
9 minute read
DRI for the Future, Part II: ThyssenKrupp, Salzgitter
ThyssenKrupp’s concept of a direct reduction plant with a melting unit
In case you haven’t noticed, there is no question mark to the headline ‘DRI for the Future?’ anymore. Things seem to be happening fast in this respect, both in Germany and beyond. In August alone, ThyssenKrupp came up with a timetable for a direct reduction plant, Salzgitter announced a feasibility study.
Advertisement
The green transformation of ThyssenKrupp Steel, Germany’s largest steel producer, is taking shape with a concept for the construction of the first direct reduction plant with an integrated melting unit (blast furnace 2.0) at the group’s mill complex in Duisburg. Above all, ThyssenKrupp is focusing on hydrogen: tests are currently being conducted to use hydrogen in conventional blast furnace operation to reduce the CO 2 footprint of steel production in the short term and produce the first batches of CO 2 -neutral steel. The next milestone will be the construction of a novel integrated direct reduction plant, allowing significant reductions in emissions.
The development of direct reduction plants (DR plants) represents a key change. DR plants operate using gases. If hydrogen is used, they release no emissions. Since carbon-neutral hydrogen will not be available in sufficient quantities in the foreseeable future, natural gas can also be used temporarily. This will lead to a significant reduction of emissions as compared to the coalbased blast furnace route. ThyssenKrupp Steel will commission the first largescale DR plant in 2024.
Integration of DR plants into the existing steel mill
In contrast to the blast furnace, DR plants do not produce hot metal, but solid sponge iron (“Direct Reduced Iron”, DRI). It must be melted down into a hot metal product for further processing into high-quality steel. Together with manufacturers, ThyssenKrupp Steel claims that it is developing a completely new plant to optimise the hot metal system. It is a power-operated melting unit, which is combined with the DR plant. Like a blast furnace, direct reduction plants with melting units produce a liquid product. As a result, the new plants can be seamlessly integrated into existing metallurgical plants. The great advantage is that the existing and proven processes in the Duisburg-based BOF melt shops can be maintained. The liquid product is processed into the proven steel grades there.
Electrical hot metal from blast furnace 2.0
This currently unique concept offers several advantages. It is largely based on the existing structures of Europe’s largest integrated steel production site, which means that considerably less investment and operating costs are involved. Another important advantage for customers is the maintenance of the complete product portfolio, as the existing steel mills and processes can still be used. One innovation, in particular, enables this path towards climate-neutral
ity: the solid material produced in the direct reduction plant is liquefied in an integrated melting unit. This blast furnace 2.0 produces “electrical hot metal”, which is processed in the existing metallurgical plant in an energy-efficient manner. The integrated direct reduction plant is to be operated with green hydrogen and green power in future. It is an important step towards the achievement of the climate goals of the company and those defined by the Paris Agreement. ThyssenKrupp has set itself the target to reduce its CO 2 emissions by 30% by 2030 and plans to complete the main part of the plant by 2025 and produce 400,000 tonnes of green steel. For 2030, the company aims at 3 million tonnes of climate-neutral steel.
Another important advantage of the concept is the relatively fast ramp-up of climate-neutral steel production. The first direct reduction plant with melting unit will have an annual production capacity of 1.2 million tonnes. As long as hydrogen is not available in sufficient quantities, the plant can be operated with natural gas. This will already allow significant CO 2 emission reductions and the production of significant amounts of green steel without compromising the quality of the products.
In late August, Federal Economics Minister Peter Altmaier and North Rhine-Westphalia’s State Premier Armin Laschet visited ThyssenKrupp’s steel complex in Duisburg. On that occasion, ThyssenKrupp AG CEO Martina Merz and ThyssenKrupp Steel CEO Bernhard Osburg revealed the timeline the group has developed for its transformation towards DRI. In his speech to the ministers, Osburg emphasised that ThyssenKrupp is pursuing a very own path. Here is a summary: “Our project is called “tkH2Steel”. This means nothing other than “ThyssenKrupp produces carBernhard Osburg, bon-neutral steel with ThyssenKrupp hydrogen and green Steel CEO electricity”. However, our blast furnace 2.0 concept is unique and differs from classic electric steel routes in three key advantages. Our concept offers the most cost-effective transformation of an integrated steel mill network - such as the one we have here covering an area of over 10 square kilometres. We need up to 30% less investment than the steel industry concepts we are familiar with today on the road to climate neutrality. How can this be achieved?
To neutralise the steel industry’s CO 2 emissions, we have to look at primary steel production, which today accounts for over 90% of global steel production.
In order to decarbonise this pig iron route, most concepts— and we have followed this path for a long time—rely on a direct reduction plant and then on the so-called EAF electric arc furnace route. However, this transformation path has some disadvantages for us: the process requires considerable intervention in the steelworks and secondary metallurgy, is highly energy-intensive and offers us only a limited product portfolio. ThyssenKrupp Steel recognised these problems early on and therefore developed Blast Furnace 2.0 as an alternative technological approach: we have integrated a conventional direct reduction plant with an innovative melting unit to create a “hydrogen-powered electric blast furnace”.
tkH2Steel transforms a complete green product portfolio
In blast furnace 2.0, green hydrogen does the reduction work, and in the lower part of the melter, green electricity takes over the liquefaction of the directly reduced iron to “electric pig iron”. This basic principle is as simple as it is efficient. With the climate-neutral pig iron produced in this way, we then enter our infrastructure, which has been optimised and available for many decades. This path is minimally disruptive and therefore requires significantly less investment:
We only change the first part of the liquid phase to the pig iron. The coking plant, the sinter plants and the blast furnaces with the large CO 2 emissions are gradually being eliminated. But we will continue to use the existing steel plants unchanged, saving billions of euros in investment.
And not only is the investment required lower; future operating costs are also much lower compared to the electric arc route. This is due to significant efficiency advantages along our process chain, such as the so-called hot link to the steel mill: the liquid electric pig iron from Blast Furnace 2.0 can be processed without energy loss, just as it is today directly in our existing steel plants. The lower operating costs will also make our green steel products very competitive.
By continuing the processes from the steel mill onwards which determine the product properties unchanged, we can offer our customers our high-quality flat steel portfolio as a green portfolio without restrictions. This is not a matter of course from a metallurgical point of view, especially in the case of highly specialised steels such as e.g. for electric mobility or in packaging steel. This is unique in Europe.”
The state premier of North Rhine Westphalia, Armin Laschet; German economy minister Peter Altmaier; ThyssenKrupp CEO Martina Merz; ThyssenKrupp Steel CEO Bernhard Osburg
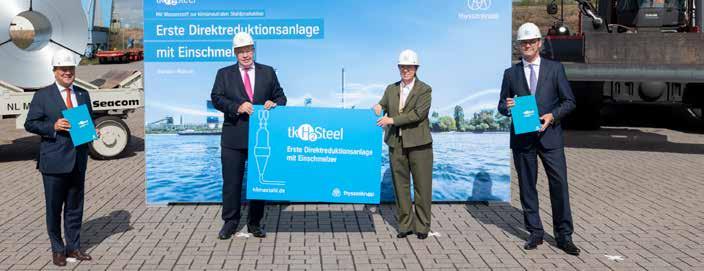
Salzgitter AG projects DRI plant on the North Sea coast
Salzgitter AG, Germany’s second-largest steelmaker, is launching a feasibility study for the construction of a direct reduced iron (DRI) plant with an upstream hydrogen electrolyser at the deepwater port of Wilhelmshaven in the federal state of Lower Saxony. To that end, it has signed an agreement with the state government of Lower Saxony, the City of Wilhelmshaven and the industrial partners Rhenus—a logistics company—and utility company Uniper.
The study includes potentially building a DRI plant and developing the necessary infrastructure for supplying it with raw materials, natural gas and hydrogen. The results are expected to be available by 31 March 2021 at the latest, Salzgitter says.
“This is another concrete step in our process of evolving toward low CO 2 , hydrogen-based steel production underpinned by our prestigious SALCOS (SAlzgitter Low CO 2 Steelmaking) technology concept. Once this step has been realised, we will be making a decisive contribution to achieving the climate targets,” says CEO Heinz Jörg Fuhrmann. If the findings of the feasibility study are successful, follow-up activities in the form of joint implementation of the project have been planned. The envisaged target is to produce two million tonnes of directly reduced iron per year, which will be transported to the city of Salzgitter by rail and processed into high-grade, environmentally compatible strip steel products in Salzgitter Flachstahl GmbH’s integrated strip steelworks.
Direct reduction
From a technological standpoint, there are options to expand the existing steelworks—in line with our endeavours to reduce emissions—and integrate new facilities. Iron ore could initially be reduced to iron using natural gas and a higher volume of hydrogen in a direct reduction reactor. The reaction takes place at 950°, producing sponge iron. This method can achieve a reduction of iron of up to 85%. The facilities in question also use an integrated process. Gas is introduced in a circular pattern and, after separation of the water produced by the reduction, cleansed of any remaining CO 2 and reused.
The challenge inherent to direct reduction consists of integrating the new facilities into the existing steelworks. Through the gradual implementation of a reactor of this kind, initial CO 2 savings of up to 50% are theoretically possible. If in the future, the entire production can be switched to a direct reduction plant, this figure could be further increased—up to 85%.
Future opportunities for direct reduction
This undertaking cannot be directly implemented from a technical and financial standpoint. The SALCOS team and collaborators from the Fraunhofer Institute are working on a concept for a staged conversion. Current calculations show that CO 2 emissions could be reduced even more substantially by 2050 than originally estimated by politicians.
Along with technological considerations, whether CO 2 -reduced steel production under SALCOS is a promising project or just a desirable vision ultimately hinges on political framework conditions and economic efficiency criteria, Salzgitter notes.
GrInHy2.0: Sunfire supplies the world’s largest High-Temperature Electrolyser to Salzgitter Flachstahl

In August, Sunfire delivered what it says is the world’s most powerful high-temperature electrolyser (HTE) for highly energy-efficient hydrogen production to Salzgitter Flachstahl GmbH. Within the GrInHy2.0 project, the HTE system with a rated electrical output of 720 kilowatts will be deployed in an industrial environment for the first time. GrInHy2.0 is another step by Salzgitter AG towards low An illustration of the GrInHy 2.0 system at Salzgitter AG CO 2 steel production within the framework of the SALCOS innovation project. The electrolyser is expected to be in operation for at least 13,000 hours by the end of 2022, producing at least 100 tonnes of green hydrogen with renewable electricity.