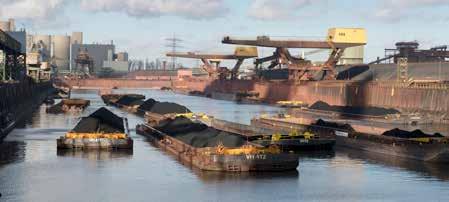
6 minute read
ThyssenKrupp: Digital Logistics on Water, in the Air and by Rail
ThyssenKrupp Steel, Germany’s largest steelmaker, is testing a digital logistics tracking system which enables every barge it uses for waterway transport to use the Internet of Things and equips it with a GPS sensor. The design minimises disruptions to raw material deliveries. The company is also testing drones for on-plant transportation and has introduced apps for train drivers.
It is around 240 kilometres by ship down the Rhine from Europoort Rotterdam to ThyssenKrupp Steel’s iron and steel mill complex in Duisburg. The river plays an important part in the supply of raw materials to the mill, and the direct route is a key locational advantage: up to 10,000 push barges supply the mill’s ports with iron ore, coal and other raw materials every year. Each of these over-75-metre-long, floating containers is capable of transThyssenKrupp receives íts coal and iron ore from Rotterdam via the Rhine river porting up to 2,700 tonnes of raw materials. This volume of traffic needs to be well-coordinated because space at raw materials. The result is sudden crane operators at the ports, from Rotthe ThyssenKrupp ports of Walsum and changes in barge traffic. terdam to Duisburg. A lot of communi
Advertisement
Schwelgern is finite: only a limited “There are disruptive factors that we cation is required for everything to run number of barges can be parked or unhave to take into account,” says Chrissmoothly. loaded at the same time. As part of its toph Pohl from the handling and storage digital logistics strategy, ThyssenKrupp logistics team responsible for raw mateOverview at all times Steel is optimising barge coordination rial handling at the mill’s ports. “They “Our goal was to implement a smart with state-of-the-art sensor technology. can all be overcome, but for that to hapdigital solution giving everyone access
Logistics can sometimes only be pen, we need to exchange the necessary to a live map of the supply chain,” explanned with short lead times. Storms information flexibly and quickly.” plains Walter Scheider from handling or poor visibility due to fog can cause It is a complex operation due to the and storage logistics at ThyssenKrupp delays, as can low Rhine water levels. numerous functions that need to be noSteel. “The idea was to reduce coordiMaintenance work on the blast furnaces tified of changes: from port planning to nation requirements and make it poscan also temporarily reduce demand for the blast furnace, from barge skippers to sible to synchronise processes better.” The most important tools for coordinating the more than 100 barges and various
ThyssenKrupp’s on-plant drone DelivAIRy, push boats along the Rhine and in the nicknamed „The Steel Bee“ ports are large amounts of operating data, cameras and telephones. The logisticians wanted to simplify this. Together with IT, handling and storage logistics and raw materials coordination, they sought a solution that would give everyone involved an overview at all times. They came up with a system whereby every barge is now IoT-capable (“Internet of Things”) and equipped with a solar-powered GPS sensor. By combining GPS data with information on orders and cargo, the team developed a digital map allowing all parties to keep track of every barge at all times—including information on tonnage, raw material car
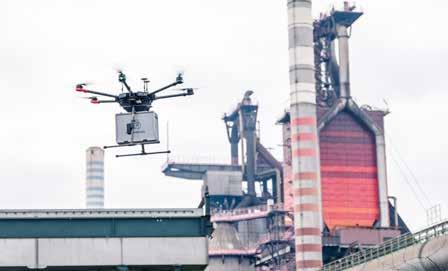
go and port arrival time calculated using artificial intelligence. As a result, time and costs can be saved—e.g., by sending a signal to shipmasters on their way to Duisburg telling them to reduce their speed— and fuel consumption— when it is clear they would have to wait outside the port anyway.
“Live tracking allows us to plan much better in advance,” explains Christoph Pohl. “At the same time, the data we collect can help us analyse and optimise processes. For example, we can track precisely where and when which barges face waiting times and then look for ways to reduce them.”
An aerial “pilot” project: The Steel Bee delivery drone
Most recently, the steelmaker started using a drone to deliver samples across the plant. Nicknamed “the steel bee”, its official project name is the delivAIRy delivery drone. It regularly takes off to deliver samples across the Duisburg steelworks site to the lab for further processing. It is part of a joint project by Kassel-based start-up Doks. innovation GmbH and ThyssenKrupp Steel to test drone delivery processes on the plant site.
The two partners have just been awarded the Regulatory Sandboxes Innovation Prize by the Federal Ministry for Economics for this ongoing project. “ThyssenKrupp offers an application far from last-mile-delivery that can already be implemented today,” says Benjamin Federmann, founder and managing director of Doks. innovation GmbH. “Thanks to the good cooperation with ThyssenKrupp and the local authorities, we can already test and establish forward-looking technologies under real conditions today.” “The transport drone flying reliably and automatically over our works site is a concrete and visible example of digitalisation in everyday industrial life. This project not only makes transportation modern and digital but also sustainable, more efficient and safer,” says Bernhard Osburg, CEO of ThyssenKrupp Steel.
Airborne at the push of a button Project manager Dr Thomas Lostak, team leader of Innovation at ThyssenKrupp Steel, is optimistic about the future. “If the automated flying robot proves successful for the transportation of lab samples, it could also be used in other areas of internal logistics in the future. The drone can be called
Communication between train drivers and schedulers is now mostly by app
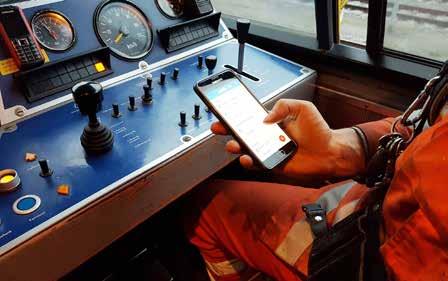
individually via an app. Time-critical deliveries on our plant site in Duisburg can now be fully automated and digitalised.” According to Lostak, the project has also been well-received by employees. The use of the drone gives form to the abstract concept of digitalisation and provides fresh momentum for other digitalisation projects.
The automated drone (no pilot required) delivers samples across the plant site, flying over main roads and railway lines in the process. As soon as the transport box is attached to the drone by a patented gripper mechanism, it can be sent to its destination at the push of a button. Unlike the cars normally used for this, the drone reaches its destination in just 10 minutes, saving time and benefiting the environment. The drone also incorporates the highest safety standards and can land at an emergency landing point if needed.
The start-up Doks. innovation was founded near the Fraunhofer Institute for Material Flow and Logistics IML in Dortmund in 2017 and relocated to Kassel in 2018. The company develops solutions for automated data capture and processing in logistics, combining innovative carrier technologies, such as drones, highly sensitive sensors and intelligent software with machine-learning algorithms to form a powerful ecosystem for efficient logistics processes.
Digitalising order scheduling in rail operations
A rail network of around 300 kilometres covers the ThyssenKrupp Steel site in the north of Duisburg. Rail is the key means of transport for raw materials and products around the site and beyond its boundaries. ThyssenKrupp Steel recently introduced an app to facilitate communication between order schedulers and engine drivers.
The previous system had reached its limits
In the past, communication was primarily via radio. The scheduler would generate an order in the system, inform the engine driver, wait for confirmation and then confirm the order in the system—a complicated and time-consuming process for everyone involved. “To change this, we set up a multidisciplinary team,” says Michael Heise, Senior Engineer from Logistics at ThyssenKrupp Steel. “Our goal was to create a digital record of work orders without the need for communication between scheduler and engine driver.”
After only four weeks, the prototype was ready for field testing, including built-in feedback from train drivers and dispatchers. The team also helped develop the underlying cloud-based system architecture. As a result, the exchange between schedulers and train drivers now takes place almost exclusively via a newly developed app.
All in all, a lot of radio communication become superfluous. Also, future apps can use the new cloud environment, which is one of the reasons why Michael Heise’s team was among the winners of the company’s internal “Steel Tomorrow” innovation competition in December 2019. Another piece of the puzzle of the ThyssenKrupp Steel digitalisation roadmap. The new app is representative of many initiatives with which ThyssenKrupp Steel is systematically driving the digital transformation forward..