
12 minute read
Ilva: A healing plan for the Italian Patient
The operation of the technically obsolete Ilva steelworks is running in the background. The Tamburi workers‘ quarter, in the foreground, is one of the most polluted quarters of Taranto.
A healing plan for the Italian patient
Advertisement
The struggle to save the Italian works known as Ilva eventually has come to a promising result. ArcelorMittal, which has been the owner of Europe‘s largest steelmaking site, and some months ago threatened to waive its ownership, in the first week of March struck a new agreement with the Italian government.
AUTHOR: Niklas Reiprich O n 4 March, ArcelorMittal announced that its Italian unit, AM InvestCo, and the Ilva commissioners signed an amendment to the original lease and purchase agreement for the steelworks. This now outlines the terms for significant investment by Italian state-sponsored entities into AM InvestCo, thereby forming the basis for an important new partnership between ArcelorMittal and the Italian government. The equity investment by the Italian government in Ilva, to be executed by 30 November 2020, will be at least equal to AM InvestCo‘s remaining liabilities against the original purchase price for Ilva, says ArcelorMittal in a press release.
The Amendment Agreement between ArcelorMittal and the Italian government is structured around a new indus
ArcelorMittal‘s employees point towards the ongoing work of the group on a roofing of the Ilva coal and iron ore dumps. The group has invested 300 million euros in this measure.

trial plan for Ilva, which involves investment in lower-carbon steelmaking technologies. The core is the construction of a DRI facility to be funded and operated by third-party investors and an EAF to be constructed by AM InvestCo.
Also, the European Green Deal, which the European Commission presented at the end of last year, offers the Italian state the opportunity to demand up to EUR 4 billion for the ecological rehabilitation of the heavily polluting Ilva steelworks. This was confirmed by David Sassoli, the Italian president of the European Parliament. The support could further ac
celerate the investment of the Italian state in the company, in partnership with ArcelorMittal.
Long chain of problems The relationship between the Ilva steelworks, the Italian government and European steelmaker ArcelorMittal has been a subject of much debate. In 2018, the ArcelorMittal won a tender procedure by the Italian government for Ilva and subsequently announced its intention to take over the unprofitable steelworks with around 10,000 employees. Including the purchase price, EUR 4.2 billion were to be invested. MPT International already summarised the concrete measures ArcelorMittal has lined up in issue 06/2019. Among them was the enclosing of the raw materials yard, the transformation of the environmental performance of the coke batteries, a modernisation of the sinter plant and proper rainwater runoff.
At the beginning of November last year, ArcelorMittal paused and announced its intention to withdraw from Ilva. This was met with strong protest from the Italian government, and both parties decided to make another attempt to save the troubled plant. First details about the plan involved the ramp-up of production from the 6 million tonnes per year suggested by ArcelorMittal, to 8 million tonnes per year. However, for this purpose—and in favour of the high investments—the group projected to cut almost 4,700 jobs at the Ilva plant over the next three years. This was not acceptable to the Italian authorities. Job security vs environmental protection Ilva’s employees and trade unionists in Taranto demonstrated their rejection of the extensive plans for job cuts and went on strike shortly afterwards. Ilva is considered the largest employer in the region, and around 15,000 families would be affected by a shutdown.
But these same families also complain about the devastating environmental impact of Ilva. For decades, black coal dust and the red dust of the iron ore dumps trickle down on the residential areas of Taranto. Especially residents of the nearby Tamburi workers’ quarter have for years been demanding a clean-up of the works. This environmental disaster has brought many managers and politicians to court in the past, according to a short study by the European Parliament.
The story behind Ilva The Ilva steelworks was opened in 1965 by a state-controlled company, which was temporarily known as Italsider. Ilva was built in the southern Italian city of Taranto, located in the Apulia region of Italy, with almost 200,000 inhabitants. The fact that a large, emission-intensive industrial site was built near residential areas is attributed to the industrial development model prevailing at the time. In 1995, the plant was sold to Riva, a privately-owned Italian steel company. Due to massive environmental violations, a receiver was appointed by government decree in June 2013 to clean up the plant in Taranto. In the same month, the company was split organisationally into Ilva SpA and Riva Forni Elettrici SpA. The receivership has continued until this day.


The idled blast furnace at ArcelorMittal Krakow is about to be restarted to fill in for a reline at ArcelorMittal Gent
Blast furnace closures – Time to idle, time to blow in
Last year has seen the idling of many blast furnaces in various parts of the world. In addition to the temporary shutdowns for scheduled maintenance/relining, many more were taken out of operation for economic reasons.
AUTHOR: Christian Köhl T he decision to idle a blast furnace in times of slackening demand is not an easy one. Blast furnaces are made to run, best at full capacity. Any interruption causes technical costs that can be higher than the loss of production and sales. And it is always a delicate decision for the people in charge. Have we assessed the market properly? Is there no alternative? Will the economic lull last long enough to justify a stoppage? Why should we when others don’t? Then there are the technical challenges of shutting down and restarting at a later date, both serious interferences of plant operation. In this article, we address some of these issues.
Insufficient data It is by no means clear how many blast furnaces have been idled as a measure
in a bad market. Worldsteelorg, for example, does not collect that kind of data, citing antitrust reasons. The most complete data is available in Europe is by Eurofer. In North and South America, there is some data by AISI and Alacero, but not necessarily the full picture. In Asia, it is virtually impossible to obtain an authoritative impression that’s comprehensive and satisfactory.
ArcelorMittal, for example, is relatively open about its closures, but still refrains from giving the full picture. “The last formal disclosure we made on blast furnaces was when we announced our Q3 results, in November 2019. At the time, we said that for Q4 2019, we would operate 41 out of 51 blast furnaces worldwide,” its statement reads. The company refrains from giving details on individual projects, like a relining at Gent in Belgium, which is supposed to be taken off-stream for some time at some point this year, but when is not quite clear yet.
One of few announcements made public in Asia came from Nippon Steel Nisshin. According to a press release, the company decided “to bank”* its no. 2 blast furnace at the Kure Works around mid-February 2020. Two blast furnaces have been operating at a low capacity after a fire accident at the Kure Works in August 2019, which, together with the deteriorating demand for steel, caused for the company to decide to put a blast furnace on pause. (*The company defines “banking” as measures to temporarily stop blast furnace production but make it possible to restart production at a later date by stopping the air blast f low.)
Plants that had blast furnaces idled for economic reasons: (List is subject to change; closures may have been temporary)
Europe • ArcelorMittal Krakow, Poland • ArcelorMittal Kryvyi Rih, Ukraine • ArcelorMittal Bremen, Germany • ArcelorMittal Taranto (possibly delayed) • Salzgitter AG, Germany • Liberty Ostrava, Czech Republic • Acciaierie Bertoli Safau (ABS) in Sisak, Croatia • ArcelorMittal Dunkirk • U.S. Steel Kosice, Slovakia • SSAB Raahe, Finland • SSAB Oxelösund, Sweden
North America • U.S. Steel at Gary Works, Indiana • U.S. Steel at Great Lakes Works in Michigan

EU Steel Industry Situation
• AK Steel in Ashland, Kentucky • ArcelorMittal Indiana Harbour West
Latin America • Altos Hornos de México (Ahmsa) • ArcelorMittal Tubarão, Brazil (+ possibly one or two other companies in Brazil)
Africa • ArcelorMittal South Africa in Vanderbijlpark
Economic and technical challenges of idling and restarting a blast furnace (BF)
Source: Company and press announcements A brief look at what to keep in mind when deciding. By Aurelio Braconi, senior manager Circular Economy & Raw Materials at Eurofer. I t’s not easy with blast furnaces (BFs), as even only reducing the production means to modify the thermal profiles. To stop a BF, you need to gradually reduce volumes, the daily output of hot metal and then give the BF time to adjust. This requires three months. The bricks in the BF need time to cool down gradually. They are a critical part of this process. If the process goes even a little bit too fast, it can cause damages to the bricks, and the equipment attached. From the outside, a BF is like a big pot. You have an internal layer, the cooling system elements, and a water flow to control the temperature. Changing volumes must happen gradually.
Thermal shock produces different responses It is a challenge to keep the thermodynamic parameters. Hot metal causes reactions. All changes to the equilibrium affect the BF. The thermal shock produces different responses in different materials that change their volumes differently, thus creating internal forces/stresses in the materials that can break. There are varying opinions on the matter, but I firmly believe that if you want to do
it right, it takes three months. I have heard stories of it being done in only a few weeks, but I have serious doubts they are true. When the BF is off, we remove all bricks. It’s an opportunity to upgrade the cooling system, install new instruments and then reline all the bricks. It takes a lot of money and time. Replacing all the bricks would cost 100 million euros or more, it depends on the dimensions of the furnace—the composition, geometry. After relining, 20 years or more is added to the service life.
A delicate decision Switching off a BF is a delicate decision for a company. The market is never really stable, but you need a very comfortable market to have enough confidence. It is more efficient to have a BOF running at full capacity. Ideally, a company has 3 BFs—2 running, 1 off. In thermodynamic terms, this is the most efficient method. Taranto used to have 4 BFs, with 2 running. Piombino and Trieste have a troubled past, and they show that restarting a BF is not easy; you need investors (money) and the right conditions. Even projects for converting a BF site into an EAF (see Piombino) appear to be a complicated process. A BF is a perfect reactor with a configuration. You have the best performance if running at full capacity. One message
Aurelio Braconi, senior manager Circular Economy & Raw Materials at Eurofer
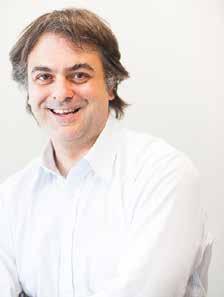
is: Guys, a BF is not an EAF. Keep in mind; it is very capital-intensive. It needs to run at full capacity. Some mills in the past kept the BF running, only to produce more ferrous slag as a by-product. Would Europe be better off with more EAFs, rather than BFs? BFs deliver the highest quality steel for most demanding applications—even more for crash impact, energy absorption. The more perfection you expect from steel, the more you must use the oxygen route. It’s a good theory having all steel come from EAFs, but in practice, there are limitations to the quality of ferrous scrap as used in EAFs. It is not clean enough. It’s perfect for long products and applications that are not very demanding in terms of steel cleanness. But certain special qualities can only be achieved with a BF. You do get some clean scrap from industry, but the largest amount is from society with the waste you need separate. There is more production from EAFs in the US, where the scrap comes mainly from pre-consumer, from production. Essentially, they buy clean scrap from stamping car sheet, for example, and they charge a lot of prereduced iron. If we did that in the EU, we would need to consider the higher price for reducing gas.
One alternative is DRI / HBI. We can do it in the EU, but is our structure ready for this in terms of energy availability, etc.? If so, companies may give it a thought. The US has cheap shale gas, and some US steelmakers have DRI installed abroad and import it. DRI and HBI can be a solution, but infrastructure and investments are needed before this type of transition can take place.
How to deal with the salamander
BFs are big shaft reactors (~3000 m3 internal volume). They are full with solid and liquid materials during normal operation. Burden and liquid descend, while gas ascends. The lower part of the BF that collects the molten hot metal is the hearth. BFs are equipped with tapholes to extract the liquid from the inside of the hearth in normal operation. The tapholes are placed around two meters above the bottom of the hearth. The room between the tapholes and the bottom of the hearth remains filled with molten hot metal. This is called the salamander. • If the stoppage is long, the salamander will solidify. • In a later stage, during blow in, it will gradually expand while heating-up. • This termal expansión (=dilatation) can crack the refractory blocks of the internal hearth linning. • Therefore, ArcelorMittal practise consists in extracting the salamander in case of long stoppages. A special salamander drill at the bottom of the hearth has to be carried out, in order to evacuate the liquid hot metal.
Information & pictures: ArcelorMittal
The physical shape of a blast furnace
Burden descent
Gas ascension

Hot blast
BFs are big shaft reactors (~3000 m 3 internal volume). They are full with solid and liquid materials during normal operation. Burden and liquid descend, while gas ascends.
The salamander drill
taphole
special salamander drill

A special salamander drill at the bottom of the hearth has to be carried out, in order to evacuate the liquid hot metal.