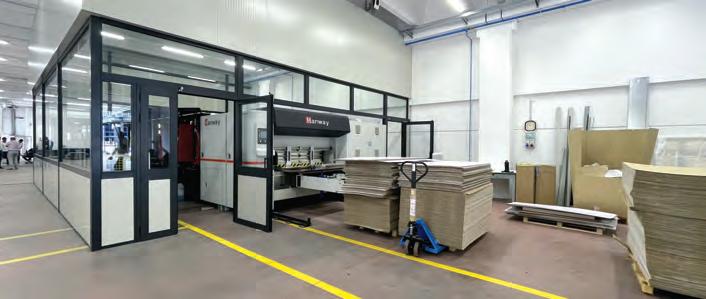
5 minute read
Zetacarton Con Hanway Glory 1606 fa un salto nel futuro
Da sinistra Christian Rinaldo, Ceo di Errelle, Giuseppe Zanfrini presidente del Cda di Zetacarton, Serena Zanfrini, amministratore delegato di Zetacarton, Filippo Bombardieri, technical sales manager di Zetacarton, e Luca Pallo, CTO e fondatore di Errelle e Hanway Italia
In Italia la prima installazione europea del sistema industriale post-print Hanway per la stampa inkjet singlepass su cartone ondulato
Tra il distretto comasco del tessile e la Brianza del mobile e dell’interior design, esattamente nella zona industriale di Senna Comasco (CO), si trova un’altra eccellenza italiana che da cinquant’anni produce cartone ondulato, scatole e imballaggi: Zetacarton, dove zeta sta per l’iniziale del cognome dei suoi fondatori Angelo Zanfrini e i figli Giovanni, Giuseppe e Cesare. Nata nel 1974, è diventata in breve tempo riferimento del proprio settore nel territorio. In realtà l’idea del business della cartotecnica viene da più lontano, quando negli anni ’50 Angelo e Maria Zanfrini diedero il via a una piccola attività tipografica a cui successivamente affiancarono la produzione di scatole in cartone teso e ondulato. Quella delle origini di Zetacarton è una storia di dedizione, competenza e passione ma anche di slanci pionieristici che l’hanno condotta al successo attuale e alla decisione di oggi di proiettarsi nell’era del digitale in collaborazione con Hanway ed Errelle (Hanway Italia).
Una leader che continua a fare progetti
Guidata da Giuseppe Zanfrini, presidente del Cda, e da Serena Zanfrini, amministratore delegato – che rappresenta la terza generazione in azienda – oggi Zetacarton è leader di mercato in Italia, con un fatturato nel 2022 di circa 78 milioni di euro e la produzione annuale di 110.000.000 mq di cartone ondulato, sia in fogli sia a modulo continuo. Per dare un’idea delle proporzioni si tratta dell’1,22% dei volumi nazionali: considerando che l’Italia è il secondo produttore in Europa è un notevole risultato. L’azienda, che opera in un moderno stabilimento di 30.000 mq coperti su una superficie totale di 60.000 mq e occupa 110 addetti, ha sempre messo a segno investimenti strategici sia per il reparto di produzione del cartone sia per le macchine da stampa flessografiche e offset, precorrendo i tempi e a volte scegliendo percorsi alternativi rispetto ai concorrenti.
“Questo è il futuro!” ci accoglie così Giuseppe Zanfrini mostrandoci la Hanway Glory 1606 installata in un’area dedicata del sito produttivo di Zetacarton. La macchina, operativa da giugno 2023, nel momento in cui visitiamo l’azienda sta stampando a pieno regime e la soddisfazione delle persone che le stanno attorno si percepisce immediatamente. Vediamo un operatore prelevare un foglio dalla pila in uscita ed esaminarlo insieme ai colleghi e ai tecnici di Hanway e Hanway Italia: “Ci siamo: perfetto”, afferma.
Flusso di produzione digitale
Chiediamo a Giuseppe Zanfrini di commentare questa tecnologia: “Siamo molto soddisfatti” risponde. “Desideravamo diversificare la produzione introducendo la tecnologia digitale per ampliare la nostra
L’alimentatore e la cabina di condizionamento costruita intorno ai moduli di stampa e asciugatura di Hanway Glory 1606, installata nello stabilimento di Senna Comasco (CO) di Zetacarton offerta di prodotti e per migrare alcuni lavori dalla stampa tradizionale all’inkjet . Dopo aver considerato anche altre soluzioni, abbiamo scelto Hanway Glory. Siamo certi che la nuova macchina sarà all’altezza delle nostre aspettative anche in futuro”. La parola futuro associata a Glory 1606 emerge più volte nella conversazione: c’è un piano industriale preciso intorno a questo investimento che prevede la messa a punto nei prossimi due anni di un’intera linea di produzione digitale automatizzata a ciclo completo. A spiegarci nel dettaglio come si concretizzerà il progetto è Filippo Bombardieri, technical sales manager dell’azienda. Percorriamo insieme a lui gli oltre 5 metri di lunghezza della macchina: “A monte dell’alimentatore installeremo un caricatore automatico che stiamo studiando ad hoc” spiega, mentre procedendo ci mostra la cabina per il condizionamento dell’aria. Costruita intorno all’unità di stampa e asciugatura a infrarossi per consentire il controllo della temperatura e dell’umidità, ha lo scopo di mantenere al massimo l’efficienza delle teste di stampa e la stabilità dei fogli di cartone. Superata l’unità di verniciatura – plus unico su questa categoria di macchina che consente di evitare la plastificazione protettiva del cartone – ci spostiamo verso lo stacker. Ma il percorso non è finito: “Da questa parte ci sarà un collegamento al capannone adiacente per congiungere la stampa al reparto di finishing dove saranno installati voltapila, plotter da taglio, fustellatrici e, infine, una linea di confezionamento del cartone” prosegue Bombardieri.

Perché
proprio Glory?
“La qualità, la versatilità del sistema e l’analisi del TCO, che abbiamo condotto facendo fede alla trasparenza dei dati forniti dal produttore, sono gli elementi che ci hanno convinti a investire in Hanway Glory 1606” afferma Giuseppe Zanfrini. Tecnologia inkjet single pass a 6 colori (CMYK+LC e LM) – anche se la configurazione scelta da Zetacarton si ferma alla quadricromia – teste di stampa Kyocera, inchiostri base acqua e compatibili con il contatto alimentare, RIP Caldera: sono le caratteristiche di questo sistema industriale, compatibile con le diverse tipologie di cartone ondulato (bianco, kraft e rivestito) e in grado di raggiungere velocità di stampa fino a 180 metri/minuto.
“Anche il rispetto per l’ambiente è un aspetto cruciale: l’utilizzo di inchiostri base acqua non nocivi per l’ambiente si sposa perfettamente con il cartone, materiale riciclabile e che può essere prodotto con una
I moduli di stampa di Hanway Glory 1606, sistema inkjet single pass per la stampa di cartone ondulato percentuale di fibra riciclata: sono tutti elementi in linea con le nostre strategie di sviluppo orientate ai criteri ESG” specifica Serena Zanfrini che ci informa che sta terminando insieme al suo team la stesura del Rapporto di sostenibilità aziendale. L’arrivo di Glory è stato ben accolto anche dagli operatori: quattro addetti del reparto stampa di Zetacarton sono stati entusiasti di passare alla divisione digitale, potendo diventare parte attiva di questo importante progetto. Fa parte del team dedicato al reparto digitale anche un nuovo addetto di prestampa.
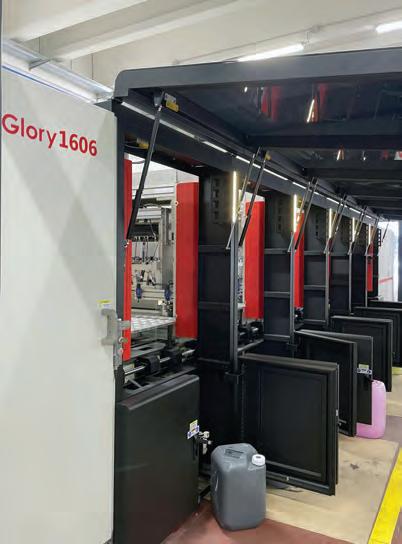
Una partnership win-win
A determinare la partnership tra Zetacarton e Hanway anche una particolare affinità di valori e modalità operative tra queste due realtà, emersa sin dal primo incontro con la forza vendite di Errelle. “Come Hanway Italia avevamo programmato l’installazione della Glory 1606 nel nostro showroom di Torino” spiega Luca Pallo CTO e fondatore di Errelle, “ma quando abbiamo presentato alcuni campioni stampati con questa tecnologia al management di Zetacarton, la decisione di investire in questo sistema è stata presa così rapidamente al punto che abbiamo destinato la spedizione della macchina direttamente al sito produttivo di Senna Comasco”. A convincere il cliente non sono state soltanto le prestazioni della macchina ma anche la grande flessibilità di Hanway nell’assecondare alcune sue esigenze di customizzazione. Su richiesta di Zetacarton il formato carta stampabile di Glory 1606 di 160x280 cm è stato portato a una lunghezza di 405 cm, per consentire la produzione di imballaggi per i mobili e per il rivestimento dei pallet; un’altra modifica ha riguardato lo spessore minimo del supporto da 1,5 mm a 1,3 mm. Per contro Zetacarton si è data disponibile a fare da beta site europeo dimostrandosi aperta ad accogliere aziende interessate a visionare la macchina e a effettuare prove di stampa. “È una sfida epocale – conclude Luca Pallo. “I nostri tecnici, quelli di Hanway e il team di Zetacarton stanno lavorando insieme per far decollare un progetto che farà da apripista per l’affermazione in Europa della tecnologia inkjet single pass per il cartone ondulato”.
Per definizione le aziende di stampa di produzione sono entità dinamiche, paragonabili a essere viventi che crescono e sono in continua evoluzione. Per il semplice motivo per cui la stampa di per sé, rispetto ad altre attività industriali, riguarda una produzione di piccoli lotti, a maggior ragione nulla rimane costante. Fatturato, clienti, lavorazioni… da commessa a commessa possono avere specifiche completamente diverse. Se da sempre software e apparecchiature possono essere sostituiti seguendo i progressi della tecnologia, oggi anche il personale potrebbe avere un turn over più frequente rispetto al passato. Per essere resilienti ai continui cambiamenti, è necessario strutturare processi solidi supportati dall'automazione del flusso di lavoro. Spesso, il lavoro viene organizzato grazie alla buona volontà dei dipendenti più lungimiranti, ma anche loro possono stancarsi e incorrere in errori nella produzione che si traducono in costi aggiuntivi per la ristampa. Qual è la soluzione, allora? È indispensabile mettere a punto un sistema flessibile e guidato dai processi in grado di ottimizzare la capacità produttiva e il lavoro delle presone. Il primo step è effettuare un assessment!