
9 minute read
The competitive substitute of conventional minimills
It all began in the early 2000s in the USA, when a minimill customer asked Danieli to design an innovative mill to compete with the country’s big steelmakers in terms of operating costs and overall investment. The development of the Danieli MicromillMI.DA-technology followed from the successful application of the endless casting and rolling technology to the production of spooled coils and wire rod, rebars and smooth rounds.
Advertisement
MI.DA. size evolution from a single, 300,000-tpy co-rolling line into two 1.5 Mtpy twin co-rolling lines
AUTHOR: Andrea De Luca, Danieli
CONTACT:Email: a.deluca@danieli.it
Today, for Danieli the MI.DA. technology is a strategic product and a primary element of its vision of the near future. With the Twin-MI. DA.-configuration it is possible to design and supply a large-scale micromill capable of producing up to 1.5 Mton of finished products in endless configuration, with very high efficiency both in terms of environmental sustainability and energy savings to minimize CO 2 emissions, as well as to preserve natural resources. The MI.DA. was initially conceived as a regional plant capable of producing up to 300,000 tpy, equipped with a single rolling line with a maximum hourly productivity of 50 tons. It was designed to meet the demand of a limited area surrounding the plant, with more competitive operating costs compared to traditional minimills of greater size. In the past decade, the MI.DA. technology made it possible to define new milestones in the progress of minimills, and to achieve goals that led Danieli to consolidate its technological position in the endless casting and rolling process, a development that started in 1998 with the ABS Luna plant. Since then both process and technology have been consolidated and several successes have been achieved, starting with CMC Arizona in 2009, passing through the latest startup of the two Egyptian Steel MI.DA. facilities for IIC in 2016 and NPSS in 2017, and the CMC #2 plant early in 2018.
Through the years Danieli has been able to cast steadily at speeds up to 7.0 m/min with even higher speed peaks, as well as to increase the overall process yield to 99% with 94% plant uptime. Now, thanks to the latest technological developments, Danieli ECR Endless Casting and Rolling process is a well-proven, reliable and cost-efficient way to produce rebar in bars, spooled coils and wirerod, and is presumably going to completely supersede the conventional minimill concept, mainly due to the revolutionary introduction of the twinstrand application to produce up to 1.5 Mtpy of finished products to match the ever-increasing market demand. In the last two years Danieli has sold six MI.DA. plants with production capacity varying from 300,000 tpy up to 1.4 Mtpy, as a prompt response to ever-increasing demand for plants with higher productivity, larger product range and higher level of automation.
Today, in China – a country of big numbers – the regional steelmaking concept is being expanded to meet customers demand for maximized production, while maintaining the consolidated operational advantages of MI.DA.
Key Technologies Such a productivity can be achieved due to the application of the latest FastCast Technology which is the new generation of continuous casting machines with increasingly competitive transformation costs. The Eco Power Mould is a further development of the Power Mould concept with the following improvements: • New geometry of the cooling channels with higher thermal exchange • Lower overall Cu thickness • New coating layer to improve rigidity • Reduced off-corner cracks resulting in increased sub-surface quality
Additional stengthening coating

Sealing coating
Eco Power Mould TM copper alloy
ECO Power mould design
• Improved cooling system • Adaptive heat transfer • Up to 60,000 t service life • Reduced media consumption • Easy to install on existing conticasters
The combination of the cartridge-type Eco PowerMould with the latest design of the FastCast Cube oscillator characterized by high stiffness, low oscillation mass and inertia for higher frequencies in oscillation, bearing-free suspension system and maintenance-free philosophy, has made it possible to reach the casting speed performance of up to 7.2 m/min, which is equivalent to a productivity of approximately 56.6 t/h for 130x130 mm square sections on a single casting strand and up to 120 t/h for larger sections.
Hy-Power drive The high frequency in oscillation is achieved through the revolutionary Hy-Power drive, which is a hydrostatically actuated system installed on board of the hydraulic cylinder and fed by just one simple electric cable, replacing the
standard hydraulic system comprised of hydraulic unit, accumulators, servo-valves and hydraulic interconnecting piping.
Plant description Guilin Pinggang Iron & Steel is equipped with one co-rolling line to produce 700,000 tpy of ribbed wirerod and a second line to produce 700,000 tpy of rebars. While the Pinggang production of both straight rebars and wirerod products will start right from the beginning on the two endless casting and rolling lines, Shanxi Jianbang plant initially will utilize only one of the two straight rebar lines, while the second line will be started up in a later phase.
Both plants will be located within existing steel complexes: At Guilin Pinggang liquid steel will come from a scrapbased EAF, while at Shanxi Jianbang liquid steel will come from a BF-BOF shop. These aspects show the flexibility in terms of liquid steel sources allowed by the MI.DA. technology. In both projects, the rolling mills are configured with an upstream induction heater for billet temperature equalization, 20 H/V hou
Hydraulic pump
Coupling
Brushless motor

Hydraulic block
singless rolling stands, apron line and DRB-Direct Rolling & Bundling system, as well as wirerod line, with finishing areas according to their configurations. Starting from 190-mm square billets cast on the 12-m radius conticasters, Guilin Pinggang will produce straight rebars from 10 to 16 mm with DRB, from 20 to 28 mm with apron line, and ribbed wire rod from 6 to 12 mm.
Process With a dedicated and optimized chemistry, it is possible to minimize and even avoid the use of alloying elements starting from low-carbon and low-manganese steel through low surface-temperature rolling. In this way the low mechanical properties that result from poor chemistry are balanced by the microstructure obtained via the UFG-Ultra Fine Grain process. Both plants will adopt the UFG process that promotes a very fine microstructure and enhanced final mechanical properties, minimizing or even avoiding the need for alloying elements, to comply with the Chinese regulations for structural steel, i.e., martensitic-free structure products with higher ductility, which can guarantee better performances in seismic regions.
Grain-size-controlled grades can ensure high stress ratios and Agt values thanks to a dedicated controlled temperature rolling strategy. With the UFG process it is possible to obtain a grain-size definition from 5 to 1 µm, which makes it possible to have a material with higher ductility because the lower grainsize prevents any potential crack from propagating. Energy Savings & Environmental Sustainability The current production process of structural steel for construction pur
Twin MI.DA. Pinggang plant layout configuration
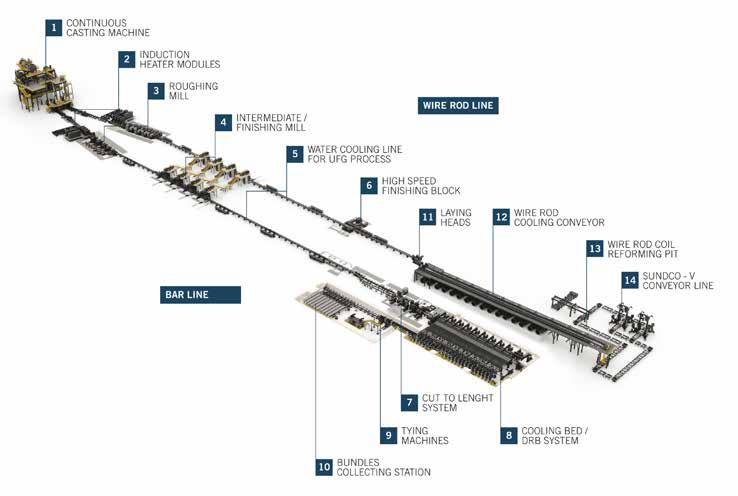
poses is going to be drastically changed, as is already happening in the USA, as well as in most countries like China that are becoming increasingly aware of the environmental impact and starting to minimize CO 2 emissions and preserve natural re sources. In this regard, China is progressively replacing the existing blast furnaces with the lower-polluting EAFs, avoiding the use of RHF for billet reheating from ambient temperature to more than 1100 °C before entering the rolling mill.
The complete absence of RHF in our ECR process avoids a huge waste of energy and gives net savings in terms of NG consumption of about 30 Nm3/ ton, equivalent to approximately 300 kWh/ton which corresponds to a reduction in CO 2 emissions on the order of 100 kg/t.Twin MI.DA. plants can generate a considerable reduction of about 150,000 ton per year in CO 2 emissions, corresponding to 75,000 circulating cars.
Industry 4.0 The ECR process has been constantly supported through the years by a strategy that aims to guarantee performance in terms of CapEx and OpEx, thanks also to the wide application of digital technologies with the aim of transforming conventional plants into Smart Plants. A Smart Plant constitutes a safe, flexible, efficient and environmentally friendly manufacturing concept based on the extensive digitalization of processes, full integration of cybernetics

Standard process microstructure and strong interconnection between humans and intelligent artificial systems. Increased automation complexity requires a different approach to assist operators in realizing the full potential of a Smart Plant.
In this regard, the 3Q Digital Pulpit provides a full “soft-desk”, totally based on computer screens through which the operator can both monitor the plant and operate it, in an ergonomical and userfriendly approach.
Summary The MI.DA. plant size and configuration has evolved continuously and steadily over the years. It has taken just a few years for it to grow from its original size of 300,000 tpy up to today’s 1.5 Mtpy production capacity through the
UFG treatment microstructure
3Q Digital Pulpit
development of the TWIN MI.DA. configuration. Advanced automation and digital solutions, fully integrated and optimized into the MI.DA. ecosystem, have led to a broad flow of information to support operators in their decision making and to replace them even in the most uncertain and dusty places. This makes the MI.DA. concept, in combination with the E.C.R. process, a proven and reliable technology to meet the market demand for high efficiency and energy savings in the production of reinforcing steel long products, both straight and coiled coils, including wire coils.

JianBang Group - China Pinggang Group - China ETRHB - Algeria Nucor Corp. - USA MENA region plant Asia region plant Nucor Corp. - USA MENA region plant VIJA - Vietnam Dana Y - Vietnam NPSS - Egypt CMC OK - USA MENA region plant IIC - Egypt CMC Arizona - USA Sidenor Sovel - Greece

MI.DA. productivity evolution 2007 Year of start-up 2020 300.000 t Yearly capacity 1.600.00 t 190x190 190x190 200x200 130x130 160x160 140x140 130x130 160x160 150x150 130x130 165x165 130x130 130x130 165x165 130x130 140x140
The key
to success

The supplier directory of the steel industry in a new edition
• Current overview of international delivery contacts in 27 categories and 120 sections
THE KEY TO STEEL INDUSTRY SUPPLIERS 2019
THE KEY TO STEEL INDUSTRY SUPPLIERS 2019
• Leading reference work for producers from the iron and steel, supplier and processing industries
