWAN China Steel Machinery Company (CSMC), a subsidiary of Taiwanese steel producer China Steel Corporation (CSC) has placed an order with Primetals Technologies to supply staves for its blast furnace 2 at the company’s Kaohsi ung plant. The new staves are part of the third rebuild of blast furnace 2. The aim is to extend the furnace´s lifetime by a further 18 years. In future, five out of six blast furnaces operated by CSC and their subsidiary Dragon Steel will operate with equipment from Primetals Technologies. Final delivery is expected for end of June 2020.
VIETNAM On 25 November 2019, Dung Quat Blast Furnace #2 was successfully blown-in by Hoa Phat Steel. This is the second of four greenfield Danieli Corus Blast Furnaces that are being bu ilt under a single contract signed in Summer of 2017. Blast Furnace #1 was blown-in on 29 June 2019 – within 24 months after contract signature. Each of the four furnaces will have a 1,080- m³ working volume, and each is desig ned for an annual production of 1 million tons. The first two furnaces are in operation and Blast Furnace #3 and #4 are clearly distinguishable in the Dung Quat skyline. These furnaces will be commissioned within 2020.
UNITED ARAB EMIRATES Al Gharbia Pipe Company has successfully taken into operation its new LSAW (Longitudinal Submerged Arc Welded) pipe plant. The new LSAW large-diameter pipe production facility was built at the Khalifa Industrial Zone Abu Dhabi (KIZAD), by a consortium of Larsen & Toubro Limited and SMS group as the EPC (Engineering, Procu rement, Construction) partner. The plant is designed for a production capa city of 240,000 tonnes per year. The pipes to be produced on the LSAW facili ty supplied by SMS group, will mainly come in grades suitable for use as ons hore & offshore line pipes, including
LSAW large-diameter pipe mill at Al Gharbia Pipe Company
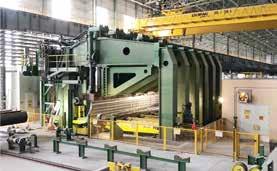
sour-gas applications. Al Gharbia is going to produce up to 12.2-meter-long pipes with outside diameters ranging from 18 to 56 inches. The maximum wall thickness is 44.5 millimeters; steel plates up to grade X80 can be processed.
Australia The Australian company Grange Resources recently replaced its belt conveyor at its Port Latte pellet plant with a steel plate conveyor from Aumund. Ac cording to the German conveyor engineers, this is designed for hot material (KZB-H) of up to 1,000 °C. This should enable the hot iron ore pellets to be transported continuously and troublefree from the shaft furnace to the coo ler. Grange Resources intends to use this measure to avoid regular plant shut downs. These were unavoidable because the belts of the old plant had to be re placed approximately every 40 days. This also increased production costs. Commissioning is expected to take place in May of this year. Europe ITALY
Danieli Automation has completed the upgrade of the 35-t AC EAF at AFCAcciaierie Fonderie Cividale, Italy. The AC electric arc furnace is now po wered by Q-ONE, a Danieli-patented system based on Insulated-Gate Bipolar Transistor (IGBT) power electronic tech nology. Two Q-ONE modules sized 12.5 kA each for a total power of 15MVA have been installed. Thanks to the new ly installed technology, arc stability was improved considerably, generating im provements in the overall melting process that, though preliminary, showed an initial saving of 5-10% energy con sumption and up to 25% power-on time reduction, while the expected 20% elec trode consumption reduction will require more heats to be confirmed. Photos: SMS group; SusanneLindholm
Feralpi Siderurgica has contracted Automazioni Industriali Capitanio (AIC) to perform a coil-handling upgrade at wire rod rolling mill in Lonato, Italy. Besides a complete revamping of the wire rod finishing area with electrical and au tomation (E&A) supply from laying head exit to coil management, the scope of the project also includes a new coil lowering station and the extension of the coil handling area with a new trimming ma chine designed according to an upgraded continuous process due to the installation of a new welder machine.
RUSSIA
No. 6 Blast Furnace at NLMK’s main site in Lipetsk, Russia, has been complete ly rebuilt during a furnace outage stretching from May until October. NLMK’s order awarded to Paul Wurth foresaw engineering, supply of equipment and site supervision related to the complete rebuild of BF6’s central unit, i.e. the blast furnace proper and directly attached sys tems and equipment. Paul Wurth’s scope of supply comprised the blast furnace shell, hearth lining with super-micropo rous carbon and ceramic cup, all other refractories, all cooling elements (copper and cast iron staves, copper cooling bo xes, tuyeres and tuyere coolers), low energy tuyere stocks and a completely new bustle pipe. The original Bell Less Top, Paul Wurth’s first ever reference in the former Soviet Union and in operation sin ce 1978, has been replaced completely by a new, state-of-the-art parallel-hopper type system (60 m 3 hopper volume) including the pressure equalizing and bleeder valves (picture top right).
Tenova LOI Thermprocess was re cently awarded an order from the JCS Pervouralsk Pipe Plant, Russia, for the delivery and installation of a conti nuous roller hearth system for stainless steel pipe. This extremely flexible furnace type is characterized by uniform heating, a definable holding time and subsequent material-specific cooling. The high temperature unifor mity and the low energy consumption of these systems ensure reproducible processes, which can be precisely adap ted to the desired heat treatment of the material. The drive sections can be opti mally matched to the respective annealing process. The heat treatment system for the JSC Pervouralsk Pipe Plant is de signed as a roller hearth furnace for the bright annealing of 2,000 kg/h of auste nitic stainless steel and nickel-based al
NLMK’s blast furnace 6 after complete relining
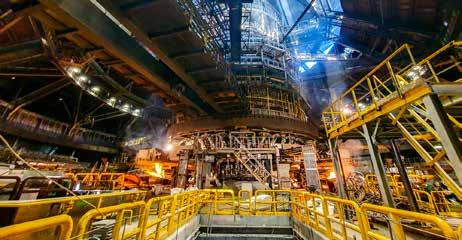
loy pipes. The solution annealing of these high-alloy steel grades is carried out in the temperature range of max. 1,100 °C to 1,200 °C. The tubes are heat-trea ted in this continuously operating roller hearth system using a 100% hydrogen atmosphere as process gas.
SWEDEN
ABB has been commissioned to supply a complete package for the automation and electrification of the HYBRIT pilot plant in Luleå, northern Sweden. The acronym of the so-called „Hydrogen Breakthrough Ironmaking Technology“ is a project to reduce CO 2 -emissions in the steel industry by replacing the use of coal within the production process with hydrogen. With this initiative, the companies SSAB, LKAB and Vatten fall have set themselves the goal of reducing Sweden‘s total carbon dioxide emissions by ten percent. To maximize the energy efficiency of the pilot plant, ABB will supply dry-insulated Resibloc transformers, which ABB claims have a low environmental impact. The compa ny is also integrating its ABB Ability system, including a software simulation so
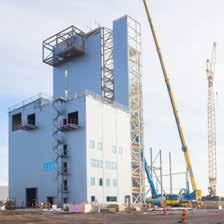
lution. This will allow users to learn and test processes in a safe offline environ ment, ABB says. This will enable rapid commissioning afterwards.
SPAIN For Acerinox Europa in Cádiz, Spain, SMS group has successfully commissio ned a torque retainer for the 120-ton AOD converter no. 2. The customer issu ed the final acceptance certificate shortly thereafter. The aim of the revamp, which was to minimize the destructive forces on the gear unit, bearings, and foundation when operating the AOD converter, was fully achieved in every respect. In additi on, the use of the new electrohydraulic torque retainer has significantly reduced uncontrolled vibrations in the gear unit and the converter vessel. The target va lues in terms of reducing torque were achieved under production conditions shortly after commissioning. SMS group supplied the torque retainer as a compact electrohydraulic unit.
UKRAINE ArcelorMittal Kryvyi Rih began hot tests of its new twin ladle furnace and continuous casting machine No. 2 (CCM2). In parallel, the company is bringing continuous casting machine No. 3 (CCM3) to design capacity. The construction of two new twin ladle furnace and CCM2, 3 with a total design capacity of 2.8 million tonnes per year is one of the key investment projects of the company. Its cost is over $160 million. The supplier of main technological equipment for construction of CCM-2 and 3 is SMS group. Overall, over 25 big internatio nal companies have become the suppliers of equipment, including Siemens, Weihua and Borthhold. Over a dozen different local contractors participated in this large-scale construction project.