
6 minute read
Beyond compliance
In order to obtain a licence to work with asbestos, an asbestos removal contractor must be able to demonstrate to the Health and Safety Executive (HSE) that they have excellent health and safety management systems, and that the required knowledge is put into practice on site.
Once a licence has been obtained, the management of the Licensed Asbestos Removal Contractor (LARC) will need to monitor all of their activities to ensure compliance with all relevant legislative requirements and associated guidance. Such compliance is seen within the asbestos industry as a minimum compliance level.
As asbestos removal is part of a permissioning regime, the normal forms of regulation (on their own) are considered insufficient, and the extra demands imposed by the regime are considered justified by the benefits it brings.
So, the effective management of a LARC, and therefore licence continuity, depends on moving beyond minimum compliance. For example, licence holders: w must identify the hazards, assess the risks, review the extent to which health and safety is part of the process, develop effective control measures (for those hazards which cannot be eliminated) and record these in their health and safety documentation, which should be reviewed and kept up to date w must ensure that control measures recorded in the health and safety documentation cover design and hardware, systems and procedures, and human organisational factors as a collective whole; and should include the licence holder’s safety criteria and performance standards, as well as plans for improvement w must properly resource their processes for producing and maintaining health and safety documentation w must implement the control measures, review them regularly and keep them up to date with a view to continuously improving them to reduce risks w must make and test arrangements for managing emergencies and mitigating their consequences.
In addition to effective leadership from top management, ARCA and the HSE would expect LARC’s to demonstrate competence at all levels of the organisation, both office based and on site. They would also expect LARC’s to make full and proper use of all information gathered from site activities, and use their findings to feed their assessments and planning of future jobs.
Minimum compliance would require certain records to be kept, e.g. daily inspections of: w enclosures (including airlocks and baglocks)
w hygiene facilities
w vacuum cleaners
w air extraction equipment
w wet injection equipment (when in use)
w
respiratory protective equipment. This would include the reporting of defects and remedial actions taken.
Going beyond minimum compliance would ascertain the accuracy of the records kept, as well as patterns, trends, identification of root causes, and implications for the future.
Other information gathered and kept from site activities may include air monitoring, which becomes far more meaningful if planned with forethought and purpose. A LARC may consider having leak tests or personal monitoring conducted during asbestos removal works as compliance (i.e. data has been gathered). However, the data is of little use if it can’t provide much useful information. Leak tests may therefore be planned for the first part of the first shift of actual asbestos removal, in specific locations such as adjacent to air extraction equipment (especially if extracted air cannot be vented directly to external atmosphere) or next to areas of the enclosure that may have been potentially difficult to seal. Such specifics are the level of detail required at the planning stage if LARC’s intend on moving beyond minimum compliance.
Personal monitoring, per se, may be thought by some as compliance, but to be meaningful and go beyond mere compliance will require taking personal monitoring a step further. One example could be determining the actual airborne fibre concentration surrounding the operative when removing the first four ceiling tiles, which may disturb debris above or introduce a sudden influx of air from the unsealed, potentially contaminated void above. How does this concentration differ from the operative placing the ceiling tiles into the waste bags?
Site audits, well designed, can also be a vital source of meaningful information. The current ARCA Site Audit has been designed with this in mind, and future reviews will continue to investigate further ways to enable the LARC to maximise the usefulness of the audit findings.
LARC’s should not confuse an abundance of data with meaningful information. LARC’s should absolutely meet the minimum compliance criteria, but in addition, should always be seeking ways to exploit the information gathered, thinking through ahead of the job what information is required.
A key element of effective health and safety management is leadership. While management may be seen as ‘doing things right’ (i.e. doing things by the book, or the company procedures), leadership is about ‘doing the right things’ (i.e. moving beyond mere compliance and rewriting the book if that is what is required). When leadership
and management work effectively together, the end result is ‘doing the right things right’.
HSE publication HSG65, Managing for Health and Safety, provides examples of what effective and ineffective leadership and management look like to check you are doing what you need to do, and also gives some examples of going beyond compliance. These are reproduced in the tables shown.

For more information on the competency qualifications that ARCA offer, visit ‘qualifications’ at www.arca.org.uk For more information on site audits and other services that ARCA offer, visit ‘support’ at www.arca.org.uk
What it looks like when done effectively
Leaders
w Maintain attention on the significant risks and implementation of adequate controls w Demonstrate their commitment by their actions; they are aware of the key health and safety issues w Ensure consultation with the workforce on health and safety w Challenge unsafe behaviour in a timely way
Management of Health and Safety
w A systematic approach is used to manage health and safety w People understand the risks and control measures associated with their work w Contractors adhere to the same standards w Appropriate documentation is available: current, organised, relevant w People understand their roles and those of others w Performance is measured – to check controls are working and standards are being implemented, and to learn from mistakes after things go wrong
Beyond Compliance
w If a formal system (such as ISO 45001, ISO 9001) is used, has it been externally certified – is the certification accredited? w Health and safety is integrated into business processes w Benchmarking is used to compare performance with others w Supply chains are influenced to improve health and safety w A ‘wellness’ programme is in place
What it looks like when done badly or not at all
Leaders
w Set no health and safety priorities w Don’t understand the need to maintain oversight w Don’t meet their own organisation’s standards/ procedures, e.g. wearing correct PPE on site/shop floor w Lack of engagement with health and safety by workers w Health and safety is seen as an add-on, irrelevance or nuisance w Poor incident history (accidents, near misses, plant damage or other indicators, e.g. poor maintenance, poor housekeeping)
Management of Health and Safety
w Incomplete or missing paperwork. Does not link to actual risks in workplace w Confusion over roles, inaction as no one takes responsibility for health and safety, distrust of management motives w Widespread, routine violations of procedures. No oversight of contractors w Information is not passed on, not understood, or not implemented w Managers are unaware of employee concerns or do not respond appropriately w Lessons are never learned
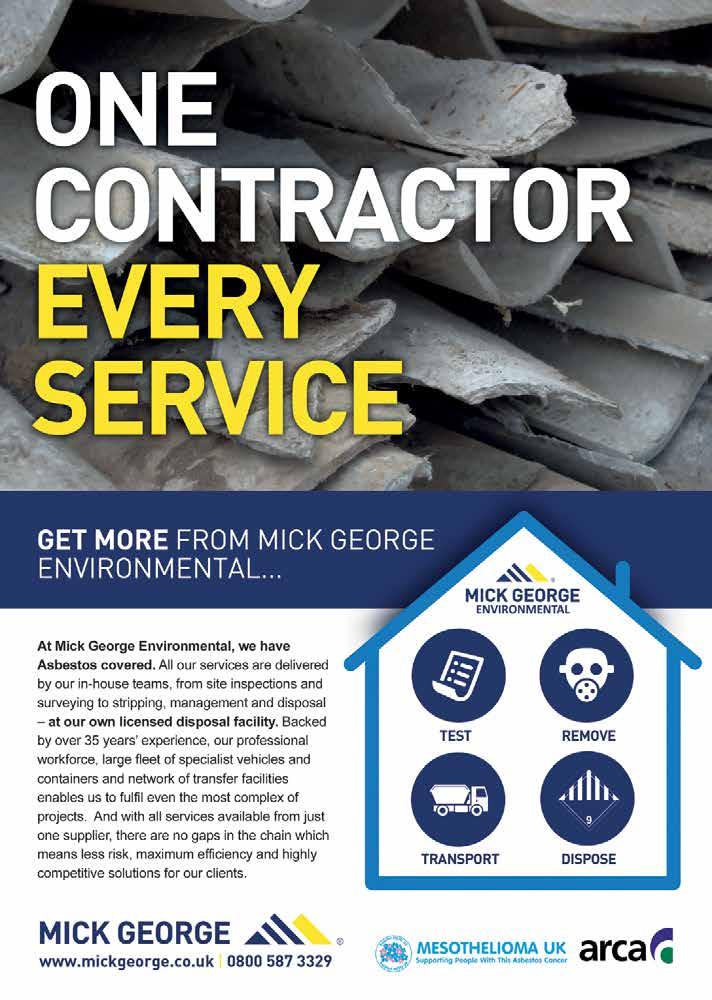